Introduction
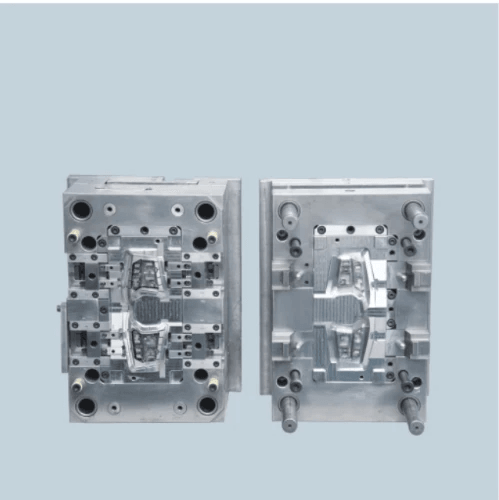
In the world of plastic injection molding, understanding the nuances of different gate types is crucial for achieving optimal results. One such gate type that has garnered attention is the tunnel gate, a design that offers unique advantages in various applications. This introduction will explore tunnel gate injection molding, elucidate the role of gates in the injection molding process, and highlight why considering tunnel gates for your projects can be a game-changer.
Understanding Tunnel Gate Injection Molding
So, what is a tunnel gate in injection molding? Simply put, it's a specialized entry point through which molten plastic flows into a mold cavity. The design features a channel that runs parallel to the parting line of the mold, allowing for efficient filling while minimizing marks on the finished product. This unique structure not only facilitates better control over material flow but also enhances aesthetic outcomes by reducing visible gate marks.
The Role of Gates in Injection Molding
Gates play a pivotal role in injection molding by controlling how molten material enters the mold cavity. Essentially, they act as valves that regulate flow and pressure during the injection process, ensuring that every nook and cranny of your design gets filled without defects. Understanding what is the gate in injection molding helps manufacturers choose wisely among various types of gates for their specific projects.
Why Consider Tunnel Gates for Your Projects
For one, they provide excellent surface finish quality and reduce post-processing requirements due to minimal visible marks on parts. Additionally, understanding what is the angle of a tunnel gate can help engineers optimize designs further—leading to improved performance and efficiency in plastic injection molding processes.
What is a Tunnel Gate in Injection Molding
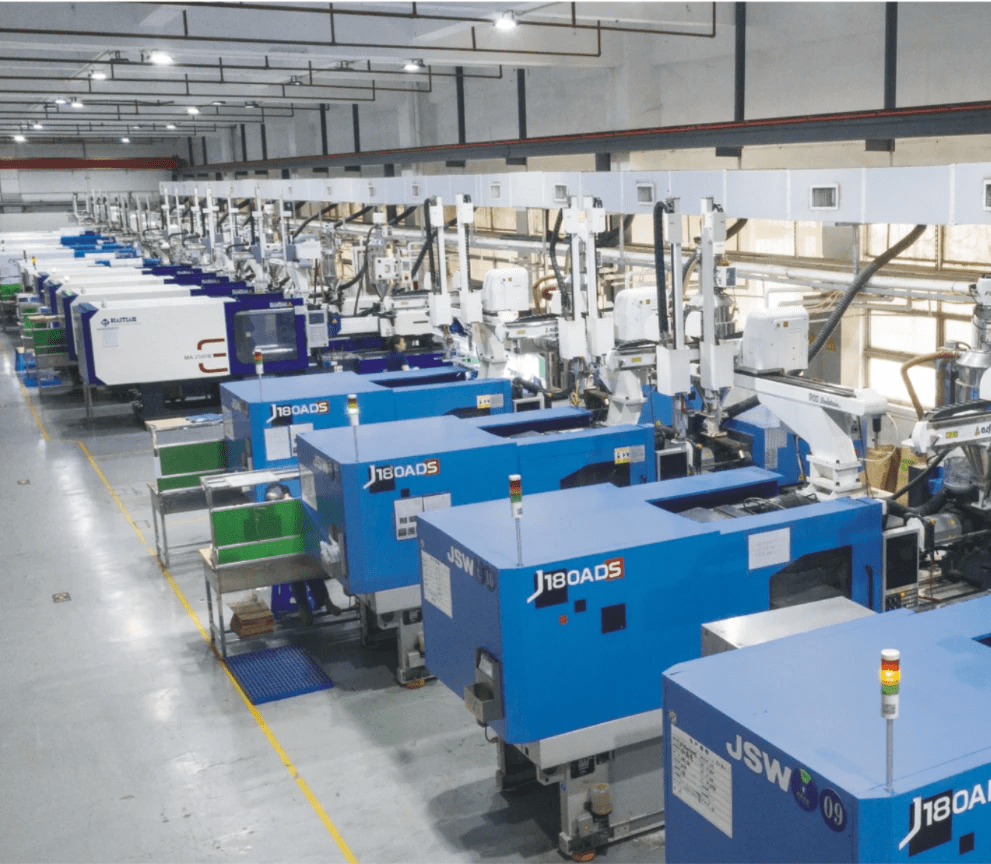
When diving into the world of tunnel gate injection molding, it's essential to grasp what exactly constitutes a tunnel gate. A tunnel gate is a specific type of injection molding gate that allows molten plastic to flow into the mold cavity through a channel or tunnel. This unique design not only facilitates efficient filling but also minimizes the risk of defects, making it a popular choice in various applications.
Definition and Key Features
So, what is a tunnel gate in injection molding? Essentially, it's an opening that connects the injection nozzle to the mold cavity via a narrow passage. One key feature of tunnel gates is their ability to provide controlled flow rates, which leads to better consistency and quality in molded parts. Additionally, they often come with specific angles—what is the angle of a tunnel gate? Typically, these gates can have varying angles depending on design requirements, but they are usually set at an incline to ensure optimal material flow.
Applications in Plastic Injection Molding
Tunnel gates find their niche across various sectors within plastic injection molding. They are particularly effective for complex geometries where precise filling is crucial—think automotive parts or intricate consumer goods. Moreover, due to their efficiency and reliability, tunnel gates are increasingly being used in high-volume production runs where consistency and quality cannot be compromised.
Benefits of Using Tunnel Gates
The benefits of using tunnel gates are numerous and compelling for any project manager considering options for their next plastic injection molding endeavor. First off, these gates reduce the likelihood of defects such as short shots or sink marks by allowing for more uniform fill patterns—who wouldn’t want that? Furthermore, because they can be designed with specific angles and dimensions tailored to your needs (yes, we’re talking about what is the angle of a tunnel gate?), you can achieve greater control over your production process compared to other types of gates for injection molding like fan or edge gates.
The Basics of Injection Molding Gates
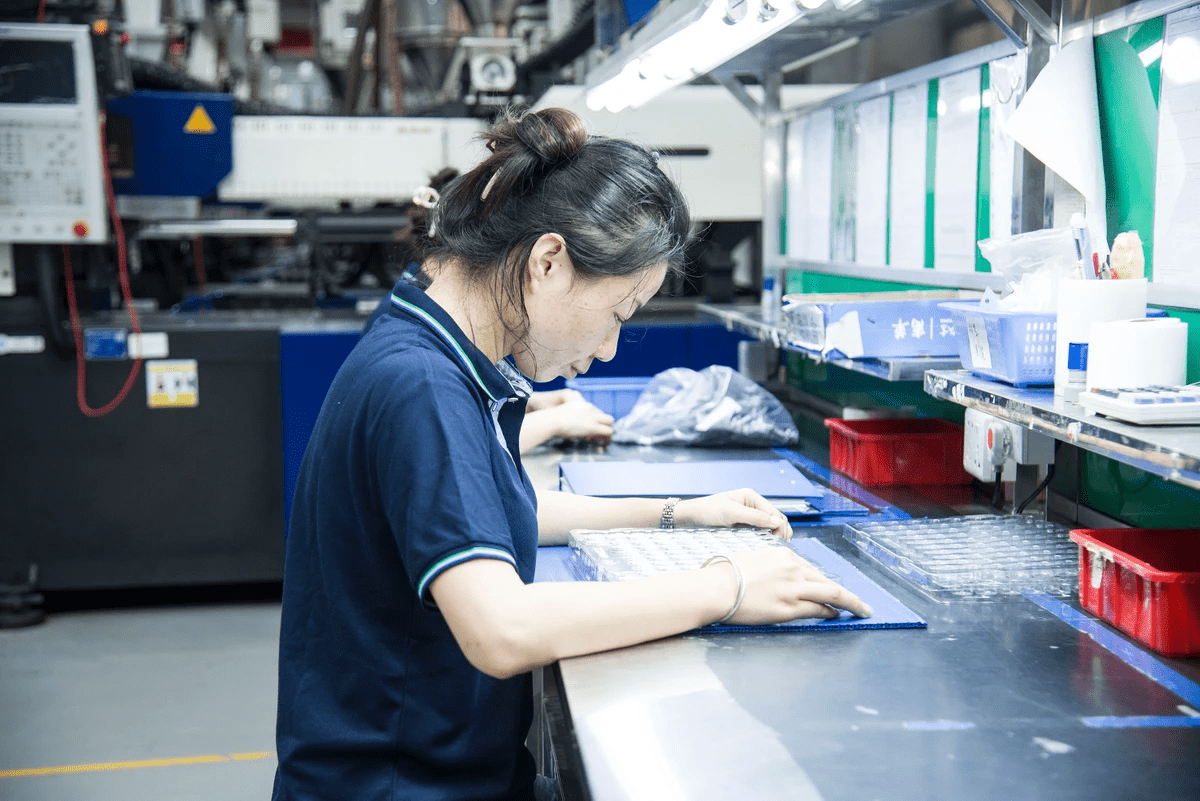
Understanding the fundamentals of injection molding gates is crucial for anyone involved in plastic injection molding. Gates are the critical points where molten plastic enters the mold cavity, influencing everything from flow patterns to surface finish. Among the various types of gates, tunnel gates are gaining popularity due to their unique design and benefits.
What is the Gate in Injection Molding?
In injection molding, the gate serves as a passageway for molten resin to flow from the runner system into the mold cavity. It plays a pivotal role in controlling how quickly and evenly the material fills the mold, which can significantly affect product quality. The type of gate used can impact factors such as cycle time, part strength, and aesthetic finish—hence why understanding What is a tunnel gate in injection molding? becomes essential for designers and engineers.
Different Types of Gates for Injection Molding
There are several types of gates for injection molding, each suited to specific applications and materials. Common types include edge gates, fan gates, and tunnel gates—each with its own set of advantages and limitations. Understanding these variations helps manufacturers select the most appropriate gate type based on production requirements and desired outcomes.
Overview of Common Gate Types
Common gate types include edge gates that are positioned on the edge of a part; fan gates that allow even distribution across wider surfaces; and tunnel gates that provide a hidden entry point into complex molds. Each type offers unique benefits: for example, while edge gates can be simpler to design, tunnel gate injection molding minimizes visible marks on finished products by hiding entry points within part geometries. Knowing What is the difference between fan gate and edge gate? can aid manufacturers in making informed decisions tailored to their specific needs.
The Engineering Behind Tunnel Gates
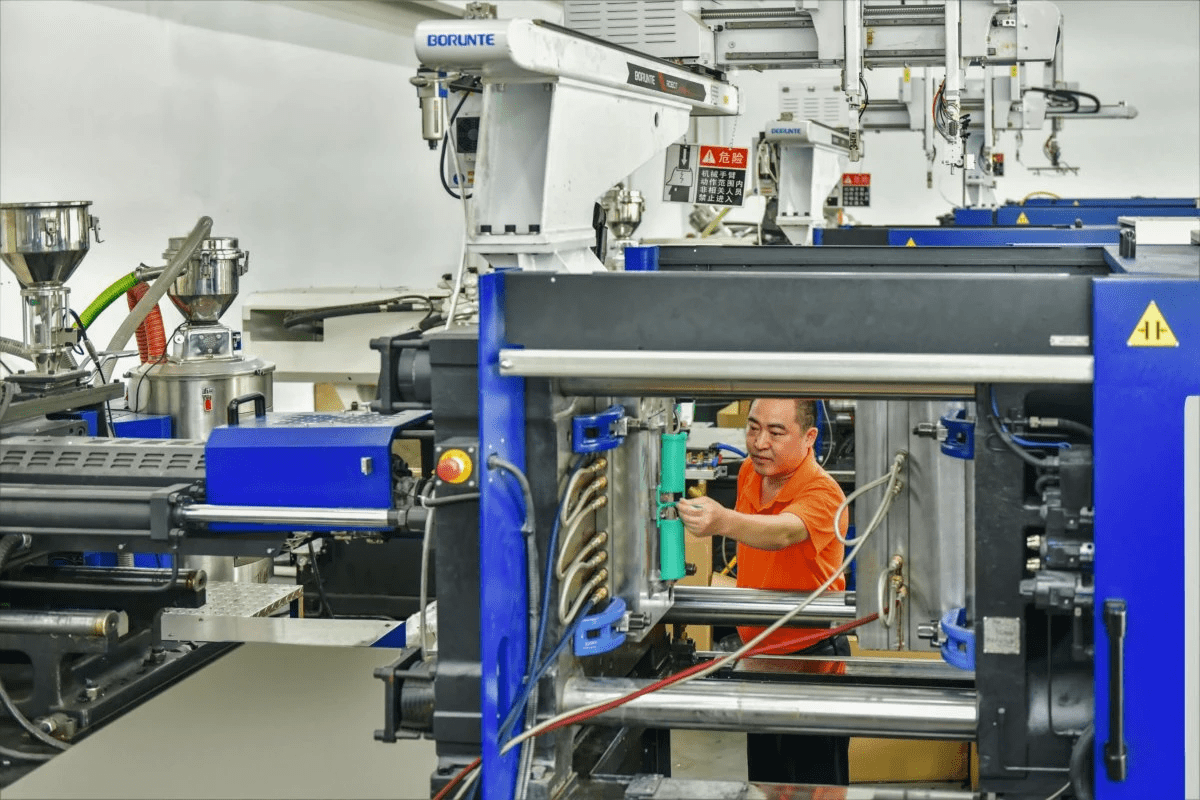
How Tunnel Gates Function in Mold Design
Tunnel gates play a vital role in the overall efficiency of plastic injection molding by ensuring that the material flows smoothly into the mold cavity. Unlike traditional gate types, such as fan or edge gates, tunnel gates create a streamlined path that facilitates better material distribution and reduces cycle times. This results in a more uniform product with fewer defects, making them an excellent choice for various applications.
What is the Angle of a Tunnel Gate?
The angle of a tunnel gate is not just a trivial detail; it significantly influences how effectively plastic fills the mold. Typically, tunnel gates are designed at angles ranging from 0 to 30 degrees, depending on specific application requirements and material properties. This angle helps control the flow rate and ensures that molten plastic reaches all areas of the cavity without causing premature cooling or solidification.
Design Considerations for Optimal Performance
When designing for tunnel gate injection molding, several factors must be taken into account to achieve optimal performance. First and foremost is ensuring proper alignment between the gate and mold cavity to prevent any misalignment issues during injection cycles. Additionally, considering aspects like cooling channels and venting can further enhance efficiency by reducing cycle times and improving part quality—key elements when comparing different types of gates for injection molding.
Comparing Tunnel Gates to Other Gate Types
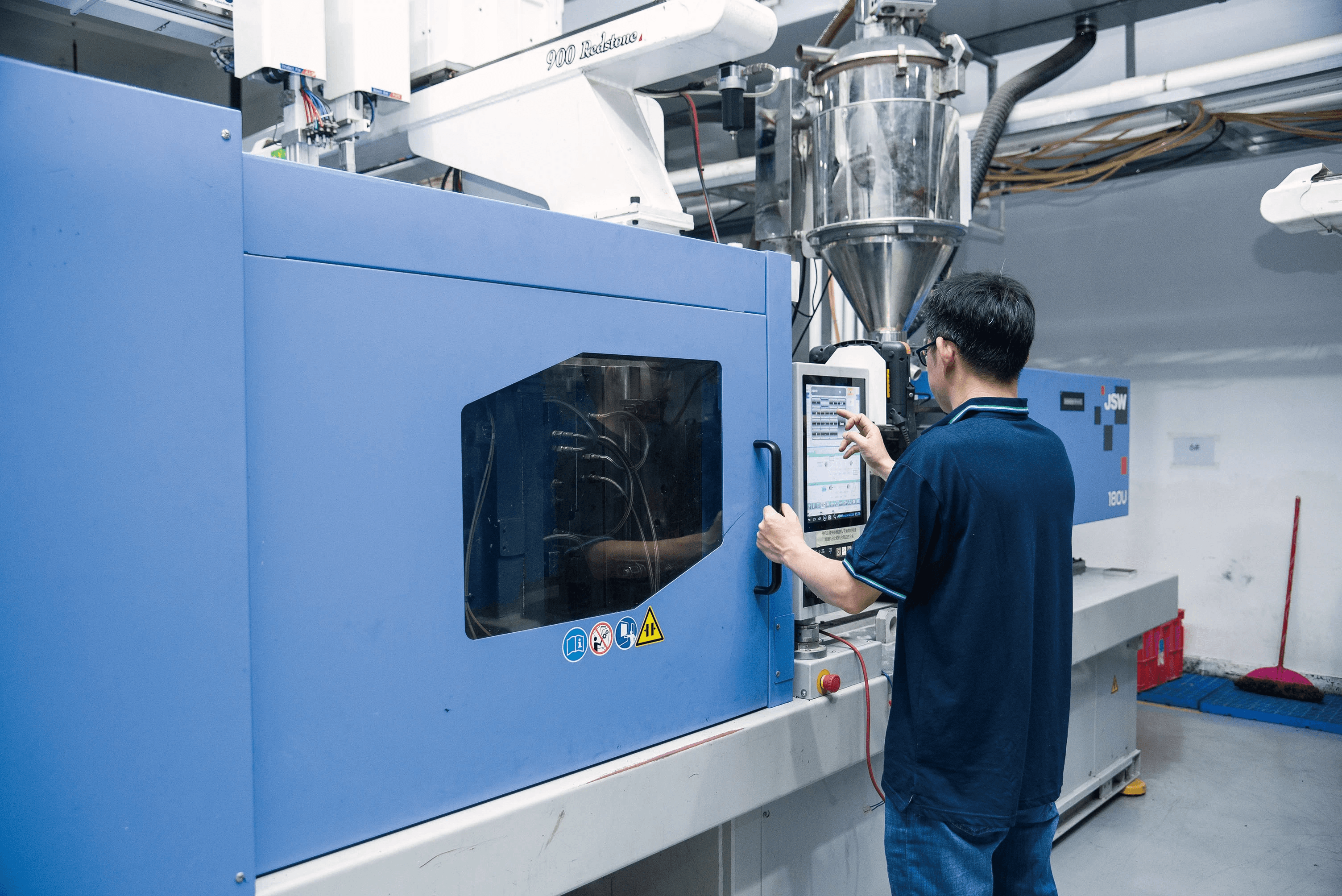
What is the Difference Between Fan Gate and Edge Gate?
So, what is a tunnel gate in injection molding compared to fan and edge gates? A fan gate typically has a wider opening that allows for more uniform filling of large parts, distributing material evenly across a larger surface area. On the other hand, an edge gate is positioned at the edge of the mold cavity and often results in a visible mark on the finished product, which may or may not be acceptable depending on your design requirements.
The angle of a tunnel gate plays a significant role in its functionality; it facilitates optimal flow while minimizing pressure loss during injection. In contrast, both fan gates and edge gates have their own angles but are designed for different purposes—fan gates focus on spreading material evenly while edge gates prioritize accessibility and ease of mold design. Understanding these distinctions helps clarify when to use each type effectively.
Pros and Cons of Each Gate Type
When considering tunnel gate injection molding versus fan or edge gates, it's important to weigh the pros and cons of each option. Tunnel gates offer minimal visible marks on finished products due to their concealed nature within the part's geometry; however, they may require more complex mold designs compared to simpler fan or edge configurations. Additionally, they excel at reducing weld lines—an essential factor in achieving high-quality finishes.
Fan gates provide excellent flow characteristics but can leave larger marks on parts due to their placement; this could be problematic if aesthetics are paramount for your project. Edge gates are straightforward to implement but can compromise part integrity by introducing stress concentrations at their entry point into the mold cavity. Each type has its strengths and weaknesses that should align with your project’s goals.
Selecting the Right Gate for Your Application
Choosing between tunnel gates, fan gates, or edge gates ultimately depends on various factors including part design, material properties, and production volume requirements in plastic injection molding projects. If aesthetics are critical and you want minimal post-processing work on visible surfaces, tunnel gate injection molding might be your best bet despite its complexity in design considerations such as what is the angle of a tunnel gate?
For larger parts where uniform filling is essential without much concern for surface marks—think about using fan gates instead; they can enhance production efficiency while still delivering quality results. Conversely, if you're looking for simplicity in mold design or working with smaller components where precision matters less than speed—edge gates could be your go-to solution.
Best Practices for Tunnel Gate Injection Molding

Design Tips from the Baoyuan Team
The Baoyuan team emphasizes that understanding what is a tunnel gate in injection molding is fundamental for effective design. When designing a tunnel gate, ensure that you consider the angle of a tunnel gate; an optimal angle can significantly influence flow characteristics and minimize defects. Additionally, incorporating proper cooling channels within the mold will enhance cycle times and improve part quality.
Another critical aspect is to analyze what is the gate in injection molding regarding size and placement—these factors can affect how well molten plastic fills the cavity. Using simulation software during the design phase allows engineers to visualize flow patterns, helping them tweak designs before physical production begins. Lastly, always keep future maintenance in mind; designing easily accessible gates will save time down the line.
Quality Assurance in Tunnel Gate Production
Quality assurance plays a pivotal role in ensuring that your tunnel gate injection molding process runs smoothly and efficiently. Implementing rigorous testing protocols helps identify any potential issues early on, reducing costly reworks later in production. Regular inspections during various stages of manufacturing ensure that everything adheres to specified tolerances.
It’s also crucial to monitor temperature control closely throughout the process; maintaining consistent temperatures ensures even flow of materials through different types of gates for injection molding like tunnel gates. Furthermore, investing in high-quality materials not only enhances durability but also boosts productivity by minimizing downtime due to material failures or defects. A well-structured quality assurance program guarantees that every piece produced meets industry standards.
Common Mistakes to Avoid
Navigating through tunnel gate injection molding can be tricky if you're not aware of common mistakes that could derail your project’s success. One frequent error involves miscalculating what is the difference between fan gate and edge gate when selecting a suitable option; understanding these differences can prevent issues related to material flow and part quality later on.
Another mistake often made is neglecting proper venting within molds; inadequate venting can lead to air traps which compromise product integrity during cooling cycles—nobody wants faulty parts! Lastly, overlooking post-production processes such as trimming or finishing might seem minor but can significantly impact overall aesthetics and functionality; always plan ahead for these steps.
Conclusion
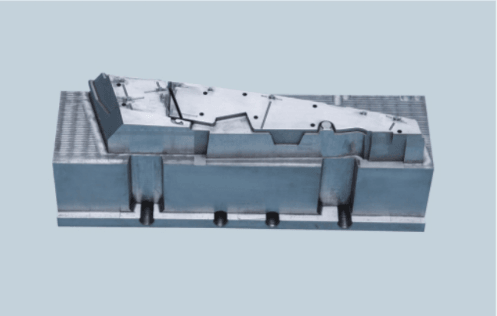
In the ever-evolving world of plastic injection molding, understanding the nuances of tunnel gate injection molding can significantly impact your project's success. From their unique design characteristics to their specific applications, tunnel gates offer a range of benefits that can enhance production efficiency and product quality. As we wrap up our discussion, let's highlight some key takeaways about these innovative gates.
Key Takeaways on Tunnel Gates
Tunnel gates are an essential type of gate in injection molding, providing a streamlined approach to material flow and reducing potential defects. Understanding what is a tunnel gate in injection molding means recognizing its ability to minimize stress on the molded part while ensuring even filling during the process. Additionally, knowing what is the angle of a tunnel gate can help engineers optimize mold designs for better performance and reduced cycle times.
Future Trends in Injection Molding Technology
The landscape of plastic injection molding continues to evolve with advancements in materials and technology. Future trends point toward increased automation and smart manufacturing processes that could further enhance the efficiency of tunnel gate injection molding systems. As manufacturers explore these innovations, they will likely refine their understanding of various types of gates for injection molding, leading to even more specialized applications tailored to modern needs.
Choosing the Right Gates for Your Projects
When it comes to selecting the right gates for your projects, it's crucial to weigh options like fan gates versus edge gates carefully. Understanding what is the difference between fan gate and edge gate can guide you in making informed decisions based on your specific application requirements. Ultimately, choosing between tunnel gate injection molding and other types will depend on factors such as part complexity, material properties, and desired finish quality.