Introduction
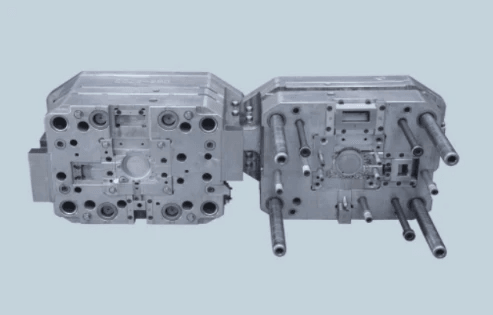
In the world of manufacturing, valve gate injection molding stands out as a sophisticated technique that enhances the quality and efficiency of plastic products. This method allows for precise control over material flow, making it a preferred choice for many manufacturers. Understanding what a valve gate in injection molding is and how it functions is crucial for anyone involved in the production process.
Understanding Valve Gate Injection Molding
Valve gate injection molding utilizes a unique mechanism that opens and closes gates to control the flow of molten plastic into molds. This precision not only reduces waste but also improves the overall finish of the final product. By mastering this concept, manufacturers can achieve better dimensional accuracy and surface quality compared to traditional methods.
Importance of Choosing the Right Gate Type
Selecting the appropriate gate type can significantly impact production efficiency, cost-effectiveness, and product quality. With various options available—including open gates, valve gates, side gates, tunnel gate injection molding, and submarine gate injection molding—understanding their differences is essential for optimizing manufacturing processes. The right choice can lead to enhanced performance while minimizing defects.
Key Concepts of Injection Molding
Injection molding involves injecting molten material into a mold cavity where it cools and solidifies into a specific shape. Key concepts include material selection, mold design, cycle time optimization, and cooling strategies—all critical factors in achieving high-quality outputs. Familiarity with these concepts lays the groundwork for understanding more specialized techniques like valve gate injection molding.
What is a Valve Gate in Injection Molding?
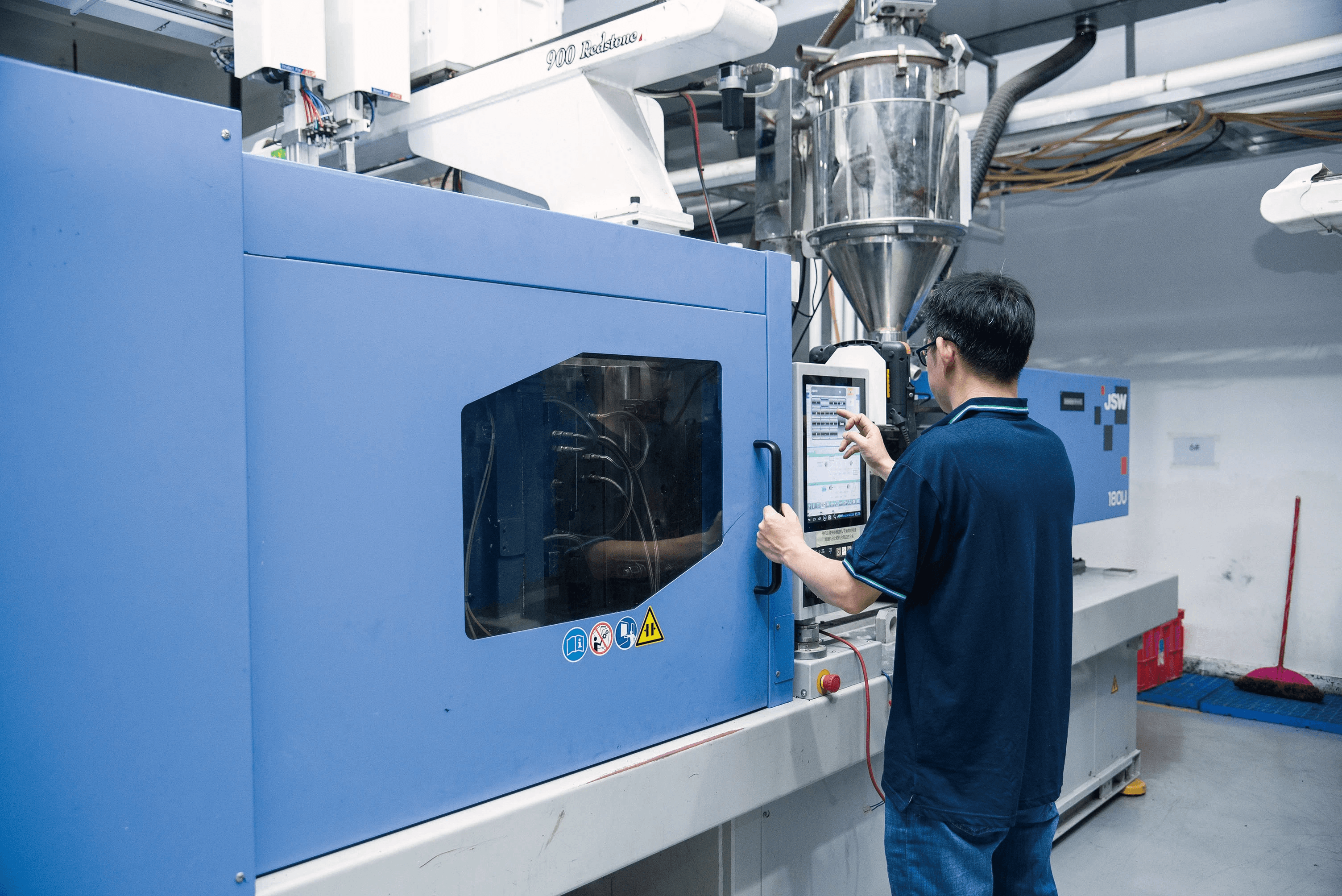
Valve gate injection molding is a specialized technique that enhances the efficiency and precision of the injection molding process. This method utilizes a valve mechanism to control the flow of molten plastic into the mold cavity, providing manufacturers with greater flexibility over their production. By using valve gates, companies can improve part quality and reduce waste, making it an attractive option for many applications.
Definition and Functionality
A valve gate in injection molding refers to a gating system that employs a mechanical or pneumatic valve to regulate material flow during the injection process. This gate opens and closes at specific times to ensure that the molten plastic fills the mold cavity precisely when needed, allowing for better control over fill patterns and pressures. The functionality of a valve gate allows for enhanced surface finish and reduced risk of defects like sink marks or warping.
Advantages of Valve Gate Injection Molding
One significant advantage of valve gate injection molding is its ability to minimize wastage by controlling when material enters the mold cavity. This precise control leads to improved cycle times and reduces scrap rates, making it more cost-effective in high-volume production scenarios. Additionally, this method allows for better part consistency, which is crucial for industries requiring tight tolerances and aesthetic finishes.
Applications in Various Industries
Valve gate injection molding finds applications across several industries due to its versatility and precision capabilities. In automotive manufacturing, it’s used for producing complex components with intricate designs where quality cannot be compromised. Similarly, electronics manufacturers leverage this technology for creating housings that require high-quality surface finishes while minimizing defects—making it indispensable across sectors from consumer goods to medical devices.
What is the Difference Between Open Gate and Valve Gate?
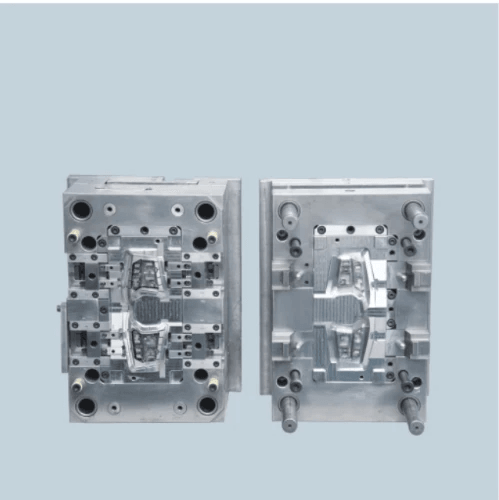
When diving into the world of injection molding, one might wonder about the differences between open gates and valve gates. While both serve to introduce molten plastic into a mold cavity, their mechanisms and outcomes are quite distinct. Understanding these differences is crucial for manufacturers aiming to optimize their production processes.
Fundamental Differences Explained
Open gates operate with a straightforward design where the gate remains open during injection, allowing material to flow freely into the mold. In contrast, valve gate injection molding employs a mechanism that can close or open based on specific requirements during the injection cycle. This fundamental difference impacts not only how materials enter the mold but also influences factors like cycle time and part quality.
The main takeaway here is that while an open gate provides simplicity and ease of use, it may lead to issues like excessive flash or uneven fill in complex geometries. On the other hand, valve gates offer precision control over material flow, which can significantly enhance part aesthetics and functionality. For manufacturers considering what is a valve gate in injection molding?, understanding these operational nuances is key to making informed choices.
Advantages and Disadvantages of Each Type
Both open gates and valve gates come with their own sets of advantages and disadvantages that manufacturers must weigh carefully. Open gates are generally easier to set up and maintain, making them ideal for high-volume runs where speed is essential. However, they can lead to higher scrap rates due to imperfections such as surface marks or excess material at the gate area.
Valve gate injection molding shines in applications requiring high-quality finishes or intricate designs since it minimizes defects associated with traditional gating systems. The downside? They often come with increased complexity in terms of tooling and higher initial costs due to additional components needed for operation. Thus, when deciding between these two types of gating systems, it’s essential for manufacturers to consider both production goals and budget constraints.
Decision Factors for Manufacturers
When evaluating what is the difference between open gate and valve gate options, several decision factors come into play for manufacturers looking to optimize their processes effectively. First on the list is product design; complex parts may benefit from valve gates due to enhanced control over material flow during filling cycles. Conversely, simpler designs might be better suited for open gates which provide quicker turnaround times.
Cost considerations also play a significant role; while valve gate systems can improve product quality significantly, they require more investment upfront compared to traditional open gating methods. Additionally, production volume should influence decisions—if you’re running low volumes but need high precision, investing in valve gate technology could be worthwhile despite its complexity.
Ultimately, understanding what are the different types of gates for injection molding—including tunnel gate injection molding or submarine gate injection molding—will equip manufacturers with knowledge that aids in selecting an appropriate system tailored specifically for their needs.
What is a Side Gate in Injection Molding?
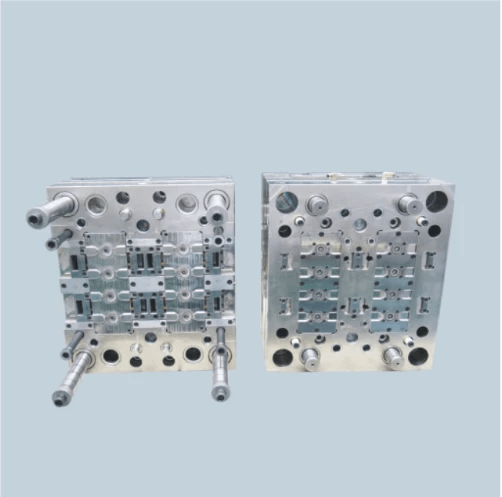
When diving into the world of injection molding, one often encounters various gate types, each with its unique characteristics and advantages. Among these, the side gate stands out as a popular choice for many manufacturers. Understanding what a side gate in injection molding is can help businesses optimize their production processes.
Overview of Side Gate Mechanisms
A side gate in injection molding refers to an entry point located on the side of the mold cavity rather than at the end or top. This mechanism allows molten plastic to flow into the mold from a lateral position, which can be advantageous for certain designs and geometries. The placement of the side gate can significantly influence how material fills the cavity, impacting both cycle times and part quality.
Use Cases and Benefits
Side gates are particularly beneficial when dealing with complex shapes or when minimizing visible marks on finished products is crucial. Industries such as automotive, consumer electronics, and medical devices frequently utilize side gates due to their ability to enhance aesthetic appeal while maintaining structural integrity. Additionally, using a side gate can reduce material waste and improve overall efficiency during production.
Comparison with Other Gate Types
When comparing side gates to other types like valve gates or open gates, several key differences emerge that manufacturers should consider. For instance, while valve gate injection molding offers precise control over flow rates and minimizes flash issues, open gates may allow for quicker cycle times but often come with trade-offs regarding quality consistency. Each type has its pros and cons; thus understanding what is the difference between open gate and valve gate becomes essential for making informed decisions about which method best suits specific project requirements.
What are the Different Types of Gates for Injection Molding?
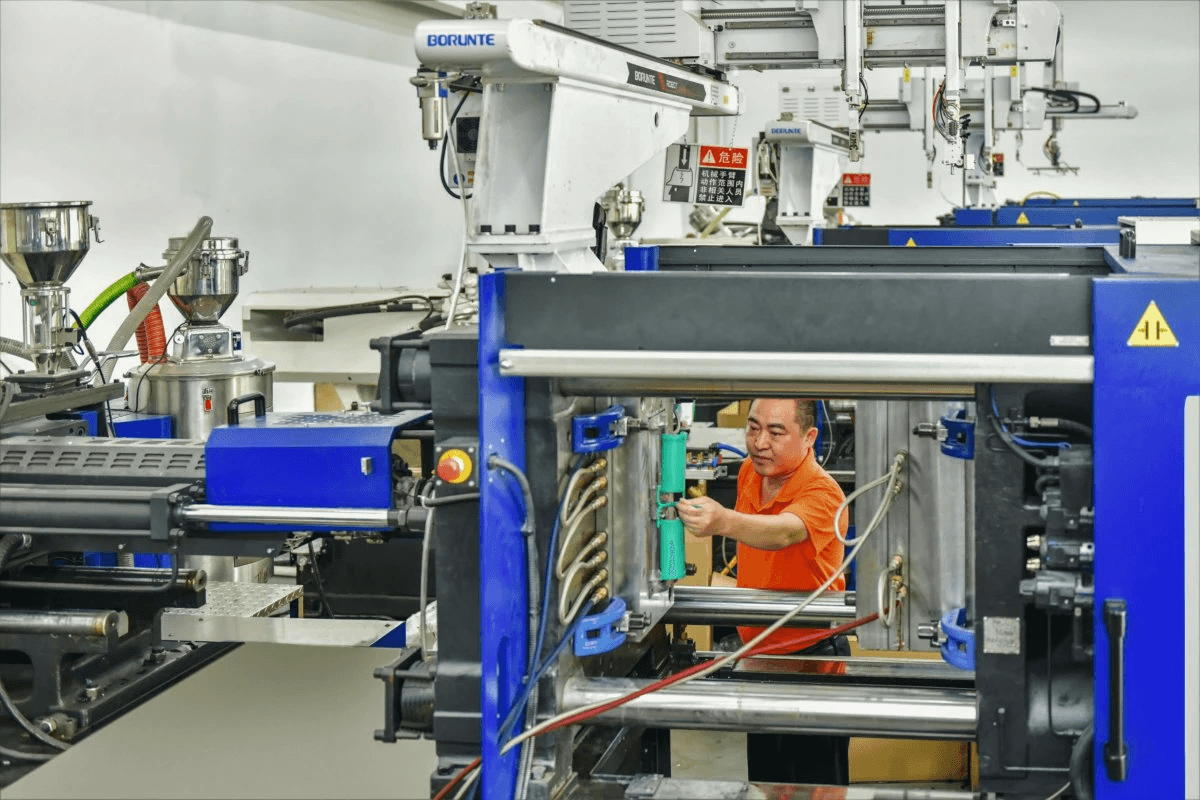
In the world of injection molding, selecting the right gate type is crucial for achieving optimal results. Various gate types serve distinct functions and come with their own sets of advantages and disadvantages. Understanding these different types can significantly impact production efficiency, product quality, and overall costs.
Overview of Common Gate Types
When discussing what are the different types of gates for injection molding, several common options emerge: open gates, valve gates, side gates, tunnel gates, and submarine gates. Each type has unique characteristics that make it suitable for specific applications or materials. Among these, valve gate injection molding stands out due to its ability to control flow precisely and minimize defects.
Open gates are straightforward but may lead to visible marks on finished products; hence they’re often used where aesthetics aren’t a priority. Valve gate injection molding provides an alternative by allowing manufacturers to shut off flow at precise moments during the process. Side gates offer another option but may not provide the same level of control as valve or tunnel gates.
Tunnel Gate Injection Molding Explained
Tunnel gate injection molding is a popular choice when designers want to hide gate marks on visible surfaces of molded parts. This method involves creating a small tunnel through which molten plastic flows into the mold cavity before being sealed off once filling is complete. The design minimizes cosmetic defects while maintaining structural integrity.
One significant advantage of tunnel gates is their ability to reduce stress concentrations in parts that require uniform strength distribution. They also allow for greater flexibility in design since manufacturers can position them strategically away from critical areas. However, they may require more complex mold designs than simpler options like open or side gates.
Submarine Gate Injection Molding Details
Submarine gate injection molding takes a different approach by placing the gate below the parting line of the mold, making it nearly invisible on finished products. This method allows for excellent aesthetic results while still providing reliable filling capabilities during production runs. Submarine gates are particularly beneficial for large parts where appearance matters but mechanical properties cannot be compromised.
The primary benefit here lies in their ability to eliminate surface blemishes that can occur with other types like open or side gates—making them ideal for consumer goods or automotive components where visual appeal is essential. On top of that, submarine gates can enhance material flow dynamics within complex molds by allowing more controlled filling patterns compared to traditional methods.
In summary, understanding what are the different types of gates for injection molding—including valve gate injection molding—can help manufacturers make informed decisions based on their specific needs and applications. Each option presents unique benefits that cater to various industry demands while ensuring high-quality outputs.
Practical Considerations for Choosing Valve Gates
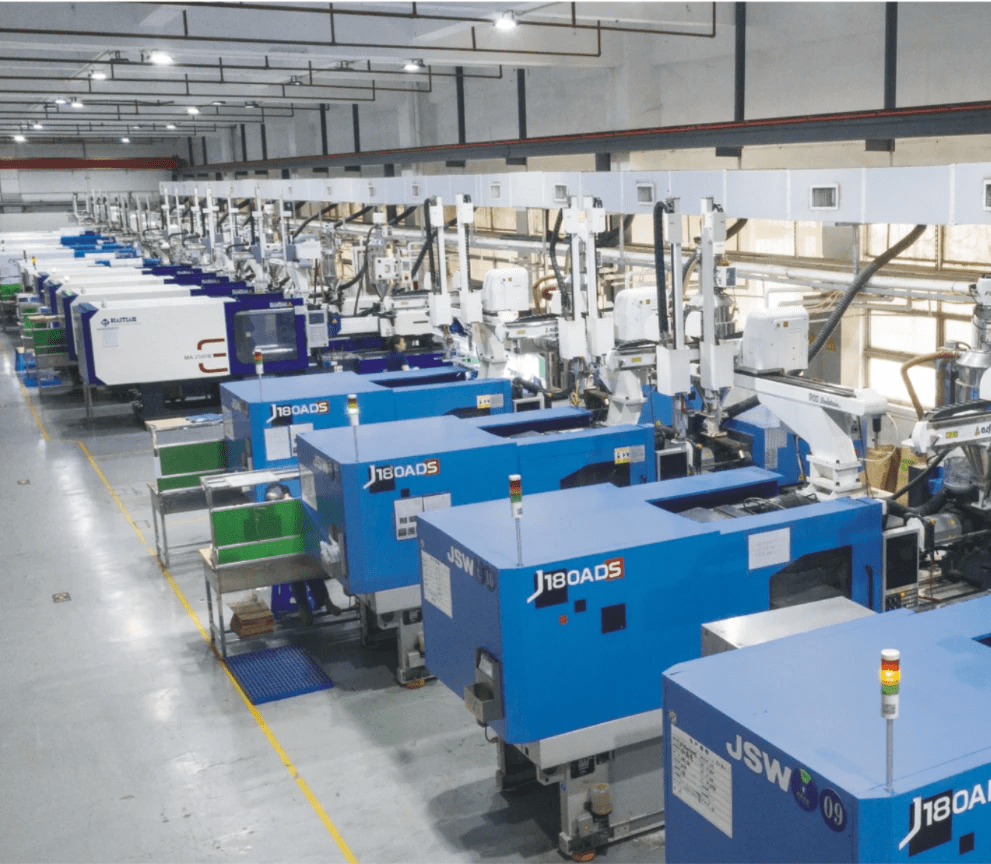
When it comes to valve gate injection molding, making the right choice of gate type can significantly affect the quality and efficiency of your production process. Manufacturers must consider various factors that influence gate selection, ensuring that they choose a design that aligns with their specific needs. Understanding the nuances of different gate types, including what is a valve gate in injection molding, can help streamline this decision-making process.
Factors Influencing Gate Selection
Several factors come into play when determining which gate type to utilize in an injection molding project. The complexity of the part geometry, material characteristics, and desired surface finish are crucial considerations. For instance, if you're dealing with intricate designs or high-precision applications, opting for valve gate injection molding might be more beneficial compared to open gates.
Additionally, cycle time and production volume are significant elements influencing your choice. Valve gates often provide better control over melt flow and cooling times, which can lead to improved cycle efficiency—an essential factor for large-scale production runs. Ultimately, understanding what is the difference between open gate and valve gate will aid manufacturers in making informed decisions tailored to their operational requirements.
Tips from the Baoyuan Team
The Baoyuan team has compiled some practical tips for manufacturers navigating the world of valve gates in injection molding. First off, always conduct thorough testing before finalizing your choice; this will help you assess performance under real-world conditions and ensure compatibility with your existing machinery. Additionally, consider collaborating with experienced mold designers who can provide insights into optimizing designs for specific applications.
Another critical tip is to keep an eye on maintenance requirements associated with different types of gates. For example, while side gates may offer certain advantages in accessibility during maintenance tasks compared to tunnel or submarine gates, they might also introduce unique challenges related to parting line visibility and potential flash issues. Balancing these considerations will ultimately lead you toward a more efficient production process.
Cost Implications and Efficiency
Cost implications play a vital role when selecting different types of gates for injection molding projects such as tunnel gate injection molding or submarine gate injection molding processes. While valve gates may have higher initial costs due to their complexity and precision components, they often result in savings over time through reduced scrap rates and improved cycle times. Therefore, manufacturers should evaluate both short-term expenditures and long-term operational efficiencies.
Moreover, it’s essential to analyze how each type of gating system impacts overall productivity levels within your facility. A well-chosen valve gate system can enhance throughput by minimizing downtime related to mold changes or maintenance issues—this translates directly into better profitability over time! By weighing these cost implications against expected performance outcomes from each gating option available on the market today—manufacturers can make decisions that truly benefit their bottom line.
Conclusion
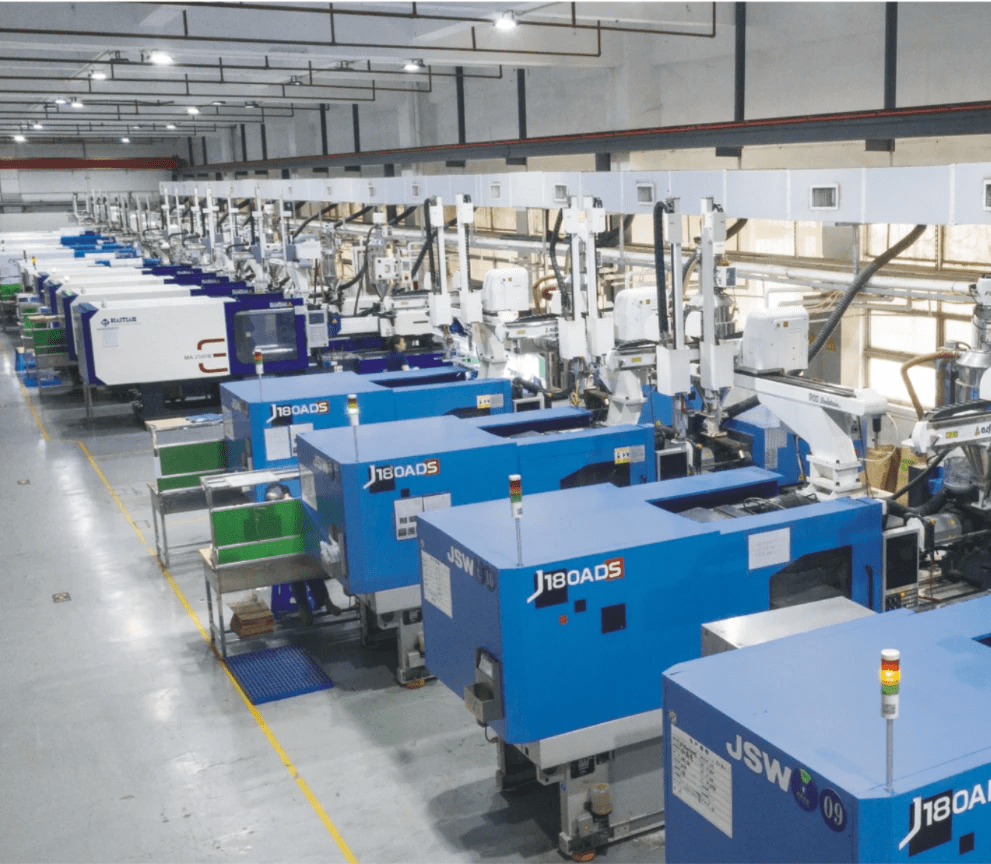
In conclusion, valve gate injection molding stands out as a highly efficient and versatile method in the realm of plastic manufacturing. By understanding what is a valve gate in injection molding, manufacturers can appreciate the precision it offers, particularly in minimizing defects and enhancing surface quality. The benefits of this technology extend beyond mere aesthetics; they play a crucial role in optimizing production processes across various industries.
Summary of Valve Gate Injection Molding Benefits
Valve gate injection molding provides significant advantages that make it a preferred choice for many applications. Not only does it allow for greater control over the flow of material, but it also reduces waste by ensuring that only the necessary amount is injected into the mold. Furthermore, this method minimizes issues like sink marks and short shots, ultimately leading to higher-quality finished products.
Final Thoughts on Gate Types
While exploring what is the difference between open gate and valve gate reveals distinct characteristics that cater to different manufacturing needs, it's essential to understand that no single solution fits all scenarios. Each type of gate—be it valve gates, side gates, tunnel gates injection molding, or submarine gate injection molding—has its unique set of benefits and drawbacks. Manufacturers must carefully weigh these factors based on their specific requirements to select the most effective gating system.
Future Trends in Injection Molding Technology
The landscape of injection molding technology continues to evolve with advancements such as smart manufacturing and automation integration. Future trends may see enhanced capabilities for valve gate injection molding systems that incorporate real-time monitoring and AI-driven optimization techniques. As these innovations unfold, they promise not only to improve efficiency but also to redefine how manufacturers approach what are the different types of gates for injection molding.