Introduction
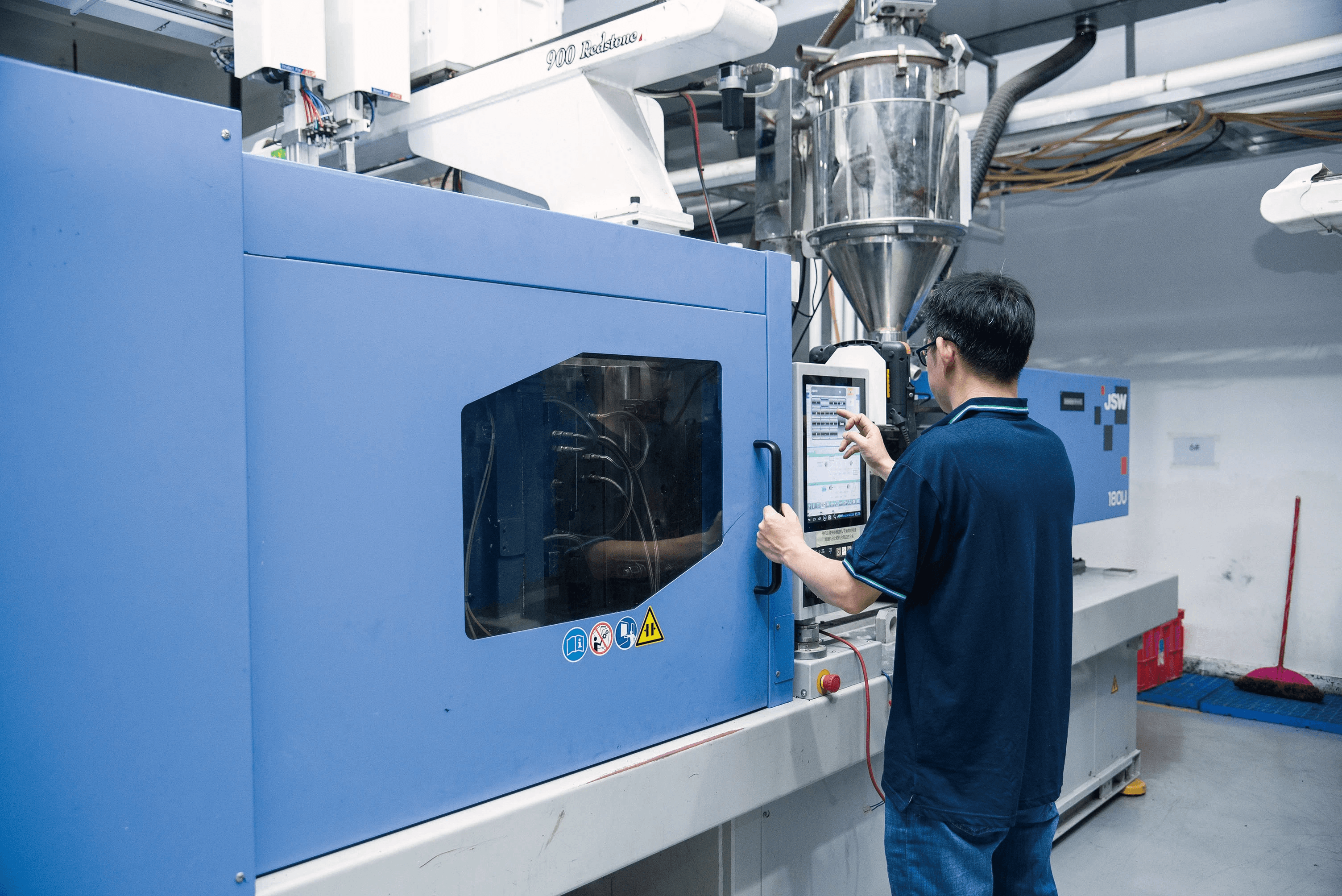
Injection moulding is a widely used manufacturing process that transforms raw materials into finished products through the use of heat and pressure. However, understanding injection moulding cost can be a complex endeavor, as it encompasses various factors that influence pricing and overall project viability. From material selection to production volume, each element plays a crucial role in determining how much does injection molding cost?
Understanding Injection Moulding Cost Factors
When diving into the intricacies of injection moulding costs, it's essential to recognize the myriad factors at play. The choice of materials significantly impacts pricing; for instance, high-performance polymers can drive up costs compared to standard plastics. Additionally, the design complexity of the mold itself can add layers of expense that must be accounted for when assessing how to calculate injection mold cost.
Exploring Cost Variations in Injection Moulding
Cost variations in injection moulding can stem from several sources, including geographical location and manufacturing capabilities. Different regions may have varying labor rates and operational expenses that contribute to discrepancies in how much does injection molding cost? Furthermore, production volume is another critical factor; larger runs often lead to lower per-unit costs due to economies of scale but require higher upfront investments.
The Importance of Accurate Cost Estimation
Accurate cost estimation is vital for businesses looking to harness the benefits of injection moulding while managing budgets effectively. Without a clear understanding of all associated costs—including labor, materials, and overhead—companies risk overspending or underestimating their project budgets. As such, addressing questions like why is injection moulding expensive becomes paramount for informed decision-making and successful project execution.
What Influences Injection Moulding Cost
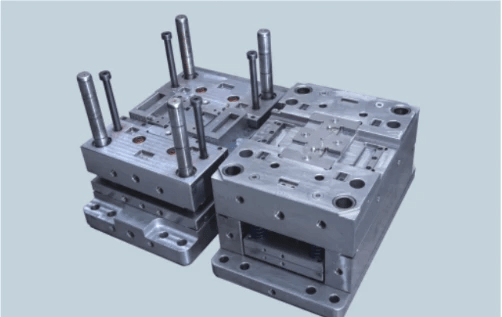
Material Selection Impacts on Pricing
One of the most significant factors affecting injection moulding cost is material selection. Different materials come with varying price tags; for instance, high-performance thermoplastics may be more expensive than standard plastics due to their enhanced properties and durability. When calculating how to calculate injection mold cost, it’s essential to consider not just the initial material expense but also how these choices impact overall production efficiency and product lifespan.
The choice of material doesn’t just influence costs; it also affects other aspects like machine settings and cycle times. For example, some materials may require specialized equipment or adjustments that could lead to increased operational costs per hour. Understanding how different materials contribute to overall expenses can help manufacturers make informed decisions that balance quality with budget constraints.
The Role of Design Complexity
Design complexity is another major player in determining why is injection moulding expensive? Intricate designs often necessitate advanced tooling and longer production times, which directly inflate costs. If a product has numerous features or tight tolerances, it may require custom molds that are not only pricier but also take longer to produce.
Moreover, complicated designs can lead to higher rates during the manufacturing process itself; after all, more complex molds mean more meticulous handling during production. This ties back into our earlier question: how much does injection molding cost? The answer often lies within those intricate design specifications that demand more resources and labor.
Production Volume and Its Effects
Production volume has a massive impact on injection moulding costs as well—larger volumes typically reduce the per-unit cost due to economies of scale. When companies ramp up production runs, they spread out fixed costs over a greater number of parts, thereby lowering individual item prices significantly. However, it's crucial for businesses to carefully evaluate their projected volumes because underestimating demand can lead to increased per-unit costs if additional runs are required later on.
Conversely, low-volume runs might result in higher per-unit prices since setup and tooling expenses remain constant regardless of output quantity. This scenario raises another critical question: how much does injection molding cost per hour? In many cases, lower production volumes lead directly to elevated hourly rates due to less efficient use of machinery and labor.
Understanding these three key influences—material selection, design complexity, and production volume—can provide valuable insight into managing injection moulding costs effectively while ensuring quality outcomes for products.
How to Calculate Injection Mold Cost

Calculating injection mold cost is an essential step in the overall process of injection moulding. Understanding how much does injection molding cost involves breaking down various components, including design expenses, labor, and overhead costs. By doing so, manufacturers can better manage their budgets and ultimately improve their profit margins.
Breakdown of Mold Design Expenses
When considering how to calculate injection mold cost, one must first look at the mold design expenses. These costs can vary significantly based on the complexity of the part being produced; intricate designs often require more time and advanced technology to execute. Additionally, factors such as material choice for the mold itself (e.g., steel vs. aluminum) will also impact these initial expenses.
Mold design expenses include not only the physical materials but also any software or tools used in the design process. For example, utilizing advanced CAD software can enhance precision but may come with a hefty price tag that contributes to overall injection moulding cost. Therefore, understanding these components helps clarify why some projects are pricier than others when asking how much does injection molding cost?
Labor Costs in Injection Moulding
Labor costs play a pivotal role in determining how to calculate injection mold cost accurately. Skilled technicians are essential for both operating machinery and ensuring that production runs smoothly without defects; their expertise comes at a premium price. Moreover, the training required for staff to operate complex equipment adds another layer of expense that needs consideration.
Additionally, labor costs fluctuate based on production volume; higher volumes often lead to lower per-unit labor costs due to economies of scale. However, if a project requires specialized skills or overtime work due to tight deadlines or unexpected issues, this can drive up overall costs significantly—leading one to ponder why is injection moulding expensive? Ultimately, understanding these labor dynamics is crucial for anyone looking into how much does injection molding cost.
Overhead and Operational Costs
Overhead and operational costs are often overlooked when discussing how much does injection molding cost? However, they represent significant ongoing expenses that manufacturers must account for in their budgets. This category includes utilities like electricity and water needed for machinery operation as well as facility maintenance costs.
Furthermore, operational efficiency plays a vital role in managing these overheads; companies that invest in automation may reduce long-term operational costs despite higher initial investments—thus impacting overall injection moulding cost positively over time. In essence, comprehending these factors allows businesses not only to answer questions about how to calculate injection mold cost but also helps them strategize better financial planning moving forward.
How Much Does Injection Molding Cost Per Hour
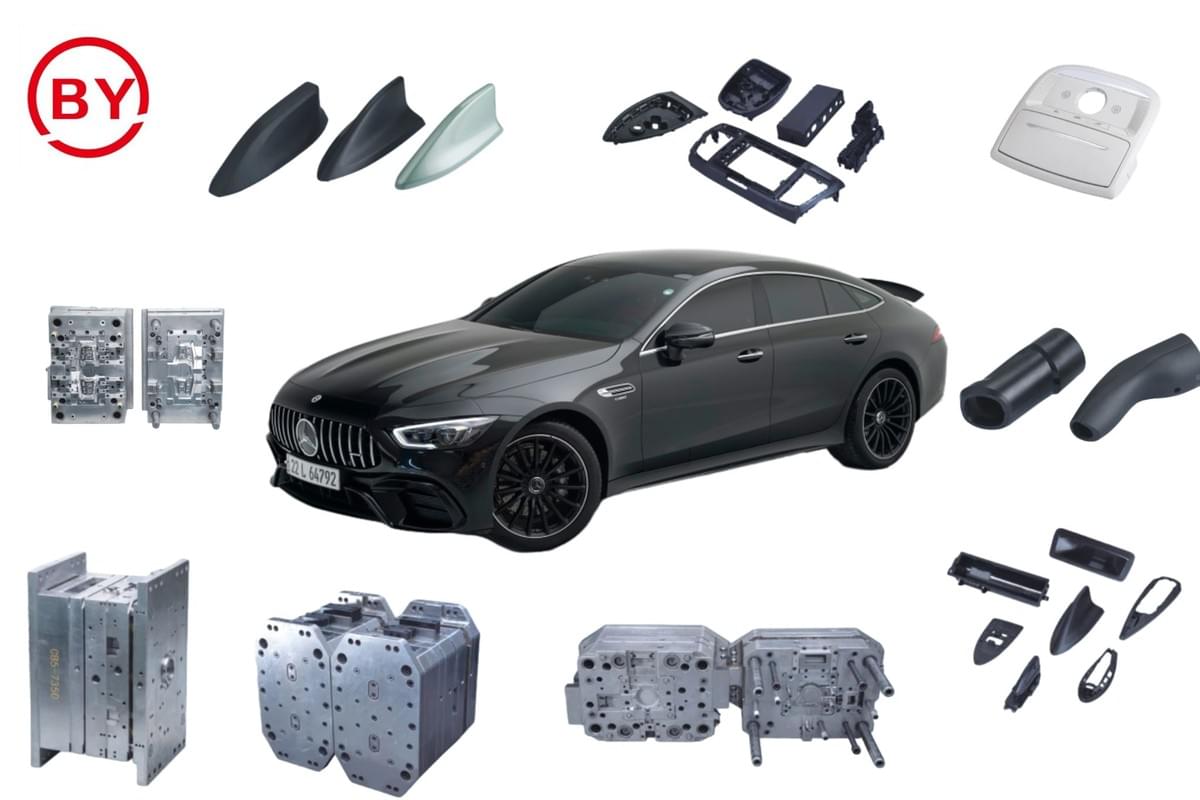
When considering the question, How much does injection molding cost per hour? it's essential to understand that several factors come into play. The hourly rates for injection molding can vary significantly based on machinery, labor, and operational costs. By dissecting these components, manufacturers can better estimate their overall injection moulding cost.
Factors Affecting Hourly Rates
Several key factors influence hourly rates in the injection molding industry. First and foremost is the type of machinery used; advanced machines equipped with automation may command higher rates due to increased efficiency and capabilities. Additionally, labor costs fluctuate based on skill levels required for operating complex machinery and maintaining quality standards—another reason why some might wonder why injection moulding is expensive.
Another factor affecting hourly rates is the complexity of the mold design itself. More intricate designs often require specialized skills or additional setup time, which can drive up costs per hour. Finally, regional variations in wages and operational overhead also play a significant role in determining how much does injection molding cost per hour.
Comparing Different Machinery Costs
When evaluating how to calculate injection mold cost accurately, comparing different machinery options becomes crucial. High-end machines may have a steep initial investment but provide superior efficiency and lower long-term operational costs. Conversely, older or less advanced equipment may be cheaper upfront but could lead to higher maintenance expenses and longer cycle times—ultimately affecting your overall injection moulding cost.
It's also vital to consider energy consumption when comparing machinery costs since more efficient machines will reduce operational expenses over time. For example, electric machines are often touted for their energy savings compared to hydraulic options. By weighing these factors carefully, businesses can make informed decisions about which equipment best aligns with their production needs while keeping an eye on overall expenses.
Case Studies from Leading Companies
To grasp how much does injection molding cost per hour in real-world scenarios, let's look at some case studies from leading companies in various industries. One automotive manufacturer reported an average hourly rate of $150 when utilizing state-of-the-art machinery paired with skilled technicians—reinforcing why many ask why injection moulding is expensive in high-stakes industries like automotive production.
In contrast, a consumer product company using older technology found its hourly rate hovered around $80 but struggled with inefficiencies that ate away at profit margins over time. These examples illustrate that while upfront costs may differ significantly between companies, the long-term return on investment often hinges on choosing the right machinery and workforce skillset—key elements influencing overall injection moulding cost.
Why Is Injection Moulding Expensive
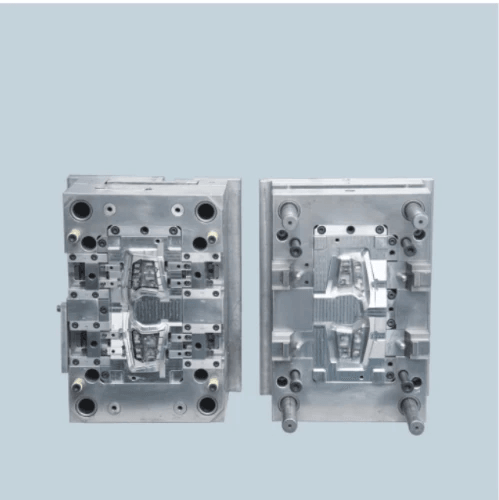
When diving into the world of injection moulding, one question often arises: Why is injection moulding expensive? The cost associated with this manufacturing process stems from various factors, including technology investments, rigorous quality assurance protocols, and the specialized skills required by teams like Baoyuan's. Understanding these elements can provide clarity on how to calculate injection mold cost effectively and why it may seem steep at first glance.
Investment in Technology and Equipment
The backbone of any successful injection moulding operation is its technology and equipment. High-quality machines designed for precision can come with hefty price tags, significantly impacting overall injection moulding costs. Additionally, ongoing maintenance and upgrades are necessary to keep these machines running efficiently, further contributing to how much does injection molding cost?
Investing in advanced technology not only ensures better product quality but also enhances production speed and efficiency. This means that while the initial investment may be high, it can lead to lower long-term costs per unit when production volumes increase. Therefore, understanding the role of technology helps clarify why is injection moulding expensive.
Quality Assurance and Testing Needs
Quality assurance is a non-negotiable aspect of the injection moulding process that adds to its overall expense. Each product must undergo rigorous testing to ensure it meets industry standards and customer expectations; this includes both pre-production samples and post-production inspections. The costs associated with quality checks can quickly add up when evaluating how much does injection molding cost.
Furthermore, implementing robust quality assurance measures requires specialized tools and technologies that contribute to operational expenses. These investments are essential for maintaining a high level of product consistency while reducing waste caused by defects or recalls—ultimately saving money in the long run. Hence, understanding quality assurance needs provides insight into why is injection moulding expensive.
The Skillset of the Baoyuan Team
A significant factor influencing the overall cost of injection moulding lies in the skillset of professionals involved in the process—like those on Baoyuan’s team. Skilled technicians who understand intricate design specifications can optimize production processes and troubleshoot issues promptly, which directly impacts labor costs associated with how to calculate injection mold cost accurately.
Moreover, having a team well-versed in advanced techniques not only enhances productivity but also leads to innovative solutions that improve efficiency over time—a crucial aspect when considering how much does injection molding cost per hour? Investing in talent ensures that projects run smoothly from start to finish while minimizing costly errors or delays. Consequently, this expertise contributes significantly to why is injection moulding expensive.
Real-World Examples of Injection Moulding Costs
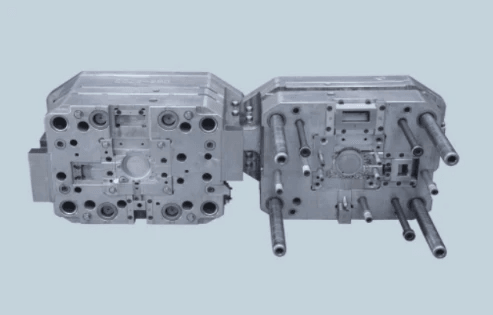
Understanding real-world examples of injection moulding costs can provide valuable insights into how various factors influence pricing in different industries. From the automotive sector to consumer products, the costs can vary significantly based on materials, design complexity, and production volume. By examining these examples, companies can better grasp how to calculate injection mold cost and manage their budgets effectively.
Case Study: Automotive Industry Costs
The automotive industry is notorious for its intricate components and high standards, leading many to wonder: how much does injection molding cost in this field? Typically, the initial investment in molds can be substantial due to the need for precision and durability. For instance, a single mold for an automotive part might range from $10,000 to $100,000 or more depending on complexity, which directly contributes to why is injection moulding expensive in this sector.
Additionally, production volumes play a crucial role; higher quantities often lead to lower per-unit costs as fixed expenses are distributed over more items. However, if a manufacturer only needs a small batch of parts, they might find themselves facing higher costs per unit due to the initial mold investment. Ultimately, understanding these dynamics helps businesses navigate their own injection moulding cost calculations effectively.
Comparing Consumer Products Pricing
When it comes to consumer products—think toys or kitchen gadgets—the question how much does injection molding cost? takes on new dimensions. Unlike automotive parts that require rigorous testing and compliance with safety standards, consumer products may have slightly lower barriers regarding design complexity and material selection. However, even here the prices can vary widely based on factors like aesthetics and functionality.
For example, producing a simple plastic toy could cost anywhere from $1 to $5 per unit when produced at scale; however, add intricate designs or special materials into the mix and those costs could skyrocket. This variance highlights that understanding how to calculate injection mold cost accurately is essential for product developers aiming for profitability without sacrificing quality. Knowing what drives these prices helps brands plan their budgets efficiently.
Insights from Baoyuan’s Projects
Baoyuan's extensive portfolio offers a treasure trove of insights regarding injection moulding costs across various projects. By analyzing our work with different industries—from electronics to healthcare—we see firsthand how diverse factors contribute to overall pricing strategies. For instance, some clients inquire about “how much does injection molding cost per hour?” as they seek clarity on operational efficiency relative to project timelines.
In many cases at Baoyuan, we’ve found that upfront investments in technology yield long-term savings by streamlining production processes—underscoring why is injection moulding expensive initially but beneficial over time. Moreover, our commitment to quality assurance adds another layer of expense but ultimately enhances product reliability—a critical factor for clients concerned about market competitiveness and customer satisfaction. These insights serve as guiding principles for any business looking at their own injection moulding journey.
Conclusion
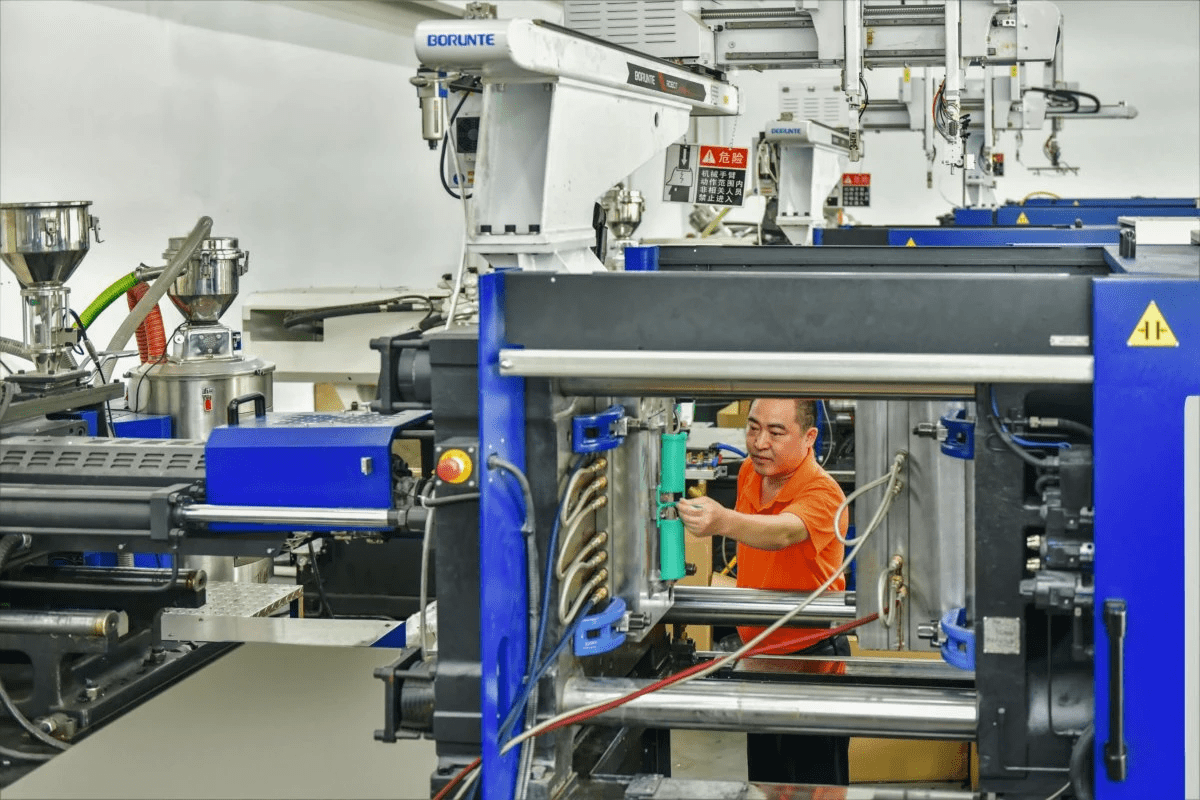
In the world of manufacturing, understanding injection moulding cost is crucial for businesses looking to optimize their production processes. From material selection to design complexity, numerous factors influence how much does injection molding cost? By grasping these elements, companies can make informed decisions that ultimately affect their bottom line.
Key Takeaways on Injection Moulding Costs
One of the most significant insights into injection moulding costs is that they are not one-size-fits-all; various elements contribute to the final price tag. For instance, knowing how to calculate injection mold cost accurately can save businesses from unexpected financial pitfalls. Moreover, acknowledging why injection moulding is expensive—such as investments in advanced technology and skilled labor—can help stakeholders justify costs and plan budgets effectively.
Best Practices for Cost Management
To manage injection moulding costs efficiently, companies should adopt a proactive approach to budgeting and planning. Regularly reviewing design specifications can help minimize unnecessary complexities that drive up expenses; after all, simpler designs often lead to lower costs! Additionally, fostering strong relationships with suppliers can yield better material prices and potentially reduce overall production costs.
Future Trends in Injection Moulding Pricing
As we look ahead, it's clear that trends in injection moulding pricing will continue evolving due to technological advancements and market demands. The rise of automation and smart manufacturing could significantly alter how much does injection molding cost per hour? Furthermore, sustainability practices are becoming more prevalent; businesses may find themselves investing in eco-friendly materials that initially seem costly but ultimately provide long-term savings.