Introduction
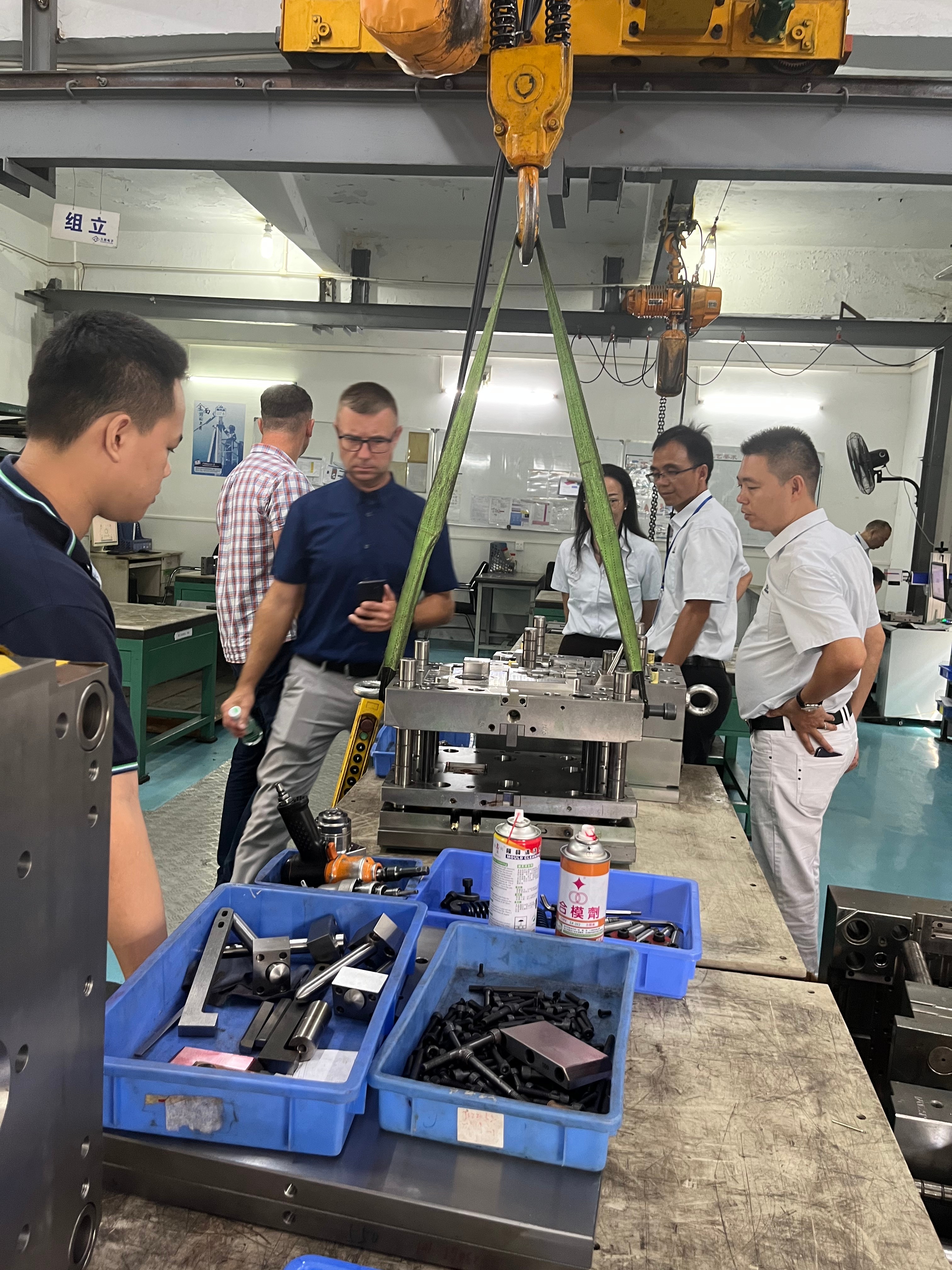
In the world of injection molding, flow lines can be both a technical challenge and a visual concern. These markings, often seen as streaks or lines on molded parts, can indicate issues in the manufacturing process. Understanding what flow lines are in injection molding is crucial for maintaining product quality and ensuring customer satisfaction.
What are Flow Lines in Injection Molding?
Flow lines in injection molding refer to the visible marks that appear on the surface of molded parts due to differences in material flow during the injection process. When molten plastic is injected into a mold, it travels along specific paths, and variations in speed or temperature can lead to these unsightly streaks. Essentially, they are a manifestation of how the material behaves as it fills the mold cavity, making it imperative for manufacturers to grasp this concept fully.
Understanding Flow Lines Defect in Injection Molding Process
The flow line defect in the injection molding process is a direct result of inconsistencies during production—be it related to material properties or environmental factors like temperature and pressure. These defects not only affect aesthetics but can also compromise functionality by creating weak points within the product structure. To mitigate such issues, it's essential to delve deeper into understanding what causes flow marks in injection molding and how they can be effectively addressed.
The Impact of Flow Lines on Product Quality
Flow lines significantly influence product quality by detracting from its visual appeal and potentially impacting its mechanical integrity. Customers often perceive products with noticeable flow marks as inferior or poorly manufactured, which could harm brand reputation and sales figures. Thus, learning how to avoid flow lines in injection molding becomes vital for businesses aiming for excellence and durability in their offerings.
Causes of Flow Marks in Injection Molding
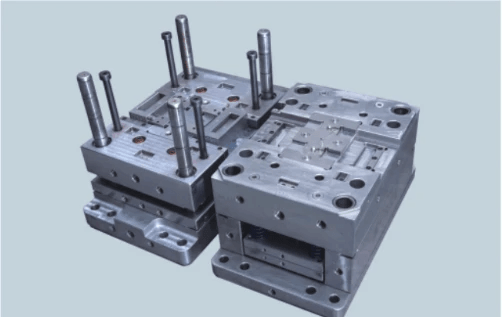
Flow marks, or flow lines, are a common defect in the injection molding process that can significantly impact product quality. Understanding what causes flow marks in injection molding is essential for manufacturers aiming to produce flawless components. This section delves into the primary culprits behind these pesky imperfections, including material properties, temperature and pressure variables, and mold design flaws.
Material Properties and Their Effects
The choice of material plays a crucial role in determining whether flow lines will appear during the injection molding process. Different polymers have varying viscosities, which can affect how smoothly they flow into the mold cavity; materials with high viscosity are more prone to creating flow lines due to their resistance to movement. Additionally, additives within the polymer can alter its behavior during processing—some may enhance fluidity while others may hinder it, leading to what causes flow marks in injection molding.
It's also important to consider the thermal properties of materials; some plastics cool down too quickly or unevenly, resulting in visible flow lines on the finished product. Therefore, selecting appropriate materials for specific applications is key when looking at how to avoid flow lines in injection molding. In summary, understanding material properties is vital for mitigating any potential defects like flow line defects in injection molding processes.
Temperature and Pressure Variables
Temperature and pressure are two critical variables that directly influence the occurrence of flow lines during injection molding. If the melt temperature is too low or if there's insufficient pressure applied during filling, it can lead to incomplete mold filling and uneven surface finishes—this is often where you'll see those unwanted flow marks creeping into your products. Conversely, excessively high temperatures can degrade certain materials or create other defects that might mimic or exacerbate flow line issues.
Moreover, maintaining consistent temperature throughout both the melt process and cooling phase is essential for achieving uniformity; fluctuations can lead to variations in viscosity that result in visible defects like flow marks on molded parts. To effectively tackle how to fix flow lines related to temperature and pressure issues, it's crucial for operators to monitor these parameters closely throughout production runs. Ultimately, understanding how these variables interact will help manufacturers prevent those pesky flaws from making an appearance.
Mold Design Flaws
Mold design flaws are another significant factor contributing to the development of flow line defects in injection molding processes. An improperly designed mold can create areas where material flows unevenly or experiences turbulence—common culprits that lead directly to visible surface imperfections like flow marks. For instance, sharp corners or abrupt changes in cross-section within a mold cavity can disrupt smooth material movement and result in unsightly defects.
Additionally, inadequate venting within a mold can trap air pockets which impede proper filling; this lack of airflow contributes not only to poor fill but also promotes conditions where unwanted flows occur as materials struggle against trapped air pressures. Addressing these design shortcomings through careful planning helps answer questions about how to avoid flow lines effectively while ensuring optimal performance from your molds over time. By focusing on improving mold design practices alongside other factors such as material selection and processing conditions, manufacturers can significantly reduce instances of those troublesome flaws.
Identifying Flow Line Defects
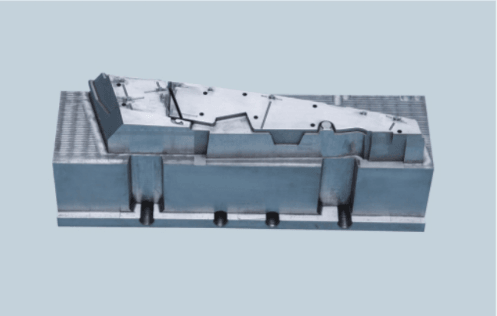
Identifying flow line defects in injection molding is crucial for maintaining product quality and preventing costly rework. Understanding the visual characteristics of flow lines, utilizing effective detection tools, and examining relevant case studies can provide valuable insights into this common issue. Let’s dive into each aspect to better understand how to identify these pesky flow lines in injection molding.
Visual Characteristics of Flow Lines
Flow lines are often visible as faint, wavy streaks or patterns on the surface of molded parts. These marks typically occur along the direction of material flow during the injection molding process, leading to a less than desirable aesthetic finish. When asking What are flow lines in injection molding?, it's important to note that these defects may vary in intensity; they can be subtle or pronounced, depending on factors such as material type and processing conditions.
In addition to affecting appearance, flow line defects can also compromise the perceived quality of a product, making it look cheap or poorly manufactured. Customers may associate visible flaws with inferior performance or durability, impacting brand reputation significantly. Therefore, recognizing these visual characteristics early on is essential for ensuring high-quality output.
Tools for Detection and Analysis
To effectively identify flow line defects in injection molding, several tools and techniques can be employed. Visual inspection remains a straightforward method; however, more advanced technologies such as infrared thermography and ultrasonic testing can provide deeper insights into potential issues within molds. These tools help detect temperature variations and inconsistencies that could lead to undesirable flow marks.
Additionally, software solutions that simulate the injection molding process can aid engineers in predicting where flow lines may occur before production begins. By analyzing variables such as temperature profiles and material behavior under pressure, teams can proactively address potential problems related to What causes flow marks in injection molding? This approach not only saves time but also reduces waste by avoiding flawed production runs.
Case Studies from the Industry
Examining real-world examples helps illuminate the challenges associated with identifying and addressing flow line defects in injection molding processes. For instance, one automotive manufacturer faced significant quality control issues due to recurring flow lines on their plastic components. By implementing rigorous inspection protocols combined with advanced detection tools like 3D scanning technology, they were able to pinpoint mold design flaws contributing to these defects.
Another case study highlights a consumer electronics company that sought ways to improve their production efficiency while minimizing aesthetic flaws like flow lines on their devices' casings. Through collaboration with material scientists and mold designers focused on optimizing parameters around How to avoid flow lines in injection molding?, they achieved remarkable results—reducing defect rates by over 30%.
These case studies illustrate how proactive identification of flow line defects not only enhances product quality but also streamlines manufacturing processes across various industries.
How to Avoid Flow Lines in Injection Molding
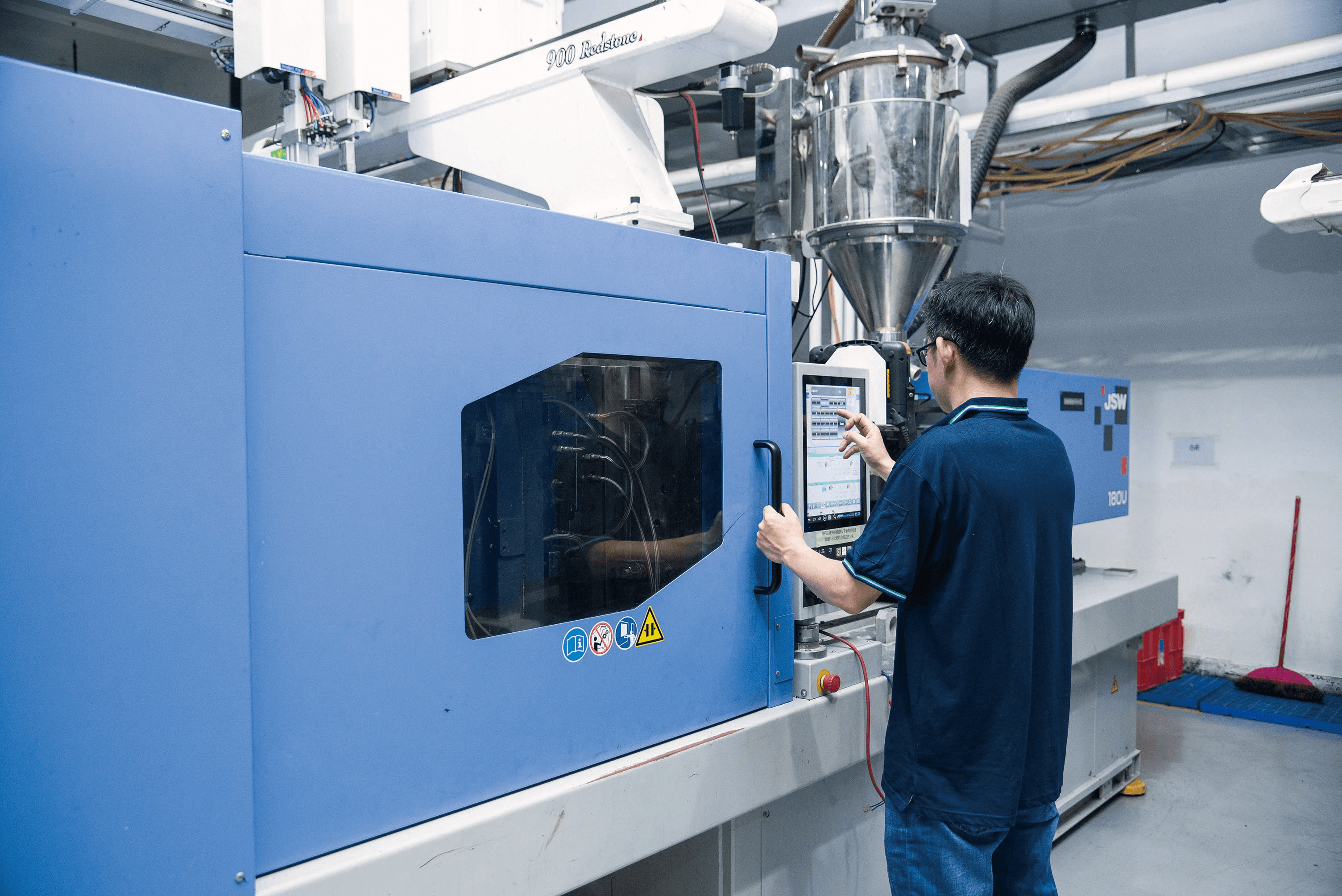
Avoiding flow lines in injection molding is crucial for maintaining product integrity and aesthetic appeal. By understanding the causes of flow marks in injection molding, manufacturers can implement strategies to minimize these defects. This section will explore best practices in material selection, optimizing injection speed and temperature, and the invaluable role of the Baoyuan team in prevention.
Best Practices in Material Selection
Selecting the right materials is fundamental when aiming to prevent flow lines in injection molding. Different polymers have varying viscosities, which significantly influence how they fill molds; using a material with suitable flow characteristics can greatly reduce the likelihood of defects. Additionally, incorporating additives or using blends can enhance fluidity and mitigate issues associated with flow line defects in the injection molding process.
When choosing materials, it’s essential to consider their thermal properties as well; some materials may require specific temperatures to achieve optimal flow without introducing unwanted marks. Furthermore, conducting thorough testing on material samples before full-scale production helps identify potential issues early on, allowing for adjustments before they become costly problems. Ultimately, a strategic approach to material selection can significantly contribute to minimizing flow marks during production.
Optimizing Injection Speed and Temperature
One of the most effective methods for avoiding flow lines in injection molding is by optimizing both injection speed and temperature settings during the process. An appropriate balance between these variables ensures that molten plastic fills the mold efficiently without leaving behind unsightly defects like flow lines. Too slow an injection speed may cause premature cooling and lead to uneven filling patterns; conversely, too fast an injection speed can create turbulence that exacerbates flow marks.
Temperature control also plays a pivotal role; maintaining optimal melt temperatures allows for better material consistency and reduces viscosity-related issues that contribute to defect formation. Regular monitoring of these parameters throughout production helps maintain quality control while preventing variations that could result in unacceptable product outcomes. In essence, fine-tuning these aspects not only enhances product quality but also extends machinery lifespan by reducing wear from improper settings.
The Role of the Baoyuan Team in Prevention
The Baoyuan team plays a critical role when it comes to preventing flow line defects during the injection molding process. With their extensive expertise and experience, they implement tailored strategies aimed at addressing specific challenges faced by manufacturers dealing with flow marks in injection molding products. Their proactive approach includes conducting comprehensive analyses of existing processes and providing actionable recommendations based on industry best practices.
By collaborating closely with clients, Baoyuan ensures that all factors contributing to potential flaws—such as mold design flaws or inadequate machine settings—are addressed effectively before production begins. Moreover, ongoing training sessions provided by Baoyuan equip teams with essential knowledge about how to avoid common pitfalls related to flow line defects in injection molding processes over time. In summary, leveraging Baoyuan’s expertise not only enhances immediate manufacturing efficiency but also fosters long-term quality assurance within organizations.
How to Fix Flow Lines
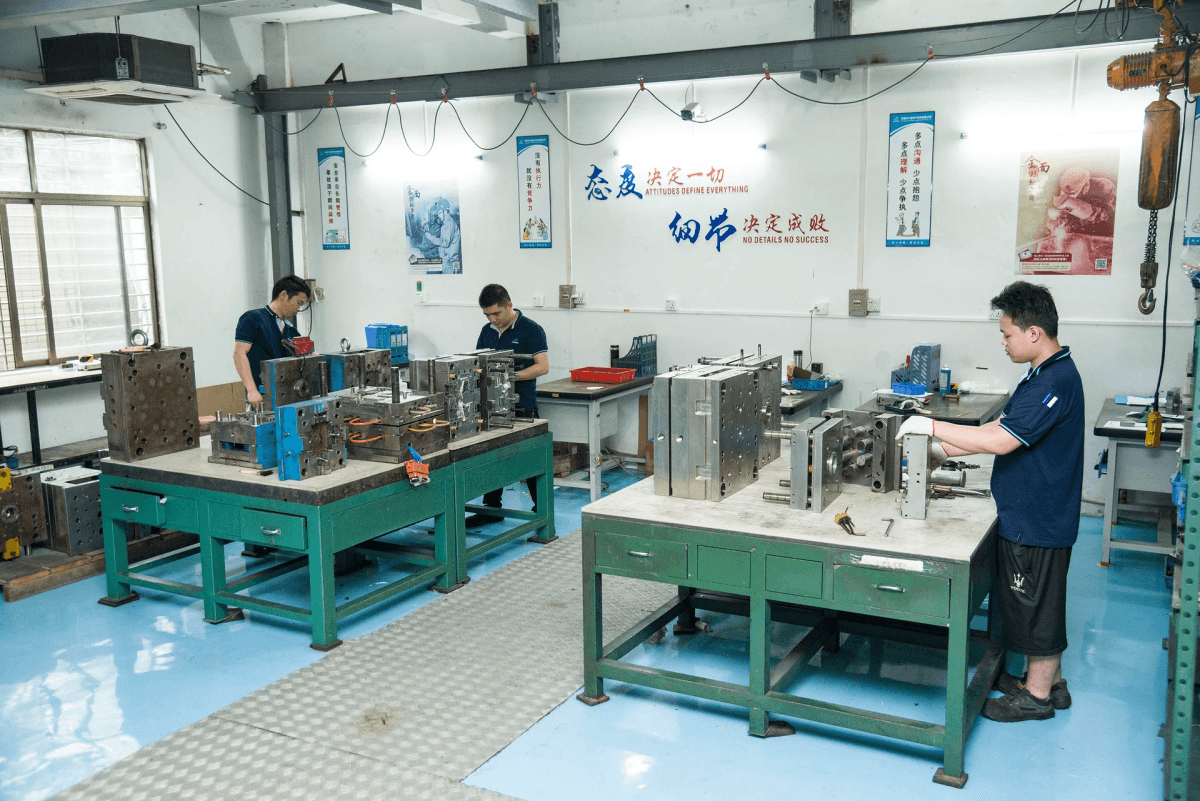
When it comes to addressing flow lines in injection molding, a proactive approach is essential. Understanding how to fix flow lines not only improves product quality but also enhances production efficiency. By implementing the right techniques and focusing on maintenance, manufacturers can significantly reduce the occurrence of flow lines defects in the injection molding process.
Techniques for Remediation and Adjustments
To effectively tackle flow marks in injection molding, several techniques can be employed for remediation and adjustments. First, adjusting the injection speed can help ensure that material fills the mold evenly, reducing turbulence that often leads to visible flow lines. Additionally, fine-tuning the temperature settings of both the material and mold can further minimize these defects; a well-regulated thermal environment ensures consistent material behavior during injection.
Another effective technique is optimizing gate location and size, which directly influences how material enters the mold cavity. By strategically placing gates or modifying their dimensions, manufacturers can facilitate smoother flows that mitigate potential flow line issues. Lastly, conducting a thorough analysis of cycle times may reveal opportunities for adjustments that lead to better filling patterns and reduced chances of flow line formation.
Importance of Mold Maintenance
Mold maintenance plays a crucial role in preventing flow lines in injection molding processes. Regular inspection and cleaning of molds are essential practices that help maintain optimal performance over time. Accumulated residue or wear on mold surfaces can disrupt material flow, leading to imperfections such as flow lines; therefore, keeping molds clean is non-negotiable.
Moreover, timely repairs are vital in ensuring that molds remain effective throughout their lifecycle. Any minor damage or misalignment should be addressed immediately to prevent exacerbating issues during production runs. By prioritizing mold maintenance as part of an overall quality assurance strategy, manufacturers can significantly reduce instances of flow marks in injection molding.
Leveraging Technology for Solutions
In today's manufacturing landscape, leveraging technology is key to solving challenges like flow line defects in injection molding processes. Advanced simulation software allows engineers to visualize material flows before actual production begins; this capability helps identify potential problem areas where flow lines might occur based on design parameters alone. Such foresight enables proactive adjustments before any physical materials are introduced into the equation.
Additionally, incorporating real-time monitoring systems into machinery provides valuable data regarding pressure and temperature fluctuations during production runs. This information empowers operators to make immediate adjustments if conditions deviate from optimal settings—ultimately helping avoid unwanted flaws like flow marks in injection molding products. Embracing these technological solutions not only enhances product quality but also fosters a culture of continuous improvement within manufacturing environments.
Long-term Solutions for Flow Lines
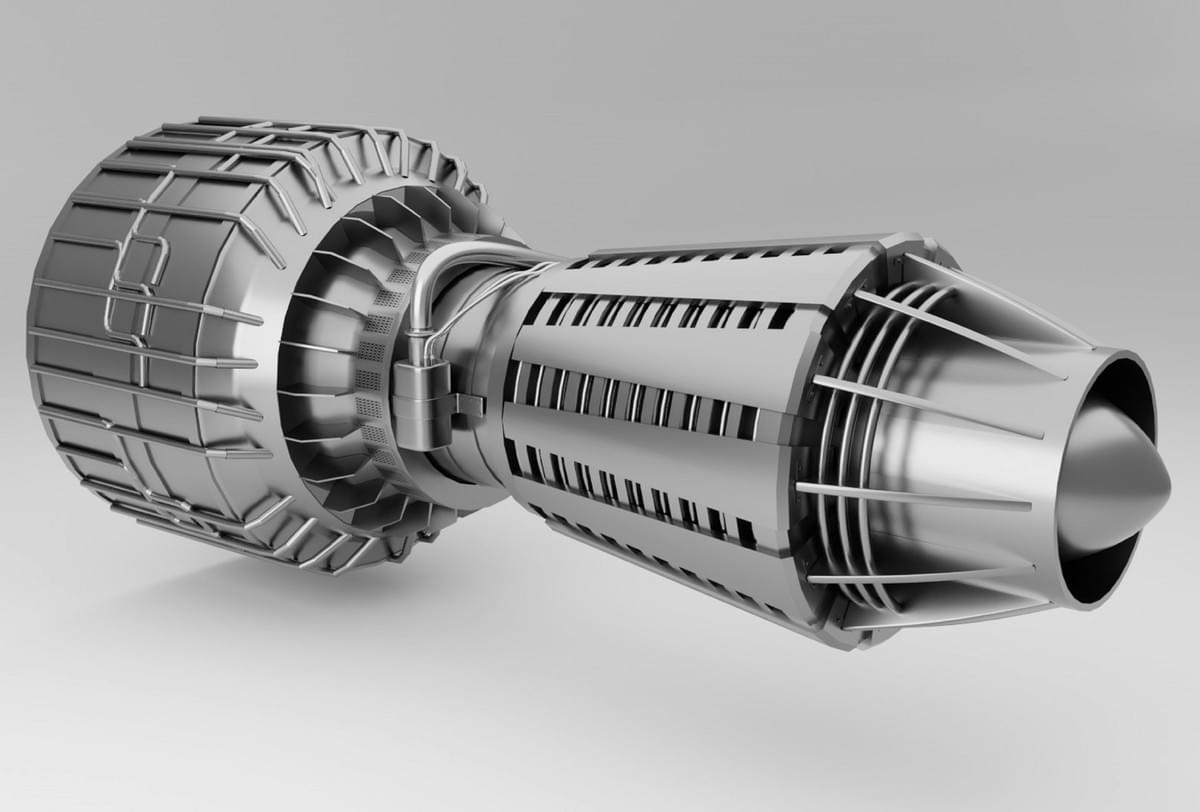
Addressing flow line defects in injection molding requires a multifaceted approach that focuses on continuous improvement, training, and cultivating a quality assurance culture. By implementing these long-term solutions, manufacturers can significantly reduce the occurrence of flow lines and enhance product quality. The goal is not just to fix existing issues but to prevent them from arising in the first place.
Continuous Improvement Practices
Continuous improvement practices are essential for anyone serious about tackling flow lines in injection molding. This involves regularly analyzing production processes and identifying areas for enhancement—think of it as an ongoing quest for perfection! By adopting methodologies like Lean Manufacturing or Six Sigma, teams can systematically eliminate waste and variability that contribute to flow line defects.
Moreover, using data-driven approaches allows manufacturers to pinpoint what causes flow marks in injection molding more effectively. Regularly reviewing production metrics will help identify trends that lead to defects, enabling proactive adjustments before problems escalate. Ultimately, fostering a culture of continuous improvement encourages everyone involved in the process to contribute ideas and solutions tailored to avoid future occurrences of flow lines.
Training and Development in Injection Molding
Training and development play a crucial role in minimizing flow line issues by equipping employees with the necessary skills and knowledge. What are flow lines in injection molding? Understanding this concept is fundamental for all team members—from machine operators to engineers—who interact with the process daily. Regular workshops or training sessions focusing on material properties, mold design, and operational techniques can significantly raise awareness about how to avoid flow lines in injection molding.
Additionally, hands-on training helps employees recognize visual characteristics of flow lines early on so they can take corrective action immediately. This proactive mindset is vital when addressing what causes flow marks in injection molding; understanding these causes empowers teams to make informed decisions during production runs. Investing time into employee development not only boosts morale but also leads to higher-quality products with fewer defects.
Building a Quality Assurance Culture
Building a quality assurance culture within an organization is paramount when striving for excellence in reducing flow line defects during the injection molding process. A strong emphasis on quality means that every individual takes ownership of their role in maintaining product standards while being vigilant about potential issues like flow lines defect in injection molding processes. Encouraging open communication about quality concerns fosters an environment where everyone feels responsible for upholding high standards.
Implementing regular audits and feedback loops helps reinforce this culture by allowing teams to assess their performance continually while learning how to fix flow lines if they do occur. Additionally, recognizing team members who contribute positively towards maintaining quality standards promotes motivation across departments—all working together toward common goals! Ultimately, establishing a robust quality assurance culture ensures that attention remains focused on preventing defects rather than merely reacting after they happen.
Conclusion
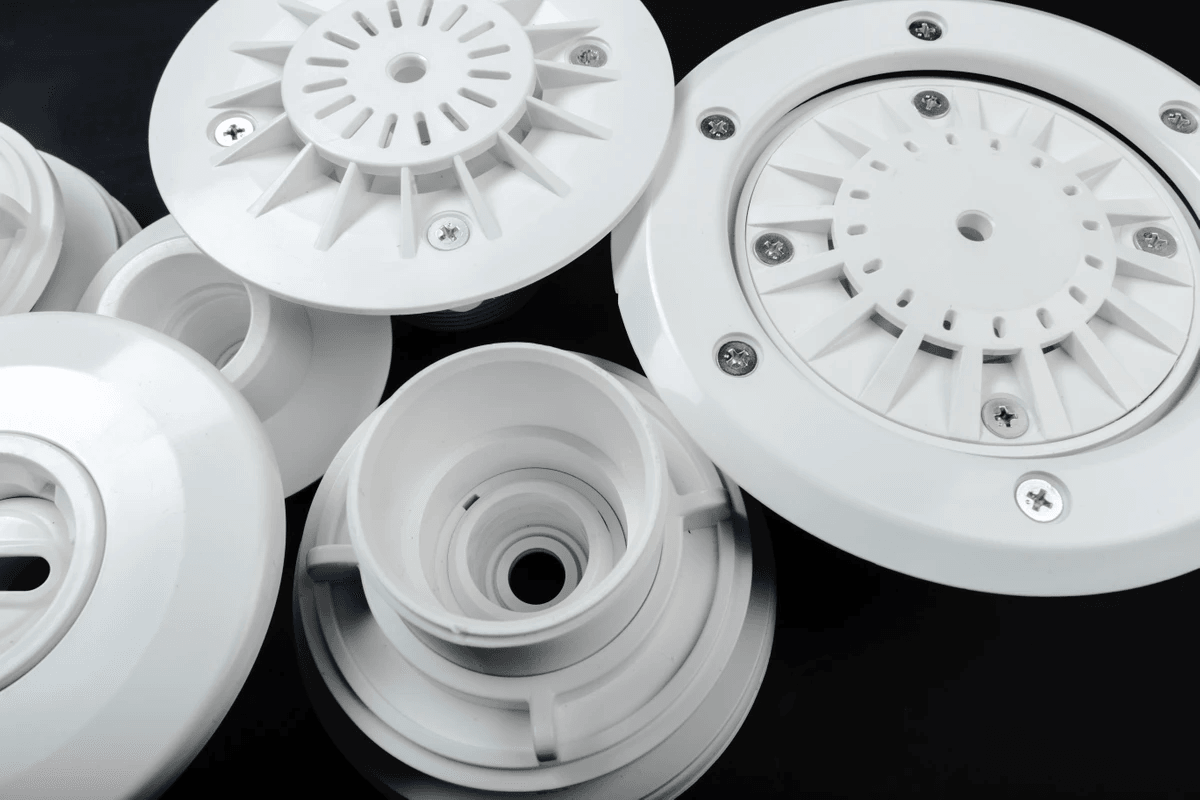
In the world of injection molding, understanding flow lines is crucial for maintaining product quality and ensuring efficient manufacturing processes. Flow lines defects can significantly affect the aesthetic and functional aspects of molded products, leading to increased costs and customer dissatisfaction. By grasping what causes flow marks in injection molding and implementing effective strategies for prevention and remediation, manufacturers can enhance their overall production quality.
Key Takeaways on Flow Lines Defect in Injection Molding Process
Flow line defects are primarily caused by variations in material properties, temperature fluctuations, and mold design flaws. Knowing how to avoid flow lines in injection molding involves a combination of selecting appropriate materials, optimizing processing conditions, and ensuring proper mold design. Additionally, regular maintenance and updates to technology play a vital role in addressing these defects effectively.
The Future of Injection Molding Technology
The future of injection molding technology looks promising with advancements aimed at minimizing flow line occurrences. Innovations such as smart sensors for real-time monitoring will help identify potential issues before they escalate into costly defects. Moreover, the integration of artificial intelligence will enable predictive analytics that can optimize processes further, ensuring high-quality outputs with fewer imperfections like flow lines.
Resources for Further Learning and Improvement
For those eager to dive deeper into the intricacies of flow line injection molding, numerous resources are available online that cover everything from basic concepts to advanced techniques. Industry-specific training programs often provide valuable insights into how to fix flow lines effectively while keeping abreast of new technologies in the field. Books, webinars, and professional organizations also serve as excellent platforms for continuous learning about what causes flow marks in injection molding.