Introduction
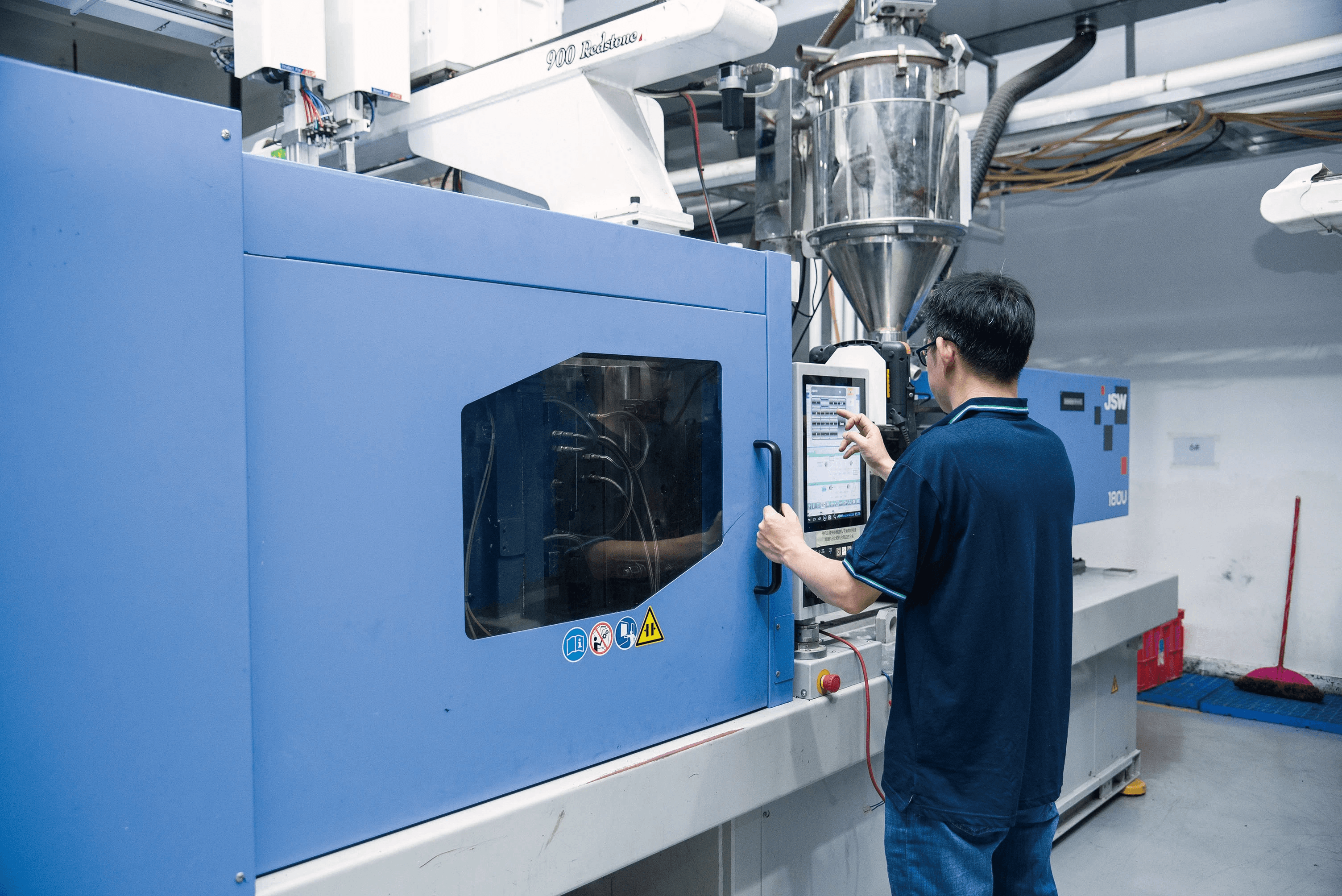
In the world of manufacturing, PVC injection moulding stands out as a versatile and efficient process for creating a wide range of plastic products. Understanding the intricacies of this method is crucial for anyone involved in production, from engineers to business owners. By digging into cost factors and applications, we can appreciate how PVC has become a go-to material across various industries.
Overview of PVC Injection Moulding
PVC injection moulding is a manufacturing technique that involves melting polyvinyl chloride (PVC) pellets and injecting them into a mold to form desired shapes. This process allows for high precision and repeatability, making it ideal for mass production of complex parts. But what is PVC molding really? It’s the art and science behind transforming raw materials into functional products that meet specific industry standards.
Importance of Understanding Cost Factors
When it comes to PVC injection moulding, understanding cost factors can make or break your project’s budget. From material costs to labor expenses, every element plays a pivotal role in determining the overall financial feasibility of production runs. By grasping these factors, manufacturers can streamline processes, enhance profitability, and ultimately answer questions like “Can PVC be injection molded?” with confidence.
Common Applications for PVC
PVC's versatility lends itself to numerous applications across different sectors. From construction materials like pipes and fittings to consumer goods such as toys and packaging, its uses are virtually limitless. As we explore further into this topic, we'll also tackle questions surrounding potential issues—like what are the problems with injection molding PVC?—and delve into its compatibility with other materials such as PVA.
Understanding PVC Injection Moulding
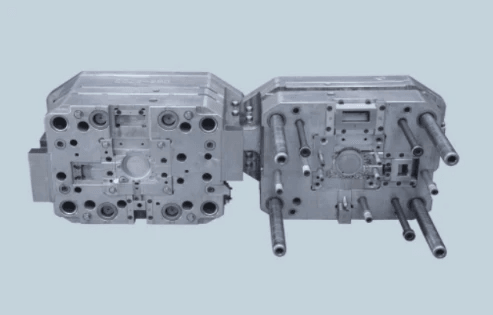
PVC injection moulding is a fascinating process that has revolutionized the way we create plastic products. This technique involves melting polyvinyl chloride (PVC) resin and injecting it into a mold to form various shapes and designs. The versatility of PVC molding makes it an attractive option for manufacturers looking to produce high-quality, durable items efficiently.
What is PVC Molding?
What is PVC molding, you ask? It's the art and science of using polyvinyl chloride in the injection moulding process to make everything from pipes to toys. Essentially, manufacturers heat PVC until it becomes pliable, then inject it into a carefully designed mold where it cools and solidifies into the desired shape. This method allows for intricate designs and high-volume production, making it a staple in various industries.
Benefits of PVC in Manufacturing
The benefits of PVC in manufacturing are numerous and compelling. First off, PVC is lightweight yet incredibly strong, which means products can be both sturdy and easy to handle. Additionally, its resistance to chemicals and moisture makes it ideal for applications ranging from construction materials to consumer goods—talk about versatility! Moreover, using pvc injection moulding can significantly reduce waste compared to other manufacturing processes since excess material can often be recycled back into production.
Can PVC be Injection Molded?
So, can PVC be injection molded? Absolutely! In fact, it's one of the most common methods used for processing this material due to its efficiency and effectiveness. However, while the answer is a resounding yes, it's essential to consider some challenges that come with injection molding PVC; for instance, controlling temperatures during processing can be tricky—too hot or too cold can lead to defects or incomplete molds. Despite these hurdles, with proper techniques in place, manufacturers can successfully harness this method for creating high-quality products.
Key Cost Factors in PVC Injection Moulding
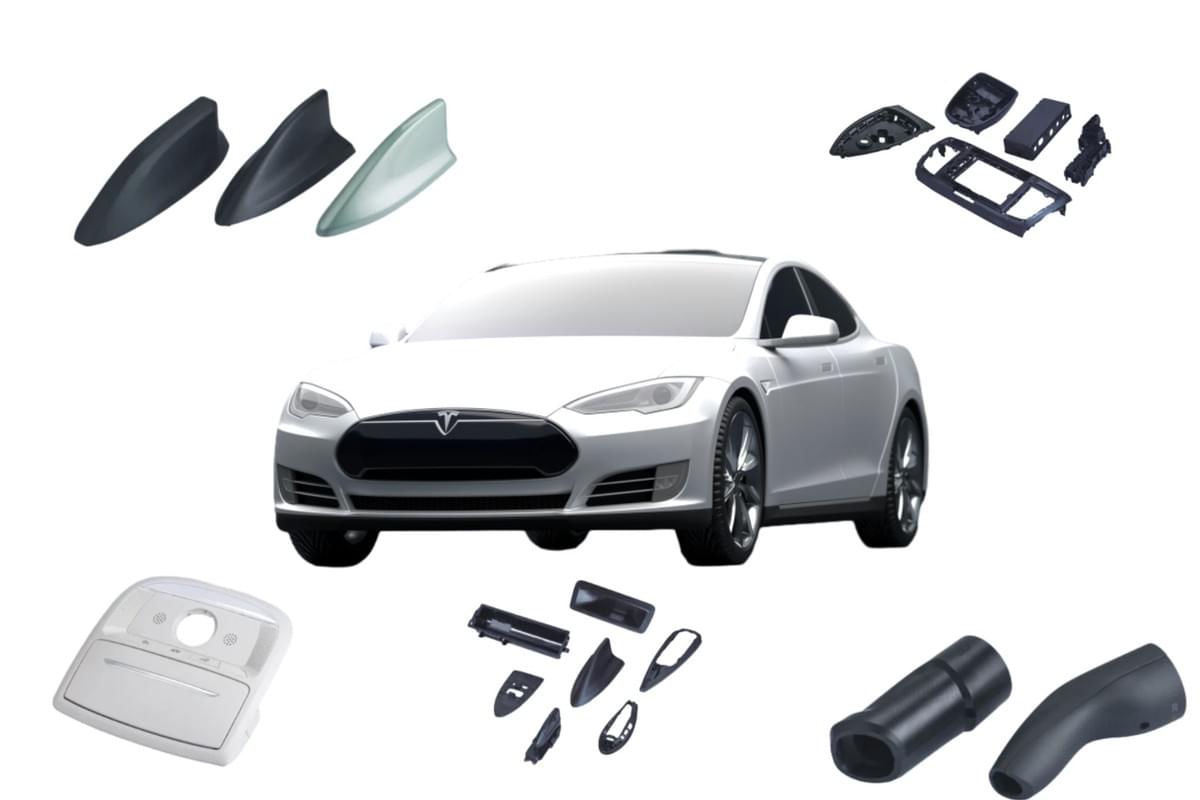
When diving into the world of PVC injection moulding, understanding the cost factors is crucial for manufacturers and businesses alike. The costs associated with this process can vary significantly based on several key components, including material expenses, machinery investments, and labor requirements. By analyzing these factors, companies can make informed decisions that enhance profitability while maintaining quality.
Material Costs and Their Impact
Material costs are a significant portion of the overall expenses in PVC injection moulding. The price of PVC resin fluctuates based on market demand and supply chain dynamics; thus, manufacturers need to keep an eye on these trends to manage costs effectively. Additionally, considering alternative materials like PVA can be beneficial in specific applications, but one must ask: Can PVA be injection molded? This question often arises when evaluating material options alongside traditional PVC.
The choice of additives also plays a role in material costs—enhancing properties like flexibility or UV resistance can increase expenses but may lead to better product performance. It’s essential to strike a balance between cost and functionality; after all, what are the problems with injection molding PVC? Understanding these challenges helps manufacturers optimize their material selections for both economic viability and performance.
Machinery and Equipment Expenses
Investing in machinery for PVC injection moulding is another critical factor that impacts overall costs. High-quality equipment is necessary to achieve precision and efficiency during production runs; however, this comes at a price.
Moreover, maintenance costs should not be overlooked as they can add up over time if machines aren’t properly cared for. Regular servicing ensures that equipment operates efficiently and reduces downtime caused by malfunctions or repairs—something every manufacturer dreads! Ultimately, businesses must weigh initial investments against ongoing operational expenses to determine the best approach for their specific needs.
Labor Costs and Skill Levels Required
Labor costs are another vital component of the total expenditure in PVC injection moulding operations. Skilled labor is necessary not only for operating complex machinery but also for troubleshooting issues that arise during production processes. When asking “Can PVC be injection molded?” it’s important to remember that skilled technicians need to understand both the technical aspects of molding as well as how different materials interact during processing.
Training staff in best practices is crucial; poorly trained employees can lead to higher scrap rates or defective products—both costly outcomes! Furthermore, labor availability varies by region; some areas may have a surplus of skilled workers while others struggle with shortages which could affect wage rates significantly over time.
Design Considerations for Cost Efficiency
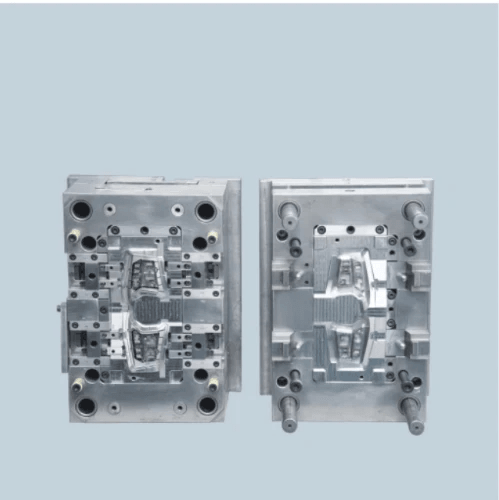
Importance of Effective Mold Design
Effective mold design is paramount in PVC injection moulding as it directly impacts production efficiency and material usage. A well-designed mold can facilitate better flow of the molten PVC, ensuring that every nook and cranny of the mold cavity is filled without defects. This not only reduces scrap rates but also addresses some common issues such as warping or incomplete filling, which are often raised when asking What are the problems with injection molding PVC?
Incorporating features like uniform wall thickness and proper venting into the mold design can lead to significant cost savings over time. Additionally, an effective mold design allows for quicker changeovers between products, further enhancing productivity in a competitive manufacturing landscape. Ultimately, investing time in designing molds efficiently pays off by lowering costs associated with rework or excessive material waste.
Can PVA be Injection Molded?
The question Can PVA be injection molded? often arises in discussions about materials used alongside PVC in various applications. While PVA (polyvinyl alcohol) is indeed a viable candidate for injection molding processes, its compatibility with PVC requires careful consideration regarding temperature settings and material properties during processing.
Both materials exhibit unique characteristics that must be understood to achieve optimal results when combining them in a single production run or part design. Understanding these nuances can help manufacturers leverage both materials effectively while avoiding common pitfalls associated with each—thus addressing concerns related to quality control during PVC injection moulding operations.
Streamlining the Production Process
Streamlining the production process involves adopting best practices that enhance efficiency while managing costs effectively within PVC injection moulding operations. Techniques such as optimizing cycle times through improved cooling methods or utilizing advanced automation technologies can significantly reduce labor costs while maintaining high-quality output levels.
Moreover, implementing lean manufacturing principles helps identify areas where resources may be wasted or processes could be improved—ultimately leading to better resource allocation and reduced overall expenses. By continuously refining their production processes, companies engaged in PVC injection moulding can remain competitive while ensuring they deliver quality products at lower prices.
Quality Control in PVC Injection Moulding
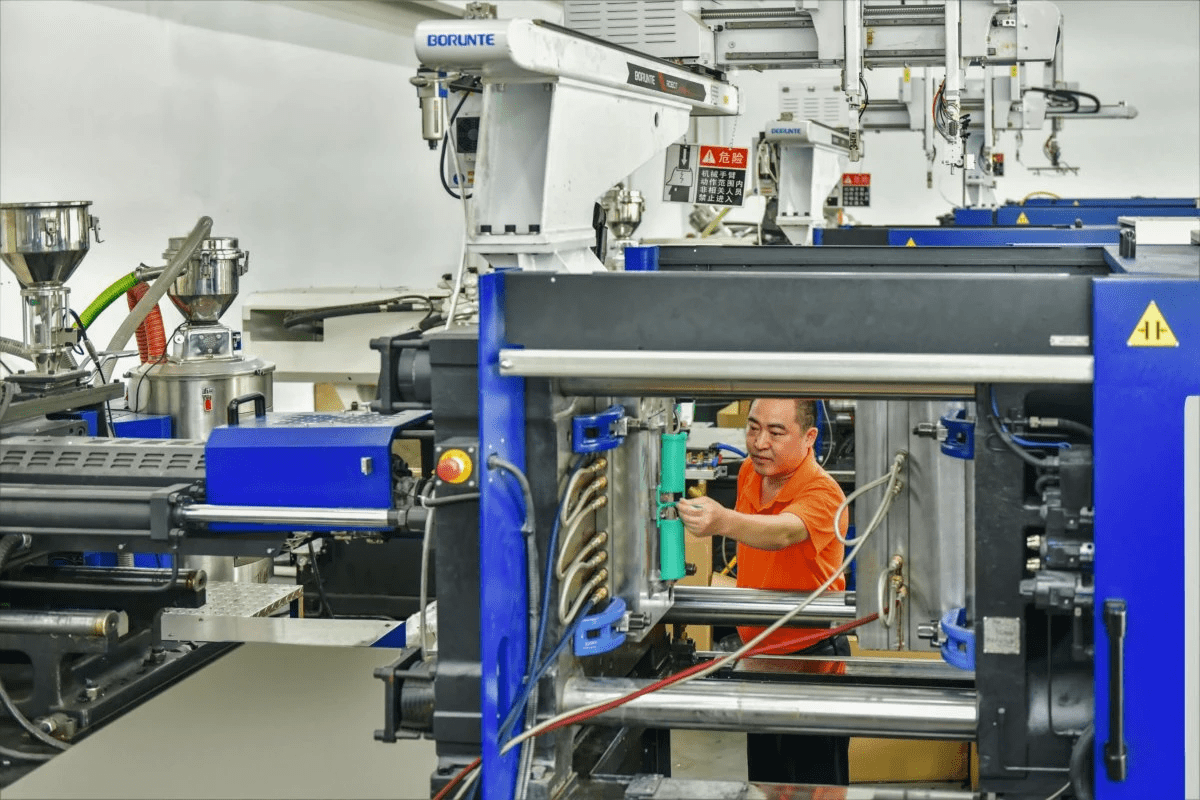
Quality control is a critical aspect of PVC injection moulding, ensuring that the final products meet industry standards and customer expectations. However, the process isn't without its challenges. By understanding the common issues associated with this method, manufacturers can implement effective strategies to enhance quality and performance.
What Are the Problems with Injection Molding PVC?
When it comes to PVC injection moulding, several problems can arise during production. One significant issue is warping, which occurs when the material cools unevenly after being injected into the mold. Additionally, poor adhesion between layers can lead to weak spots in the final product, raising concerns about durability and functionality.
Another problem is flash—excess material that seeps out of the mold during injection. This not only affects aesthetics but also requires additional trimming and labor costs for cleanup. Moreover, color consistency can be a challenge; variations in pigmentation may lead to discrepancies in product appearance if not monitored closely throughout the process.
Quality Assurance Techniques Used by Baoyuan
At Baoyuan, quality assurance techniques play a pivotal role in mitigating issues related to PVC injection moulding. Their approach includes rigorous testing protocols at various stages of production to ensure that each component meets specific criteria for strength and durability. Advanced technologies such as real-time monitoring systems help detect anomalies early on, allowing for immediate corrective measures.
Moreover, Baoyuan emphasizes employee training on best practices for handling materials like PVC effectively—ensuring that everyone involved understands how their actions impact overall quality. Regular audits of machinery and equipment also contribute significantly; by maintaining optimal conditions for production, they minimize defects linked to machinery errors.
Balancing Cost and Quality
Finding a balance between cost and quality is an ongoing challenge in PVC injection moulding that requires strategic planning and execution. While it might be tempting to cut corners on materials or processes to save money upfront, this often leads to higher long-term costs due to increased waste or product returns resulting from quality issues. Therefore, investing in high-quality materials and robust quality assurance techniques proves beneficial over time.
Furthermore, effective design plays a crucial role in this balance; well-designed molds reduce scrap rates while enhancing product consistency—ultimately leading to lower costs per unit produced without sacrificing quality standards. In this competitive market landscape where consumer expectations are high, companies must strive not only for efficiency but also for excellence in every aspect of their manufacturing processes.
Future Trends in PVC Injection Moulding
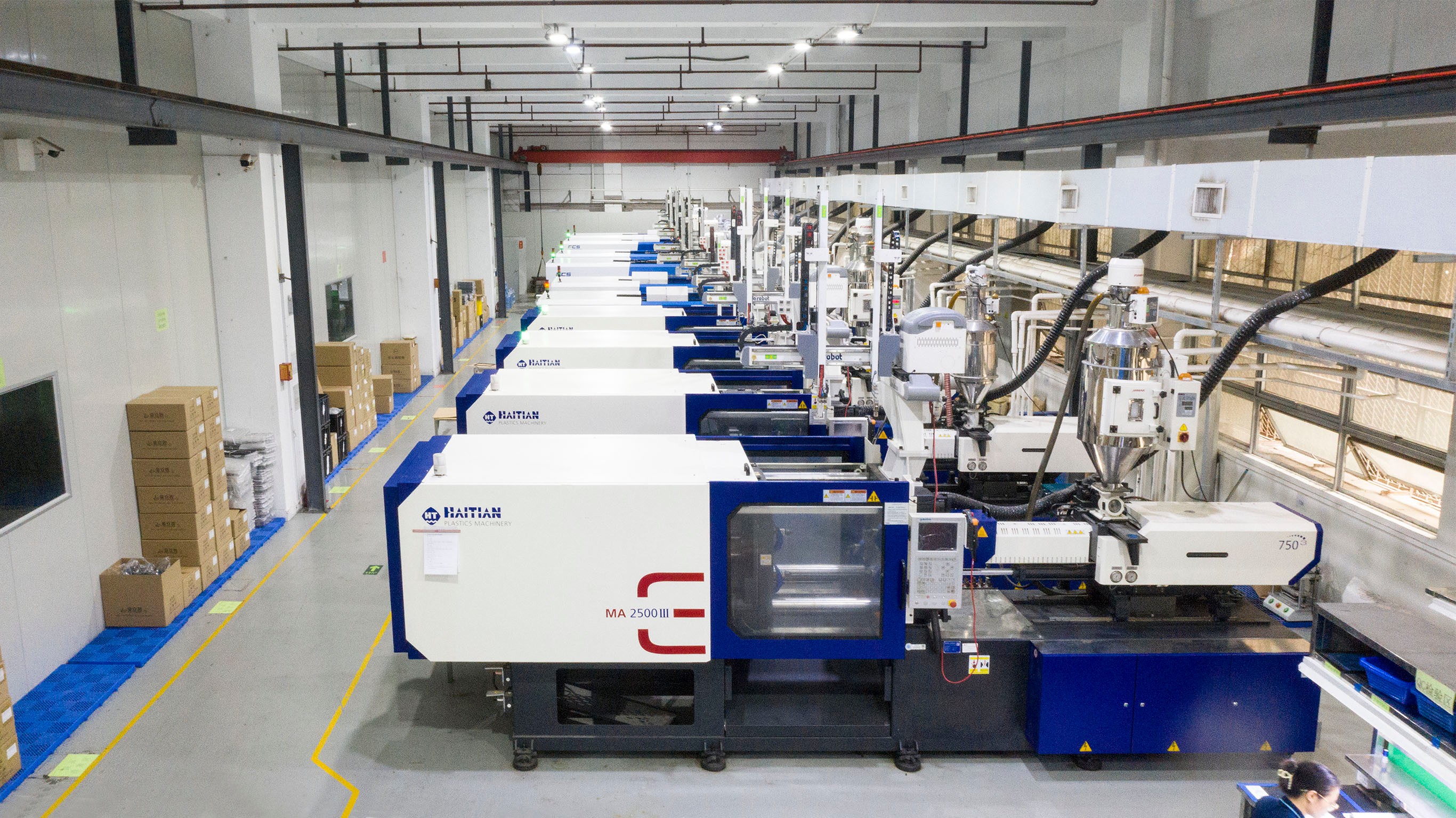
The landscape of PVC injection moulding is rapidly evolving, driven by innovations in materials and technology, a growing emphasis on sustainability practices, and fluctuating market demands. Staying ahead of these trends is essential for manufacturers wanting to optimize their processes and costs effectively. As we explore these future trends, it’s crucial to consider how they will shape the industry’s direction.
Innovations in Materials and Technology
Innovations are redefining what is possible with PVC injection moulding, enhancing both the performance of the material and the efficiency of production processes. New formulations of PVC are being developed that improve flexibility, durability, and resistance to environmental factors—making them even more attractive for various applications. Moreover, advancements in injection moulding technology have led to faster cycle times and reduced energy consumption, answering the question: Can PVC be injection molded? Absolutely! The latest machinery allows for more intricate designs while minimizing waste.
Additionally, smart manufacturing technologies like IoT (Internet of Things) are being integrated into production lines. This means manufacturers can monitor processes in real-time, ensuring quality control while optimizing costs associated with labor and materials. As these innovations continue to emerge, they promise not only improved product quality but also a significant reduction in the common problems associated with injection molding PVC.
Sustainability Practices in the Industry
Sustainability has become a buzzword across industries—and for good reason! In PVC injection moulding specifically, there is a concerted effort toward reducing environmental impact through recycling initiatives and sustainable sourcing of materials. Many manufacturers are now exploring bioplastics or recycled PVC options that still meet performance standards while being kinder to our planet.
Another aspect of sustainability involves optimizing production processes to minimize waste generated during manufacturing. By improving efficiency within their operations—whether through better mold design or advanced technology—companies can significantly reduce their carbon footprint while addressing consumer demand for greener products. With this shift towards sustainability practices in the industry comes an opportunity for businesses that want to lead by example; after all, consumers increasingly favor brands committed to eco-friendly practices.
Market Demand and Its Influence on Costs
Market demand plays a pivotal role in shaping costs associated with PVC injection moulding. As industries such as automotive, construction, and consumer goods continue to grow, so does the need for high-quality PVC products—driving up demand for efficient production methods that maintain cost-effectiveness without sacrificing quality. This constant fluctuation raises important questions: What are the problems with injection molding PVC? How can manufacturers adapt?
To navigate these challenges successfully, companies must be agile enough to respond quickly to changing market conditions while maintaining competitive pricing structures. Furthermore, as newer applications emerge that utilize advanced forms of PVC—like those found in medical devices or electronics—the cost dynamics will inevitably shift again due to increased complexity or regulatory requirements surrounding these specialized uses.
In conclusion, staying informed about innovations in materials and technology will be key for anyone involved in pvc injection moulding moving forward; embracing sustainability practices can yield not only environmental benefits but also cost savings; lastly understanding market demands will help ensure businesses remain competitive amidst ever-evolving challenges.
Conclusion
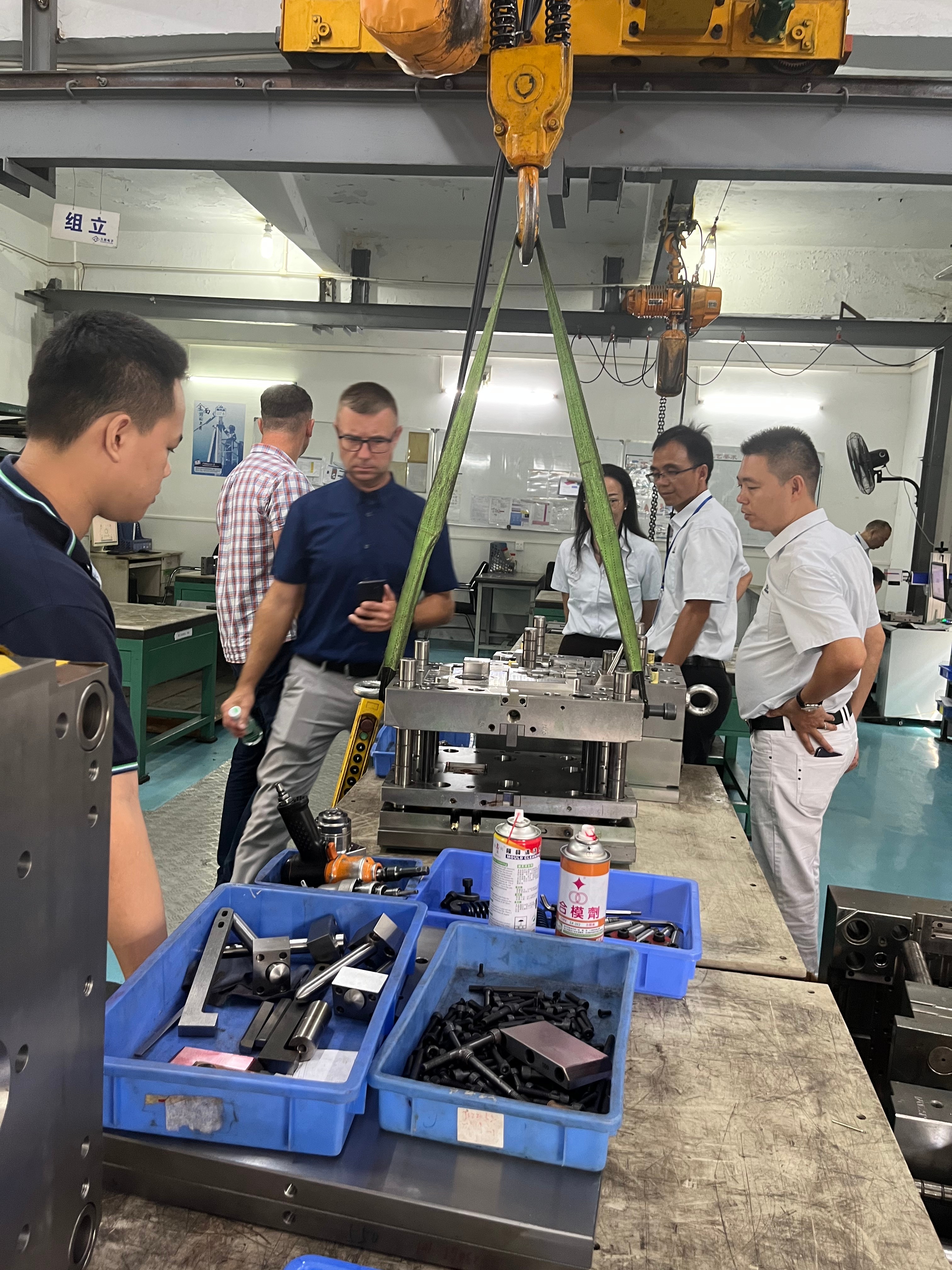
In summary, understanding the cost factors in PVC injection moulding is crucial for manufacturers looking to optimize their processes. From material costs to labor expenses and machinery investments, each element plays a vital role in determining the overall expenditure. By recognizing these factors, businesses can make informed decisions that enhance profitability while maintaining quality.
Recap of Cost Factors in PVC Injection Moulding
The journey through the world of PVC injection moulding reveals several key cost factors that cannot be overlooked. Material costs are foundational; high-quality PVC can significantly impact the final product's durability and appearance. Additionally, machinery and equipment expenses contribute heavily to initial investments, while labor costs fluctuate based on skill levels required for effective production.
The Role of Efficient Design and Quality Control
Efficient design is paramount in reducing costs associated with PVC injection moulding while ensuring optimal performance. A well-thought-out mold design not only minimizes waste but also enhances production speed—making it easier to answer the question: Can PVC be injection molded? Furthermore, implementing rigorous quality control measures helps address potential issues such as those found in What are the problems with injection molding PVC? thus balancing cost with quality effectively.
Insights from the Baoyuan Team on Best Practices
The Baoyuan team emphasizes that adopting best practices in PVC injection moulding can lead to remarkable efficiency gains. They advocate for continuous improvement through innovative techniques and materials—addressing queries like Can PVA be injection molded? by exploring alternative materials when necessary. Ultimately, their insights serve as a reminder that staying informed about industry trends is key to navigating both challenges and opportunities within this dynamic field.