Introduction

Clear injection molded plastics have become a game-changer in various industries, offering both aesthetic appeal and functional benefits. These versatile materials are produced through the plastic injection molding process, allowing for the creation of complex shapes while maintaining transparency. With applications ranging from consumer products to industrial components, clear injection molded plastics are redefining what’s possible in design and manufacturing.
What Are Clear Injection Molded Plastics
Clear injection molded plastics refer to transparent materials created through the plastic injection molding process, which involves melting plastic pellets and injecting them into molds. This technique enables manufacturers to produce high-quality, detailed parts that can be both visually appealing and structurally sound. Common types of clear injection moldable plastics include acrylic plastic and polypropylene plastic, each offering unique properties suitable for various applications.
Benefits of Clear Injection Molded Plastics
The benefits of clear injection molded plastics are numerous and compelling for businesses seeking efficient production solutions. First and foremost is their impressive transparency, which enhances product visibility and aesthetic appeal—perfect for retail displays or packaging. Additionally, these materials boast durability and resistance to impact, making them ideal for products that require longevity without sacrificing style; they also offer cost-effectiveness when produced at scale through reliable plastic injection molding services.
Applications of Clear Injection Molded Plastics
Clear injection molded plastics find their way into an array of applications across multiple sectors. From consumer goods like containers and household items to more specialized uses in automotive parts or medical devices, the versatility is astounding. Companies often turn to experienced injection molding companies for tailored solutions that leverage these innovative materials—ensuring they meet specific industry standards while maximizing efficiency in production.
Overview of Injection Molding Process
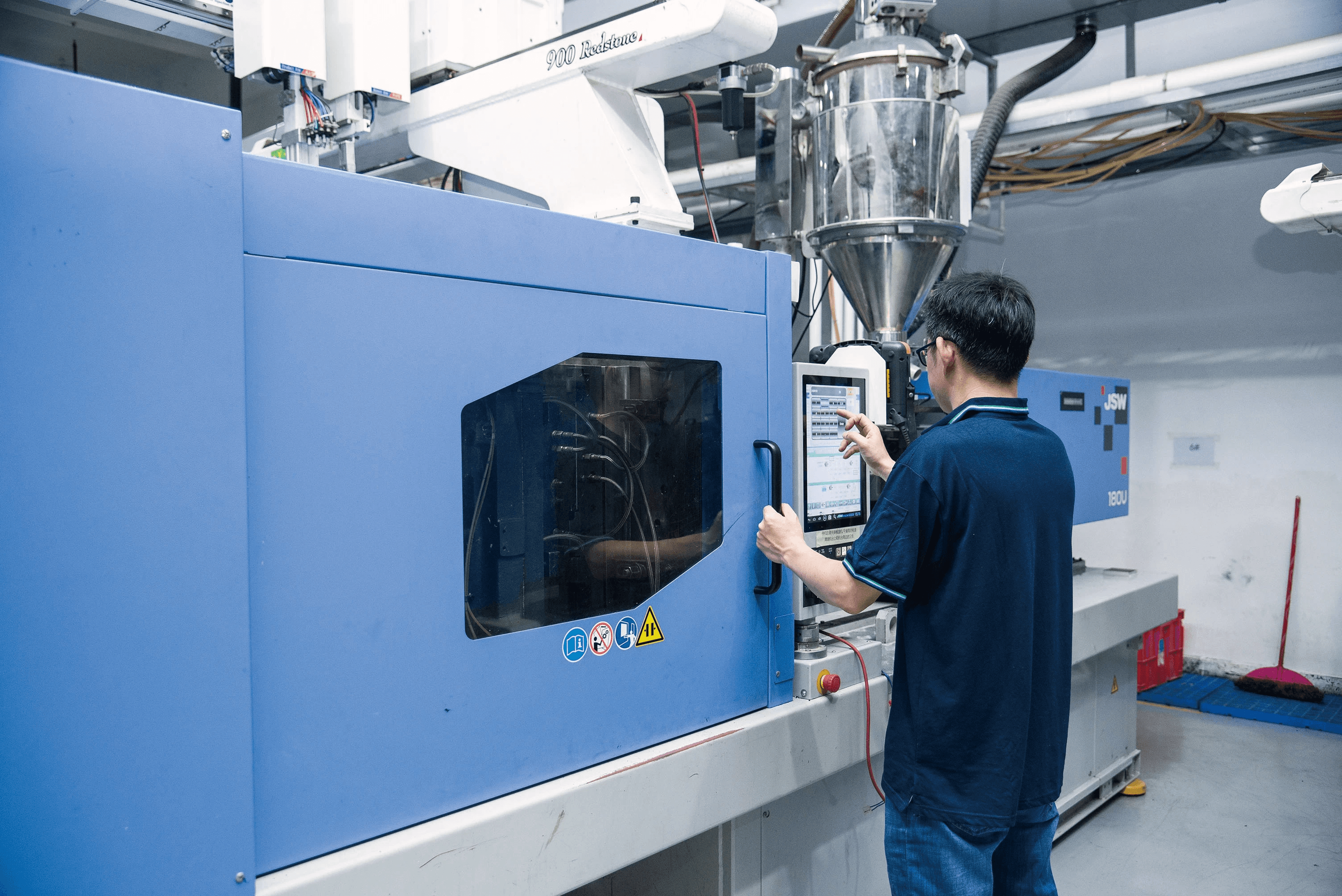
The injection molding process is a cornerstone of manufacturing, especially for producing clear injection molded plastics. This technique involves injecting molten plastic into a mold to create precise shapes and designs, making it an ideal choice for various applications. Understanding the fundamentals of this process helps businesses leverage plastic injection molding services effectively.
The Basics of Plastic Injection Molding
At its core, plastic injection molding is about transforming raw plastic materials into usable products through heat and pressure. The process begins with heating the chosen thermoplastic, such as acrylic plastic or polypropylene plastic, until it becomes molten. Once liquefied, this material is injected into a mold cavity where it cools and solidifies to form the final product.
The beauty of using clear injection molded plastics lies in their versatility; they can be molded into complex shapes while maintaining transparency and strength. This method not only allows for high-volume production but also ensures consistency in quality across batches. As a result, industries ranging from automotive to consumer goods benefit from the efficiency and reliability that plastic injection molding offers.
Key Equipment Used in the Process
To execute effective plastic injection molding, several key pieces of equipment are essential. The primary machine used is the injection molding machine itself, which consists of an injector unit and a clamping unit; these work together to heat and inject the molten plastic into molds. Other important components include temperature control systems to maintain optimal processing conditions and cooling systems that help solidify the injected material quickly.
Molds are another critical aspect; they are custom-designed for specific products made from various types of injection moldable plastics like acrylic or polypropylene plastic. Additionally, auxiliary equipment such as grinders for recycling scrap material or robots for automation can enhance production capabilities further. Investing in high-quality machinery ensures that an injection molding company can produce clear injection molded plastics efficiently while minimizing waste.
Role of an Injection Molding Company
An experienced injection molding company plays a vital role in bringing ideas to life through clear injection molded plastics. These companies not only manage the entire production process but also provide valuable expertise in material selection and design optimization tailored to client needs. By partnering with skilled professionals who specialize in plastic injection molding services, businesses can ensure their products meet industry standards while achieving cost-effectiveness.
Moreover, these companies often assist clients from concept development through prototyping and mass production stages—making them indispensable allies in product development cycles. They also focus on quality assurance practices to guarantee that every batch meets strict specifications while maintaining transparency that helps build trust with customers. Ultimately, choosing the right injection molding partner can significantly influence project success by ensuring timely delivery without compromising on quality.
Types of Clear Injection Moldable Plastics
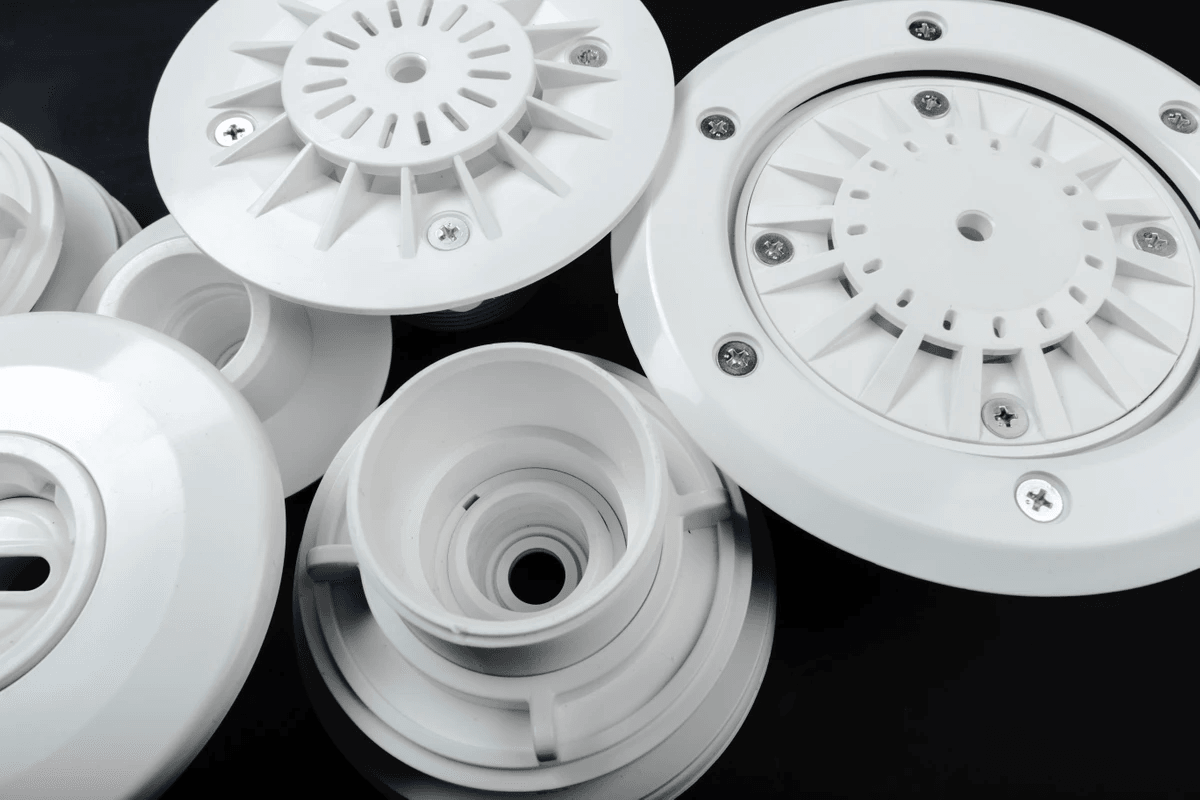
Acrylic Plastic Explained
Acrylic plastic, often known by its trade names like Plexiglas or Lucite, is a popular choice in the world of clear injection molded plastics. This material boasts exceptional clarity and can be manufactured to mimic glass, making it an ideal candidate for applications where transparency is essential. Additionally, acrylic is lightweight yet surprisingly durable, offering a combination that makes it suitable for everything from display cases to automotive parts.
One of the standout features of acrylic plastic is its excellent weather resistance, which allows it to maintain clarity even when exposed to UV light over time. This characteristic makes it a preferred choice for outdoor applications such as signage and lighting fixtures. Furthermore, acrylic can be easily colored or treated with coatings to enhance its aesthetic appeal while retaining its impressive transparency.
In terms of processing, acrylic can be seamlessly integrated into various plastic injection molding processes thanks to its excellent flow characteristics during molding. This adaptability ensures that manufacturers can produce intricate designs without sacrificing quality or clarity in their products. For those seeking reliable plastic injection molding services, acrylic remains a top contender in the realm of clear plastics.
Polypropylene Plastic Characteristics
Polypropylene plastic is another noteworthy material within the category of clear injection molded plastics that deserves attention. Known for its versatility and chemical resistance, polypropylene offers a unique balance between durability and flexibility that many industries find appealing. While typically not as transparent as acrylic, advancements in processing techniques have allowed for clearer grades that still retain many benefits associated with this robust polymer.
One significant advantage of polypropylene lies in its low density compared to other plastics; this means lighter components without compromising strength or performance. It also exhibits excellent fatigue resistance—making it ideal for applications requiring repeated flexing or bending without breaking down over time. Industries such as automotive and consumer goods frequently utilize polypropylene due to these beneficial characteristics.
Moreover, when considering an injection molding company for your project needs involving polypropylene plastic, it's essential to ensure they have experience with this material's specific requirements during production processes. Proper temperature control and mold design are critical factors that influence the final outcome when working with polypropylene in clear injection molded plastics applications.
Other Popular Injection Moldable Plastics
Beyond acrylic and polypropylene lies a treasure trove of other popular injection moldable plastics worth exploring in your quest for suitable materials. For instance, polycarbonate stands out due to its remarkable impact resistance—making it nearly unbreakable compared to glass alternatives while still offering high levels of transparency similar to acrylics or polypropylenes.
Another noteworthy option includes polystyrene—a lightweight thermoplastic known primarily for its clarity but also appreciated for ease during processing within an injection molding setup. Polystyrene’s affordability makes it particularly attractive among manufacturers looking at mass production without sacrificing quality standards associated with clear products.
Lastly, consider using PETG (glycol-modified polyethylene terephthalate) if you're searching specifically within high-performance categories; this material combines outstanding transparency with superior chemical resistance—ideal not just aesthetically but functionally too! As you evaluate your choices among different types of clear injection molded plastics available today through various plastic injection molding services providers—the possibilities are virtually limitless!
Advantages of Using Clear Injection Molded Plastics
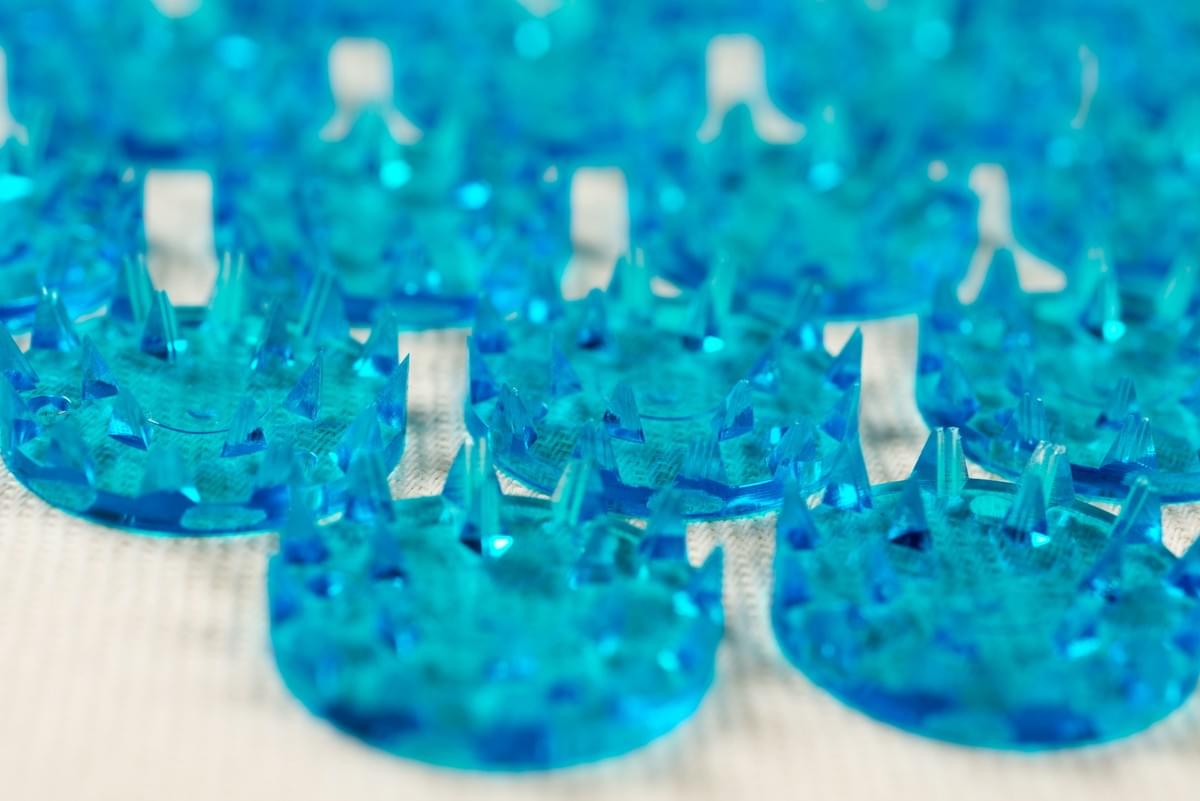
Clear injection molded plastics have gained significant traction in various industries due to their unique advantages. These materials not only enhance product aesthetics but also offer durability and cost-effective manufacturing solutions. By understanding these benefits, businesses can make informed choices when selecting plastic injection molding services for their projects.
Transparency and Aesthetic Appeal
One of the standout features of clear injection molded plastics is their exceptional transparency, which allows for vibrant colors and intricate designs to shine through. This aesthetic appeal makes them a preferred choice for consumer products, packaging, and display items where visibility is crucial. Whether it's acrylic plastic or other types of injection moldable plastics, the ability to see through the material adds a layer of sophistication that can elevate any design.
Moreover, the clarity of these materials can enhance branding efforts; products that showcase their contents often attract more attention on shelves or online marketplaces. By utilizing clear injection molded plastics, companies can create visually appealing products that resonate with consumers' desires for quality and style. This combination of beauty and functionality makes clear plastics an excellent choice across various applications.
Durability and Resistance to Impact
Durability is another compelling advantage of clear injection molded plastics, which are engineered to withstand wear and tear in demanding environments. Materials like polypropylene plastic are known for their impressive resistance to impact, ensuring that products remain intact even under stress or accidental drops. This resilience not only protects the integrity of the product but also contributes to customer satisfaction by reducing the likelihood of returns due to damage.
In addition to impact resistance, many clear injection molded plastics exhibit excellent weatherability, making them suitable for both indoor and outdoor applications. Their ability to maintain clarity over time without yellowing or becoming brittle enhances their appeal in long-term usage scenarios such as lighting fixtures or outdoor signage. Choosing durable materials from a reputable injection molding company ensures that your products will stand the test of time while maintaining their aesthetic qualities.
Cost-Effectiveness for Mass Production
When it comes to mass production, clear injection molded plastics shine as a cost-effective solution compared to other manufacturing methods. The efficiency of plastic injection molding allows companies to produce large volumes quickly without sacrificing quality or precision in each piece produced. This scalability means businesses can meet demand without incurring excessive costs while still enjoying high-quality results.
Additionally, using advanced techniques within plastic injection molding services helps minimize waste during production processes—an essential factor in keeping costs low while promoting sustainability practices within manufacturing industries. Lower material costs combined with reduced labor expenses make clear injection molded plastics an attractive option for companies looking to optimize their budgets while delivering top-notch products on time.
In summary, embracing the advantages offered by clear injection molded plastics—such as transparency, durability, and cost-effectiveness—can significantly benefit businesses across multiple sectors seeking reliable solutions tailored to modern consumer needs.
Choosing the Right Plastic Injection Molding Services
Selecting the right plastic injection molding services can make or break your project, especially when working with clear injection molded plastics. With so many providers out there, it's essential to weigh various factors that can influence your decision. From material expertise to production capabilities, understanding what each injection molding company offers is crucial for achieving desired results.
Factors to Consider When Selecting a Provider
When choosing a provider for plastic injection molding, consider their experience with different types of injection moldable plastics, including acrylic plastic and polypropylene plastic. The company's track record in producing high-quality clear injection molded plastics should be a top priority; after all, you want your final product to shine both literally and figuratively! Additionally, evaluate their technological capabilities—advanced machinery can significantly enhance precision and efficiency in the production process.
Another important factor is customer service; a responsive team that communicates well can ease the entire process from design to delivery. Don't forget about scalability—can they handle both small-scale prototypes and large-volume mass production? Lastly, check for certifications or quality standards that ensure consistency in their output; after all, nobody wants surprises when it comes to product quality.
Baoyuan: A Leader in Plastic Injection Molding
Baoyuan stands out as a leader in plastic injection molding services due to its commitment to innovation and excellence in producing clear injection molded plastics. With years of experience under their belt, they have honed their skills in working with various materials like acrylic plastic and polypropylene plastic while maintaining high standards of quality control. Their advanced machinery and skilled workforce enable them to tackle complex designs and deliver outstanding results every time.
Moreover, Baoyuan offers customized solutions tailored specifically to meet the unique needs of each client—whether you're looking for intricate designs or simple components, they’ve got you covered! Their dedication doesn't stop at just delivering products; they also prioritize customer satisfaction through transparent communication throughout the entire process. If you're on the hunt for reliable plastic injection molding services that don’t compromise on quality or service, Baoyuan should be at the top of your list.
Importance of Quality Assurance in Production
Quality assurance plays a pivotal role in ensuring that your clear injection molded plastics meet industry standards and customer expectations. A robust quality assurance program checks every stage of production—from material selection (like acrylic plastic or polypropylene plastic) through final inspection—to ensure consistency and reliability across batches. This not only minimizes defects but also builds trust between you and your chosen injection molding company.
Moreover, investing time into understanding how a provider implements quality control measures can save you headaches down the line; no one wants to deal with costly reworks or delays due to subpar products! Regular audits and testing help maintain high-quality output while adhering to safety regulations—a must-have consideration when selecting any provider for your plastic injection needs.
In conclusion, choosing the right provider for your clear injection molded plastics requires careful consideration of various factors including experience with materials like acrylics or polypropylenes as well as commitment towards quality assurance practices. By keeping these elements front-of-mind during your search for an ideal partner in plastic injection molding services—you’ll be well on your way toward achieving successful outcomes!
Innovations in Clear Injection Molding
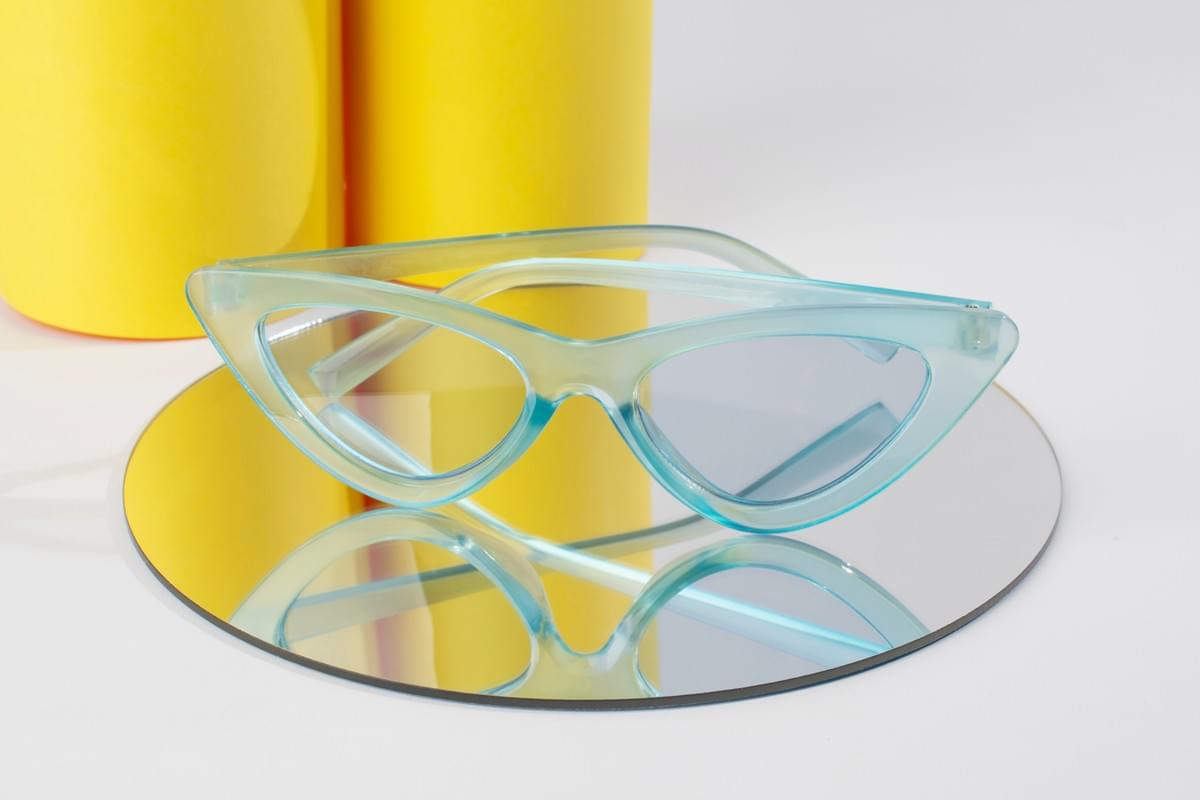
The world of clear injection molded plastics is continually evolving, driven by technological advancements and creative design trends. These innovations not only enhance the quality and efficiency of plastic injection molding but also open up new possibilities for applications across various industries. As companies seek to improve their offerings, staying updated on these innovations becomes essential for anyone involved in the plastic injection molding services sector.
New Technologies Influencing the Industry
Recent developments in technology have significantly transformed the landscape of plastic injection molding. For instance, advancements in 3D printing techniques allow for rapid prototyping of molds, reducing lead times and costs associated with traditional mold-making processes. Additionally, smart manufacturing technologies—such as IoT-enabled machines—are being integrated into injection molding companies, enabling real-time monitoring and optimization of production processes to ensure high-quality output of acrylic plastic and other injection moldable plastics.
Moreover, innovative materials are emerging that enhance the properties of clear injection molded plastics. For example, blends that incorporate polypropylene plastic with other polymers can result in improved strength and flexibility without compromising transparency. Such breakthroughs are crucial for industries requiring durable yet visually appealing products.
Trends in Design and Customization
As consumer preferences evolve, so do design trends within the realm of clear injection molded plastics. There is a growing demand for customized solutions that cater to specific aesthetic and functional requirements while maintaining clarity and durability. This trend has led many manufacturers to offer personalized services that allow clients to tailor their products from color choices to intricate designs using advanced software tools.
Another notable trend is the integration of multi-functional features into designs made from acrylic plastic or polypropylene plastic. For instance, designers are increasingly incorporating elements like built-in lighting or unique textures into their products to create eye-catching displays or functional items that stand out in a crowded market. This level of customization not only enhances product appeal but also fosters brand loyalty among consumers who value unique offerings.
Environmental Considerations in Plastic Production
With growing awareness around environmental sustainability, innovations in clear injection molded plastics are also focusing on eco-friendly practices within the industry. Many companies are now exploring biodegradable materials or recycled content options when producing injection moldable plastics to minimize environmental impact while still meeting performance standards required by consumers and businesses alike.
Additionally, advancements in energy-efficient machinery are helping reduce waste during the production process itself—a win-win scenario for both manufacturers and Mother Earth! Companies offering plastic injection molding services are increasingly adopting these technologies as part of their commitment to sustainability while ensuring they deliver high-quality products made from materials like acrylic plastic or polypropylene plastic.
Furthermore, regulatory changes aimed at reducing single-use plastics have prompted innovation within this space as well; manufacturers are now tasked with creating more sustainable alternatives without sacrificing performance or clarity inherent in clear injection molded plastics.
Conclusion
Clear injection molded plastics have carved a niche in various industries, and their future looks bright. With advancements in technology and increasing demand for transparency and durability, these materials are expected to evolve further. As manufacturers continue to innovate, clear injection molded plastics will likely see broader applications across sectors.
The Future of Clear Injection Molded Plastics
The future of clear injection molded plastics is promising, driven by ongoing innovations in plastic injection molding techniques. Companies are investing in research and development to enhance the properties of materials like acrylic plastic and polypropylene plastic, making them more versatile for different applications. Additionally, sustainability initiatives are pushing the industry towards eco-friendly alternatives that maintain the clarity and strength consumers expect.
Why Clear Plastics Are a Preferred Choice
Clear plastics stand out for their aesthetic appeal, combining transparency with durability that many other materials simply cannot match. The ability to mold complex shapes while retaining visual clarity makes clear injection molded plastics an attractive choice for designers and engineers alike. Furthermore, their cost-effectiveness in mass production means businesses can achieve high-quality results without breaking the bank—an enticing prospect for any company looking to optimize its manufacturing process.
Finding Reliable Plastic Injection Molding Solutions
When searching for reliable plastic injection molding services, it's essential to consider factors such as experience, technology used, and quality assurance practices employed by the injection molding company. A well-established provider will have a track record of delivering high-quality products using advanced techniques suitable for various types of injection moldable plastics like acrylic plastic and polypropylene plastic. By prioritizing these aspects when selecting a partner, businesses can ensure they receive the best possible solutions tailored to their unique needs.