Introduction
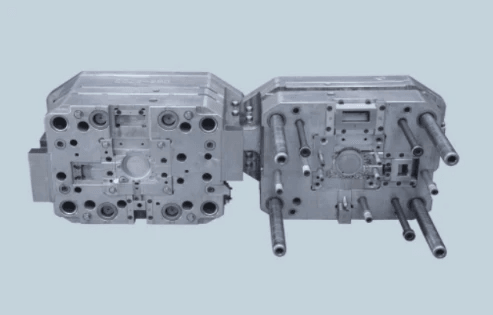
Injection molding is a widely used manufacturing process that allows for the efficient production of complex shapes and parts. However, one of the most persistent issues faced in this process is flash, a defect that can compromise both the quality and functionality of molded products. Understanding what causes flash in injection molding is crucial for manufacturers aiming to maintain high standards and reduce waste.
Understanding Flash in Injection Molding
Flash refers to the unwanted material that seeps out from between the mold halves during the injection molding process, creating thin, excess material along the edges of a part. This seemingly minor flaw can lead to significant problems if not addressed properly; it affects both aesthetics and structural integrity. By grasping how flash forms, manufacturers can better tackle its prevention and removal.
Importance of Identifying the Causes
Identifying what may cause flash to form is vital for effective troubleshooting and quality control in injection molding operations. High injection pressure, inadequate mold design, or unsuitable material choices are just a few factors that contribute to this defect. By pinpointing these root causes early on, companies can implement strategies on how to prevent flash in injection molding processes.
Overview of Injection Molding Flaws
Flash is just one among various flaws that can occur during injection molding; others include warping, sink marks, and short shots. Each defect presents unique challenges but understanding them collectively helps improve overall production efficiency. In this guide, we will delve deeper into why flash occurs and explore techniques for reducing flash in injection molding as well as effective troubleshooting methods.
Defining Flash in Injection Molding
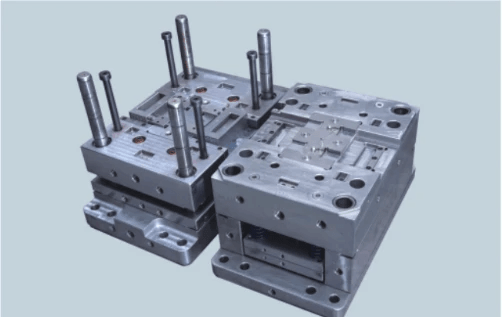
Understanding flash is crucial for anyone involved in the injection molding process. It refers to the unwanted excess material that seeps out of the mold cavity during production, leading to defects on the final product. Identifying what causes flash in injection molding is essential for maintaining product quality and optimizing manufacturing efficiency.
What is Injection Molding Flash?
Injection molding flash occurs when molten plastic escapes from the mold cavity, creating thin, unwanted projections at the parting line or other areas of a molded component. This defect can compromise both aesthetics and functionality, making it a significant concern for manufacturers. The reason for flash can often be traced back to issues such as high injection pressure or poor mold design.
Characteristics of Flash Defects
Flash defects are typically characterized by their thin, feather-like appearance along the edges of a molded part. They can vary in thickness and length but are usually noticeable enough to be deemed unacceptable by quality control standards. Understanding how to reduce flash in injection molding involves recognizing these characteristics early in the production process.
Flash vs. Other Molding Defects
While flash is one type of defect, it's essential to differentiate it from other common issues like warping or sink marks. Unlike these defects that often result from cooling problems or material shrinkage, flash primarily stems from excess material being forced out due to high pressure or poor mold fit. Knowing what may cause flash to form helps in pinpointing specific adjustments needed during production.
Common Causes of Flash Formation

Flash in injection molding can be a vexing issue for manufacturers, and understanding what causes flash in injection molding is crucial for maintaining quality. Identifying the root causes can help implement effective solutions, ensuring smooth production processes and high-quality outputs. Let's dive into some of the most common culprits behind this pesky defect.
High Injection Pressure and Speed
One of the primary reasons for flash formation is high injection pressure and speed during the molding process. When the pressure exceeds the mold's capacity, it forces molten material to escape through gaps between mold halves, resulting in unwanted flash. To combat this issue, manufacturers must carefully monitor injection parameters and consider how to reduce flash in injection molding by optimizing these settings.
High speeds can also lead to turbulence within the melt flow, increasing the likelihood of material leaking into areas where it shouldn't be. This not only contributes to flash but may also compromise part integrity and surface finish. By adjusting both pressure and speed, manufacturers can minimize these risks while enhancing overall product quality.
Improper Mold Design and Maintenance
Another significant factor that may cause flash to form is improper mold design or insufficient maintenance practices. If molds are not designed with adequate tolerances or alignment features, they can create gaps that allow excess material to escape during injection. Regular inspections are essential for identifying wear or damage that might exacerbate these issues.
Inadequate cooling channels or uneven temperature distribution can also lead to inconsistent solidification rates, further contributing to flash defects. Ensuring proper mold design paired with routine maintenance helps prevent these problems from arising in the first place—after all, prevention is better than cure when it comes to tackling what is the reason for flash?
Material Selection and Temperature Issues
The choice of materials used in injection molding plays a critical role in determining whether flash will occur during production runs. Certain polymers have specific flow characteristics; if selected incorrectly for a particular application or process setup, they may exacerbate flashing problems. Additionally, using materials that are too hot can increase viscosity loss leading to excessive flow.
Temperature management is equally important; if molds are too cold or too hot compared to optimal operating conditions, they may contribute to poor filling patterns which create additional risk for defects like flashing. By closely monitoring both material selection and temperature conditions throughout production processes, manufacturers can effectively address how to prevent flash in injection molding.
How to Prevent Flash in Injection Molding?
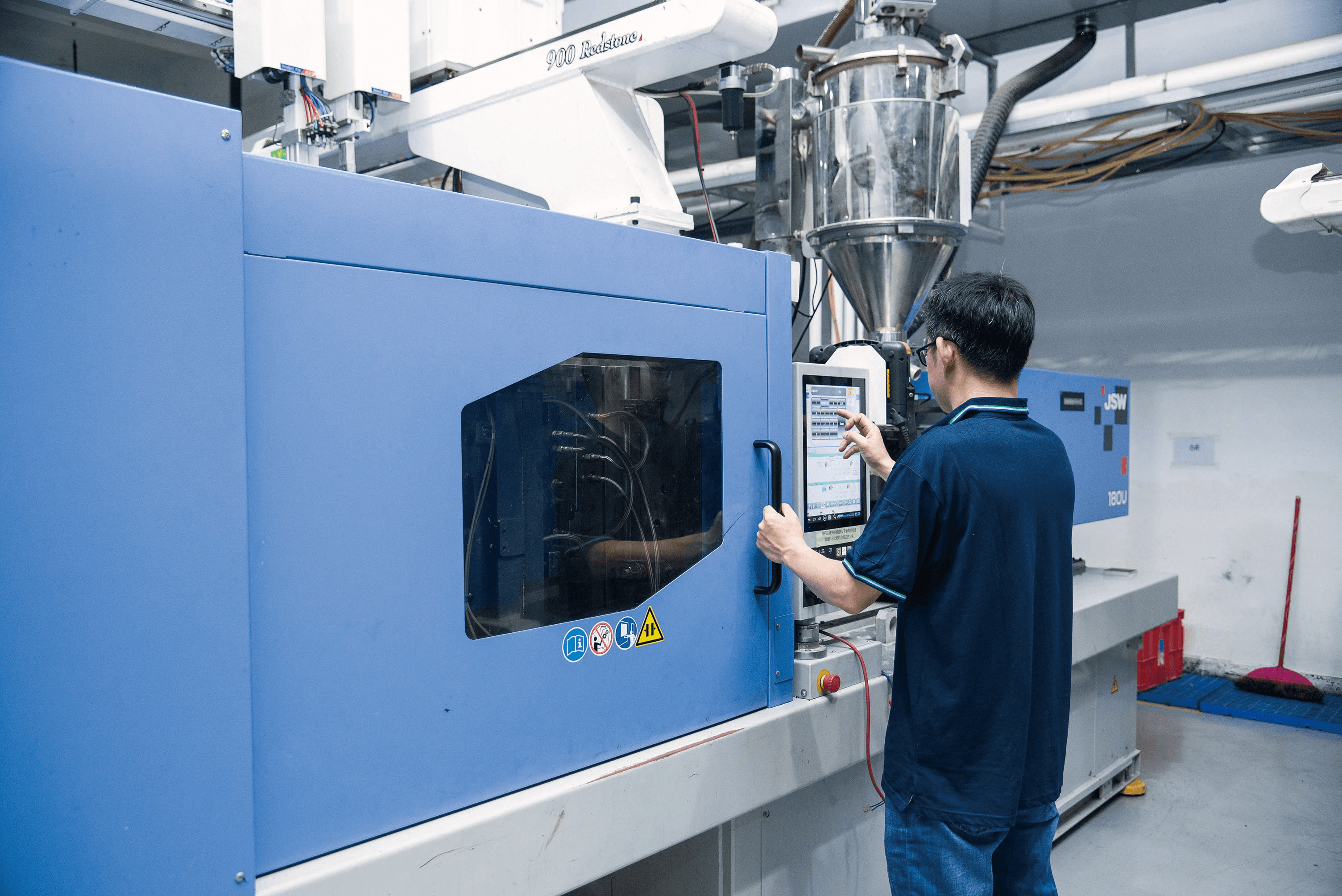
Preventing flash in injection molding is crucial for maintaining product quality and reducing waste. Understanding what causes flash in injection molding can help manufacturers implement effective strategies to minimize its occurrence. This section delves into the essential practices that can significantly reduce the risk of flash defects.
Optimizing Injection Parameters
One of the primary factors that contribute to flash formation is improper injection parameters. Adjusting the injection speed, pressure, and temperature can play a pivotal role in preventing flash defects. For instance, high injection pressure may lead to excessive material flow, which is often what causes flash in injection molding; therefore, fine-tuning these parameters can help mitigate this issue.
Additionally, slow and controlled injection speeds allow for better material distribution within the mold cavity. This not only reduces the chances of excess material escaping but also improves overall part quality. Understanding how to reduce flash in injection molding through optimized parameters will ultimately lead to more efficient production processes.
Regular Mold Maintenance and Inspection
Mold design plays a critical role in determining whether or not flash occurs during production runs. Regular maintenance and inspection of molds are vital steps toward identifying potential issues before they escalate into costly problems like flash defects. What may cause flash to form could be as simple as worn-out components or debris obstructing proper sealing.
Keeping molds clean and well-maintained ensures that they function optimally during each cycle, reducing the likelihood of material leakage at seams or edges where flash typically forms. Furthermore, routine inspections allow manufacturers to catch wear-and-tear early on, thereby preventing unexpected downtime due to mold repairs or replacements. By prioritizing mold maintenance, companies can effectively tackle one of the root causes of flashing.
Using Quality Materials and Additives
The choice of materials significantly impacts both product performance and defect rates like flashing. Using high-quality resins designed for specific applications can drastically reduce the chance of encountering what is known as an injection molding flash defect. Additionally, incorporating additives that enhance flow characteristics may help improve consistency during injections.
Selecting materials with appropriate thermal properties also minimizes temperature-related issues that might contribute to excessive expansion or contraction—common culprits behind unwanted flashes. Manufacturers should consider investing time into researching suitable materials tailored for their specific projects while keeping a close eye on how these choices affect overall production quality. Ultimately, using quality materials will be a game-changer when it comes to addressing what causes flash in injection molding.
Flash Molding Defect Troubleshooting
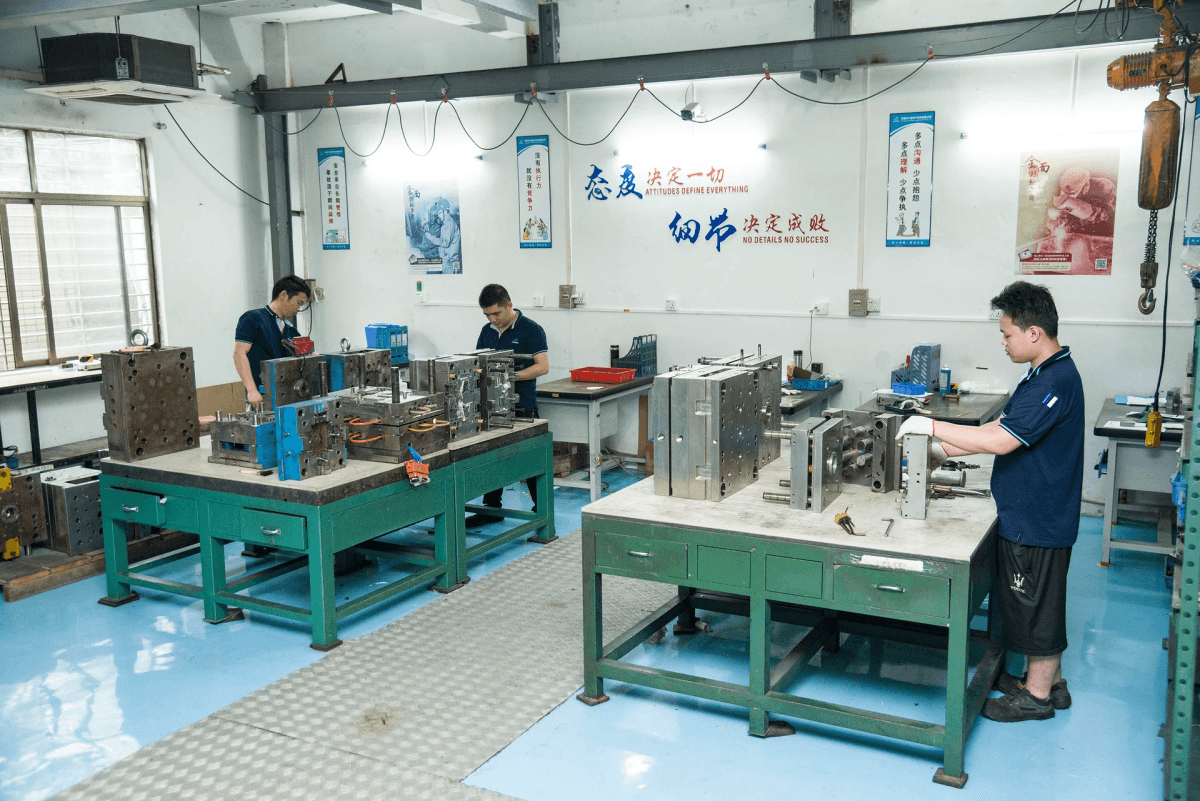
Troubleshooting flash defects in injection molding is crucial for ensuring product quality and operational efficiency. Understanding what causes flash in injection molding is the first step toward effective resolution. By identifying symptoms, diagnosing the root causes, and leveraging expert assistance, manufacturers can significantly reduce the incidence of flash defects.
Identifying Symptoms of Flash Defects
Recognizing the symptoms of flash defects is essential for timely intervention. Common indicators include excess material along the parting line or edges, which may appear as thin flaps or ridges on molded parts. Additionally, a visual inspection may reveal uneven surfaces or inconsistencies that signal what may cause flash to form during production.
In many cases, these symptoms become apparent during quality control checks or after parts have been ejected from the mold. Operators should remain vigilant for any signs of irregularities, as early detection can prevent further complications down the line. Ultimately, understanding how to prevent flash in injection molding begins with keen observation of these telltale signs.
Techniques for Diagnosing the Cause
Once symptoms are identified, it's time to dive into diagnosing the cause of flash defects. A systematic approach often involves reviewing injection parameters such as pressure and speed; high values can lead to excessive force that forces material into unwanted areas. Assessing mold design and maintenance practices also plays a vital role in uncovering potential flaws contributing to what is the reason for flash?
Another effective technique involves analyzing material selection and temperature settings; improper choices here can exacerbate issues related to flow dynamics within the mold cavity. Utilizing diagnostic tools like pressure sensors and thermal cameras can provide valuable insights into conditions during production runs. By understanding what may cause flash to form, manufacturers can implement targeted strategies for improvement.
Role of the Baoyuan Team in Troubleshooting
The Baoyuan team brings specialized knowledge and experience to tackle injection molding flash troubleshooting effectively. Their expertise allows them to quickly identify issues based on symptoms observed during production runs while providing insights into how to reduce flash in injection moulding processes overall. With a focus on collaboration with operators and engineers alike, they ensure that all aspects of manufacturing are considered.
In addition to hands-on support during troubleshooting sessions, Baoyuan offers training resources aimed at fostering a deeper understanding of common flashing issues within teams. They emphasize preventive measures alongside corrective actions—helping teams learn not just how to remove flash in injection molding but also how to avoid it altogether through best practices and ongoing education initiatives.
Ultimately, leveraging their skills leads not only to resolving immediate concerns but also enhances long-term operational efficiencies across manufacturing lines plagued by recurring flashes.
How to Remove Flash in Injection Molding?
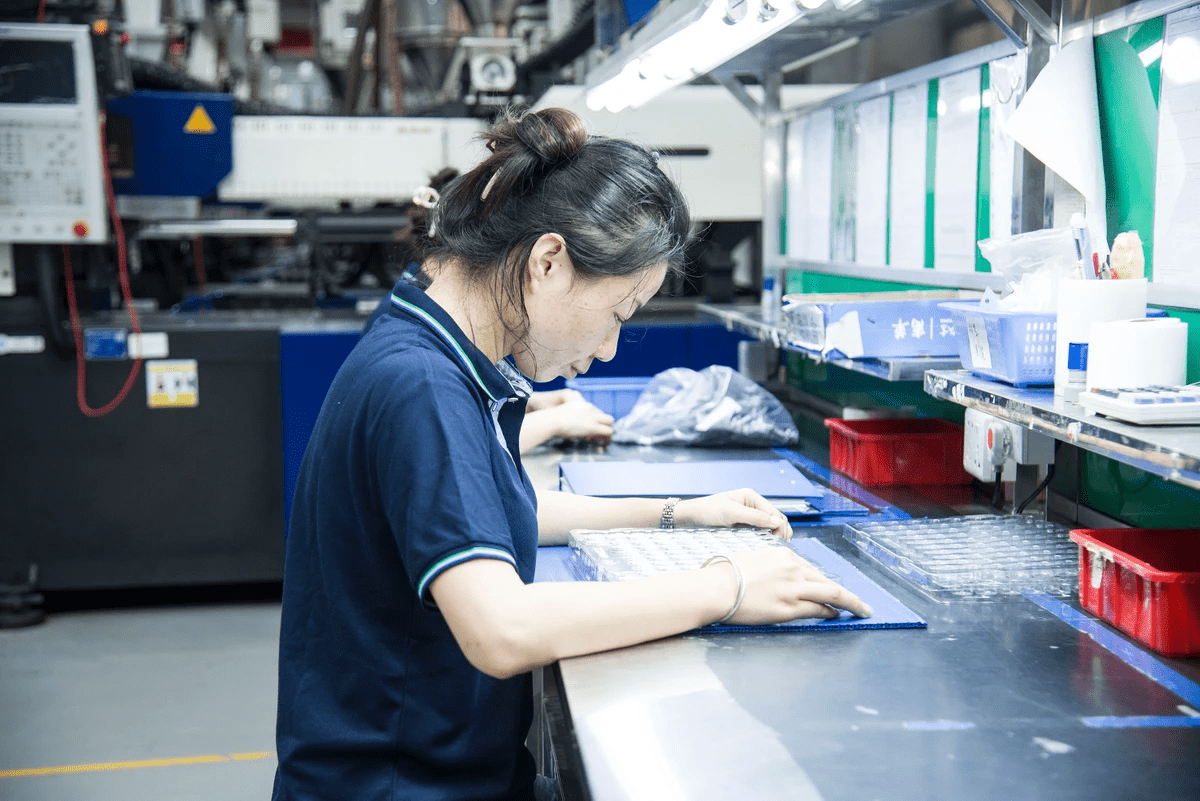
Removing flash from injection molded parts is a critical step in ensuring product quality and functionality. Flash not only affects the aesthetic appeal of the product but can also compromise its structural integrity. Understanding how to remove flash efficiently can save time, reduce costs, and improve overall production processes.
Manual vs. Automated Removal Techniques
Automated systems often utilize robotic arms or specialized machinery designed to handle flash removal efficiently, minimizing human error and enhancing safety on the production floor. The choice between manual and automated methods ultimately depends on factors like production volume, complexity of parts, and budget constraints. Regardless of the method chosen, knowing what causes flash in injection molding is essential for implementing effective removal strategies.
Best Practices for Flash Removal
To effectively tackle flash defects during manufacturing, it’s vital to follow best practices tailored to your specific operation. First off, always assess the part design and mold conditions; redesigning molds with better tolerances can prevent excessive material from escaping during injection molding processes—one of the main reasons for flash formation. Additionally, maintaining consistent temperature control throughout the process helps reduce thermal expansion issues that may lead to unwanted flashing.
Using proper tooling techniques during both molding and post-processing stages ensures that any residual material is removed without damaging the part itself—this ties back into understanding how to prevent flash in injection molding from occurring in the first place! Regular training sessions for staff on best practices will also enhance their ability to identify potential issues early on before they escalate into significant problems.
Importance of Post-Processing
Post-processing plays a crucial role in addressing any remaining imperfections after initial manufacturing steps are completed. This stage allows manufacturers not only to remove visible flash but also to perform additional finishing operations like sanding or polishing that enhance product quality further—after all, nobody wants a product marred by unsightly defects!
Moreover, post-processing provides an opportunity for quality checks where teams can evaluate whether previous steps adequately addressed what may cause flash to form initially; this feedback loop ensures continuous improvement within operations while reinforcing good practices among employees involved in injection molding processes.
In conclusion, understanding how to remove flash in injection molding effectively requires a combination of appropriate techniques and ongoing education about potential defect causes—like high pressures or improper mold designs—to truly minimize future occurrences of this pesky issue!
Conclusion
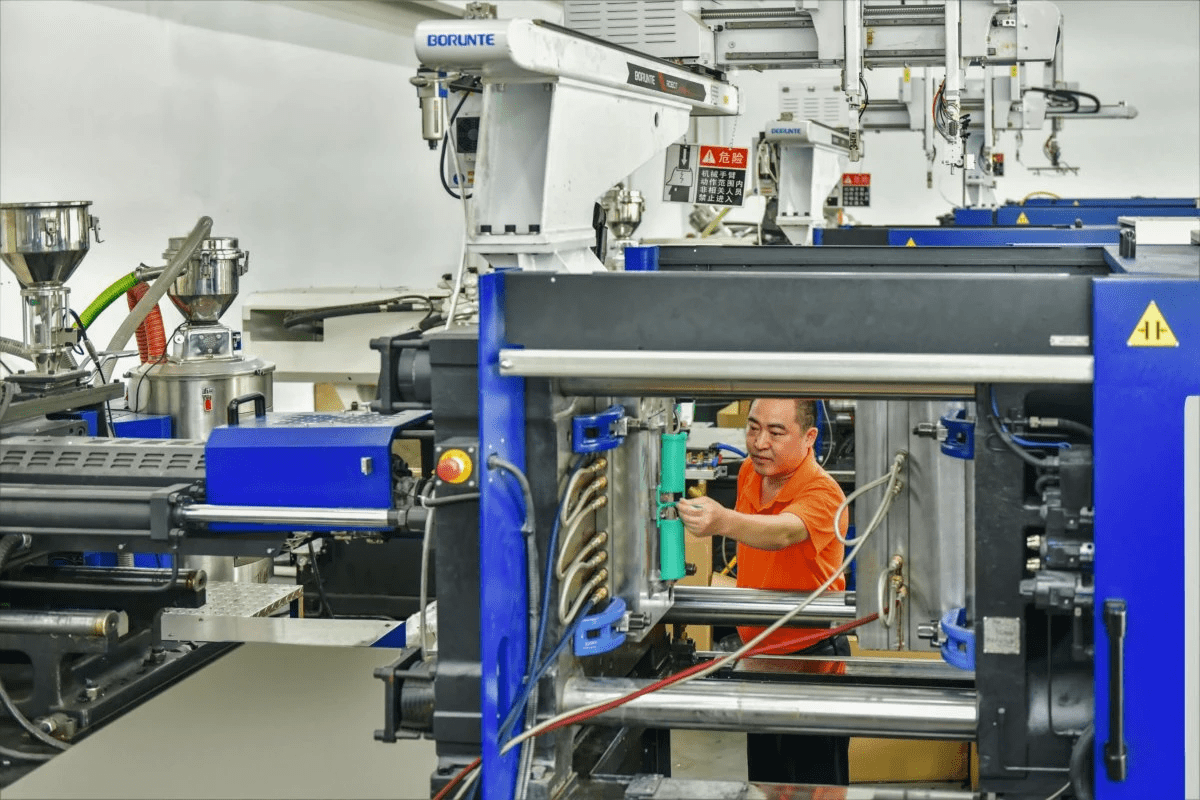
In the world of injection molding, understanding flash is crucial for maintaining product quality and operational efficiency. Flash defects can arise from various factors, including high injection pressure or improper mold design, leading to increased production costs and reduced customer satisfaction. By identifying what causes flash in injection molding, manufacturers can take proactive steps to improve their processes.
Key Takeaways on Flash Causes
Flash in injection molding typically occurs due to excessive pressure or speed during the injection process. Common reasons for flash include inadequate mold closure, wear and tear on molds, and material selection issues. Understanding these causes helps manufacturers pinpoint potential problems before they escalate into costly production delays.
Strategies for Prevention and Troubleshooting
To prevent flash in injection molding, it's vital to optimize injection parameters such as speed and pressure while ensuring proper mold design and maintenance. Regular inspections can help identify issues before they lead to defects, while choosing the right materials can further reduce the likelihood of flash formation. When troubleshooting flash molding defects, employing a systematic approach allows teams to diagnose problems effectively and implement corrective actions promptly.
Resources for Further Learning on Flash Defects
For those eager to dive deeper into the nuances of flash defects in injection molding, numerous resources are available online. Websites dedicated to manufacturing best practices often provide insights into what may cause flash to form and how to remove it efficiently. Additionally, industry forums and webinars offer valuable tips on how to reduce flash in injection moulding through shared experiences from professionals facing similar challenges.