Introduction
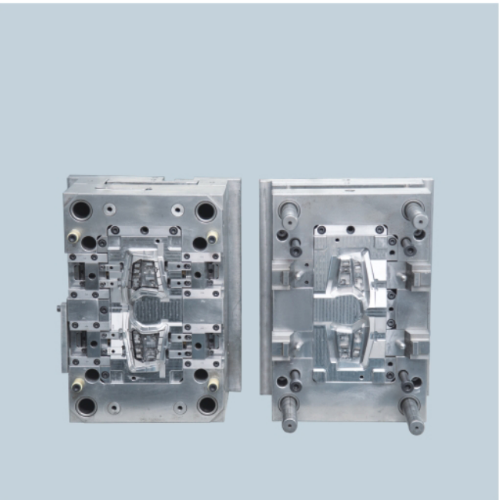
When it comes to injection molding, understanding the basics of injection molds is crucial. The components of an injection mold play a vital role in the overall process, and knowing their functions and importance is key to achieving successful outcomes. Whether you're new to the world of injection molding or looking to deepen your knowledge, delving into the parts of an injection mold will provide valuable insights into this intricate manufacturing process.
Understanding the Basics of Injection Molds
Injection mold components are the building blocks of a successful molding operation. From the mold base to the ejection system, each part plays a specific role in shaping and producing high-quality plastic products. By understanding the structure and function of these components, manufacturers can optimize their production processes and achieve superior results.
Exploring the 5 Components of an Injection Mold
The five main components of an injection mold include the mold base, cavities and cores, cooling systems, materials, and ejection systems. Each component serves a distinct purpose in ensuring that the molding process runs smoothly and efficiently. By exploring these components in detail, manufacturers can gain a deeper understanding of how each part contributes to the overall functionality of an injection mold.
Why Knowing the Parts of an Injection Mold Matters
Having a comprehensive knowledge of injection mold components is essential for several reasons. It enables manufacturers to make informed decisions about mold design, material selection, and production processes. Additionally, understanding these parts allows for better troubleshooting and maintenance practices, ultimately leading to improved productivity and cost-efficiency in manufacturing operations.
The Baoyuan Team's Expertise in Injection Mold Design
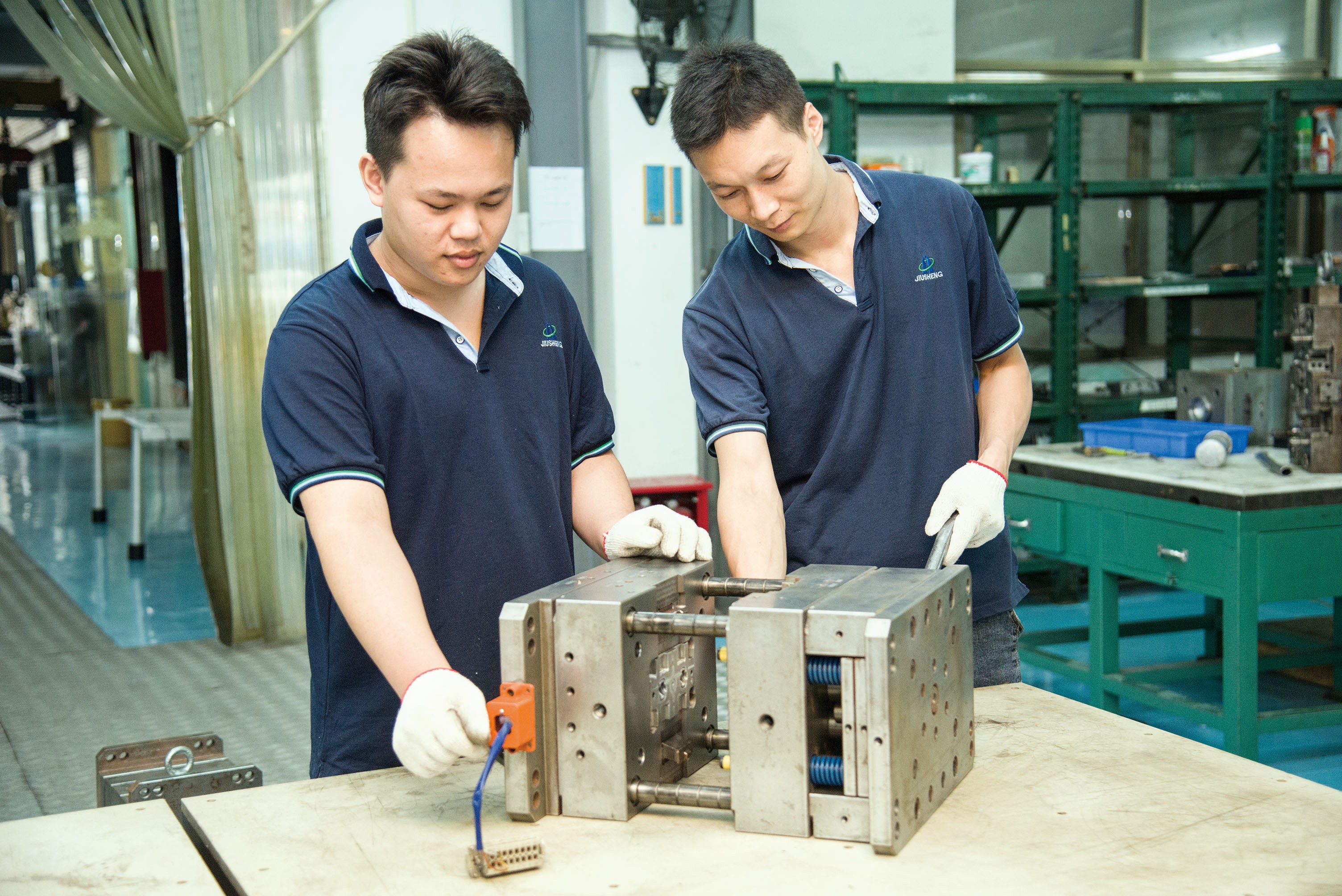
Baoyuan's team of experts is well-versed in the intricate parts of an injection mold, ensuring top-notch quality in every project. With a combination of seasoned senior management and technical personnel, they bring a wealth of experience to the table, guaranteeing precision and excellence in every aspect of injection mold design.
Baoyuan's Senior Management and Technical Personnel
The backbone of Baoyuan's success lies in its exceptional senior management and technical personnel. Their deep understanding of the components of an injection molding machine allows them to lead the team with expertise, ensuring that every project meets the highest standards. Their dedication to staying updated with the latest advancements in injection mold technology sets them apart as industry leaders.
Furthermore, Baoyuan's senior management and technical personnel are known for their ability to adapt to changing market demands and customer requirements. Their flexibility and agility in responding to new challenges ensure that the company remains at the forefront of innovation in injection mold technology. By consistently delivering cutting-edge solutions, they have built a reputation for being reliable and forward-thinking partners in the industry.
Baoyuan's Proficiency in Software for Mold Design
Baoyuan takes pride in its proficiency in utilizing cutting-edge software for mold design. This allows them to meticulously plan and execute each project, taking into account every part of an injection mold structure with precision. Their mastery of software ensures that their designs are not only innovative but also efficient, resulting in superior products for their clients.
Furthermore, Baoyuan's expertise in software for mold design allows them to easily adapt to any changes or modifications requested by their clients. This flexibility ensures that they can meet the specific needs of each project, providing customized solutions that go above and beyond expectations. By staying up-to-date with the latest advancements in software technology, Baoyuan remains at the forefront of mold design, setting them apart as industry leaders.
Baoyuan's Specialization in Single-color and Double-color Products
One area where Baoyuan truly excels is their specialization in single-color and double-color products. Their understanding of injection molding parts enables them to create seamless designs that meet even the most complex requirements. With a keen eye for detail and a commitment to excellence, they consistently deliver outstanding results that exceed expectations.
Baoyuan's expertise in single-color and double-color products is further enhanced by their use of advanced materials and cutting-edge technology. By staying abreast of the latest industry developments, they are able to offer innovative solutions that push the boundaries of what is possible in injection molding. This dedication to staying ahead of the curve ensures that Baoyuan remains a leader in their field, constantly raising the bar for quality and precision in their products.
The Core Components of an Injection Mold
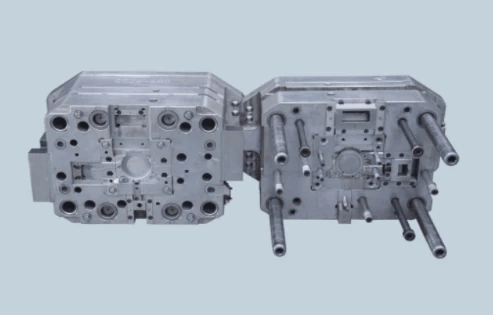
Understanding the Mold Base
The mold base is the foundation of an injection mold, providing support for all other components. It is typically made of steel and houses the various cavities, cores, and cooling channels. The design and construction of the mold base are crucial in ensuring the accuracy and precision of the final molded product.
The cavities and cores within the mold base are essential for shaping the final product. The cavities form the outer shape of the product, while the cores create internal features. These components work together to produce a precise and detailed mold. Proper maintenance of the cavities and cores is crucial to ensure consistent quality in the molded products.
Exploring the Cavities and Cores
Cavities and cores are the primary shaping components of an injection mold, creating the desired form and structure of the final product. The cavities form the outer shape, while the cores create internal features. These components must be meticulously designed and manufactured to achieve high-quality injection molding parts.
Cavities and cores are the primary shaping components of an injection mold, creating the desired form and structure of the final product. The cavities form the outer shape, while the cores create internal features. These components must be meticulously designed and manufactured to achieve high-quality injection molding parts.
The Role of Injection Mold Cooling Systems
Cooling systems play a critical role in maintaining consistent temperatures during the injection molding process, preventing warping or defects in the final product. They consist of intricate channels within the mold that allow for efficient heat dissipation. Properly designed cooling systems are essential for achieving precise and uniform injection molding parts.
By understanding these core components of an injection mold - including the mold base, cavities, cores, and cooling systems - manufacturers can optimize their designs for superior quality products.
The Importance of Injection Mold Materials
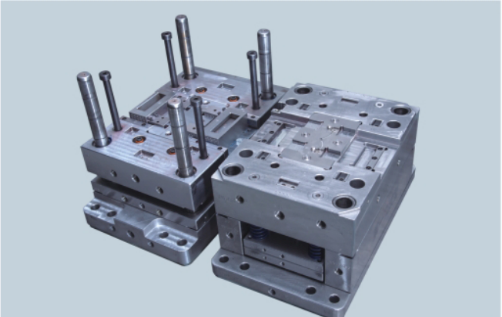
The Impact of Material Selection on Mold Performance
Selecting the right materials for injection molds is crucial to ensure optimal performance and durability. The choice of material can affect factors such as mold lifespan, resistance to wear and tear, and the ability to withstand high temperatures and pressures during the injection molding process. Additionally, the material selection can impact the surface finish of the molded parts, as well as the overall production cycle time. It's important to consider not only the mechanical properties of the material but also its ability to be polished and textured for specific design requirements.
Factors to Consider When Choosing Injection Mold Materials
When choosing materials for injection molds, factors such as thermal conductivity, hardness, corrosion resistance, and machinability must be carefully considered. It's essential to select materials that can withstand the demands of the specific molding application while maintaining dimensional stability and surface finish quality.
When choosing materials for injection molds, factors such as thermal conductivity, hardness, corrosion resistance, and machinability must be carefully considered. It's essential to select materials that can withstand the demands of the specific molding application while maintaining dimensional stability and surface finish quality. Additionally, the material's ability to resist wear and tear over time should be taken into account to ensure the longevity of the mold. Moreover, considering the cost-effectiveness of the material is crucial in optimizing production efficiency and minimizing expenses.
Baoyuan's Quality Assurance in Injection Mold Materials
At Baoyuan, we understand the critical role that material selection plays in ensuring top-notch mold performance. Our team meticulously selects high-quality materials with proven track records in injection molding applications. With our stringent quality assurance processes, clients can trust that our injection mold materials are of the highest standard.
The Functionality of Injection Mold Ejection Systems
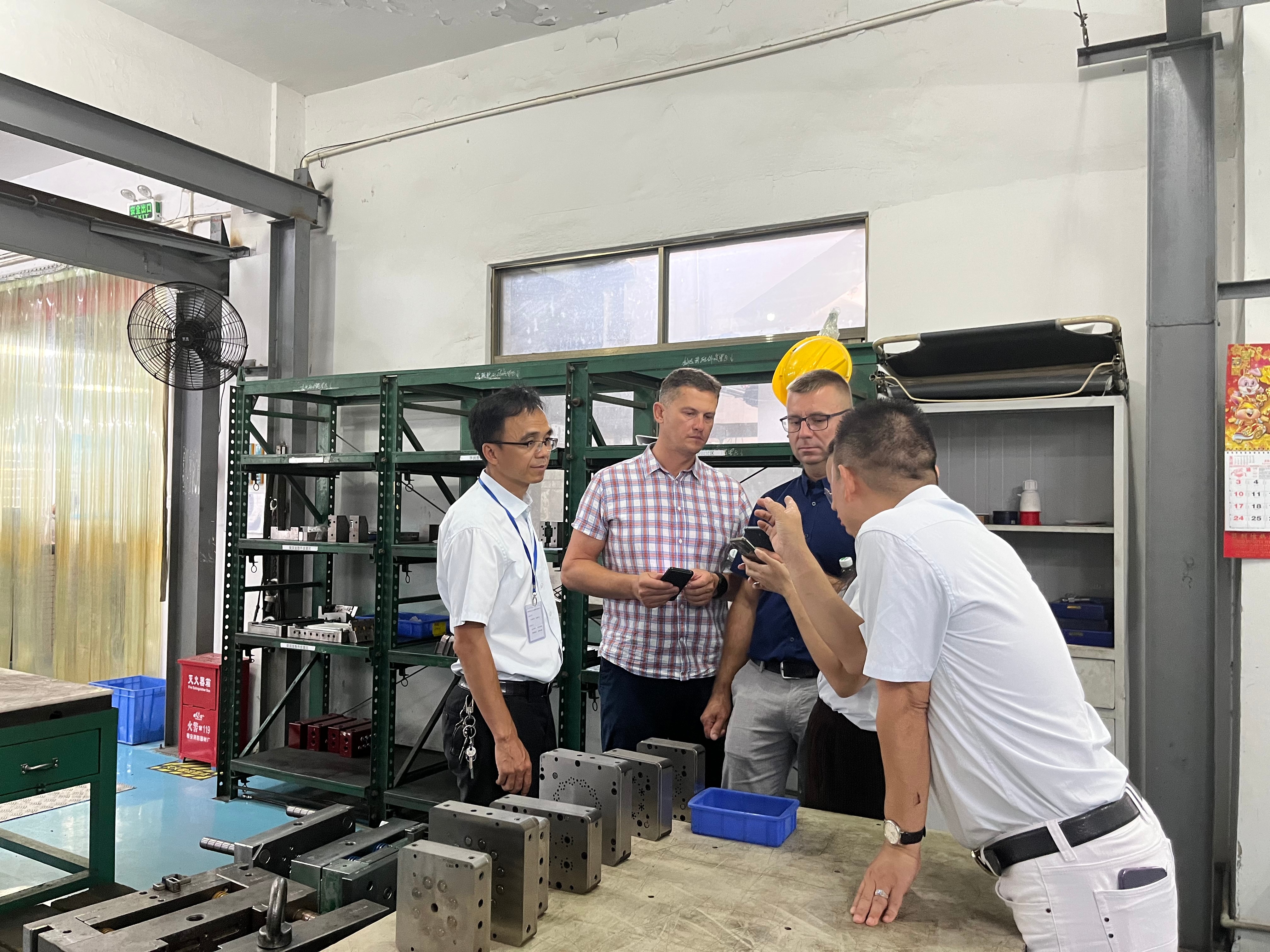
When it comes to injection mold ejection systems, they play a crucial role in the production process by pushing the finished part out of the mold cavity. This is achieved through the use of ejector pins or sleeves that are strategically positioned within the mold structure to ensure smooth and efficient part ejection.
How Ejection Systems Work in an Injection Mold
Ejection systems work by utilizing mechanical force to push the finished part out of the mold cavity once it has solidified. This is done either through a direct ejection system where pins are used to push the part out, or through an indirect ejection system where sleeves are utilized for a more controlled ejection process. Both methods are essential for ensuring that parts are ejected without any damage or distortion.
Common Types of Ejection Systems
Common types of ejection systems include pin ejection systems, stripper plate ejection systems, and sleeve ejectors. Pin ejection systems involve using ejector pins that are inserted into the mold base to push out the finished part. Stripper plate ejection systems utilize a plate that pushes against the part to release it from undercuts, while sleeve ejectors provide a more controlled and uniform ejection process.
Baoyuan's Expertise in Mold Opening Mechanisms
Baoyuan excels in designing and implementing efficient mold opening mechanisms that complement various types of injection molds. Their expertise lies in customizing ejection systems based on specific product requirements, ensuring smooth and precise part release while maintaining high productivity levels.
Achieving Precision with Injection Mold Guiding Systems
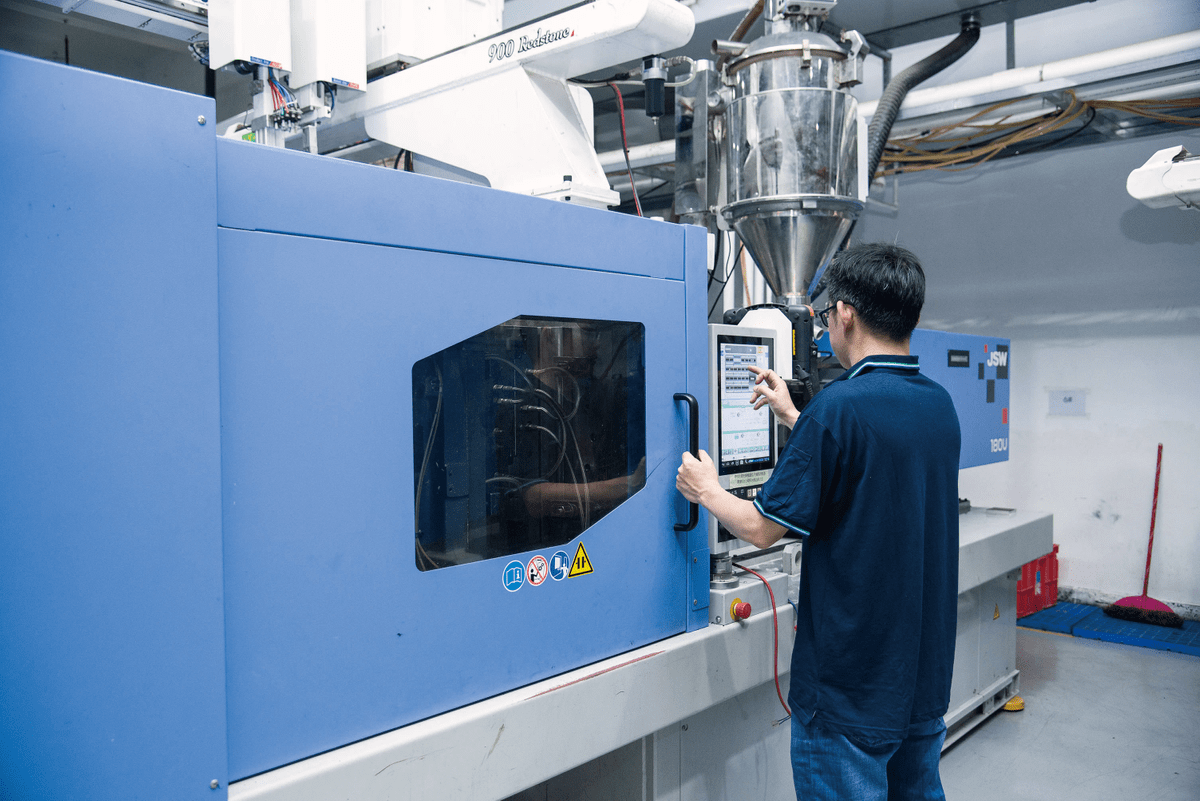
Understanding the Role of Guiding Systems
Injection mold guiding systems play a crucial role in ensuring the precise alignment and movement of mold components during the injection molding process. These systems help maintain the accuracy and consistency of the molded parts by guiding the opening and closing movements of the mold.
Different Types of Guiding Systems
There are various types of guiding systems used in injection molds, including pins, bushings, and slides. Each type serves a specific purpose in controlling the movement of mold components to achieve accurate part production. The selection of the guiding system depends on factors such as part complexity, material flow, and mold design requirements.
Baoyuan's Precision in Injection Mold Guiding
At Baoyuan, precision is at the core of our injection mold guiding systems. Our team meticulously designs and implements guiding systems that ensure optimal alignment and movement, resulting in high-quality molded parts with tight tolerances. With our expertise, clients can trust that their injection molding projects will benefit from superior precision and consistency.
Conclusion
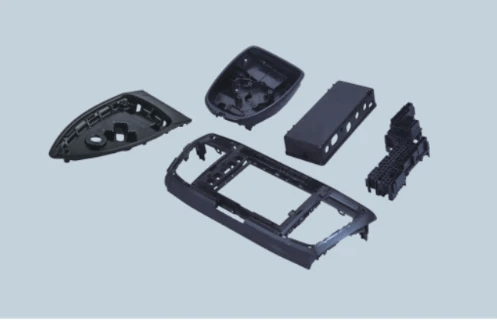
Mastering the Basics of Injection Mold Components
Understanding the intricacies of the parts of an injection mold is crucial for successful mold design and production. From the mold base to the ejection systems, each component plays a vital role in creating high-quality injection molding parts.
Key Considerations for Injection Mold Design
When designing an injection mold, it's essential to consider factors such as material selection, guiding systems, and ejection mechanisms. These elements directly impact the functionality and precision of the mold, ultimately affecting the quality of the final product.
Partnering with Baoyuan for Superior Injection Molding Solutions
Baoyuan's expertise in injection mold design and production makes them the ideal partner for achieving superior results. With a team proficient in software for mold design and specialization in single-color and double-color products, Baoyuan delivers top-notch injection molding solutions.