Introduction
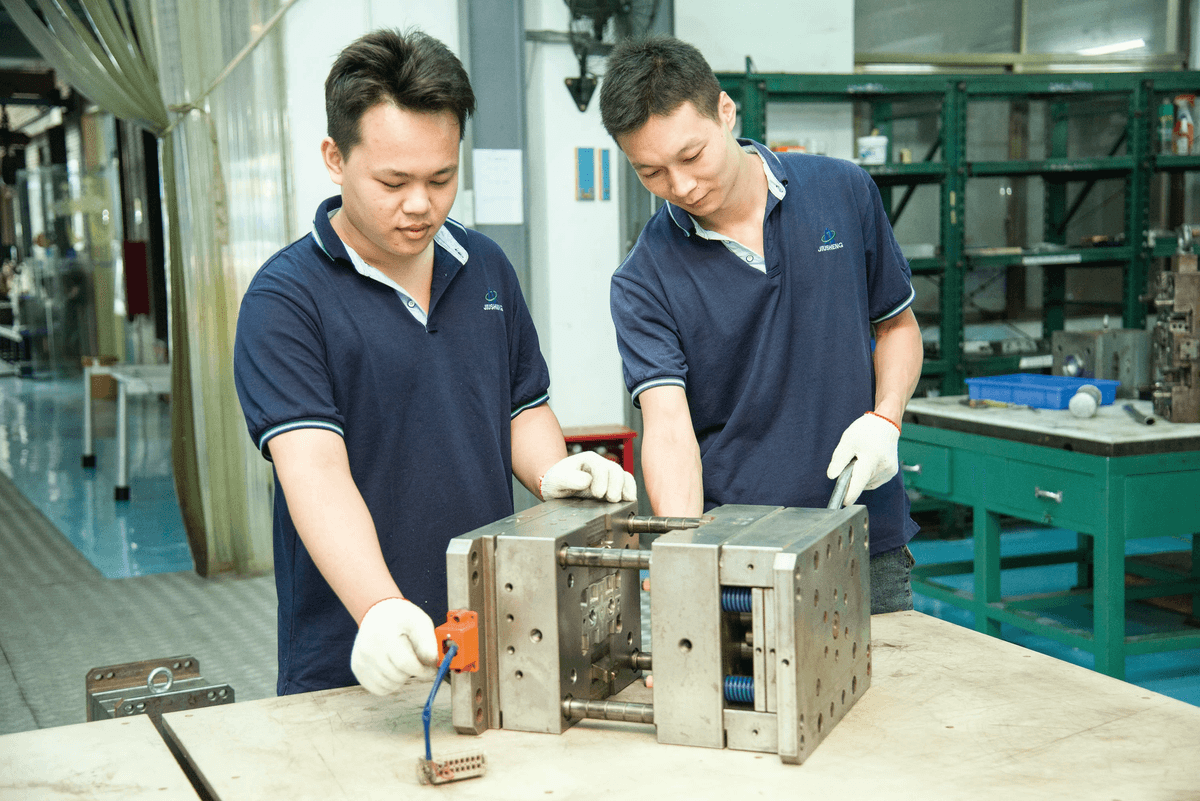
Are you looking to improve your injection molding process? Look no further than two-shot injection molding! This innovative technique creates complex, multi-material parts in a single operation, revolutionizing the manufacturing industry. Let's explore its countless advantages and examples.
Understanding
Two-Shot Injection Molding
Two-shot injection molding, also known as two-shot or two-shot molding, is a manufacturing process that enables the production of intricate parts by injecting two different materials into a single mold. This method opens up endless possibilities for creating products with varying colors, textures, and properties in one seamless operation.
Advantages of
Two-Shot Molding
Two-shot injection molding offers a multitude of benefits that revolutionize the production process. Here's a closer look at its advantages:
- Streamlined Production: By eliminating the need for multiple operations and assembly, two-shot injection molding significantly reduces production time and complexity.
- Reduced Material Waste: This technique minimizes material waste by efficiently using two different materials in a single molding process.
- Cost-Effectiveness: Combining streamlined production and reduced waste reduces production costs.
- Enhanced Durability and Aesthetics: Two-shot injection molding allows for creating products with superior strength, visual appeal, and intricate designs.
Two-shot injection molding offers a compelling combination of efficiency, cost-effectiveness, and superior product quality, making it a valuable asset for manufacturers across various industries.
Exploring
Two-Shot Injection Molding Examples
Two-shot molding has made its mark across various industries, from automotive components to consumer electronics. Think of dual-color buttons on remote controls or soft-grip handles with hard plastic cores—these are just a few examples of how two-shot injection molding has transformed product design and functionality.
The Basics of Two-Shot Injection Molding
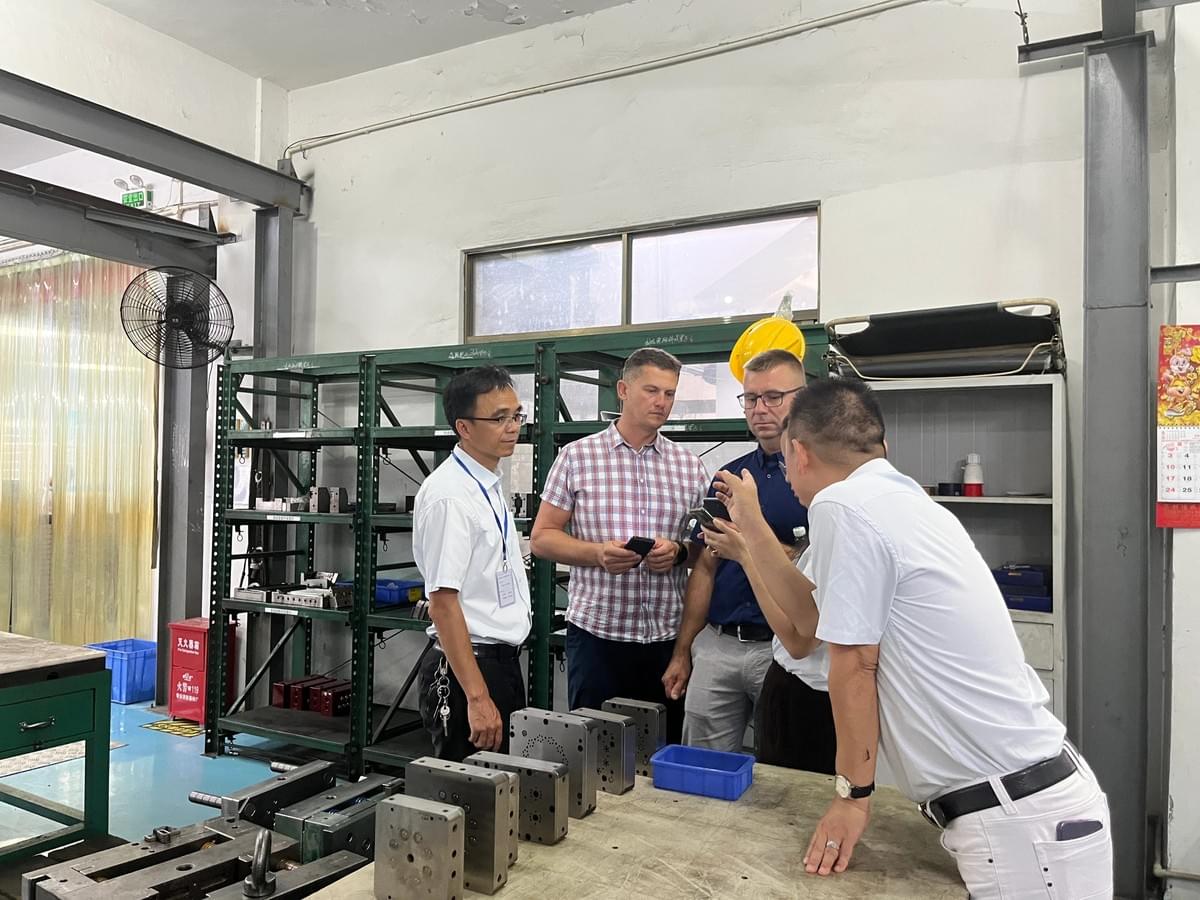
Two-shot injection or two-shot molding is a manufacturing process combining two different materials into one part. This innovative technique allows for creating complex and unique designs that would be difficult to achieve with traditional injection molding methods.
Understanding the Process
The sequential injection molding process creates strong, visually appealing, multi-functional parts in a single step. Here's how it works:
- Material Injection: The first material is injected into the mold.
- Mold Rotation/Movement: The mold is rotated or moved to allow for the injection of the second material.
- Cooling and Solidification: After both materials are injected, the mold is cooled, solidifying the materials and forming a strong bond between them.
This innovative technique eliminates the need for multiple parts and complex assembly processes, resulting in seamless, high-quality products with minimal finishing work. Sequential injection molding allows for intricate designs with varying textures and colors, and the combination of materials enhances functionality, making it suitable for a wide range of applications.
Key Components of
Two-Shot Molding
Key components of two-shot molding include a specialized tooling system that enables the precise placement and injection of each material. Additionally, specialized injection molding machines are required to carry out this intricate process effectively.
The specialized tooling system in two-shot molding allows for the precise placement and injection of each material, ensuring that the final product meets the required specifications. This level of precision is crucial in creating complex and intricate designs that require multiple materials to be molded together seamlessly. Without this specialized tooling system, achieving such high levels of accuracy would be nearly impossible.
Benefits of
Two-Shot Injection Molding
The benefits of two-shot injection molding are significant, including reduced production costs, improved part quality, enhanced design flexibility, and increased productivity. Manufacturers can streamline production by eliminating secondary operations and assembly processes and reducing lead times.
With its ability to produce complex parts with multiple materials in a single operation, two-shot injection molding is revolutionizing the manufacturing industry and opening up new possibilities for product design and development.
Two-Shot Injection Molding Techniques
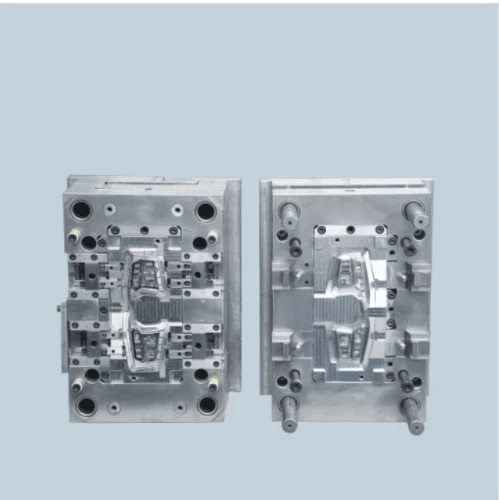
Overmolding
Overmolding is a two-shot molding process where one material is molded over another to create a single part. This technique commonly adds soft-touch grips or ergonomic features to products, providing functionality and aesthetics. Overmolding allows designers to combine different materials, colors, and textures in a single part, making it a popular choice for consumer electronics, medical devices, and automotive components. Additionally, over-molding can improve the durability and lifespan of products by providing an extra layer of protection against wear and tear. This can be particularly beneficial for handheld devices or tools frequently used in demanding environments.
Insert Molding
Insert molding involves molding one material around an insert or substrate to create a finished part. This technique is widely used in producing electronic connectors, medical devices, and consumer goods where metal or plastic inserts must be encapsulated within the final part. Insert molding allows for integrating multiple components into a single assembly, reducing the need for secondary assembly processes and improving overall product quality and durability.
Insert molding is a versatile manufacturing process that offers numerous benefits for product design and production. By encapsulating metal or plastic inserts within the final part, insert molding allows for creating complex, multi-component assemblies in a single operation. This streamlines the manufacturing process and reduces the risk of component misalignment or failure. Additionally, insert molding enables designers to incorporate features such as threaded inserts or electrical contacts directly into the molded part, eliminating the need for additional fasteners or connectors.
Rotary Platen Design
Rotary platen two-shot injection molding machines feature rotating mold plates, allowing multi-material or multi-color injection molding in a single-machine cycle. This design efficiently produces complex parts with varying material properties or colors without additional tooling or equipment changes. Rotary platen technology offers manufacturers greater flexibility in part design and production, making it ideal for applications such as automotive interiors, consumer goods, and household appliances.
Design Considerations for Two-Shot Molding
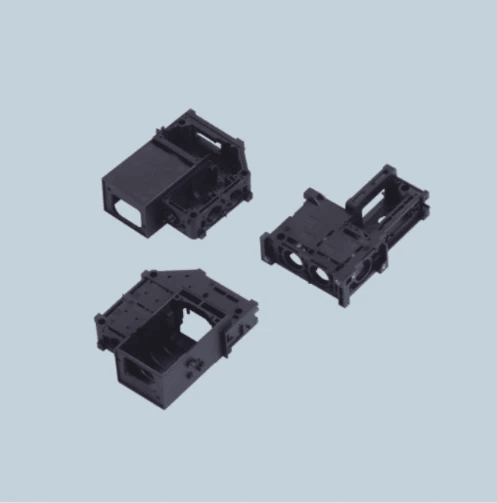
Regarding material selection for a two-shot molding project, choosing compatible materials that will bond effectively during the over-molding or insert molding process is essential. The first shot material should have good adhesion properties to ensure a strong bond with the second shot material. Additionally, considering the properties of each material is crucial in achieving the desired functionality and appearance of the final product.
Material Selection
For instance, in a two-shot injection molding project where a soft TPE (thermoplastic elastomer) is over-molded onto a rigid plastic substrate, it's essential to select materials with similar melting temperatures and shrinkage rates to prevent warping or delamination issues. Conducting thorough compatibility tests and understanding the bonding characteristics of different materials are key factors in successful material selection for two-shot molding projects.
Part Design for
Two-Shot Molding
Part design plays a critical role in ensuring the success of a two-shot injection molding process. Designing parts with proper wall thickness, draft angles, and suitable undercuts is essential for smooth ejection and preventing defects such as sink marks or voids. Moreover, designing parts with proper gating locations and flow paths can help optimize material flow during the injection process, resulting in high-quality finished parts.
Tooling and Mold Design
Precision is paramount when it comes to tooling and mold design for two-shot molding. The mold must accommodate both shots of material while ensuring precise alignment between cavities for accurate over-molding or insert molding. Proper venting and cooling systems should also be incorporated into the mold design to prevent issues such as trapped air or uneven cooling that could lead to part defects.
By carefully considering these design aspects when embarking on a two-shot molding project, manufacturers can maximize efficiency, minimize waste, and produce high-quality finished parts that meet their customers' requirements.
Advancements in Two Shot Injection Molding
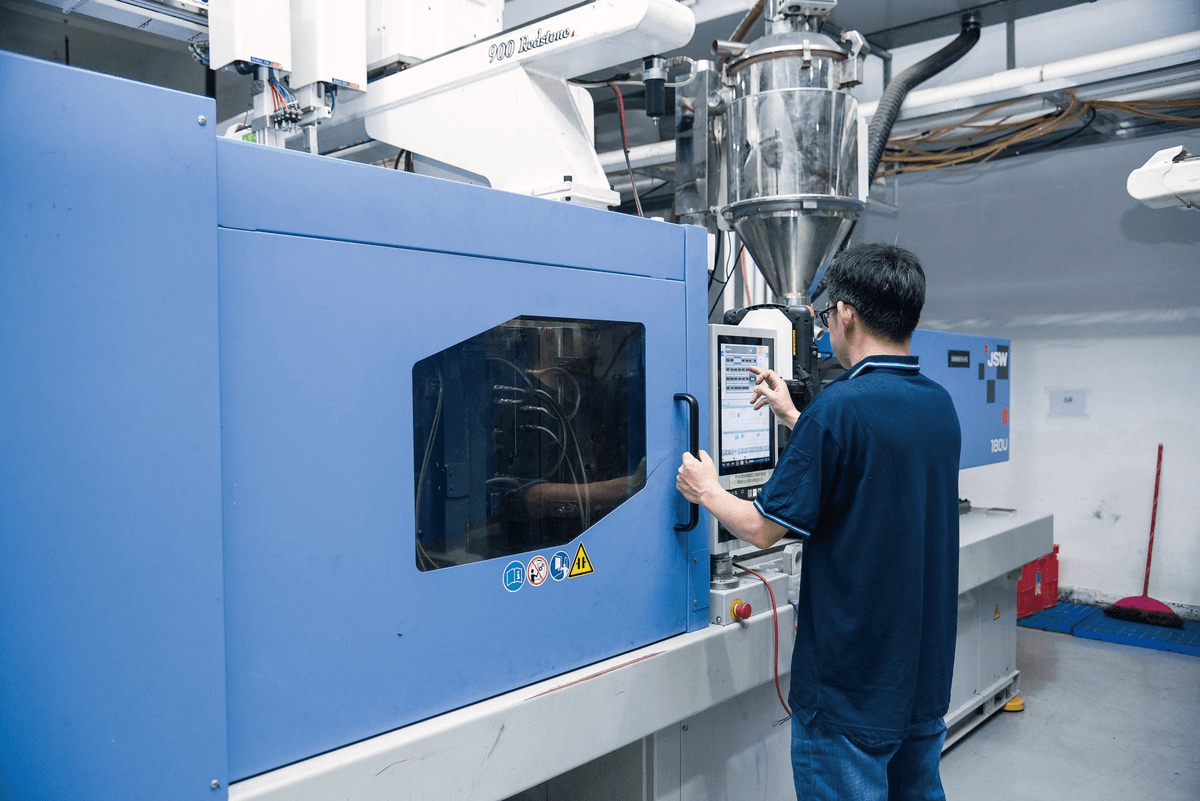
As the demand for more complex and durable products rises, the industry has seen several innovations in two-shot molding. Manufacturers are now using advanced materials and technologies to enhance the quality and functionality of two-shot molded products. These innovations have increased efficiency, reduced production costs, and improved part performance, making two-shot molding an attractive option for various industries.
Industry Innovations
One notable industry innovation in two-shot injection molding is the development of multi-material injection molding machines. These machines can handle different materials simultaneously, allowing manufacturers to create intricate designs with varying textures and colors in a single process. Additionally, mold design and tooling technology advancements have enabled precise control over material placement, resulting in higher-quality finished products with minimal waste.
Furthermore, using advanced robotics and automation in two-shot injection molding processes has significantly increased production efficiency and reduced labor costs. Robots can now perform intricate tasks such as material handling, part removal, and quality inspection with speed and precision, minimizing the risk of human error. This integration of robotics has also improved workplace safety by removing workers from potentially hazardous tasks, ultimately creating a more sustainable and productive manufacturing environment.
Future Trends in
Two-Shot Molding
Looking ahead, the future of two-shot molding is expected to focus on sustainability and eco-friendly practices. With growing environmental concerns, manufacturers are exploring bio-based and recycled materials for use in two-shot injection molding processes. Furthermore, digitalization and automation are anticipated to streamline production workflows and optimize part quality significantly.
As the demand for sustainable manufacturing practices continues to grow, two-shot molding is expected to see an increased use of bio-based and recycled materials. This shift towards eco-friendly materials aligns with environmental concerns and presents an opportunity for manufacturers to reduce their carbon footprint. By incorporating these materials into the two-shot injection molding process, companies can demonstrate their commitment to sustainability while meeting the needs of environmentally conscious consumers.
Baoyuan's Contribution to Two Shot Technology
Baoyuan is a leader in advancing two-shot technology through continuous research and development. Their dedication is evident in several ways:
- Cutting-edge solutions: Baoyuan has introduced innovative products like precision mold design software and state-of-the-art multi-material injection molding machines.
- Enhanced efficiency and quality: These solutions allow manufacturers to achieve greater precision and efficiency, leading to higher-quality products.
- Sustainable practices: Baoyuan prioritizes sustainability by developing methods to reduce waste and minimize environmental impact.
By prioritizing innovation and sustainability, Baoyuan sets new standards for the two-shot molding industry.
Choose the Right Injection Molding Process
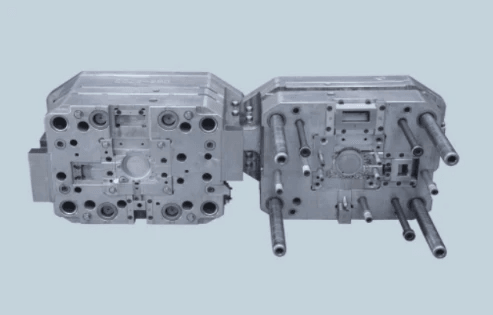
In the competitive world of injection molding, choosing the right process is crucial for success. Two-shot molding offers numerous advantages, including reduced manufacturing costs and improved product quality. By harnessing its potential, companies can create complex and innovative products that stand out in the market. Baoyuan's expertise in two-shot injection molding makes it a valuable partner for companies looking to leverage this advanced technology.
When selecting an injection molding process, factors such as production volume, part complexity, and material requirements must be considered. Two-shot molding is an excellent choice for producing multi-material or multi-colored components with high precision and efficiency. By understanding the unique benefits of two-shot molding, manufacturers can make informed decisions that optimize their production processes.
Harnessing the Potential of
Two-Shot Molding
Two-shot molding opens up a world of possibilities for product design and functionality. From creating soft-touch grips on hard plastic tools to integrating seals or gaskets directly into parts, this advanced technique enables engineers to push the boundaries of what's possible in plastic injection molding. By embracing two-shot molding, companies can differentiate their products in the market and meet evolving consumer demands.
Leveraging Baoyuan's Expertise in Two Shot Injection Molding
As a leader in two-shot technology, Baoyuan brings unparalleled expertise and innovation to the table. With a deep understanding of material compatibility, tooling design, and process optimization, Baoyuan helps clients unlock the full potential of two-shot injection molding. By partnering with Baoyuan, companies can access cutting-edge solutions that elevate their products and drive business growth.
Two-shot injection molding is revolutionizing the manufacturing industry by producing complex parts with multiple materials or colors in a single operation. By choosing this advanced technique and leveraging expert partners like Baoyuan, businesses can stay ahead of the curve and deliver exceptional products that captivate consumers' attention.