Introduction
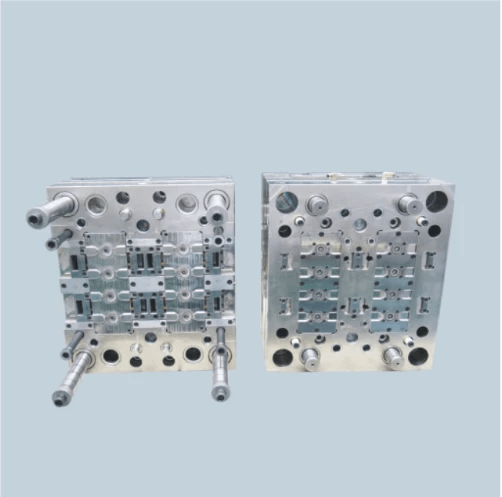
Injection molding is a fascinating process that transforms raw plastic into intricate, high-quality products used across various industries. To fully grasp the nuances of this technique, it’s essential to understand the foundational concepts, including the critical role of parting lines in molding. In this exploration, we will demystify essential terminology and set the stage for a deeper dive into what makes parting lines such a pivotal element in injection molding.
Understanding Injection Molding Basics
At its core, injection molding involves injecting molten plastic into a mold to create specific shapes and designs. This method is celebrated for its efficiency and precision, making it a go-to choice for manufacturing everything from automotive parts to consumer goods. However, understanding injection molding basics isn't just about knowing how it works; it's also about recognizing how each component—especially the parting line—contributes to the final product's quality and manufacturability.
The Role of Parting Lines in Molding
Parting lines are often overlooked yet play an indispensable role in injection molding processes. They mark where two halves of a mold meet and can significantly affect both the aesthetics and functionality of molded parts. By understanding what is a parting line in molding, manufacturers can make informed decisions that enhance product design while minimizing production challenges.
Essential Terminology Explained
To navigate the world of injection molding effectively, familiarizing oneself with key terms is essential. Terms like parting surface, gate, and runner frequently appear in discussions around parting line injection molding but might leave newcomers scratching their heads. Clarifying these terminologies not only aids comprehension but also empowers designers and engineers to optimize their approaches when considering how to decide parting line placements for maximum efficiency.
What is a Parting Line in Molding?
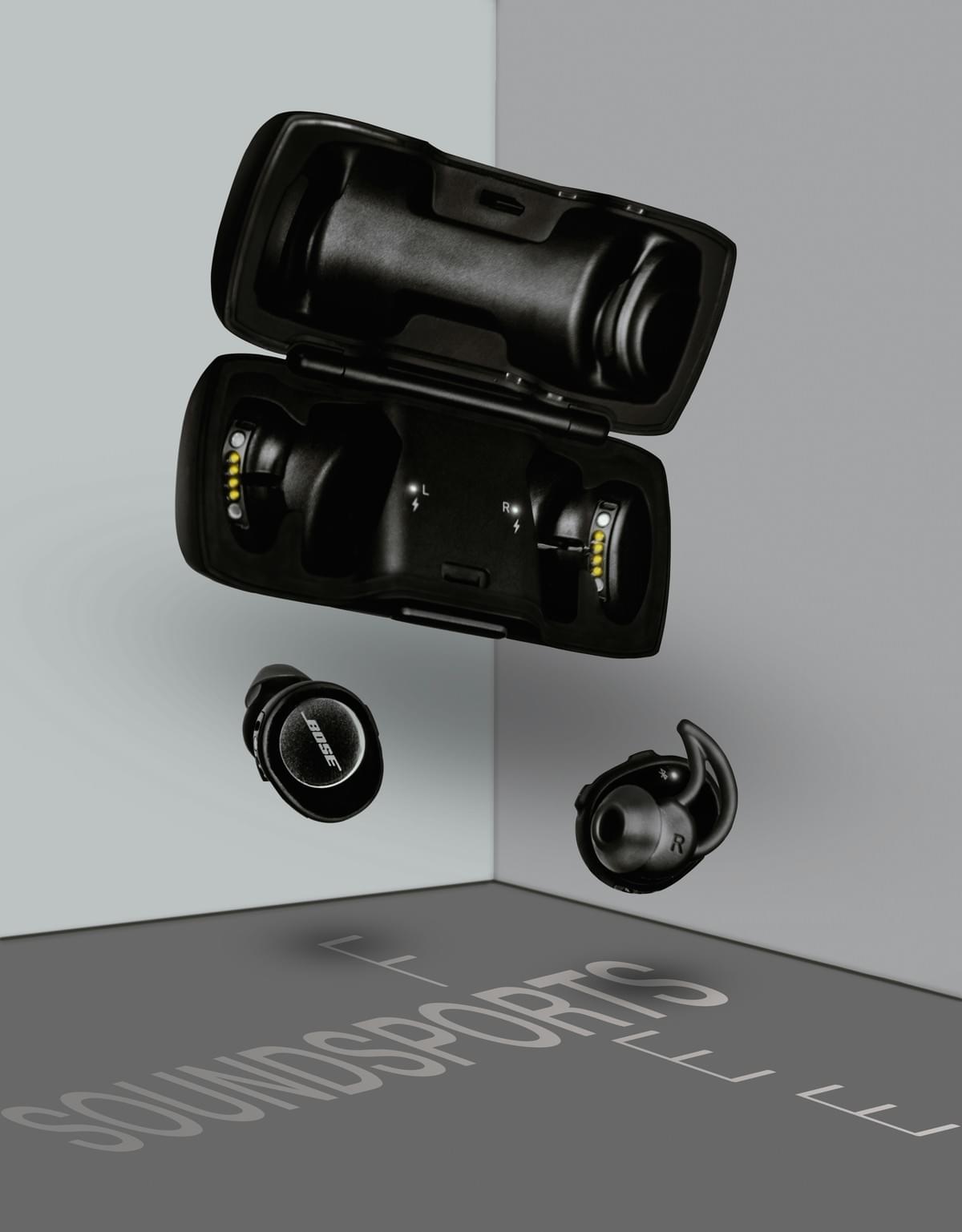
When diving into the world of injection molding, one term that frequently pops up is parting line. So, what is a parting line in molding? Simply put, it's the line where two halves of a mold meet. This seemingly simple feature plays an essential role in the overall success of the injection molding process and can significantly impact both aesthetics and functionality.
Definition and Importance
The parting line injection molding serves as the boundary between the mold's two halves, which are crucial for shaping plastic components. Its importance cannot be overstated; it determines how well parts are released from molds and affects surface finish quality. A poorly defined or misaligned parting line can lead to defects such as flash or uneven surfaces, compromising product integrity.
Types of Parting Lines
There are several types of parting lines that designers can choose from based on their specific needs. The most common types include straight lines, curved lines, and complex geometries designed to minimize visual impact on finished products. Understanding these types allows engineers to select the best option when determining how to decide parting line placement for optimal results.
Common Misconceptions
One common misconception about parting lines is that they are merely aesthetic features with no functional significance. In reality, they play a pivotal role in both mold design and production efficiency; neglecting them can lead to increased costs due to rework or scrap rates. Additionally, some believe that all molds should have perfectly aligned parting lines—this isn't always necessary; sometimes strategic misalignment can enhance product performance or ease of assembly.
What is the Parting Surface in Injection Molding?
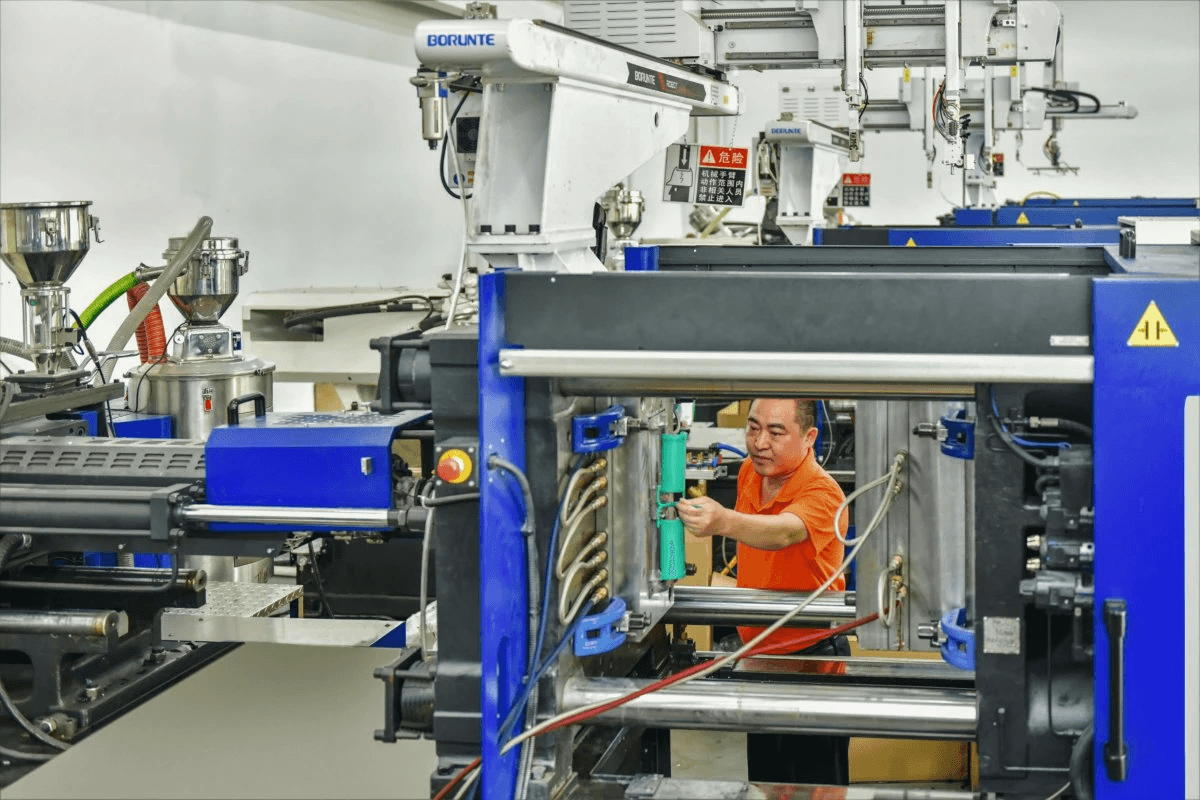
Understanding the parting surface is crucial for anyone involved in injection molding. The parting surface serves as the boundary between the two halves of a mold, which opens and closes during the injection process. This area directly influences how well a molded part comes out, making its design and execution pivotal in achieving high-quality results.
The Anatomy of the Parting Surface
The parting surface consists of several key components that work together to facilitate efficient molding. This includes features like draft angles, which help parts release from the mold more easily, and alignment pins that ensure precise fitment when closing the mold halves. Additionally, proper surface finish on this area can prevent defects such as flash or uneven surfaces, emphasizing its importance in answering “What is a parting line in molding?”
How It Affects Product Quality
The design of the parting surface has a direct impact on product quality during injection molding. If not correctly executed, it can lead to issues such as sink marks or warping, compromising both aesthetics and functionality of the final product. Therefore, understanding “What is the function of parting lines?” becomes essential; they not only define where molds separate but also influence how materials flow within them.
Real-World Examples
Consider automotive components like dashboards or panels; these often require intricate designs with tight tolerances influenced by their respective parting surfaces. A poorly designed parting line injection molding setup could result in misaligned pieces or even production delays due to excessive rework needed for defective parts. In contrast, effective management of these surfaces ensures smoother production cycles and higher-quality end products across various industries.
How to Decide Parting Line?
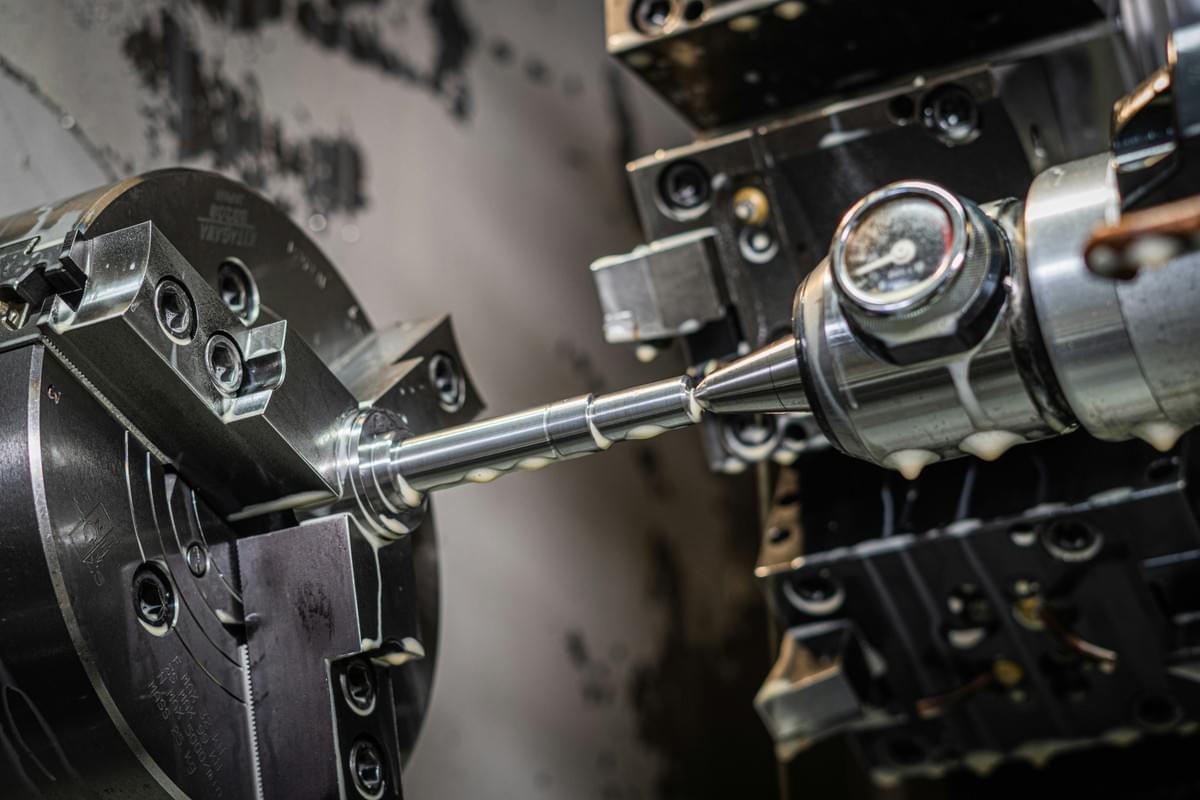
Deciding on the parting line in injection molding is a critical step that can significantly influence both the manufacturing process and the final product's quality. The parting line is where two halves of a mold meet, and choosing its location requires careful consideration of various factors to ensure efficiency and effectiveness. Understanding what is a parting line in molding and how it relates to the overall design is essential for achieving optimal results.
Factors Influencing Parting Line Decisions
Several factors come into play when determining where to place the parting line in injection molding. One primary consideration is the geometry of the part; complex shapes may necessitate more strategic placements to avoid undercuts or other design challenges. Additionally, material flow characteristics can affect how well molten plastic fills the mold, making it crucial to think about how these elements interact with what is the parting surface in injection molding.
Another significant factor involves aesthetic considerations—if visible, a poorly placed parting line can detract from a product’s appearance. Engineers must also consider manufacturing constraints such as mold cost, cycle time, and ease of assembly when deciding on a suitable location for the parting line injection molding. Ultimately, balancing these factors will lead you closer to an efficient design that meets production goals.
Design Considerations to Keep in Mind
When designing parts with an eye toward their future parting lines, several key considerations should guide your decisions. First and foremost, strive for simplicity; simpler designs often translate into easier manufacturing processes and fewer complications related to what is a parting line in molding. Keeping features like ribs or bosses away from potential seam areas can help reduce issues during demolding.
Another important aspect involves ensuring adequate draft angles on surfaces adjacent to your chosen parting line; this facilitates easier removal from the mold while minimizing wear over time. Additionally, consider how your choice affects assembly processes down the road—misaligned parts due to poor planning could lead to costly rework later on! Understanding what is the function of parting lines will help you make informed choices during this phase.
Tips from the Baoyuan Team
The Baoyuan team emphasizes collaboration between design engineers and tooling specialists when deciding on a parting line location; this teamwork fosters innovative solutions that might not surface otherwise! Don’t shy away from prototyping—creating sample molds can provide valuable insights into practical challenges associated with your planned design before full-scale production kicks off.
Additionally, utilize software tools that simulate flow dynamics within molds; these programs can highlight potential issues related to material distribution along different parts of your design while reinforcing decisions around where best to place your chosen section for optimal performance! Finally, always remember: every decision regarding what is a parting line in molding impacts both quality control measures and production efficiency—so take them seriously!
What is the Function of Parting Lines?
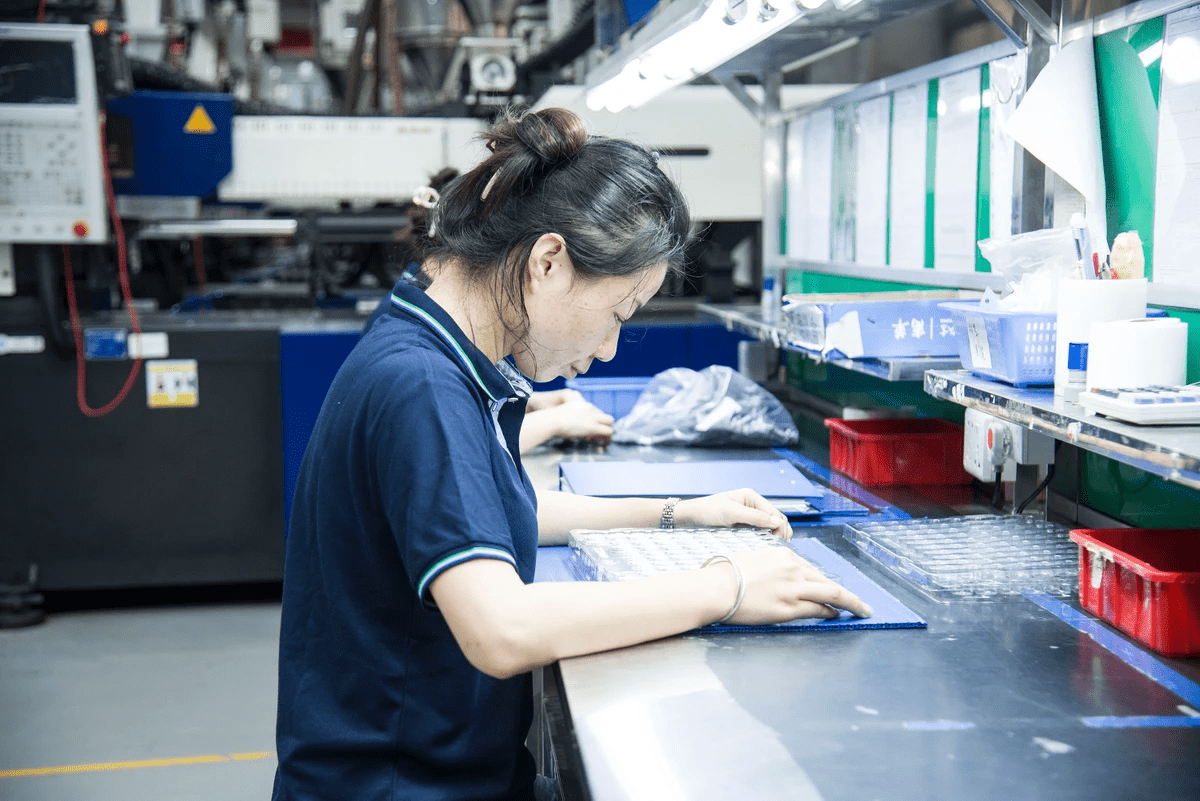
When diving into the world of injection molding, one cannot overlook the critical role that parting lines play in the process. A parting line in injection molding serves as a boundary where two halves of a mold meet, allowing for the removal of the finished product without damage. Understanding what is a parting line in molding is essential for both manufacturers and designers, as it directly impacts the efficiency and quality of production.
Key Functions in Injection Molding
Parting lines are not just arbitrary seams; they serve several key functions in injection molding. Firstly, they facilitate the separation of mold halves, ensuring that products can be ejected smoothly after cooling. Additionally, they help define the overall shape and features of molded parts, which reinforces their importance when considering what is the parting surface in injection molding.
Moreover, parting lines can influence aesthetic aspects like surface finish and visual appeal. A well-placed parting line can minimize visible marks on a product's exterior while maintaining structural integrity. Therefore, knowing how to decide parting line placement effectively can make or break a project’s success.
Impact on Production Efficiency
The efficiency of an injection molding operation hinges significantly on how well parting lines are managed. Properly designed parting lines contribute to faster cycle times since they simplify mold opening and closing procedures. When considering what is a parting line in molding, it's crucial to recognize that an optimal design can lead to reduced downtime and increased output.
Furthermore, efficient management of parting lines minimizes defects during production runs, which ultimately saves time and resources associated with rework or scrap materials. For manufacturers looking to enhance their processes, understanding how to decide parting line locations strategically can yield measurable improvements in production efficiency.
Troubleshooting Common Issues
Despite their importance, issues related to parting lines often arise during injection molding processes—making troubleshooting essential for maintaining quality standards. Common problems include visible seam marks or misalignment between mold halves due to poorly positioned parting lines. Addressing these concerns requires an understanding of what is the function of parting lines and how they interact with other design elements.
To tackle such issues effectively, manufacturers should conduct thorough assessments during both design and testing phases—ensuring that all factors influencing how to decide parting line placement are taken into account. By proactively identifying potential pitfalls associated with poorly designed or executed parting lines, companies can prevent costly mistakes down the road.
Best Practices for Managing Parting Lines
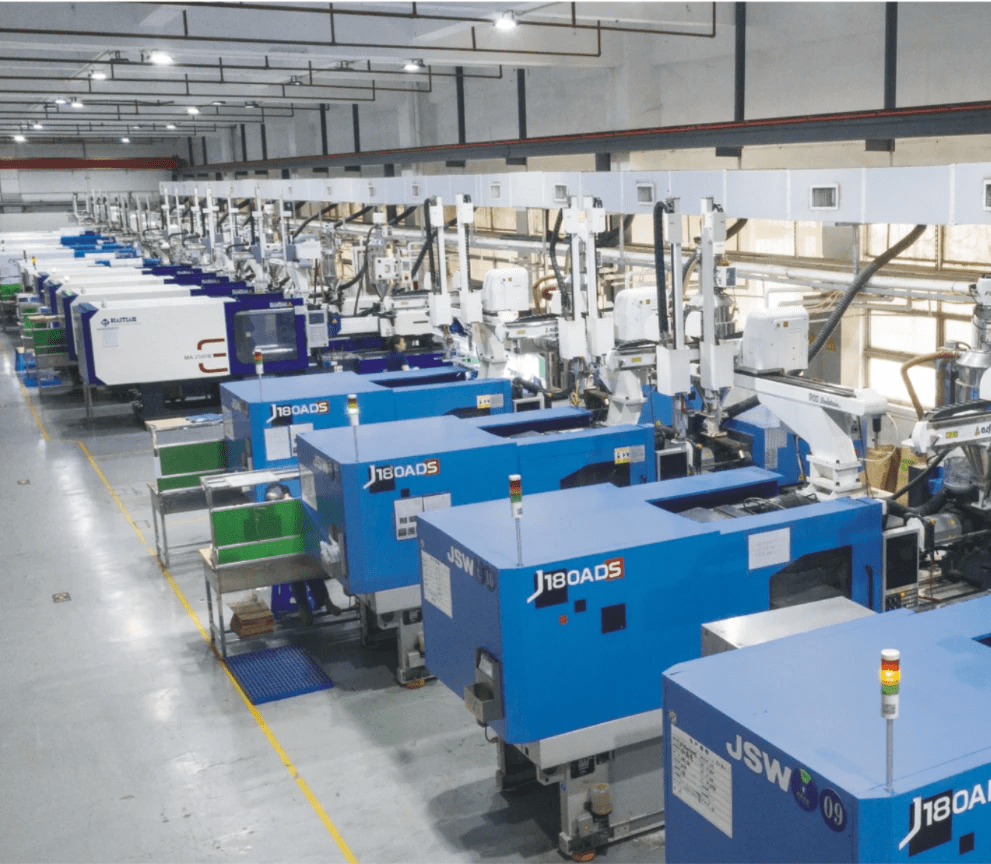
Strategies for Optimal Design
The first step in optimizing your design is to carefully consider the location of the parting line. This involves analyzing the geometry of your product and determining where the mold halves will meet without compromising structural integrity or aesthetics. Remember, what is the parting surface in injection molding isn’t just about functionality; it also affects how easily parts are ejected from molds, which can impact overall production speed.
Another strategy is to utilize draft angles effectively along the parting line. Draft angles facilitate easier ejection of molded parts by reducing friction between the mold and the product. Additionally, incorporating features like undercuts should be done with caution as they complicate how to decide parting line placement and may require more complex mold designs.
Lastly, collaborating with experienced designers during this phase can yield valuable insights on how to decide parting line placement efficiently. They may suggest innovative solutions that enhance both functionality and manufacturability—things you might not have considered otherwise!
Common Errors and How to Avoid Them
One common error in managing parting lines involves neglecting draft angles altogether, leading to difficulties during ejection. This oversight often results in damaged parts or even mold wear over time—definitely a scenario you want to avoid! Always double-check your designs for adequate draft angles; they are essential for smooth operation.
Another pitfall is misjudging where to place your parting line based on cosmetic considerations alone rather than functional needs. While aesthetics matter, remember that what is a function of parting lines goes beyond looks—they play a crucial role in ensuring proper alignment and minimizing defects during molding cycles.
Finally, failing to communicate effectively with all stakeholders involved can lead to discrepancies between design intent and final output. Regular meetings with engineers, designers, and production staff ensure everyone understands what is required when it comes down to managing those pesky part lines effectively!
Insights from Industry Professionals
Industry professionals emphasize that thorough planning is key when dealing with what is a parting line in molding decisions. They recommend using simulation software early in the design phase; this allows teams to visualize potential issues before they arise on the shop floor—saving both time and resources! Such tools help clarify how different designs affect what is the function of parting lines throughout production processes.
Moreover, many experts advocate for continuous education on evolving technologies related to injection molding techniques—this keeps teams updated on best practices as well as new materials available that could enhance performance at those critical junctions we call “part lines.”
Lastly, networking within industry circles provides invaluable insights about managing challenges related specifically around injection molding processes—including effective strategies for handling complex geometries at those vital separation points!
Conclusion
In the world of injection molding, understanding the nuances of parting lines is crucial for both design and production efficiency. From defining what a parting line in molding is to recognizing the significance of the parting surface in injection molding, these elements play a pivotal role in creating high-quality products. As we wrap up our discussion, it’s clear that mastering how to decide parting line placement can make all the difference between a flawless mold and one riddled with defects.
Recap of Parting Line Injection Molding
Parting line injection molding serves as a fundamental concept that every designer and engineer should grasp. It involves understanding where two halves of a mold meet, which directly influences product quality and manufacturing efficiency. By revisiting what is a parting line in molding, we can appreciate how its placement affects not only aesthetics but also functionality in the final product.
Importance of Proper Parting Surface Management
Proper management of the parting surface in injection molding cannot be overstated; it ensures smooth operation during production and helps prevent costly errors down the line. An optimized parting surface allows for easier ejection of parts while minimizing imperfections like flash or misalignment. When considering how to decide parting line locations, recognizing their impact on production flow and overall product integrity becomes paramount.
Final Thoughts from the Baoyuan Team
The Baoyuan Team emphasizes that understanding what is the function of parting lines goes beyond mere technicalities; it's about enhancing your entire manufacturing process. By implementing best practices for managing these lines, you can significantly boost your production efficiency while reducing waste and rework costs. Remember, every detail counts when it comes to injection molding—so take these insights to heart as you refine your designs!