Introduction
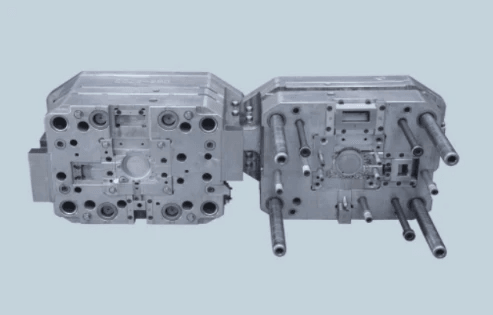
In the world of plastic manufacturing, fan gate injection molding stands out as a technique that optimizes both efficiency and quality. This method utilizes a unique gate design to control the flow of molten plastic into molds, ensuring that every inch of the mold is filled uniformly. Understanding fan gate injection molding is essential for manufacturers looking to enhance their production processes and achieve superior results in their injection molded parts.
Understanding Fan Gate Injection Molding
Fan gate injection molding refers to a specific type of gating system used in plastic injection molding where multiple channels distribute material evenly across a mold cavity. Unlike traditional gating methods, the fan gate design allows for better control over material flow, reducing potential defects caused by uneven filling. This technique not only improves the overall aesthetics of molded parts but also enhances their structural integrity, making it a preferred choice in various applications.
The Importance of Mold Design
Mold design plays a crucial role in determining the success of any plastic injection process, including fan gate injection molding. A well-thought-out mold design can significantly influence material flow, cooling rates, and cycle times, ultimately affecting product quality and production costs. By prioritizing effective mold design principles, manufacturers can maximize efficiency while minimizing waste and defects in their plastic injection projects.
Exploring Injection Moldable Plastics
The choice of materials is another critical aspect when it comes to fan gate injection molding and overall plastic injection processes. There are numerous types of injection moldable plastics available on the market today, each with its unique properties suited for specific applications. From high-performance thermoplastics to cost-effective alternatives, understanding these materials will help manufacturers select the right options that align with their production goals while ensuring optimal performance in their molded parts.
What is Fan Gate Injection Molding
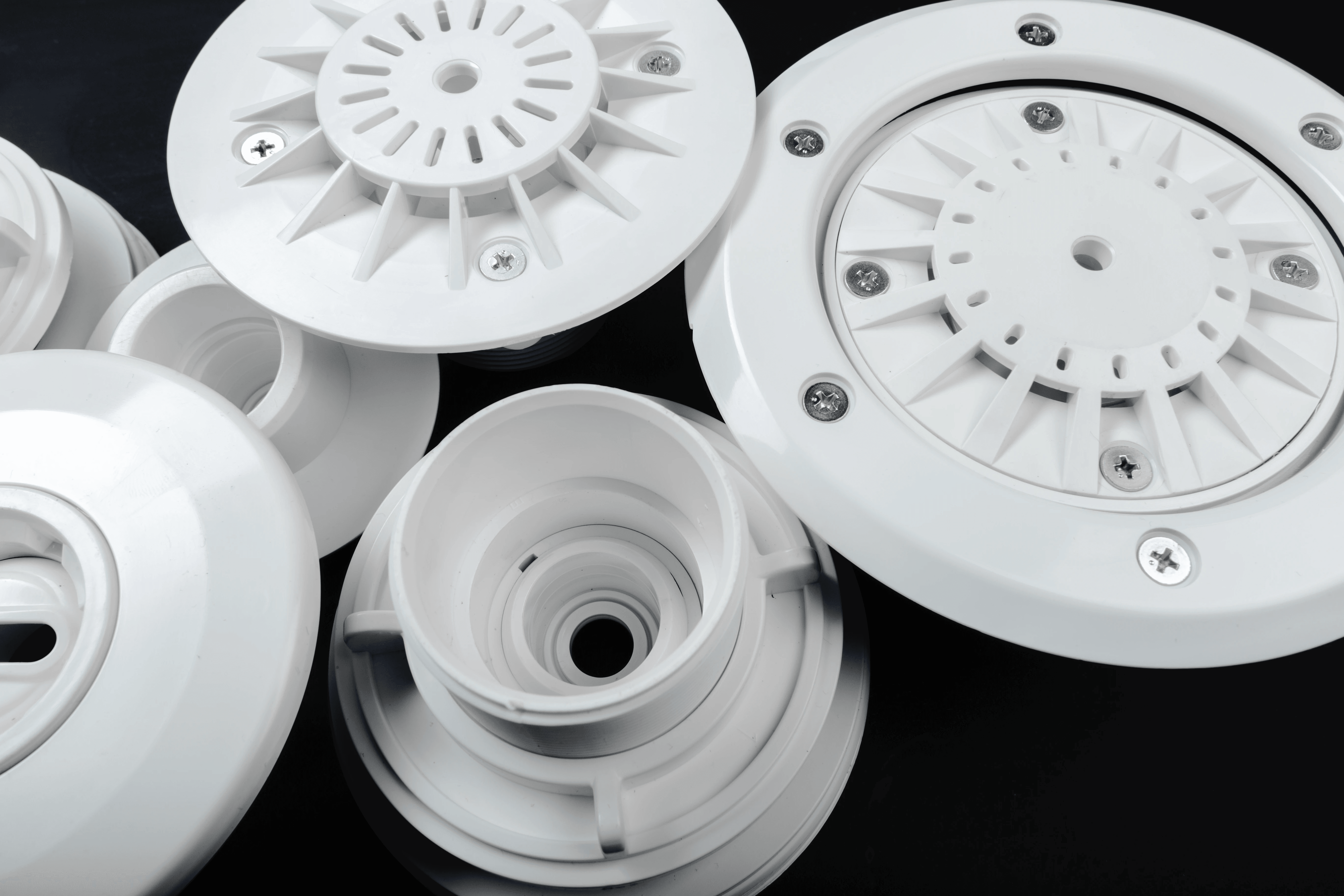
Fan gate injection molding is a specialized technique within the broader field of plastic injection molding. It employs a unique gate design that enhances material flow, resulting in improved production efficiency and part quality. This method is particularly beneficial for creating complex shapes with minimal defects, making it a popular choice among manufacturers.
Definition and Overview
At its core, fan gate injection molding utilizes a fan-shaped gate that distributes molten plastic evenly across the mold cavity. This design allows for better filling of intricate geometries and reduces the risk of air entrapment, which can lead to defects in injection molded parts. By optimizing the flow of injection moldable plastics, this technique enhances overall productivity while ensuring high-quality outputs.
Differences from Other Molding Types
What sets fan gate injection molding apart from traditional methods is its unique gating system that promotes uniform material distribution. Unlike standard pin or edge gates, fan gates allow for wider entry points that facilitate faster filling times and reduced pressure drop during the injection process. This results in fewer sink marks and improved surface quality compared to other molding techniques like molding over molding or direct gate methods.
Applications in Manufacturing
Fan gate injection molding finds applications across various industries due to its versatility and efficiency in producing high-quality components. It's commonly used in automotive parts, consumer electronics housings, and medical device components where precision is paramount. Additionally, manufacturers searching for plastic injection molding near me often seek out this method for its ability to deliver reliable results while minimizing waste and production costs.
Advantages of Using Fan Gate Injection Molding
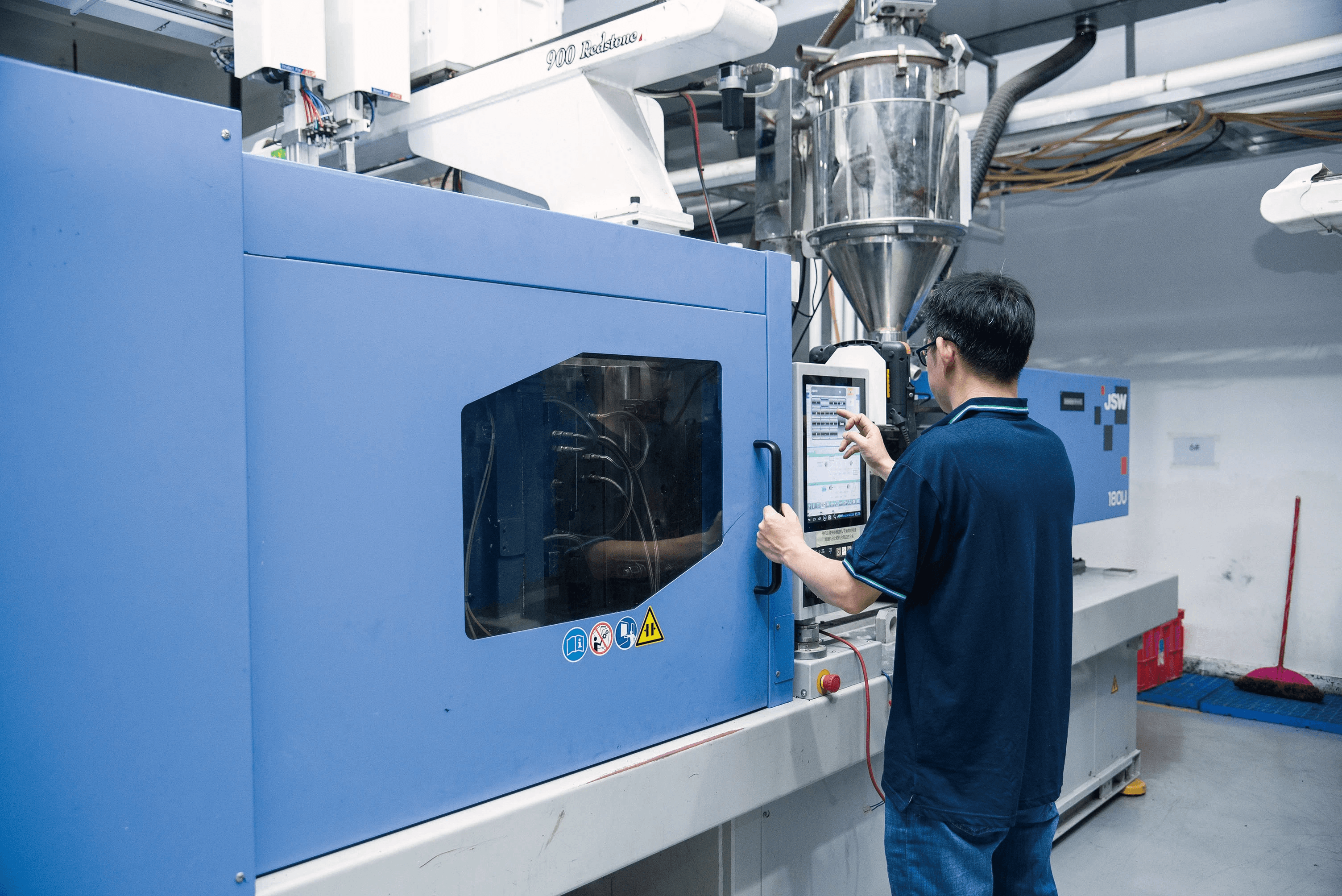
Fan gate injection molding brings a myriad of advantages to the table, making it a favored choice in the realm of plastic injection molding. Its unique design and functionality not only enhance production efficiency but also improve the overall quality of injection molded parts. Let's dive into some specific benefits that set fan gate injection molding apart from other techniques.
Enhanced Material Flow
One of the standout features of fan gate injection molding is its ability to facilitate enhanced material flow during the injection process. The fan-shaped design allows for a more uniform distribution of molten plastic, reducing the risk of defects such as voids or incomplete fills in mold cavities. This efficient flow minimizes pressure drops and ensures that even complex geometries are filled accurately, resulting in high-quality mold plastic injection outputs.
Moreover, enhanced material flow can lead to shorter cycle times in production, allowing manufacturers to ramp up their output without compromising quality. This is particularly beneficial for those searching for plastic injection molding near me, as faster turnaround times can significantly impact local businesses' competitiveness. Ultimately, better material flow translates into fewer wasted resources and higher efficiency throughout the manufacturing process.
Improved Surface Quality
When it comes to aesthetics and functionality, improved surface quality is another significant advantage offered by fan gate injection molding. The controlled filling process helps produce smooth surfaces with fewer imperfections compared to other methods like traditional sprue gates or edge gates. As a result, products made through this technique often require less post-processing work—saving time and costs associated with finishing processes.
Additionally, superior surface quality enhances product performance by minimizing friction and wear when parts interact with one another or their environment—a critical factor in applications involving moving components or assemblies. With fan gate injection molding becoming increasingly popular for various industries, manufacturers can confidently produce high-quality products that meet stringent market demands without sacrificing efficiency.
Cost-Effectiveness in Production
Cost-effectiveness is always at the forefront when considering different manufacturing techniques, and fan gate injection molding excels in this area as well. By optimizing material usage through efficient designs and reduced waste during production runs, companies can achieve significant savings over time—especially important for businesses dealing with large volumes of plastic injection molded parts.
Moreover, since this method leads to fewer defects and lower rejection rates due to its superior flow characteristics, manufacturers enjoy reduced costs related to rework or scrap materials—a win-win situation! When combined with innovations in plastic injection technologies that further streamline processes, it’s clear why many organizations are leaning towards fan gate designs for their mold projects.
Key Design Considerations
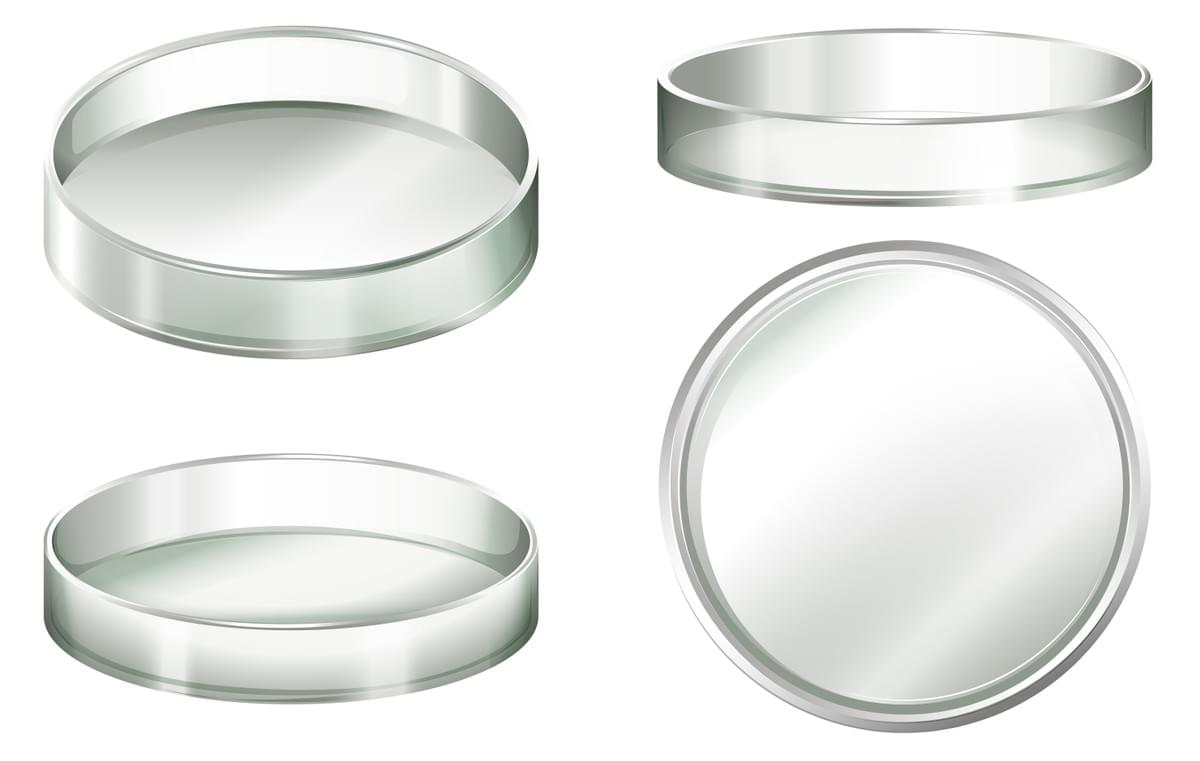
When diving into the world of fan gate injection molding, several key design considerations come to the forefront. These factors not only influence the efficiency of the production process but also impact the overall quality of the injection molded parts. Understanding these aspects is crucial for achieving optimal results in plastic injection molding.
Gate Size and Location
The size and location of the gate in fan gate injection molding play a pivotal role in determining how smoothly plastic flows into the mold cavity. A well-placed gate ensures that molten plastic enters quickly, minimizing potential defects in the final product. If you’re searching for “plastic injection molding near me,” remember that precise gate design can significantly enhance material flow and surface finish.
Choosing an appropriate gate size is equally important; too small can lead to incomplete filling, while too large may cause excessive material waste or uneven cooling. Additionally, strategic placement can help avoid areas prone to warping or stress concentrations, which are common pitfalls in mold design. Ultimately, getting this right is essential for producing high-quality injection molded parts that meet industry standards.
Balancing Flow in Multiple Cavities
In cases where multiple cavities are utilized during fan gate injection molding, balancing flow becomes a critical consideration. Achieving uniform material distribution across all cavities ensures consistent quality and reduces cycle times—key factors for any manufacturer looking to optimize their processes with plastic injection molding techniques. An imbalance can lead to variations in wall thickness and surface quality, ultimately affecting product performance.
To balance flow effectively, designers often employ techniques such as adjusting runner sizes or incorporating pressure sensors within the system. This attention to detail not only enhances efficiency but also minimizes waste—an essential aspect when working with valuable injection moldable plastics. Understanding how to manage these variables will set your project apart from competitors who overlook this vital step.
Common Design Pitfalls
Navigating through common design pitfalls is crucial for successful fan gate injection molding projects. One prevalent mistake is neglecting proper venting; without adequate air escape routes, trapped air can create defects like voids or burn marks on finished products—issues that no one wants when producing high-quality plastic injection molded parts!
Another frequent error involves ignoring thermal dynamics; improper cooling rates can lead to warping or dimensional inaccuracies post-molding—a nightmare scenario for any manufacturer focused on precision engineering with mold plastic injection techniques. By being aware of these pitfalls and proactively addressing them during the design phase, you’ll save time and resources down the line while ensuring top-notch quality control throughout your production process.
The Role of Materials in Injection Molding
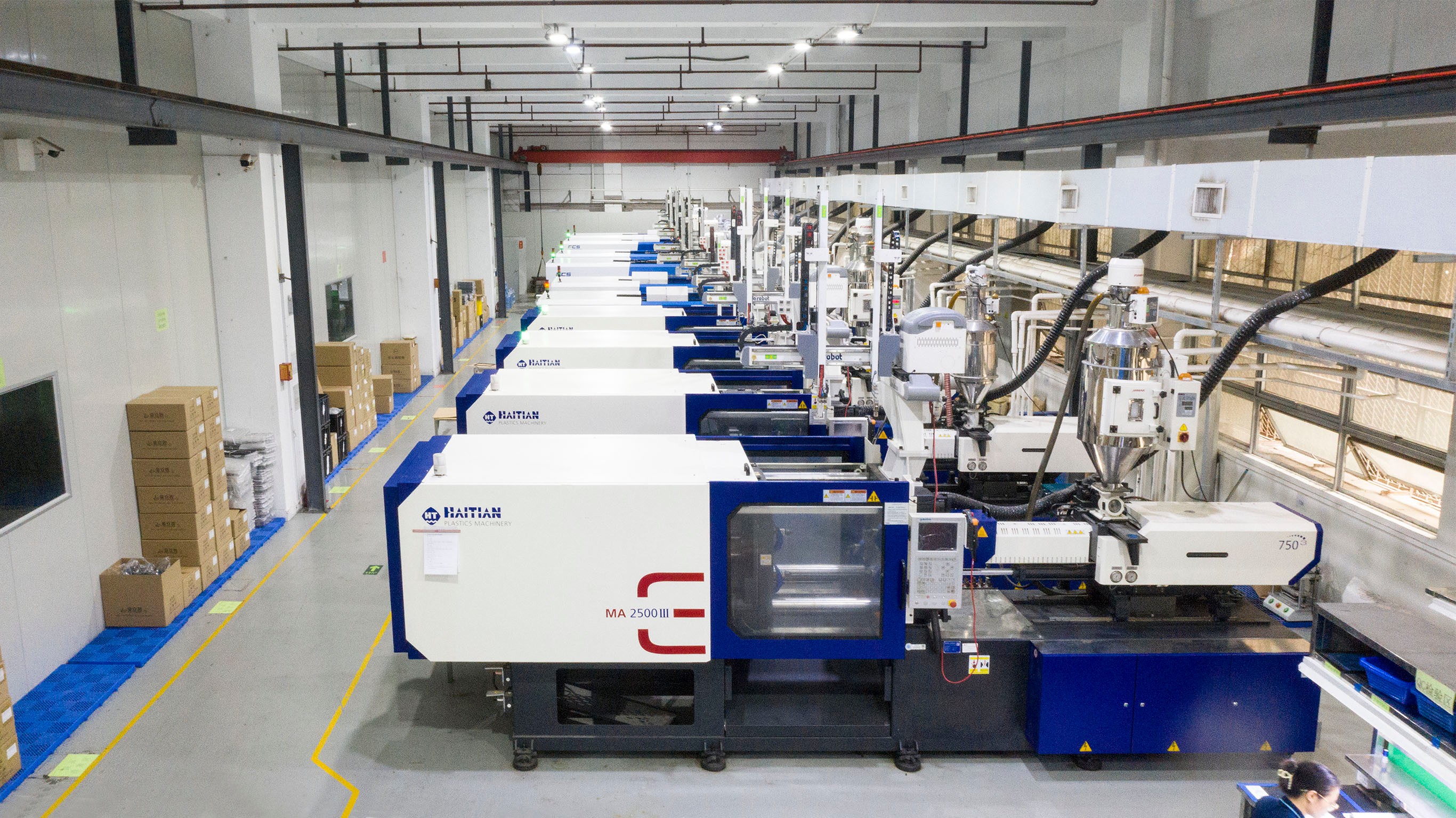
When it comes to fan gate injection molding, the choice of materials is crucial for achieving optimal results. The right injection moldable plastics can significantly influence the performance, durability, and aesthetic appeal of the final product. Understanding various plastic types and their properties is essential for anyone involved in mold plastic injection.
Popular Injection Moldable Plastics
In the realm of plastic injection molding, several materials stand out due to their versatility and performance characteristics. Polypropylene (PP) is a favorite because of its lightweight nature and resistance to chemicals, making it ideal for a range of applications from automotive components to consumer products. Additionally, acrylonitrile-butadiene-styrene (ABS) is widely used for its toughness and ability to be molded into intricate shapes, proving invaluable in creating high-quality injection molded parts.
Polyethylene (PE) also deserves mention; it's known for its flexibility and resilience, often utilized in packaging solutions. For more specialized applications, engineering plastics like polycarbonate (PC) offer superior strength and transparency but come at a higher cost. Each type of injection moldable plastic brings unique advantages that can enhance the overall efficiency of fan gate injection molding processes.
The Impact of Material Choice on Quality
Material selection plays a pivotal role in determining the quality of products produced through plastic injection molding techniques. Choosing the wrong material can lead to issues such as warping or poor surface finish in your injection molded parts. Conversely, selecting high-quality materials tailored for specific applications ensures better flow characteristics during fan gate injection molding, resulting in smoother finishes and enhanced durability.
Moreover, different plastics react uniquely under varying temperatures and pressures during the molding process; understanding these properties is vital for achieving consistent results. For instance, some materials may require specific processing conditions to avoid defects like sink marks or short shots—issues that can be costly both financially and temporally if not addressed early on. Thus, careful consideration when choosing materials directly correlates with product quality.
Innovations in Plastic Injection Technologies
As technology advances, so do innovations within the field of plastic injection molding—particularly concerning material use and processing methods. Recent developments have introduced advanced composite materials that combine traditional plastics with additives like glass fibers or carbon nanotubes to improve mechanical strength without adding significant weight. These innovations allow manufacturers to produce lighter yet stronger components through fan gate injection molding techniques.
Additionally, advancements such as 3D printing technologies are being integrated into traditional plastic injection processes—enabling rapid prototyping before full-scale production begins. This hybrid approach allows designers greater flexibility while ensuring that final products meet stringent quality standards without excessive waste or delays associated with conventional methods like mold plastic injection alone.
In conclusion, understanding the role of materials in fan gate injection molding not only enhances production efficiency but also drives innovation within the industry.
Quality Assurance in Fan Gate Injection Molding
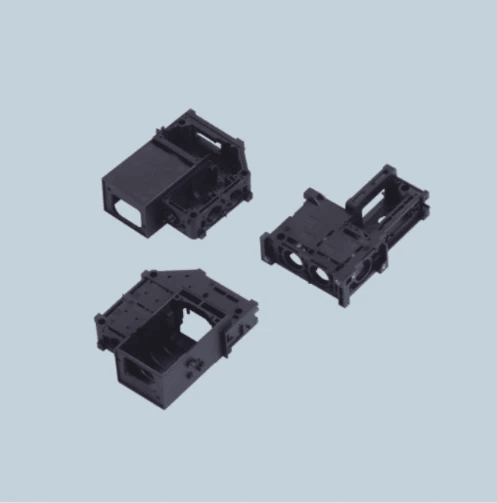
In the world of fan gate injection molding, quality assurance is paramount to ensure that the final products meet stringent industry standards. This process involves a series of systematic testing procedures designed to evaluate the integrity and performance of injection molded parts. By implementing rigorous quality checks throughout the production cycle, manufacturers can significantly enhance the reliability of their plastic injection molding processes.
Procedures for Testing Injection Molded Parts
Testing injection molded parts begins with visual inspections to identify any surface defects or irregularities that could compromise functionality. Following this, more sophisticated methods such as dimensional analysis and mechanical testing are employed to assess properties like strength and flexibility in various conditions. These comprehensive procedures not only verify compliance with specifications but also help in fine-tuning mold design and material selection for future projects involving mold plastic injection.
Importance of Process Control
Process control is the backbone of efficient fan gate injection molding operations, ensuring consistency and minimizing variability across batches. By closely monitoring parameters such as temperature, pressure, and cooling times during production, manufacturers can prevent defects that arise from fluctuations in these critical factors. This meticulous attention to process control translates into higher-quality products made from injection moldable plastics while reducing waste and rework costs.
Integrating Quality into Production
Integrating quality into production goes beyond mere testing; it involves embedding quality assurance practices within every step of the plastic injection molding workflow. From initial design considerations through to final inspection, a culture of quality must be fostered among all team members involved in manufacturing processes like molding over molding. By prioritizing quality at every stage—whether searching for plastic injection molding near me or optimizing designs—manufacturers can achieve superior outcomes that resonate with clients' expectations.
Conclusion
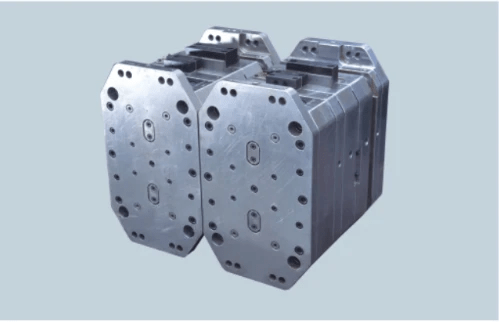
In the realm of manufacturing, the efficiency of production methods can make or break a business. Fan gate injection molding stands out as a method that enhances material flow and improves surface quality, making it an ideal choice for creating high-quality injection molded parts. By leveraging innovative mold designs and selecting the right injection moldable plastics, manufacturers can maximize productivity while minimizing waste.
Maximizing Efficiency in Production Methods
To truly harness the benefits of fan gate injection molding, companies must focus on optimizing their production processes. This involves not only selecting appropriate mold plastic injection techniques but also ensuring that the design accommodates efficient material flow throughout multiple cavities. By prioritizing these aspects, businesses can significantly reduce cycle times and increase output without sacrificing quality.
Future Trends in Injection Molding
The future of plastic injection molding is bright, with ongoing advancements shaping how products are manufactured. Innovations like smart manufacturing technologies and eco-friendly materials are paving the way for more sustainable practices in fan gate injection molding and beyond. Additionally, trends such as molding over molding are gaining traction, allowing manufacturers to create multi-material parts that enhance functionality and aesthetics.
Why Partner with Experts like Baoyuan
When navigating the complexities of fan gate injection molding, partnering with industry experts like Baoyuan can be invaluable. Their extensive knowledge in plastic injection processes ensures that you receive tailored solutions for your specific needs—whether you're searching for plastic injection molding near me or looking to optimize your current operations. With their guidance, you can confidently produce top-notch injection molded parts while staying ahead of market trends.