Introduction
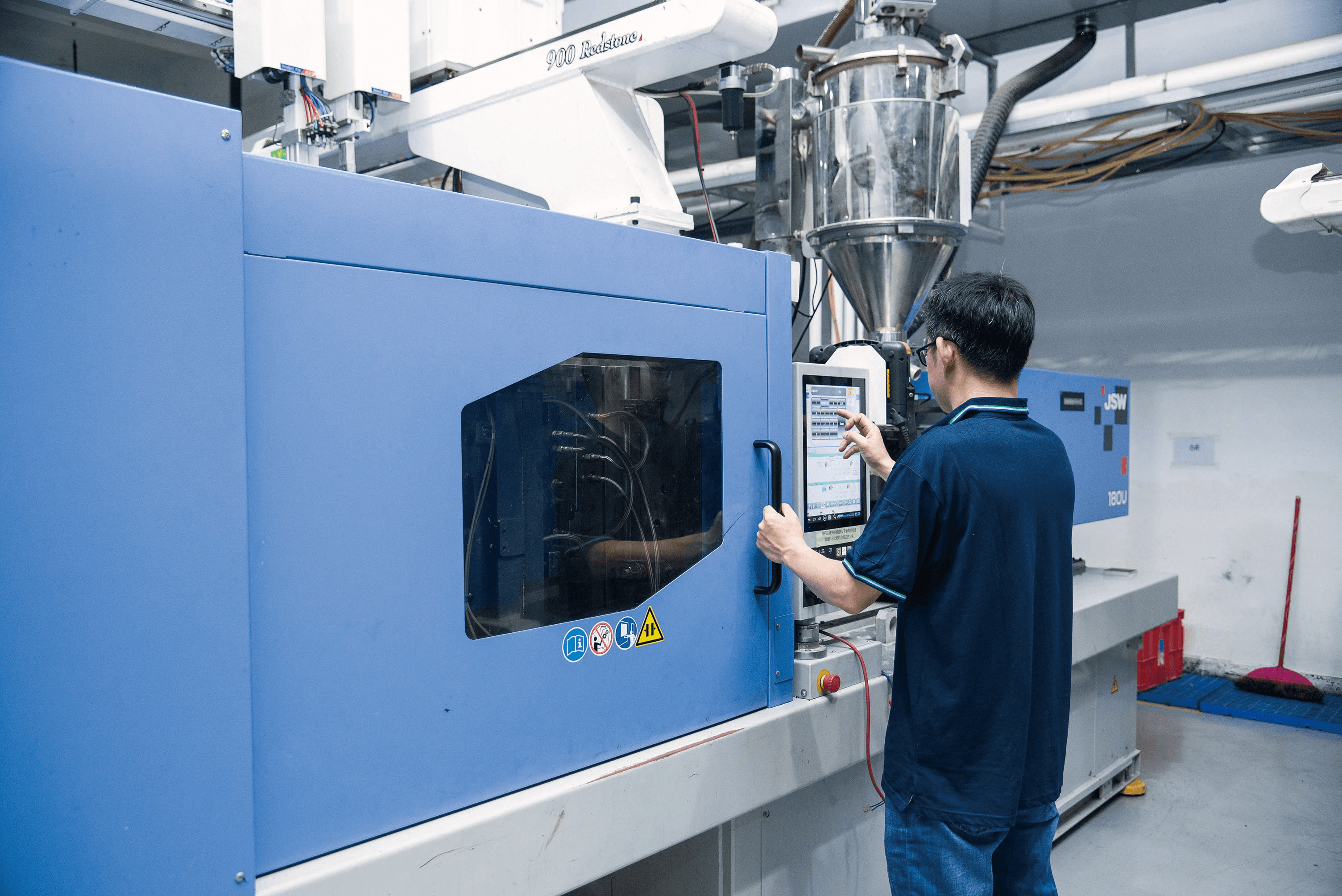
In the world of healthcare, the phrase injection molding medical devices is becoming increasingly synonymous with innovation and efficiency. This advanced manufacturing process allows for the creation of precise, high-quality components that are vital in various medical applications. But what exactly is medical injection molding, and why does it hold such significance in modern medicine?
Understanding Medical Injection Molding
Medical injection molding is a specialized manufacturing technique designed to produce intricate parts used in healthcare products. By injecting molten plastic into a mold, manufacturers can create complex shapes with remarkable accuracy and consistency. The beauty of this process lies not just in its ability to produce large quantities but also in its capacity for customization, making it ideal for developing tailored solutions for unique medical needs.
Importance of Precision in Medical Devices
Precision is paramount when it comes to medical devices; even the slightest error can have dire consequences on patient safety and treatment efficacy. Hence, the relationship between precision engineering and medical injection molding cannot be overstated—these molded components must meet stringent regulatory standards while delivering reliable performance. In an industry where lives are at stake, ensuring that every part fits perfectly is not just important; it’s critical.
Overview of the Injection Molding Process
The injection molding process begins with designing a mold based on specific product requirements, followed by melting plastic pellets that will form the device components. Once melted, this plastic is injected into the mold under high pressure, where it cools and solidifies into its final shape. This efficient method not only allows for rapid production but also minimizes waste—a crucial factor in today’s environmentally-conscious manufacturing landscape.
What is Medical Injection Molding?
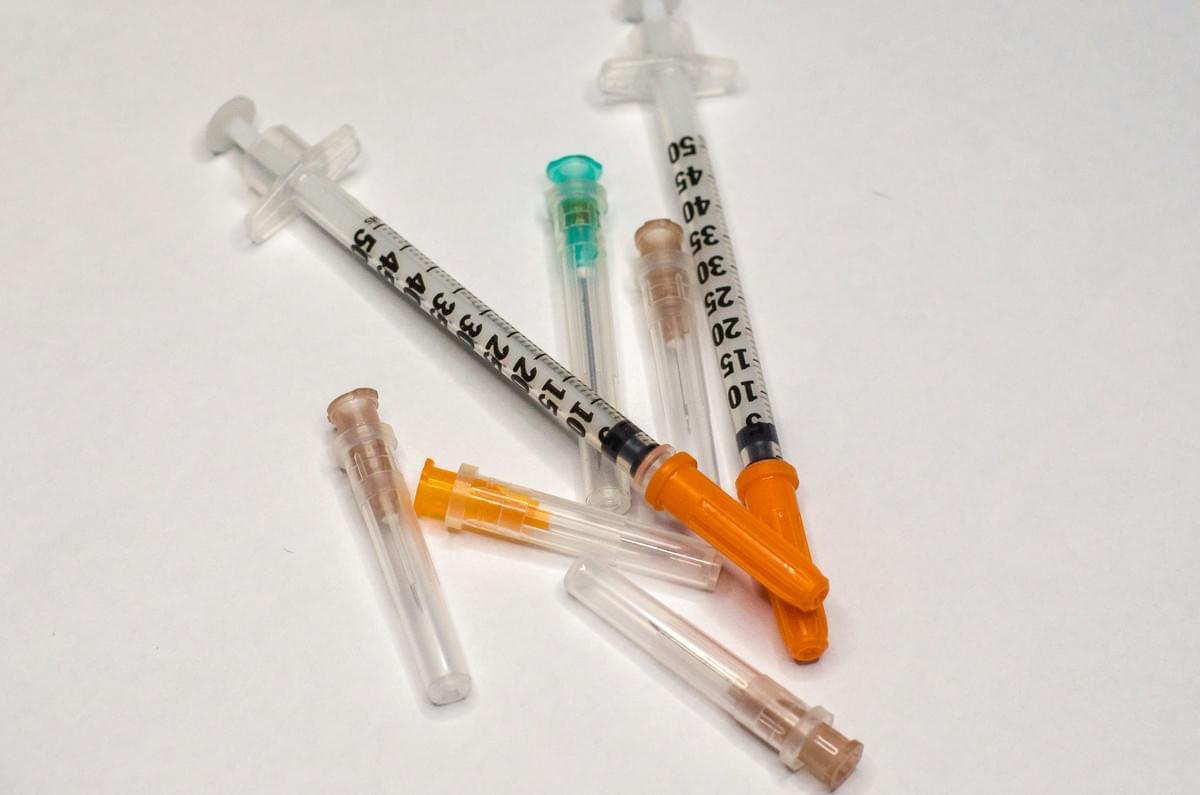
Medical injection molding is a specialized manufacturing process that creates components for medical devices with high precision and reliability. This technique involves injecting molten material into a mold to form intricate shapes, which are then cooled and solidified. The result? High-quality, consistent products essential for the healthcare industry.
Definition and Key Principles
At its core, medical injection molding refers to the production of medical devices using an automated process that ensures uniformity and accuracy in each piece produced. The key principles include temperature control, pressure application, and rapid cooling to maintain the integrity of materials used in sensitive applications like surgical instruments or drug delivery systems. By adhering to strict tolerances and standards, manufacturers can produce components that meet stringent regulatory requirements.
Advantages over Traditional Manufacturing
One of the most significant advantages of injection molding for medical devices is its ability to produce complex geometries with minimal waste. Unlike traditional manufacturing methods such as machining or manual assembly, injection molding allows for high-volume production while maintaining cost-effectiveness. Additionally, this method ensures consistency across batches, which is crucial when dealing with life-saving devices where precision matters.
Applications in the Medical Field
Medical injection molding finds applications across a wide range of products essential in healthcare settings. From syringes and IV components to surgical tools and diagnostic equipment, the versatility of this process makes it invaluable in developing innovative solutions tailored to specific needs. As healthcare continues to evolve, so too does the demand for advanced injection molded products that enhance patient care and safety.
What Products Can be Made from Injection Molding?
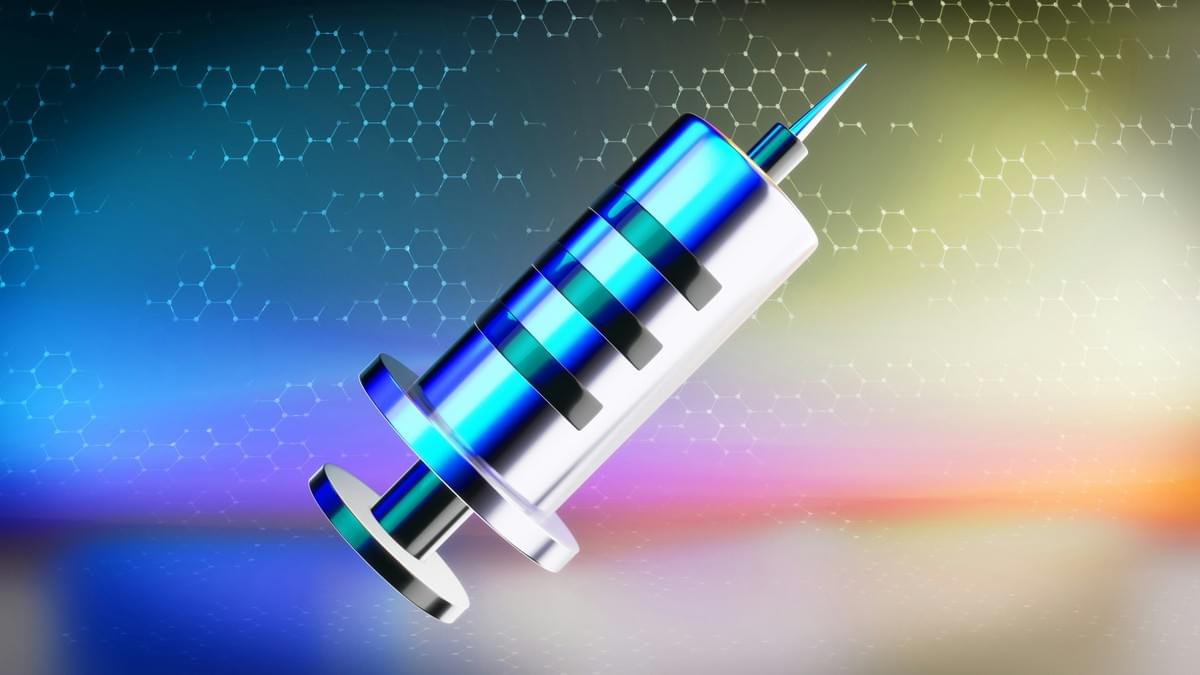
Common Medical Devices and Tools
Common medical devices and tools produced through injection molding include syringes, surgical instruments, and drug delivery systems. These items are essential for patient care, often requiring high levels of accuracy in their design and functionality. The advantages of injection molding medical devices extend beyond mere production efficiency; they also ensure that these critical tools are manufactured with materials that meet safety regulations.
In addition to syringes and surgical instruments, other common products include respiratory masks, IV components, and diagnostic equipment housings. Each of these items benefits from the precision offered by injection molding processes, which allows manufacturers to create complex shapes while maintaining stringent tolerances. As healthcare continues to evolve, so too does the demand for innovative solutions stemming from what is medical injection molding?
Innovation in Customized Medical Solutions
Innovation in customized medical solutions is one of the most exciting aspects of injection molding in healthcare. With advancements in technology, manufacturers can now tailor products specifically designed for individual patients or unique applications within hospitals or clinics. This customization not only enhances patient outcomes but also streamlines workflows within healthcare settings.
For example, prosthetics can be designed using injection molded parts that perfectly fit an individual's anatomy, offering both comfort and functionality. Additionally, specialized surgical tools can be created on-demand using 3D modeling software before being produced through injection molding techniques. This shift towards personalized medicine highlights how versatile and adaptable what products can be made from injection molding truly are.
Examples of Injection Molded Products
Examples of injection molded products span across various categories within the medical field—each demonstrating how this manufacturing process meets specific needs effectively. Some notable examples include orthopedic implants like knee joints or dental crowns crafted through precise molds to ensure compatibility with human anatomy.
Furthermore, everyday items such as pill bottles or disposable gloves are also produced using this method due to its efficiency and cost-effectiveness compared to traditional manufacturing methods. As we explore more about what is the market for medical injection molding?, it becomes clear that these examples reflect a growing trend towards utilizing advanced manufacturing technologies in producing reliable healthcare solutions.
What is the Market for Medical Injection Molding?
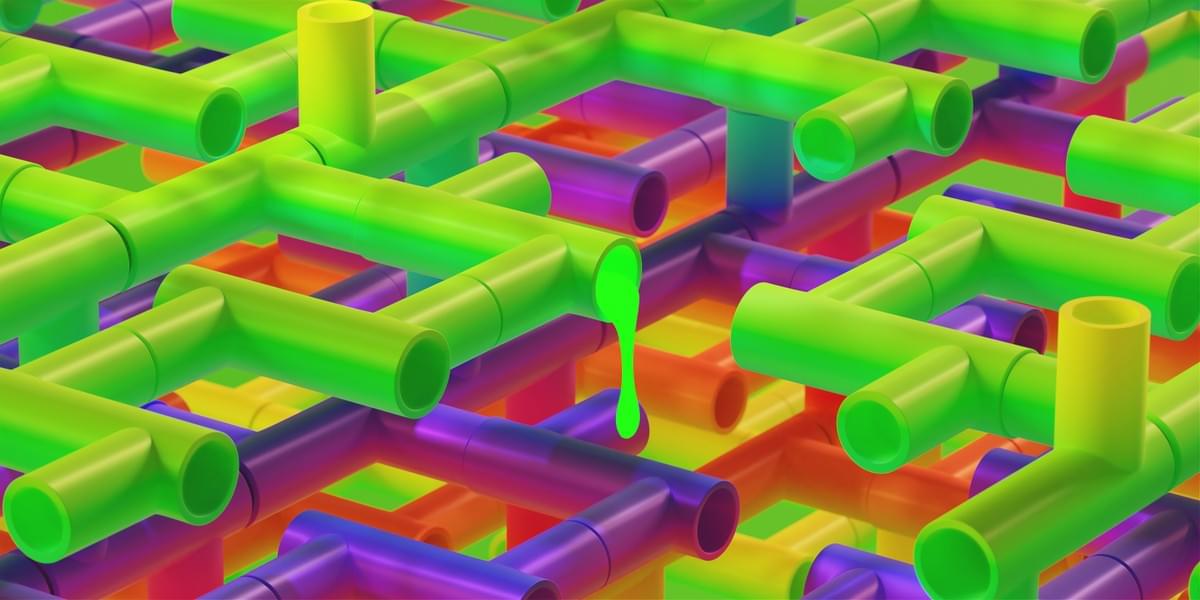
The market for medical injection molding is rapidly evolving, driven by technological advancements and a growing demand for precision-engineered medical devices. This sector has gained traction due to the increasing need for efficient manufacturing processes that can produce high-quality, sterile products at scale. As healthcare continues to innovate, understanding what is medical injection molding becomes essential for stakeholders looking to capitalize on emerging opportunities.
Growth Trends and Statistics
Recent statistics reveal that the global market for injection molding medical devices is projected to grow significantly over the next few years. Factors contributing to this growth include an aging population, rising healthcare expenditures, and an increased focus on advanced manufacturing techniques. According to industry reports, the market could expand at a compound annual growth rate (CAGR) of around 7% through 2028, highlighting just how lucrative this field has become.
Major Players and Market Insights
The landscape of medical injection molding companies is filled with both established giants and innovative newcomers striving to make their mark. Major players like Medtronic, Johnson & Johnson, and Baxter dominate the scene with their extensive portfolios of injection molded products designed for various applications. However, smaller firms are also gaining traction by focusing on specialized niches within the market—showing that there’s room for creativity in what products can be made from injection molding.
Regulatory Factors Influencing the Market
Navigating regulatory factors is crucial in the realm of medical injection molding; compliance with stringent health regulations ensures product safety and efficacy. Organizations such as the FDA in the United States impose rigorous standards that manufacturers must adhere to when producing injection molding medical devices. Understanding these regulations not only influences production timelines but also shapes how companies innovate within this space while maintaining quality assurance.
What Equipment is Used in Injection Molding?
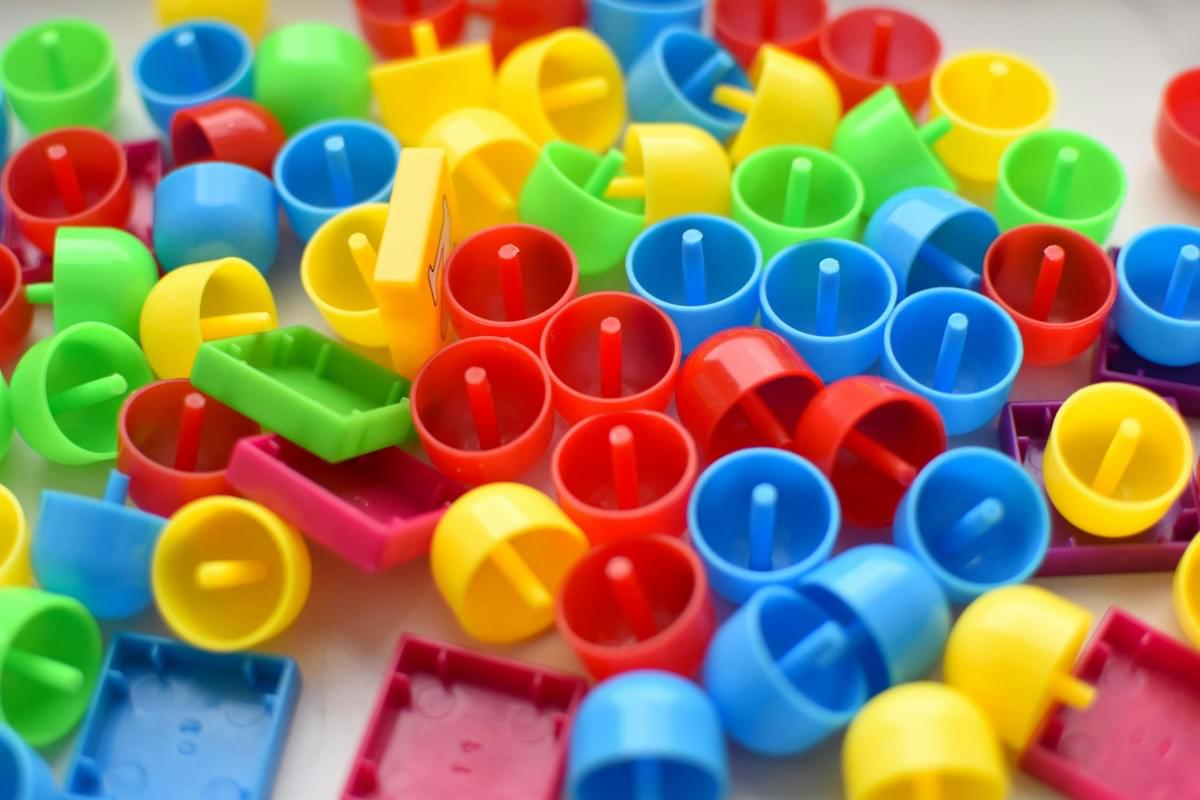
Types of Injection Molding Machines
There are several types of injection molding machines tailored for different applications within the realm of medical device manufacturing. The most common types include hydraulic, electric, and hybrid machines, each offering unique advantages depending on the specific requirements of production. Hydraulic machines are known for their strength and versatility, while electric machines provide greater energy efficiency and precision—ideal for intricate designs often required in medical applications.
Moreover, hybrid machines combine features from both hydraulic and electric systems, striking a balance between performance and energy consumption. When considering what products can be made from injection molding, selecting the right machine type is crucial for achieving optimal results in terms of quality and cost-effectiveness. Ultimately, understanding these machine types helps manufacturers choose the best fit for their specific needs in medical injection molding.
Essential Tools and Technologies
In addition to injection molding machines, several essential tools and technologies enhance the efficiency of producing injection molded products. These include molds that are specifically designed for various medical applications; they dictate the shape and details of each device produced. Advanced technologies like computer-aided design (CAD) software allow engineers to create precise mold designs that meet stringent regulatory standards.
Furthermore, temperature control systems are critical during the injection process to ensure materials flow correctly and solidify uniformly—this is particularly important when producing components that require high levels of accuracy such as surgical instruments or drug delivery systems. Other tools such as robots may also be integrated into production lines to automate tasks like loading materials or packaging finished products efficiently.
Overview of the Injection Molding Process Flow
The process flow in injection molding involves several key stages that transform raw plastic materials into finished medical devices ready for use. Initially, raw plastic pellets are fed into a hopper where they are heated until they melt into a viscous state suitable for shaping. This molten material is then injected into precisely crafted molds under high pressure—a critical step because it ensures that every detail adheres perfectly to specifications outlined during design.
Once injected into molds, cooling systems help solidify the material quickly while maintaining its intended properties; this phase must be carefully monitored to avoid defects often associated with improper cooling rates. Finally, once cooled sufficiently, molds open up to release finished parts which undergo further inspection before being packaged or assembled into larger devices—ensuring compliance with industry standards throughout production.
Injection Molding Medical Devices List
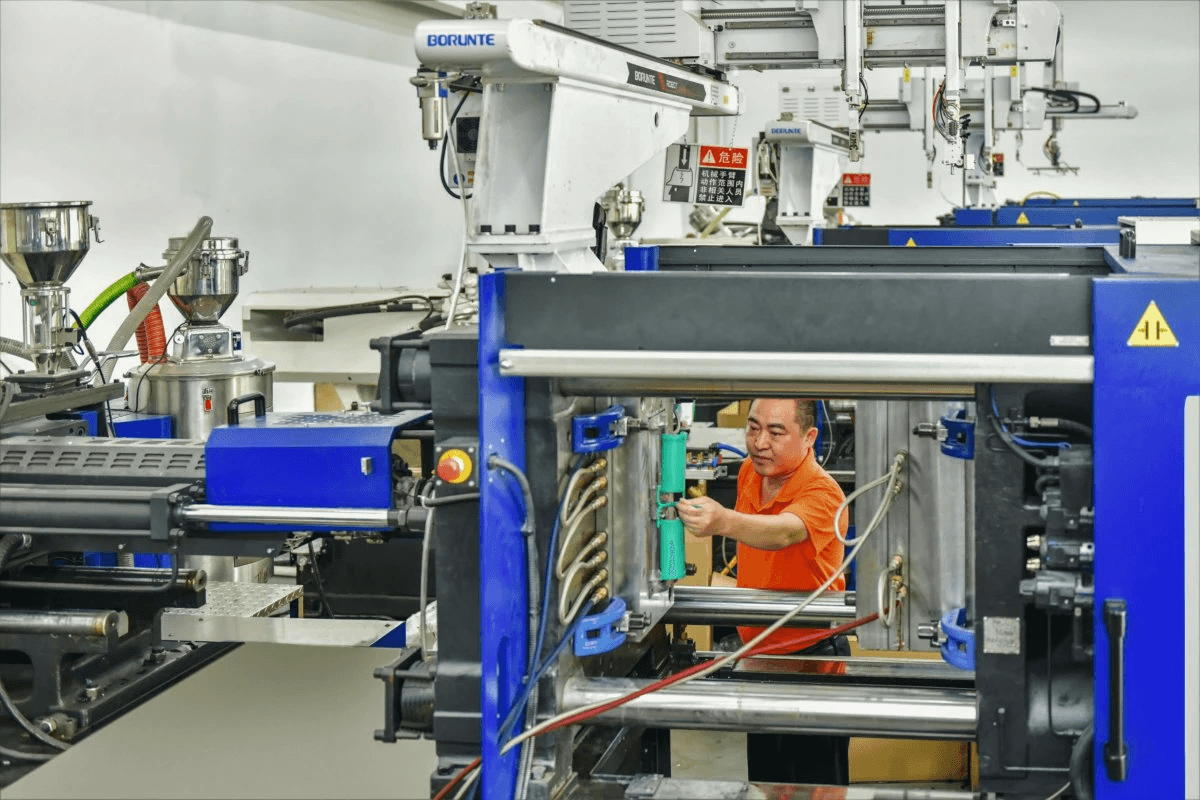
The realm of injection molding medical devices is vast and varied, showcasing how this innovative manufacturing process can revolutionize healthcare products. From simple tools to complex devices, the applications of medical injection molding are extensive and continually evolving. Understanding the categories, key features, and innovations in this field can provide valuable insight into its significance.
Categories of Devices Involved
Medical injection molding encompasses a wide range of device categories that serve diverse functions within the healthcare industry. These include surgical instruments, diagnostic equipment, drug delivery systems, and various consumables like syringes and IV bags. Each category highlights how injection molding can meet stringent quality standards while ensuring precision in design and functionality.
Key Features of Common Products
Common products made through injection molding boast several key features that enhance their usability and safety in medical settings. For instance, many devices are designed for single-use to prevent cross-contamination, while others incorporate ergonomic designs for improved handling by healthcare professionals. Additionally, these products often utilize biocompatible materials to ensure patient safety during use.
Notable Innovations in Medical Injection Molding
The landscape of medical injection molding is continually shaped by notable innovations aimed at improving patient care and device performance. Recent advancements include the development of smart syringes equipped with sensors to monitor dosage accuracy or temperature-sensitive materials that change properties based on environmental conditions. Such innovations not only enhance functionality but also pave the way for more customized solutions tailored to specific medical needs.
Conclusion
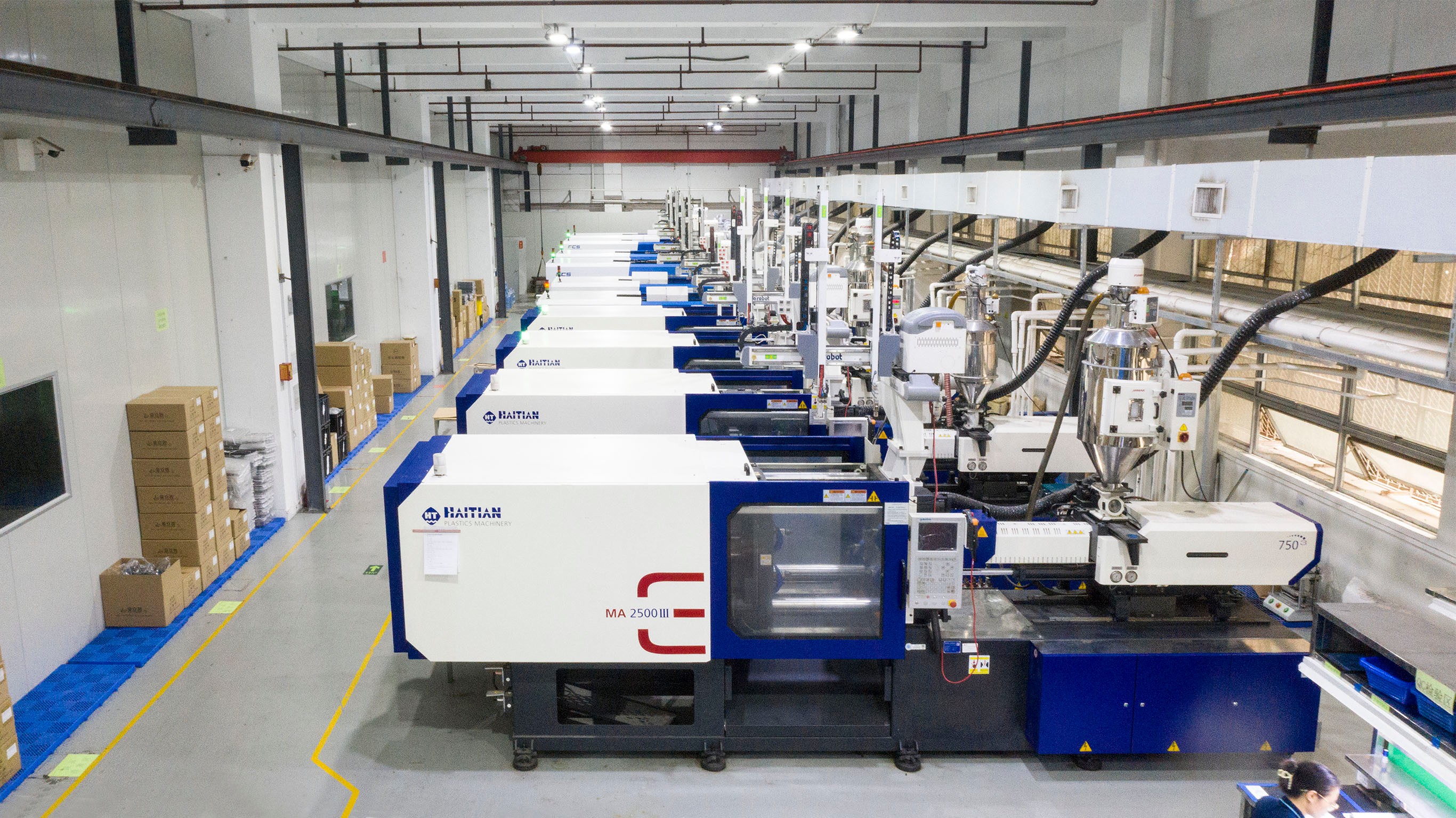
In the ever-evolving landscape of healthcare, medical injection molding stands out as a crucial technology driving innovation and efficiency in the production of medical devices. As we've explored, understanding what is medical injection molding and its applications offers insight into how precision manufacturing shapes the future of healthcare solutions. With the demand for high-quality, reliable products on the rise, staying ahead in this field means embracing future trends and advancements.
Future Trends in Medical Injection Molding
The future of injection molding medical devices looks promising, with several trends emerging that could redefine the industry. Automation and advanced materials are paving the way for more efficient processes and higher-quality products, allowing manufacturers to respond quickly to market demands. Additionally, personalized medicine is gaining traction; thus, customized solutions made through injection molding are likely to become increasingly prevalent.
Leading Medical Injection Molding Companies
When it comes to medical injection molding companies, a few names consistently rise to the top due to their innovation and reliability. These companies leverage cutting-edge technology and adhere strictly to regulatory standards while producing a diverse range of products that cater to various medical needs. By focusing on quality control and customer satisfaction, these leaders set benchmarks for others in the industry.
Why Choose Baoyuan for Your Injection Molding Needs
Choosing Baoyuan for your injection molding needs means partnering with a company dedicated to excellence in every aspect of production. With extensive experience in creating precision-engineered medical devices and an unwavering commitment to quality assurance, Baoyuan stands out from other manufacturers. Whether you're exploring what products can be made from injection molding or looking for specific solutions listed under our comprehensive injection molding medical devices list, Baoyuan has you covered.