Introduction
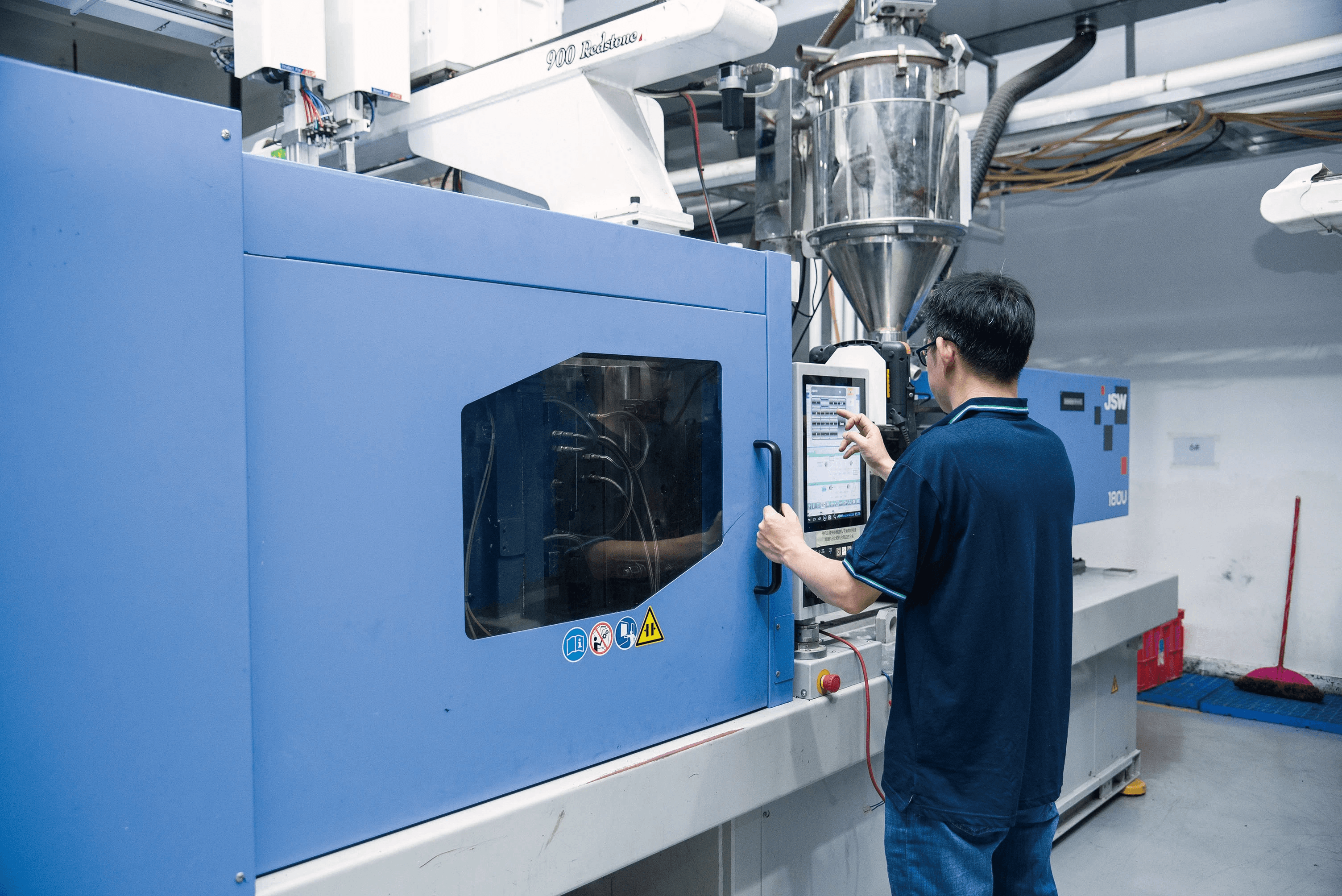
The automotive industry is constantly evolving, and one of the key players in this transformation is automotive injection moulding. This process has revolutionized how manufacturers produce parts, offering efficiency and precision that traditional methods simply cannot match. By utilizing plastic injection molding services, companies can create complex components that meet the high standards required in today's vehicles.
Understanding Automotive Injection Moulding
Automotive injection moulding is a manufacturing process that involves injecting molten plastic into a mold to create specific parts for vehicles. This method allows for the mass production of intricate designs with remarkable accuracy and repeatability. As a result, automotive manufacturers are increasingly turning to this technique to streamline their production lines and enhance product quality.
Significance of Injection Molding in Manufacturing
Injection molding holds significant importance in manufacturing due to its ability to produce high volumes of parts at a lower cost compared to other methods. This cost efficiency makes it an attractive option for automotive companies looking to maximize profits while maintaining quality standards. Furthermore, the speed at which injection molding can deliver finished products plays a crucial role in meeting market demands.
Overview of Injection Moldable Plastics
Injection moldable plastics are specially formulated materials designed for use in the injection molding process. These plastics offer various advantages such as lightweight properties, durability, and design versatility, making them ideal for automotive applications. With numerous plastic injection molding companies investing in research and development, advancements in these materials continue to enhance their performance and sustainability within the industry.
What is Automotive Injection Moulding?
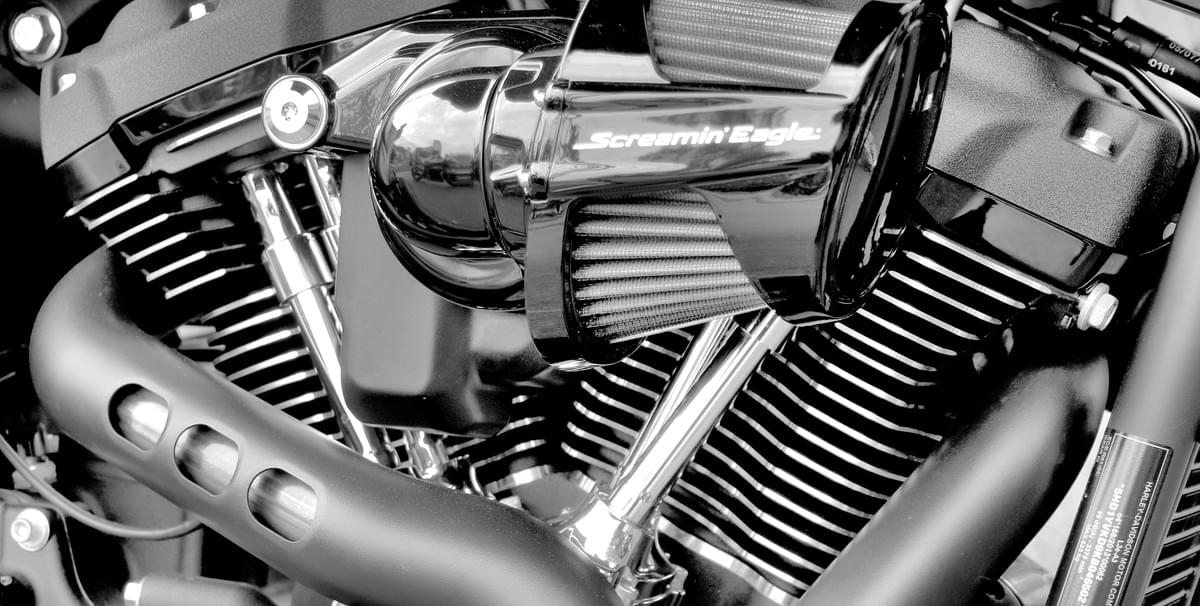
Automotive injection moulding is a manufacturing process specifically tailored for producing plastic components used in vehicles. This technique involves injecting molten plastic into a mold, where it cools and solidifies to form precise shapes. With its ability to create complex geometries and high volumes efficiently, automotive injection moulding has become a cornerstone of modern vehicle production.
Defining the Process
At its core, automotive injection moulding is about precision and efficiency. The process begins with the melting of thermoplastic materials, which are then injected under high pressure into a mold cavity designed for specific parts. Once cooled, the molded plastic can be ejected from the mold, ready for further processing or assembly into vehicles.
This method allows for rapid production cycles and minimizes waste compared to traditional manufacturing techniques. Plastic injection molding services have evolved to include advanced technologies that enhance speed and accuracy while maintaining cost-effectiveness. As a result, automotive manufacturers can produce everything from small clips to large panels with remarkable consistency.
Importance in Automotive Manufacturing
The importance of automotive injection moulding in manufacturing cannot be overstated; it significantly impacts both cost and quality control within the industry. By utilizing plastic injection molding, manufacturers can achieve mass production without sacrificing design integrity or performance characteristics of components. This efficiency translates directly into reduced labor costs and shorter lead times for new vehicle models.
Moreover, as vehicles become increasingly complex with integrated technology and lightweight materials, the role of injection moldable plastics becomes even more critical. These materials not only offer design flexibility but also contribute to fuel efficiency by reducing overall vehicle weight. In an industry where every gram counts towards performance metrics, automotive injection moulding stands as a vital solution.
Common Applications in Vehicles
Automotive injection moulding finds applications across various vehicle components that require durability and precision engineering. Common uses include interior parts such as dashboard components, trim pieces, and center consoles made from high-quality injection moldable plastics that withstand wear over time while enhancing aesthetic appeal. Additionally, exterior parts like bumpers and fenders benefit from this process due to their need for impact resistance.
Furthermore, functional elements such as connectors, housings for electronic devices, and even fuel tanks are produced through plastic injection molding techniques due to their reliability under extreme conditions. The versatility of this process means that nearly every part you see in modern automobiles has likely been shaped by automotive injection moulding at some stage of its life cycle—making it an unsung hero in the world of auto manufacturing.
Benefits of Using Plastic Injection Molding
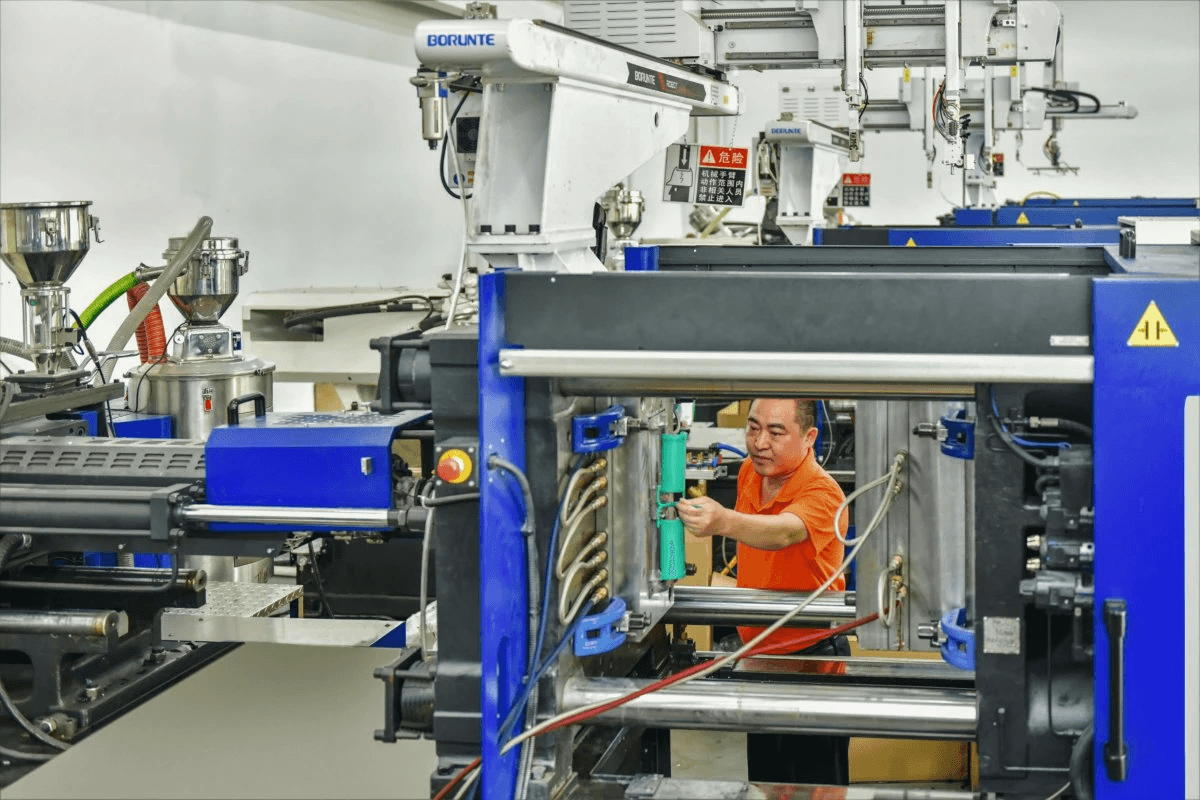
When it comes to automotive injection moulding, the benefits are as clear as a freshly polished car hood. This manufacturing process has revolutionized how parts are produced, making it a go-to choice for many plastic injection molding companies. Let's delve into the key advantages that make plastic injection molding the superhero of the automotive world.
Cost Efficiency and Mass Production
Cost efficiency is one of the standout features of automotive injection moulding that keeps manufacturers coming back for more. The ability to produce large quantities of parts in a short time frame means that production costs can be significantly reduced, allowing companies to maximize their profit margins. With the right plastic injection molding services, manufacturers can streamline operations and achieve economies of scale without compromising on quality.
In addition to cost savings, mass production capabilities mean that businesses can respond swiftly to market demands. When an automotive manufacturer needs thousands of identical components, injection molding tooling enables them to meet those needs with precision and speed. This level of efficiency not only lowers costs but also shortens lead times, ensuring vehicles hit the market faster than ever before.
Moreover, this cost-effective approach extends beyond just initial production; it also reduces waste during manufacturing processes. Since injection moldable plastics can be recycled or reused in subsequent runs, companies find themselves saving on material costs while promoting sustainability—a win-win situation in today’s eco-conscious landscape.
Design Flexibility with Injection Molding
One of the most appealing aspects of plastic injection molding is its remarkable design flexibility. Automotive designers often face challenges when creating intricate shapes or complex geometries; however, with advanced injection molding techniques, these challenges can be easily overcome. The ability to incorporate multiple features into a single part reduces assembly time and enhances overall performance.
Furthermore, designers have access to a vast array of materials when utilizing plastic injection molding services—each offering different properties tailored for specific applications in vehicles. Whether it's lightweight thermoplastics or high-strength composites, these options allow engineers to innovate without being limited by traditional manufacturing constraints. As a result, we see cutting-edge designs that push boundaries while maintaining functionality.
This design flexibility also enables rapid prototyping and testing phases during product development cycles. Manufacturers can quickly create prototypes using various types of injection moldable plastics and evaluate their performance before committing to full-scale production—saving both time and resources while ensuring top-notch quality control throughout the process.
Enhanced Product Durability
Durability is paramount in any automotive component—and here’s where plastic injection molding truly shines! The robust nature of parts produced through this method means they can withstand harsh conditions commonly faced by vehicles on the road today. From extreme temperatures to chemical exposure from fuels or oils, well-designed molded plastics offer exceptional resistance compared to other materials.
Additionally, advancements in material technology have led to even stronger formulations specifically designed for use within automotive applications. Many modern plastics used in automotive injection moulding exhibit properties such as impact resistance and fatigue strength that were once reserved for metals alone! This evolution not only enhances product longevity but also contributes positively toward reducing maintenance costs over time—a major consideration for manufacturers looking at total cost ownership.
Finally—and perhaps most importantly—enhanced durability translates directly into improved safety standards for vehicles themselves! With reliable components sourced from reputable plastic injection molding companies using state-of-the-art techniques like rigorous quality assurance protocols during production processes ensures each part meets stringent industry regulations before reaching consumers’ hands.
Key Players in the Plastic Injection Molding Industry
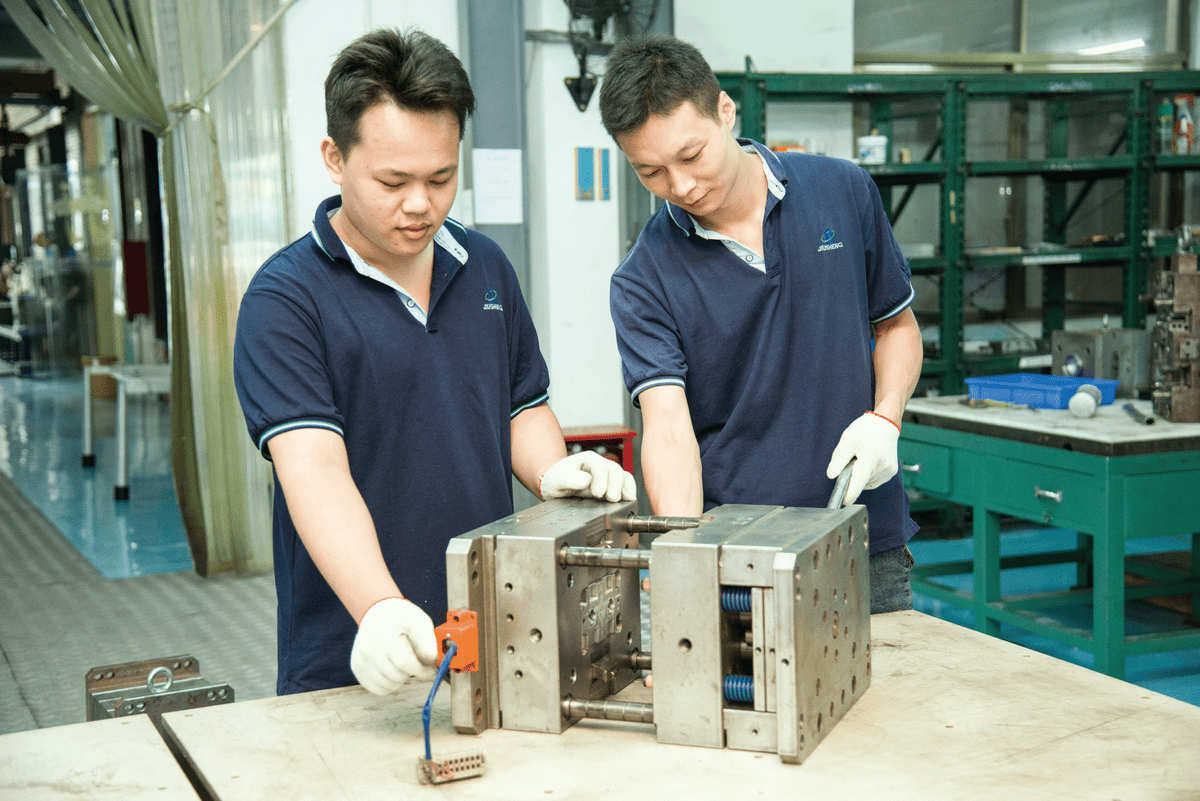
The plastic injection molding industry is a dynamic landscape filled with various companies that specialize in automotive injection moulding and related services. These notable players not only drive innovation but also set standards for quality and efficiency in the manufacturing process. Understanding who these key players are can help businesses make informed decisions when selecting plastic injection molding services.
Notable Plastic Injection Molding Companies
Among the notable plastic injection molding companies, several stand out for their contributions to automotive manufacturing. Companies like BASF, DuPont, and LG Chem have made significant strides in developing advanced injection moldable plastics that enhance vehicle performance and sustainability. Their expertise in injection molding tooling allows them to produce high-quality components that meet the rigorous demands of the automotive sector.
Additionally, smaller firms such as Protolabs and Xcentric Mold & Engineering are gaining traction by offering rapid prototyping and specialized plastic injection molding services tailored for niche markets within the automotive industry. These companies leverage cutting-edge technology to deliver innovative solutions quickly, addressing specific client needs while maintaining high standards of production efficiency.
With a diverse range of capabilities and specialties, these leading plastic injection molding companies play a crucial role in shaping the future of automotive parts manufacturing through their commitment to quality and innovation.
Role of Baoyuan in Injection Molding Services
Baoyuan has emerged as a significant player in providing comprehensive plastic injection molding services tailored specifically for the automotive sector. With a focus on precision engineering, Baoyuan excels at producing complex components using state-of-the-art injection moldable plastics that meet stringent industry standards. Their expertise spans from initial design concepts through to final production, ensuring clients receive end-to-end support throughout the entire process.
One of Baoyuan's standout features is its investment in advanced injection molding tooling technologies that enhance production speed without compromising quality. This capability allows them to offer cost-effective solutions for mass production while maintaining flexibility in design—an essential factor for automotive manufacturers looking to innovate rapidly. By prioritizing customer collaboration and feedback, Baoyuan ensures that their services align closely with market needs.
In an increasingly competitive landscape, Baoyuan’s commitment to sustainability also sets it apart from other plastic injection molding companies by integrating eco-friendly practices into its operations—demonstrating how responsible manufacturing can coexist with profitability.
Comparing Services of Leading Molding Firms
When comparing services among leading plastic injection molding firms, several factors emerge as critical differentiators: technology adoption, customization options, and turnaround times on projects involving automotive injection moulding processes. Companies like BASF focus heavily on material science innovations while others emphasize rapid prototyping capabilities or specialized tooling techniques unique to specific applications within the auto industry.
It's also essential to consider scalability; some firms excel at handling large-volume orders efficiently while others may cater more effectively to small batch productions or custom designs using various types of injection moldable plastics. The ability to pivot between different service offerings often reflects a company’s adaptability—a vital trait as consumer demands evolve over time.
Ultimately, selecting the right partner among these top-tier firms involves assessing how well they align with your specific project goals regarding both technical requirements and budget constraints within your automotive projects involving plastic injection molding services.
The Injection Molding Tooling Process
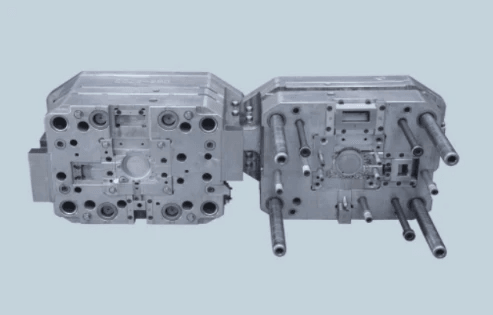
The injection molding tooling process is a critical aspect of automotive injection moulding, serving as the foundation for producing high-quality plastic components. This process involves creating specialized molds that shape the molten plastic into desired forms, ensuring precision and consistency in manufacturing. Understanding the intricacies of injection molding tooling is essential for anyone involved in plastic injection molding services.
Understanding Injection Molding Tooling
Injection molding tooling refers to the design and fabrication of molds used in the plastic injection molding process. These molds are typically made from durable materials like steel or aluminum, capable of withstanding high pressures and temperatures during production. The quality and design of these tools directly impact the efficiency of manufacturing automotive parts, making them a crucial element in automotive injection moulding.
In essence, effective tooling can significantly reduce production costs while enhancing product quality, making it vital for plastic injection molding companies to invest in advanced tooling techniques. Properly designed molds allow for quicker cycle times and less material waste, contributing to more sustainable manufacturing practices within the industry. As technology advances, so too does the sophistication of injection moldable plastics and their associated tooling processes.
Steps Involved in Tool Design
The tool design process consists of several key steps that ensure optimal functionality and performance during production runs. Initially, engineers collaborate with designers to create a detailed blueprint based on specific requirements for each automotive component being produced through plastic injection molding services. This blueprint includes considerations such as part geometry, material selection, cooling channels, and ejection mechanisms.
Once the design is finalized, it moves into prototyping where a test mold may be created to identify any potential issues before full-scale production begins. During this phase, adjustments can be made to improve accuracy or efficiency based on testing results—ensuring that when it comes time for actual production runs using injection moldable plastics, everything operates smoothly and effectively.
Finally, after thorough testing and validation of prototypes are completed successfully, full-scale molds are manufactured using precision machining techniques. This careful approach ensures that each step aligns with best practices in automotive injection moulding while maintaining cost-effectiveness throughout the entire process.
Quality Assurance and Testing Procedures
Quality assurance is paramount when it comes to ensuring that products manufactured through plastic injection molding meet industry standards and consumer expectations. Comprehensive testing procedures are implemented at various stages—from initial tool design through final product inspection—to guarantee consistency in dimensions and performance characteristics across all produced parts.
One common practice involves conducting melt flow index tests on raw materials before they enter production; this provides insight into how well an injected material will perform under different conditions encountered during manufacturing processes involving automotive applications. Additionally, once components are molded from these materials using specialized tools designed specifically for their intended use cases—rigorous inspections follow suit—including dimensional checks against CAD specifications as well as functional tests simulating real-world scenarios.
By adhering strictly to established quality assurance protocols throughout every phase—from tool design through final inspection—plastic injection molding companies can ensure reliable outcomes while minimizing defects or inconsistencies inherent within mass-produced items like those found within modern vehicles today!
Innovations in Injection Moldable Plastics
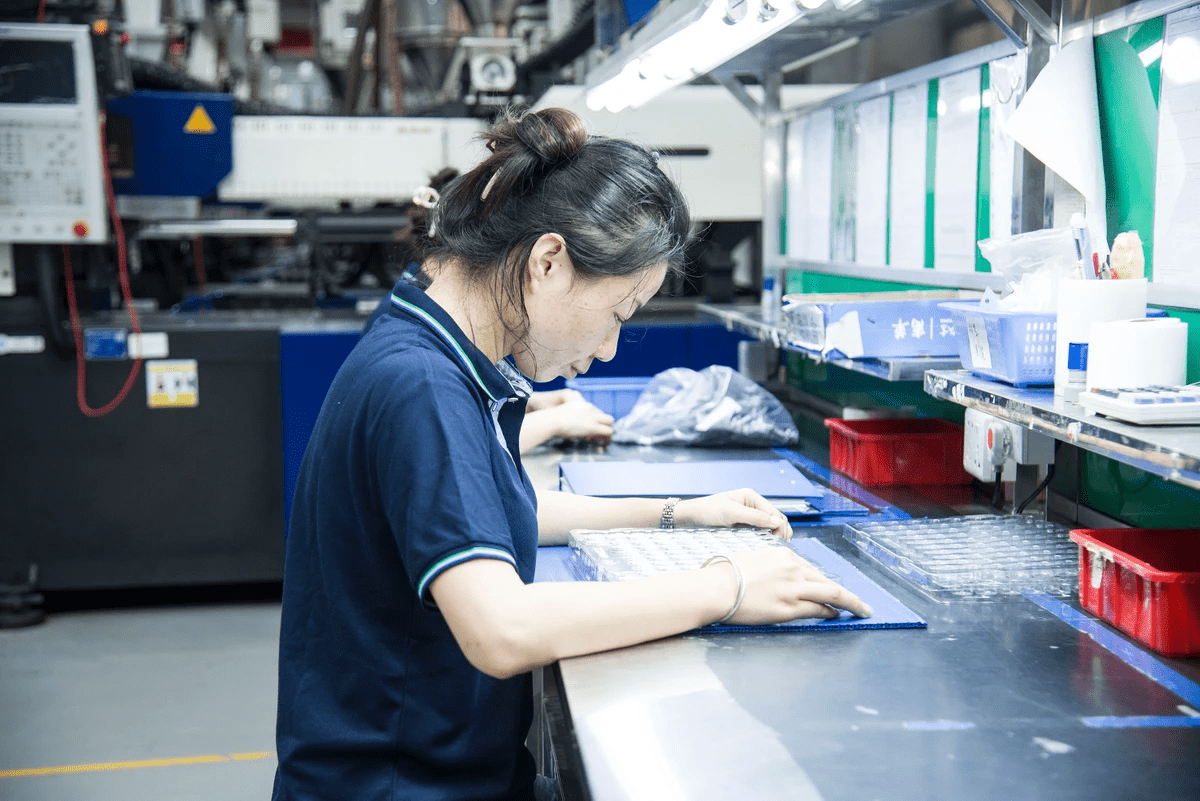
Innovation in the realm of injection moldable plastics is driving the automotive industry towards greater efficiency, sustainability, and performance. As automotive manufacturers increasingly rely on plastic injection molding services, advancements in material technology are enabling the production of lighter, stronger components that enhance vehicle performance. This section delves into key innovations shaping the future of automotive injection moulding.
Advancements in Material Technology
The evolution of material technology has been a game changer for automotive injection moulding. New formulations of injection moldable plastics are designed to withstand extreme temperatures and stress while maintaining lightweight properties that contribute to fuel efficiency. Additionally, these advanced materials often incorporate features such as enhanced impact resistance and improved aesthetics, making them ideal for various vehicle applications.
Plastic injection molding companies are continuously exploring new polymers and composite materials that further optimize production processes and product quality. For instance, thermoplastic elastomers (TPEs) offer flexibility akin to rubber while being easier to mold and recycle than traditional rubber compounds. With ongoing research into bio-based plastics and high-performance composites, the future looks bright for innovations in automotive applications.
Eco-Friendly Practices in Molding
Sustainability is becoming a cornerstone of modern manufacturing practices, including plastic injection molding. Many companies are now adopting eco-friendly practices that minimize waste and reduce environmental impact throughout the injection molding tooling process. These initiatives include utilizing recycled materials for producing new components and implementing energy-efficient machinery during production.
Moreover, advancements such as closed-loop systems help ensure that excess materials are captured and reused rather than discarded, promoting a circular economy within the industry. By embracing sustainable practices, plastic injection molding services not only meet regulatory requirements but also cater to an increasingly environmentally conscious consumer base looking for greener vehicle options. The integration of eco-friendly methods into automotive injection moulding reflects a significant shift towards responsible manufacturing.
Future Trends in Automotive Manufacturing
Looking ahead, several trends are poised to redefine how automotive manufacturers approach plastic injection molding. One notable trend is the increasing integration of smart technologies within molded components; sensors embedded within parts can monitor performance metrics or even provide real-time data back to manufacturers for predictive maintenance purposes. This kind of innovation exemplifies how automotive injection moulding can evolve beyond traditional uses.
Additionally, 3D printing is beginning to intersect with conventional plastic injection molding processes—enabling rapid prototyping and low-volume production runs without sacrificing quality or performance standards typically associated with mass production methods. As electric vehicles gain traction globally, there will be a rising demand for lightweight yet durable materials tailored specifically for EV applications through innovative plastic solutions.
In summary, innovations in material technology paired with eco-friendly practices set the stage for exciting developments in automotive manufacturing through improved plastic injection molding techniques—ensuring that this sector remains at the forefront of technological advancement while addressing environmental concerns.
Conclusion
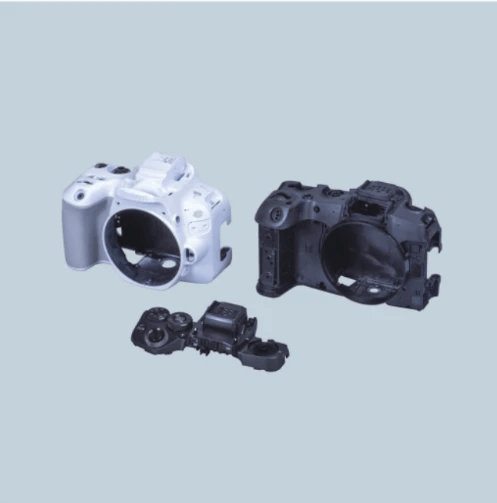
In summary, automotive injection moulding is a cornerstone of modern vehicle manufacturing, providing numerous benefits that enhance production efficiency and product quality. The use of plastic injection molding not only streamlines mass production but also allows for intricate designs and robust components. As the automotive industry continues to evolve, the role of injection moldable plastics will only become more significant.
Recap of Automotive Injection Moulding Benefits
Automotive injection moulding offers a plethora of advantages that make it indispensable in today’s manufacturing landscape. Cost efficiency stands out as one of the primary benefits, enabling manufacturers to produce large quantities without compromising on quality or design flexibility. Additionally, the durability of products created through plastic injection molding ensures they can withstand the rigors of automotive applications, ultimately leading to greater customer satisfaction.
Choosing the Right Plastic Injection Molding Services
Selecting the right plastic injection molding services can be a game-changer for any automotive manufacturer looking to optimize their production process. It’s essential to consider factors such as experience, technology used in injection molding tooling, and customer service when evaluating different plastic injection molding companies. By choosing wisely, manufacturers can leverage innovative solutions that enhance their product offerings while maintaining cost-effectiveness.
Future of Injection Molding in Automotive Industry
Looking ahead, the future of injection molding in the automotive industry appears bright with ongoing advancements in material technology and eco-friendly practices gaining traction. Manufacturers are increasingly focusing on sustainable practices when using injection moldable plastics, which not only helps reduce environmental impact but also appeals to conscious consumers. As innovations continue to emerge within this field, we can expect even more exciting developments that will shape how vehicles are designed and produced.