Introduction
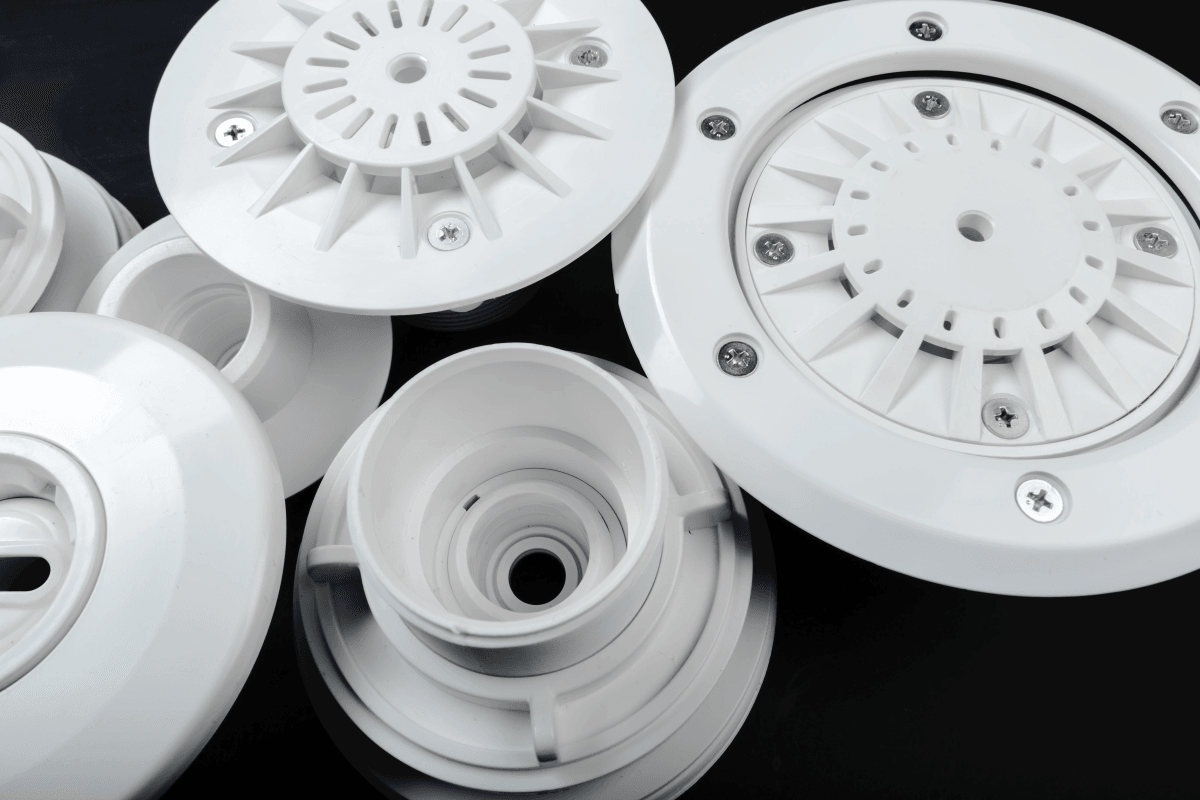
When it comes to plastic manufacturing, there are various methods and processes involved in creating different types of plastics. Understanding the different types of plastic manufacturing methods is crucial for businesses and manufacturers looking to produce high-quality plastic products. With the importance of knowing plastic manufacturing options, companies can make informed decisions about which process is best suited for their specific needs.
Understanding Plastic Manufacturing Methods
Plastic manufacturing methods encompass a wide range of techniques such as injection molding, blow molding, extrusion molding, rotational molding, and thermoforming. Each method has its own unique set of advantages and limitations that cater to specific applications and industries. Injection molding, for example, is ideal for high-volume production of complex plastic parts with tight tolerances. On the other hand, rotational molding is well-suited for creating large, hollow parts such as tanks and containers. Understanding the strengths and weaknesses of each method is crucial in determining the most suitable approach for a particular manufacturing project.
Exploring Different Types of Plastic Manufacturing
There are seven most common types of plastic: polyethylene (PE), polypropylene (PP), polyvinyl chloride (PVC), polystyrene (PS), polyethylene terephthalate (PET), acrylic (PMMA), and polycarbonate (PC). These plastics are manufactured using various processes like injection molding, blow molding, extrusion molding, rotational molding, and thermoforming.
In addition to the common types of plastic and manufacturing processes mentioned earlier, it's important to consider the environmental impact of plastic manufacturing. With growing concerns about plastic pollution and its effects on the planet, manufacturers are exploring more sustainable options such as bioplastics and recycled plastics. These alternatives can help reduce the carbon footprint of plastic production and minimize the amount of plastic waste ending up in landfills or oceans.
The Importance of Knowing Plastic Manufacturing Options
Understanding the different types of plastic manufacturing options is essential for businesses to choose the right process that aligns with their production requirements and product specifications. By knowing the available options, companies can make informed decisions on which plastics manufacturing process is right for them. Injection molding, for example, is ideal for high-volume production of complex plastic parts with tight tolerances. On the other hand, blow molding is more suitable for producing hollow objects such as bottles and containers. By understanding these distinctions, businesses can optimize their production processes and achieve cost-effective results.
Injection Molding
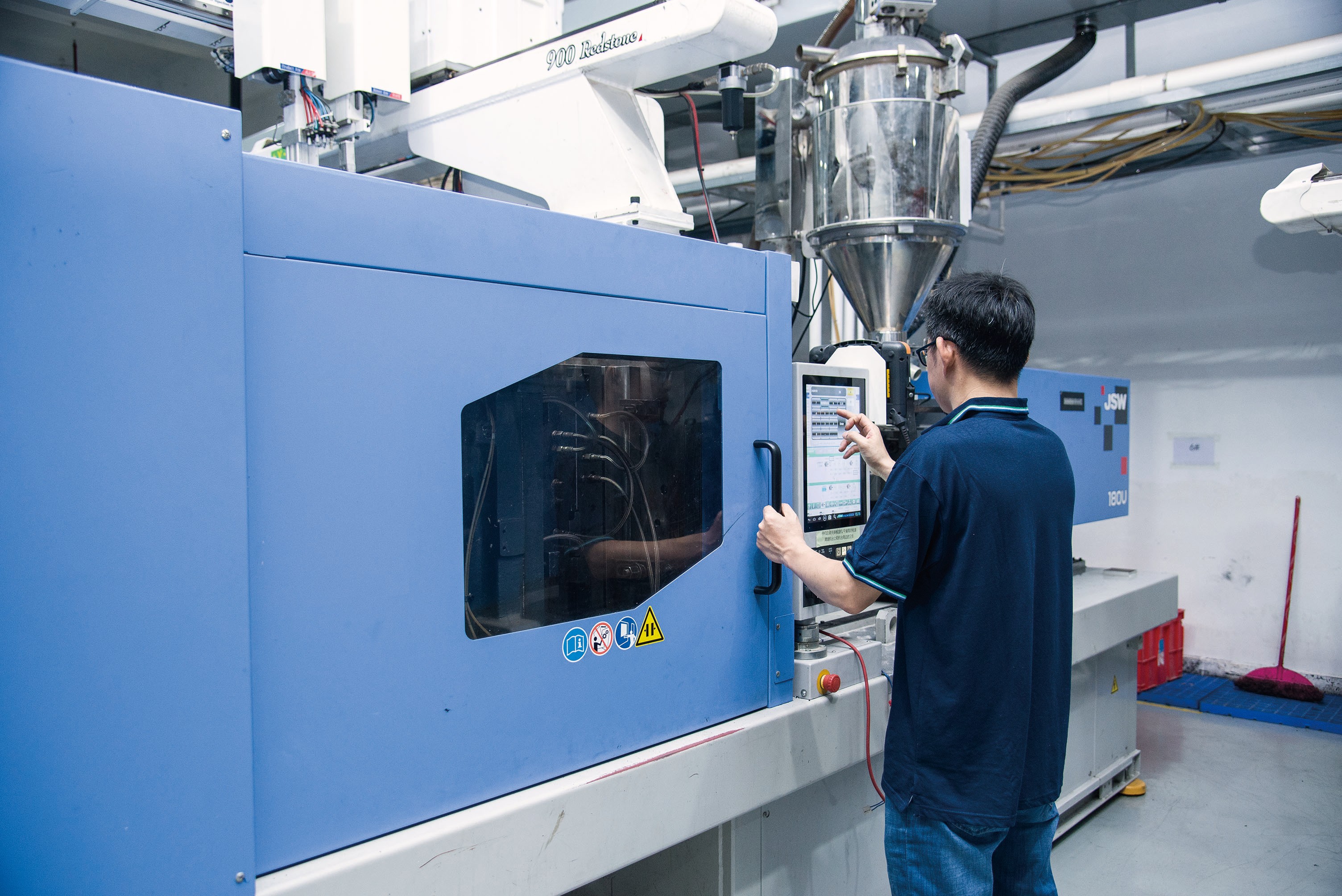
When it comes to plastic manufacturing, injection molding is a popular method used by many companies, including Baoyuan. This process involves injecting molten plastic into a mold cavity, allowing it to cool and harden before being ejected as a finished product. The advantages of injection molding include high production rates, repeatable and precise results, and the ability to use a wide range of materials. However, limitations such as high initial tooling costs and the need for uniform wall thickness should be considered.
Baoyuan's Expertise in Injection Molding
Baoyuan has honed its expertise in injection molding over the years, mastering the intricacies of this manufacturing method to deliver top-quality plastic products to its clients. With state-of-the-art equipment and a team of skilled professionals, Baoyuan can handle complex designs and intricate details with ease, ensuring that every product meets the highest standards of quality.
In addition to its technical expertise, Baoyuan also prides itself on its ability to provide cost-effective solutions for its clients. By optimizing the injection molding process and utilizing efficient production techniques, Baoyuan is able to minimize waste and reduce overall manufacturing costs without compromising on quality. This not only benefits the clients by offering competitive pricing but also contributes to a more sustainable approach to plastic product manufacturing.
Advantages and Limitations of Injection Molding
The advantages of injection molding make it an attractive option for producing a wide variety of plastic products in large quantities. Its ability to create highly detailed parts with excellent surface finishes sets it apart from other methods. However, the initial tooling costs can be significant, making it less suitable for small production runs or prototypes.
Additionally, injection molding offers the advantage of high efficiency and repeatability, ensuring consistent quality across large production runs. This makes it a cost-effective option for mass-producing plastic parts, especially when compared to other manufacturing methods. However, the need for specialized equipment and skilled operators can add to the overall production costs, making it important to carefully weigh the benefits against the limitations.
Innovative Techniques in Injection Molding
Innovation is key in the world of injection molding, and Baoyuan is at the forefront of developing new techniques to improve efficiency and quality. From advanced mold design software to cutting-edge material technologies, Baoyuan continues to push the boundaries of what is possible with injection molding.
Baoyuan's dedication to innovation extends beyond just the manufacturing process itself. The company also invests heavily in research and development to discover new materials and techniques that can revolutionize the industry. By staying ahead of the curve, Baoyuan ensures that its clients have access to the most advanced and high-quality products on the market.
Blow Molding
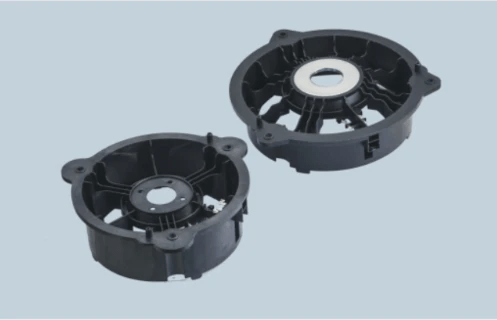
Blow molding is one of the most common types of plastic manufacturing, involving the use of air pressure to inflate softened plastic into a mold cavity. There are several variations in blow molding techniques, including extrusion blow molding, injection blow molding, and stretch blow molding. Each technique offers unique benefits and is suitable for different applications in plastic manufacturing.
Variations in Blow Molding Techniques
Extrusion blow molding involves the production of hollow products such as bottles and containers by extruding a parison (hollow tube) into a mold cavity and then blowing air into it to expand the plastic against the mold walls. Injection blow molding combines injection molding and blow molding to create high-precision products with complex shapes, such as medical equipment and small consumer goods. Stretch blow molding is commonly used to produce PET bottles for beverages, offering high clarity and impact resistance.
Applications of Blow Molding in Plastic Manufacturing
Blow molding techniques are widely used in various industries for producing a diverse range of products, including packaging materials, automotive components, toys, and household items. The ability to create lightweight yet durable products makes blow molding an ideal choice for manufacturers looking to optimize material usage while maintaining product quality and performance.
Extrusion Molding
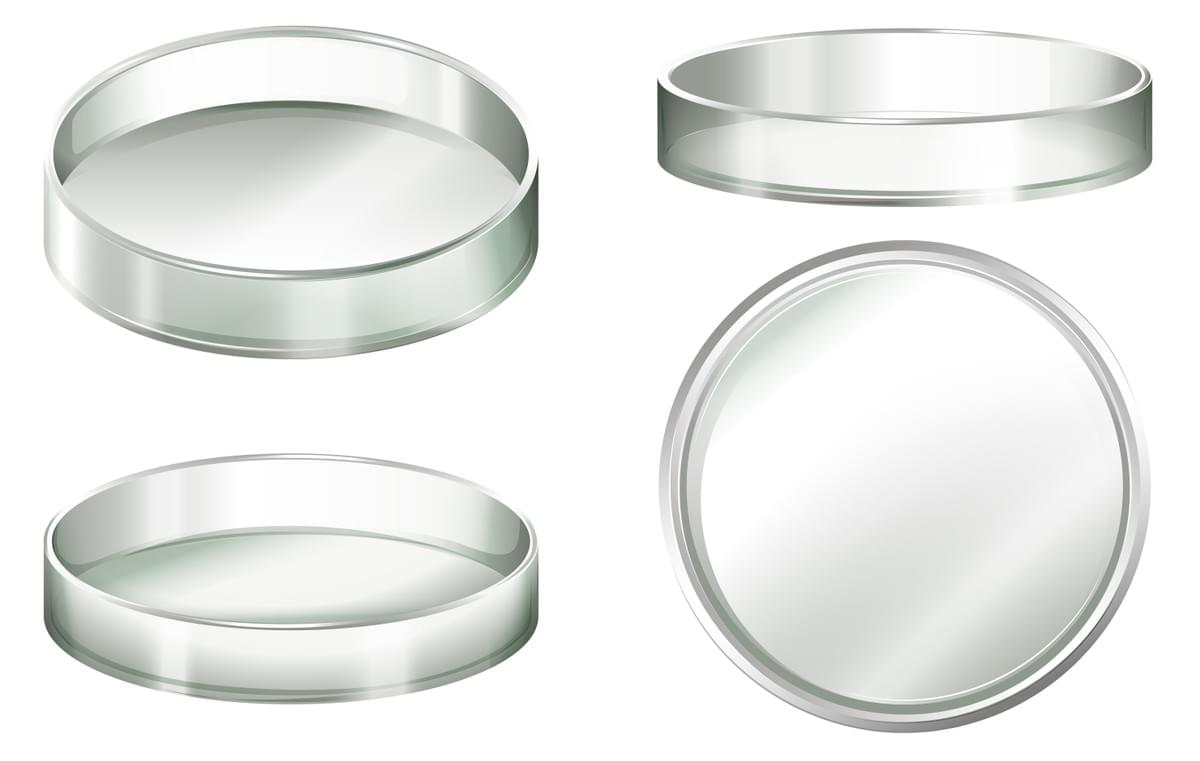
Extrusion molding is one of the most common types of plastic manufacturing methods, involving the use of a die to shape molten plastic into a continuous profile. This process allows for the production of long, uniform shapes with consistent cross-sections, making it ideal for creating items such as pipes, tubing, and window frames.
Unique Features of Extrusion Molding
One unique feature of extrusion molding is its ability to produce complex shapes with varying thicknesses and intricate designs. This method also offers the advantage of producing seamless products without the need for additional assembly or joining processes. Additionally, extrusion molding can accommodate a wide range of thermoplastic materials, offering flexibility in material selection for different applications.
Customization Opportunities in Extrusion Molding
Extrusion molding provides extensive customization opportunities, allowing for the creation of products with specific dimensions and properties tailored to meet individual requirements. With the ability to control parameters such as temperature, speed, and pressure during the extrusion process, manufacturers can achieve precise material properties and product characteristics. This level of customization makes extrusion molding suitable for a diverse range of industries and applications.
Remember that choosing the right plastic manufacturing process is crucial to achieving high-quality products that meet your specific needs. Understanding the unique features and customization opportunities offered by each method will help you make an informed decision on which type of plastic manufacturing is right for you. Baoyuan's expertise in extrusion molding ensures that you have a reliable partner in delivering top-notch plastic products tailored to your exact specifications.
Rotational Molding
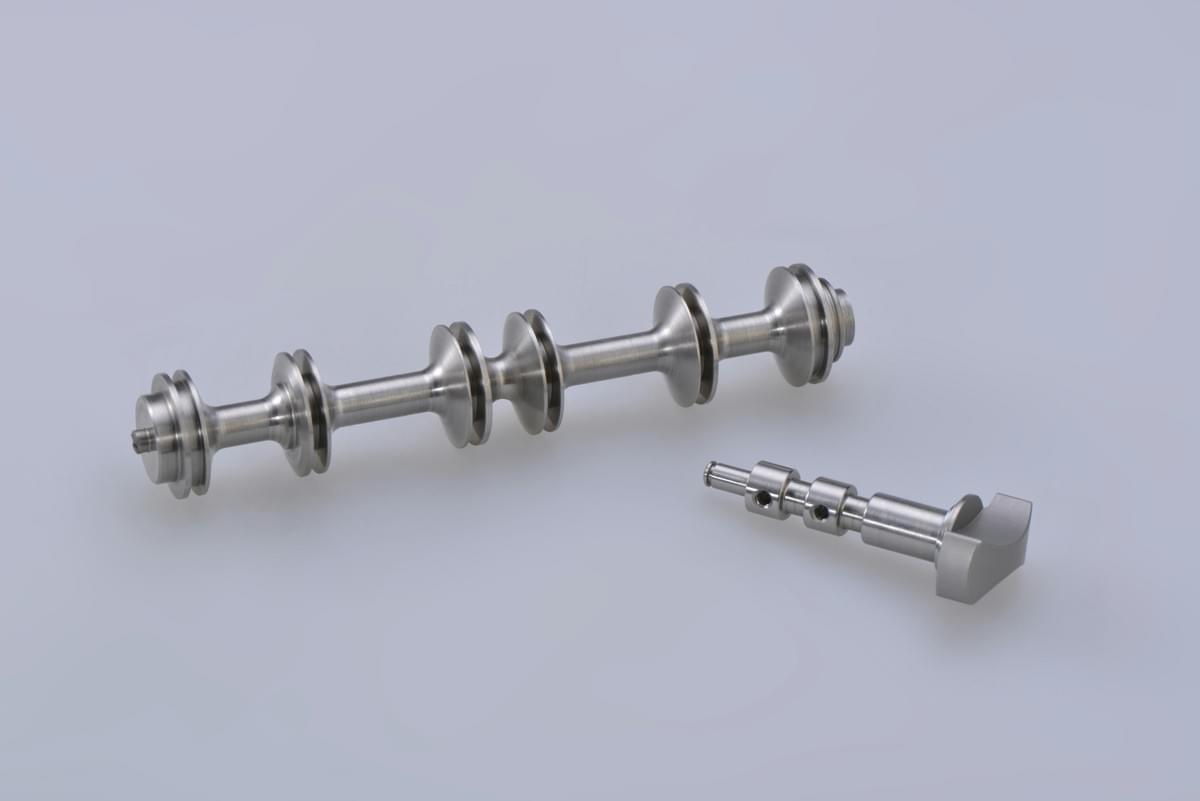
Rotational molding is one of the most versatile types of plastic manufacturing methods, offering a wide range of benefits for producing hollow plastic products. Its ability to create seamless, stress-free parts makes it ideal for items like storage tanks, playground equipment, and even medical devices.
Benefits of Rotational Molding
One of the key advantages of rotational molding is its ability to produce large, complex parts with uniform wall thickness and high durability. This makes it an excellent choice for items that need to withstand harsh environments or heavy use. Additionally, rotational molding allows for intricate designs and shapes that would be difficult or impossible to achieve with other manufacturing methods.
Environmental Impact of Rotational Molding
In terms of sustainability, rotational molding stands out as a relatively eco-friendly process. The method typically uses powdered resin instead of liquid, which reduces material waste and allows for easy recycling. Additionally, the energy consumption during production is lower compared to other plastic manufacturing options, making it a greener choice for environmentally conscious businesses.
Thermoforming

Thermoforming is one of the most versatile types of plastic manufacturing, offering a wide range of process innovations. From pressure forming to vacuum forming, thermoforming allows for intricate designs and complex shapes to be achieved with ease. This method is ideal for producing items such as packaging, trays, and even automotive parts.
Process Innovations in Thermoforming
In recent years, advancements in thermoforming technology have revolutionized the process. New techniques such as twin sheet forming and plug assist forming have allowed for greater design flexibility and improved structural integrity in thermoformed products. These innovations have expanded the possibilities for using thermoforming in various industries, making it a highly sought-after manufacturing method.
Sustainability Aspects of Thermoforming
Thermoforming is also making strides in sustainability, with the ability to use recycled materials and produce minimal waste during the manufacturing process. By incorporating eco-friendly materials and optimizing energy usage, thermoforming has become an environmentally conscious choice for plastic manufacturing. This makes it an attractive option for businesses looking to reduce their carbon footprint while still achieving high-quality products.
Conclusion
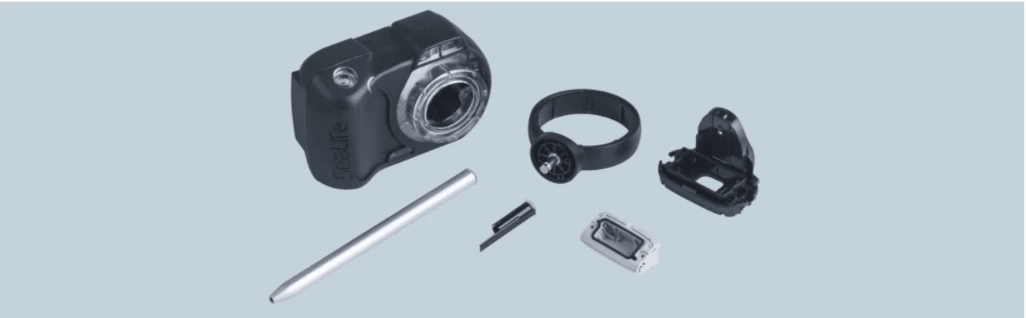
When it comes to plastic manufacturing, it's crucial to choose the right process for your specific needs. With various types of plastic manufacturing methods available, such as injection molding, blow molding, extrusion molding, rotational molding, and thermoforming, it's important to consider factors like production volume, design complexity, and material requirements. Baoyuan is your trusted partner in quality plastic injection molding manufacturing, offering expertise in a wide range of plastic manufacturing options and processes.
Choosing the Right Plastic Manufacturing Process
Selecting the appropriate plastic manufacturing process is essential for achieving the desired results. Whether you need high-volume production or intricate designs, understanding the advantages and limitations of each method will help you make an informed decision that aligns with your project goals.
When considering the right plastic manufacturing process, it's important to evaluate the environmental impact of each method. Some processes may produce more waste or emissions than others, so understanding the sustainability implications can help you make a responsible choice for your project. Additionally, consider the cost implications of each manufacturing process. Some methods may require significant investment in tooling and equipment, while others may be more cost-effective for smaller production runs. By weighing these factors, you can ensure that your chosen manufacturing process aligns with your budget and environmental values.
Factors to Consider in Plastic Manufacturing Selection
Factors such as cost-effectiveness, lead time, material properties, and environmental impact should be taken into account when selecting a plastic manufacturing process. By evaluating these considerations alongside your specific project requirements, you can determine which method best suits your needs.
When considering cost-effectiveness in plastic manufacturing selection, it's important to weigh the initial investment of each process against the long-term benefits and potential savings. While some methods may have a higher upfront cost, they could result in lower production costs over time due to increased efficiency or reduced material waste. By carefully analyzing the financial implications of each option, you can make an informed decision that aligns with your budget and overall business goals.
Baoyuan: Your Partner in Quality Plastic Injection Molding Manufacturing
Baoyuan specializes in providing top-notch plastic injection molding services tailored to meet diverse industry demands. With a commitment to innovation and excellence, Baoyuan offers a comprehensive range of solutions to address various manufacturing challenges while ensuring superior quality and customer satisfaction.
At Baoyuan, we understand the importance of staying ahead of the curve in the ever-evolving manufacturing industry. That's why we invest in cutting-edge technology and equipment to ensure our clients benefit from the latest advancements in plastic injection molding. Our team of experienced engineers and technicians are constantly exploring new techniques and materials to offer innovative solutions that drive efficiency and cost-effectiveness for our customers.