Introduction
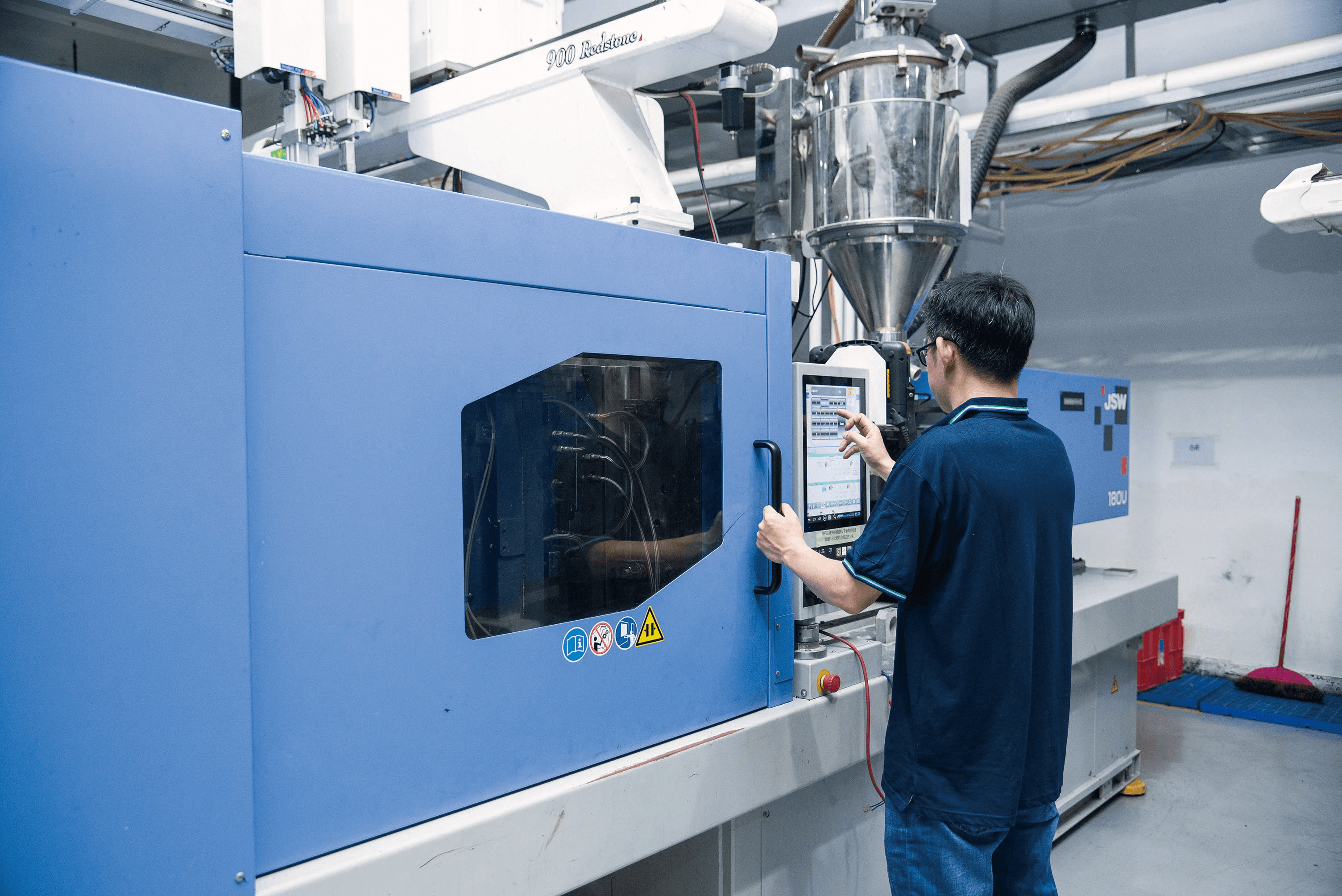
Injection molding color mixing is a fascinating yet challenging aspect of the manufacturing process that can make or break a product’s appeal. As manufacturers strive to create visually appealing plastic parts, they often encounter hurdles that can lead to inconsistent colors and even discoloration. Understanding these challenges is essential for anyone looking to optimize their production processes and deliver high-quality products.
Common Challenges in Injection Molding Color Mixing
One of the most common challenges in injection molding color mixing is achieving uniformity across batches, which is crucial for maintaining brand integrity. Variations in pigment distribution can lead to noticeable differences in shade, leaving manufacturers wondering, What causes discoloration in injection molding? Additionally, factors such as equipment calibration and material quality can complicate the mixing process further, making it imperative to implement best practices for consistency.
The Impact of Discoloration on Quality
Discoloration not only affects the aesthetic appeal of a product but also its perceived quality and marketability. When consumers notice inconsistencies or unexpected hues, it raises questions about the overall craftsmanship and reliability of the item—something no manufacturer wants to face. Therefore, understanding how to make a plastic color that meets expectations becomes pivotal for success in today’s competitive landscape.
Key Factors for Achieving Ideal Colors
Achieving ideal colors in injection molding involves several key factors including pigment selection, processing conditions, and equipment performance. Knowing what is the difference between core and mold can also influence how colors manifest during production; each plays a distinct role in color application and final appearance. By honing in on these elements, manufacturers can significantly enhance their ability to produce vibrant and consistent colors while minimizing issues like discoloration throughout their processes.
Understanding Injection Molding Color Mixing
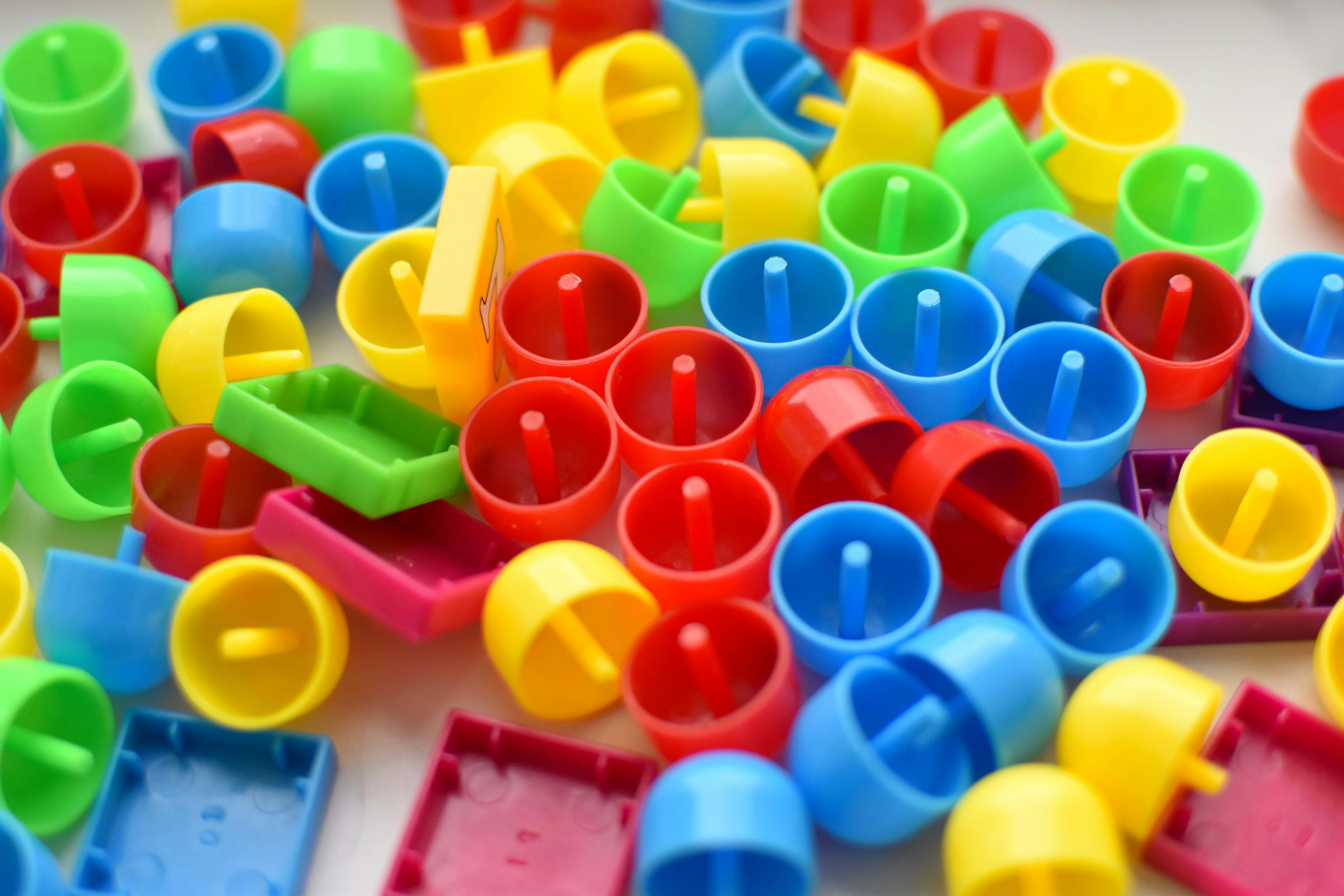
Injection molding color mixing is an intricate dance of science and art, where the right pigments and resins come together to create a vivid palette for plastic products. The process involves not just choosing colors but ensuring they blend seamlessly without losing their vibrancy or consistency. By grasping the underlying principles of how colors interact in plastics, manufacturers can avoid common pitfalls and deliver products that meet both aesthetic and functional demands.
The Science Behind Color Mixing in Plastics
At its core, injection molding color mixing relies on the physical properties of pigments and dyes interacting with polymer matrices. When you mix colors, you're essentially manipulating light absorption and reflection; different materials will absorb certain wavelengths while reflecting others, creating the final hue. This interaction can be influenced by factors such as particle size of pigments, dispersion quality, and even the chemical composition of the base resin—making it crucial to understand what causes discoloration in injection molding.
Moreover, achieving a uniform color requires careful consideration of blending techniques during processing. If not done properly, you may end up with streaks or uneven patches that detract from your product's appeal. Therefore, mastering the science behind these interactions is vital for anyone looking to perfect their injection molding color mixing game.
Importance of Consistency in Color
Consistency is king when it comes to injection molding color mixing; after all, nobody wants a rainbow when they ordered a solid shade! Variability in color can lead to customer dissatisfaction and increased production costs due to rework or scrap material. Maintaining uniformity requires meticulous attention to detail throughout every stage—from selecting pigments that match your desired outcome to ensuring proper machine calibration during production runs.
Inconsistent coloring can stem from several issues like inadequate mixing processes or fluctuations in material quality—both potential culprits for unsightly variations. To combat this challenge effectively, manufacturers must implement stringent quality control measures at each step of production; this means regular checks on pigment batches and even considering what is the difference between core and mold when designing parts for optimal results.
By prioritizing consistency, companies can enhance their reputation while minimizing waste—a win-win situation!
Identifying Common Mixing Problems
Even seasoned professionals face challenges with injection molding color mixing; knowing how to identify these issues early can save time and resources down the line! One common problem is poor pigment dispersion which often leads to mottled surfaces or uneven coloration—certainly not what anyone hopes for when trying to make a plastic color look flawless!
Another frequent issue arises from temperature fluctuations during processing; if temperatures are too high or too low at any point in time, it could affect how well colors mix together—resulting in unexpected shades or even discoloration altogether! Understanding these potential pitfalls allows manufacturers to troubleshoot effectively before they escalate into larger problems.
Lastly, equipment malfunction can also contribute significantly to inconsistent results—this emphasizes why choosing reliable machinery along with regular maintenance checks should be part of any serious operation’s strategy regarding injection molding color mixing.
What Causes Discoloration in Injection Molding?
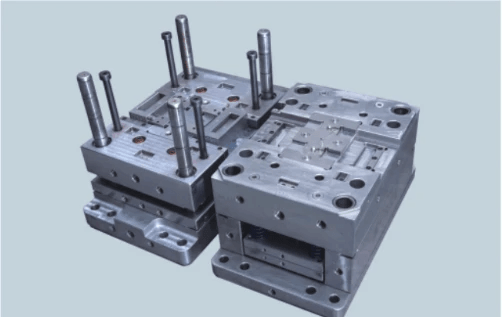
Discoloration in injection molding can be a significant issue that affects the aesthetic and functional qualities of the final product. Understanding what causes this discoloration is crucial for manufacturers aiming to achieve consistent results in injection molding color mixing. By identifying the underlying factors, such as chemical reactions, temperature fluctuations, and material quality, companies can take proactive measures to mitigate these challenges.
Chemical Reactions and Their Effects
Chemical reactions during the injection molding process can lead to unwanted discoloration in plastics. For instance, certain pigments may react with additives or contaminants present in the resin, resulting in color changes that were not anticipated during formulation. This unpredictability highlights why understanding what causes discoloration in injection molding? is essential for maintaining color integrity throughout production.
Additionally, some materials may undergo oxidation when exposed to heat or light during processing. This oxidation can alter the chemical structure of pigments and dyes used in plastic color formulation, leading to fading or darkening of colors over time. Therefore, careful selection of compatible materials is necessary to minimize adverse chemical interactions that could compromise the desired outcome.
Temperature Fluctuations and Their Impact
Temperature control plays a vital role in achieving consistent results in injection molding color mixing. Fluctuations can cause thermal degradation of both the base material and any added pigments or dyes, leading to undesirable changes in color quality. When temperatures exceed recommended levels during processing, it can result in a burnt appearance or uneven coloration across parts.
Moreover, inconsistent cooling rates within molds can further exacerbate discoloration issues by causing uneven solidification of plastic components. This uneven cooling often leads to variations that are visible on the surface of molded products. To avoid these pitfalls, manufacturers must closely monitor temperature settings throughout each stage of production.
Material Quality and Its Role in Discoloration
The quality of raw materials used significantly influences the occurrence of discoloration during injection molding processes. Low-quality resins may contain impurities that not only affect mechanical properties but also lead to inconsistent coloration when mixed with pigments or dyes. Therefore, sourcing high-grade materials is paramount for those asking how to make a plastic color? effectively without compromising on visual appeal.
Furthermore, recycled plastics often pose additional challenges regarding consistency due to varying compositions from batch to batch; this inconsistency can result in unpredictable coloring outcomes when attempting injection molding color mixing with recycled content. Manufacturers should prioritize rigorous testing and quality assurance measures when selecting materials for their projects—this will help ensure optimal results while minimizing risks associated with discoloration.
The Role of Equipment in Color Mixing
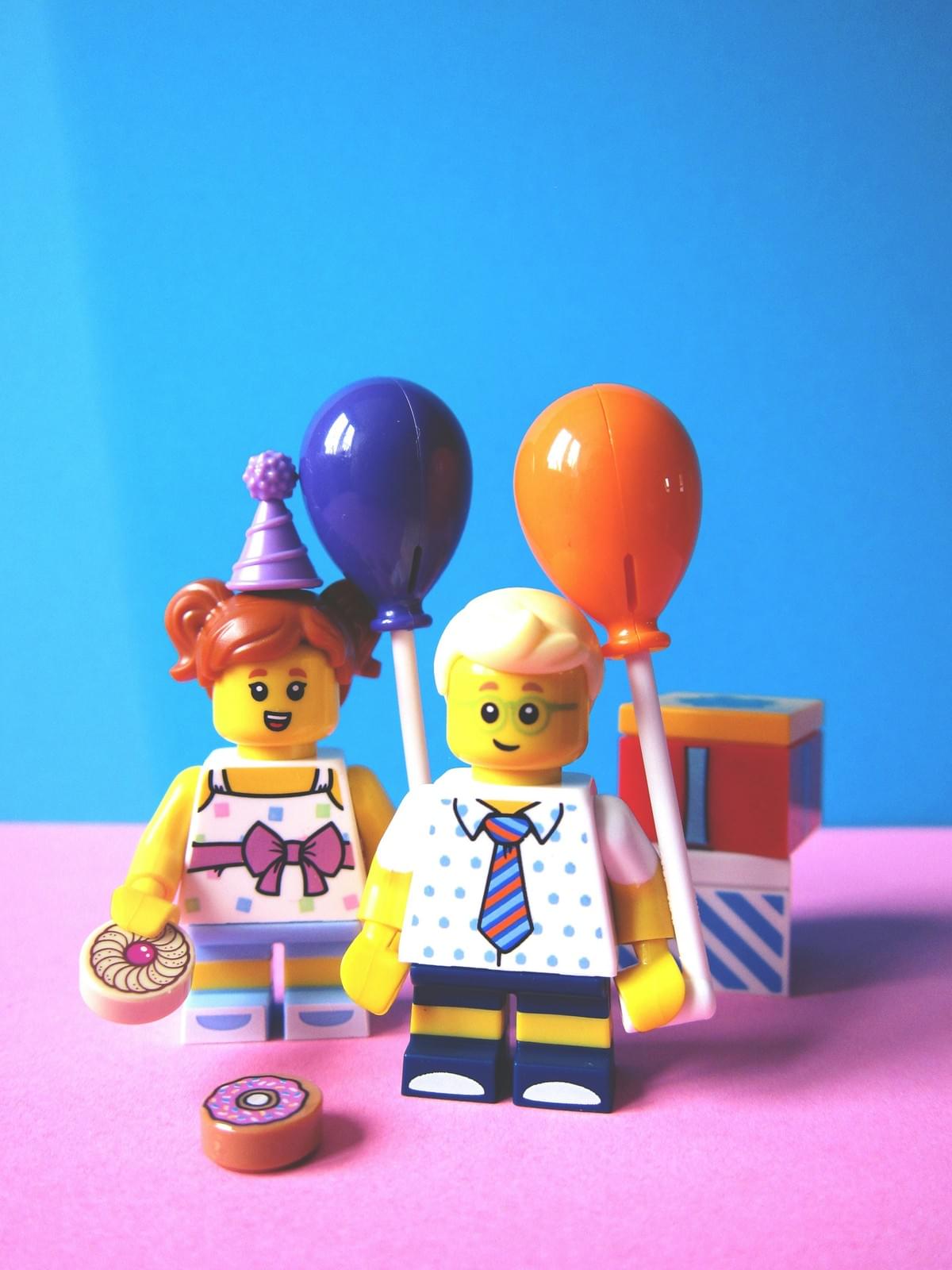
When it comes to injection molding color mixing, the equipment you choose can make or break your color consistency and quality. The right injection molding machine not only enhances the mixing process but also minimizes issues like discoloration. Selecting a machine that aligns with your specific production needs is crucial for achieving the desired plastic colors.
Choosing the Right Injection Molding Machine
Selecting the appropriate injection molding machine is a foundational step in effective color mixing. Different machines offer various capabilities, such as shot size, pressure control, and mixing options that can significantly impact how colors blend together. When evaluating options, consider factors like material compatibility and whether the machine can handle the pigments or dyes specified for your project—because nothing ruins a good color faster than an incompatible setup!
Importance of Maintenance and Calibration
Regular maintenance and calibration are essential for ensuring that your equipment delivers consistent results in injection molding color mixing. Over time, wear and tear can lead to variations in temperature and pressure, which are critical components when discussing what causes discoloration in injection molding? A well-maintained machine not only prolongs its lifespan but also ensures that every batch achieves uniformity in color—no one likes a surprise shade of green when they were expecting blue!
Up-to-date Technology for Improved Mixing
In an industry where precision is key, up-to-date technology plays a vital role in enhancing color mixing processes. Advanced machines come equipped with features like real-time monitoring systems that help identify inconsistencies before they become larger issues. By staying current with technological advancements, manufacturers can optimize their operations to produce high-quality plastic colors while minimizing waste due to improper mixes.
How to Make a Plastic Color?
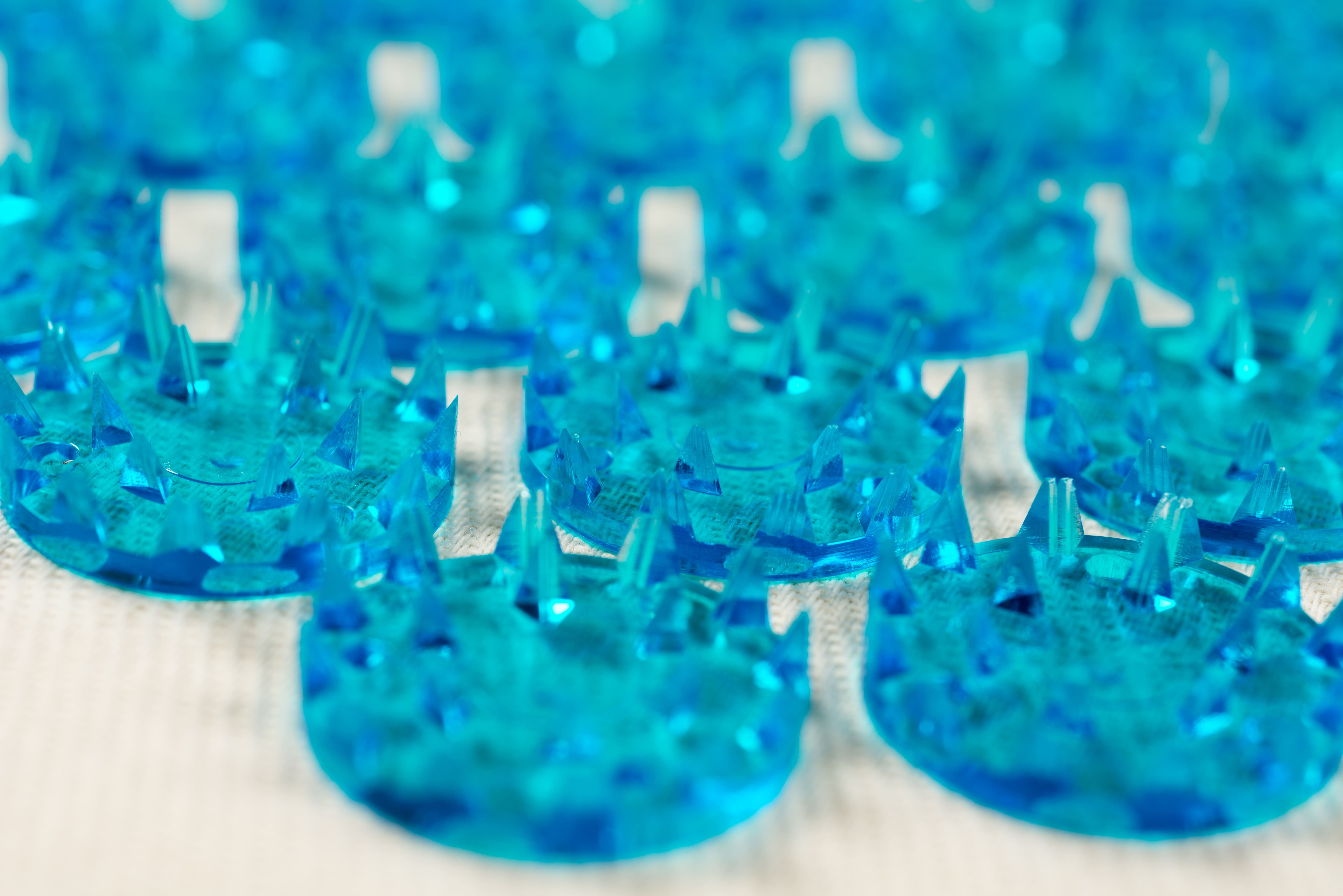
Creating the perfect color for plastic through injection molding color mixing is both an art and a science. It involves careful consideration of various factors, including the selection of pigments and dyes, effective mixing techniques, and a willingness to engage in trial and error. Mastering these elements can lead to vibrant, consistent colors that enhance product quality.
Selecting the Right Pigments and Dyes
The first step in how to make a plastic color involves choosing the right pigments and dyes that will blend well with your base resin. Not all pigments are created equal; some may cause discoloration in injection molding due to their chemical nature or compatibility with specific materials. Understanding what causes discoloration in injection molding is crucial—certain pigments can react negatively under heat or pressure, leading to unexpected results.
When selecting pigments, consider their opacity, lightfastness, and heat stability. Opt for high-quality dyes that not only provide vibrant colors but also maintain consistency throughout the production process. This choice will ultimately influence how your final product looks—after all, no one wants a dull piece when they were aiming for bright red!
Mixing Techniques for Perfect Color
Once you've selected your pigments and dyes, it’s time to dive into mixing techniques essential for achieving that perfect hue in injection molding color mixing. One popular method is pre-mixing your colors with a carrier resin before introducing them into the injection molding machine; this can help ensure even distribution throughout your material. Additionally, using masterbatches—concentrated mixtures of pigment with resin—can simplify the process while providing reliable results.
Another technique worth exploring is using high-shear mixers which create uniform dispersion of pigment particles within the plastic matrix. This method minimizes clumping or settling that could lead to inconsistent colors across different batches of products. Remember: achieving perfect color isn't just about throwing everything together; it requires finesse!
Trial and Error in Color Formulation
The road to mastering how to make a plastic color often involves trial and error—a necessary evil in creative processes like injection molding color mixing! Don’t be discouraged if your first few attempts don’t yield the desired result; instead, treat these experiences as learning opportunities that guide you towards perfection. Documenting each formulation’s outcomes will help you identify patterns and refine your approach over time.
Experimenting with different ratios of pigment-to-resin can unveil surprising results; sometimes less is more! Moreover, involving team members from various backgrounds can bring fresh perspectives on what might work better based on their unique experiences with material properties or equipment settings related to what causes discoloration in injection molding processes.
In conclusion, creating captivating plastic colors through effective injection molding color mixing necessitates thoughtful selection of materials coupled with innovative techniques—and yes, plenty of experimentation! Embrace this journey as you learn not only how different elements interact but also what makes each piece truly stand out on its own.
Core vs. Mold in Color Mixing
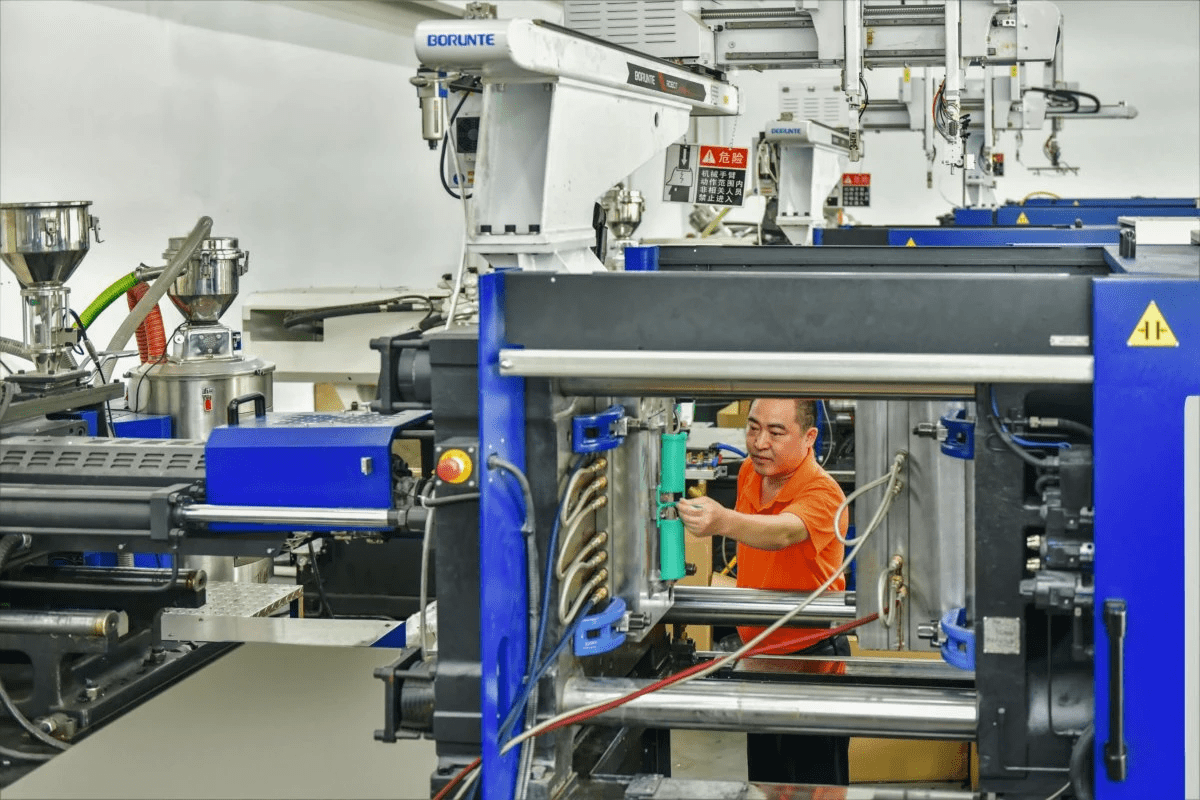
In the world of injection molding color mixing, understanding the distinction between core and mold is crucial for achieving the desired color outcomes. While both components play a vital role in shaping the final product, they serve different functions during the injection molding process. The core is typically the internal part that forms the cavity of the molded piece, while the mold refers to the outer shell that encases it.
What is the Difference Between Core and Mold?
The core and mold work together to create complex shapes, but their roles differ significantly in injection molding color mixing. The core shapes the interior features of a part, whereas the mold defines its exterior contours and surface finish. This difference is essential when considering how each component can influence color distribution and consistency throughout a plastic product.
When exploring What is the difference between core and mold?, it's important to note that variations in design can affect how well colors mix within these areas. For instance, cores may have intricate designs requiring precise pigment placement to avoid uneven coloring. In contrast, molds can be designed with features that promote better dispersion of colors during processing.
How Each Affects Color Outcome
The impact of cores and molds on color outcome cannot be overlooked when discussing What causes discoloration in injection molding? An improperly designed core might lead to areas where pigments fail to blend adequately, resulting in streaking or uneven coloration within a plastic part. Similarly, molds that do not allow for optimal flow paths can cause inadequate mixing or even thermal degradation of pigments.
When evaluating What is the color of plastic injection?, one must consider how both components contribute to achieving uniformity in hue across a finished product. For example, if a mold has sharp corners or narrow channels, it may hinder proper mixing during injection molding color mixing processes—leading to unwanted discoloration or inconsistencies in shade perception across different parts.
Best Practices for Mold Design
To ensure successful results in injection molding color mixing, adhering to best practices for mold design is paramount. First off, designing molds with smooth transitions and rounded edges helps facilitate better flow rates and promotes even distribution of colors throughout each cavity—minimizing issues related to What causes discoloration in injection molding?
Additionally, incorporating features like vents or strategically placed gates can improve material flow dynamics while allowing trapped air to escape during filling cycles—further enhancing overall quality control over what is perceived as the color of plastic injection. Regular maintenance checks on these components are also essential; ensuring they remain clean will help maintain consistent results over time.
Finally, collaborating with experienced professionals who understand how to make a plastic color effectively will lead you down a path toward creating vibrant products without compromising quality or consistency—ensuring your brand stands out amidst fierce competition!
Conclusion
In the world of injection molding color mixing, achieving consistent and vibrant colors can often feel like navigating a labyrinth. However, by understanding the underlying principles and addressing common issues, manufacturers can significantly enhance their processes. From identifying what causes discoloration in injection molding to mastering how to make a plastic color, every step taken towards improvement is a step towards success.
Implementing Reliable Mixing Techniques
To ensure the best outcomes in injection molding color mixing, implementing reliable mixing techniques is essential. This involves not only selecting high-quality pigments but also understanding how to mix them effectively to achieve desired results. By focusing on proper equipment maintenance and calibration, manufacturers can minimize discrepancies that lead to discoloration and ensure that each batch meets quality standards.
Learning from the Baoyuan Team's Expertise
The Baoyuan team brings invaluable insights into overcoming challenges in injection molding color mixing. Their extensive experience sheds light on crucial factors such as the difference between core and mold in terms of color application and retention. By leveraging their expertise, businesses can refine their processes for making plastic colors while avoiding pitfalls associated with poor material quality or improper temperature management.
Staying Ahead in Injection Molding Color Mixing
Staying ahead in injection molding color mixing requires an ongoing commitment to innovation and adaptation. Companies must remain vigilant about advancements in technology that can improve mixing efficiency and consistency while actively educating their teams about best practices for preventing discoloration. By continually refining methods for how to make a plastic color and embracing new solutions, manufacturers can maintain a competitive edge in an ever-evolving industry.