Introduction
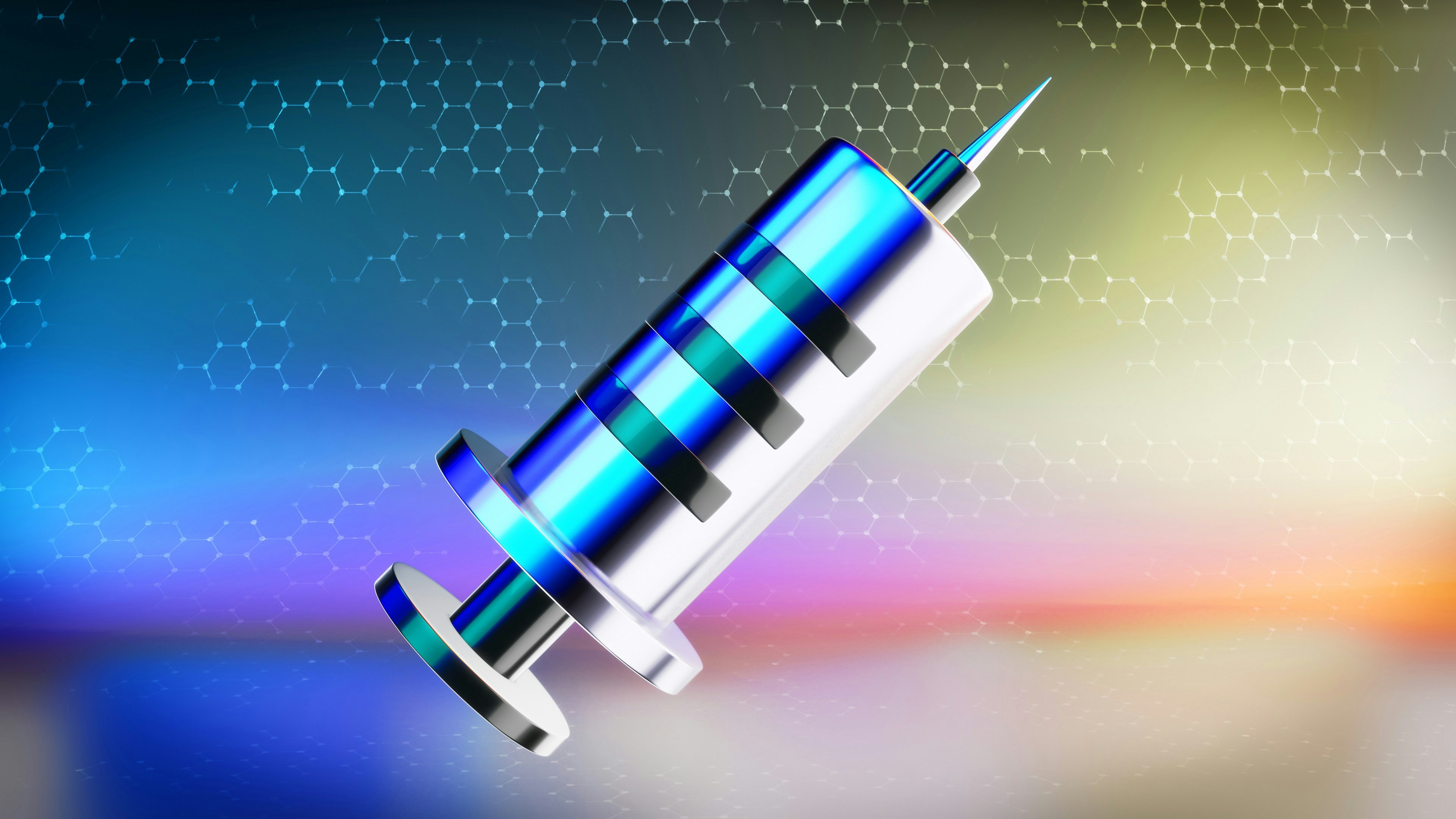
The healthcare industry is undergoing a transformative shift, with plastic playing an increasingly pivotal role in medical devices. From syringes to surgical tools, the versatility of plastic injection molding medical devices has revolutionized how products are designed, manufactured, and utilized in clinical settings. Understanding the nuances of this process is essential for anyone involved in healthcare innovation.
Exploring the Role of Plastic in Healthcare
Plastic has become a cornerstone material in healthcare due to its lightweight nature, durability, and cost-effectiveness. Medical professionals have come to rely on plastic for a myriad of applications; it’s not just about affordability but also about improving patient outcomes through innovative designs. As we delve into what medical devices are made of plastic, it becomes evident that this material is integral to modern medicine.
The Importance of Precision in Mold Design
Precision in mold design cannot be overstated when it comes to producing high-quality plastic medical equipment. The intricate details required for functionality and safety demand meticulous attention during the injection molding process. A small error can lead to significant ramifications, making it crucial for manufacturers to prioritize precision in every aspect of their work.
Understanding the Basics of Plastic Injection Molding
At its core, what is medical injection molding? It’s a manufacturing process that involves injecting molten plastic into a mold to create specific shapes and components tailored for various medical applications. This technique not only facilitates mass production but also ensures consistency and reliability across all products—qualities that are non-negotiable when dealing with health-related items.
What is Medical Injection Molding?
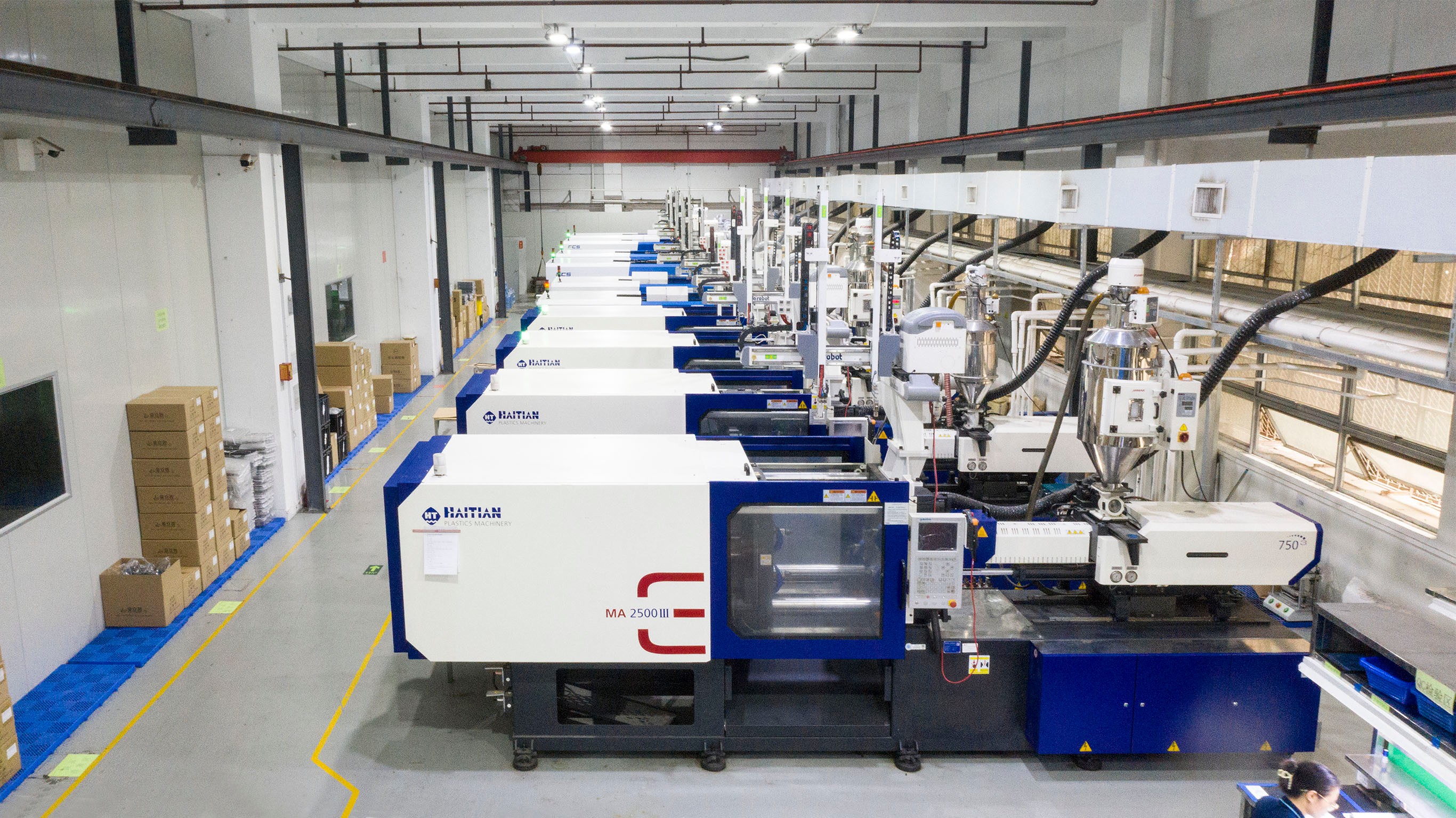
Medical injection molding is a specialized manufacturing process that produces plastic components for healthcare applications. This technique allows for the rapid and efficient production of intricate shapes and designs, which are essential in the medical field. With precision at its core, medical injection molding ensures that each part meets stringent regulatory standards, making it an invaluable method for creating reliable plastic medical devices.
The Process Explained
The process of medical injection molding begins with the creation of a mold, which is designed to form the desired shape of the plastic component. Once the mold is ready, plastic pellets are heated until they melt and then injected into the mold under high pressure. After cooling and solidifying, the mold opens to release the finished product, allowing for quick production cycles that are essential in meeting healthcare demands.
This method stands out because it can produce large quantities of identical parts with minimal waste, making it cost-effective for manufacturers. Additionally, advancements in technology have enhanced precision and reduced cycle times even further. As a result, many medical injection molding companies can deliver high-quality products rapidly while ensuring compliance with industry regulations.
Key Benefits for Healthcare Applications
One of the primary benefits of using plastic injection molding in medical devices lies in its ability to create complex geometries that would be difficult or impossible to achieve through other manufacturing methods. This capability allows engineers to design innovative solutions tailored specifically to healthcare needs. Furthermore, plastic components produced via this method often exhibit superior strength-to-weight ratios compared to traditional materials.
Another advantage is the versatility offered by various plastics used in this process; these materials can be selected based on specific requirements such as biocompatibility or resistance to sterilization methods like autoclaving or ethylene oxide gas exposure. This flexibility enables manufacturers to create a wide range of products suitable for different applications within healthcare environments. Ultimately, these benefits contribute significantly to improving patient outcomes and enhancing overall care.
Real-World Examples in Medical Devices
Medical injection molding has found its way into numerous applications within healthcare settings—think syringes, IV bags, and surgical instruments—all made from durable plastics designed through this process. For instance, many disposable items such as catheters and blood collection tubes rely on precision molded components that ensure safety and efficacy during use. These examples highlight just how integral this manufacturing technique has become in producing reliable plastic medical equipment.
Moreover, innovations continue to emerge; companies are developing advanced drug delivery systems utilizing molded components that improve patient compliance while reducing side effects associated with medications delivered via traditional methods. Case studies demonstrate how successful collaborations between engineers and manufacturers have led to breakthroughs like smart inhalers equipped with sensors—a fusion of technology and medicine made possible by sophisticated plastic injection molding techniques.
In summary, understanding what medical devices are made of plastic reveals not only their importance but also how critical processes like medical injection molding contribute significantly towards advancing healthcare solutions today.
What Medical Devices are Made of Plastic?
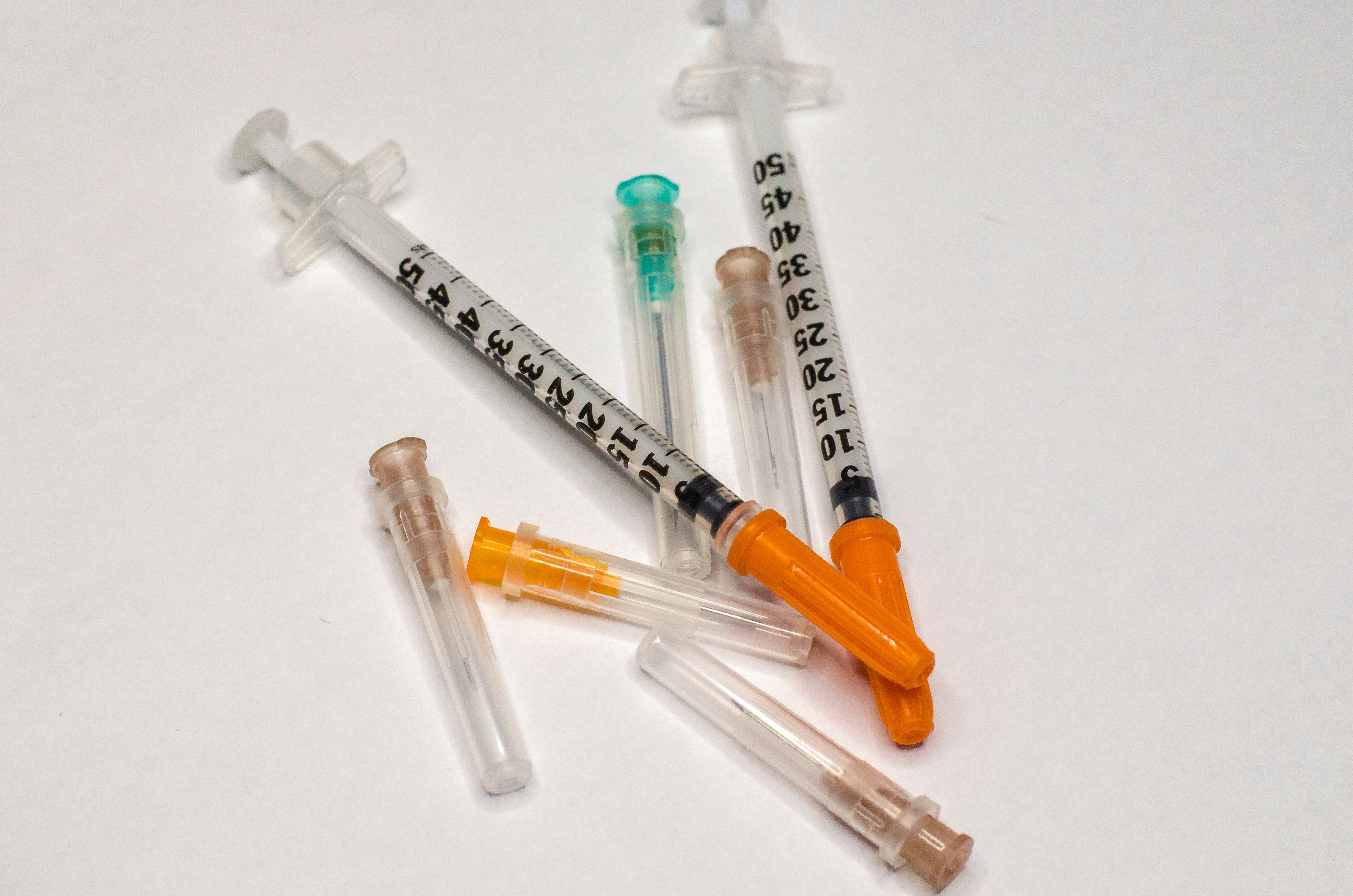
In the ever-evolving landscape of healthcare, plastic injection molding medical devices have become indispensable. These devices range from simple syringes to complex diagnostic tools, all benefiting from the versatility and efficiency of injection molding techniques. Understanding what medical devices are made of plastic can illuminate their critical role in modern medicine.
Common Devices Utilizing Injection Molding
Plastic injection molding is the backbone for a myriad of medical devices that we often take for granted. Common products include syringes, IV bags, and surgical instruments, all crafted with precision to ensure safety and efficacy. These items not only require high-quality materials but also must adhere to stringent regulations that govern their production.
Among the plastic products made by injection molding, components like housings for electronic monitoring devices and drug delivery systems are noteworthy. The ability to create intricate designs with minimal waste makes this manufacturing method particularly appealing for medical applications. Moreover, the scalability of plastic injection molding allows manufacturers to meet fluctuating demands without compromising on quality.
Innovations in Plastic Medical Equipment
The realm of plastic medical equipment manufacturers is buzzing with innovations that push the boundaries of what's possible in healthcare technology. New materials and advanced techniques are being developed to enhance biocompatibility and functionality in medical devices made from plastics. Innovations such as biodegradable plastics or those with antimicrobial properties are paving the way for safer patient care.
Furthermore, advancements in 3D printing technologies complement traditional plastic injection molding methods by enabling rapid prototyping and customization of medical devices. This synergy allows for tailored solutions that meet specific patient needs while maintaining compliance with industry standards. As a result, these innovations not only improve device performance but also streamline production processes.
Case Studies of Success
Examining real-world examples reveals how effectively plastic injection molding has transformed healthcare outcomes through successful medical device applications. For instance, a notable case involves a leading manufacturer that developed a new line of disposable surgical instruments using advanced plastics designed for optimal sterilization compatibility—addressing one of the four material requirements for plastics used in medical devices: durability under sterilization processes.
Another success story features a company that produced lightweight yet robust orthopedic implants via plastic injection molding techniques, significantly improving patient comfort during recovery while ensuring structural integrity post-surgery. Such case studies highlight how collaboration between engineers and healthcare professionals leads to innovative solutions that meet stringent safety standards while enhancing patient care.
Material Requirements for Plastic Medical Devices

In the realm of plastic injection molding medical devices, selecting the right materials is crucial to ensure functionality, safety, and compliance with industry standards. The materials used must meet stringent requirements to withstand various conditions while ensuring patient safety. Understanding these material requirements can help manufacturers produce high-quality plastic medical equipment that meets regulatory expectations.
The Four Key Material Requirements
When it comes to what are the 4 material requirements for plastics used in medical devices, there are four key criteria that need to be addressed: mechanical properties, thermal stability, chemical resistance, and biocompatibility. Mechanical properties dictate how well a device can perform under stress or strain during its lifecycle. Thermal stability ensures that the plastic maintains its integrity when subjected to sterilization processes or environmental changes, while chemical resistance protects against degradation from exposure to various substances.
Biocompatibility is arguably the most critical requirement since it determines how a material interacts with biological systems. Medical injection molding companies must prioritize this aspect to ensure that any plastic products made by injection molding do not cause adverse reactions in patients. By focusing on these four key material requirements, manufacturers can create effective and reliable medical devices.
Compatibility with Sterilization Processes
Compatibility with sterilization processes is another essential consideration in the production of plastic medical equipment. Medical devices often undergo sterilization methods such as autoclaving or ethylene oxide treatment before they reach healthcare settings; thus, the materials must be able to endure these harsh conditions without losing their structural integrity or performance characteristics. Failure to account for this could lead to compromised devices that pose risks during surgical procedures.
Moreover, understanding what medical devices are made of plastic helps manufacturers select appropriate polymers that can withstand repeated sterilization cycles without degrading over time. This compatibility not only extends the lifespan of the device but also ensures patient safety by maintaining a sterile environment for use in critical situations. Therefore, evaluating how well materials respond to different sterilization techniques is paramount for success in medical injection molding.
Ensuring Biocompatibility and Safety
Ensuring biocompatibility and safety goes hand-in-hand with selecting suitable materials for plastic injection molding medical devices. Manufacturers need to conduct thorough testing and validation processes to confirm that their chosen plastics do not elicit harmful reactions when interacting with human tissues or fluids. This level of scrutiny is necessary because even minor contaminants can lead to significant health risks for patients relying on these devices.
In addition to biocompatibility testing, collaboration between plastic medical equipment manufacturers and regulatory bodies is vital in establishing guidelines and standards for safe practices within the industry. With ongoing advancements in technology and material science, there’s an opportunity for more innovative solutions that enhance both performance and safety features in future designs of medical devices made from plastics. Ultimately, prioritizing biocompatibility ensures a safer experience for both patients and healthcare providers alike.
Choosing the Right Injection Molding Companies
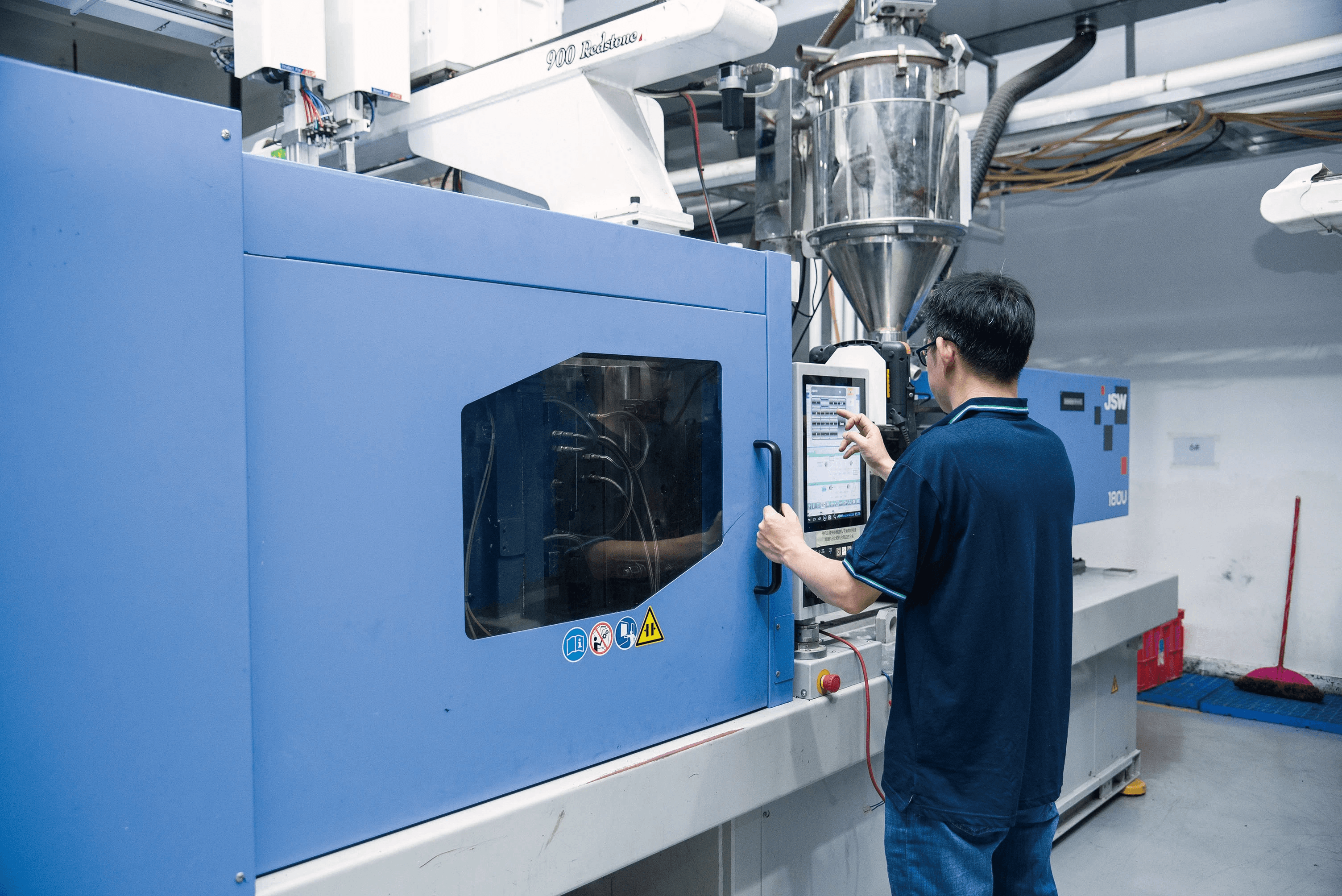
Selecting the right injection molding companies is crucial for the success of plastic injection molding medical devices. With so many options available, it’s essential to consider various criteria that ensure quality, compliance, and innovation. A well-chosen partner can significantly impact the design and functionality of medical equipment made from plastic.
Criteria for Selecting Medical Injection Molding Companies
When looking for a reliable medical injection molding company, several key criteria should guide your decision-making process. First and foremost, experience in manufacturing plastic medical devices is vital; companies must understand regulatory requirements and industry standards thoroughly. Additionally, assessing their technological capabilities is essential—advanced machinery and techniques often lead to better precision in mold design.
Another critical factor is their commitment to quality assurance practices; this includes certifications such as ISO 13485, which demonstrate adherence to strict quality management systems tailored for the healthcare sector. Moreover, evaluating a company's track record with previous projects can provide insights into their reliability and ability to meet deadlines without compromising on quality. Lastly, strong communication skills are essential; a responsive partner fosters collaboration that can enhance product development.
Highlighting Notable Firms like Baoyuan
Among the notable firms in the realm of plastic medical equipment manufacturers is Baoyuan, a company renowned for its expertise in medical injection molding processes. Baoyuan has established itself as a leader by specializing in creating high-quality components that meet stringent safety standards required for healthcare applications. Their innovative approach allows them to stay ahead of trends while ensuring that their products align with what medical devices are made of plastic.
Baoyuan’s portfolio showcases an impressive range of products—from surgical instruments to diagnostic tools—demonstrating versatility in what plastic products are made by injection molding techniques. Their commitment to continuous improvement means they frequently invest in state-of-the-art technology and skilled personnel who understand both engineering principles and healthcare needs. By choosing a firm like Baoyuan, manufacturers can ensure they are partnering with an organization dedicated to excellence.
Evaluating Quality Assurance Practices
Quality assurance practices play an integral role when selecting medical injection molding companies; these processes help guarantee that every component produced meets regulatory standards and customer expectations alike. A robust quality control system should include regular audits, testing protocols for biocompatibility, and thorough documentation practices that track every step of production—especially critical when discussing what are the 4 material requirements for plastics used in medical devices.
Furthermore, potential partners should demonstrate transparency regarding their testing methods and results; this openness builds trust between manufacturers and clients while ensuring compliance with safety regulations during production cycles. Companies committed to ongoing training programs also show dedication not just toward current practices but future innovations within plastic injection molding medical devices as well.
In summary, selecting the right injection molding companies requires careful consideration of various criteria including experience, technology capabilities, certification status, communication skills, and commitment to quality assurance practices—all essential elements contributing toward successful partnerships in producing effective plastic medical equipment.
Trends in Plastic Medical Equipment Manufacturing
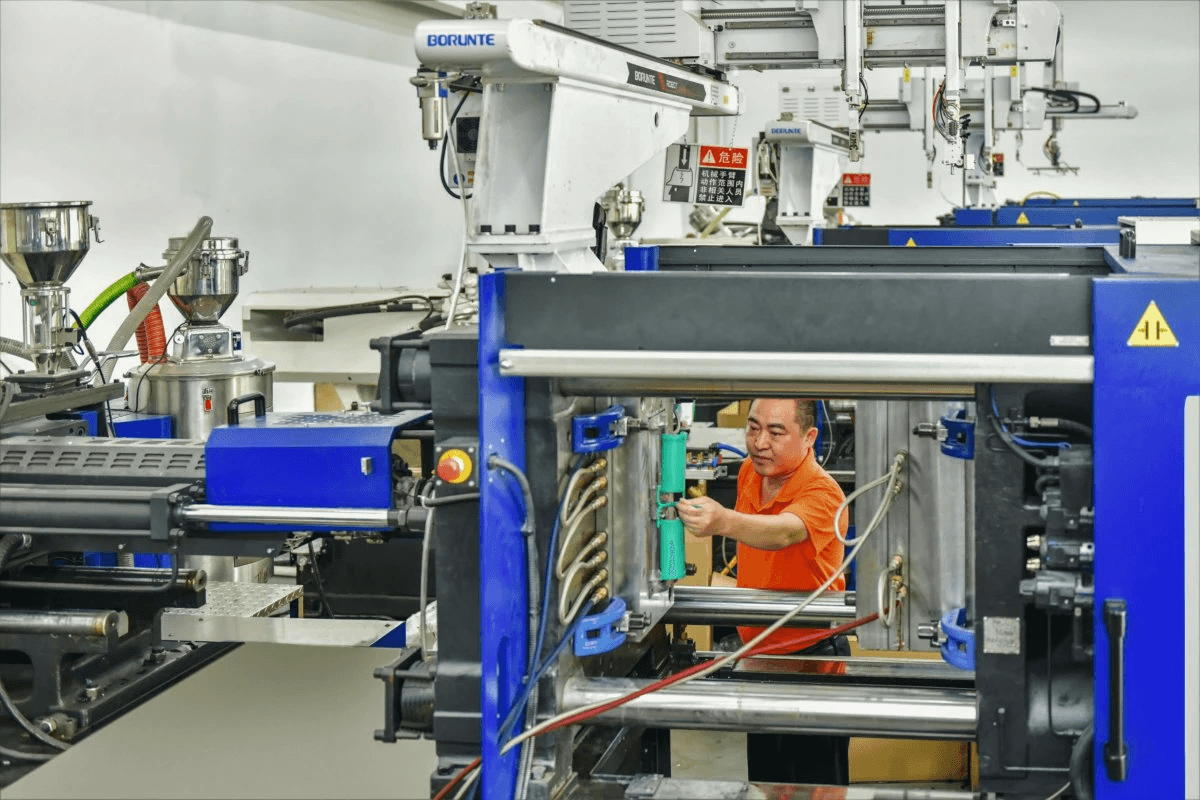
The landscape of plastic medical equipment manufacturing is evolving rapidly, driven by technological advancements and a growing emphasis on sustainability. As the demand for plastic injection molding medical devices increases, manufacturers are continually exploring innovative processes and materials to enhance performance and safety. In this section, we will delve into the latest trends shaping the industry, focusing on advances in technology, sustainable practices, and what the future holds for plastic medical equipment manufacturers.
Advances in Technology and Their Impact
Recent advancements in technology have significantly transformed what is possible with medical injection molding. Innovations such as 3D printing and automation are streamlining production processes, allowing for quicker turnaround times without compromising on quality. These technologies not only improve efficiency but also enable the creation of complex designs that were previously unattainable—making it easier to produce a diverse range of plastic products made by injection molding.
Moreover, the integration of smart manufacturing techniques is enhancing precision in mold design, which is crucial for creating reliable plastic medical devices. With real-time data monitoring and advanced simulation software, companies can optimize their production lines to reduce waste and increase output quality. This technological evolution empowers medical injection molding companies to respond swiftly to market demands while maintaining high standards of safety and compliance.
Sustainable Practices in Injection Molding
Sustainability has become a central theme in many industries, including healthcare; thus, sustainable practices in injection molding are gaining traction among plastic medical equipment manufacturers. Companies are increasingly adopting eco-friendly materials—such as biodegradable plastics or recycled polymers—to minimize environmental impact while still meeting stringent performance requirements for medical devices.
Additionally, energy-efficient machinery and waste reduction strategies are being implemented throughout the production process to promote sustainability further. By focusing on these green initiatives, manufacturers not only comply with regulatory standards but also appeal to environmentally conscious consumers who prioritize sustainability when considering what medical devices are made of plastic.
Future Outlook for the Industry
Looking ahead, the future outlook for plastic injection molding medical devices appears promising as innovation continues to drive growth within the sector. With ongoing research into new materials that meet the four key material requirements for plastics used in medical devices—strength, durability, biocompatibility, and sterilization compatibility—the potential applications seem limitless.
As technology advances further and consumer preferences shift toward more sustainable options, we can expect an increase in collaboration between healthcare providers and plastic medical equipment manufacturers to develop tailored solutions that address specific needs within patient care settings. Ultimately, this synergy will pave the way for groundbreaking innovations that redefine how we think about what products are made by injection molding.
Conclusion
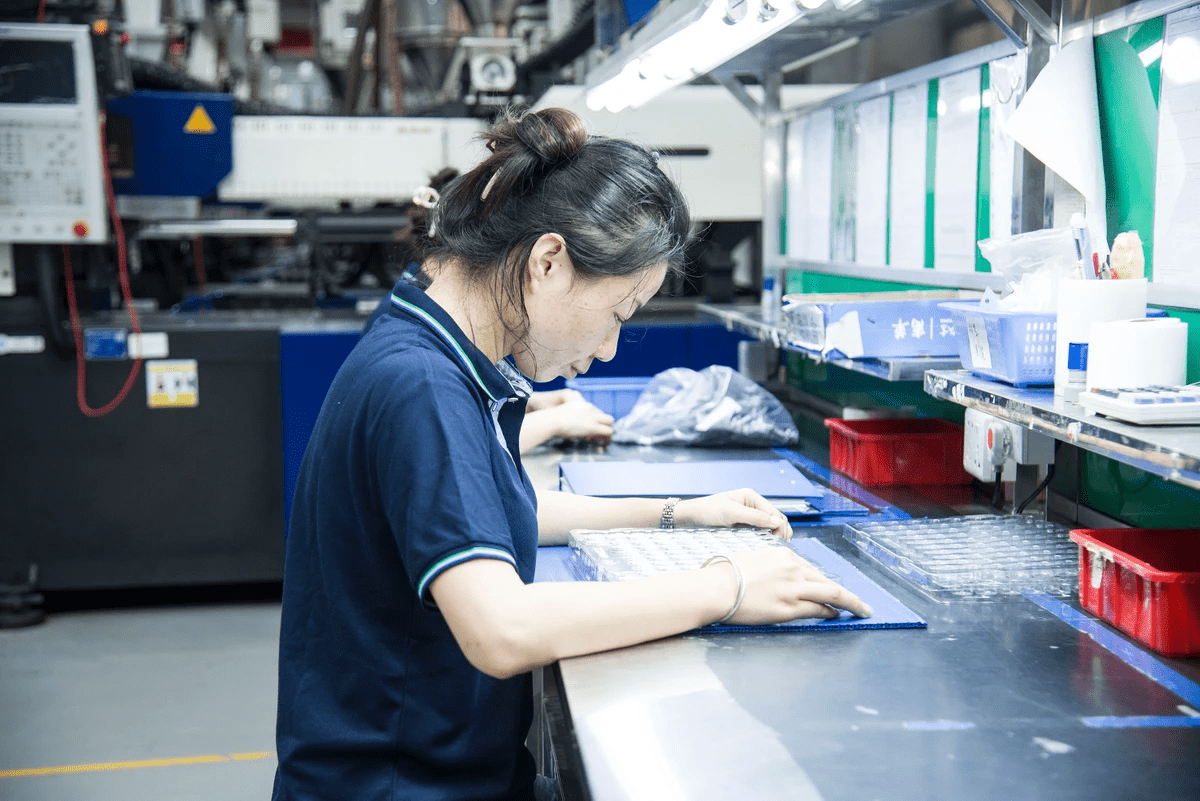
In the ever-evolving landscape of healthcare, plastic injection molding medical devices are becoming increasingly vital. As we look ahead, the future of these devices appears promising, with innovations paving the way for enhanced functionality and safety. The ability to produce complex shapes and designs through medical injection molding is not just a technological marvel but a necessity that addresses the demands of modern medicine.
The Future of Plastic Injection Molding Medical Devices
The future trajectory for plastic injection molding medical devices is set to be shaped by advancements in materials and manufacturing techniques. With ongoing research into new polymers, manufacturers can create lighter, stronger, and more biocompatible products that meet stringent healthcare standards. As we push boundaries in what medical devices are made of plastic, there’s potential for breakthroughs that could revolutionize patient care.
Innovations That Are Driving Change
Innovations in plastic medical equipment are not limited to materials alone; they encompass processes as well. For instance, advancements in 3D printing technology are being integrated with traditional medical injection molding methods to create customized solutions tailored to individual patient needs. Additionally, smart technologies embedded within these devices promise improved monitoring and diagnostics capabilities that will redefine healthcare delivery.
Key Takeaways for Manufacturers and Practitioners
For manufacturers and practitioners alike, understanding what the four material requirements for plastics used in medical devices are—biocompatibility, chemical resistance, mechanical strength, and sterilization compatibility—is crucial for success in this field. Selecting reputable medical injection molding companies like Baoyuan can ensure adherence to quality standards while fostering innovation in product development. Ultimately, staying informed about trends will empower stakeholders to navigate the complexities of plastic medical equipment manufacturing effectively.