Introduction
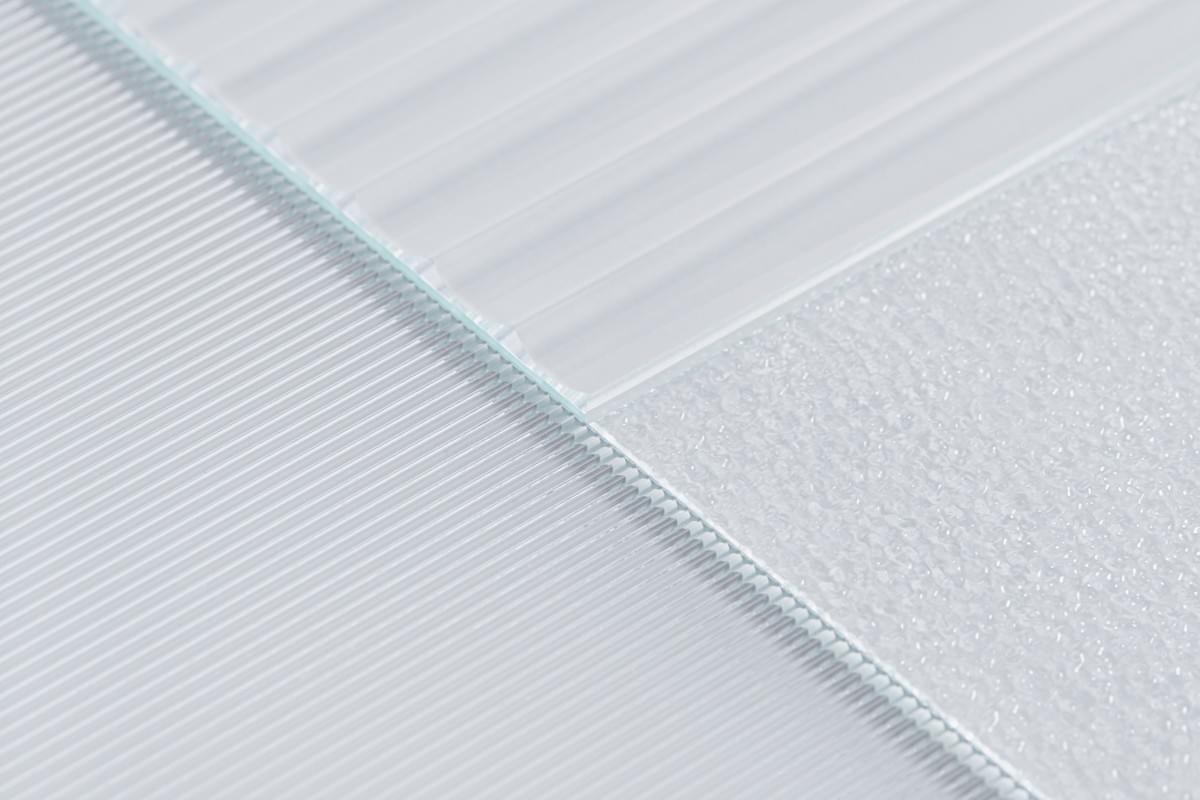
When it comes to plastic injection molded parts, understanding the differences between polycarbonate and ABS materials is crucial. Polycarbonate and ABS injection molding have unique properties and applications, making knowing which material best suits your specific needs essential. Factors such as impact strength, heat resistance, and chemical resistance play a significant role in choosing between polycarbonate and. abs for your injection molded parts.
Understanding Polycarbonate and ABS Materials
Polycarbonate is known for its exceptional impact strength and high transparency, making it ideal for applications requiring a clear or see-through component. ABS offers good impact resistance and toughness with the added benefit of being easily machinable and thermoformable. Both materials have distinct advantages, making them suitable for various industrial and consumer product applications.
Key Differences Between Polycarbonate and ABS
Polycarbonate (PC) and ABS (Acrylonitrile Butadiene Styrene) are common thermoplastics used in various applications. However, their distinct physical properties make them better suited for different situations. Here's a breakdown of their key differences:
- Impact Strength: Polycarbonate boasts superior impact strength and is ideal for high-durability products like bulletproof windows and riot shields.
- Heat Resistance: Conversely, ABS offers better resistance to heat, allowing it to withstand higher temperatures without warping or melting. This makes it suitable for applications like car parts under the hood.
- Chemical Resistance: ABS also exhibits better resistance to certain chemicals than polycarbonate. This property makes it a good choice for products that might come into contact with cleaning solutions or other chemicals.
Both polycarbonate and ABS are valuable thermoplastics, but understanding their specific strengths will help you choose the right material for your project.
Factors to Consider When Choosing Between Polycarbonate and ABS
Several factors should be considered when deciding between polycarbonate and ABS for your plastic mold injection needs. The specific application requirements, such as environmental conditions, mechanical stress, and chemical exposure, will significantly determine which material best suits the job. Factors such as cost-effectiveness and ease of manufacturing should also be considered when choosing between polycarbonate and ABS.
Physical Properties
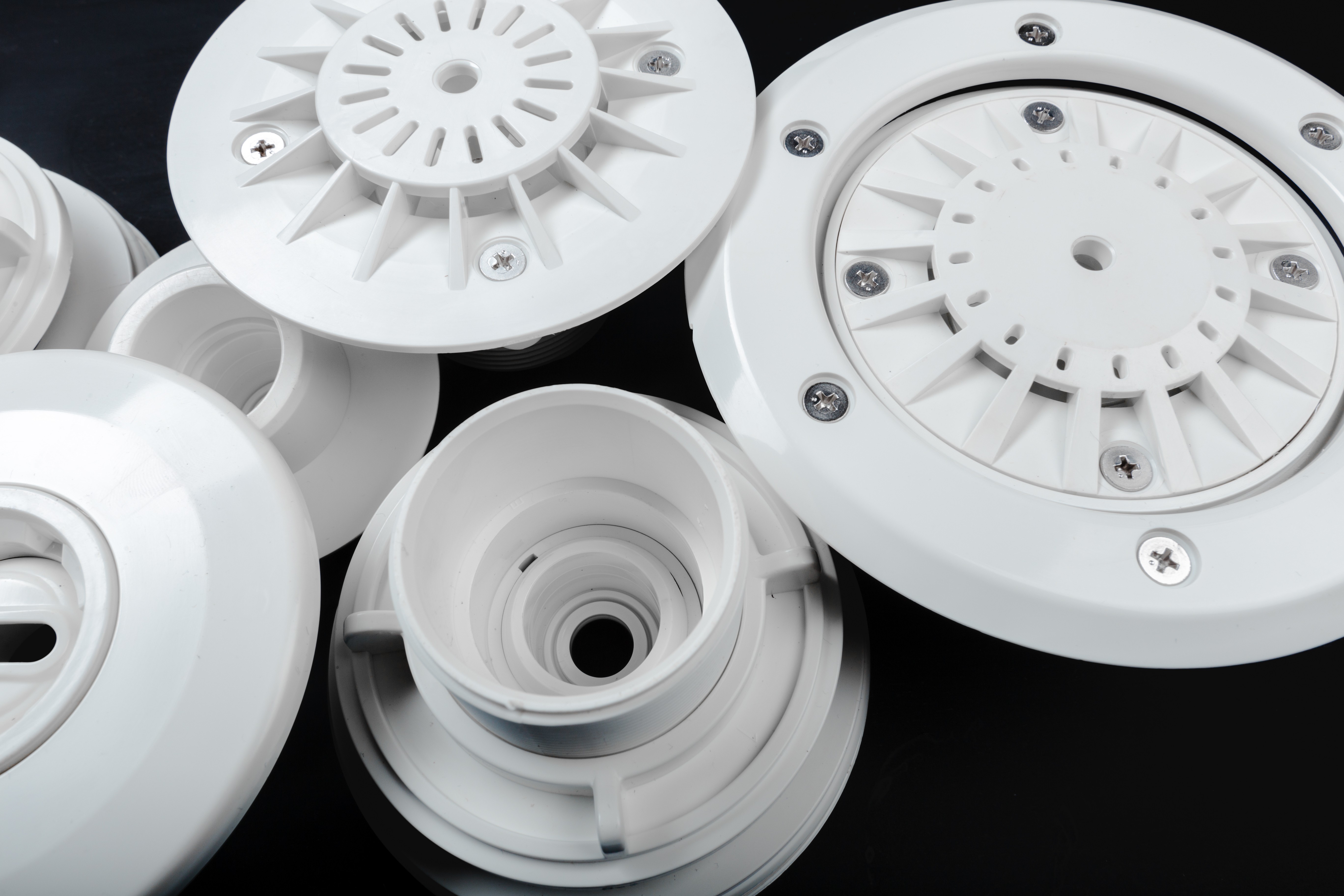
When comparing polycarbonate vs ABS, it's important to consider their physical properties. Polycarbonate is known for its exceptional impact strength, making it a popular choice for applications requiring durability and resistance to breakage. On the other hand, ABS also offers good impact resistance, although not as high as polycarbonate. This makes ABS suitable for applications where moderate impact strength is sufficient.
Impact Strength: Polycarbonate vs ABS
Polycarbonate injection molding results in plastic molded parts with superior impact strength, making it ideal for products that need to withstand heavy use or potential impacts. Its ability to maintain structural integrity under pressure sets it apart from ABS injection molding, which offers good but not as high impact resistance.
Polycarbonate's superior impact strength also makes it a top choice for products exposed to extreme weather conditions or high levels of physical stress. This material is often used to construct outdoor equipment, safety gear, and automotive components where durability is paramount. In contrast, while ABS offers good impact resistance, it may not be suitable for applications with a higher risk of heavy use or potential impacts.
Heat Resistance: Polycarbonate vs ABS
In terms of heat resistance, polycarbonate outperforms ABS. It can withstand higher temperatures without deforming or losing its properties, making polycarbonate a preferred choice for applications where exposure to heat is a concern, such as automotive components and electronic enclosures.
In addition to its superior heat resistance, polycarbonate offers excellent chemical resistance compared to ABS. This means that polycarbonate is less likely to degrade or react with various chemicals, making it a more reliable choice for applications where exposure to potentially corrosive substances is a concern. From industrial equipment to medical devices, polycarbonate's chemical resistance makes it a versatile and durable option for a wide range of uses.
Chemical Resistance: Polycarbonate vs ABS
Regarding chemical resistance, both polycarbonate and ABS exhibit good resistance to a wide range of chemicals. However, polycarbonate has an edge over ABS due to its ability to withstand a broader range of chemicals without degradation or damage.
Polycarbonate and ABS are famous for applications requiring chemical resistance, such as in the automotive and electronic industries. While both materials can withstand various chemicals, polycarbonate outperforms ABS due to its superior resistance to a broader spectrum of substances. This makes polycarbonate an ideal choice for environments where exposure to multiple chemicals is a concern, providing long-lasting durability and reliability.
Applications
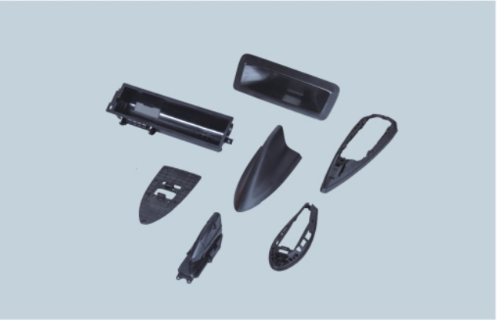
Industrial Use: Polycarbonate vs ABS
Polycarbonate and ABS are popular choices for industrial use in plastic injection-molded parts. Polycarbonate injection molding is preferred for applications that require high-impact resistance and transparency, such as machine guards, safety helmets, and protective gear. On the other hand, ABS injection molding is commonly used for housing components in industrial equipment and machinery due to its excellent dimensional stability and resistance to chemicals and heat.
In addition, polycarbonate is also a popular choice for consumer products that require high durability and clarity, such as eyewear, phone cases, and water bottles. Its ability to withstand impact and maintain transparency makes it a preferred material for these applications. On the other hand, ABS is commonly used in consumer products like kitchen appliances, toys, and luggage due to its strength and resistance to heat and chemicals. This versatility makes both polycarbonate and ABS valuable options for a wide range of industrial and consumer applications.
Consumer Products: Polycarbonate vs ABS
Polycarbonate vs. ABS is a common debate among consumer product manufacturers. Polycarbonate's superior impact strength and optical clarity make it ideal for electronic device housings, eyewear, and water bottles. Meanwhile, ABS's ease of processing and affordability make it a top choice for manufacturing consumer products such as kitchen appliances, luggage shells, and toys.
Polycarbonate's resistance to high temperatures and flame retardant properties make it a preferred material for automotive headlamp lenses and interior trim components. Its ability to withstand impact and extreme weather conditions makes it suitable for exterior automotive parts like bumpers and body panels. On the other hand, ABS's excellent dimensional stability and ability to be easily painted or plated make it a popular choice for automotive interior components such as dashboard panels, door handles, and trim pieces.
Automotive Industry: Polycarbonate vs ABS
The automotive industry relies heavily on polycarbonate and ABS injection molding for various applications. Polycarbonate's high impact resistance makes it suitable for manufacturing headlight lenses, interior trim components, and exterior body panels. On the other hand, ABS's excellent surface finish quality makes it a preferred material for producing automotive interior parts like dashboards, door panels, and trim components.
Furthermore, the choice between polycarbonate and ABS for automotive applications also depends on the specific requirements for each part. For example, polycarbonate may be preferred for headlight lenses due to its high optical clarity and resistance to yellowing over time, while ABS may be chosen for interior trim components that require a sleek, high-gloss finish. This versatility allows automotive manufacturers to select the most suitable material for each application, ensuring optimal vehicle performance and aesthetics.
Manufacturing Process
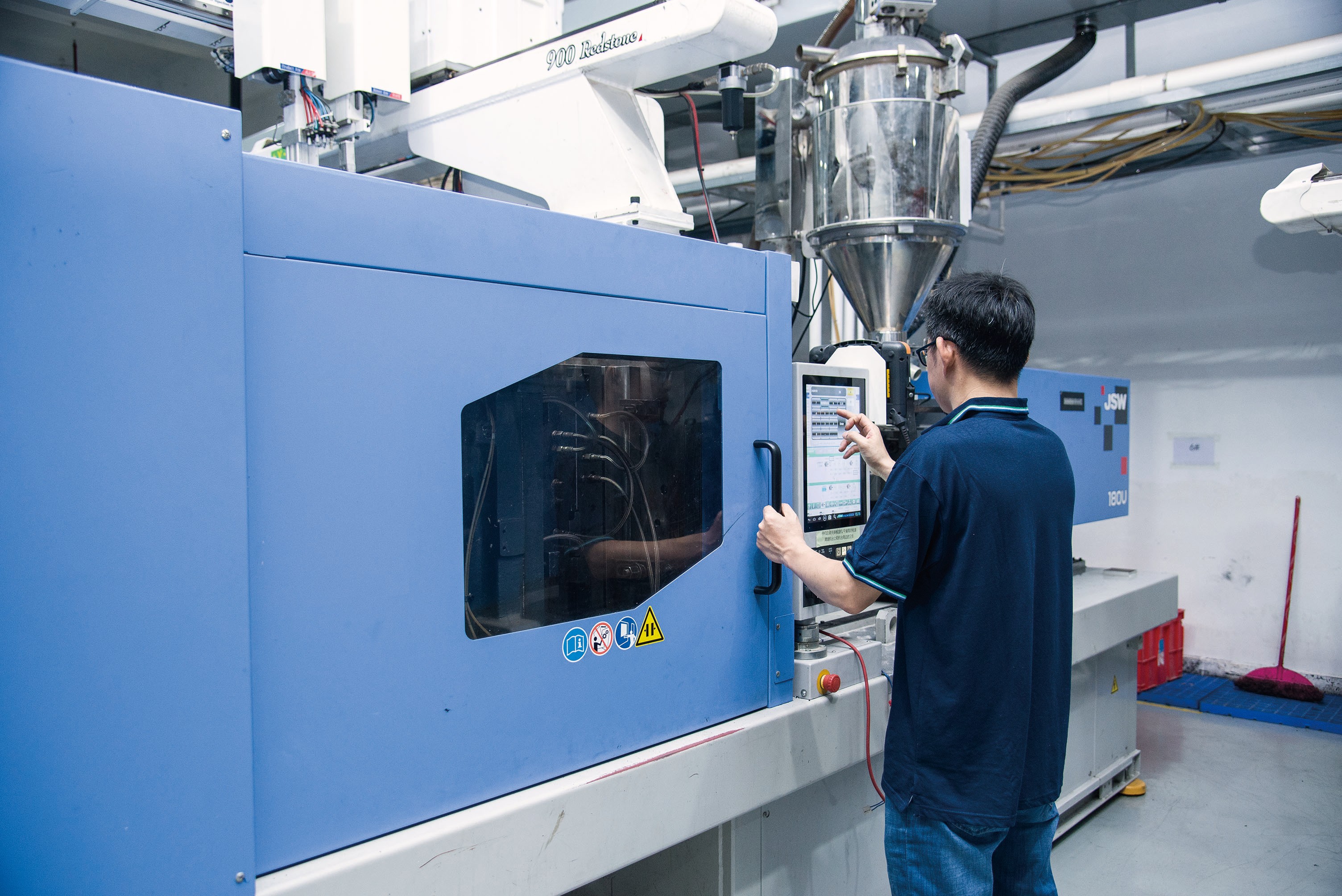
Regarding polycarbonate vs. ABS, Baoyuan is a leader in plastic injection molding. With extensive experience and knowledge in both materials, Baoyuan excels in polycarbonate and ABS injection molding, ensuring high-quality plastic injection-molded parts for various applications.
Baoyuan's Expertise in Polycarbonate and ABS Molding
Baoyuan's expertise in polycarbonate vs ABS molding sets them apart from the competition. They understand the unique properties of each material and can produce precise and durable injection-molded parts that meet specific requirements for impact strength, heat resistance, and chemical resistance. In addition to its technical proficiency, Baoyuan prides itself on offering cost-effective solutions without compromising quality. This combination of expertise and affordability makes them a top choice for businesses looking for high-quality plastic products.
Baoyuan's Specialization in Single-color and Double-color Plastic Products
Baoyuan stands out in the plastic product industry by offering exceptional versatility and unmatched customization. Here's what sets them apart:
- Single & Double-Color Expertise: Baoyuan designs plastic products in single and double colors, utilizing top-tier polycarbonate and ABS materials.
- Complex Designs Made Easy: Their advanced manufacturing processes allow for the easy creation of intricate designs, ensuring a perfect fit for various applications across numerous industries.
- Unmatched Customization: Baoyuan takes customization a step further. Their experienced engineers and designers collaborate closely with clients to understand their needs and deliver innovative solutions that surpass expectations. This commitment to customization allows them to create unique and tailored products for various applications.
Combining versatility with exceptional customization, Baoyuan ensures your plastic product needs are met and exceeded.
Baoyuan's Advanced Mold Design and Injection Molding Techniques
With advanced mold design and injection molding techniques, Baoyuan ensures the highest quality standards for their polycarbonate vs ABS products. Their attention to detail and precision result in consistently reliable plastic mold injection outcomes that exceed customer expectations.
With a focus on continuous improvement and innovation, Baoyuan stays ahead of the curve in mold design and injection molding techniques. By investing in the latest technology and staying up-to-date with industry trends, they can offer cutting-edge solutions that set them apart from their competitors. This commitment to staying at the forefront of their industry ensures that customers receive the most advanced and high-quality polycarbonate vs ABS products available on the market.
By choosing Baoyuan for your polycarbonate vs ABS needs, you can be confident that you are working with a trusted partner who delivers superior quality products through expert manufacturing processes.
Choose the Right Material for Your Specific Needs
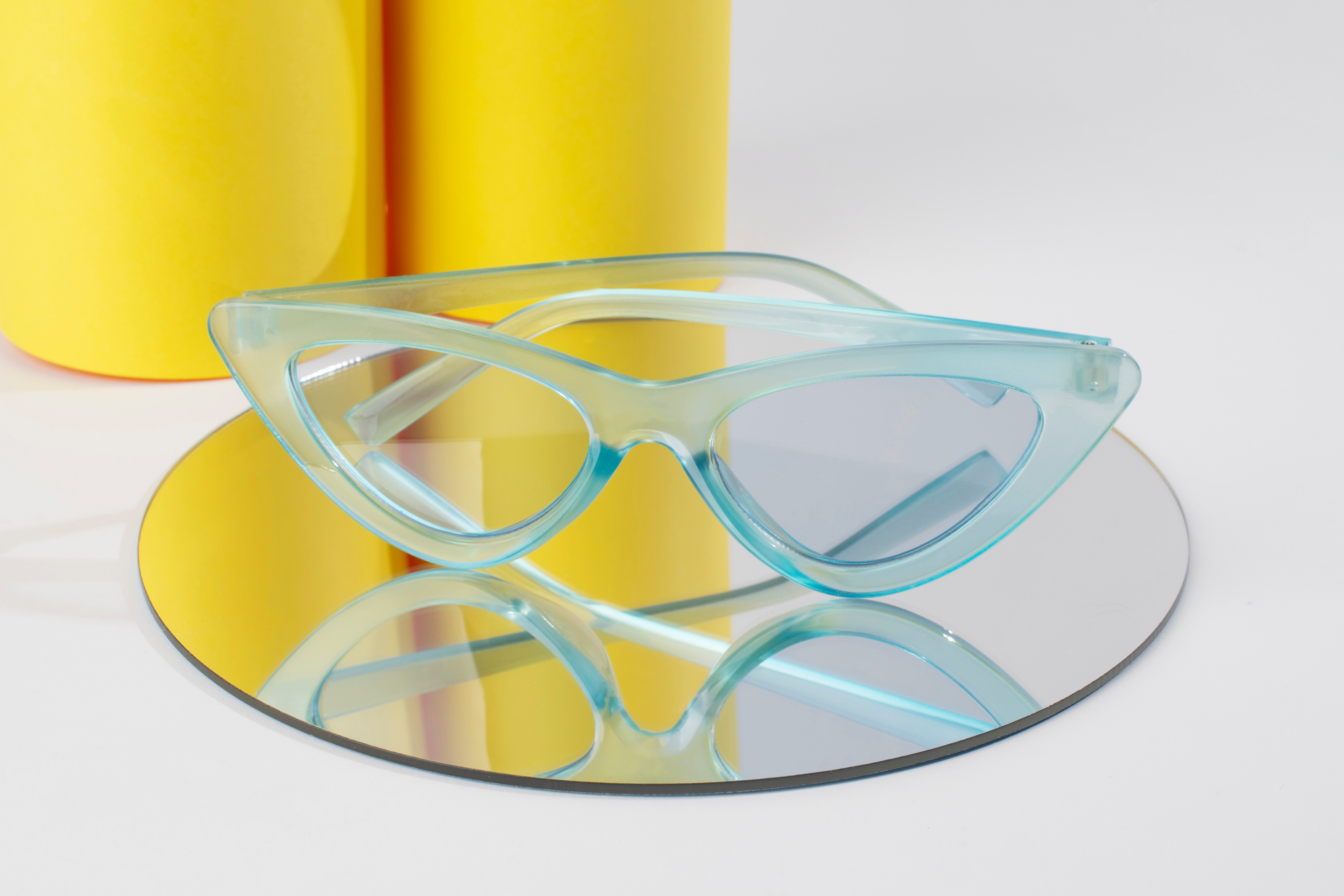
When choosing the right material for your specific needs, the differences between polycarbonate and ABS are crucial to consider. Polycarbonate injection molding offers superior impact strength and heat resistance, making it ideal for applications that require durability and toughness. On the other hand, ABS injection molding provides excellent chemical resistance, making it suitable for a wide range of industrial and consumer products. Understanding these distinctions will help you make informed decisions for your plastic mold injection projects.
Whether you require plastic injection-molded parts with exceptional impact strength or chemical resistance, understanding the advantages of polycarbonate vs. ABS is essential in choosing the right material for your specific needs. Polycarbonate's superior impact strength is ideal for applications of protective gear and automotive components. At the same time, ABS's chemical resistance is well-suited for consumer products like electronic housing and appliances.
When considering the right material for your specific needs, it's important to consider the cost-effectiveness of polycarbonate vs ABS. While polycarbonate may offer superior impact strength, ABS is often more affordable and can provide adequate chemical resistance for many consumer products. Understanding the balance between performance and cost can help you make a well-informed decision when choosing between these materials for your plastic injection molded parts.
Baoyuan's Superior Quality Assurance in Polycarbonate and ABS Products
At Baoyuan, we are your one-stop shop for top-quality plastic injection molded parts and expert advice on material selection. Here's what sets us apart:
- Unmatched Polycarbonate vs. ABS Expertise: Our team can guide you through the key differences between these popular materials to ensure you select the best fit for your application.
- Superior Quality Assurance: Our advanced manufacturing processes guarantee that each part meets the highest durability, performance, and reliability standards.
- Dedicated Support: We understand the importance of informed decisions. That's why our team is always available to answer your questions and provide guidance throughout the entire process, from material selection to design optimization and production.
Let Baoyuan be your partner in achieving success with your next injection molded project.
Making Informed Decisions for Polycarbonate and ABS Applications
Making informed decisions for polycarbonate vs ABS applications requires a deep understanding of their physical properties and specific advantages. With Baoyuan's extensive experience in polycarbonate injection molding and ABS injection molding, we can provide valuable insights into the best material choice for your unique requirements. Trust us to guide you through the decision-making process with our expertise in plastic mold injection.