Introduction
When it comes to plastic for injection molding, choosing the right material is crucial for achieving high-quality results. Understanding the best plastic for injection molding involves considering factors such as heat resistance, flexibility, and durability. The importance of quality plastic in injection molding cannot be overstated, as it directly impacts the final product's performance and longevity.
Understanding the Best Plastic for Injection Molding
Selecting the best plastic for injection molding involves evaluating various types of injection moldable plastics such as polypropylene, polyethylene, and polystyrene. Each type has unique characteristics that make them suitable for different applications in plastic manufacturing.
Factors to Consider in Plastic Selection
Factors to consider in plastic selection include the intended use of the final product, environmental conditions, and cost-effectiveness. These considerations play a significant role in determining which type of plastic is best suited for a specific injection molding project.
Importance of Quality Plastic in Injection Molding
Quality plastic is essential in injection molding to ensure that the finished products meet industry standards and customer expectations. Using high-quality materials not only enhances the performance of injection molded parts but also contributes to their longevity and overall value.
Types of Plastic for Injection Molding

When it comes to plastic for injection molding, there are several types to consider. Polypropylene is a popular choice due to its high melting point and excellent chemical resistance, making it ideal for automotive parts and packaging. Polyethylene, known for its flexibility and impact resistance, is commonly used in medical devices and consumer goods. Polystyrene, with its low cost and ease of molding, is often seen in disposable cutlery and packaging materials.
Polypropylene
Polypropylene is a versatile plastic that can be easily molded using an injection molding machine. Its heat resistance makes it suitable for applications where high temperatures are involved, such as in the automotive industry for manufacturing interior components like dashboards and door trims.
Polyethylene
Polyethylene is a popular choice in plastic manufacturing due to its ability to be molded into various shapes with ease. Its durability makes it an ideal material for medical devices such as syringes and containers, as well as for consumer goods like bottles and toys.
Polystyrene
Polystyrene is a cost-effective option for injection moldable plastics, often used in the production of disposable cutlery, food packaging, and insulation materials due to its lightweight nature and ease of molding.
Remember that choosing the right type of plastic is crucial in ensuring the success of your injection mold project!
Characteristics of Ideal Plastic for Injection Molding
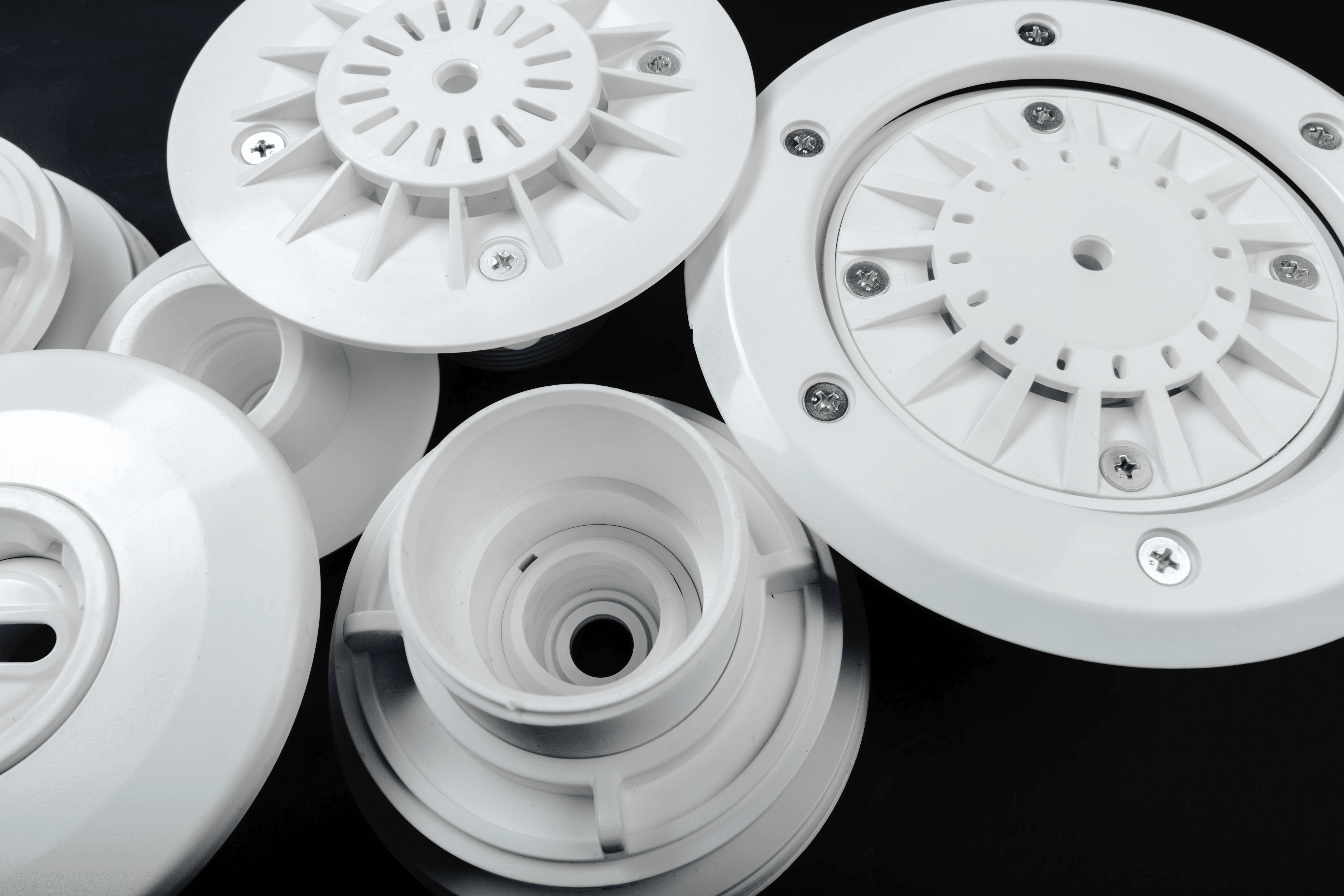
When it comes to plastic for injection molding, heat resistance is a crucial characteristic to consider. The plastic must be able to withstand high temperatures without deforming or losing its structural integrity. This is especially important during the injection molding process, where the plastic is melted and then injected into the mold at elevated temperatures.
Flexibility is another key feature of injection moldable plastics. The plastic must be able to bend and stretch without breaking, allowing it to be molded into various shapes and sizes without compromising its strength or durability. This ensures that the final product can withstand everyday wear and tear while maintaining its form.
Durability is essential for plastic used in injection molding as well. The material must be able to withstand repeated use and exposure to external elements without deteriorating or losing its properties. This is especially important for products that will be used in demanding environments, such as automotive parts or medical devices.
With these characteristics in mind, it becomes clear that not all plastics are suitable for injection molding. It takes careful consideration and expertise in mold plastic injection to select the right material for each application. Baoyuan's extensive experience in plastic manufacturing and injection molding machine technology allows us to expertly choose the best injection moldable plastics for your specific needs.
Baoyuan's dedication to quality control ensures that only the most suitable plastics are used in our injection molding processes. Our precision injection molding techniques guarantee that each product meets the highest standards of performance and reliability. With Baoyuan as your partner, you can trust that your products will benefit from the ideal characteristics of plastic for injection molding.
In conclusion, choosing the right plastic for injection molding requires careful consideration of its heat resistance, flexibility, and durability. Baoyuan's expertise in mold design and precision manufacturing makes us your ideal partner for quality plastic solutions. With our commitment to maximizing the potential of plastic in injection molding, we ensure that your products meet and exceed industry standards.
Baoyuan’s Expertise in Plastic Selection
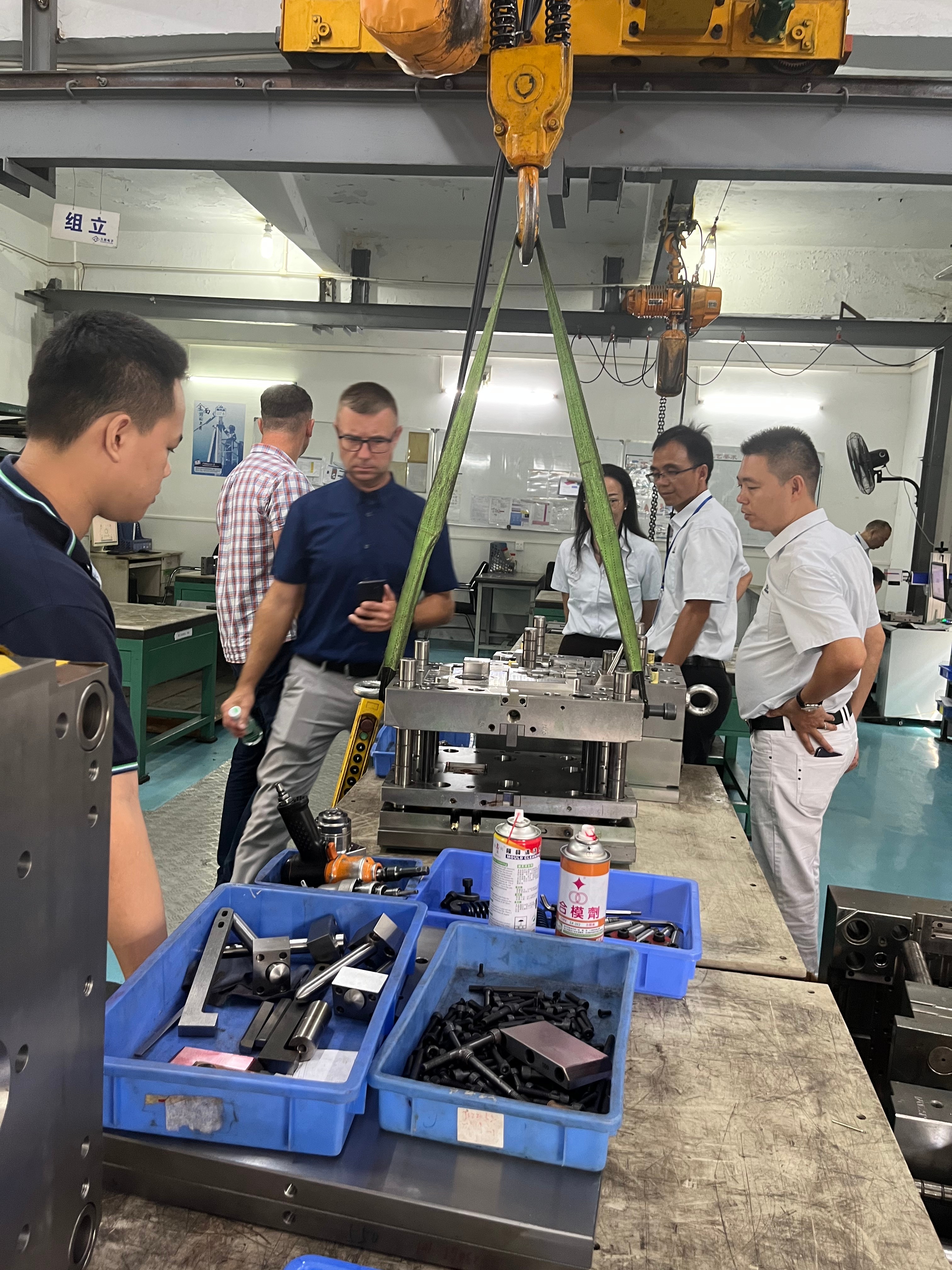
Baoyuan prides itself on its senior management team, boasting years of experience in the plastic manufacturing industry. With their extensive knowledge and expertise, they are well-versed in the intricate process of selecting the best plastic for injection molding, ensuring top-notch quality and functionality for every product.
Senior Management with Years of Experience
The senior management team at Baoyuan has a wealth of experience in mold plastic injection, having navigated through various challenges and innovations in the industry. Their deep understanding of injection moldable plastics enables them to make informed decisions when it comes to selecting the most suitable materials for each project, guaranteeing exceptional results. With their proficiency in mold design and injection molding, they are able to optimize production processes, minimize waste, and ensure that each product meets the highest quality standards. Their expertise also allows them to identify potential issues early on and implement effective solutions, saving time and resources for their clients.
Proficiency in Mold Design and Injection Molding
Baoyuan's proficiency in mold design and injection molding sets them apart as leaders in the field. Their mastery of the intricacies involved in mold plastic injection allows them to optimize production processes, resulting in high-quality plastic products that meet and exceed industry standards. With a keen understanding of material properties and production techniques, Baoyuan ensures that their plastic products are not only durable and reliable but also cost-effective for their clients. By staying ahead of the curve in terms of technological advancements and industry best practices, Baoyuan consistently delivers innovative solutions that push the boundaries of what is possible in mold design and injection molding.
Quality Assurance for Plastic Products
At Baoyuan, quality assurance is paramount when it comes to plastic for injection molding. Their stringent quality control measures ensure that every product meets the highest standards of durability, flexibility, and heat resistance. This commitment to excellence makes Baoyuan a trusted partner for all plastic injection molding needs. In addition to their rigorous testing procedures, Baoyuan also places a strong emphasis on sustainable manufacturing practices. By using eco-friendly materials and reducing waste in production, they are able to provide high-quality plastic products while minimizing their environmental impact.
Best Practices for Using Plastic in Injection Molding

Proper Mold Design for Different Plastic Types
When it comes to plastic for injection molding, proper mold design is crucial to ensure the success of the process. Different types of plastics require specific mold designs to achieve the desired results. Understanding the unique properties of each injection moldable plastic is essential in creating molds that can withstand the pressures and temperatures involved in the injection molding process.
Different types of plastics, such as ABS, polycarbonate, and polypropylene, have varying properties that require specific mold designs to achieve the desired results. For example, ABS plastic is known for its toughness and impact resistance, so the mold design needs to account for these properties to ensure the final product meets quality standards. On the other hand, polycarbonate is valued for its optical clarity and high heat resistance, requiring a mold design that can withstand higher temperatures during the injection molding process.
Precision Injection Molding Techniques
Precision is key when it comes to plastic injection molding. Utilizing advanced injection molding machines and techniques allows for precise control over the entire process, resulting in high-quality plastic products. From temperature control to pressure management, precision injection molding techniques ensure that each product meets strict quality standards.
Precision injection molding techniques also involve the use of advanced mold design and tooling technology. This ensures that the plastic material is injected into the mold with extreme precision, resulting in consistent and accurate product dimensions. By utilizing state-of-the-art mold design and tooling, manufacturers can achieve high repeatability and produce complex plastic parts with intricate details.
Quality Control Measures
In plastic manufacturing, quality control measures are essential to guarantee the reliability and durability of the final products. Implementing stringent quality control checks throughout the entire injection molding process ensures that any defects or imperfections are identified and addressed promptly. This commitment to quality control ultimately leads to superior plastic products that meet or exceed industry standards.
Furthermore, implementing quality control measures in plastic manufacturing helps to minimize waste and reduce production costs. By catching defects early on in the injection molding process, manufacturers can avoid having to scrap entire batches of products, saving both time and resources. This focus on quality also contributes to a more sustainable and environmentally friendly manufacturing process, as it reduces the amount of material that ends up in landfills.
Applications of Plastic for Injection Molding
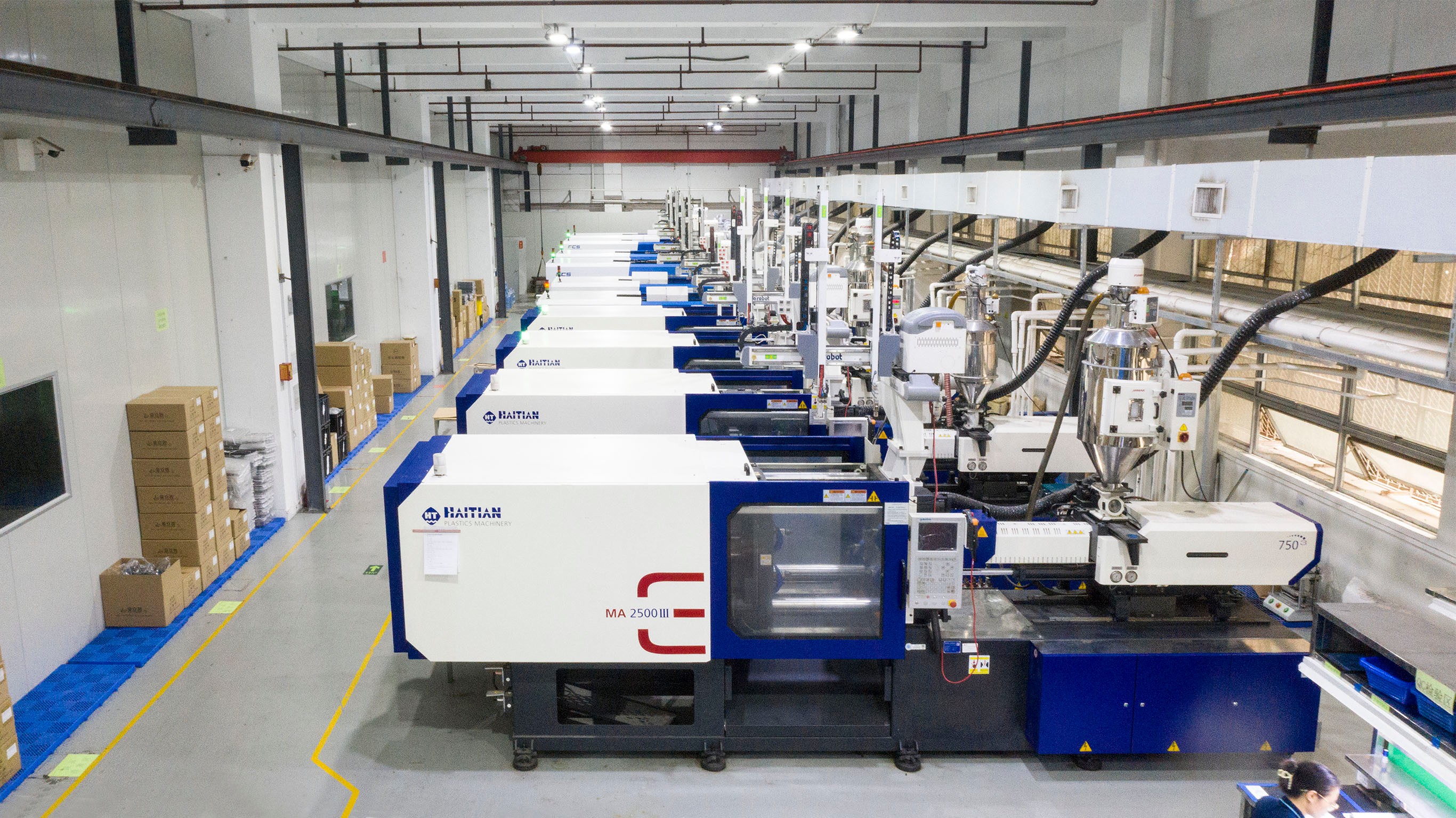
When it comes to injection moldable plastics, the automotive industry heavily relies on the durability and flexibility of plastic for various components such as bumpers, dashboards, and interior trim. The use of plastic injection molding in automotive parts manufacturing has revolutionized the industry by allowing for cost-effective production and lightweight materials that enhance fuel efficiency.
Automotive Parts
In the medical field, plastic injection molding is crucial for producing intricate and precise components for devices such as syringes, IV connectors, and surgical instruments. The ability to manufacture these medical devices with high-quality plastics ensures safety, reliability, and cost-effectiveness in healthcare settings.
In addition to medical devices, plastic injection molding plays a crucial role in producing automotive parts such as interior panels, bumpers, and dashboard components. The use of high-quality plastics in manufacturing these automotive components ensures durability, strength, and resistance to wear and tear, ultimately enhancing the safety and performance of vehicles on the road. Furthermore, the precision and intricacy achieved through injection molding allow for the creation of complex designs that contribute to the aesthetic appeal of modern automobiles.
Medical Devices
Consumer goods encompass a wide range of products that benefit from plastic injection molding, including household items, electronic casings, packaging materials, and toys. The versatility of plastic manufacturing allows for the creation of custom-designed consumer goods that are both aesthetically pleasing and functional.
Medical devices are another important category that benefits from plastic injection molding. From syringes to surgical instruments, plastic manufacturing allows for the production of precise, durable, and cost-effective medical devices that are essential for healthcare providers. The ability to create complex shapes and intricate designs makes plastic injection molding a valuable process for producing high-quality medical equipment.
Consumer Goods
Consumer goods cover a wide range of products that are used by individuals on a daily basis. From household items to electronic gadgets, plastic is an essential material in the manufacturing of these goods. The versatility and durability of plastics make them ideal for creating a variety of consumer products, including kitchenware, toys, and packaging materials. With Baoyuan’s expertise in plastic selection and injection molding, they can ensure that the consumer goods produced meet the highest standards of quality and performance. Whether it's designing intricate components for electronics or creating aesthetically pleasing household items, Baoyuan has the capabilities to deliver top-notch plastic solutions for consumer goods.
Conclusion
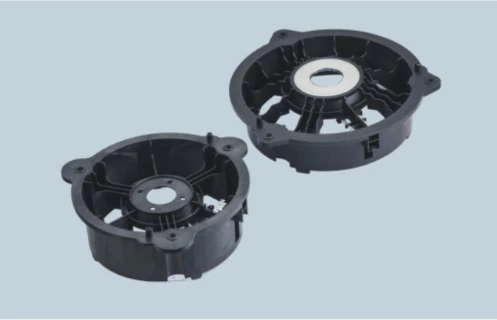
Choosing the Right Plastic for Your Injection Molding Needs
When it comes to choosing the right plastic for injection molding, it's crucial to consider factors such as heat resistance, flexibility, and durability. By understanding the specific needs of your project, you can select the best plastic that will result in high-quality and durable products.
Baoyuan: Your Partner for Quality Plastic Solutions
With Baoyuan's expertise in plastic selection and injection molding, you can trust that your project is in good hands. Our senior management team has years of experience in plastic manufacturing and injection moldable plastics, ensuring that we provide top-notch solutions for your needs.
Maximizing the Potential of Plastic in Injection Molding
By partnering with Baoyuan, you can maximize the potential of plastic in injection molding. Our precision injection molding techniques and quality control measures guarantee that your products meet the highest standards. With our dedication to excellence, we ensure that your plastic injection molding needs are met with utmost satisfaction.