Introduction
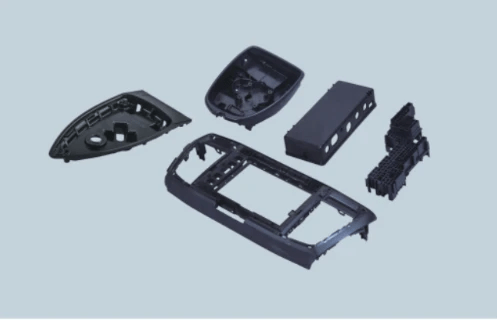
When it comes to plastic injection mold cost, understanding the various factors that impact it is crucial for effective cost management. From material selection to production volume, each aspect plays a significant role in determining the overall expense of injection molding. By carefully considering these key factors, businesses can achieve cost-effective mold solutions while maintaining high-quality standards.
Understanding Plastic Injection Mold Cost
The cost of plastic injection molding involves numerous components, including material expenses, tooling costs, and production volume considerations. It's essential to have a comprehensive understanding of these elements to accurately assess and manage the overall mold cost.
The Impact of Various Factors
Several factors influence plastic injection mold cost, such as material selection, design complexity, and production volume. Each of these aspects has a direct impact on the overall expenses incurred during the mold making and custom injection molding processes.
Key Considerations for Cost Management
Effective cost management in plastic injection molding requires careful consideration of various factors such as material selection, design complexity, and supplier relationships. By strategically managing these elements, businesses can optimize their production tooling costs while ensuring high-quality results.
Material Selection
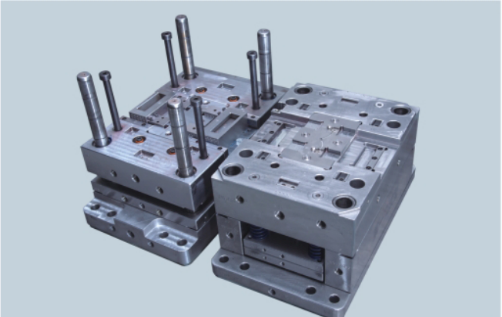
When it comes to plastic injection mold cost, material selection plays a crucial role in determining the overall expenses. The type of material chosen for the molding process can significantly impact the cost, as certain materials may be more expensive or require specialized equipment for processing. It's essential to carefully consider the balance between material quality and cost-effectiveness to ensure that the end product meets performance requirements without exceeding budget constraints.
Impact of Material Choice on Cost
The choice of material for plastic injection molding can have a direct impact on the overall cost of production. Some materials, such as high-performance engineering resins, may come with a higher price tag due to their advanced properties and manufacturing requirements. On the other hand, commodity plastics may offer a more cost-effective solution for less demanding applications. By understanding the specific needs of the project and evaluating different material options, manufacturers can make informed decisions that align with both performance and budget goals.
Balancing Quality and Cost
Balancing quality and cost in material selection is essential for achieving successful injection molding outcomes while managing expenses effectively. While it may be tempting to opt for cheaper materials to reduce upfront costs, compromising on quality can lead to long-term issues such as part failure or increased maintenance requirements. By carefully assessing the performance requirements of the molded parts and exploring different material options, manufacturers can strike a balance that maximizes quality without overspending.
It is also important to consider sustainable material options when balancing quality and cost in material selection. By choosing eco-friendly materials, manufacturers can not only contribute to environmental conservation but also benefit from the long-term cost savings associated with sustainable materials. Additionally, using sustainable materials can enhance a company's brand image and appeal to environmentally conscious consumers, providing a competitive edge in the market. Therefore, considering sustainable material options is a crucial aspect of achieving successful injection molding outcomes while managing expenses effectively.
Sustainable Material Options
In today's environmentally conscious landscape, sustainable material options are gaining traction within the plastic injection molding industry. Manufacturers are increasingly looking towards eco-friendly alternatives that not only reduce environmental impact but also offer long-term cost savings through resource efficiency and waste reduction. Sustainable materials such as bioplastics or recycled thermoplastics present an opportunity to align production practices with sustainability goals while potentially lowering overall mold costs.
As the demand for sustainable material options continues to grow, manufacturers are also exploring innovative ways to incorporate renewable resources into their production processes. This includes the use of bio-based materials derived from plants or other organic sources, offering a more environmentally friendly alternative to traditional plastics. By integrating these sustainable materials into plastic injection molding, manufacturers can not only reduce their carbon footprint but also appeal to eco-conscious consumers who prioritize sustainability in their purchasing decisions.
Design Complexity
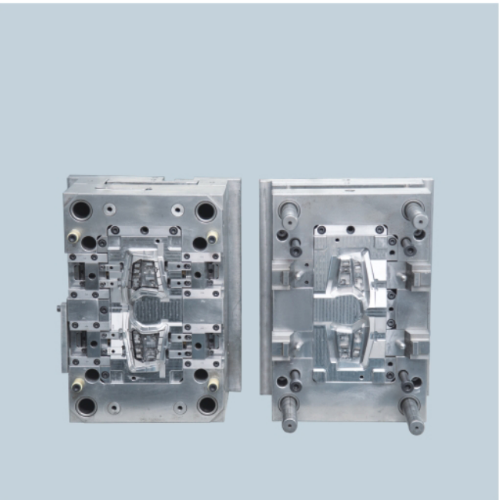
When it comes to plastic injection molding, the design complexity plays a significant role in determining the overall cost. Intricate designs with multiple undercuts, tight tolerances, or complex geometries can increase the mold making and production tooling costs. Therefore, it's crucial to carefully consider the design complexity and its impact on cost before moving forward with the manufacturing process.
Influence of Design Complexity on Cost
Design complexity directly affects plastic injection mold cost, as intricate designs often require more advanced tooling and equipment, leading to higher production costs. Additionally, complex designs may result in longer production times and increased material waste, further driving up expenses. By understanding how design complexity impacts cost, manufacturers can make informed decisions to optimize their designs for cost-effective production.
Design for Manufacturability (DFM) is a critical strategy for minimizing the impact of design complexity on production costs. By incorporating DFM principles into the design process, manufacturers can identify and address potential manufacturing challenges early on, reducing the need for costly modifications during production. This proactive approach not only streamlines the manufacturing process but also helps to optimize product quality and performance.
Design for Manufacturability
To mitigate the impact of design complexity on cost, it's essential to prioritize design for manufacturability. This approach involves designing parts and molds with ease of manufacturing in mind, reducing unnecessary complexities that drive up expenses. By collaborating closely with experienced mold makers and custom injection molding experts during the design phase, manufacturers can identify potential cost-saving opportunities without compromising quality.
Streamlining the Design Process
Streamlining the design process is key to controlling plastic injection mold cost while maintaining high-quality standards. Utilizing advanced CAD software and simulation tools can help identify potential issues early in the design phase, allowing for necessary adjustments to optimize manufacturability and minimize costs. By streamlining the design process, manufacturers can achieve efficient production tooling and mold making processes that align with their budgetary constraints.
Remember that managing plastic injection mold cost is crucial for achieving long-term success in manufacturing. By carefully considering the influence of design complexity on cost and implementing strategies such as designing for manufacturability and streamlining the design process, manufacturers can achieve optimal results without breaking the bank.
Production Volume
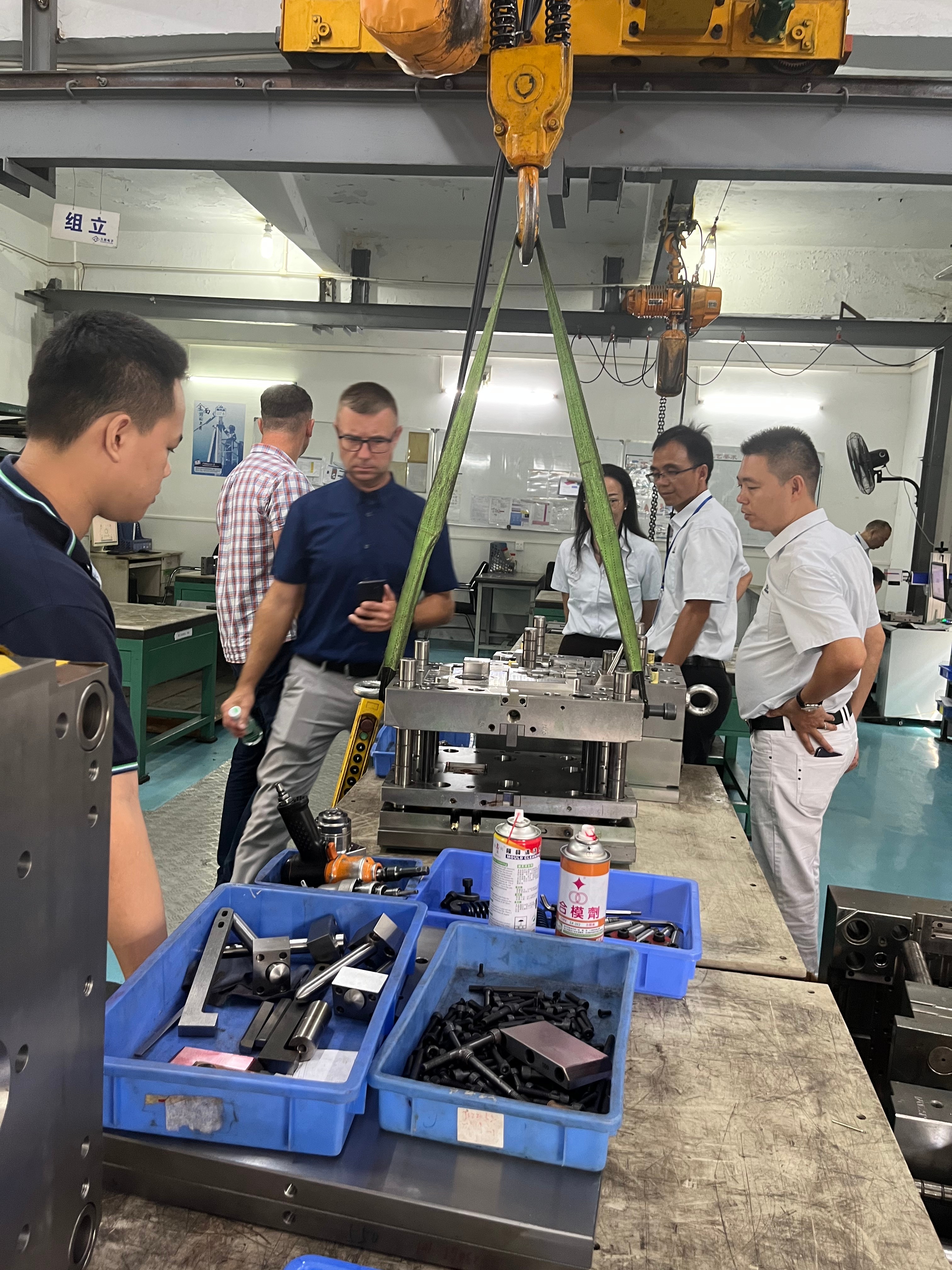
When it comes to plastic injection mold cost, production volume plays a significant role in determining the overall expenses. The concept of economies of scale is particularly relevant in injection molding, as larger production runs often result in lower per-unit costs. This means that the more parts you produce, the lower the cost per part becomes, making mass production a more cost-effective option.
Economies of Scale in Injection Molding
Economies of scale refer to the cost advantages that a business can achieve by increasing its output. In the context of injection molding, this means that as the production volume increases, the fixed costs associated with tooling and equipment are spread out over a larger number of units, resulting in lower average costs per part. By taking advantage of economies of scale, businesses can optimize their manufacturing processes and reduce overall plastic injection mold cost.
As production volume increases, businesses can also benefit from reduced material costs. Bulk purchasing of raw materials allows for lower per-unit costs, further contributing to the overall cost advantage of mass production in injection molding. Additionally, with higher production volumes, businesses can negotiate better rates with suppliers and streamline their supply chain, leading to additional cost savings.
Prototype vs. Mass Production Costs
While prototyping is an essential step in custom injection molding, it's important to recognize that prototype costs are typically higher on a per-unit basis compared to mass production costs. This is due to the fact that prototypes often require specialized tooling and equipment adjustments, as well as smaller production runs which don't benefit from economies of scale. As such, it's crucial for businesses to carefully plan and budget for both prototype and mass production expenses when considering plastic molding projects.
Additionally, businesses should consider the potential for varied production volumes when planning for plastic molding projects. While mass production offers cost advantages due to economies of scale, it's important to anticipate fluctuations in demand and be prepared to adjust production accordingly. This may involve the ability to ramp up production quickly to meet increased demand or scale back production during slower periods. By factoring in these potential scenarios, businesses can better manage their resources and optimize their manufacturing processes.
Planning for Varied Production Volumes
Given the impact of production volume on plastic injection mold cost, it's essential for businesses to plan for varied production volumes based on market demand and product lifecycle considerations. By understanding how changes in production volume affect unit costs, companies can make informed decisions about scaling up or down their manufacturing operations as needed. This flexibility allows businesses to adapt to changing market conditions while maintaining cost-effective mold solutions.
Furthermore, businesses should also consider the potential impact of tooling and equipment on production volume planning. Investing in high-quality, durable molds and machinery can help to minimize downtime and maintenance costs, ensuring that production can continue smoothly even during periods of high demand. Additionally, businesses should explore options for flexible tooling and equipment that can easily be adjusted to accommodate changes in production volume, providing a cost-effective solution for scaling operations up or down as needed.
Tooling and Equipment
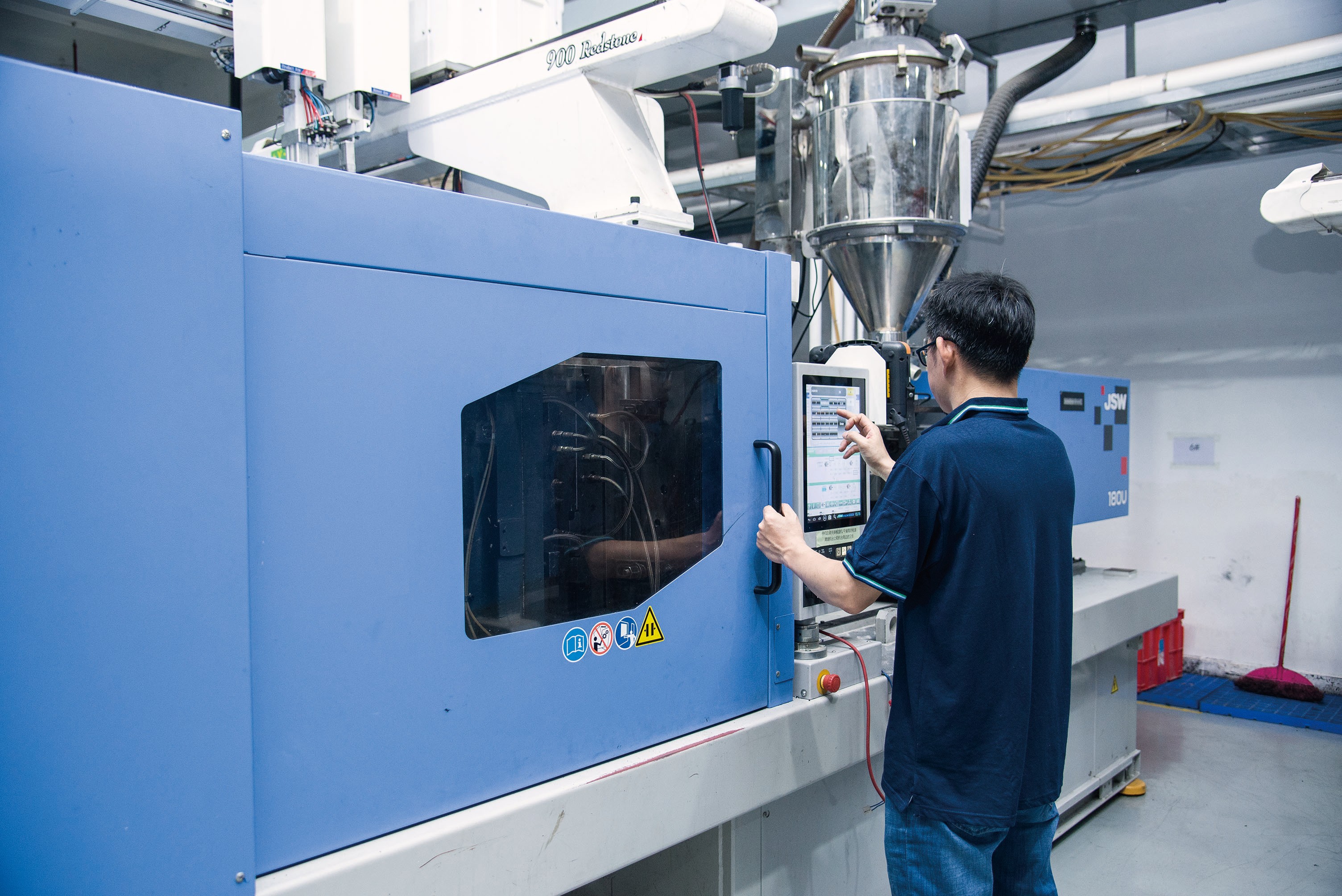
When it comes to plastic injection molding, the importance of quality tooling cannot be overstated. High-quality molds are essential for producing consistent, precise parts, reducing the need for costly rework or repairs. By investing in well-crafted molds, manufacturers can minimize production downtime and ensure a higher return on their initial investment in mold making.
Advanced equipment plays a crucial role in optimizing the injection molding process. From state-of-the-art machinery to cutting-edge automation technology, modern equipment can significantly improve production efficiency and reduce cycle times. This not only leads to cost savings but also allows for greater flexibility in meeting varying production demands.
Optimizing production tooling involves a strategic approach to mold design and maintenance. By working closely with experienced mold designers and technicians, manufacturers can identify opportunities to streamline tooling processes, reduce material waste, and enhance overall productivity. This proactive approach ensures that the full potential of custom injection molding is realized without unnecessary expenses.
By understanding the critical role of quality tooling and advanced equipment in plastic injection molding, manufacturers can effectively manage their costs while achieving superior results. With optimized production tooling and state-of-the-art machinery, companies can confidently pursue custom injection molding solutions that deliver exceptional value without compromising on quality or efficiency.
Supplier Relationships
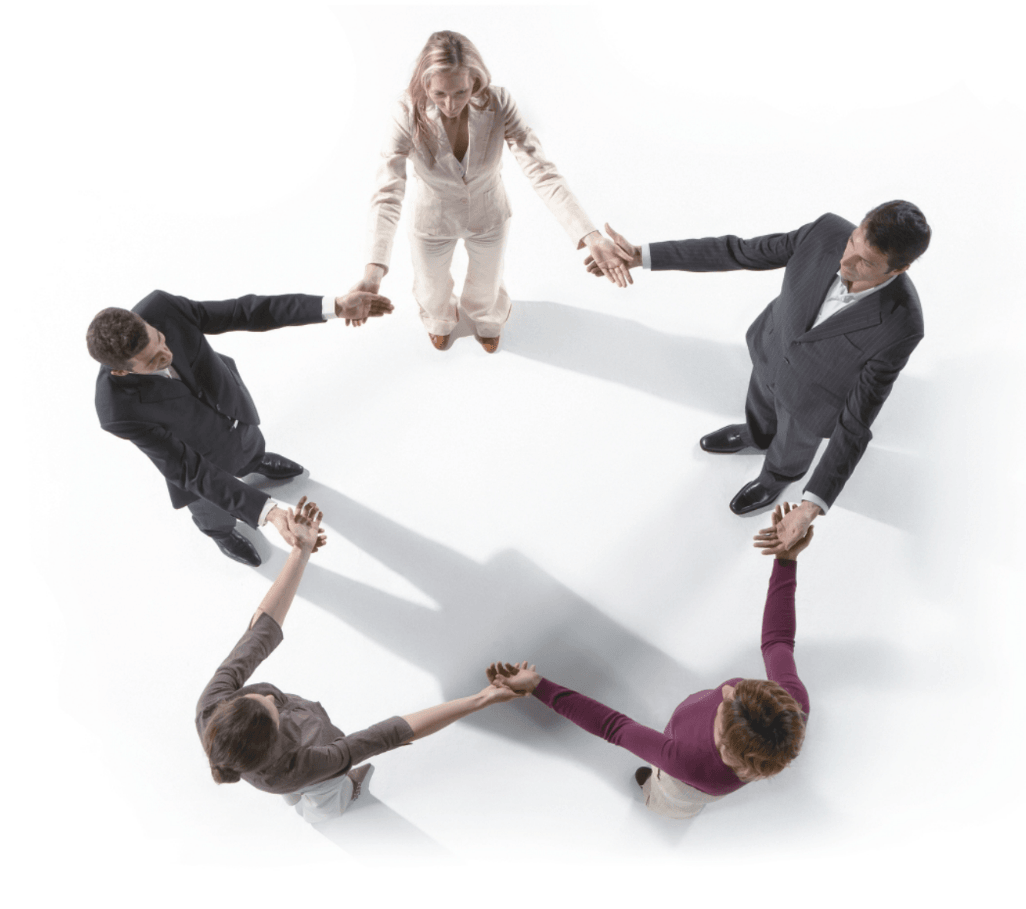
Collaborating with Reliable Suppliers
When it comes to managing plastic injection mold cost, collaborating with reliable suppliers is crucial. By partnering with experienced and reputable suppliers, you can ensure the quality and consistency of materials and components for your injection molding needs. This partnership also allows for better communication and problem-solving, leading to more efficient production processes.
Negotiating Pricing and Terms
Negotiating pricing and terms with suppliers is a key aspect of managing plastic injection mold cost. By engaging in open discussions and leveraging your business relationship, you can work towards favorable pricing that aligns with your budget while maintaining quality standards. Establishing clear terms and conditions can also help in avoiding potential misunderstandings down the line.
Baoyuan's Expertise in Supplier Management
With Baoyuan's extensive expertise in supplier management, you can benefit from their established network of trusted partners in the industry. Their team is adept at negotiating competitive pricing and favorable terms on behalf of their clients, ensuring cost-effective solutions without compromising on quality or reliability.
By fostering strong relationships with suppliers, negotiating effectively, and leveraging Baoyuan's expertise in supplier management, you can achieve strategic cost management for custom injection molding projects while maximizing value for your investment.
Conclusion
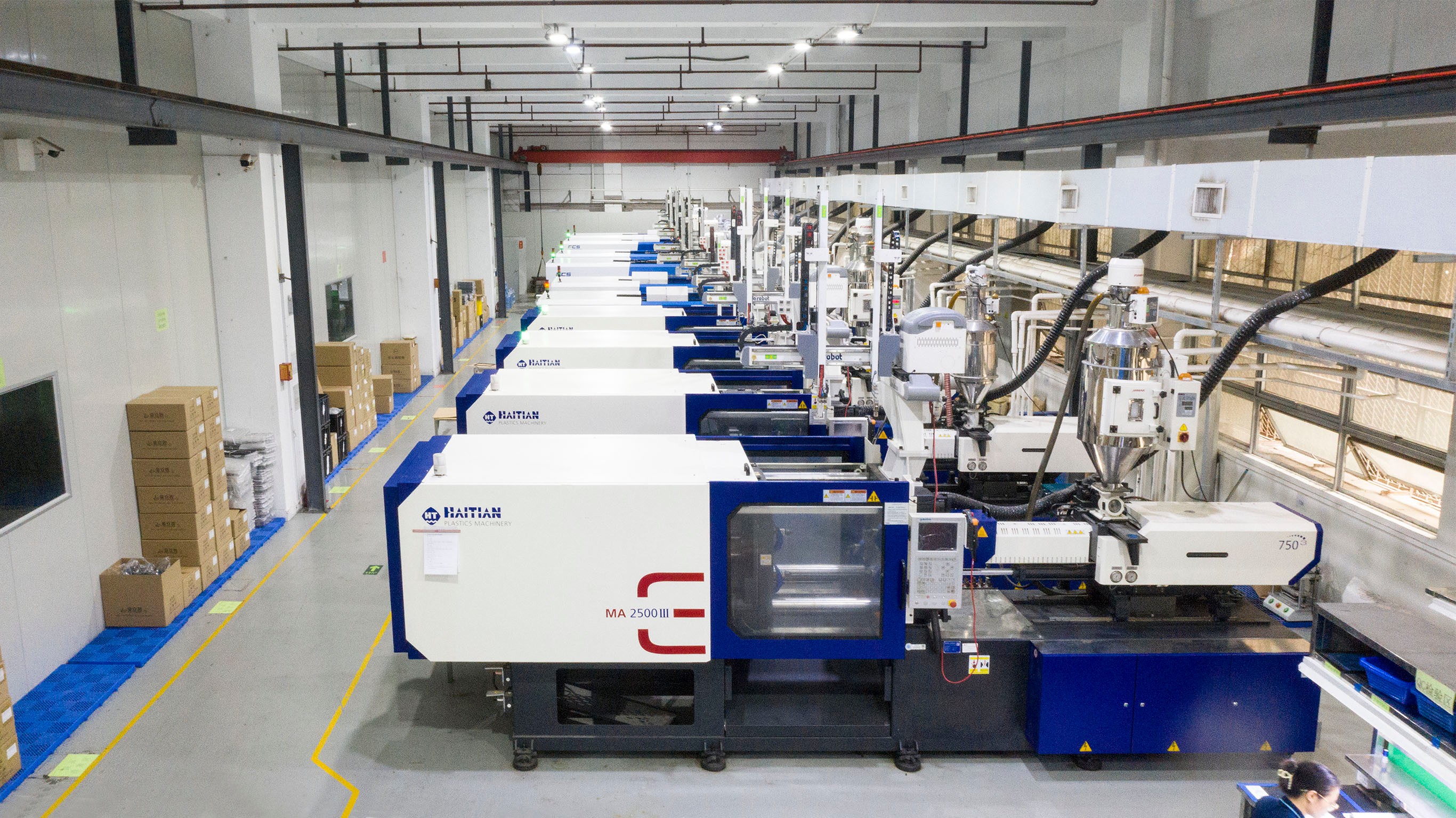
In the competitive world of plastic injection molding, strategic cost management is key to success. By carefully considering material selection, design complexity, production volume, tooling and equipment, and supplier relationships, companies can effectively manage plastic injection mold cost. Baoyuan's expertise in custom injection molding and mold making can be leveraged to achieve cost-effective solutions.
Strategic Cost Management for Injection Molding
Strategic cost management in plastic injection molding involves a holistic approach that takes into account various factors such as material selection, design complexity, production volume, tooling and equipment, and supplier relationships. By carefully managing these aspects, companies can optimize their costs while maintaining high-quality standards in their products.
Leveraging Baoyuan's Expertise
Baoyuan's extensive experience in custom injection molding and mold making makes them an invaluable partner for companies looking to optimize their plastic injection mold cost. With a focus on quality tooling and advanced equipment, Baoyuan offers expertise that can help businesses achieve efficient production processes with minimal waste.
Achieving Cost-Effective Mold Solutions
By collaborating with Baoyuan, businesses can achieve cost-effective mold solutions that balance quality with affordability. With a focus on sustainable material options and streamlined design processes, Baoyuan's expertise can help companies navigate the complexities of plastic molding while keeping costs under control.