Introduction
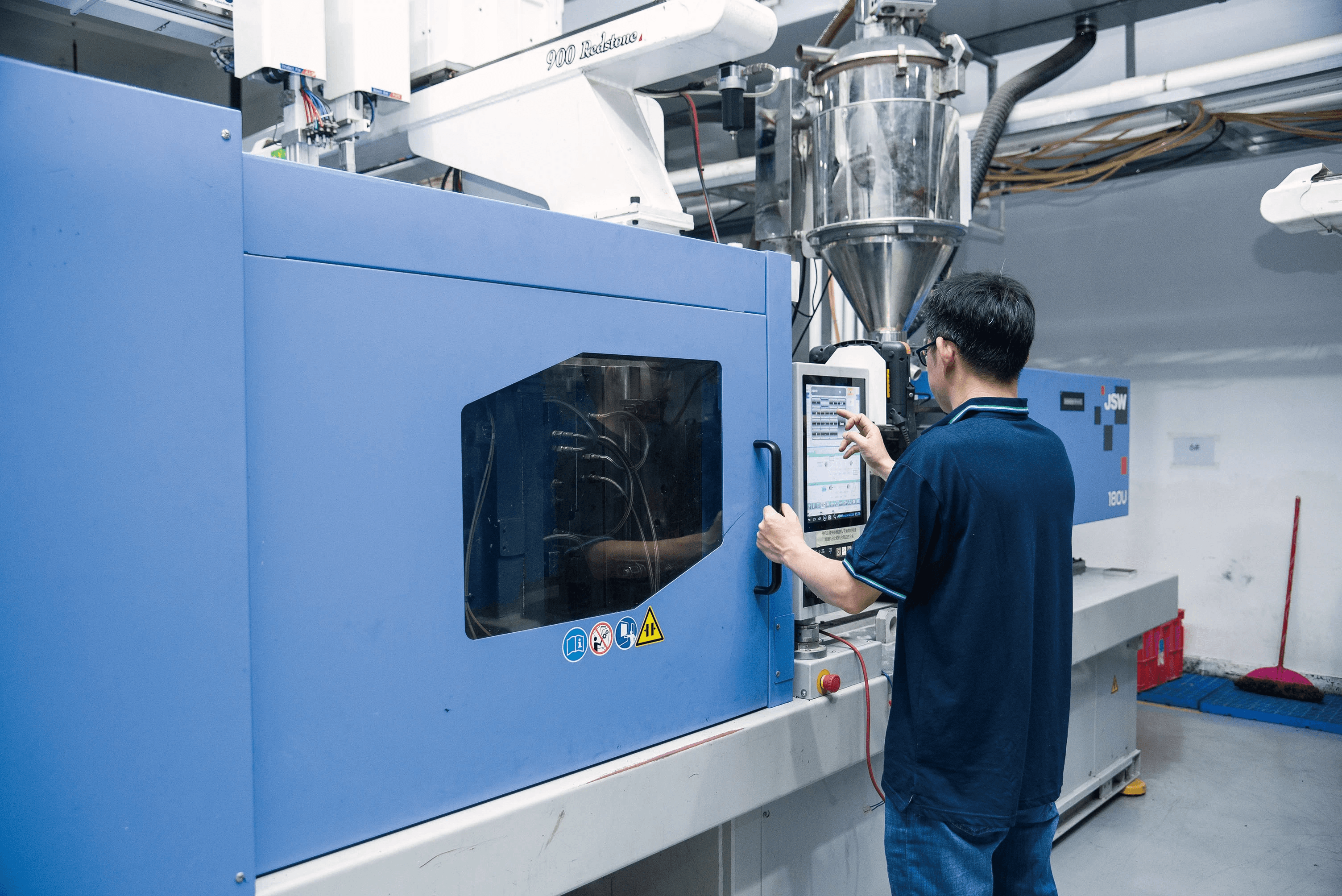
Injection molding acrylic is a fascinating process that combines artistry with engineering precision. It involves creating complex shapes and designs by injecting molten acrylic into a mold, allowing manufacturers to produce high-quality plastic products efficiently. This method not only enhances the aesthetic appeal of products but also ensures durability, making it a preferred choice in various industries.
Understanding Injection Molding Acrylic
At its core, injection molding acrylic refers to the technique of shaping acrylic materials using an injection molding machine. The process begins with heating the acrylic until it reaches a molten state, which is then injected into a carefully designed mold. This allows for intricate designs and smooth finishes that are often sought after in applications ranging from automotive parts to household items.
Importance of Quality in Acrylic Production
Quality is paramount in the production of injection molded acrylic products; any flaws can lead to significant waste and increased costs. High-quality standards ensure that finished products meet both functional and aesthetic requirements, enhancing customer satisfaction and brand reputation. Moreover, maintaining quality throughout the injection molding process minimizes defects such as warping or surface imperfections, which can compromise product integrity.
Overview of Key Techniques
The world of injection molding encompasses several key techniques that play crucial roles in achieving optimal results with acrylic materials. Techniques such as mold flow analysis help predict how molten material will fill the mold cavity, ensuring even distribution and minimizing defects during production. Additionally, advancements in software technology have revolutionized mold design processes, allowing for greater precision and efficiency in plastic injection molding operations.
Selecting the Right Materials
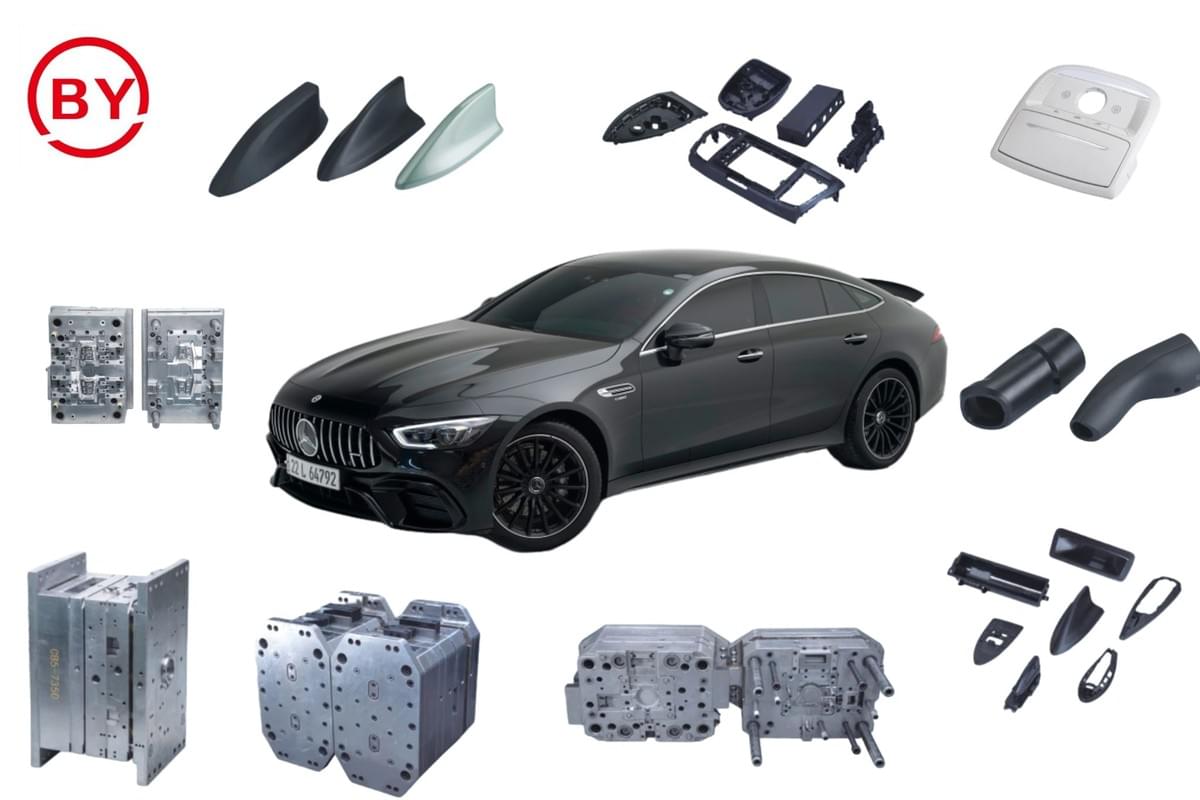
Advantages of Acrylic as a Material
Acrylic stands out in the world of injection moldable plastics for several reasons. First and foremost, it offers superior clarity that rivals glass while being much lighter and more durable. Additionally, acrylic is highly resistant to impact and weathering, making it an ideal choice for both indoor and outdoor applications where longevity is crucial.
Another advantage of using acrylic in injection molding is its excellent processing characteristics. The material flows smoothly during the mould injection moulding process, allowing for intricate designs without compromising structural integrity. This ease of processing translates into reduced cycle times and lower production costs—an attractive proposition for manufacturers looking to optimize their plastic injection molding operations.
Furthermore, acrylic can be easily colored or textured during production, providing manufacturers with endless design possibilities. Whether creating clear displays or vibrant colored components, acrylic’s adaptability makes it a star player in various industries—from automotive parts to consumer goods.
Comparing Acrylic to Other Plastics
While there are numerous types of plastics available for injection casting processes, acrylic often emerges as a preferred choice when compared to alternatives like polycarbonate or PVC. Unlike polycarbonate, which may be more prone to scratching despite its toughness, acrylic maintains its aesthetic appeal over time with proper care. This characteristic makes it particularly valuable in applications where appearance matters—think signage or decorative items.
Moreover, when pitted against PVC—a material known for its rigidity—acrylic offers greater flexibility without losing strength during the plastic injection molding process. This flexibility allows designers more freedom when crafting complex shapes that require precision without compromising durability. Ultimately, choosing between these materials depends on specific project requirements; however, acrylic consistently proves itself as a reliable option across various sectors.
Lastly, unlike some thermoplastics that can warp under heat exposure or stress conditions during production processes like mould plastic injection techniques, acrylic retains dimensional stability even at elevated temperatures. This property ensures consistent quality throughout mass production runs while minimizing defects related to warping or shrinkage—key factors that can derail manufacturing efforts.
Key Properties for Injection Molding
To achieve optimal results in injection molding acrylic projects, certain key properties must be considered during material selection and processing stages. One critical property is melt flow index (MFI), which influences how well the material fills molds under pressure during plastic injection molding operations. A suitable MFI ensures uniform filling without voids or inconsistencies that could compromise part performance later on.
Another important property is thermal stability; this determines how well the material withstands heat during both processing stages and end-use applications without degrading or losing integrity over time. For instance, maintaining appropriate temperature management techniques throughout the moulding process helps preserve these essential characteristics while preventing common defects associated with overheating.
Lastly—and perhaps most importantly—is understanding how different additives can enhance performance properties such as UV resistance or flame retardancy in specific applications involving injected molded parts made from acrylic materials specifically designed for demanding environments like automotive interiors or outdoor fixtures needing long-lasting durability against harsh elements encountered outdoors regularly.
Designing Effective Mold Systems
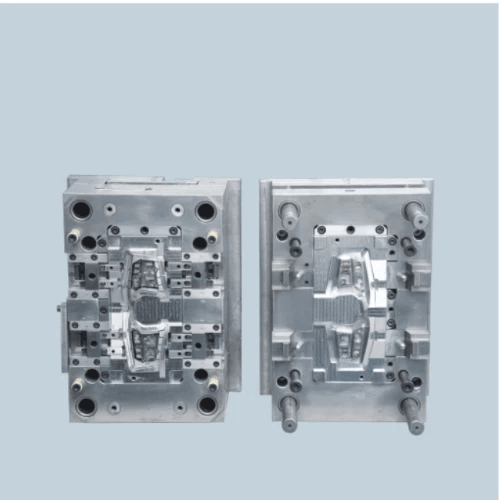
Designing effective mold systems is a cornerstone of successful injection molding acrylic. A well-designed mold not only enhances the quality of the final product but also optimizes production efficiency and reduces costs. In this section, we will explore the principles of mold design, the significance of mold flow analysis, and how advanced software tools are revolutionizing the process.
Principles of Mold Design
Mold design is an art and science that requires a careful balance of various factors to achieve optimal results in plastic injection molding. The primary goal is to create a mold that can consistently produce high-quality parts with minimal defects while ensuring efficient cycle times. Key considerations include the selection of materials for durability, proper cooling channel placement for temperature management, and designing features that facilitate easy part ejection after injection casting.
Another crucial aspect is considering draft angles—slight slopes on vertical surfaces that allow for easier removal from the mold. Without adequate draft angles, parts can become stuck, leading to costly delays and potential damage during ejection. Additionally, incorporating robust venting systems into the mould injection moulding process helps prevent air traps that could compromise part integrity.
Importance of Mold Flow Analysis
Mold flow analysis (MFA) plays an indispensable role in optimizing injection molding processes by simulating how molten material flows through the mold cavity before actual production begins. By using MFA software, designers can visualize potential issues such as air entrapment or uneven cooling patterns that could lead to defects in injection molding acrylic products. This proactive approach allows for adjustments in design or process parameters to enhance overall quality.
Moreover, conducting thorough mold flow analysis can significantly reduce trial-and-error phases during prototyping stages by identifying bottlenecks early on. This not only saves time but also minimizes material waste—a crucial consideration given rising costs in plastic injection molding materials today. Ultimately, effective MFA ensures that molds are designed with precision and foresight, leading to smoother operations once production commences.
Role of Advanced Software in Mold Design
The advent of advanced software tools has transformed how professionals approach designing molds for plastic injection molding applications like acrylics. These sophisticated programs offer features such as 3D modeling capabilities and real-time simulations that enable engineers to visualize complex designs before they are manufactured physically. With these tools at their disposal, teams can experiment with different configurations quickly without incurring significant costs associated with physical prototypes.
Furthermore, many modern software solutions integrate seamlessly with CAD systems used for creating detailed designs of molds tailored specifically for injection castings or other applications involving injection-moldable plastics. This integration streamlines workflows between design and manufacturing teams while fostering collaboration across disciplines—ultimately enhancing product quality through shared insights and expertise.
As we delve deeper into optimizing processes related to injection molding acrylics throughout this guide's subsequent sections—understanding these foundational aspects will empower manufacturers aiming for excellence within their operations.
Optimizing the Injection Molding Process
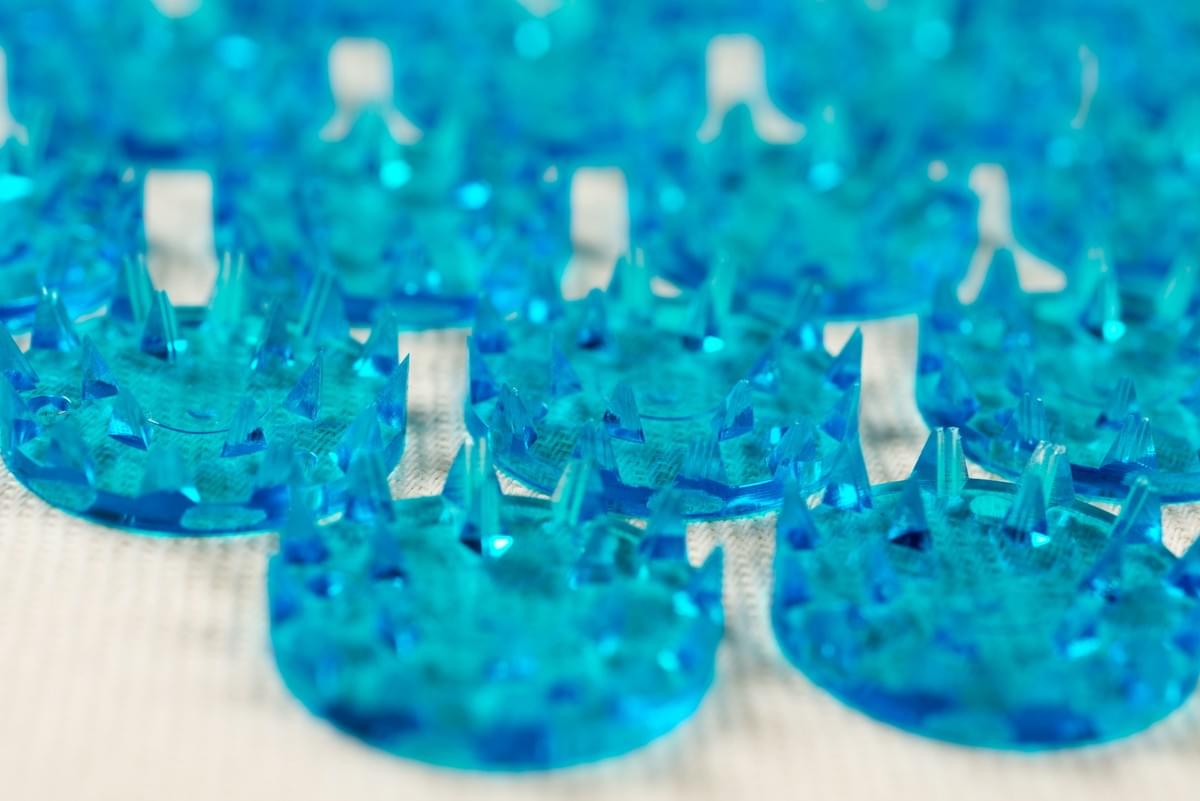
Optimizing the injection molding process is crucial for achieving high-quality results in injection molding acrylic. By fine-tuning various parameters, manufacturers can enhance productivity while minimizing defects. This section delves into key parameters, temperature management techniques, and cycle time optimization strategies that are essential for successful plastic injection molding.
Key Parameters in Injection Molding
When it comes to injection molding, several key parameters play a pivotal role in determining the quality of the final product. These include injection speed, pressure, and hold time—all of which must be meticulously controlled to ensure optimal results. For instance, adjusting the injection speed can significantly impact how well the acrylic flows into the mold cavity during the mould injection moulding process.
Moreover, maintaining appropriate pressure levels is vital for achieving uniform density throughout the molded part. Inadequate pressure may lead to incomplete filling or air entrapment issues, while excessive pressure can cause defects like flash or warping in plastic injection molding applications. Therefore, understanding and controlling these key parameters is essential for producing high-quality injection moldable plastics.
Temperature Management Techniques
Temperature management is another critical factor in optimizing the injection molding process for acrylic materials. The melting temperature of acrylic must be carefully monitored to prevent degradation during processing; otherwise, it could lead to poor mechanical properties and surface finish issues in your final product. Employing advanced temperature control systems ensures that both barrel and mold temperatures remain within optimal ranges throughout production.
Additionally, utilizing techniques such as preheating molds or implementing cooling channels can help maintain consistent temperatures during each cycle of plastic injection molding. This not only enhances material flow but also reduces cycle times by ensuring rapid cooling after filling. Ultimately, effective temperature management directly contributes to improved quality and consistency in your injected parts.
Cycle Time Optimization Strategies
Cycle time plays a significant role in overall production efficiency when working with injection moldable plastics like acrylics. To optimize cycle times effectively, manufacturers should analyze each phase of the process—from filling and cooling to ejection—to identify potential bottlenecks that could slow down production rates. Implementing strategies such as reducing cooling times through optimized mold designs or using faster ejection mechanisms can significantly enhance throughput.
Another strategy involves leveraging simulation software during the design phase to predict and adjust cycle times before actual production begins—this proactive approach allows manufacturers to address potential issues early on without wasting valuable resources on trial-and-error methods later down the line. By focusing on these optimization strategies within your plastic injection molding workflow, you’ll not only improve efficiency but also elevate product quality across batches.
Quality Control in Acrylic Production
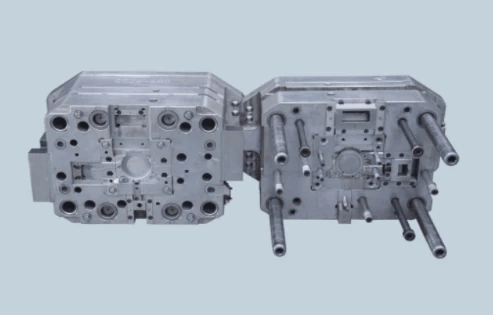
Quality control is paramount in the production of injection molding acrylic products, ensuring that the final output meets both aesthetic and functional standards. Implementing robust quality assurance techniques can significantly reduce defects and enhance customer satisfaction. From material selection to the final inspection, every step must be scrutinized to maintain high-quality standards in plastic injection molding processes.
Techniques for Quality Assurance
To ensure top-notch quality in injection molding acrylic, several techniques can be employed throughout the production process. Regular inspections during various stages of mould injection moulding can help catch issues early, preventing costly reworks later on. Additionally, utilizing statistical process control (SPC) allows manufacturers to monitor production parameters and identify trends that may lead to defects before they occur.
Another effective technique is implementing a comprehensive testing regime for finished products. This includes mechanical testing, visual inspections, and dimensional checks to ensure that each piece conforms to specifications. By adopting these quality assurance measures, companies can confidently produce reliable injection moldable plastics that stand up to consumer expectations.
Common Defects in Injection Molding Acrylic
Despite best efforts at quality control, common defects can still arise during the plastic injection molding process. One of the most prevalent issues is warping or distortion of parts due to improper cooling rates or uneven material distribution during mold filling. Other frequent defects include air traps—bubbles formed when air gets trapped in the mould—and surface blemishes caused by inadequate surface finish on the mold itself.
Understanding these potential pitfalls is crucial for anyone involved in injection casting or mould design. Addressing these issues early through rigorous testing and adjustments ensures a smoother manufacturing process and higher-quality end products. Manufacturers must also stay vigilant about contamination from foreign materials which could compromise the integrity of their acrylic components.
Strategies for Maintaining Consistency
Maintaining consistency in production is vital for achieving high-quality results with injection molding acrylic components across batches. One effective strategy involves establishing standardized operating procedures (SOPs) for every stage of production—from material handling to machine settings—to minimize variability between runs. Regular training sessions for operators also help reinforce these practices and promote adherence to quality standards.
Another important aspect is regular maintenance of equipment used in plastic injection molding processes; worn-out machinery can lead to inconsistencies that affect product quality negatively. Implementing predictive maintenance schedules helps identify potential equipment failures before they disrupt production cycles or compromise product integrity. Lastly, fostering a culture of continuous improvement encourages teams to seek out innovative solutions for enhancing consistency across all facets of acrylic production.
Innovations in Injection Molding
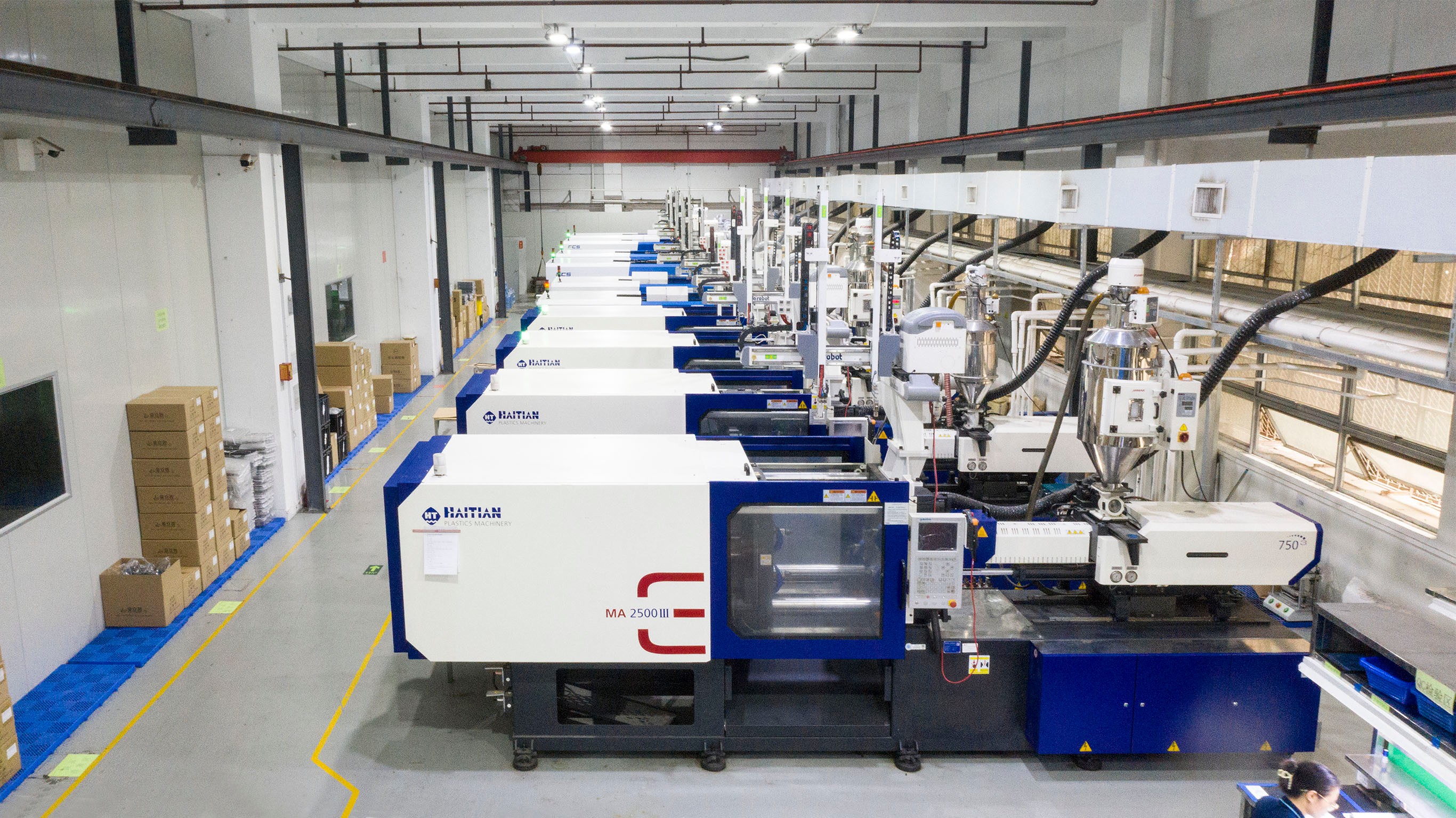
In the ever-evolving world of manufacturing, innovations in injection molding are reshaping the landscape, particularly for injection molding acrylic. These advancements not only enhance efficiency but also improve product quality and reduce waste. The integration of cutting-edge technologies is paving the way for a more sustainable and effective production process.
Latest Technologies Transforming the Industry
The injection molding industry is witnessing a surge in advanced technologies that are transforming traditional practices. For instance, 3D printing is increasingly being used to create prototypes and molds for injection casting, allowing manufacturers to test designs before committing to full-scale production. Additionally, smart sensors and IoT devices are now being integrated into mold plastic injection systems to monitor conditions in real-time, ensuring optimal performance throughout the production cycle.
Another notable innovation is the development of specialized injection moldable plastics that offer enhanced properties such as improved strength and flexibility. These materials can be tailored for specific applications, making them ideal for producing high-quality acrylic components through plastic injection molding processes. As these technologies continue to evolve, they promise to streamline operations while maintaining high standards in quality control.
Role of Automation in Injection Molding
Automation plays a pivotal role in revolutionizing injection molding processes by increasing precision and reducing human error. Automated systems can efficiently manage tasks such as material handling, mold changes, and quality inspections with minimal downtime. This not only speeds up production but also ensures consistency across batches of products made from injection molding acrylic.
Moreover, robotic arms are becoming common fixtures on factory floors, taking over repetitive tasks that were once performed manually. This shift allows skilled workers to focus on more complex tasks requiring critical thinking and creativity rather than mundane operations related to mould injection moulding processes. As automation technology advances further, we can expect even greater improvements in productivity and efficiency within the industry.
Future Trends in Acrylic Injection Molding
Looking ahead, several trends are set to shape the future of acrylic injection molding significantly. One prominent trend is the increasing demand for sustainable practices within manufacturing sectors; this includes using recycled materials or bio-based plastics that reduce environmental impact while maintaining performance standards similar to traditional plastics used in plastic injection molding mold processes.
Additionally, advancements in artificial intelligence (AI) will likely play a crucial role in optimizing production schedules based on real-time data analysis from various stages of manufacturing — from design through final inspection — ensuring quicker turnaround times without sacrificing quality assurance measures typically associated with injection casting techniques.
As we move forward into an era defined by rapid technological advancement and environmental responsibility, those involved with acrylic products will need to adapt swiftly or risk being left behind as competitors embrace these innovations wholeheartedly.
Conclusion
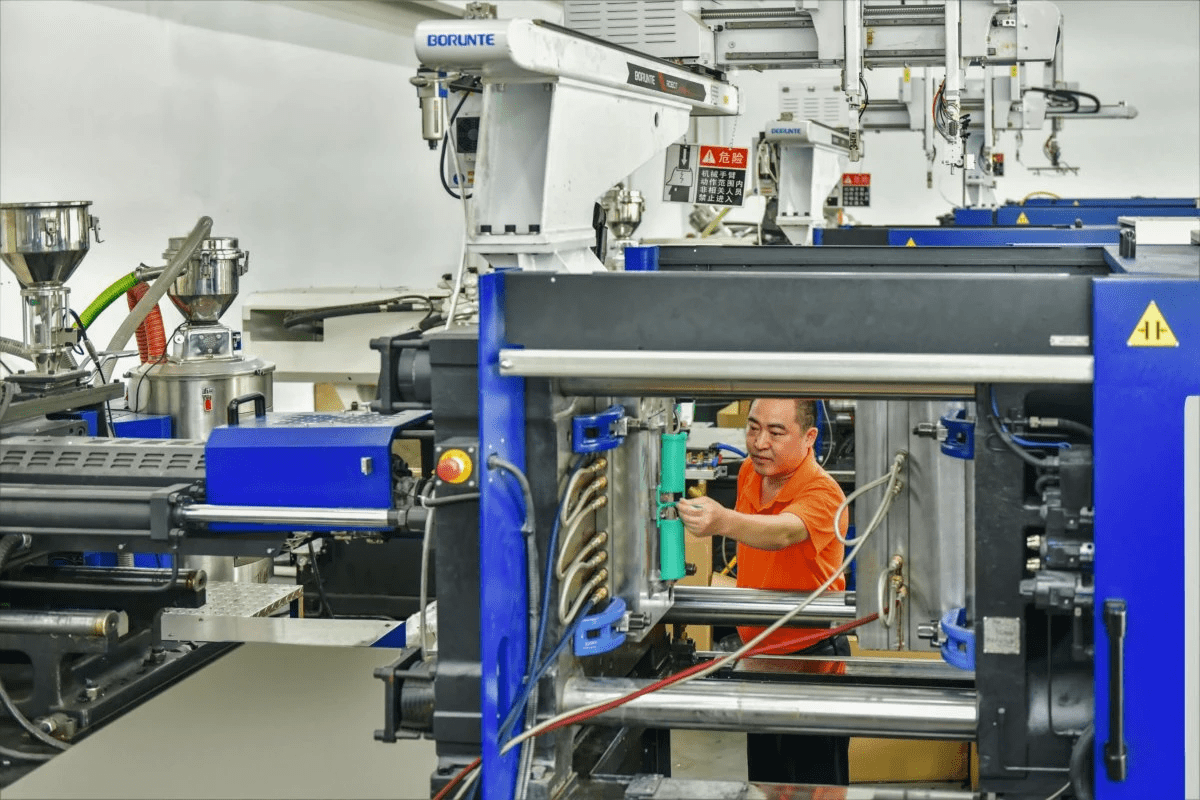
In wrapping up our exploration of injection molding acrylic, it’s clear that quality and precision are paramount in this intricate process. The techniques and practices discussed not only enhance the production of acrylic products but also ensure that they meet industry standards and customer expectations. By understanding the nuances of injection molding, manufacturers can significantly improve their output and efficiency.
Best Practices for Successful Injection Molding
When it comes to successful injection molding, preparation is key. Begin with selecting the right materials, ensuring that your acrylic is suitable for the specific demands of your project; this sets a solid foundation for any injection casting or mould injection moulding process. Additionally, investing time in thorough mold design and flow analysis will prevent common pitfalls, leading to a smoother plastic injection molding experience.
Moreover, maintaining optimal parameters throughout the production cycle is crucial. This includes temperature management to ensure consistency and quality while minimizing defects in your finished products. Regularly reviewing these practices can help you refine your approach to mold plastic injection processes, resulting in superior outcomes every time.
How the Baoyuan Team Ensures Quality
At Baoyuan, quality assurance is woven into every step of our production process for injection molding acrylic products. Our team employs rigorous testing methods to catch any potential defects before they reach the customer—because nobody likes surprises when it comes to product integrity! By utilizing advanced technologies alongside traditional craftsmanship, we ensure that our plastic injection molding molds meet high standards.
Furthermore, continuous training and development keep our team updated on best practices and innovations within the industry. This commitment not only enhances individual skills but fosters a culture focused on excellence across all facets of production—from material selection to final inspection. With such dedication at Baoyuan, we consistently deliver top-tier results in moulding processes.
Final Thoughts on Acrylic Injection Molding Techniques
In conclusion, mastering acrylic injection molding techniques requires a blend of art and science—understanding materials deeply while employing cutting-edge technology effectively. The insights shared here emphasize that success hinges on meticulous planning and execution throughout various stages: from designing effective mold systems to optimizing cycle times during production runs with plastic injection molding molds.
As we look ahead at future trends influencing this dynamic field—like automation and innovative materials—the potential for growth remains vast for those willing to adapt and evolve their strategies in response to market demands. Embracing these advancements ensures that manufacturers stay competitive while producing high-quality products through efficient processes like injection casting.