Introduction
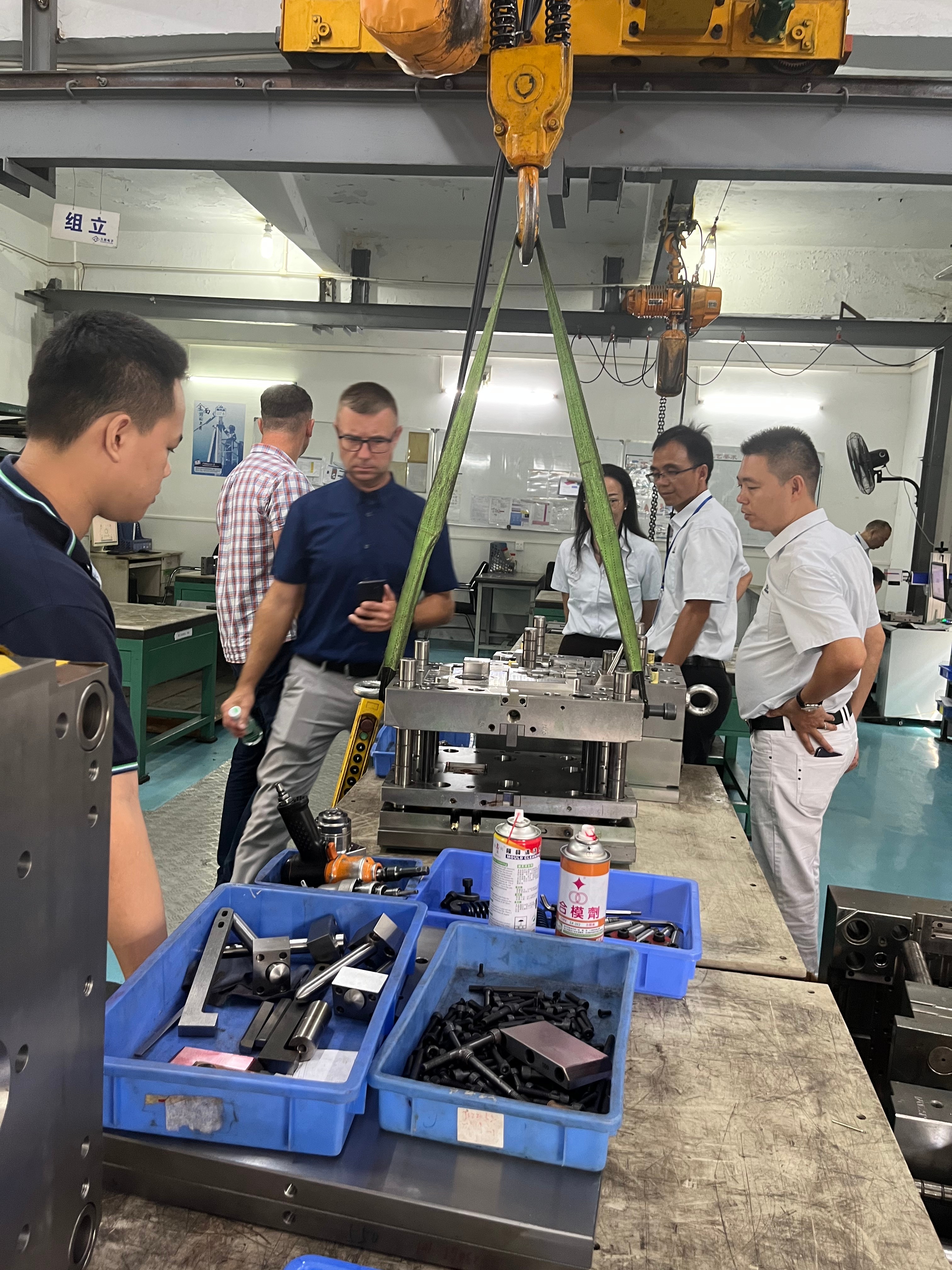
Injection molding is a fascinating process that transforms raw materials into intricate designs, but it can also be fraught with challenges. One of the most common issues faced in this realm is flash in injection molding, which can tarnish the quality of the finished product and lead to increased production costs. Understanding what causes flash in injection molding and how to troubleshoot it effectively is essential for any manufacturer aiming for excellence.
Understanding Flash in Injection Molding
Flash refers to the unwanted excess material that seeps out between the mold halves during the injection process. This defect not only affects aesthetics but can also compromise functionality, making it a critical issue to address. To tackle flash effectively, one must first grasp its origins and implications within the broader context of injection molding defects.
Significance of Proper Mold Design
A well-designed mold serves as the backbone of successful injection molding operations; it dictates not only product quality but also efficiency and cost-effectiveness. Without proper mold design, manufacturers may find themselves grappling with various issues including flash, weld lines in injection molding, and even sink marks in injection molding. Thus, investing time and resources into mold design is paramount for achieving optimal results.
Common Injection Molding Defects
Beyond flash, several other defects can plague an injection-molded part—each with its own set of challenges and solutions. Weld lines occur when two flow fronts meet but do not fuse properly, while sink marks manifest as depressions on surfaces due to uneven cooling or inadequate material fill. Identifying these common injection molding defects early allows for timely intervention and ensures a smoother production process.
What Causes Flash in Injection Molding

Flash in injection molding can be a frustrating issue for manufacturers, often leading to increased production costs and wasted materials. Understanding the underlying causes is crucial for effective injection molding flash troubleshooting. By identifying the factors that contribute to mold flash, manufacturers can implement strategies to mitigate this defect.
Material Selection and Its Impact
The choice of material plays a significant role in determining whether flash occurs during the injection molding process. Certain plastics may have a higher tendency to expand or deform under heat and pressure, leading to unwanted overflow at the mold seams. Additionally, using materials that are incompatible with the mold design can exacerbate issues like weld lines in injection molding or sink marks in injection molding, further complicating production quality.
When selecting materials, it’s essential to consider their viscosity and flow characteristics as well. Materials that flow too easily may fill the mold cavity quickly but can also lead to excessive pressure buildup, resulting in flash if not managed properly. Therefore, careful material selection is one of the first steps in how to avoid flash in injection molding.
Injection Pressure and Temperature
Injection pressure and temperature are pivotal factors that influence flash occurrences during molding operations. High injection pressures can force molten plastic into areas of the mold where it shouldn’t go, resulting in unsightly flash around parting lines or other mold features. Similarly, elevated temperatures can increase material flow but also risk causing thermal expansion beyond what the mold can contain.
Finding a balance between pressure and temperature is key for maintaining control over material behavior during processing. If these parameters are not optimized, you may find yourself facing an array of injection molding defects including not just flash but also weld lines and sink marks that compromise product integrity. Thus, monitoring these variables closely is essential for effective troubleshooting when dealing with flash issues.
Poorly Designed Molds
One of the most significant contributors to flash in injection molding is poorly designed molds themselves. Inadequate venting or misalignment between mold halves can create conditions ripe for excess plastic leakage as it fills cavities under high pressure. Furthermore, molds lacking proper draft angles may trap material at critical points leading to uneven filling and subsequent flashing.
Designing molds with precision involves considering various aspects such as cooling channels, gate locations, and overall geometry—all factors that play into how well a part will form without defects like flash or weld lines in injection molding occurring later on during production runs. Regular reviews of mold design practices can help pinpoint flaws before they manifest as costly errors on the shop floor; hence investing time upfront pays off handsomely later on by reducing instances of defects such as sink marks in injection molding too.
Injection Molding Flash Troubleshooting
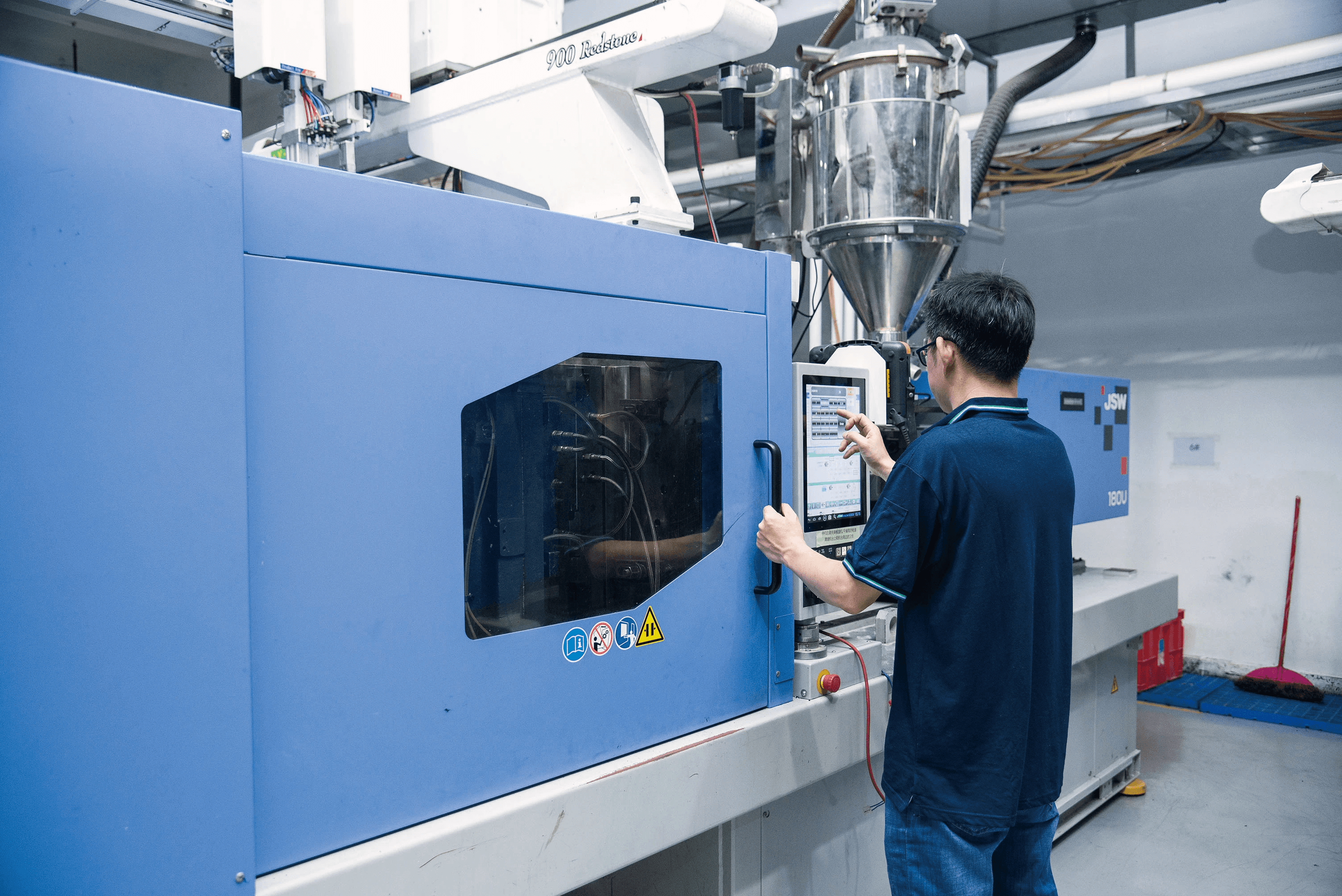
Diagnosing the Problem
The first step in addressing flash in injection molding is accurately diagnosing the problem. Operators should closely examine mold components for wear and tear, as poorly designed molds can significantly contribute to this defect. Additionally, assessing material selection is vital; certain plastics are more prone to flash due to their flow characteristics and thermal properties.
Once you've identified potential issues with mold design or materials, consider factors like injection pressure and temperature settings. High pressure can exacerbate flash by forcing more material into areas where it shouldn't go, while inadequate temperature may lead to incomplete filling and irregularities. By systematically analyzing these variables, you can pinpoint what causes flash in injection molding specific to your operation.
Recommended Adjustments and Changes
After diagnosing the issue, it's time for some recommended adjustments and changes that can help mitigate flash problems effectively. Start by recalibrating your machine settings; reducing injection pressure or adjusting cooling times could make a significant difference in preventing excessive material flow into unwanted areas.
Another critical aspect involves refining mold design techniques—ensuring proper venting can alleviate trapped gases that contribute to flashing. Regularly inspecting molds for wear or damage will also go a long way toward maintaining quality standards and avoiding common injection molding defects such as sink marks in injection molding or weld lines in injection molding.
Role of the Baoyuan Team in Solutions
The Baoyuan team plays a pivotal role in providing solutions for those grappling with flash issues during their manufacturing processes. With extensive experience in tackling various types of defects—including mold flash in semiconductor applications—the team brings valuable insights into effective troubleshooting strategies tailored specifically for your needs.
Their expertise allows them to assist clients not only with immediate fixes but also with long-term preventive measures on how to avoid flash in injection molding altogether. By collaborating with Baoyuan’s specialists, manufacturers can enhance their processes through training programs that focus on operator education regarding best practices for maintaining quality control throughout production cycles.
How to Avoid Flash in Injection Molding
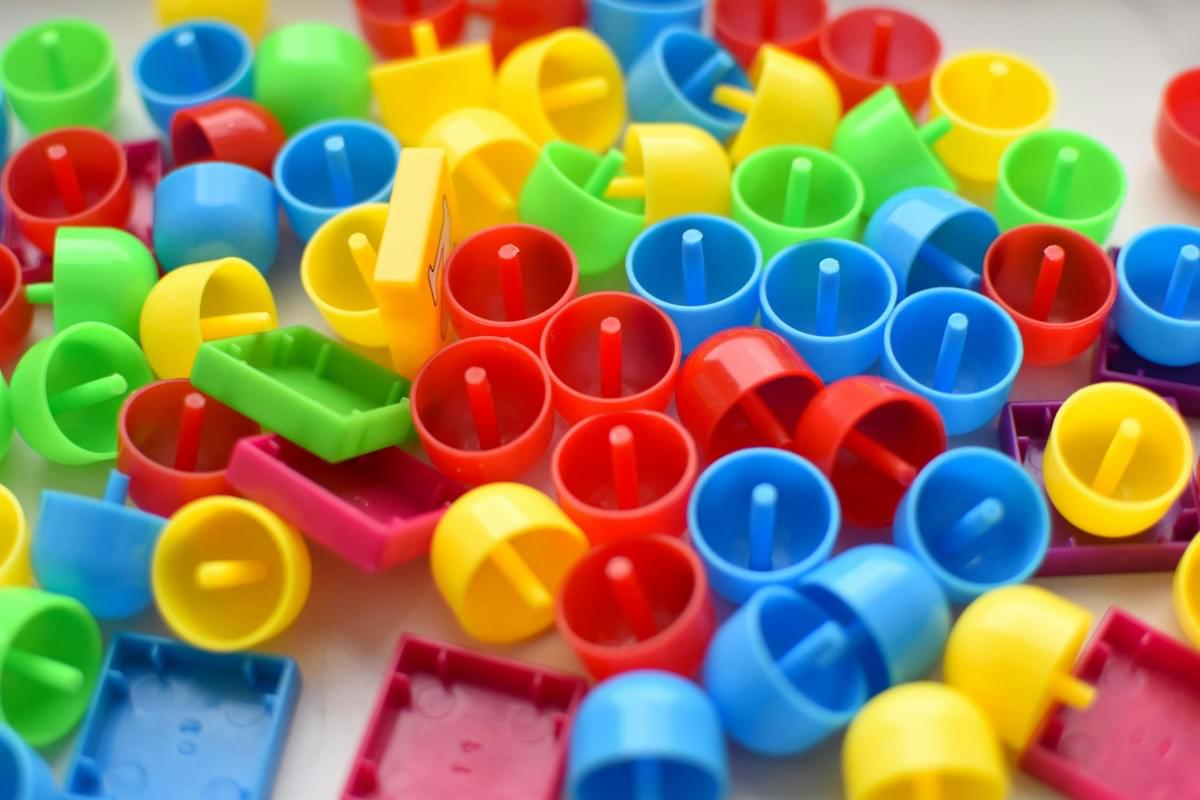
Avoiding flash in injection molding is crucial for maintaining product quality and reducing waste. By implementing effective strategies during the design and production phases, manufacturers can significantly decrease the likelihood of defects. This section explores essential techniques, temperature control, and maintenance practices that help prevent flash.
Effective Mold Design Techniques
When it comes to avoiding flash in injection molding, mold design is your first line of defense. A well-designed mold minimizes gaps where excess material can escape, thus preventing unwanted flash. Key considerations include ensuring proper venting, selecting appropriate draft angles, and maintaining uniform wall thickness to avoid weak points that could lead to defects like weld lines in injection molding.
Moreover, utilizing advanced simulation software during the design phase allows engineers to predict potential issues before they arise. Such proactive measures not only enhance mold performance but also streamline production processes by reducing downtime caused by injection molding flash troubleshooting. Remember that a solid foundation in mold design translates directly into fewer defects and higher-quality products.
Maintaining Consistent Temperature and Pressure
Another critical factor in how to avoid flash in injection molding is maintaining consistent temperature and pressure throughout the process. Fluctuations can lead to variations in material flow, causing excess material to squeeze out of the mold cavity—hello, flash! Implementing precise temperature controls for both the mold and the melt ensures that materials behave as expected during injection.
Additionally, monitoring pressure levels is essential; too much pressure can exacerbate issues related to flash while also contributing to other injection molding defects like sink marks in injection molding or excessive wear on molds themselves. Regularly calibrating equipment helps maintain these parameters within optimal ranges, making it easier for operators to produce high-quality parts consistently.
Importance of Regular Maintenance
Regular maintenance is often an overlooked aspect of preventing flash in injection molding but is vital nonetheless. Just as you wouldn’t drive a car without regular oil changes or tire rotations, molds require routine checks and servicing to ensure they’re functioning optimally. Diligent maintenance helps identify wear-and-tear issues early on before they escalate into larger problems that may result in costly downtime or defective products.
Incorporating a structured maintenance schedule not only prolongs the life of your molds but also enhances overall production efficiency by minimizing unexpected breakdowns associated with poorly maintained equipment. This proactive approach ultimately reduces instances of flashing while simultaneously improving quality control across all stages of production—resulting in fewer weld lines and sink marks as well!
Related Issues: Weld Lines and Sink Marks
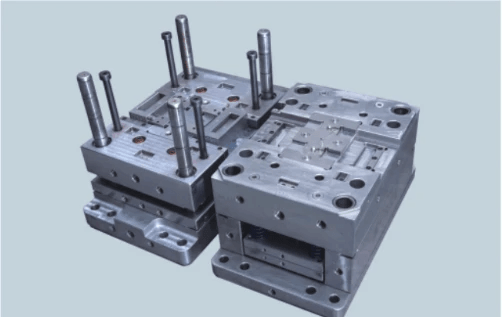
In the world of injection molding, flash is not the only defect that manufacturers need to be wary of. Two other common issues are weld lines and sink marks, both of which can significantly affect the quality of molded parts. Understanding these defects is crucial for achieving optimal results in injection molding processes.
Understanding Weld Lines in Injection Molding
Weld lines occur when two or more flow fronts meet during the injection molding process but do not fuse properly, creating a visible line on the surface of the molded part. These lines can compromise both aesthetics and structural integrity, making them a significant concern in high-quality applications. Factors contributing to weld lines include low injection speed, improper temperature settings, and inadequate material flow—issues that often overlap with what causes flash in injection molding.
Impact of Sink Marks on Quality
Sink marks are depressions that form on the surface of a molded part due to uneven cooling or inadequate packing pressure during injection molding. These defects can detract from both visual appeal and functional performance, making them particularly troublesome for products requiring high precision or aesthetic quality. Notably, sink marks often arise alongside other issues like weld lines and flash in injection molding; thus, addressing one may lead to improvements across multiple defect types.
Strategies to Mitigate These Defects
To effectively combat weld lines and sink marks in injection molding, manufacturers should adopt several best practices aimed at enhancing mold design and processing parameters. First off, optimizing gate design can improve material flow dynamics—helping to minimize weld line occurrences while also addressing potential sources of flash in injection molding. Additionally, maintaining consistent packing pressure and temperature during production is essential; this helps ensure uniform cooling rates that can mitigate both sink marks and other related defects like mold flash in semiconductor applications.
For those looking to further refine their approach to avoiding these defects, regular maintenance checks on equipment are crucial as well as continuous operator training focused on identifying signs of issues early on—because prevention is always better than cure!
Practical Tips for Successful Injection Molding
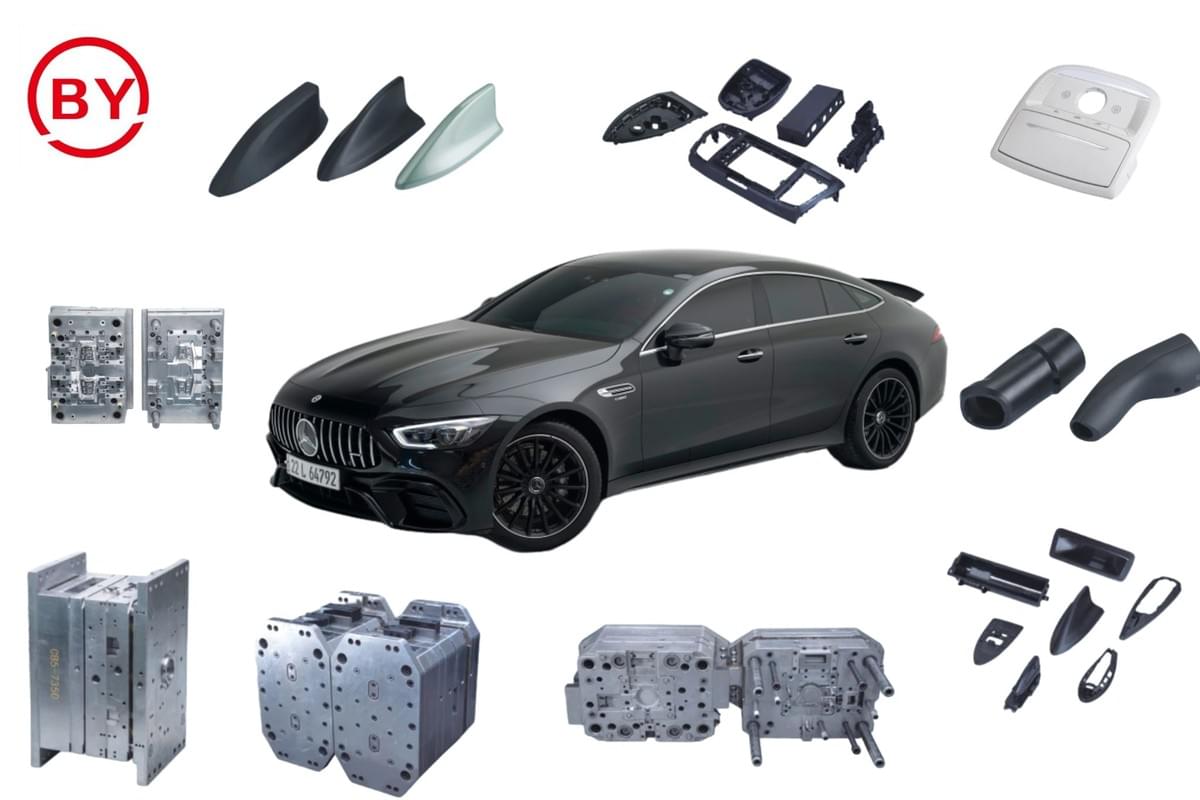
Navigating the world of injection molding can feel like a maze, especially when you're trying to avoid defects like flash in injection molding. To ensure success, it’s crucial to focus on training operators, maintaining strict quality control, and leveraging technology for continuous improvement. By implementing these strategies, you can minimize the risks associated with what causes flash in injection molding and enhance overall production quality.
Training and Education for Operators
The foundation of any successful injection molding operation lies in well-trained operators who understand the intricacies of their machines and processes. Comprehensive training programs should cover not only the basics of injection molding but also delve into specific issues such as injection molding flash troubleshooting techniques. When operators are equipped with knowledge about how to avoid flash in injection molding, they become more adept at identifying potential problems before they escalate into costly defects.
Moreover, regular workshops and refresher courses can keep your team updated on the latest technologies and methodologies in the field. This ongoing education fosters a culture of continuous improvement where operators actively seek ways to enhance efficiency and reduce defects like weld lines in injection molding or sink marks in injection molding. Ultimately, investing time in training pays off by reducing downtime and improving product quality.
Importance of Quality Control
Quality control is the backbone of any manufacturing process, especially when it comes to preventing defects such as mold flash in semiconductor applications or other products. Implementing stringent quality control measures helps catch issues early on—before they turn into major problems that compromise your production run. Regular inspections can identify signs of what causes flash in injection molding or other defects like weld lines and sink marks that could affect product integrity.
Utilizing statistical process control (SPC) tools allows manufacturers to monitor their processes continuously and make data-driven decisions that enhance quality outcomes. With effective quality control protocols, you’ll not only maintain high standards but also foster customer trust by delivering consistent products free from common injection molding defects. This proactive approach ensures that your operations remain competitive while minimizing waste.
Utilizing Technology for Continuous Improvement
In today’s fast-paced manufacturing landscape, technology plays an essential role in improving efficiency and reducing errors associated with flash in injection molding. Advanced monitoring systems can provide real-time data on pressure variations, temperature fluctuations, and cycle times—key factors that contribute to what causes flash in injection molding scenarios. By leveraging this data effectively, teams can quickly address potential issues before they lead to significant production delays.
Moreover, adopting simulation software allows engineers to visualize mold designs under various conditions without wasting materials on trial-and-error approaches. This proactive method helps identify design flaws early on while offering insights into how to avoid flash in injection molding altogether through refined mold configurations or adjustments during production runs. Embracing technological advancements not only streamlines processes but also enhances overall product quality by minimizing risks associated with common defects such as weld lines or sink marks.
Conclusion
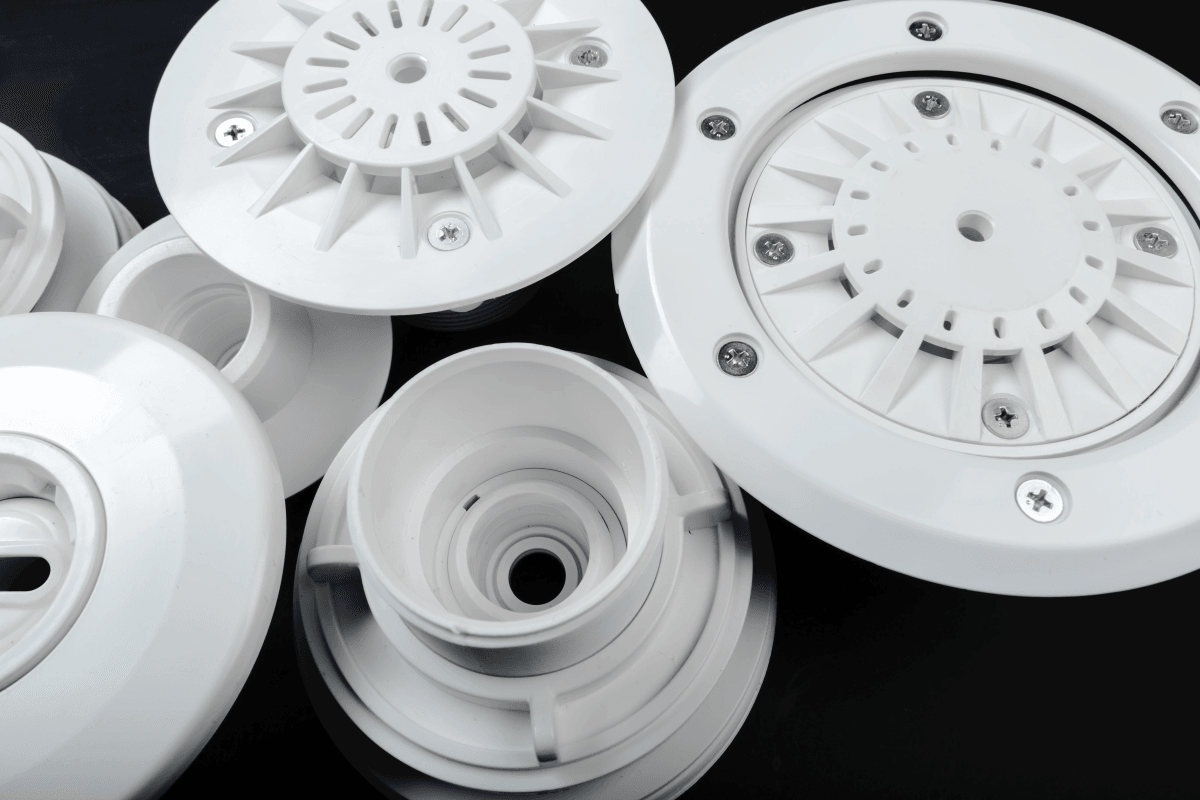
In the realm of injection molding, understanding and addressing flash is crucial for maintaining product quality and efficiency. By recognizing the causes of flash in injection molding, manufacturers can implement effective strategies to mitigate this common defect. Ultimately, a well-designed mold paired with diligent troubleshooting can significantly enhance production outcomes.
Key Takeaways for Mold Design
A robust mold design is the first line of defense against flash in injection molding. Key elements such as proper venting, optimal gate placement, and accurate tolerances play vital roles in preventing excess material from escaping the mold cavity. Additionally, considering how factors like weld lines in injection molding and sink marks can affect overall quality will lead to more durable products.
Recap of Troubleshooting Techniques
When it comes to injection molding flash troubleshooting, a systematic approach is essential. Start by diagnosing what causes flash in injection molding—be it material selection or machine settings—and then make informed adjustments accordingly. Regularly revisiting these techniques ensures that not only flash but also other defects like weld lines and sink marks are kept at bay.
Next Steps for Quality Injection Molding
To ensure continuous improvement in quality injection molding processes, it’s important to establish a culture of training and education among operators. Emphasizing the importance of quality control measures will help catch defects early on before they escalate into bigger issues like mold flash in semiconductor applications or excessive sink marks in injection molding parts. Incorporating advanced technology can further streamline processes and enhance overall production efficiency.