Introduction
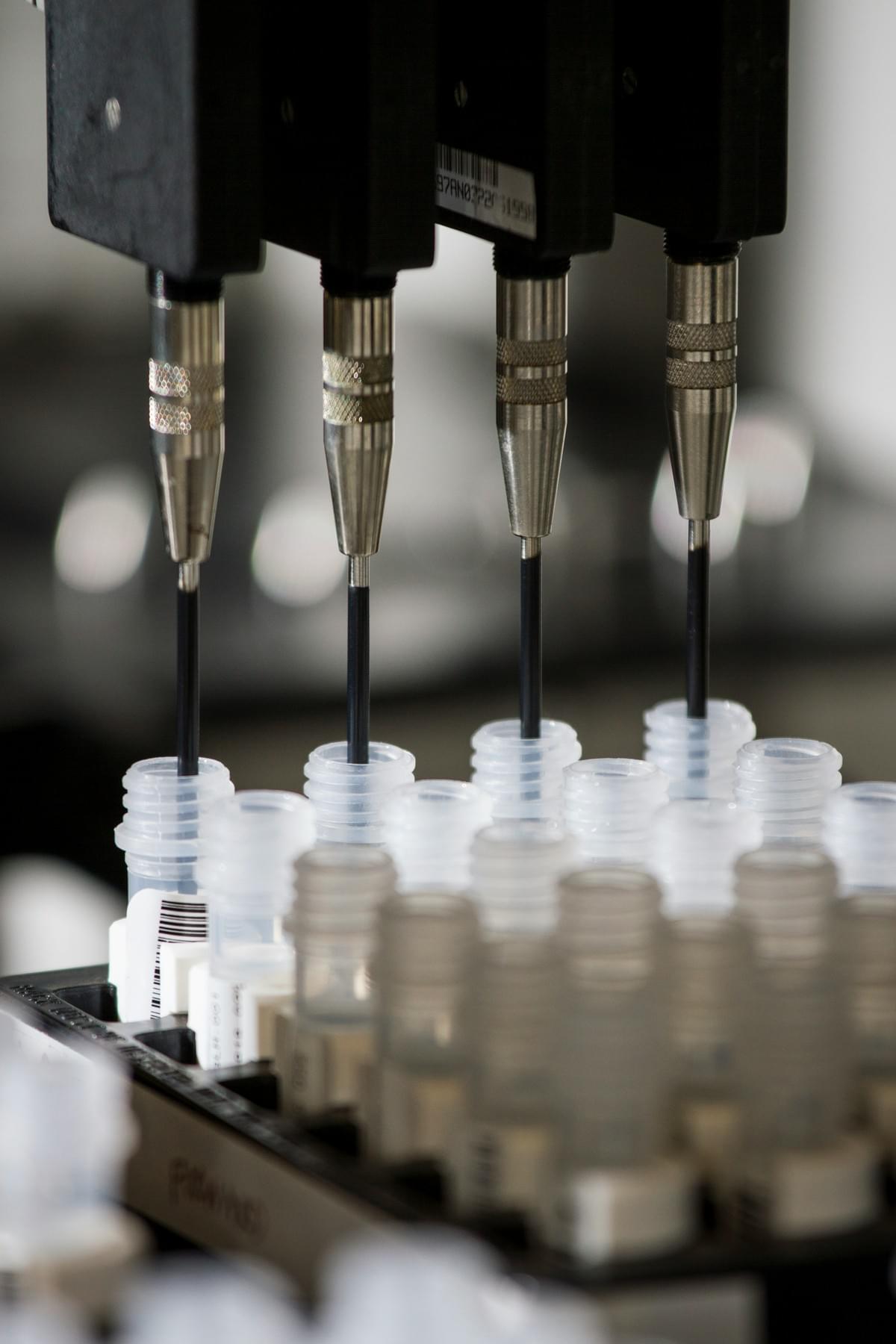
Injection mold flashing is a common yet frustrating issue in the world of manufacturing, particularly in injection molding processes. This phenomenon occurs when excess material seeps out from the mold cavity during the injection process, leading to unsightly and often problematic defects on the final product. Understanding injection mold flashing is crucial for manufacturers aiming to produce high-quality components that meet stringent specifications.
Understanding Injection Mold Flashing
So, what is flashing in injection molding? Simply put, it refers to the thin layer of excess material that forms along the parting line of a molded component. This unwanted byproduct not only detracts from the aesthetic appeal of the product but can also compromise its structural integrity and functionality. Recognizing this issue early on can save time and resources in production.
The Impact of Flash on Mold Quality
The impact of flash on mold quality cannot be overstated; it can significantly alter both the appearance and performance of a molded part. Excess flash may lead to increased post-processing costs as manufacturers must trim or sand down these imperfections before products can be sold or used. Additionally, persistent flash issues may indicate deeper problems within the molding process that could affect overall production efficiency.
Key Factors Contributing to Flash
Several key factors contribute to flash in injection molding, making it essential for manufacturers to address them proactively. These include design flaws such as inadequate draft angles or improper tolerances, material selection issues that affect flow properties, and incorrect process parameters like temperature and pressure settings. By understanding what causes flashes in molds, companies can implement effective strategies for prevention and mitigation.
What is Flashing in Injection Molding?
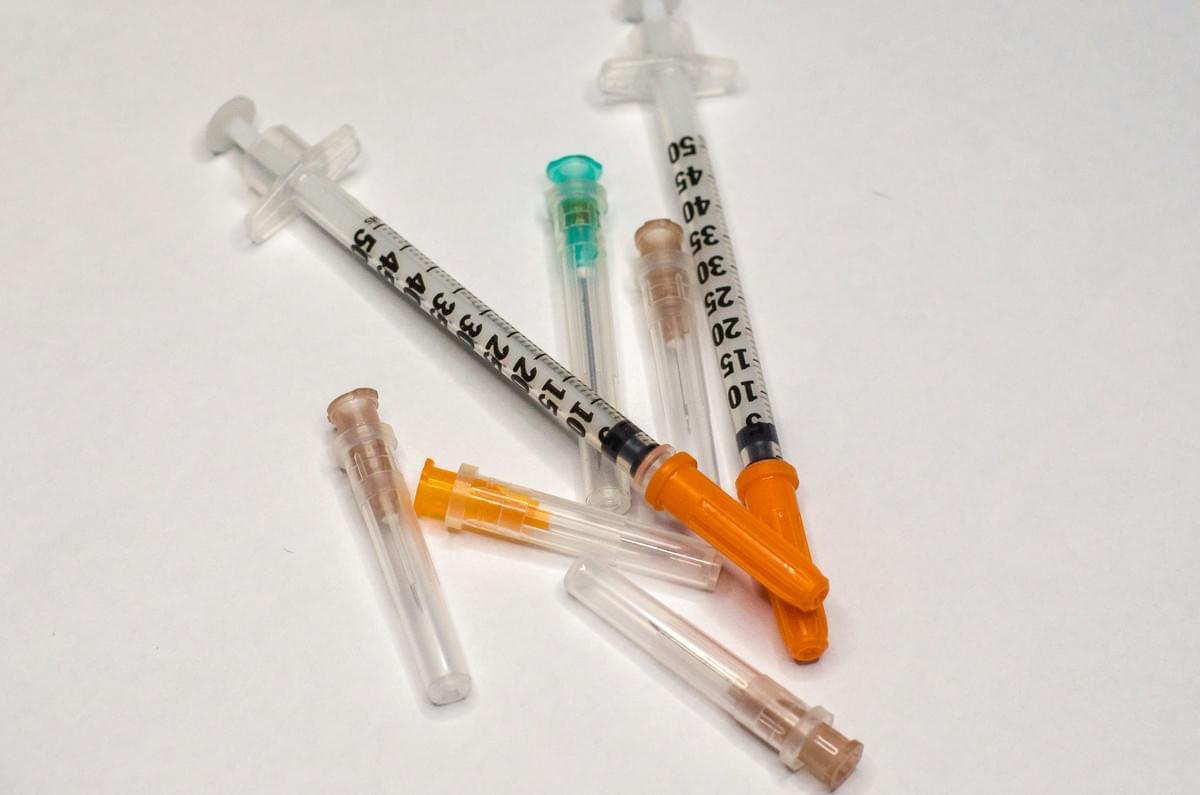
Definition of Flashing
Flashing occurs when molten plastic escapes from the mold cavity and solidifies outside of its intended shape. This defect can manifest as thin layers or ridges along the parting line or even at other unexpected locations on the molded piece. Understanding this definition is crucial for anyone involved in injection mold flashing, as it sets the stage for identifying and addressing related issues.
Common Scenarios of Flash Issues
There are several common scenarios where flash issues may arise in injection molding. For instance, if a mold is improperly aligned or if there’s excessive clamp pressure, flash can occur quite easily. Additionally, worn-out molds or those with inadequate venting can exacerbate these problems, leading to frequent occurrences of what is known as the flash issue in molds.
Importance of Addressing Flash
Addressing flash in injection molding isn’t just about maintaining aesthetics; it's vital for ensuring product quality and performance. If left unaddressed, flashing can lead to increased production costs due to rework and scrap rates while also impacting customer satisfaction with subpar products. Therefore, understanding how to reduce flash in injection moulding becomes essential for manufacturers striving for excellence.
What is the Flash Issue in Mold?
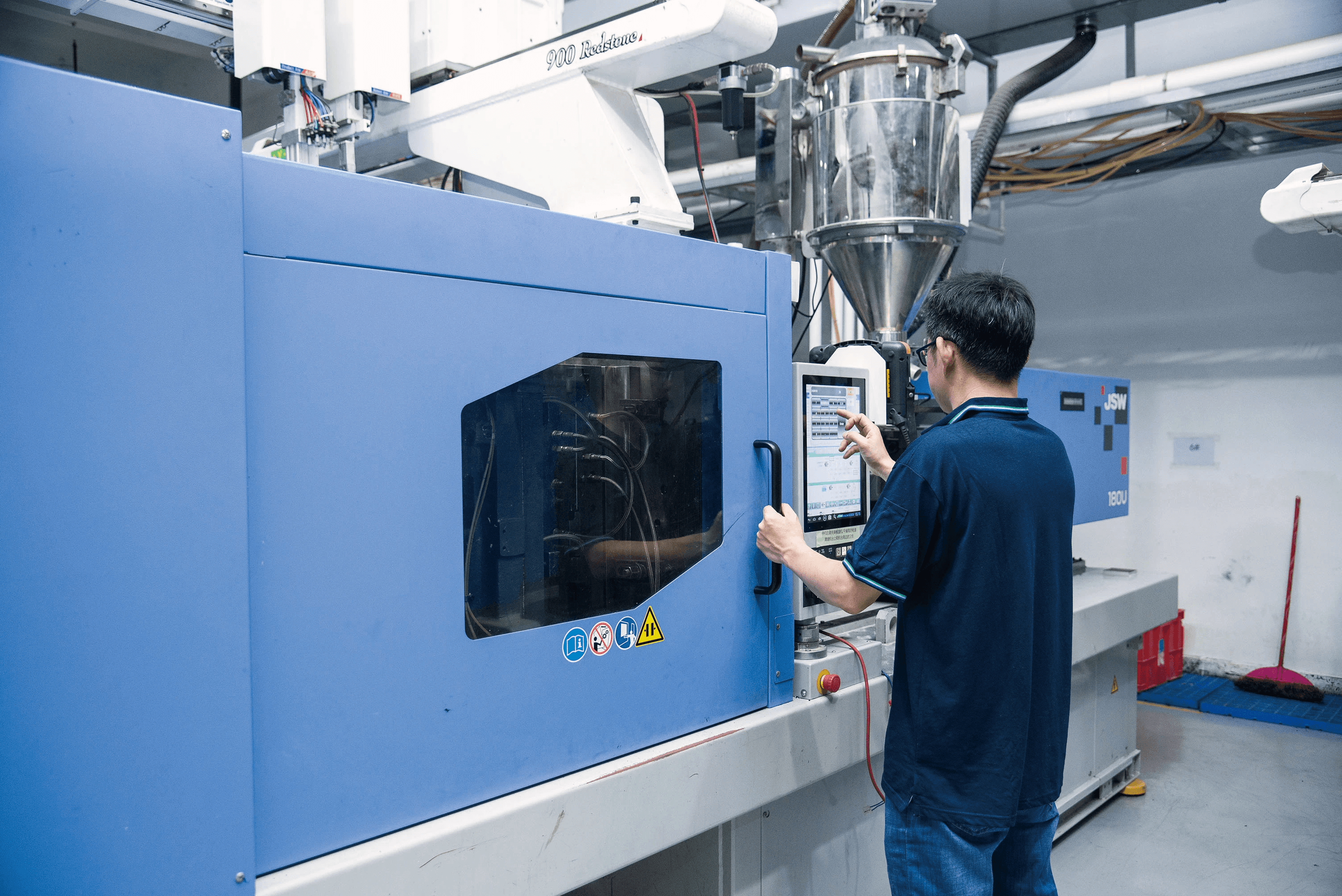
Injection mold flashing is a common challenge in the world of manufacturing, where excess material seeps out from the mold's parting line during the injection process. This issue can compromise the quality and aesthetics of molded parts, leading to increased production costs and time delays. Understanding what constitutes this flash issue in molds is crucial for manufacturers aiming to produce high-quality components.
Identifying Flash Problems
Identifying flash problems involves close inspection of molded parts for any unwanted protrusions or excess material along seams or edges. These flashes are often indicative of underlying issues such as improper mold alignment or excessive injection pressure during the molding process. Spotting these problems early on can save manufacturers from costly rework and ensure that their products meet quality standards.
Real-World Examples of Flashing
Real-world examples of injection mold flashing can be found across various industries, from automotive to consumer goods. For instance, a manufacturer producing plastic casings for electronics may encounter flash due to variations in temperature control within the mold. Another example includes a toy manufacturer facing aesthetic issues when excess plastic forms around intricate details, highlighting how critical it is to address what is flashing in injection molding promptly.
Techniques for Recognition
Techniques for recognizing flash issues include visual inspections and using specialized tools like calipers and gauges to measure part dimensions accurately. Additionally, employing advanced imaging systems can help pinpoint areas where flash may occur before production runs begin. By developing a keen eye for detail and utilizing these techniques, manufacturers can effectively manage what is the flash issue in molds, leading to improved product quality and reduced waste.
What is the Root Cause of Flashing?
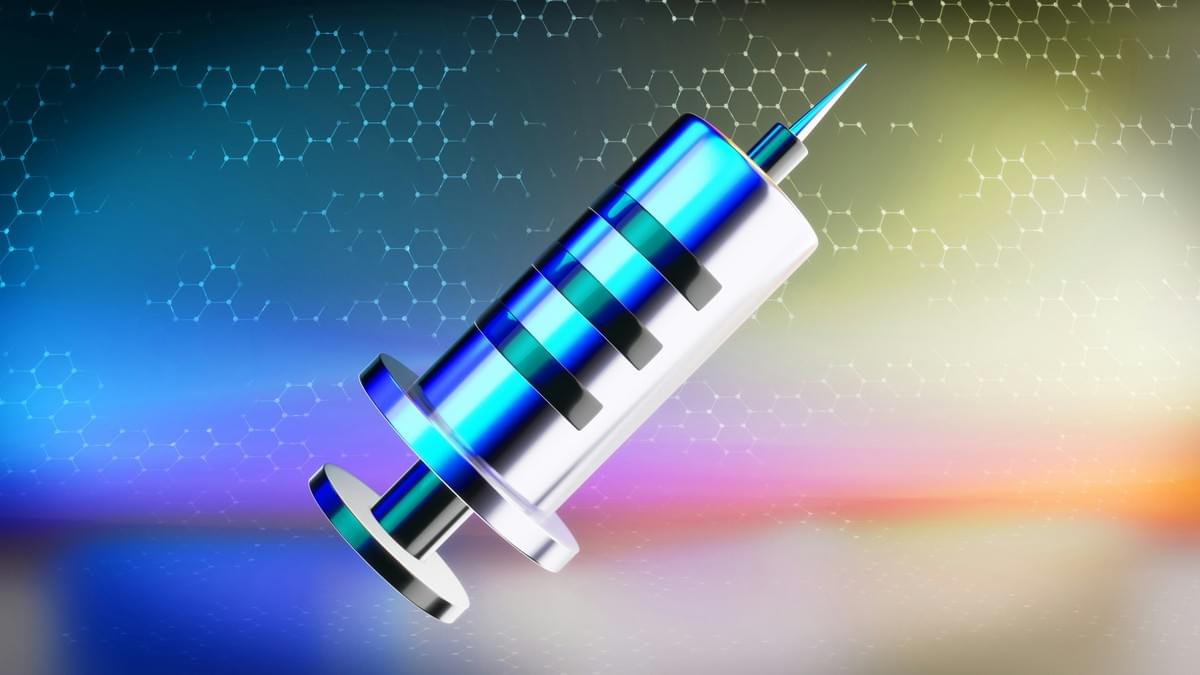
When it comes to injection mold flashing, understanding its root causes is crucial for effective troubleshooting and prevention. Flashing can severely impact product quality, leading to increased production costs and waste. Identifying the underlying issues helps manufacturers develop targeted strategies to mitigate flash problems.
Analyzing Design Factors
The design of the mold plays a pivotal role in determining whether flashing will occur during the injection molding process. Poorly designed molds with inadequate venting or improper alignment can lead to excess material escaping from the mold cavity, resulting in what is known as flash. Furthermore, intricate designs with tight tolerances may exacerbate these issues, making it essential to analyze design factors meticulously before production begins.
In addition to mold geometry, considerations such as draft angles and wall thickness significantly influence how materials flow and solidify within the mold. If these factors are not optimized, they can contribute directly to what is flashing in injection molding. Therefore, engaging in thorough design reviews can help identify potential pitfalls that lead to flash issues.
Material Selection and Its Role
Material selection is another critical factor when examining what causes bubbles in injection molding and how it relates to flashing. Different materials have varying flow characteristics; some may be more prone to expanding or trapping air during processing than others. Selecting a material that aligns with your specific application requirements can mitigate risks associated with both flash and bubble formation.
Moreover, using recycled or lower-quality materials may introduce inconsistencies that heighten the likelihood of injection mold flashing occurring during production runs. These inconsistencies can result in variations in viscosity or density that affect how well the material fills the mold cavity without leaking out as flash. Hence, careful consideration of material properties should be part of any comprehensive strategy for reducing flash in injection moulding.
The Importance of Process Parameters
Finally, process parameters such as temperature settings, injection speed, and pressure play a significant role in determining whether flashing will occur during production cycles. If temperatures are too high or pressures are mismanaged, molten plastic may escape from the intended cavity—leading directly to flash issues on finished parts. Thus, maintaining optimal process conditions is essential for minimizing defects related to both flash and bubbles.
Monitoring these parameters closely allows manufacturers not only to reduce incidents of injection molding flash troubleshooting but also enhances overall product quality assurance efforts. Regular calibration of machinery combined with real-time monitoring systems helps catch deviations early on before they escalate into larger problems like excessive flashing or trapped air pockets within molded parts.
In summary, understanding what is the root cause of flashing requires a multifaceted approach involving design analysis, careful material selection, and stringent control over process parameters—all critical for achieving successful outcomes in high-quality injection molding projects.
What Causes Bubbles in Injection Molding?
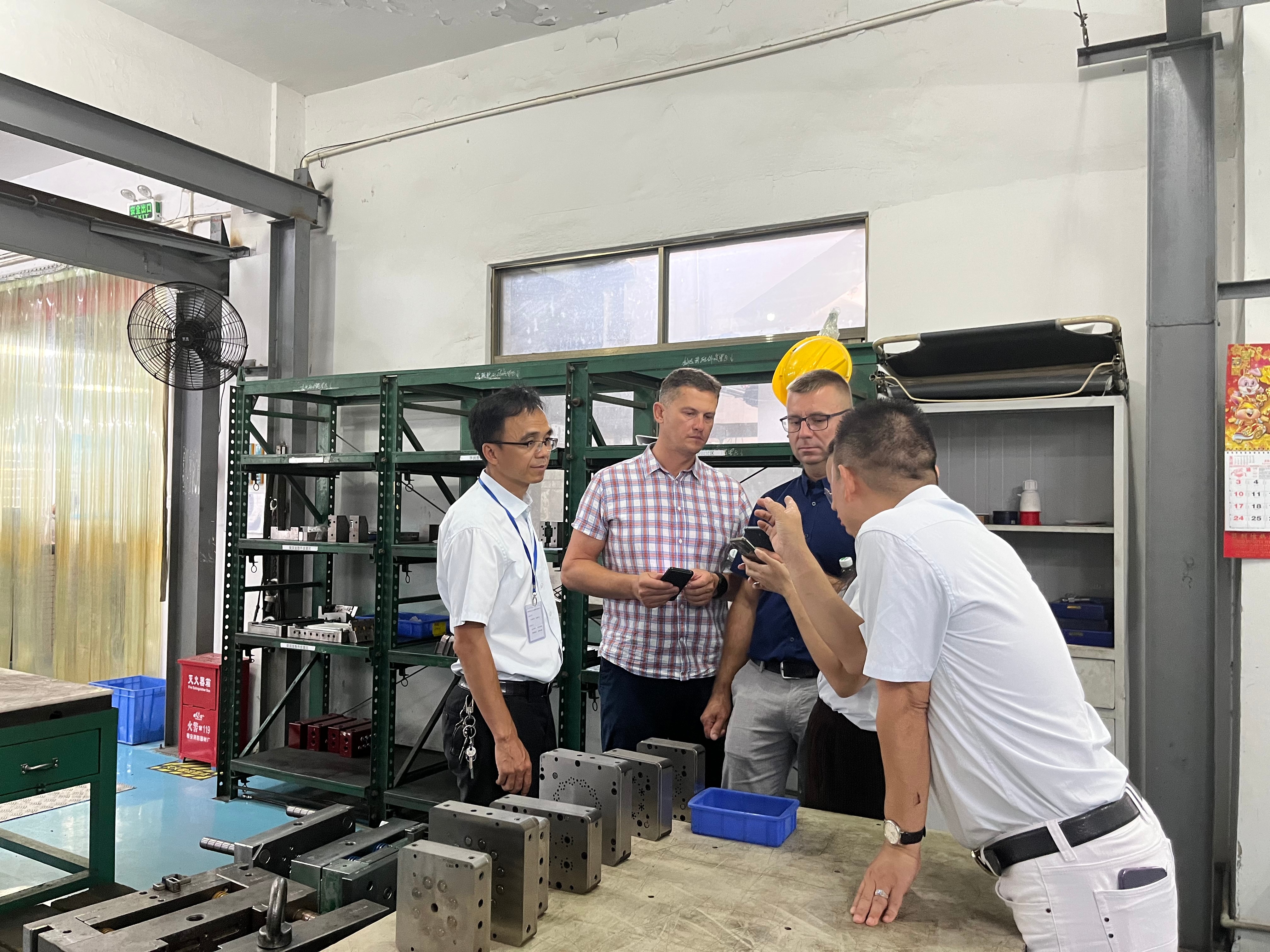
Bubbles in injection molding can be a frustrating issue, often linked to injection mold flashing. When air becomes trapped during the injection process, it can lead to unwanted bubbles that compromise the integrity of the molded part. Understanding the connection between flashing and bubbles is essential for effective injection molding flash troubleshooting.
The Connection Between Flash and Bubbles
Flashing occurs when excess material seeps out from between mold halves, creating unwanted projections on a finished part. This phenomenon can also contribute to bubble formation as trapped air is unable to escape during the injection process. Essentially, both flash and bubbles are symptomatic of underlying issues within mold design or processing parameters, making it crucial to address them simultaneously.
Examining Gas Traps and Air Pockets
Gas traps and air pockets are common culprits behind bubble formation in molded parts. When molten plastic flows into the mold cavity, any irregularities or blockages can create areas where air accumulates, leading to unsightly bubbles post-cooling. Identifying these gas traps early on is vital; otherwise, they could result in significant quality control issues down the line.
Solutions for Controlling Bubbles
To tackle bubble formation effectively, one must first understand what causes bubbles in injection molding in relation to flashing issues. Adjusting process parameters like temperature and pressure can help mitigate gas entrapment by ensuring a smooth flow of material into the mold cavity without interruptions. Additionally, employing techniques such as vacuum-assisted molding or using vented molds can significantly reduce bubble occurrences while improving overall quality.
Injection Molding Flash Troubleshooting
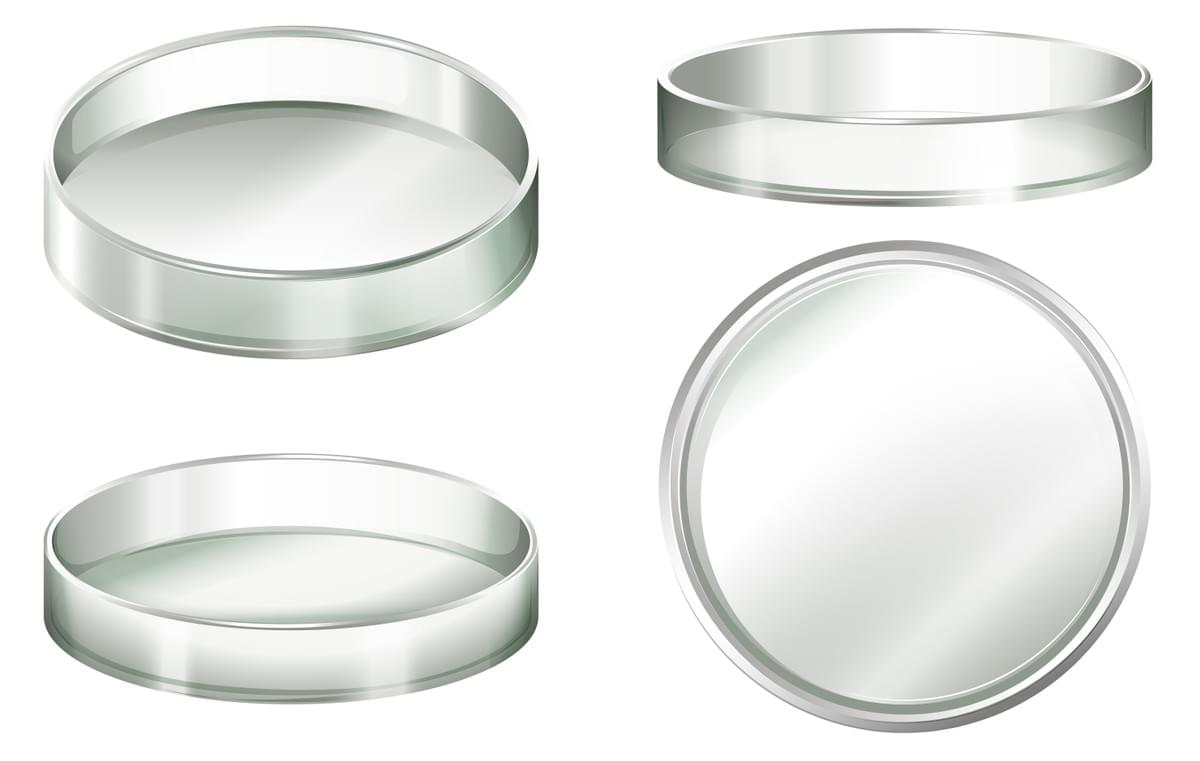
When it comes to injection mold flashing, troubleshooting is essential for maintaining quality and efficiency in production. Understanding the intricacies of what is flashing in injection molding can help identify and rectify issues before they escalate. This section will guide you through a structured approach to diagnose and resolve flash problems effectively.
Step-by-Step Troubleshooting Guide
To tackle injection molding flash troubleshooting, start by inspecting the mold design. Check for any misalignments or defects that could lead to gaps, as these are often the root cause of flashing. Once you confirm that the mold design is sound, evaluate your material selection; using inappropriate materials can contribute significantly to what is the flash issue in mold.
Next, examine process parameters such as temperature and pressure settings during injection molding. High pressures can cause excess material to escape, leading to unwanted flash around the parting line. If all else fails, perform a thorough review of your cooling time; improper cooling can also exacerbate flash issues by preventing proper solidification of parts.
Common Tools and Techniques
Several tools and techniques are available for effective injection molding flash troubleshooting. Utilizing calipers or micrometers allows for precise measurements of part dimensions, helping identify areas where excess material may be present due to flashing. Additionally, employing thermal imaging cameras can reveal hot spots that indicate uneven cooling—another factor contributing to what causes bubbles in injection molding.
Visual inspection tools like magnifying glasses or borescopes are also invaluable for spotting subtle flashes that might go unnoticed otherwise. Don't forget about simulation software; it helps in predicting potential issues before they manifest on the production floor by providing insights into flow dynamics within molds.
Case Studies and Lessons Learned
Examining real-world cases sheds light on common pitfalls associated with injection mold flashing and provides valuable lessons learned from industry experience. For instance, one manufacturer struggled with persistent flash due to inadequate venting in their molds; once they optimized ventilation channels, they saw a significant reduction in flash occurrence. This case highlights how understanding what is the root cause of flashing can lead directly to effective solutions.
Another example involved a company facing excessive bubbles during production runs caused by trapped air pockets—often linked back to poor material handling practices prior to injection molding processes. By implementing better drying procedures for their materials, they managed not only to reduce bubble formation but also minimize overall flash issues significantly.
In summary, mastering injection molding flash troubleshooting requires a keen eye for detail and an understanding of various contributing factors—from design flaws and material choices down to process parameters like temperature control and venting strategies. By applying systematic approaches along with lessons learned from past experiences, manufacturers can enhance product quality while curbing costly rework associated with excessive flashing.
How to Reduce Flash in Injection Moulding
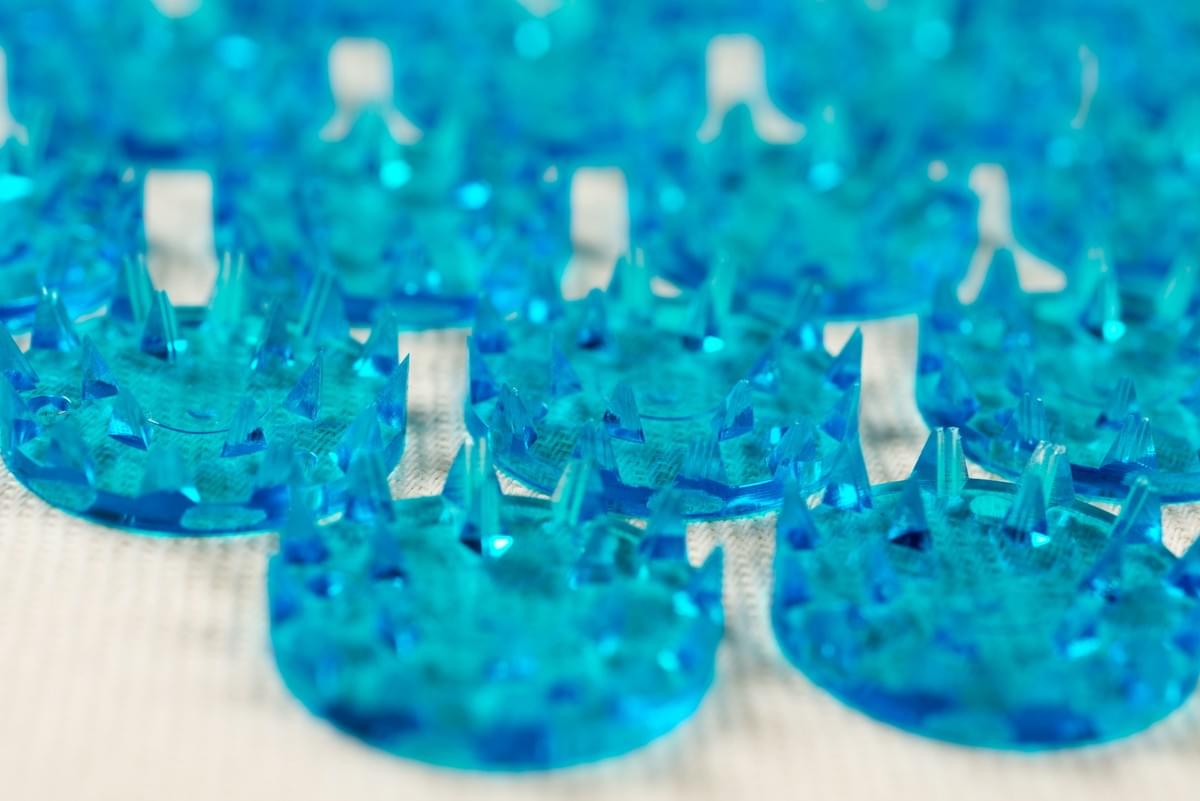
Reducing injection mold flashing is crucial for ensuring high-quality production and minimizing waste. By implementing effective strategies, manufacturers can significantly decrease the occurrence of flash and improve overall efficiency. This section will delve into recommended strategies, the role of the Baoyuan team, and best practices for quality assurance.
Recommended Strategies for Reduction
To tackle injection mold flashing effectively, it's essential to start with a thorough analysis of the mold design. Ensuring that the mold has proper alignment and adequate venting can help mitigate flash issues significantly. Additionally, optimizing process parameters such as temperature, pressure, and cooling time will aid in achieving consistent results while addressing what is flashing in injection molding.
Another effective strategy involves selecting appropriate materials that are less prone to expansion or contraction during the injection process. This can help reduce what is the flash issue in mold by minimizing material overflow at the parting line. Regular maintenance of molds also plays a vital role; worn-out or damaged molds can exacerbate flash problems, making it imperative to keep them in top condition.
Lastly, conducting regular training sessions for operators on how to identify early signs of flashing can foster a proactive approach to quality control. By focusing on these recommended strategies for reduction, manufacturers can effectively combat issues related to injection mold flashing.
The Role of the Baoyuan Team
The Baoyuan team brings invaluable expertise when it comes to addressing challenges associated with injection molding processes. Their extensive knowledge about what causes bubbles in injection molding allows them to implement tailored solutions that target specific issues like flash effectively. With their guidance, companies can develop customized action plans that directly address what is the root cause of flashing.
Moreover, Baoyuan's collaborative approach ensures that all stakeholders are involved in identifying potential improvements throughout production cycles. They provide hands-on support during troubleshooting sessions by employing advanced techniques from their arsenal of injection molding flash troubleshooting methods. This teamwork not only resolves current problems but also helps prevent future occurrences of flash.
In addition to technical support, Baoyuan emphasizes continuous education within organizations about best practices related to reducing flash in injection moulding processes. Their commitment fosters an environment where quality assurance becomes a shared responsibility among all employees.
Best Practices for Quality Assurance
Implementing best practices is essential for maintaining high standards in quality assurance when dealing with injection mold flashing issues. Regular inspections and testing should be conducted at various stages of production to identify any potential problems early on—this proactive approach helps address what is flashing in injection molding before it escalates into larger issues.
Utilizing advanced monitoring technologies during production allows manufacturers to track critical parameters closely and adjust them as necessary when deviations occur—this ensures adherence to optimal conditions while tackling what is the flash issue in mold head-on. Additionally, creating comprehensive documentation throughout each stage provides valuable insights into recurring problems and aids future troubleshooting efforts.
Finally, fostering open communication channels among team members enhances collaboration toward achieving common goals related to reducing flash occurrences effectively while maintaining high-quality standards across products. By adhering strictly to these best practices for quality assurance within their operations, manufacturers will find themselves equipped with robust solutions against challenges posed by injection mold flashing.
Conclusion
In the world of injection molding, understanding injection mold flashing is crucial for ensuring product quality and efficiency. Throughout this guide, we have explored the intricacies of flashing, including what it is, its root causes, and how it can lead to other issues like bubbles in injection molding. By addressing these problems through effective injection molding flash troubleshooting techniques and implementing strategies on how to reduce flash in injection moulding, manufacturers can significantly enhance their production processes.
Recap of Flashing Causes and Solutions
To recap, flashing in injection molding occurs when excess material seeps out from the mold cavity during the injection process. Key factors contributing to this issue include design flaws, improper material selection, and incorrect process parameters. Solutions range from redesigning molds to adjusting machine settings—each tailored approach aims to minimize or eliminate the flash issue in mold production.
Final Thoughts on Quality Injection Molding
Quality injection molding hinges not only on precision but also on proactive measures against common issues like flashing. By prioritizing quality assurance practices and fostering a culture of continuous improvement, manufacturers can produce high-quality components that meet industry standards. Remember that addressing questions such as What is the root cause of flashing? is essential for long-term success in any manufacturing operation.
Learning from Industry Experts
Learning from industry experts provides invaluable insights into best practices for tackling challenges like injection mold flashing effectively. Engaging with professionals who have faced similar issues can lead to innovative solutions that may not be immediately apparent through standard troubleshooting methods alone. Ultimately, collaborating with experienced teams can elevate your understanding of what causes bubbles in injection molding and how to mitigate these problems efficiently.