Introduction
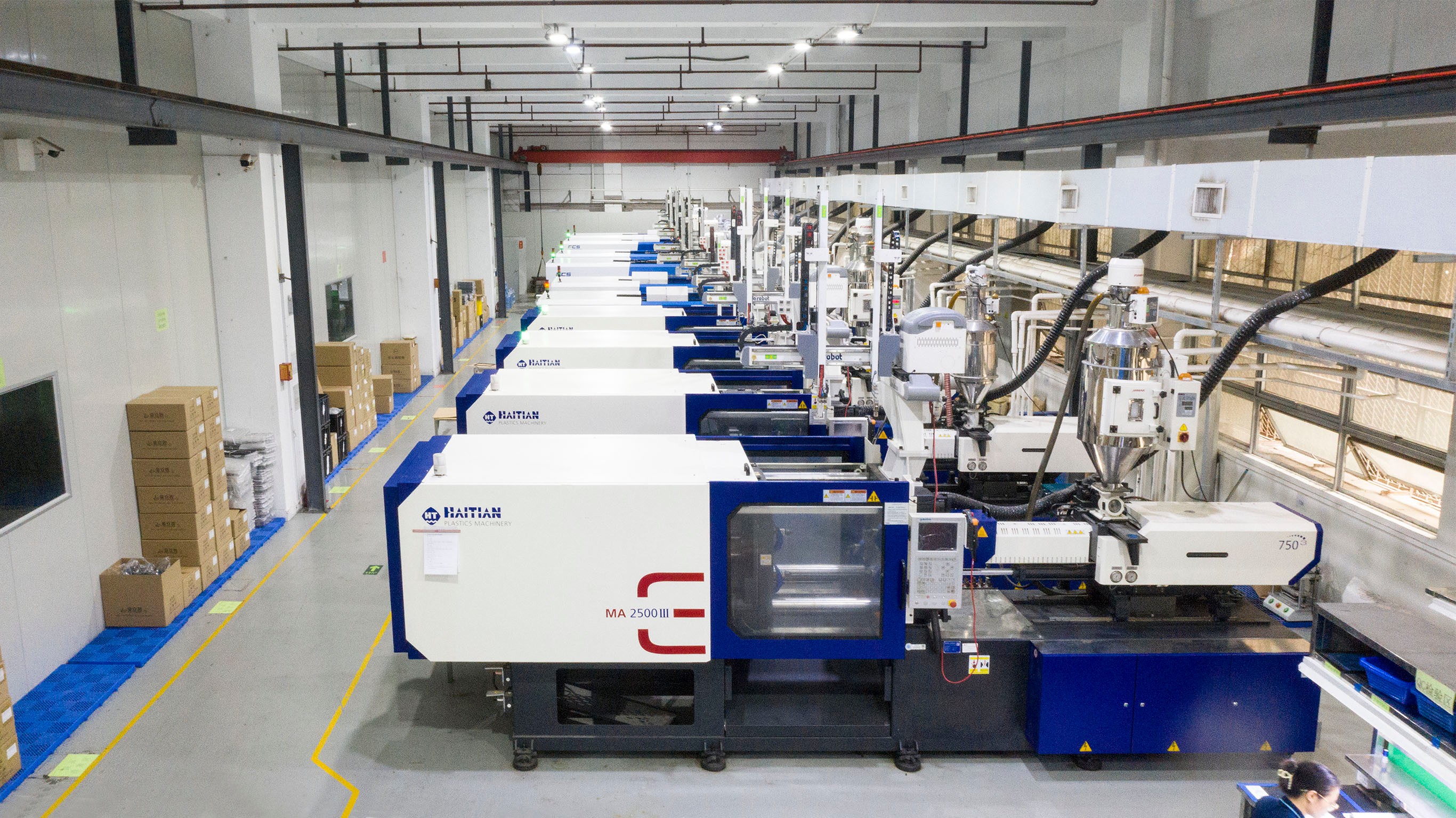
In the fast-paced world of product development, rapid injection molding has emerged as a game-changer. This innovative approach to injection molding allows designers and engineers to create high-quality prototypes in record time, significantly speeding up the entire design process. As companies strive to bring their products to market faster than ever, understanding the nuances of rapid injection molding becomes crucial.
Why Rapid Injection Molding Matters
Rapid injection molding is not just a trend; it represents a fundamental shift in how we think about manufacturing and prototyping. By utilizing advanced techniques and technologies, businesses can reduce lead times while maintaining the integrity of their designs. This method is particularly vital for industries where time-to-market can dictate success or failure.
The Benefits of Speed in Prototyping
Quick iterations allow for immediate feedback and adjustments, enabling designers to refine their products without long delays associated with traditional methods. This agility not only enhances creativity but also leads to more cost-effective solutions in developing injection molded parts.
Key Terms in Injection Molding
To navigate the landscape of rapid injection molding effectively, it's essential to familiarize yourself with some key terms. Understanding concepts like production tooling and molding over molding will empower you to make informed decisions about your projects. With a solid grasp of these terms, you can better appreciate the intricacies involved in choosing the right injection molding services for your needs.
Understanding Rapid Injection Molding
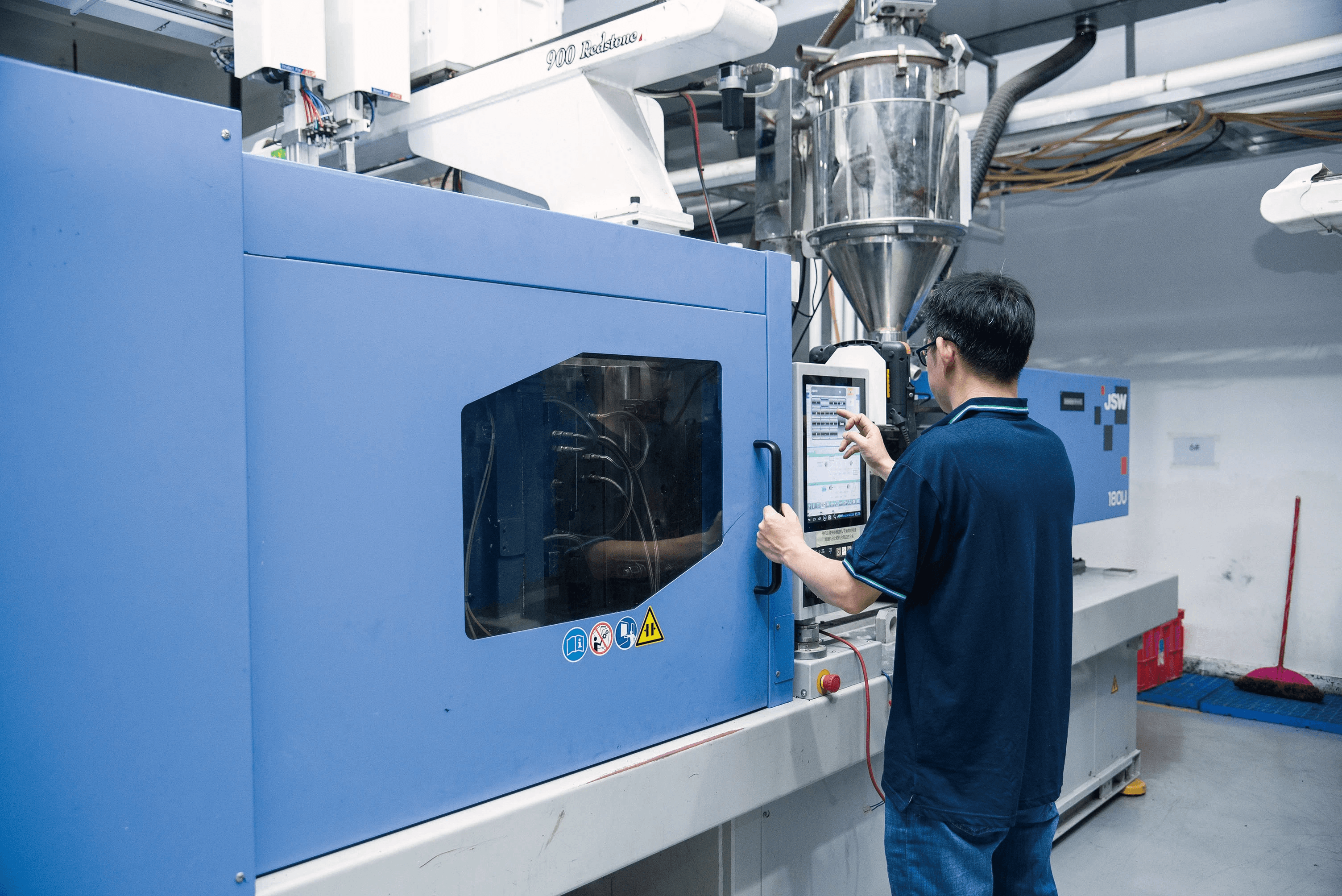
It enables designers and engineers to create high-quality injection molded parts in a fraction of the time compared to traditional methods. This speed not only accelerates product development cycles but also allows for greater flexibility in design iterations, making it an invaluable tool for modern businesses.
What is Rapid Injection Molding?
At its core, rapid injection molding refers to the process of quickly producing plastic parts using injection molding techniques, often with a focus on prototype tooling. This method utilizes advanced technologies and materials to create molds that can produce parts at an accelerated pace without sacrificing quality. By leveraging rapid prototype tooling, companies can generate functional prototypes that closely resemble the final product, enabling thorough testing and validation before mass production.
How It Differs from Traditional Methods
The primary distinction between rapid injection molding and traditional methods lies in speed and efficiency. Traditional injection molding involves longer lead times due to complex mold creation processes that require extensive machining and finishing work. In contrast, rapid injection molding streamlines this process by utilizing quicker mold fabrication techniques such as 3D printing or CNC machining, resulting in faster turnaround times for prototype tooling and significantly reduced costs for early-stage projects.
The Process of Rapid Prototyping
The process of rapid prototyping through injection molding begins with the design phase, where engineers create detailed 3D models of the desired parts using CAD software. Once finalized, these designs are translated into molds using advanced production tooling methods that prioritize speed without compromising accuracy. After mold creation, plastic material is injected into these molds to produce high-quality injection molded parts ready for testing—allowing teams to quickly iterate on their designs based on real-world feedback.
Features of Modern Injection Molding Services
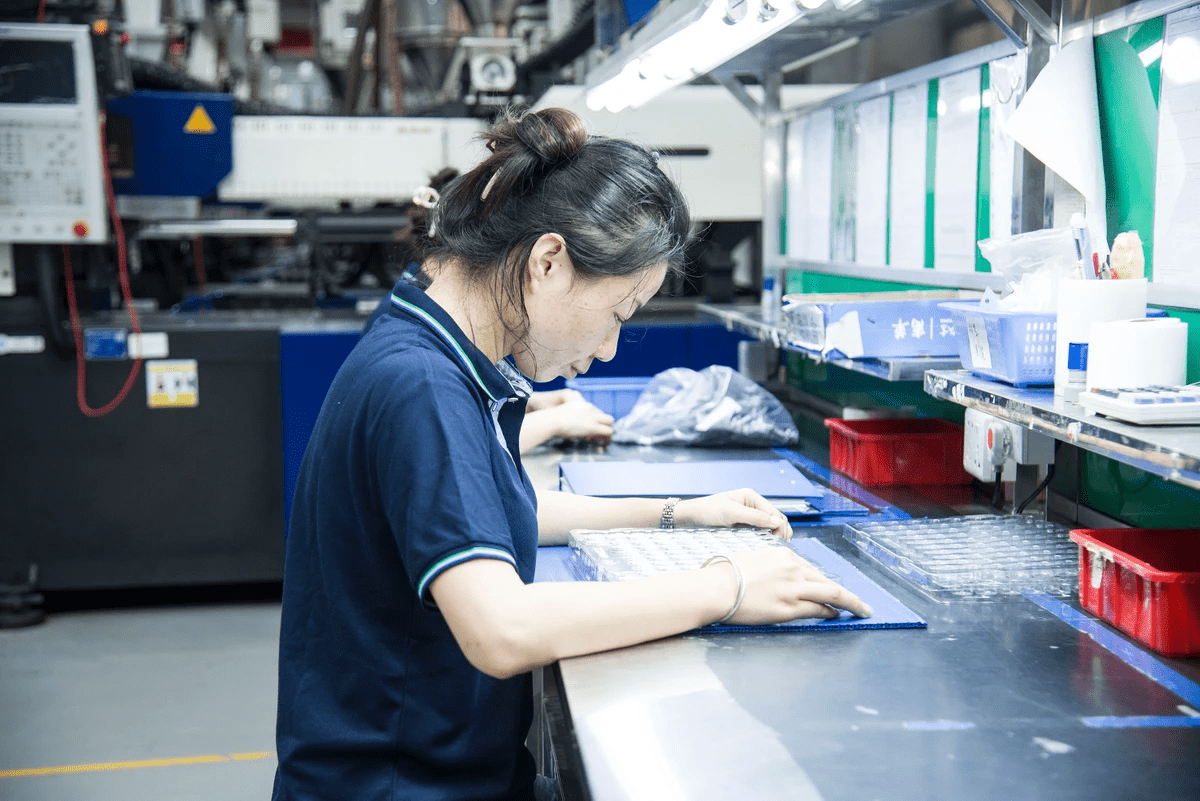
Modern injection molding services have evolved significantly, leveraging advanced technologies and innovative materials to enhance the efficiency and quality of production. At the heart of these advancements is rapid injection molding, which streamlines the entire process from design to finished product. Understanding these features can help businesses make informed decisions when selecting injection molding services for their projects.
Advanced Technology in Design
The integration of advanced technology in design has revolutionized rapid injection molding, enabling designers to create intricate and precise components with ease. Computer-Aided Design (CAD) software allows for high levels of customization and rapid iteration, making it easier to refine prototypes before moving into production tooling. Additionally, 3D printing plays a crucial role in creating molds quickly, reducing lead times significantly compared to traditional methods.
With these technological advancements, companies can produce complex geometries that were previously difficult or impossible to achieve with standard injection molding techniques. This flexibility not only enhances product performance but also opens up new avenues for innovation across various industries. Ultimately, the use of cutting-edge design technology ensures that businesses remain competitive in a fast-paced market.
Materials Used for Injection Molded Parts
The selection of materials used in rapid injection molding is critical to achieving desired product characteristics such as strength, durability, and aesthetic appeal. Modern injection molded parts can be crafted from a diverse range of thermoplastics and thermosetting polymers that cater to specific application requirements. Common materials include ABS for its toughness, polycarbonate for impact resistance, and silicone for flexibility—each offering unique benefits tailored to different end-use scenarios.
Furthermore, advancements in material science have led to the development of specialty compounds that enhance performance attributes like heat resistance or chemical stability. This variety allows manufacturers to choose the best-suited material based on functional needs while optimizing costs through efficient production tooling processes. As a result, businesses can confidently select materials that align with their project goals without compromising quality or performance.
The Role of Production Tooling
Production tooling is an essential component in the realm of rapid prototype tooling and encompasses everything from mold creation to final part production. The effectiveness of production tooling directly influences both speed and quality during the manufacturing process; therefore, investing in high-quality tools is vital for successful outcomes in injection molding services. Precision-engineered molds ensure consistent part dimensions while minimizing defects—a key factor when scaling up from prototypes to full-scale production runs.
Moreover, modern techniques such as conformal cooling channels within molds significantly reduce cycle times by improving temperature control during processing. This innovation not only enhances efficiency but also helps maintain material integrity throughout production runs—crucial when producing high-volume items from complex designs using molding over molding techniques. By understanding the importance of robust production tooling systems, companies can improve their overall productivity while delivering superior products.
Advantages of Prototype Tooling
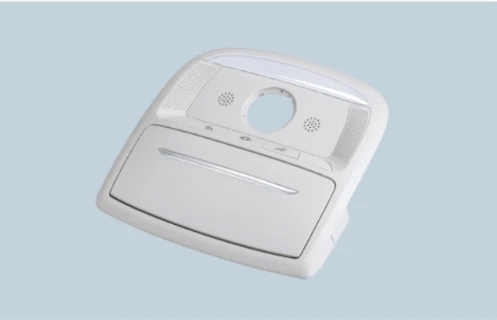
By leveraging advanced techniques in injection molding, businesses can create high-quality injection molded parts quickly and efficiently. This not only accelerates time-to-market but also allows for greater innovation and creativity in design.
Speed and Efficiency
One of the standout benefits of prototype tooling is its remarkable speed and efficiency. Rapid injection molding minimizes lead times, enabling designers to produce prototypes in a fraction of the time compared to traditional methods. This swift turnaround allows teams to test and iterate on designs rapidly, ensuring that products meet market demands without unnecessary delays.
Moreover, the efficiency gained through modern production tooling translates into streamlined operations. With advanced machinery and processes, manufacturers can produce multiple injection molded parts simultaneously, maximizing output while reducing manual labor costs. This combination of speed and efficiency makes prototype tooling an invaluable asset for companies looking to stay ahead in competitive markets.
Cost-Effectiveness in Prototyping
Cost-effectiveness is another compelling advantage of utilizing prototype tooling within rapid injection molding processes. Traditional prototyping methods often incur significant expenses due to lengthy production cycles and material waste; however, rapid prototype tooling mitigates these costs by optimizing resource usage and minimizing waste generation. As a result, businesses can allocate their budgets more effectively while still achieving high-quality results.
Additionally, by reducing both time and material costs associated with prototyping, companies can invest their savings into further research or development initiatives—ultimately fostering innovation within their product lines. The ability to create cost-effective injection molded parts without sacrificing quality or performance is a game-changer for many organizations navigating tight budgets or financial constraints.
Flexibility in Design Iterations
Flexibility is crucial when it comes to refining designs during the prototyping phase; this is where prototype tooling shines brightly within rapid injection molding frameworks. The iterative nature of this process allows designers to make quick adjustments based on testing feedback or market trends without facing extensive delays or additional costs associated with traditional methods. Consequently, teams can experiment freely with various concepts until they arrive at the most effective solution.
Furthermore, molding over molding techniques enable even greater versatility when combining different materials or features within a single part design—allowing for complex geometries that may not have been feasible otherwise. This flexibility fosters collaboration between engineers and designers as they work together seamlessly throughout each stage of product development—ultimately leading to superior end-products that resonate with consumers' needs.
Best Practices for Molding Over Molding
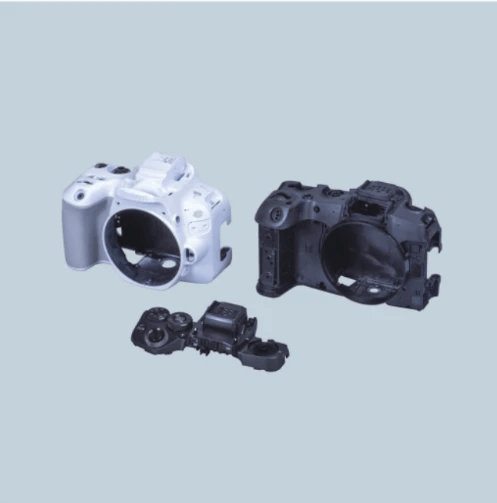
Molding over molding is an innovative technique that enhances the performance and aesthetics of injection molded parts. By layering materials, manufacturers can achieve complex designs that were previously difficult to produce using traditional methods. To ensure the best results, it’s essential to follow specific best practices tailored for rapid injection molding.
Techniques for Optimal Results
To achieve optimal results in molding over molding, precision is key. First, ensuring a tight fit between the base and the overlay material can significantly enhance bond strength and durability. Additionally, controlling temperature and pressure during the injection process is crucial; these factors influence how well materials fuse together, ultimately affecting the quality of your prototype tooling.
Another effective technique involves selecting the right sequence of operations in production tooling. For instance, pre-heating certain components can facilitate better adhesion between layers while minimizing defects like warping or delamination. Lastly, regular maintenance of injection molding equipment ensures consistent performance and reduces downtime—an essential aspect when speed is a priority in rapid injection molding.
Applications in Product Design
Molding over molding has found its niche in various applications within product design, particularly where functionality meets aesthetics. For example, automotive parts often utilize this method to create components that require both strength and visual appeal—think of dashboard panels with soft-touch finishes combined with hard structural elements. This versatility makes it an attractive option for industries ranging from consumer electronics to medical devices.
Moreover, incorporating multiple materials allows designers to tailor properties such as flexibility or rigidity according to specific needs. In rapid prototype tooling, this means you can quickly iterate designs without being limited by single-material constraints—a game-changer for teams looking to innovate swiftly and efficiently. As product design continues evolving toward more complex structures, mastering molding over molding will be vital for staying competitive.
Choosing the Right Materials
Selecting appropriate materials is paramount when engaging in molding over molding processes within rapid injection molding frameworks. Each layer's material must not only complement each other but also serve distinct functional roles; for instance, combining a strong core material with a softer outer layer can enhance both durability and user experience. Understanding material properties such as thermal stability and chemical resistance will guide you toward making informed choices that yield high-quality injection molded parts.
Additionally, working closely with your injection molding services provider can help identify suitable materials based on project requirements—whether you're focusing on cost-effectiveness or high-performance characteristics like impact resistance or UV stability. The right combination not only improves product longevity but also streamlines production processes by reducing waste associated with trial-and-error iterations during prototyping phases.
In summary, mastering best practices for molding over molding requires attention to detail across techniques, applications in product design, and careful selection of materials—all pivotal elements that contribute to successful rapid injection molding projects.
The Expertise of Baoyuan in Injection Molding
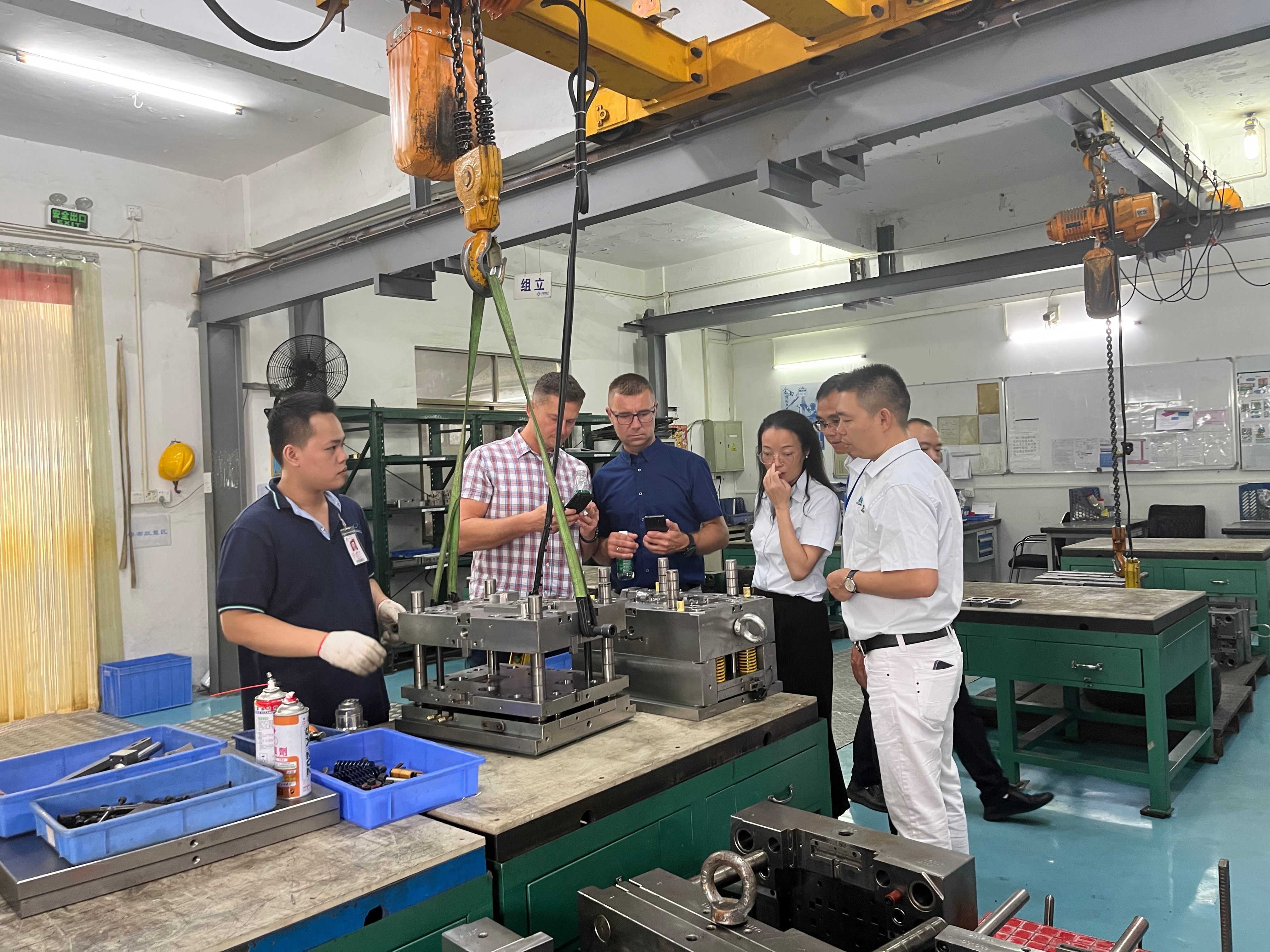
Skilled Personnel in Mold Design
At Baoyuan, skilled personnel are the backbone of effective mold design for rapid prototype tooling. Their extensive experience allows them to create molds that optimize efficiency while maintaining high-quality standards. By leveraging advanced software and design techniques, these experts ensure that every detail is meticulously crafted for seamless integration into the production tooling process.
The team understands that each project presents unique challenges and opportunities, which is why they are dedicated to continuous learning and adaptation within the field of injection molding. This commitment translates into innovative solutions tailored specifically to client needs, enhancing both speed and functionality in product development. Ultimately, having a skilled workforce means faster turnaround times without compromising on quality—a win-win for anyone looking for reliable injection molding services.
Quality Assurance in Production
Quality assurance is paramount at Baoyuan, especially when it comes to rapid injection molding processes where precision is key. The company employs stringent testing protocols throughout production to ensure that all injection molded parts meet or exceed industry standards. This rigorous approach not only minimizes defects but also fosters trust among clients who rely on consistent quality for their projects.
Baoyuan's quality assurance extends beyond mere inspection; it involves proactive measures at every stage of production tooling, from initial design concepts through final output. By utilizing state-of-the-art technology and methodologies, they can identify potential issues before they escalate into larger problems—saving time and resources along the way. Clients can rest easy knowing their products are produced under a watchful eye committed to excellence.
Successful Projects and Case Studies
Baoyuan's portfolio boasts an array of successful projects that highlight its prowess in rapid injection molding and prototype tooling applications across various industries. From automotive components to consumer electronics, each case study illustrates how tailored solutions lead to remarkable outcomes while adhering to tight timelines. These success stories serve as testament not only to Baoyuan’s capabilities but also its dedication towards pushing boundaries within injection molding services.
One notable project involved developing complex multi-material components using advanced molding over molding techniques—showcasing both creativity and technical skill in overcoming design challenges faced by clients. Such achievements have positioned Baoyuan as a leader in the field, consistently delivering exceptional results while fostering long-term partnerships with satisfied customers worldwide. With a track record like this, it's clear why so many companies turn to Baoyuan for their rapid prototype tooling needs.
Conclusion
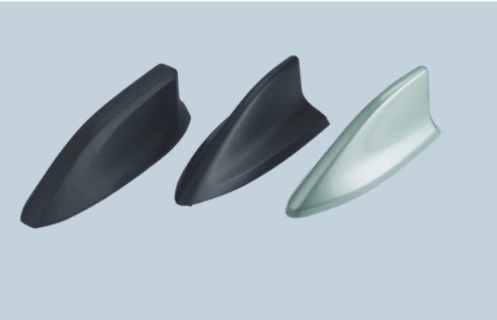
In a world where speed and efficiency are paramount, rapid injection molding has emerged as a game-changer in the manufacturing landscape. This innovative approach not only accelerates the prototyping process but also enhances design flexibility and cost-effectiveness. As we wrap up, let’s delve into some key takeaways that highlight its significance and future potential.
Key Takeaways on Rapid Injection Molding
Rapid injection molding is revolutionizing how businesses approach product development by allowing for faster iterations of injection molded parts. This method significantly reduces lead times compared to traditional techniques, enabling companies to bring their products to market quicker than ever before. Additionally, the adaptability of prototype tooling makes it easier for designers to refine concepts without incurring excessive costs.
How to Choose the Right Injection Molding Services
Selecting the right injection molding services can feel like finding a needle in a haystack—especially with so many options available! Look for providers that specialize in rapid prototype tooling, as this indicates their capability to handle fast-paced projects while maintaining quality. It’s also wise to consider their experience with production tooling and molding over molding techniques, which can impact both the performance and aesthetics of your final product.
The Future of Rapid Prototype Tooling
The future of rapid prototype tooling looks incredibly promising as technology continues to evolve at breakneck speed. Advancements such as 3D printing integration and enhanced materials will further streamline processes in rapid injection molding, making it more accessible for businesses of all sizes. As industries lean towards faster turnaround times and greater customization, those who embrace these innovations will undoubtedly gain a competitive edge in their respective markets.