Introduction

In the world of plastic manufacturing, understanding plastic injection mold pricing is crucial for businesses looking to optimize their production processes. The cost of a plastic injection mold can vary significantly based on various factors, making it essential to have a clear grasp of what influences these prices. By delving into the intricacies of injection molding, companies can make informed decisions that align with their budget and production goals.
Understanding Plastic Injection Mold Pricing
Plastic injection mold price is not merely a number; it encapsulates the complexity of materials, labor, and technology involved in creating high-quality molds. When evaluating costs, one must consider the type of injection moldable plastics used and how they affect both initial investment and long-term durability. By comprehensively assessing these elements, businesses can better predict expenses and avoid unpleasant surprises down the line.
Importance of Accurate Cost Estimates
Accurate cost estimates are vital for any project involving plastic injection moulding service, as they provide a roadmap for budgeting and resource allocation. An underestimation can lead to financial strain or project delays, while overestimation may result in missed opportunities due to inflated budgets. Therefore, having precise calculations helps ensure that companies remain competitive in an ever-evolving market landscape.
Key Factors Influencing Mold Prices
These include design complexity, material selection, production volume, and customization requirements—all of which can significantly sway overall costs. Understanding these variables empowers businesses to negotiate better deals with their suppliers and optimize their investments in plastic injection molding projects.
What is Plastic Injection Molding?
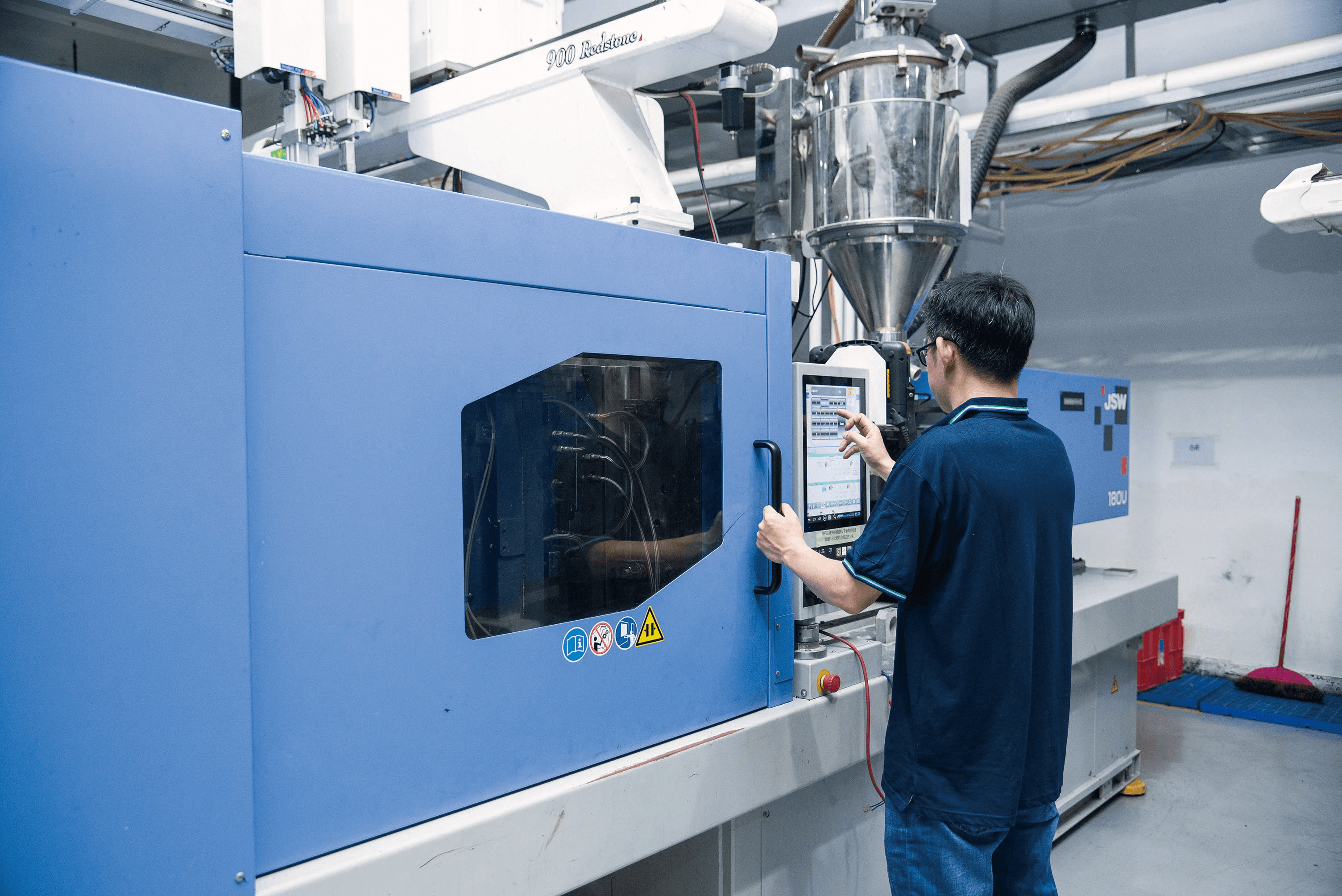
Plastic injection molding is a manufacturing process that involves the creation of plastic parts by injecting molten plastic into a mold. This method allows for high precision and repeatability, making it an ideal choice for producing large quantities of items with uniform quality. The versatility of injection molding leads to its widespread use across various industries, from automotive to consumer goods.
A Brief Overview of the Process
The process begins with the selection of injection moldable plastics, which are heated until they reach a molten state. Once liquefied, the plastic is injected into a precisely designed mold under high pressure, allowing it to fill every cavity and detail. After cooling and solidification, the mold is opened, and the finished part is ejected—a process that can be repeated rapidly for mass production.
Common Applications in Various Industries
Injection molding finds applications in numerous fields due to its efficiency and cost-effectiveness in plastic manufacturing. In the automotive industry, components like dashboards and bumpers are commonly produced using this technique. Other sectors such as electronics rely on injection molding for creating intricate housings for devices, while medical industries utilize it for producing reliable surgical instruments and packaging.
Benefits of Using Injection Molding
One of the primary benefits of using plastic injection molding is its ability to produce complex shapes with high accuracy at lower costs per unit when manufacturing at scale. Additionally, this process minimizes waste since excess material can often be recycled back into production—making it an environmentally friendly option compared to other methods. Finally, rapid production times mean that businesses can respond quickly to market demands without compromising on quality or precision.
Breakdown of Plastic Injection Mold Costs
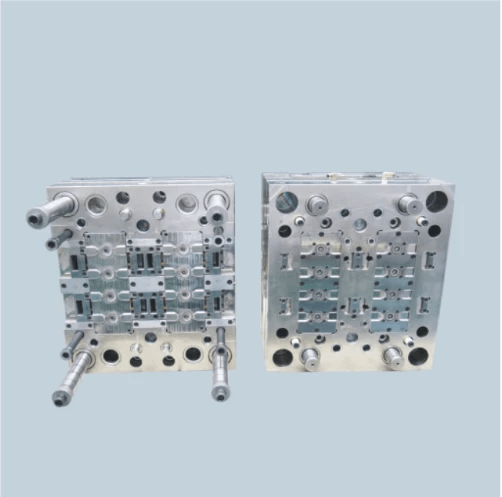
Material Costs for Injection Moldable Plastics
The first significant factor affecting plastic injection mold prices is the cost of materials used in the process. Different types of injection moldable plastics come with varying price tags, influenced by factors such as availability, quality, and specific properties required for your application. For instance, high-performance thermoplastics may be more expensive but offer superior durability and functionality compared to standard options.
When selecting a material for your project, consider not only the upfront costs but also how these materials will perform in real-world applications. Cheaper plastics may save you money initially but could lead to increased costs down the line due to failures or replacements. Therefore, investing in quality injection moldable plastics can ultimately lead to better performance and lower total costs over time.
In addition to raw material costs, keep an eye on market trends that can affect pricing fluctuations in plastic manufacturing. Global supply chain issues or changes in demand for specific polymers can impact your overall budget significantly. Staying informed about these trends will help you make strategic decisions regarding your choice of materials.
Labor and Production Expenses
Labor and production expenses are another crucial component when calculating plastic injection mold prices. The complexity of your design dictates how much time skilled technicians will need to spend on setup and operation during the molding process. More intricate designs typically require specialized skills or longer production cycles, which can drive up labor costs significantly.
Additionally, factors such as machine maintenance and energy consumption play a role in determining overall production expenses associated with mould plastic injection services. Efficient machinery often leads to reduced cycle times and lower operational costs; therefore, selecting a provider with modern equipment can be beneficial in managing expenses effectively.
It’s also worth noting that labor rates vary by region; thus choosing a local service provider may help minimize transportation fees while ensuring timely delivery of services without compromising quality standards in plastic manufacturing.
Additional Charges for Customization
Customization is often essential when it comes to meeting specific client requirements or unique product designs within the realm of injection molding services. However, this added flexibility usually comes at an extra cost—hence why it's vital to understand how customization affects overall plastic injection mold price estimates before committing fully.
From creating custom molds tailored precisely for your project needs to incorporating unique features like textures or colors into each piece produced through mould plastic injection—these enhancements require additional resources that contractors factor into their pricing models accordingly. Always ask potential service providers about their customization capabilities upfront so there are no surprises later on!
Keep in mind that while customization might add initial expenses upfront during production phases; it often leads directly toward higher customer satisfaction levels down-the-line through improved product performance! So weigh those long-term benefits against short-term investments carefully when considering options available from various plastic injection moulding service providers out there today!
How to Choose a Plastic Injection Moulding Service
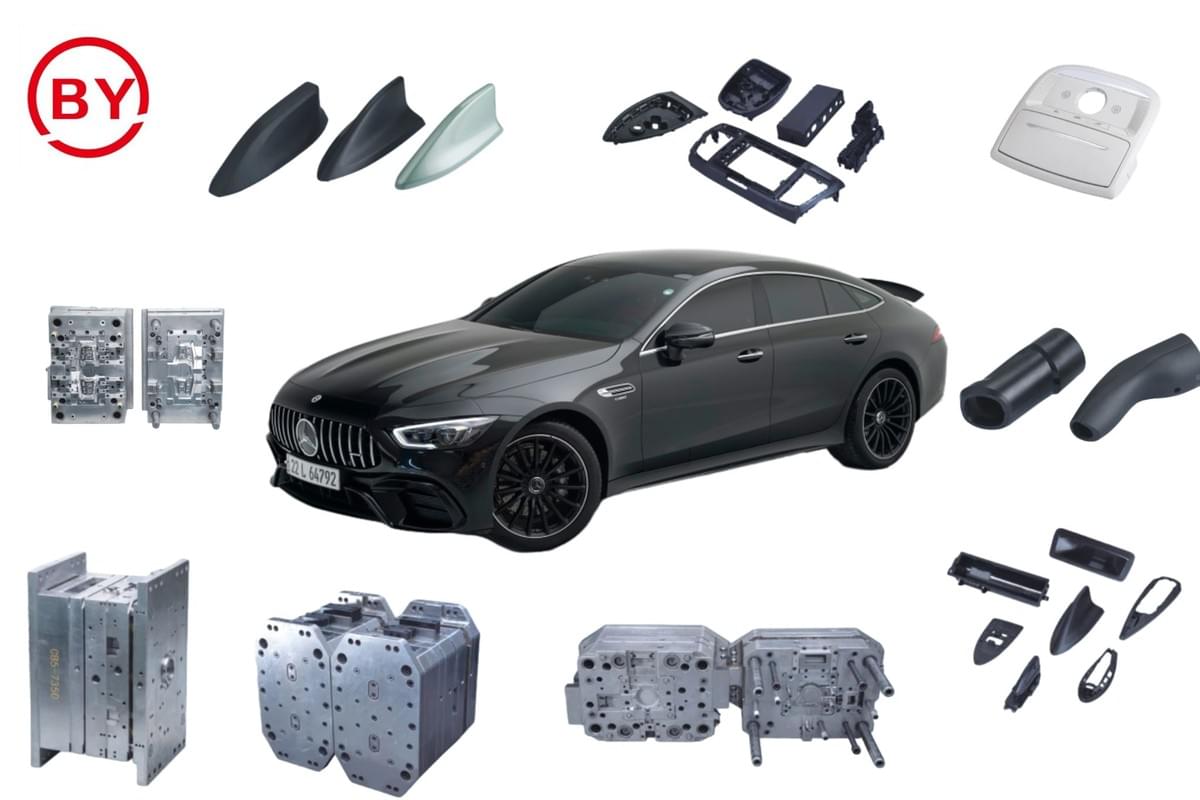
Choosing the right plastic injection moulding service can feel like navigating a maze, especially with so many options available. It’s crucial to evaluate various factors to ensure you get the best value for your investment, particularly concerning plastic injection mold price. A well-chosen partner can make a significant difference in both quality and efficiency of your plastic manufacturing needs.
Evaluating Provider Experience and Reputation
Additionally, consider whether the provider has experience in your specific industry or application. Different sectors may have unique requirements that necessitate specialized knowledge in mold plastic injection techniques or material selection. A reputable provider will not only understand these nuances but will also be able to offer tailored solutions that meet your needs efficiently.
Importance of Technical Expertise
Technical expertise is another critical factor when choosing a plastic injection moulding service. The intricacies involved in designing and producing molds require skilled professionals who are well-versed in the latest technologies and techniques within the field of injection molding. This expertise can significantly influence both the quality of the final product and the overall production timeline.
A knowledgeable team will be better equipped to troubleshoot issues as they arise, ensuring that your project stays on track without unnecessary delays or cost overruns related to mold design flaws or material mishaps. Furthermore, having access to technical experts means you can benefit from innovative solutions that may enhance both performance and cost-effectiveness—crucial elements when considering long-term projects where every dollar counts.
Comparing Service Offerings and Pricing
Once you've narrowed down potential providers, it's time to compare their service offerings alongside pricing structures related to plastic injection mold price. Not all services are created equal; some might offer additional features such as design consultation or post-production support that could save you time and money down the line. Make sure you understand what each provider includes in their quoted prices for services like prototyping, tooling, and production runs.
It's also wise to inquire about any hidden fees associated with customization or adjustments during production phases—these costs can quickly add up if you're not careful! By comparing multiple quotes while keeping an eye on what each service entails, you'll be better positioned to make an informed decision that aligns with both your budgetary constraints and project requirements.
The Role of Design in Mold Plastic Injection
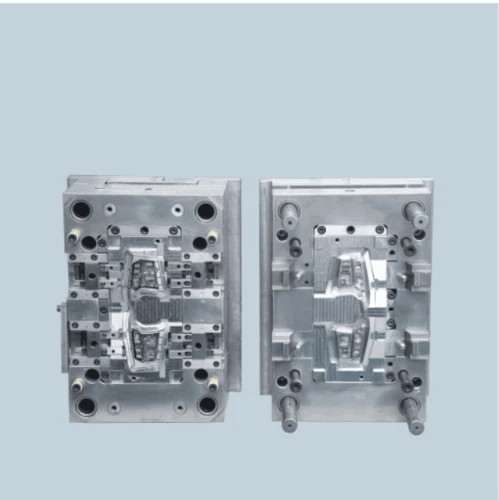
Designing for Cost Efficiency
Designing for cost efficiency involves selecting the right materials and optimizing the geometry of the parts being produced. By utilizing injection moldable plastics that require less complex molds, manufacturers can effectively lower their plastic injection mold price while maintaining product quality. Additionally, simplifying part designs can minimize machining time and reduce labor costs associated with production.
Another important aspect is incorporating features like draft angles and uniform wall thicknesses into the design to facilitate easier ejection from molds. These adjustments not only help in reducing potential defects but also contribute to quicker cycle times during production runs. Ultimately, a focus on cost-efficient design leads to significant savings over the life cycle of a product in plastic manufacturing.
Impact of Mold Design on Production Time
The intricacies of mold design have a direct correlation with production time in plastic injection molding processes. A well-designed mold allows for faster cycle times due to efficient cooling and ejection mechanisms—factors that directly affect how quickly products can be produced and brought to market. Conversely, poorly designed molds may lead to extended production times as they require more maintenance or adjustments during operation.
Moreover, intricate designs may necessitate additional steps such as secondary operations or assembly processes that further elongate production timelines. This increased duration not only affects immediate costs but also impacts long-term profitability by delaying product availability in competitive markets. Therefore, investing in smart mold designs not only enhances efficiency but also serves as a strategic advantage within the realm of mould plastic injection services.
Case Study: Baoyuan’s Design Solutions
Baoyuan has established itself as a leader in providing innovative solutions for plastic injection moulding service through its commitment to effective design strategies. One notable case involved a client seeking high-volume production of complex components at an affordable price point; Baoyuan's team focused on streamlining the initial designs by using advanced software simulations before actual fabrication began. This proactive approach allowed them to identify potential issues early on and modify designs accordingly—ultimately leading to reduced costs without sacrificing quality.
Through their expertise in utilizing cutting-edge technology alongside traditional engineering principles, Baoyuan was able to deliver molds that significantly decreased cycle times while keeping the overall plastic injection mold price competitive within the industry standards. Their success story illustrates how thoughtful design plays an integral role not just during development but throughout every phase of production—reinforcing why businesses should prioritize effective mould plastic injection strategies when planning their projects.
Understanding Production Volume and Pricing
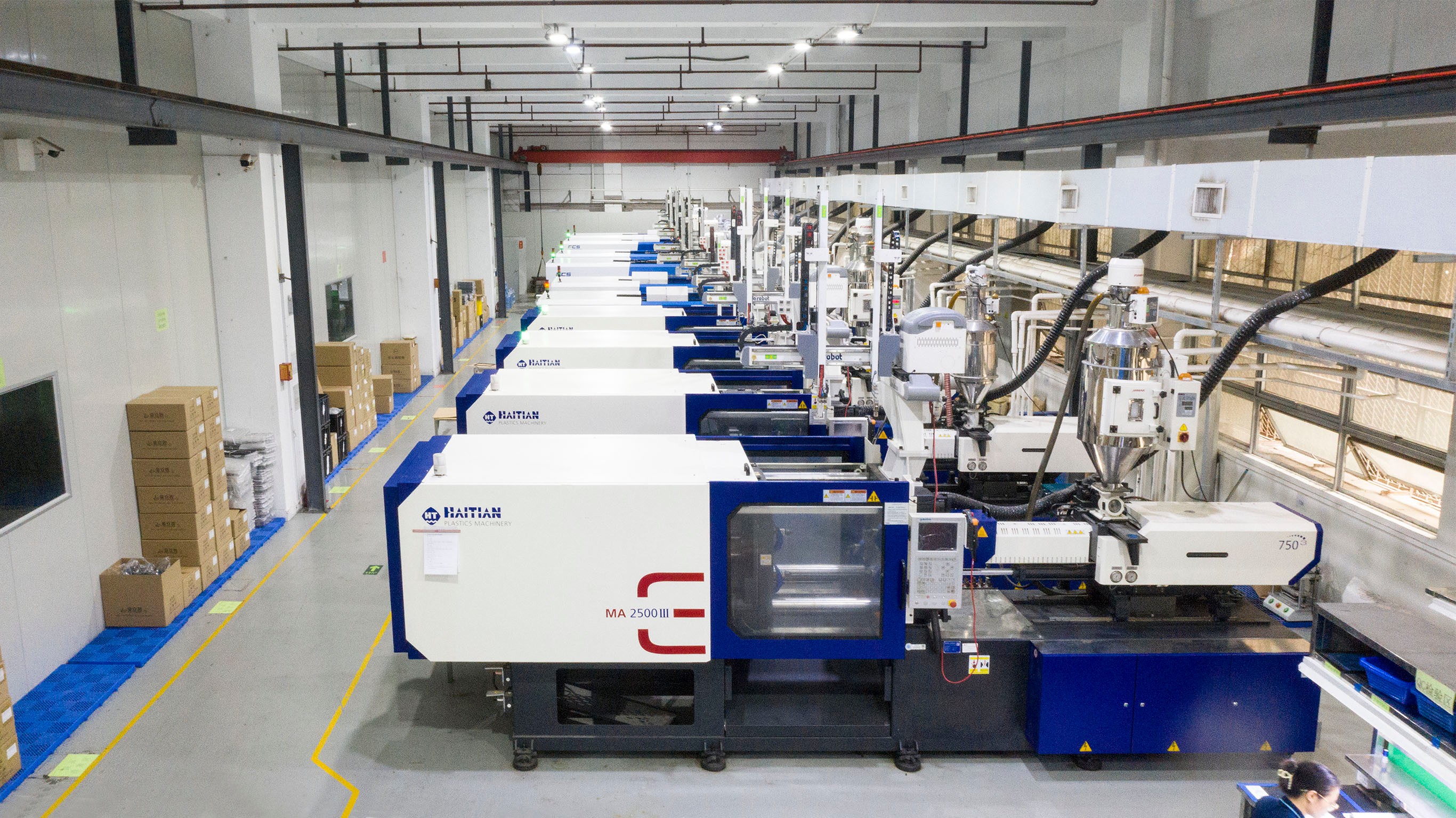
When it comes to plastic injection molding, understanding how production volume influences the plastic injection mold price is crucial. The relationship between the quantity of parts produced and the cost of molds can significantly impact your budget and project timeline. In this section, we’ll explore how different volumes affect pricing structures in the realm of injection molding.
How Volume Affects Plastic Injection Mold Price
The plastic injection mold price is closely tied to the volume of parts being manufactured. Generally, higher production volumes lead to lower per-unit costs as the initial investment in mold creation gets distributed over a larger number of items. Conversely, for low-volume projects, such as prototypes or limited runs, the cost per unit can skyrocket since fixed costs are not amortized across many pieces.
This phenomenon occurs because creating molds for injection molding involves substantial upfront expenses—designing and fabricating molds requires skilled labor and premium materials. Therefore, when engaging a plastic injection moulding service for small quantities, you might find that your overall costs are disproportionately high compared to mass production scenarios. It's essential to factor in these dynamics when planning your project’s budget.
Additionally, production volume can influence other aspects like lead times and material selection. For instance, if you’re producing a large batch of parts using injection moldable plastics, you might have more flexibility in choosing materials that could further optimize costs without compromising quality.
The Economics of Mass Production vs. Prototyping
When weighing the economics of mass production against prototyping in plastic manufacturing, it's vital to recognize that each approach has its merits depending on your project's goals. Mass production typically offers lower costs per unit due to economies of scale; however, it requires a significant upfront investment in mold design and fabrication—hence why understanding plastic injection mold prices is essential before committing.
On the flip side, prototyping allows companies to test designs and make adjustments before investing heavily in full-scale production runs. While this may seem more expensive on a per-unit basis initially due to higher tooling costs spread over fewer pieces, it can save money long-term by preventing costly errors down the line during mass manufacturing phases.
Ultimately, choosing between these two paths often hinges on your product's lifecycle stage—if you're still refining designs or testing market viability with small batches using mould plastic injection techniques may be worthwhile until you're ready for full-scale production.
Decision-Making for Long-Term Projects
For long-term projects involving repeated orders or consistent demand for specific parts through plastic injection molding processes, making informed decisions about volume becomes even more critical. It's wise to consider not only current needs but also potential future requirements when evaluating pricing structures with your chosen plastic injection moulding service provider.
A strategic approach would involve negotiating terms based on projected volumes rather than just immediate orders; many manufacturers will offer discounts or tiered pricing based on expected order quantities over time—this can help mitigate rising material costs associated with fluctuating demand cycles within industries reliant upon consistent supply chains.
Moreover, think about scalability: if you anticipate growth or shifts in demand patterns down the road, ensure that your chosen partner has capabilities that match those evolving needs without incurring excessive new setup fees related solely back towards initial tooling investments needed at higher output levels later on down this journey!
Conclusion
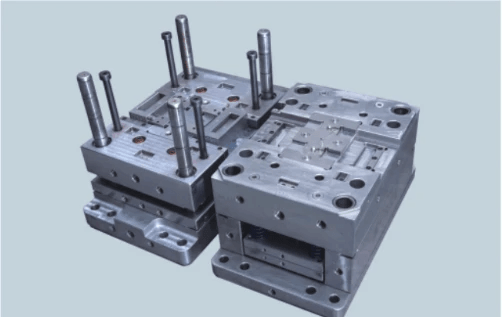
In the world of plastic manufacturing, understanding the intricacies of plastic injection mold pricing is crucial for businesses looking to optimize their production processes. From material costs to labor expenses and customization charges, each factor plays a significant role in determining the overall cost of your project. By grasping these elements, companies can better navigate the often complex landscape of injection molding.
Recap of Key Cost Factors
When assessing plastic injection mold prices, it's essential to consider several key factors that influence costs. Material selection for injection moldable plastics can vary significantly, impacting both quality and price. Labor and production expenses also contribute heavily to the final bill, especially when custom designs are involved in the mould plastic injection process.
Additionally, the design phase is pivotal; an efficient mold design not only reduces costs but also enhances production speed. Understanding these components allows businesses to make informed decisions about their projects while ensuring they receive value for their investment in a plastic injection moulding service. Remember that every choice you make—from materials to services—can affect your bottom line.
Making Informed Decisions on Mold Services
Choosing the right plastic injection molding service can feel overwhelming with so many options available today. Start by evaluating potential providers based on their experience and reputation within the industry; this ensures you're working with knowledgeable partners who understand your needs. Technical expertise is equally important; look for teams that can offer innovative solutions tailored specifically for your project.
Don’t forget to compare service offerings and pricing among different providers—this will help you gauge where you might find cost savings without sacrificing quality or efficiency in your mould plastic injection process. Ultimately, making informed decisions means balancing price with performance, ensuring you get both a competitive rate and high-quality results in your production runs.
Baoyuan: Your Partner in Injection Molding Solutions
At Baoyuan, we understand that navigating the complexities of plastic manufacturing can be daunting—but we're here to simplify that journey for you! With our extensive expertise in providing top-notch plastic injection moulding services, we ensure that our clients receive exceptional value at competitive prices without compromising on quality or efficiency. Our commitment is not just to meet expectations but exceed them through innovative design solutions and cutting-edge technology.
We pride ourselves on being more than just a supplier; we aim to be your trusted partner in all aspects of mold plastic injection processes from start to finish. When you choose Baoyuan, you're choosing a team dedicated to helping you achieve success through effective strategies tailored specifically for your unique requirements—because together we can create something extraordinary!