Introduction
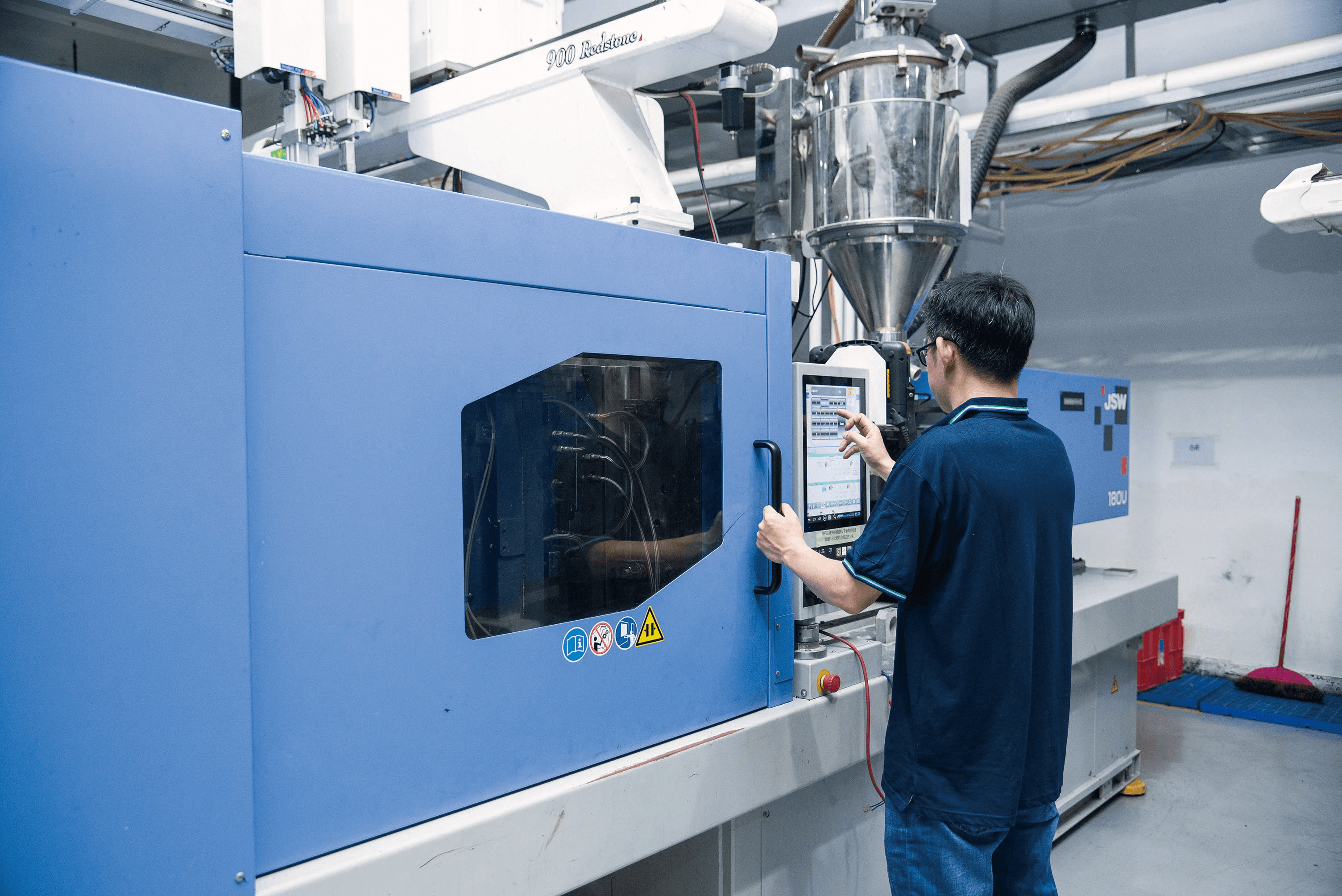
In recent years, the manufacturing landscape has witnessed a significant transformation with the rise of PPE injection molding. This innovative technique not only streamlines production processes but also enhances the overall quality of molded products. As industries increasingly turn to plastic injection molding, understanding the intricacies of molding inspection becomes essential for maintaining high standards.
The Rise of PPE Injection Molding
PPE injection molding has emerged as a go-to solution for producing high-quality components across various sectors, from automotive to consumer goods. This method utilizes injection moldable plastics that offer exceptional durability and versatility, making it an attractive choice for manufacturers seeking reliability and performance. The demand for efficient production methods has propelled this technology into the spotlight, highlighting its importance in today’s competitive market.
Enhancing Efficiency in Production
One of the primary benefits of employing PPE injection molding is its ability to enhance efficiency in production lines. By leveraging advanced machinery and optimized processes, manufacturers can significantly reduce cycle times while increasing output quality. This efficiency not only translates into cost savings but also allows businesses to meet customer demands promptly without compromising on product integrity.
The Role of Molding Inspection
Molding inspection plays a critical role in ensuring that every piece produced through plastic injection molding meets stringent quality standards. Effective inspection techniques help identify defects early in the process, preventing costly rework and ensuring that only top-notch products reach consumers. By prioritizing thorough inspection protocols, manufacturers can boost their production efficiency while maintaining a strong reputation for quality in the market.
Understanding PPE Injection Molding
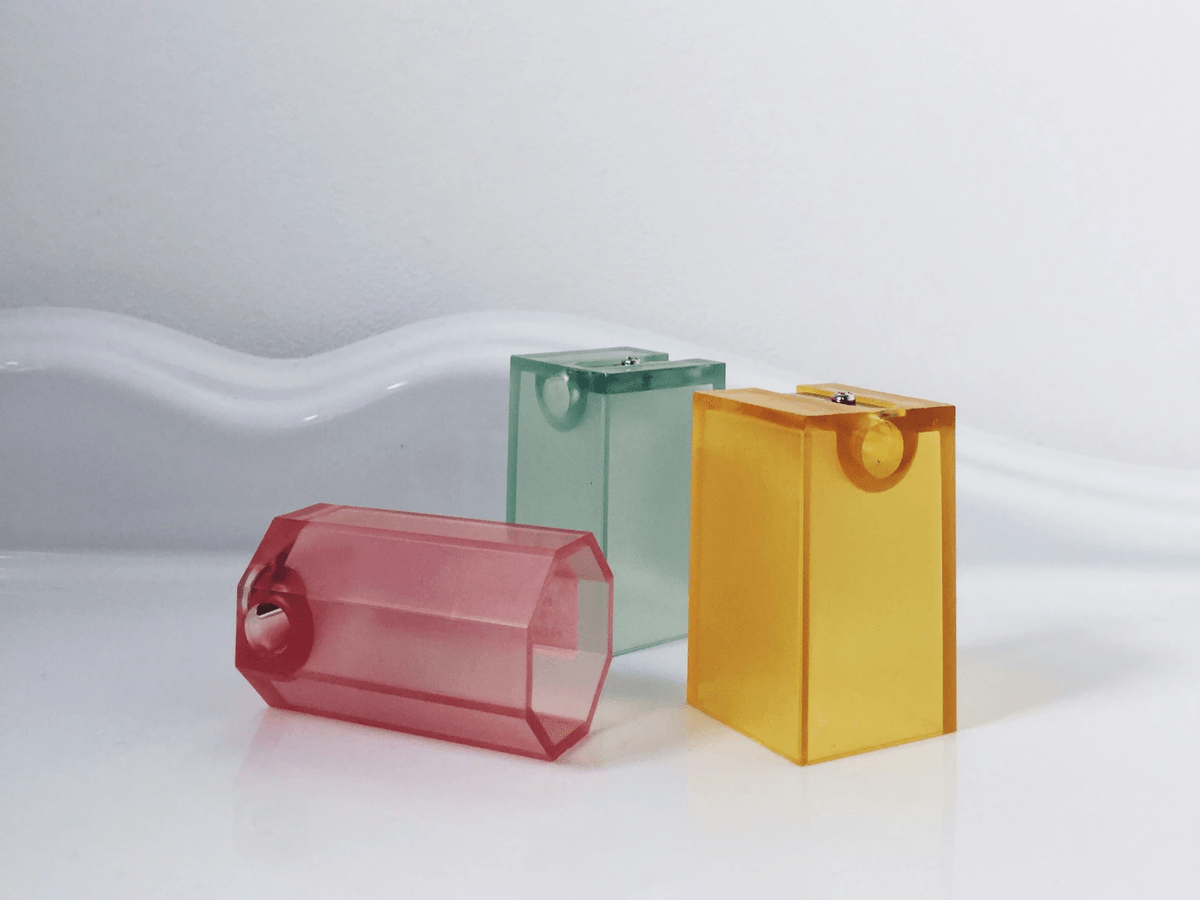
PPE injection molding is revolutionizing the way plastic components are produced across various industries. With its ability to create complex shapes and designs, injection molding has become a preferred method for manufacturers looking to enhance efficiency and reduce waste. Let's dive deeper into the fundamentals of this process, why PPE is a go-to material, and its wide-ranging applications.
Basics of Injection Molding
At its core, injection molding involves injecting molten material into a mold to create solid parts. This process is particularly popular in plastic injection molding, where various types of injection moldable plastics are used to produce everything from small components to large structural parts. The key advantage of this method lies in its ability to produce high volumes of identical items with minimal waste, making it an efficient choice for manufacturers.
The machinery involved in mould injection moulding typically includes an injection unit and a clamping unit that work together seamlessly. The molten plastic is injected under high pressure into the mold cavity, where it cools and solidifies into the desired shape. Once cooled, the mold opens, and the finished part can be ejected—ready for inspection or further processing.
Why Choose PPE for Your Molding Needs
PPE (Polyphenylene Ether) stands out as an excellent choice for your molding needs due to its unique properties. This thermoplastic material offers superior strength, dimensional stability, and resistance to heat and chemicals compared to other plastics commonly used in injection molding. Additionally, PPE's lightweight nature makes it ideal for applications where reducing weight is crucial without compromising durability.
One significant advantage of using PPE in plastic injection molding lies in its versatility; it can be easily processed using standard equipment designed for other thermoplastics while maintaining exceptional performance characteristics. Furthermore, with proper molding inspection techniques during production, manufacturers can ensure that each piece meets stringent quality standards—ultimately leading to fewer defects and higher customer satisfaction.
Choosing PPE also allows companies to innovate their product designs without worrying about material limitations commonly associated with traditional plastics. Its compatibility with various additives enhances functionality while providing opportunities for customization through color or texture variations during the moulding process.
Applications of PPE in Various Industries
PPE finds its way into numerous industries due to its remarkable properties that cater specifically to industry needs. In automotive manufacturing, for instance, it’s often used in components such as electrical connectors and housing parts that require both durability and resistance against harsh environments like heat or chemicals found under the hood of vehicles.
In electronics, PPE's insulating properties make it an ideal choice for producing housings and components that need reliable protection against electrical interference while maintaining lightweight characteristics essential for portable devices. Moreover, medical device manufacturers appreciate how easy it is to clean and sterilize products made from this versatile material—making PPE a top pick when safety standards are paramount.
Beyond these sectors, you will find applications ranging from consumer goods packaging to industrial equipment components—all benefiting from the strength and reliability provided by ppe injection molding processes coupled with effective molding inspection practices ensuring product integrity at every stage of production.
The Process of Mould Injection Moulding
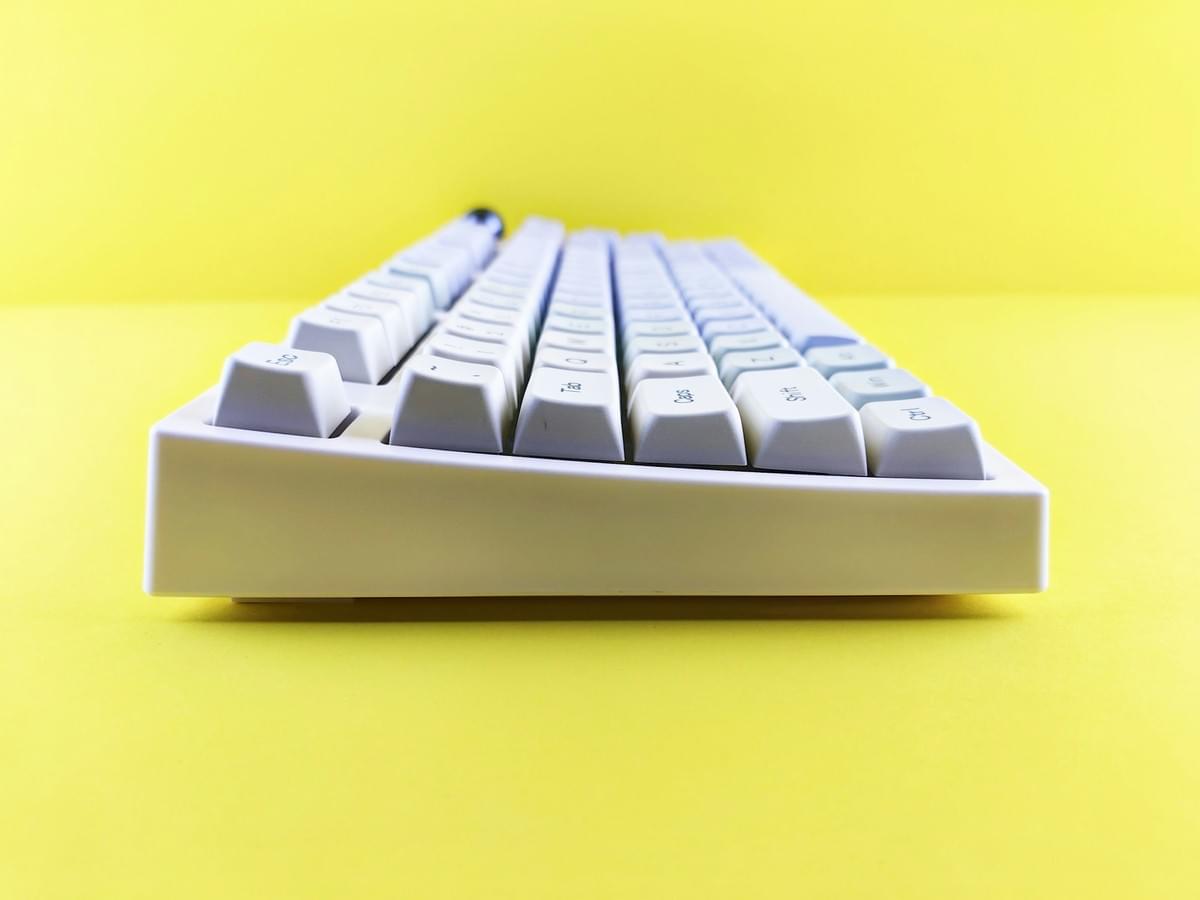
Mould injection moulding is a fascinating blend of science and artistry, transforming raw materials into functional products through a highly controlled process. At the heart of this operation lies an array of specialized equipment and advanced technology designed to ensure precision and efficiency in production. Understanding the intricacies of this process, from equipment to key considerations, is essential for anyone looking to dive into the world of PPE injection molding.
Equipment and Technology Used
The backbone of any successful injection molding operation is its equipment, which includes injection molding machines, molds, and auxiliary tools. These machines utilize hydraulic or electric power to inject molten plastic into precisely engineered molds that shape the final product. Additionally, advancements in technology have led to smarter control systems that enhance monitoring during production, ensuring that every aspect of the mould injection moulding process meets stringent quality standards.
In the realm of PPE injection molding specifically, using high-quality plastic injection molding molds is crucial for creating durable products that can withstand rigorous applications across various industries. The choice of machinery also plays a significant role; modern electric machines offer energy efficiency while providing consistent results compared to traditional hydraulic models. Embracing innovative technologies not only streamlines production but also allows for greater flexibility when working with different types of injection moldable plastics.
Steps in the Injection Molding Process
The journey from concept to finished product in plastic injection molding involves several carefully orchestrated steps. It begins with material preparation where resin pellets are dried and prepped before being fed into the machine's hopper. Once heated until they reach a molten state, these materials are injected under high pressure into a closed mold cavity where they cool and solidify into their desired shape.
Following cooling comes ejection—the moment when your molded part emerges triumphantly from its confines! This step requires precision; if not executed correctly during the mould injection moulding process, it could lead to defects or damage to both the product and mold itself. Finally, post-processing techniques such as trimming or surface finishing may be employed before inspection takes place—ensuring each piece meets quality standards through thorough molding inspection.
Key Considerations for Successful Production
Success in PPE injection molding hinges on several critical factors that can significantly impact production outcomes. First among these is material selection; choosing appropriate plastic types tailored for specific applications ensures optimal performance and durability in end products made from plastic injection molding processes. Additionally, maintaining precise temperature control throughout each phase helps avoid common pitfalls like warping or incomplete filling.
Another vital consideration is mold design; effective designs not only facilitate efficient material flow but also ease ejection processes post-cooling—a must-have for smooth operations! Regular maintenance checks on equipment further enhance reliability while minimizing downtime during production runs—keeping your output steady and predictable over time without sacrificing quality due to unforeseen breakdowns or inefficiencies in manufacturing methods like mould injection moulding.
Importance of Molding Inspection
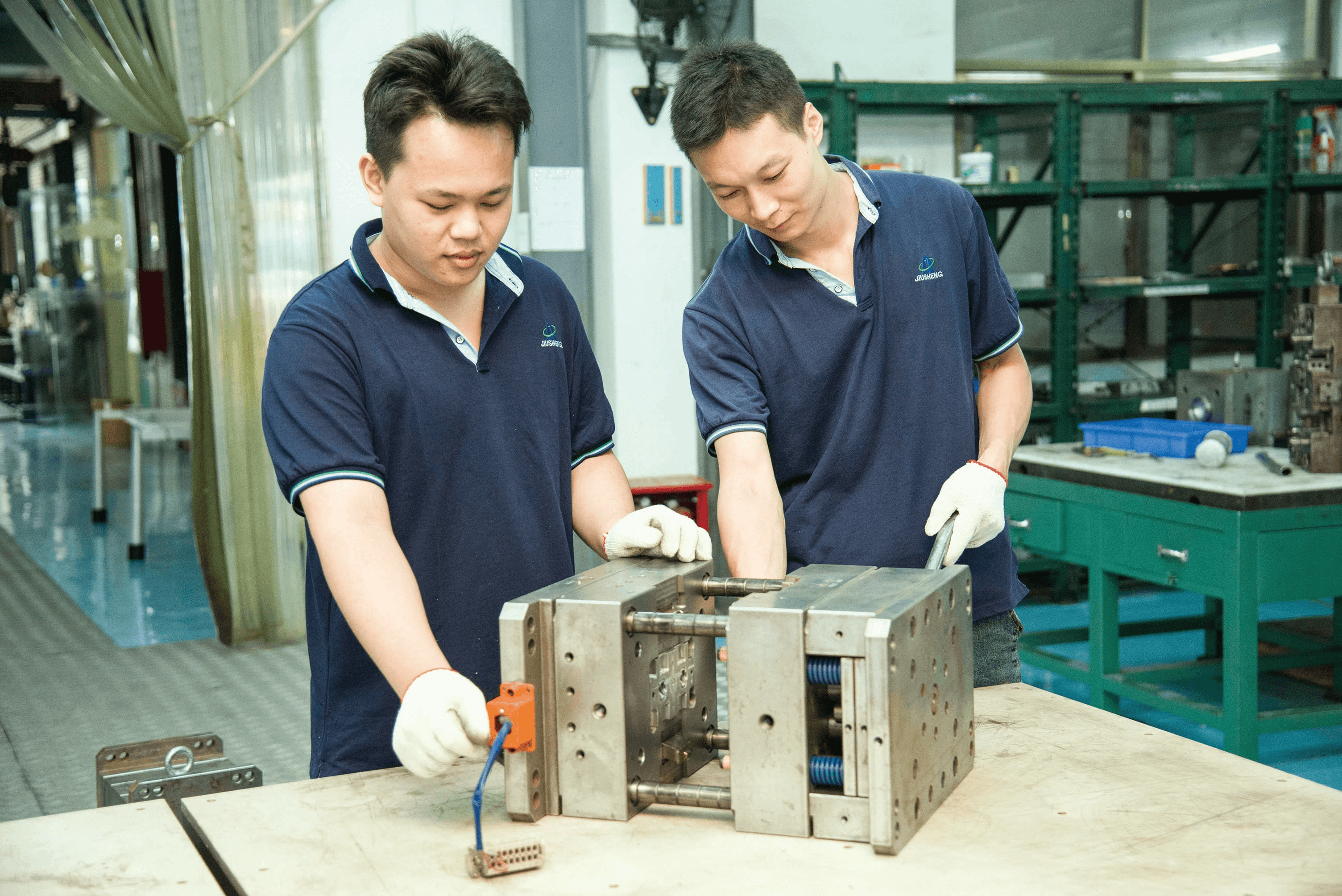
In the world of PPE injection molding, ensuring quality is paramount. Molding inspection serves as a critical checkpoint in the production process, helping to identify defects early and maintain high standards. With the right inspection techniques in place, manufacturers can enhance their product reliability while reducing waste and rework.
Ensuring Quality in Injection Molding
Quality assurance in injection molding is not just a luxury; it’s a necessity. By implementing rigorous molding inspection protocols, manufacturers can catch issues such as inconsistencies or material flaws before they escalate into larger problems. This proactive approach ensures that every batch of plastic injection molding products meets the required specifications and customer expectations.
Moreover, when using injection moldable plastics like PPE, maintaining quality becomes even more crucial due to the specific applications these materials serve. For instance, any defect in a molded component used for medical applications could have serious consequences. Therefore, effective molding inspection processes are essential for safeguarding both product integrity and consumer safety.
Techniques for Effective Molding Inspection
There are various techniques employed to ensure effective molding inspection throughout the injection molding process. Visual inspections are often the first line of defense against defects; trained personnel examine molded products for surface imperfections or dimensional inaccuracies. Advanced methods such as ultrasonic testing or X-ray imaging can also be utilized to detect internal flaws that may not be visible externally.
In addition to these techniques, automated inspection systems equipped with cameras and sensors can significantly enhance efficiency and accuracy in monitoring production quality. These systems provide real-time feedback on mold performance and product consistency, allowing quick adjustments if needed. By integrating both traditional and modern inspection methods, manufacturers can ensure their plastic injection molding processes yield high-quality results consistently.
How Inspection Impacts Production Efficiency
The impact of thorough molding inspection on production efficiency cannot be overstated. When defects are identified early through effective inspections, costly delays associated with rework or scrap reduction are minimized—saving time and resources during production cycles. Furthermore, consistent quality leads to improved customer satisfaction rates since clients receive products that meet their specifications without unpleasant surprises.
Additionally, regular inspections foster a culture of continuous improvement within manufacturing teams by identifying recurring issues that need addressing—be it equipment malfunctions or material inconsistencies related to certain types of mould injection moulding processes like those involving PPE materials specifically designed for durability and safety purposes. Ultimately, investing time in comprehensive molding inspections not only boosts efficiency but also enhances overall business reputation within competitive markets.
Advantages of Plastic Injection Molding
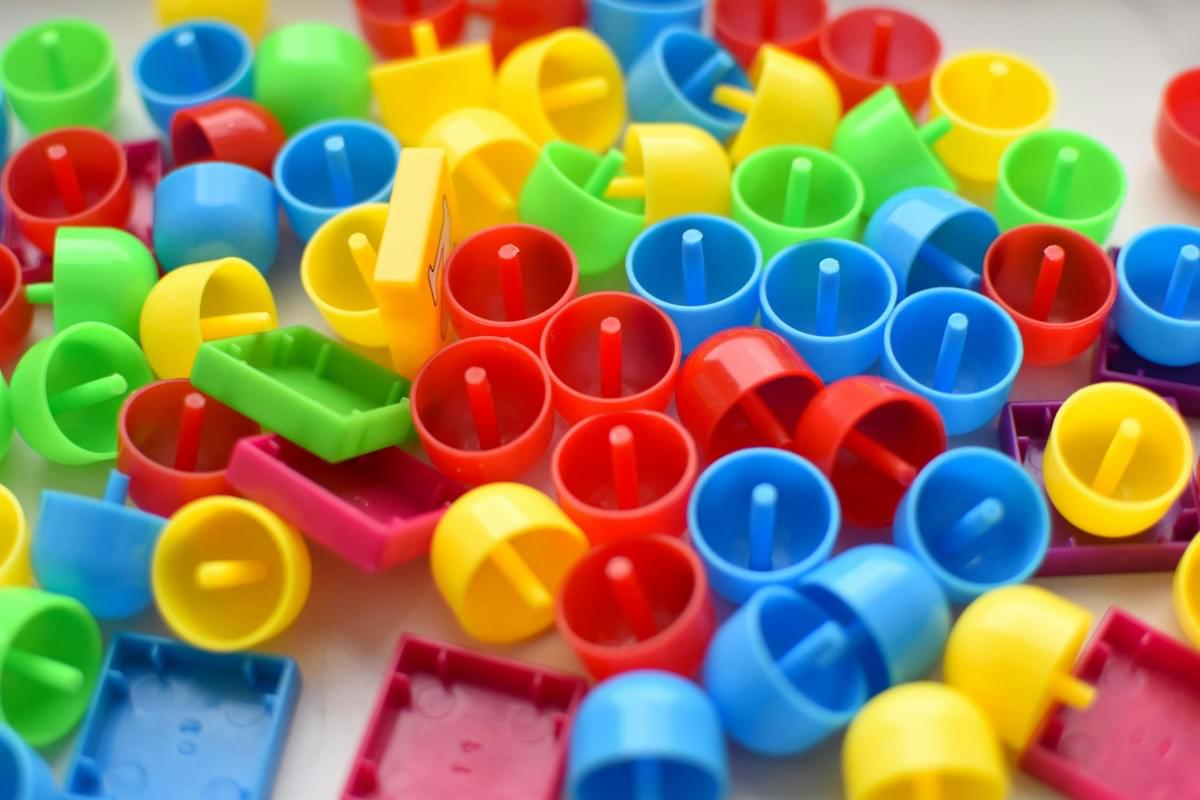
Plastic injection molding has revolutionized manufacturing, offering a plethora of advantages that make it a go-to choice for many industries. Among these benefits are cost-effectiveness, flexibility in design, and the strength and durability of molded products. As businesses increasingly turn to PPE injection molding, understanding these advantages can help them optimize their production processes.
Cost-Effectiveness in Production
One of the most significant advantages of plastic injection molding is its cost-effectiveness in production. The initial setup costs for mold creation can be high, but once established, the process allows for mass production at a lower cost per unit. This efficiency is particularly beneficial when using injection moldable plastics like PPE, as it reduces waste and maximizes output.
Additionally, the speed of production means that companies can respond quickly to market demands without incurring excessive costs. By minimizing labor costs through automation and streamlining the manufacturing process, businesses can allocate resources more effectively. Ultimately, this results in higher profit margins while maintaining quality standards through rigorous molding inspection.
Flexibility and Customization Options
Plastic injection molding offers remarkable flexibility and customization options that cater to diverse industry needs. With advanced technology available for mould injection moulding, manufacturers can create intricate designs tailored to specific applications or client requirements. This adaptability makes it easy to switch between different projects or modify existing designs without significant downtime.
Moreover, the ability to use various types of mold plastic injection allows manufacturers to experiment with colors, textures, and finishes while ensuring product integrity remains intact. Whether producing single-color items or complex double-color products, customization becomes seamless with efficient planning and execution. This versatility not only enhances product appeal but also sets brands apart in competitive markets.
Strength and Durability of Moulded Products
The strength and durability offered by products made through plastic injection molding cannot be overstated. Utilizing high-quality materials such as PPE ensures that molded items withstand wear and tear over time while maintaining their structural integrity. This durability is crucial across industries where reliability is paramount—think automotive parts or medical devices where failure is not an option.
Additionally, proper molding inspection during the production process guarantees that each item meets stringent quality standards before reaching consumers or clients. By investing in strong materials combined with meticulous inspection techniques, businesses can produce items that stand up against rigorous usage conditions without compromising performance or safety standards. In essence, choosing plastic injection molding translates into long-lasting solutions that resonate well with both manufacturers and end-users alike.
Baoyuan’s Expertise in Injection Molding
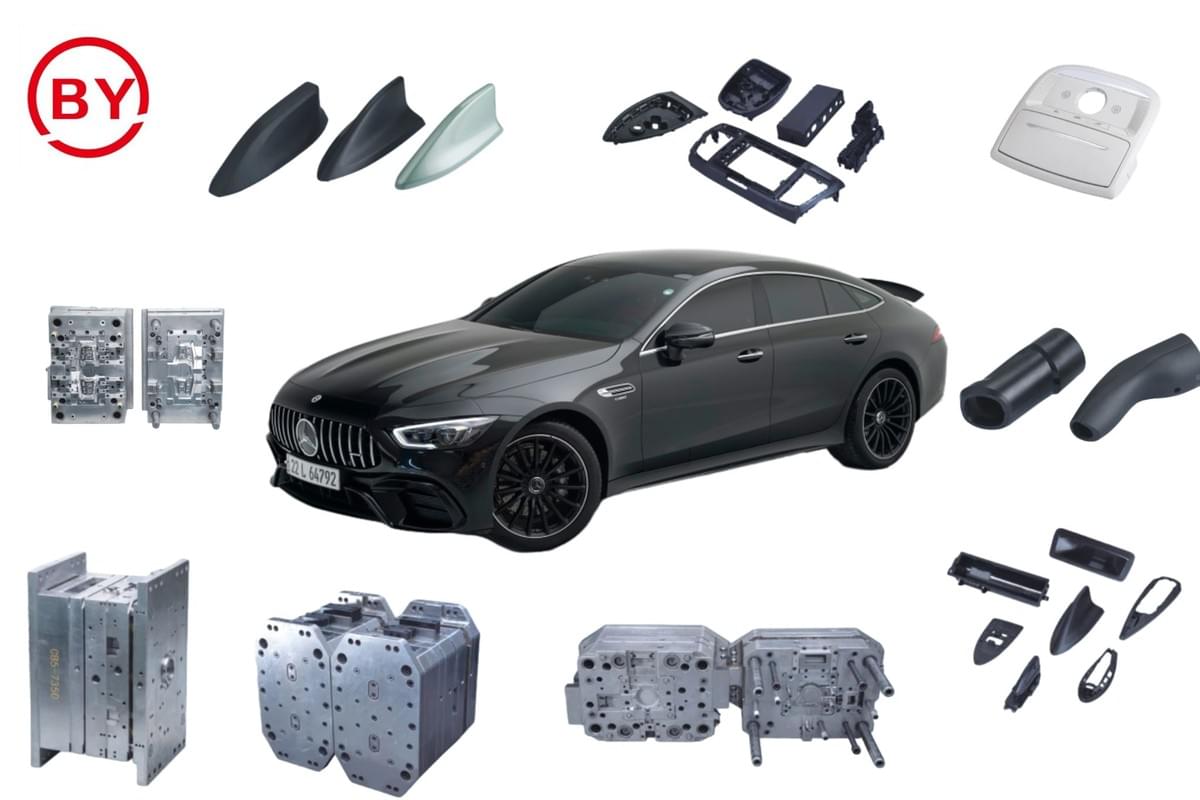
In the competitive landscape of injection molding, Baoyuan stands out as a beacon of innovation and quality. With a focus on PPE injection molding, the company harnesses cutting-edge technology to deliver products that meet diverse industry needs. Their commitment to excellence ensures that every aspect of the molding process is optimized for performance and reliability.
Innovative Solutions from the Baoyuan Team
The Baoyuan team prides itself on developing innovative solutions tailored to the unique challenges of plastic injection molding. By integrating advanced techniques in mould injection moulding, they create products that not only meet but exceed client expectations. Their approach combines creativity with technical expertise, resulting in efficient production processes and high-quality outcomes.
Moreover, Baoyuan's dedication to research and development means they are constantly exploring new materials and methods in injection moldable plastics. This forward-thinking mindset allows them to offer custom solutions that cater specifically to various applications across industries. From concept to completion, their innovative spirit drives improvements in efficiency and product performance.
Quality Assurance in Single-Color and Double-Color Products
Quality assurance is paramount at Baoyuan, especially when it comes to single-color and double-color products produced through plastic injection molding. The company employs rigorous molding inspection protocols at every stage of production, ensuring that all items meet stringent quality standards before reaching clients. This attention to detail not only enhances product integrity but also builds trust with customers who rely on consistent quality.
Baoyuan's expertise extends beyond traditional methods; they utilize advanced technologies for precise monitoring during the mould injection moulding process. This proactive approach helps identify potential issues early on, allowing for timely interventions that minimize waste and maximize efficiency. As a result, clients benefit from durable products designed for longevity without compromising on aesthetics or functionality.
Furthermore, by specializing in both single-color and double-color options, Baoyuan caters to a wide range of design preferences while maintaining high quality across all products. Their ability to balance complexity with reliability sets them apart as leaders in the field of plastic injection molding.
Utilizing Technology for Superior Mold Production
At Baoyuan, technology is at the heart of superior mold production processes used in PPE injection molding applications. The company invests heavily in state-of-the-art equipment designed specifically for precision and efficiency during the plastic injection molding process. By incorporating automation and smart manufacturing techniques into their workflow, they ensure consistent results while reducing lead times significantly.
In addition to modern machinery, Baoyuan employs sophisticated software tools for design simulation and mold flow analysis during production planning stages. These technologies enable them to predict potential challenges early on within the mould injection moulding cycle—ultimately leading to better decision-making throughout project execution. Such foresight minimizes downtime while maximizing overall productivity.
Baoyuan’s commitment doesn’t stop at just equipment; it extends into continuous training programs for their workforce as well—ensuring everyone is equipped with up-to-date knowledge about emerging trends related specifically towards mold plastic injection advancements within this dynamic industry landscape.
Conclusion
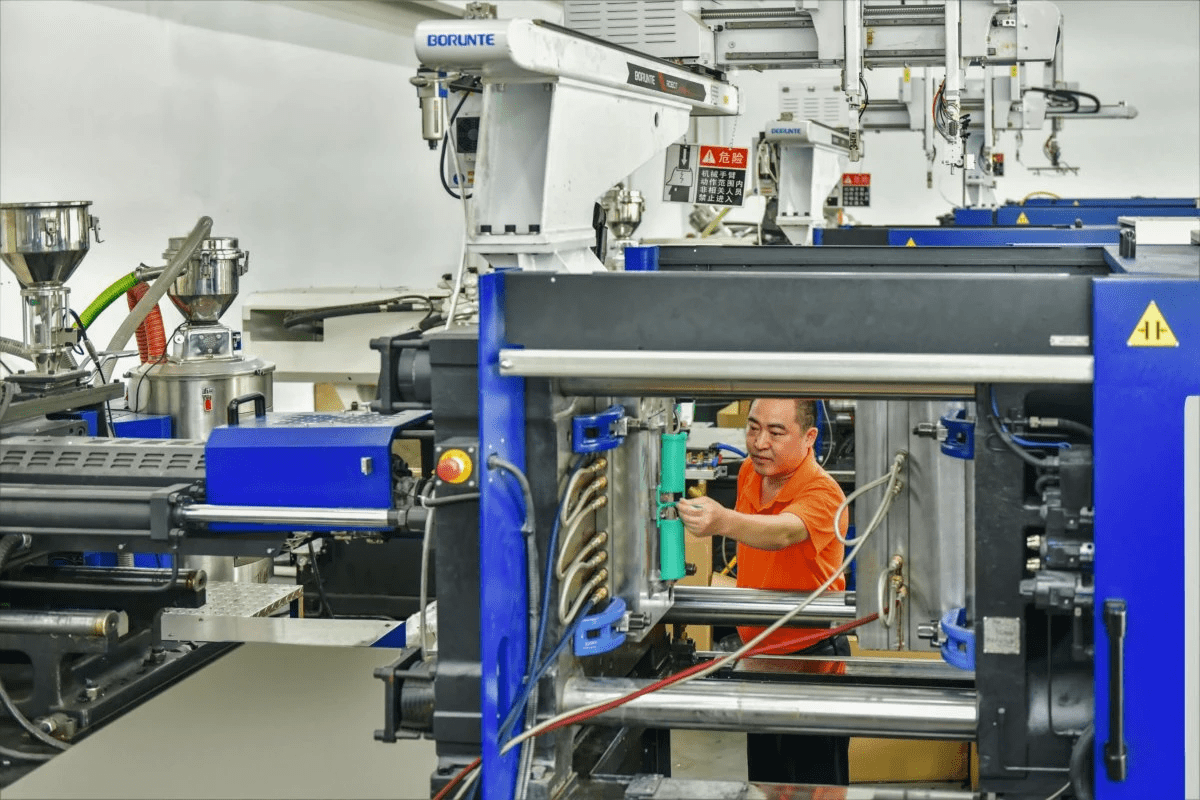
In conclusion, the landscape of PPE injection molding is evolving rapidly, driven by advancements in technology and an increasing demand for quality and efficiency. As industries continue to embrace the benefits of injection molding, particularly with materials like PPE, the future looks promising for both manufacturers and consumers alike. With a focus on innovation and sustainability, the potential applications of plastic injection molding are boundless.
Future of PPE Injection Molding
The future of PPE injection molding is poised for significant growth as industries recognize its advantages in producing durable and lightweight products. The trend towards sustainable practices will also influence how injection moldable plastics are developed, pushing for more eco-friendly materials without sacrificing performance. Furthermore, advancements in molding inspection techniques will ensure that quality remains paramount as production scales up.
Strategies for Maximizing Production Efficiency
To maximize production efficiency in mould injection moulding processes, companies should invest in state-of-the-art equipment that minimizes downtime and maximizes output. Implementing rigorous molding inspection protocols can help identify defects early on, reducing waste and ensuring that only high-quality products reach the market. Additionally, fostering a culture of continuous improvement among staff can lead to innovative solutions that enhance overall productivity.
Choosing the Right Partner for Molding Solutions
Selecting the right partner for your plastic injection molding needs is crucial to achieving optimal results. Look for a company with proven expertise in handling various types of injection moldable plastics while maintaining stringent quality control through effective molding inspection techniques. A reliable partner will not only understand your specific requirements but also offer customized solutions that align with your production goals.