Introduction
Polypropylene has carved out a significant niche in today's materials landscape, becoming a go-to choice for various industries. As we delve into the world of polypropylene material, it’s essential to recognize its unique properties and versatility. From automotive components to consumer goods, the applications of polypropylene are vast and continually evolving.
Understanding Polypropylene's Role Today
In recent years, polypropylene has emerged as a star player in the realm of plastics, thanks in part to its impressive properties such as lightweight durability and resistance to chemicals. This versatile polymer is not only cost-effective but also adaptable, making it suitable for an array of applications across different sectors. The growing demand for sustainable materials has further elevated the profile of polypropylene uses, as manufacturers seek eco-friendly alternatives without sacrificing performance.
Exploring Polypropylene's Popular Applications
The scope of polypropylene applications is extensive; from packaging solutions that ensure product longevity to automotive parts designed for efficiency and safety, this material is everywhere! Its lightweight nature makes it an ideal candidate for reducing vehicle weight while enhancing fuel efficiency in the automotive industry. Additionally, the consumer goods sector benefits from injection molded polypropylene products that combine functionality with aesthetic appeal.
The Rise of Injection Molding Techniques
Injection molding has revolutionized how we produce items using polypropylene material, allowing for intricate designs and high-volume manufacturing with minimal waste. This technique enables manufacturers to create complex shapes that would be difficult or impossible to achieve through traditional methods. Furthermore, injection molding products made from polypropylene exhibit superior strength and durability, making them a preferred choice in many industries today.
The Basics of Polypropylene
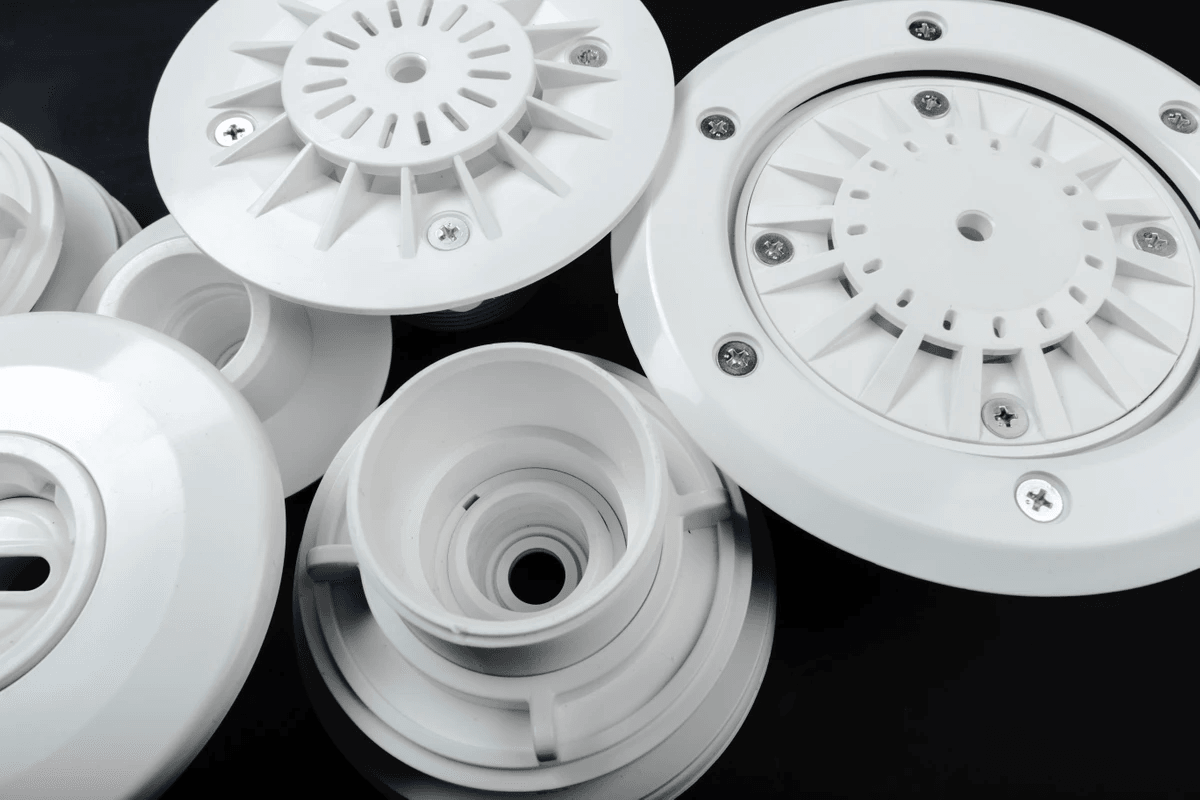
Polypropylene is a widely used thermoplastic polymer that has become a staple in various industries due to its versatility and adaptability. This remarkable material, often referred to as PP, is known for its lightweight nature and impressive strength, making it ideal for a plethora of applications. In the realm of manufacturing, injection molded polypropylene stands out as a preferred method for creating complex shapes and designs.
What is Polypropylene Material?
Polypropylene material is a synthetic resin made from the polymerization of propylene monomers. As one of the most commonly produced plastics globally, polypropylene boasts a unique combination of properties that make it suitable for diverse applications. From packaging to automotive components, this versatile polymer can be found everywhere, showcasing its importance in modern manufacturing.
Key Properties of Polypropylene
The key properties of polypropylene include its excellent chemical resistance, low density, and high melting point compared to other plastics like polyethylene. These characteristics make injection molded polypropylene an ideal choice for products that require durability under stress or exposure to chemicals. Additionally, polypropylene's inherent flexibility allows it to be molded into intricate designs without compromising structural integrity.
Overview of Polypropylene Uses in Industry
Polypropylene uses span across multiple sectors including automotive, consumer goods, and packaging solutions. In the automotive industry, injection molded polypropylene components are utilized for everything from interior trim to battery cases due to their lightweight yet sturdy nature. Meanwhile, in packaging applications, this material provides an effective barrier against moisture and contaminants while being cost-effective—a win-win situation for manufacturers looking to optimize performance without breaking the bank.
Injection Molded Polypropylene: The Process
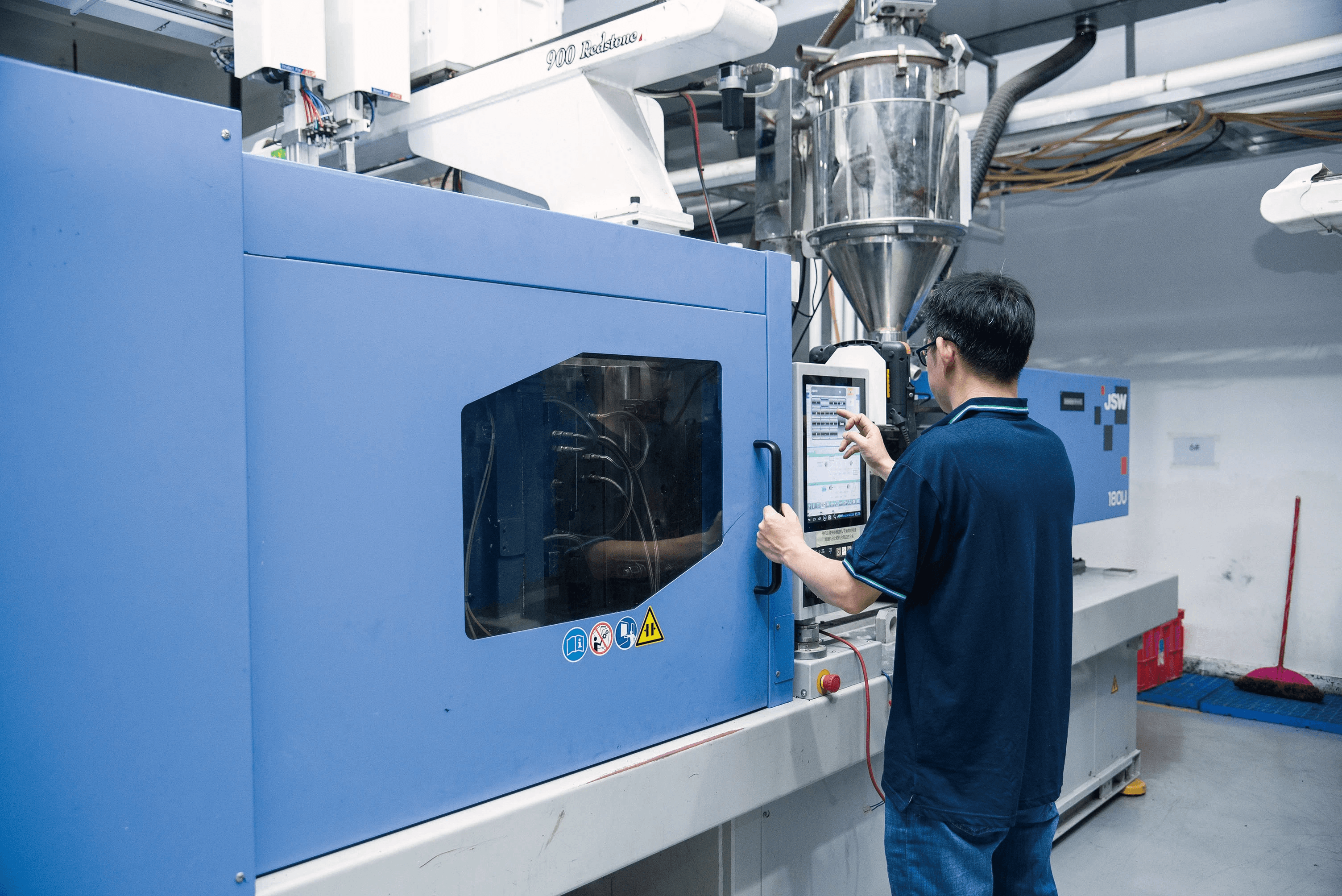
Injection molded polypropylene is a game-changer in the world of manufacturing, offering versatility and efficiency that many other materials simply can't match. This process allows for the creation of complex shapes and designs that are both durable and lightweight, making it a go-to choice for various industries. With its unique properties, polypropylene material has found its way into countless applications, revolutionizing how products are made.
Steps Involved in Injection Molding
The journey of injection molded polypropylene begins with the careful preparation of the raw material, where polypropylene pellets are fed into a heated barrel. Here, they undergo melting before being injected into a precisely designed mold under high pressure. Once cooled and solidified, the mold opens to reveal your finished product—a perfect blend of efficiency and quality thanks to the intricate steps involved in polypropylene injection molding.
This meticulous process not only ensures consistency but also maximizes production rates, making it ideal for high-volume manufacturing scenarios. Each step—from heating to cooling—plays a crucial role in preserving the unique polypropylene properties that make it so desirable across various sectors. As industries continue to innovate, mastering these steps will be essential for producing cutting-edge injection molding products.
Advantages of Injection Molding Products
One of the standout advantages of using injection molded polypropylene is its incredible design flexibility; manufacturers can create intricate shapes that would be difficult or impossible with other methods like blow molding or extrusion. Additionally, this technique allows for rapid production cycles, which means businesses can meet market demands more swiftly while maintaining high-quality standards in their polypropylene applications. The strength-to-weight ratio offered by this material is another benefit; lightweight yet robust products can lead to cost savings in transportation and handling.
Moreover, injection molding minimizes waste during production since excess material can often be reused or recycled within the process itself—an important consideration given today’s focus on sustainability. This aspect aligns well with growing consumer preferences for environmentally friendly products while still delivering on performance expectations associated with traditional materials like pp polyethylene. With all these advantages combined, it's no wonder that many industries are leaning towards injection molded products.
Comparing Injection Molding and Other Techniques
When comparing injection molding to other manufacturing techniques such as blow molding or rotational molding, several factors come into play regarding efficiency and output quality. While blow molding might excel at producing hollow objects like bottles from polyethylene materials, it lacks the precision that comes with injection molded polypropylene parts—especially when complex geometries are involved. On the other hand, rotational molding offers excellent versatility but often at lower production rates compared to what you can achieve through efficient injection processes.
Cost-effectiveness also plays a significant role in this comparison; although initial setup costs may be higher for injection molds due to their complexity and precision requirements, they ultimately provide better returns on investment through faster cycle times and reduced waste over time compared to alternative methods like extrusion for certain applications. In summary, while each technique has its merits depending on specific needs or situations within industry sectors utilizing different types of plastics—including pp polyethylene—the advantages offered by injection molded polypropylene make it hard to beat when looking at overall performance and adaptability across various applications.
Polypropylene Applications Across Industries
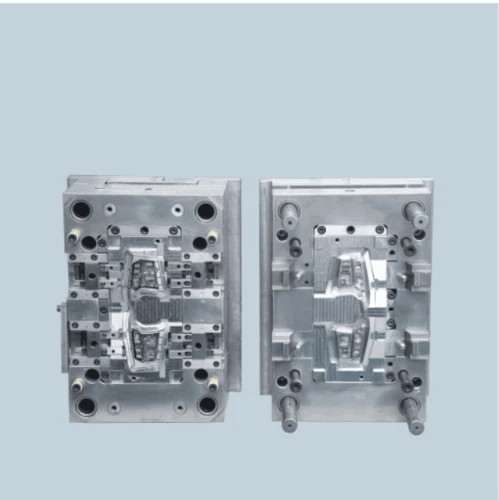
Polypropylene is a versatile material that has carved out significant niches across various industries, showcasing its adaptability and utility. From automotive innovations to packaging solutions and consumer goods, the applications of polypropylene are as diverse as they are impactful. This section delves into how injection molded polypropylene is revolutionizing these sectors and enhancing product performance.
Automotive Industry Innovations
The automotive industry has embraced injection molded polypropylene for its lightweight yet durable properties, which contribute significantly to fuel efficiency and vehicle performance. Polypropylene material is used in a variety of components, from interior trims to under-the-hood parts, thanks to its excellent resistance to heat and chemicals. With the rising demand for electric vehicles, manufacturers are increasingly turning to polypropylene uses that support sustainability while maintaining high standards of safety.
Moreover, the flexibility afforded by polypropylene injection molding allows for intricate designs that can be tailored for specific vehicle models. This adaptability means that manufacturers can create parts that not only meet functional requirements but also enhance aesthetic appeal. As the automotive sector continues to innovate, the role of injection molded polypropylene will only become more critical in driving advancements.
Packaging Solutions with Polypropylene
In the realm of packaging, polypropylene stands out due to its strength-to-weight ratio and moisture resistance, making it an ideal choice for various applications. From food containers to industrial packaging solutions, injection molded polypropylene products are designed to keep contents safe while minimizing environmental impact through recyclability. The lightweight nature of this material helps reduce shipping costs and carbon footprints—an essential consideration in today's eco-conscious market.
Additionally, brands appreciate how polypropylene properties allow for vibrant printing options on packaging materials without compromising durability or quality. This enhances brand visibility while ensuring products remain securely packaged during transit and storage. As companies strive for sustainable practices, the shift towards using more recyclable materials like polypropylene will continue shaping packaging trends.
Consumer Goods Featuring Polypropylene
Consumer goods represent one of the most expansive fields where polypropylene applications shine brightly; from household items like containers and furniture to toys and personal care products—polypropylene is everywhere! The resilience offered by this material means it withstands daily wear-and-tear while remaining stylish and functional—a win-win scenario for consumers looking for longevity in their purchases. Moreover, many popular brands are now leveraging injection molded polypropylene designs that cater specifically to modern consumer preferences.
The versatility inherent in this polymer allows designers considerable freedom when creating innovative shapes and forms that appeal directly to consumers' tastes—think trendy kitchenware or sleek storage solutions! Additionally, with growing awareness about health safety standards in consumer products, using PP polyethylene ensures compliance with regulations while providing peace of mind regarding product safety. It’s clear why so many consumer goods rely on this adaptable material.
The Role of Technology in Polypropylene Molding
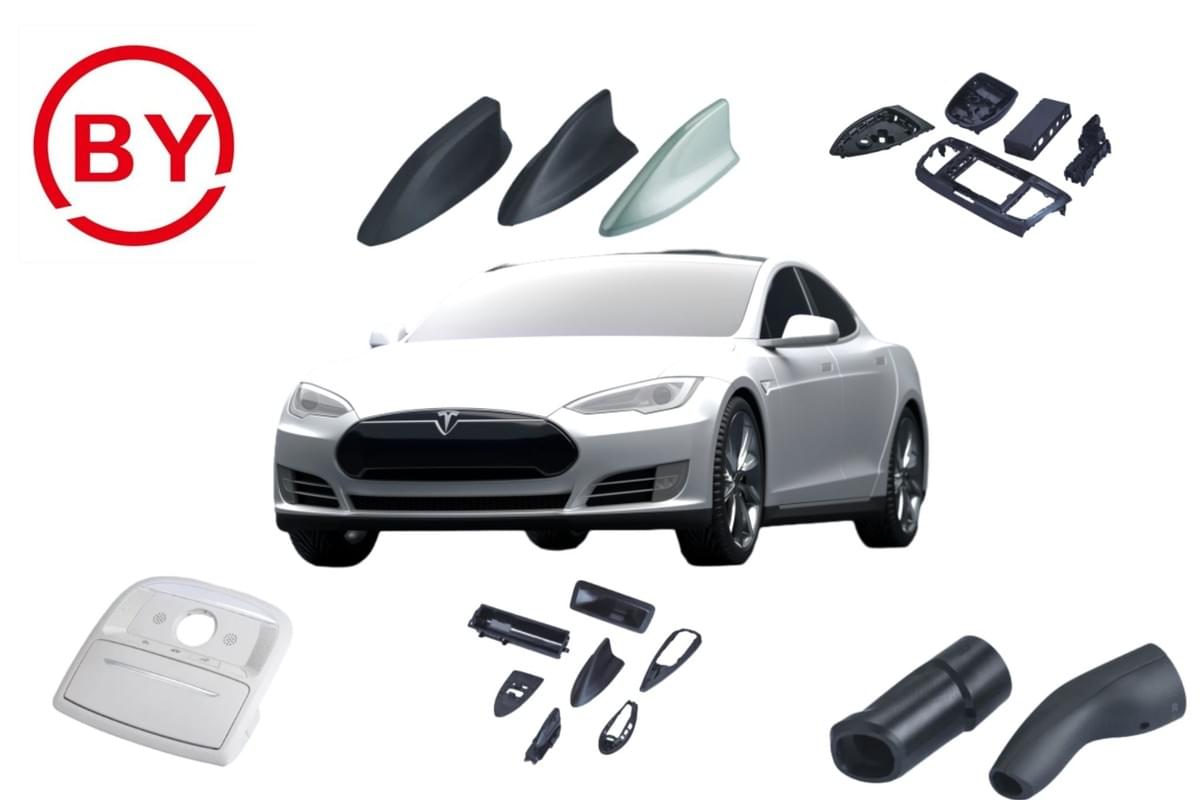
In the rapidly evolving world of manufacturing, technology plays a pivotal role in enhancing the efficiency and quality of injection molded polypropylene products. From sophisticated software that aids in mold design to stringent quality assurance processes, technological advancements have revolutionized how polypropylene material is utilized across various industries. This section delves into how these innovations shape the production landscape for polypropylene uses and applications.
Advanced Software for Mold Design
The design phase is crucial for creating efficient injection molding products, and advanced software has transformed this process dramatically. Programs equipped with 3D modeling capabilities allow engineers to visualize and optimize mold designs before production begins, ensuring that every detail aligns with desired polypropylene properties. By utilizing simulation tools, manufacturers can predict how the polypropylene material will behave during molding, reducing errors and waste while maximizing efficiency.
These design technologies not only streamline the creation of molds but also enhance collaboration among teams, allowing for real-time adjustments based on feedback or testing results. As a result, companies can produce more complex shapes and designs for their injection molded polypropylene applications without compromising on quality or performance. This integration of technology ensures that manufacturers remain competitive in a market where precision and innovation are paramount.
Quality Assurance in Polypropylene Production
Advanced inspection technologies such as automated vision systems are employed to monitor product consistency throughout the production process, ensuring that each batch meets stringent industry standards. These systems analyze various aspects of finished goods—from dimensional accuracy to surface finish—allowing manufacturers to catch defects early on.
Moreover, continuous monitoring helps maintain optimal conditions during the molding process by analyzing temperature fluctuations and pressure levels within machines designed for polyethylene or other materials. This level of scrutiny not only enhances the durability of polypropylene applications but also builds consumer trust in products made from this versatile material. Ultimately, robust quality assurance practices lead to greater customer satisfaction and reduced costs associated with rework or recalls.
Baoyuan's Expertise in Injection Molding
Baoyuan stands out as a leader in injection molding expertise, particularly when it comes to leveraging cutting-edge technology for superior production outcomes. With years of experience specializing in injection molded polypropylene solutions, Baoyuan has honed its processes to maximize efficiency while delivering high-quality products tailored to client specifications. Their commitment to innovation means they routinely adopt new technologies that enhance both mold design and production capabilities.
By prioritizing research and development alongside practical application techniques, Baoyuan ensures its clients benefit from state-of-the-art machinery combined with expert knowledge about polypropylene properties and uses across different sectors. The company's reputation is built on its ability to produce reliable injection molding products that meet diverse industry needs—from automotive components to consumer goods—demonstrating their versatility within the realm of polypropylene applications.
Environmental Considerations and Future Trends
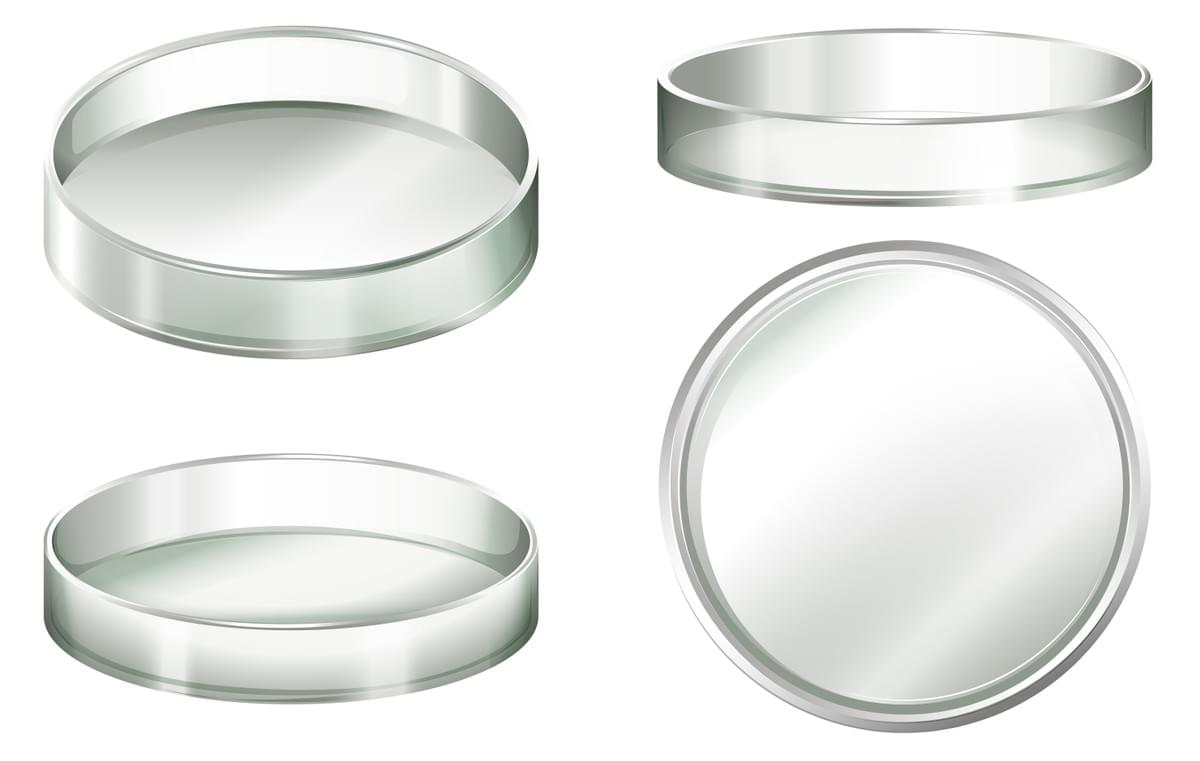
As the world becomes increasingly aware of environmental issues, the sustainability of materials like polypropylene has come under scrutiny. Polypropylene material is often touted for its versatility and durability, but its environmental footprint is a growing concern. Understanding how injection molded polypropylene fits into the sustainability landscape is crucial for both manufacturers and consumers alike.
Sustainability of Polypropylene Material
Polypropylene is known for its lightweight nature and resistance to chemical degradation, making it a popular choice in various industries. However, the sustainability of polypropylene material goes beyond just its properties; it also depends on how it’s produced and disposed of. With advancements in production techniques, there are now more eco-friendly methods to create injection molded polypropylene products that minimize energy consumption and waste.
Moreover, many manufacturers are now focusing on reducing their carbon footprint by utilizing recycled materials in their production processes. This not only helps in conserving resources but also promotes a circular economy where polypropylene uses extend beyond initial applications. As consumers become more environmentally conscious, companies producing injection molding products from sustainable sources will likely gain a competitive edge.
Recyclability and Life Cycle of Polypropylene Products
The challenge remains that many consumers are not fully aware of how to properly recycle these products, leading to increased landfill waste. Educating the public about proper disposal methods can enhance the recyclability rates of polypropylene applications significantly. Additionally, innovations such as chemical recycling technologies promise even greater potential for recovering valuable polymers from discarded items.
Innovations on the Horizon in Polypropylene Applications
Looking ahead, there are numerous innovations on the horizon that could further enhance the appeal of injection molded polypropylene across various sectors. Researchers are exploring bio-based alternatives that maintain similar properties while reducing reliance on fossil fuels for production—opening doors for greener options without compromising quality or functionality. These developments could reshape how we view traditional pp polyethylene alongside more sustainable choices.
Furthermore, smart technologies integrated into manufacturing processes may improve efficiency and reduce waste associated with injection molding techniques. Enhanced monitoring systems can ensure quality assurance at every stage of production while minimizing environmental impact—a win-win scenario for both manufacturers and consumers alike! As these innovations unfold, they will likely redefine existing perceptions about polypropylene uses across industries.
Conclusion
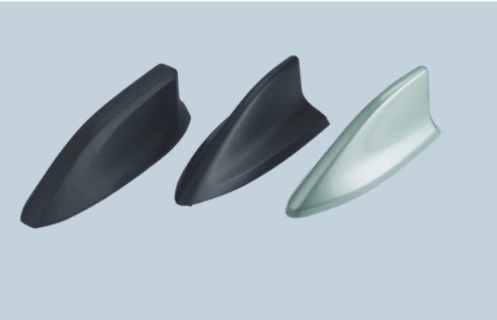
In conclusion, the versatility of polypropylene material is nothing short of remarkable. From its lightweight nature to its resistance to chemicals and moisture, polypropylene has established itself as a go-to choice across various industries. Its myriad of polypropylene applications—from automotive components to household goods—demonstrates how this polymer can meet diverse manufacturing needs while maintaining efficiency and cost-effectiveness.
The Versatility of Polypropylene Material
Polypropylene material stands out due to its unique properties, which include high tensile strength and flexibility. These characteristics make it an ideal candidate for a wide range of polypropylene uses, particularly in injection molded products where precision is key. Whether it's packaging solutions or automotive parts, the adaptability of polypropylene ensures that it can be tailored to meet specific requirements without compromising on quality.
Future Prospects for Injection Molding
The future prospects for injection molding are bright, especially with advancements in technology that enhance the efficiency and precision of creating injection molded polypropylene products. As industries continue to innovate, we can expect new applications that leverage the inherent properties of polypropylene material, leading to smarter designs and more sustainable practices. Moreover, as manufacturers embrace automation and advanced techniques like 3D printing alongside traditional methods, the landscape for injection molding will undoubtedly evolve.
Why Choose Injection Molded Polypropylene?
Choosing injection molded polypropylene comes with a host of benefits that cater to both manufacturers and end-users alike. The combination of cost-effectiveness, durability, and design flexibility makes it an attractive option for producing high-quality products at scale. Additionally, with increasing emphasis on sustainability in manufacturing processes, opting for injection molded polypropylene aligns well with eco-friendly initiatives while still delivering exceptional performance across various applications.