Introduction

Polypropylene injection moulding is a crucial process in manufacturing various products. Understanding the intricacies of this process is essential for achieving high-quality results. Baoyuan's expertise in injection moulding makes them a reliable partner for your polypropylene moulding needs. Let's delve into the basics of polypropylene injection moulding and uncover the key factors for success.
Understanding Polypropylene Injection Moulding
Polypropylene injection molding process involves melting polypropylene material and injecting it into a mold to create a specific shape. This versatile material is widely used in industries due to its excellent properties, making it an ideal choice for various applications.
Baoyuan's Expertise in Injection Moulding
Baoyuan has established itself as a leader in the field of injection moulding, with a deep understanding of polypropylene injection molding parameters and processes. Their commitment to excellence and precision sets them apart, ensuring that every project meets the highest standards.
The Basics of Polypropylene Injection Moulding
The success of polypropylene injection moulding hinges on optimizing parameters such as temperature, pressure, and material selection. Achieving consistent quality requires careful attention to detail at every stage of the process, from mold design to quality assurance.
Choosing the Right Polypropylene Material
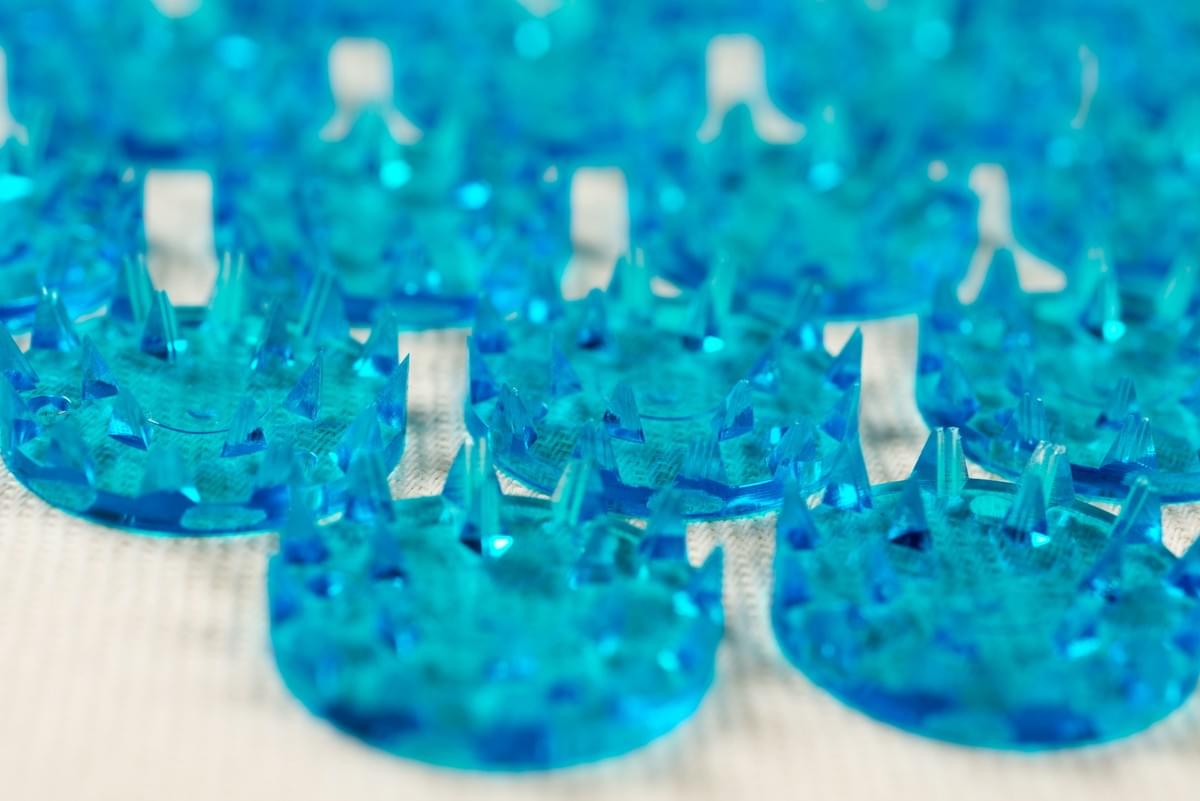
When selecting the right polypropylene material for injection moulding, it's crucial to consider factors such as melt flow rate, impact resistance, and chemical resistance. The material's flowability and shrinkage characteristics play a significant role in the injection molding process, affecting the final product's quality and dimensional accuracy.
Factors to Consider for Material Selection
Factors to consider when selecting polypropylene material for injection moulding include its thermal stability, impact strength, and resistance to chemicals and moisture. The material's flowability and ease of processing are also important considerations that can impact the efficiency of the injection molding process.
In addition to the material's physical properties, it is important to consider the environmental impact of using polypropylene for injection moulding. Understanding the recyclability and biodegradability of the material can help in making more sustainable choices for manufacturing processes. Furthermore, the availability and cost of polypropylene should also be taken into account, as these factors can affect the overall feasibility of using this material for injection moulding. Considering these aspects alongside its thermal stability and impact strength can lead to a more comprehensive material selection process.
Impact of Material Properties on Moulding Process
The material properties of injection molded polypropylene, such as its melt flow rate and crystallinity, have a direct impact on the moulding process. These properties influence the temperature at which the material should be processed, as well as the pressure required for optimal filling of the mold cavity.
The melt flow rate of polypropylene affects its ability to flow through the mold cavity, which in turn impacts the filling and cooling stages of the moulding process. A higher melt flow rate may result in faster filling of the cavity but could also lead to warping or sink marks if not properly controlled. On the other hand, a lower melt flow rate may require higher processing temperatures and pressures to achieve optimal filling, potentially increasing production costs.
Baoyuan's Recommendations for Polypropylene Material
Baoyuan recommends using polypropylene materials with a balanced combination of high melt flow rate for easy processing and good impact resistance for durable end products. Additionally, choosing materials with excellent chemical resistance ensures that the final products can withstand harsh environments.
Baoyuan's recommendations for polypropylene materials are based on the need for a balanced combination of high melt flow rate and good impact resistance. This ensures that the material is easy to process during injection molding while also resulting in durable end products with the ability to withstand impacts. Moreover, the choice of materials with excellent chemical resistance is crucial for ensuring that the final products can endure exposure to harsh environments, making them suitable for a wide range of applications.
Optimizing Injection Molding Parameters
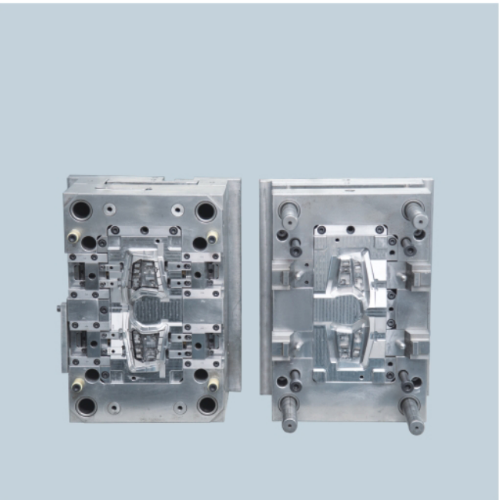
When it comes to polypropylene injection moulding, understanding the key parameters is crucial for achieving high-quality results. Factors such as injection speed, pressure, and temperature play a significant role in the molding process. Baoyuan's expertise in polypropylene injection molding process allows them to provide valuable insights into optimizing these parameters for maximum efficiency and quality.
Key Parameters for Polypropylene Injection Moulding
The success of polypropylene injection molding heavily relies on controlling key parameters such as melt temperature, mold temperature, injection pressure, and cooling time. The melt temperature must be carefully monitored to ensure proper flow and filling of the mold cavity. Mold temperature also impacts the final part quality by affecting shrinkage and warpage. Additionally, maintaining optimal injection pressure and cooling time is essential for achieving consistent and defect-free parts.
Controlling the melt temperature is crucial for achieving the desired flow and filling of the mold cavity. It is important to carefully monitor and adjust the melt temperature to prevent issues such as voids or incomplete filling of the mold. In addition, maintaining a consistent and optimal mold temperature is essential for minimizing shrinkage and warpage, which can greatly impact the final part quality. By paying close attention to these key parameters, manufacturers can ensure that their polypropylene injection molding process yields high-quality and defect-free parts.
Baoyuan's Tips for Setting Injection Molding Parameters
Baoyuan's extensive experience in polypropylene injection moulding enables them to offer valuable tips for setting injection molding parameters. They emphasize the importance of precise control over melt and mold temperatures to prevent issues like sink marks or voids in the final product. Furthermore, they recommend fine-tuning injection pressure based on the part design to minimize stress and improve dimensional accuracy.
To achieve optimal results in polypropylene injection molding, Baoyuan also stresses the importance of carefully monitoring cooling times. By adjusting the cooling time, they can prevent warping and ensure that the final product maintains its intended shape and dimensions. Additionally, Baoyuan recommends conducting thorough testing and analysis to identify any potential issues with the injection molding parameters before mass production begins. This proactive approach can save time and resources by addressing any issues early on in the process.
Balancing Temperature and Pressure for Quality Results
Achieving a delicate balance between temperature and pressure is critical in polypropylene injection molding. The proper combination of these factors ensures that the material flows smoothly into the mold while maintaining structural integrity during cooling. Baoyuan's expertise allows them to navigate this balance effectively, resulting in high-quality polypropylene parts with consistent mechanical properties and surface finish.
Designing and Building Polypropylene Molds
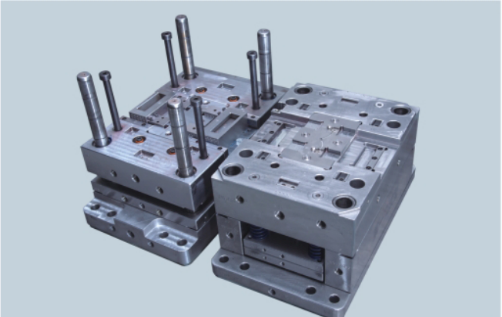
When it comes to polypropylene injection moulding, the design of the mold plays a crucial role in the success of the process. The mold design determines the final shape and features of the injection molded polypropylene product, making it essential to get it right from the start.
Importance of Mold Design in Injection Moulding
Mold design is critical in polypropylene injection molding process as it directly impacts product quality, production efficiency, and cost-effectiveness. A well-designed mold ensures that the molten polypropylene material flows smoothly and evenly, resulting in high-quality finished products with minimal defects.
Baoyuan's Approach to Mold Design and Construction
Baoyuan's approach to mold design and construction involves a meticulous analysis of product requirements, material properties, and production parameters. By leveraging advanced CAD/CAM software and cutting-edge manufacturing technologies, Baoyuan creates precision-engineered molds that are tailored to each client's specific needs.
By conducting a thorough analysis of product requirements, material properties, and production parameters, Baoyuan ensures that each mold is designed to meet the highest standards of precision and durability. This meticulous approach allows Baoyuan to create molds that not only meet the client's immediate needs but also stand the test of time in demanding production environments. The use of advanced CAD/CAM software and cutting-edge manufacturing technologies further enhances the quality and accuracy of each mold, providing clients with a reliable solution for their manufacturing needs.
Ensuring Precision and Durability in Polypropylene Molds
To ensure precision and durability in polypropylene molds, Baoyuan utilizes high-quality steel alloys and state-of-the-art machining processes. Each mold undergoes rigorous testing and quality assurance measures to guarantee its longevity and performance throughout countless injection molding cycles.
Quality Assurance in Polypropylene Moulding
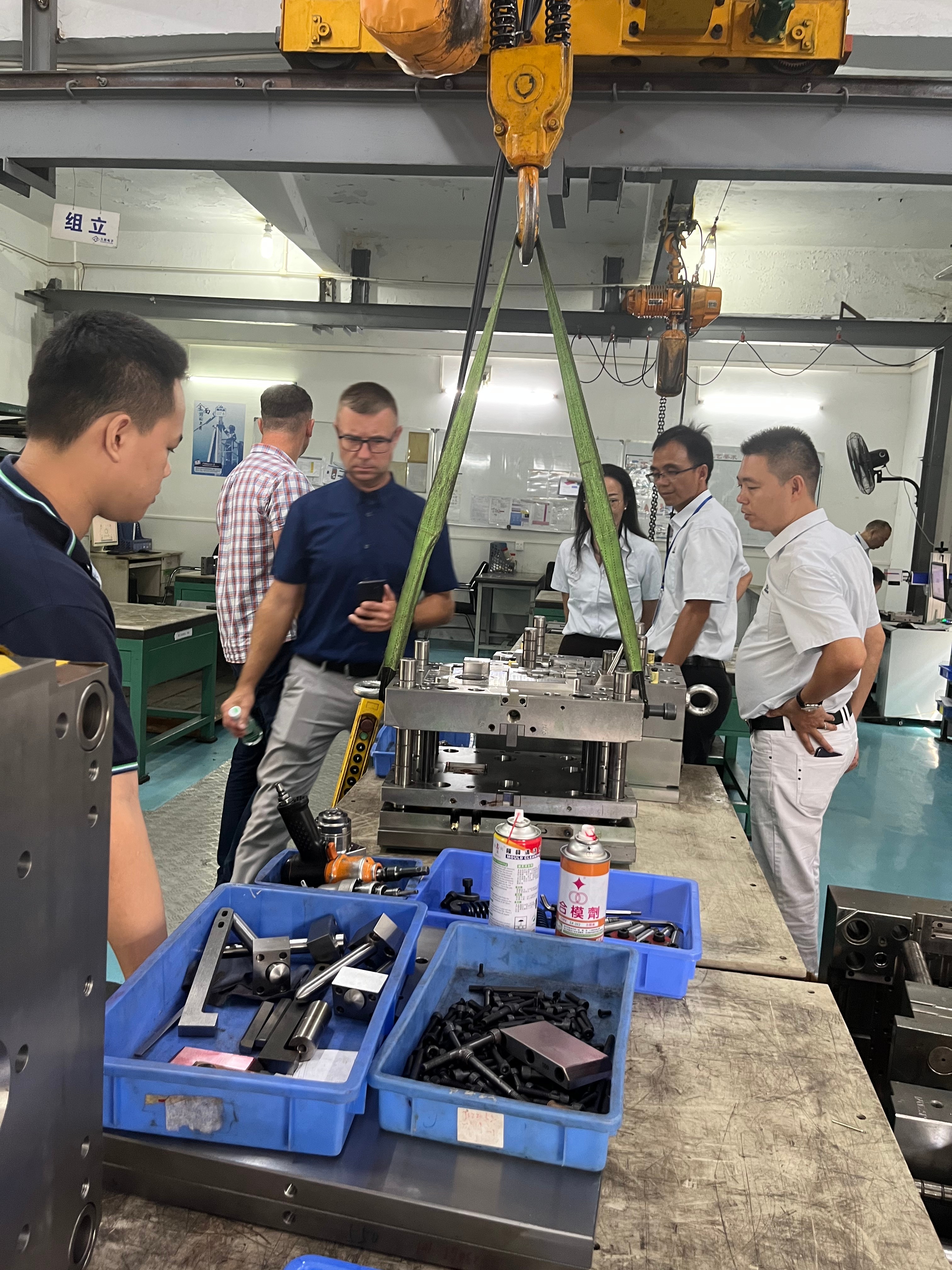
When it comes to quality assurance in polypropylene injection moulding, Baoyuan leaves no stone unturned. Stringent quality control measures are implemented at every stage of the process to ensure that the final products meet the highest standards. From material inspection to final product testing, Baoyuan's commitment to quality is unwavering.
Baoyuan's Quality Control Measures
Baoyuan's quality control measures begin with the careful selection and inspection of polypropylene materials for injection moulding. Each batch of material undergoes rigorous testing to ensure consistency and adherence to specified properties. Throughout the injection moulding process, regular inspections and quality checks are conducted to identify any deviations from set parameters and address them promptly.
After the injection moulding process is completed, Baoyuan conducts thorough testing on the finished products to ensure they meet the highest quality standards. This includes dimensional checks, visual inspections, and performance testing to verify that each item meets customer specifications. Any products that do not meet the required standards are promptly identified and either reworked or rejected to maintain consistency and quality.
Addressing Common Challenges in Polypropylene Moulding
Injection molded polypropylene material properties can pose challenges such as warping, sink marks, or inconsistent shrinkage. Baoyuan's team of experts is well-equipped to address these challenges through precise parameter adjustments, mold design modifications, and material selection optimization. By proactively identifying potential issues, Baoyuan ensures that the final products meet stringent quality standards.
Tips for Ensuring Consistent Quality in Production
To ensure consistent quality in production, Baoyuan emphasizes the importance of maintaining optimal PP injection molding temperature and pressure throughout the process. By carefully balancing these parameters and regularly monitoring their impact on the final products, Baoyuan achieves a high level of consistency and uniformity in its polypropylene injection molded products.
By consistently maintaining optimal PP injection molding temperature and pressure, Baoyuan also ensures that its products meet the required standards for strength, durability, and performance. This attention to detail not only results in high-quality products but also reduces the likelihood of defects or inconsistencies that could impact customer satisfaction. Additionally, by adhering to strict quality control measures throughout the production process, Baoyuan can confidently deliver reliable and uniform polypropylene injection molded products to its customers.
Conclusion
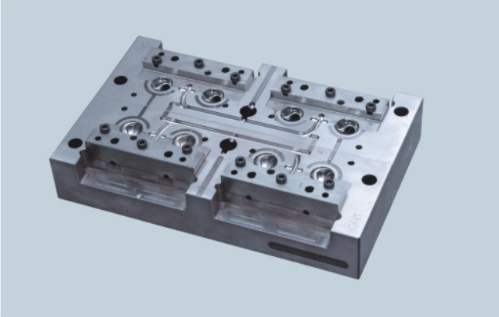
Polypropylene injection moulding is a complex process, but with the right knowledge and expertise, success is within reach. Baoyuan's commitment to excellence in polypropylene injection moulding ensures that your products meet the highest standards of quality and durability. By mastering the art of polypropylene moulding, Baoyuan guarantees exceptional results for all your injection moulding needs.
Achieving Success with Polypropylene Injection Moulding
With Baoyuan's guidance and expertise in polypropylene injection moulding, achieving success in your production process is inevitable. By understanding the intricacies of the polypropylene injection molding process and optimizing parameters such as PP injection molding temperature, you can ensure efficient and high-quality results every time.
Baoyuan's Commitment to Excellence
Baoyuan's unwavering commitment to excellence sets them apart as leaders in the industry of polypropylene injection moulding. Their dedication to precision in designing and building polypropylene molds, as well as their rigorous quality control measures, guarantees that your products will meet or exceed expectations. With a keen focus on innovation, Baoyuan stays ahead of the curve by continuously investing in the latest technology and machinery to ensure optimal efficiency and precision in their manufacturing processes. This commitment to staying at the forefront of industry advancements means that you can trust Baoyuan to deliver cutting-edge solutions for all your polypropylene moulding needs.
Mastering the Art of Polypropylene Moulding
By partnering with Baoyuan, you are not only gaining access to their wealth of knowledge and experience in polypropylene injection moulding but also empowering yourself to master this intricate art form. With their guidance on material selection, mold design, and quality assurance practices, you can elevate your production processes to new heights. Furthermore, Baoyuan's expertise extends to troubleshooting and problem-solving, ensuring that any issues that arise during the moulding process can be swiftly addressed and resolved. This level of support provides peace of mind and confidence in the reliability of your production operations.