Introduction
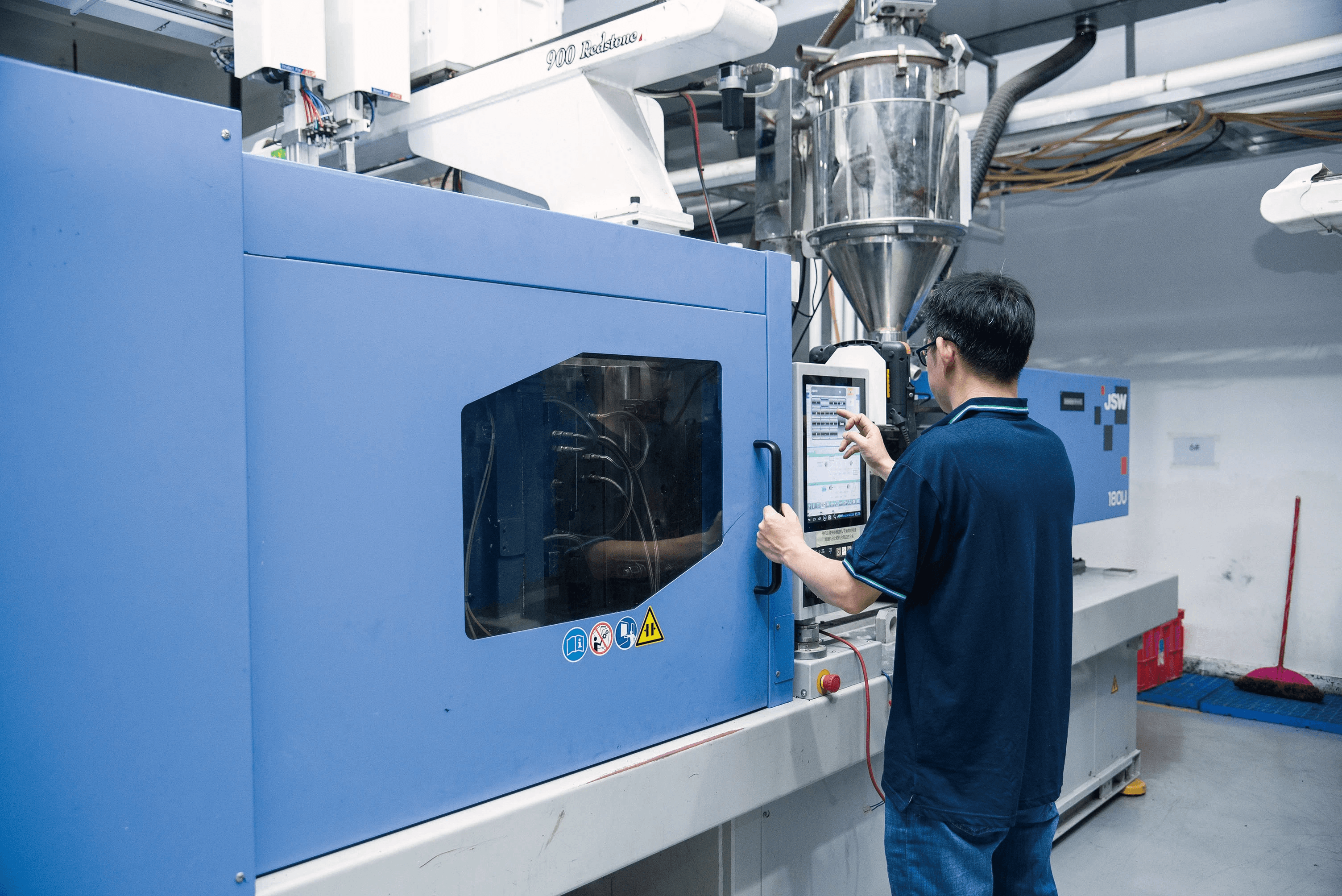
In the fast-paced world of manufacturing, efficiency is key, and few processes exemplify this better than plastic injection molding. This method not only streamlines production but also ensures the creation of high-quality injection molding products that meet diverse industry needs. As businesses increasingly shift towards sustainable practices and customized solutions, understanding small series production becomes essential for staying competitive.
The Efficiency of Plastic Injection Molding
Plastic injection molding is celebrated for its remarkable efficiency in producing a wide array of components quickly and accurately. By utilizing advanced machinery and precise techniques, manufacturers can create intricate designs using injection moldable plastics with minimal waste. This efficiency translates to shorter lead times and lower costs, making it an attractive option for companies looking to optimize their production processes.
Understanding Small Series Production
Small series production refers to the practice of manufacturing limited quantities of products, often tailored to specific customer needs or market demands. This approach allows businesses to be more agile, responding rapidly to changes without incurring the hefty expenses associated with large-scale production runs. In the realm of mould injection moulding, small series production offers a unique opportunity for innovation while maintaining high quality standards.
Advantages of High-Quality Injection Molding
High-quality injection molding is synonymous with precision and durability, ensuring that each product meets stringent quality control measures. The advantages extend beyond mere aesthetics; well-designed plastic molds enhance functionality and longevity in various applications—from automotive parts to consumer goods. By investing in high-quality mold plastic injection processes, companies can significantly reduce defects and improve overall customer satisfaction.
What is Plastic Injection Molding?
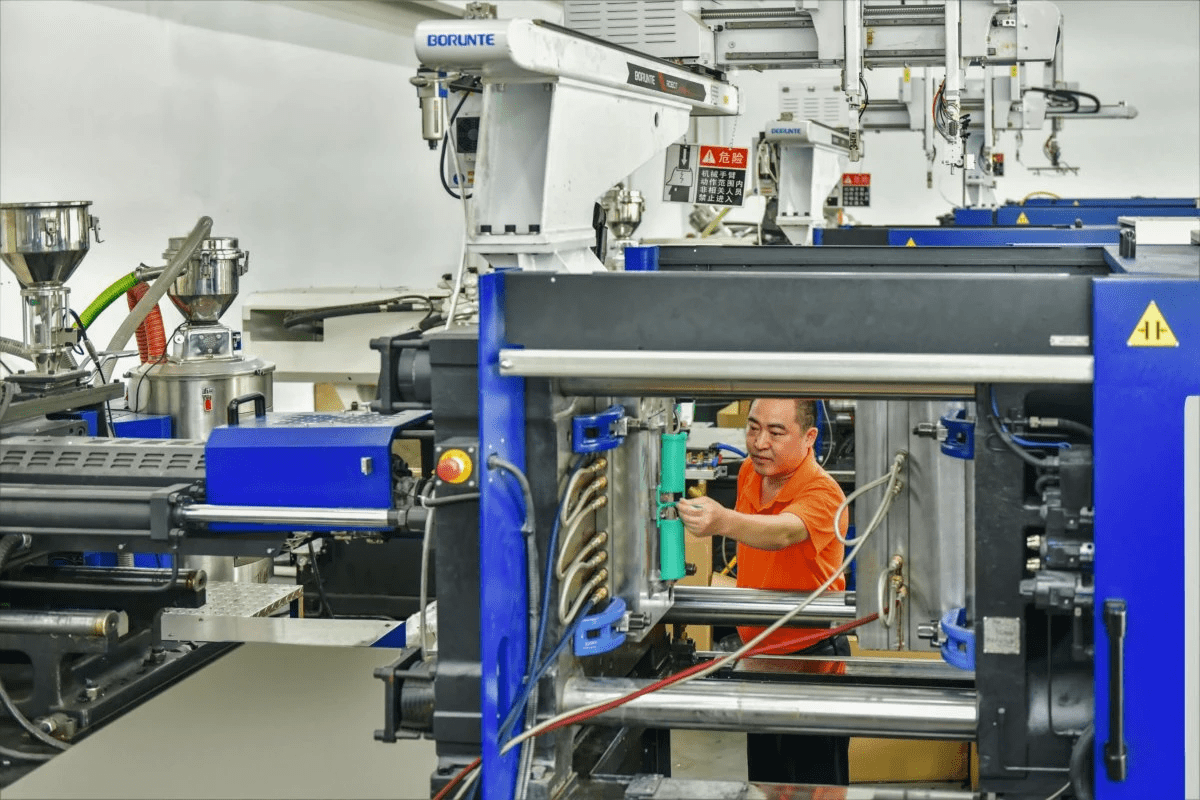
Plastic injection molding is a manufacturing process that involves injecting molten plastic into a mold to create various products. This method allows for the mass production of intricate shapes and designs with remarkable precision, making it a favored choice in numerous industries. The beauty of this process lies in its ability to produce high quality injection molding components quickly and efficiently.
The Basics of Injection Molding
At its core, injection molding is about transforming raw plastic into useful products through heat and pressure. The process begins with heating plastic pellets until they melt, followed by injecting the molten material into a pre-designed mold. Once cooled, the mold is opened to reveal the finished part, showcasing how effective this technique can be for producing consistent and high-quality items.
The versatility of injection molding means it can accommodate various types of plastic materials, including thermoplastics and thermosetting plastics. Each type offers unique properties that can be tailored to specific applications, further enhancing the appeal of using injection moldable plastics. Thus, whether it's creating automotive parts or everyday household items, this process stands out for its adaptability.
Key Components of the Process
The success of plastic injection molding hinges on several key components that work harmoniously together. First up is the **injection unit**, where raw plastic pellets are heated and melted before being injected into the mold cavity under high pressure. Next comes the **mold itself**, which is crafted with precision to ensure that each product meets exact specifications.
Additionally, there’s the **clamping unit**, which holds the mold tightly closed during injection to prevent leakage or deformation of the final product. Together with these units are various auxiliary equipment such as cooling systems that help solidify the molten plastic post-injection swiftly. All these components contribute significantly to achieving high quality in each batch produced through mould injection moulding.
Common Applications of Injection Moldable Plastics
Plastic injection molding finds its way into countless applications across diverse sectors due to its efficiency and versatility. From automotive parts like dashboards and bumpers to consumer goods such as containers and toys, injected molded plastics are everywhere you look! Their lightweight nature combined with strength makes them ideal for industries ranging from electronics to medical devices.
Moreover, custom projects often benefit from using high quality injection molding techniques because they allow for intricate designs without sacrificing durability or performance characteristics. For instance, companies frequently choose mold plastic injection methods when developing prototypes or short-run production items because it ensures rapid turnaround times while maintaining superior quality standards. Overall, it's clear that this method plays an essential role in modern manufacturing practices.
The Role of Baoyuan in Injection Molding
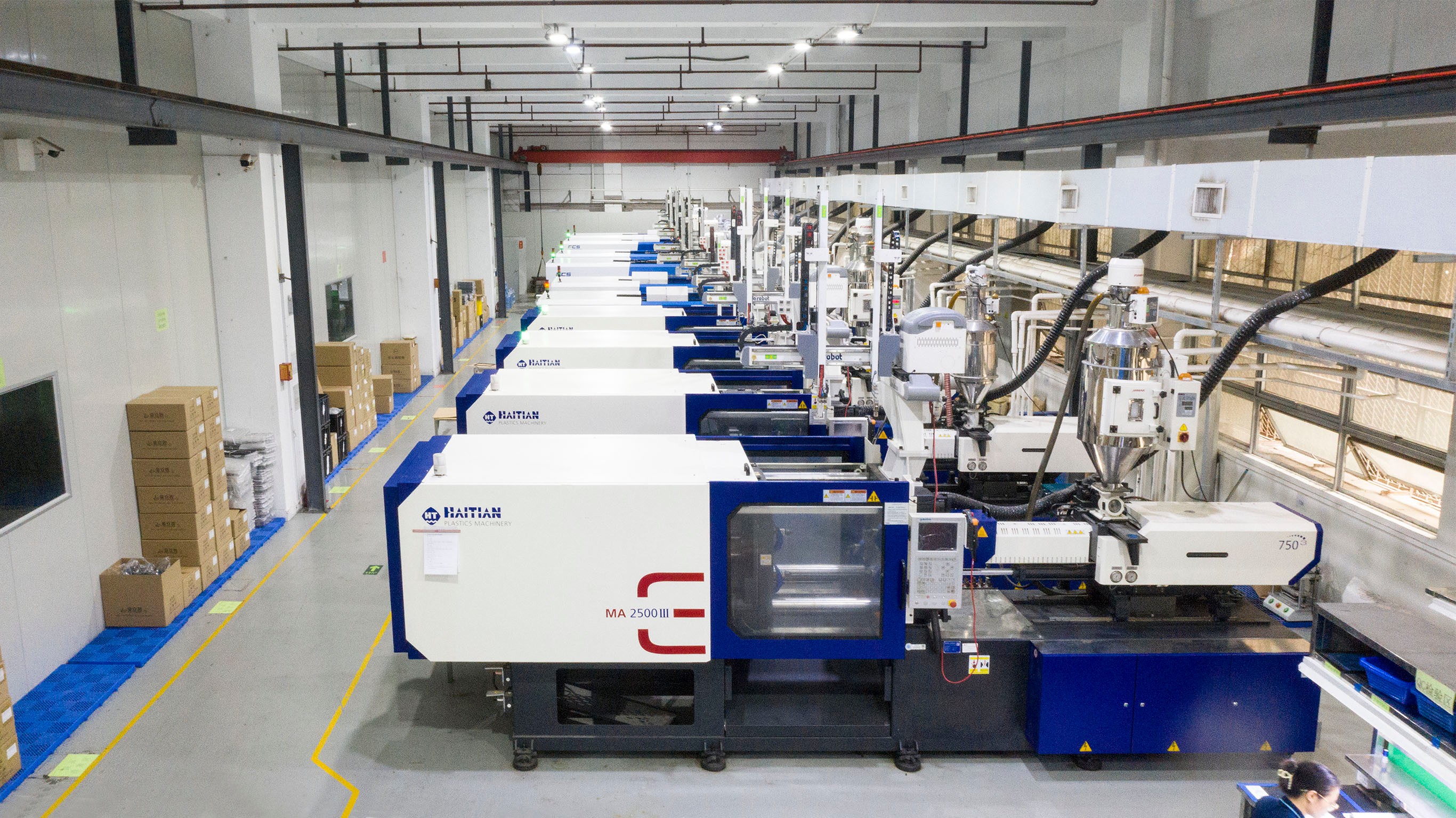
Expertise in Mold Design and Production
Baoyuan's prowess in mold design is a cornerstone of their success in injection molding. Their team comprises seasoned professionals who understand the intricacies of mould injection moulding, enabling them to create molds that optimize efficiency and precision. This level of expertise translates into superior products made from injection moldable plastics, ensuring that every project benefits from high-quality standards.
The company's commitment to continuous improvement means they stay ahead of industry trends and technologies. This dedication not only enhances their production capabilities but also positions them as innovators within the field of plastic molding. With Baoyuan at the helm, clients can trust that their mold plastic injection needs are met with unparalleled craftsmanship.
Technology-Driven Solutions for Molding
In today's fast-paced manufacturing landscape, technology plays a vital role in enhancing production processes. Baoyuan embraces cutting-edge innovations that streamline operations and improve overall quality during plastic injection molding projects. From advanced computer-aided design (CAD) software to state-of-the-art machinery, their technology-driven approach ensures efficient mold production without compromising on quality.
Moreover, Baoyuan’s integration of automation into their processes allows for quicker turnaround times while maintaining consistency across large volumes of products. This capability is particularly beneficial for businesses seeking solutions for short-run projects or small series production without sacrificing quality or increasing costs significantly. The result is a seamless experience for clients looking for reliable partners in high-quality injection molding.
Commitment to Quality Assurance
Quality assurance is not just an afterthought at Baoyuan; it's embedded within every step of their process from start to finish. They implement rigorous testing protocols throughout the plastic injection molding cycle, ensuring that each product meets stringent quality standards before it reaches clients' hands. This unwavering commitment helps build trust with customers who depend on high-quality products made from durable injection moldable plastics.
Baoyuan's focus on quality extends beyond just the final product; it encompasses everything from material selection to mold maintenance practices within their facilities. By prioritizing excellence at all levels, they ensure that every aspect contributes to producing reliable molds and components through effective mould injection moulding techniques. Ultimately, this dedication sets them apart as a go-to choice for businesses aiming for perfection in plastic molding applications.
Small Series Production: A Game Changer
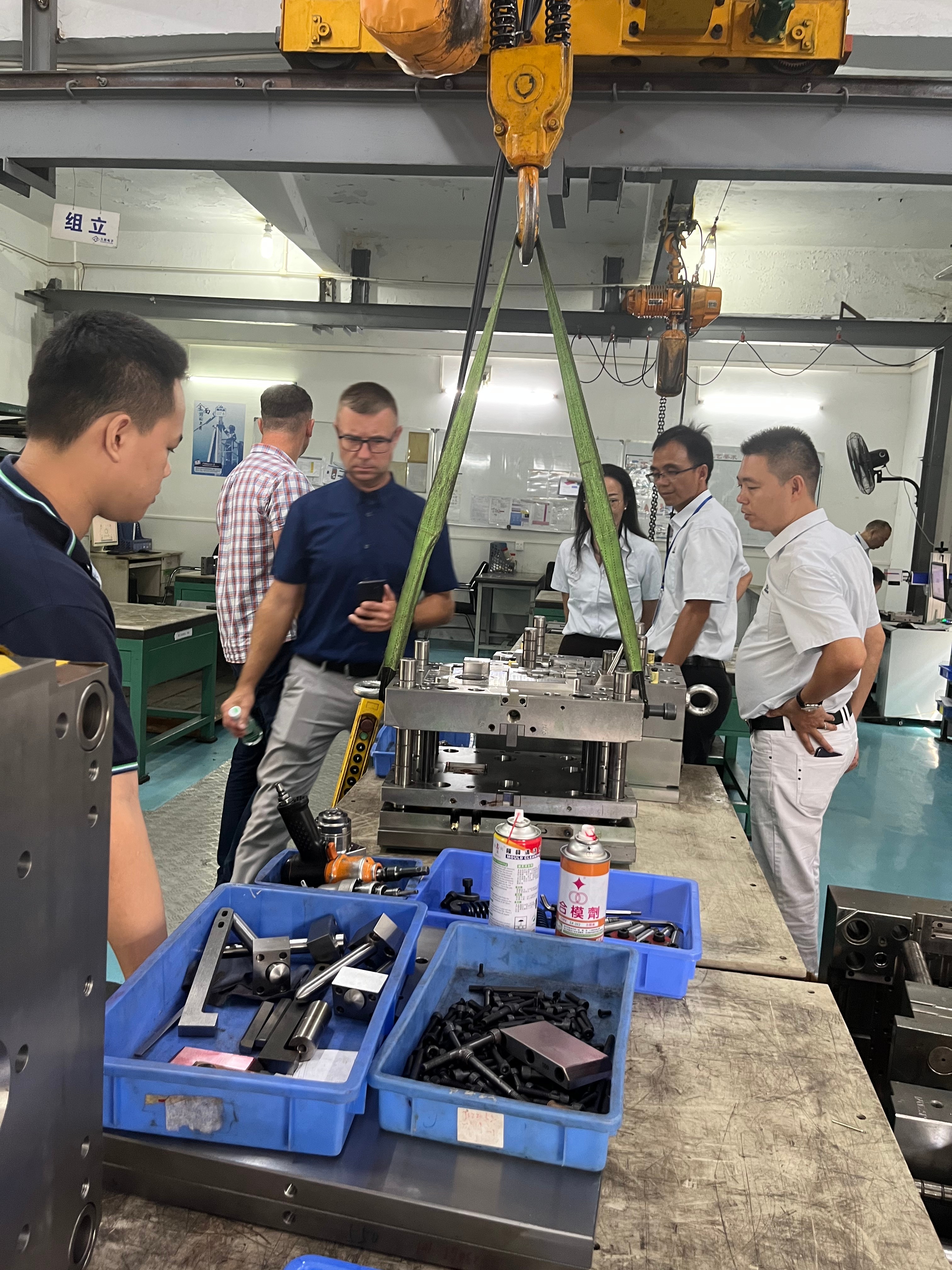
In the world of manufacturing, small series production has emerged as a game changer, particularly in the realm of high-quality injection molding. This approach allows businesses to produce limited quantities of products without compromising on quality or efficiency. As industries evolve, the demand for customized solutions and rapid prototyping has made short run injection molding an attractive option for many manufacturers.
Benefits of Short Run Injection Molding
Short run injection molding offers several benefits that make it an appealing choice for companies looking to innovate quickly. First and foremost, it enables manufacturers to test new designs and concepts without committing to large production runs. This flexibility is crucial in today’s fast-paced market, where consumer preferences can shift overnight, making high quality injection molding essential for staying ahead.
Moreover, small series production allows for greater customization compared to traditional manufacturing methods. Businesses can create tailored products using various injection moldable plastics that meet specific customer needs or niche markets. This adaptability not only enhances product offerings but also strengthens brand loyalty as customers appreciate personalized solutions.
Cost Efficiency and Time Savings
When it comes to cost efficiency, short run plastic injection molding shines brightly. By producing smaller quantities of items, companies can significantly reduce upfront costs associated with mass production while still maintaining high quality standards in their output. The savings extend beyond just material costs; shorter lead times mean faster time-to-market, allowing businesses to capitalize on emerging trends quickly.
Time savings are another critical advantage of small series production in the context of plastic molding processes. With streamlined operations and advanced technology used in mold plastic injection techniques, manufacturers can complete projects more swiftly than ever before. Faster turnaround times translate into increased productivity and profitability—an enticing proposition for any business aiming to thrive in a competitive landscape.
Examples of Successful Small Series Projects
Numerous industries have successfully leveraged small series production through high quality injection molding techniques to achieve remarkable results. For instance, automotive companies often utilize this method when developing prototype parts or limited-edition models that require precision engineering with specific design features using specialized mould injection moulding processes. These projects not only showcase the capabilities of short run production but also illustrate how it meets industry demands efficiently.
Another notable example is the consumer electronics sector, where brands frequently release limited-time gadgets or accessories that cater to evolving tech trends using custom mold plastic injection strategies. By employing short run plastic injection molding techniques, these companies can launch innovative products while minimizing waste from unsold inventory—a win-win situation!
Lastly, healthcare providers have embraced small series production for medical devices that require strict regulatory compliance and rapid adjustments based on patient feedback or technological advancements—once again demonstrating how effective high-quality plastic injection molding can be across diverse sectors.
Choosing the Right Injection Mold for Your Needs
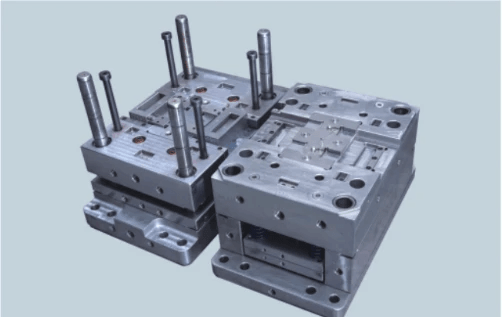
Selecting the right injection mold is crucial for achieving high-quality injection molding results. The mold you choose can significantly impact not only the efficiency of production but also the quality of the final product made from injection moldable plastics. Understanding various factors, comparing options, and recognizing design implications are all essential steps in this decision-making process.
Factors to Consider in Mold Selection
When it comes to mold selection, several factors come into play that can make or break your plastic injection molding project. First and foremost, consider the complexity of your part; intricate designs may require more advanced molds that can handle detailed features without compromising on quality. Additionally, think about material compatibility—certain plastics work better with specific molds, so understanding which injection moldable plastics suit your needs is essential for optimal performance.
Another critical factor is production volume; if you’re looking at high-volume runs, investing in a durable plastic injection molding mold will pay off in the long run due to its longevity and reliability. Conversely, if you’re focused on small series production, a simpler mold might suffice while still delivering acceptable quality. Lastly, evaluate cost-effectiveness—striking a balance between upfront investment and long-term benefits is key to successful mould injection moulding.
Comparing Single-Color vs. Double-Color Molding
Choosing between single-color and double-color molding can significantly affect both aesthetics and functionality of your product made from plastic molding techniques. Single-color molding is often more straightforward and cost-efficient, making it an excellent choice for projects where simplicity reigns supreme or when budget constraints are tight. However, double-color molding opens up a world of possibilities by allowing for multi-tonal designs that enhance visual appeal and product differentiation.
The process of double-color moulding does require more sophisticated equipment and expertise but can result in products that stand out in competitive markets—think vibrant toys or ergonomic handles with contrasting colors! It’s essential to weigh these benefits against potential costs when deciding which method aligns best with your project goals while ensuring high-quality injection molding standards are met.
Impact of Mold Design on Product Quality
The design of your plastic injection molding mold plays a pivotal role in determining the overall quality of the finished product. A well-thought-out design minimizes defects such as warping or surface imperfections, ensuring that each piece meets stringent quality criteria associated with high-quality injection molding processes. Moreover, effective cooling channels within the mold design contribute significantly to cycle time reduction—faster cooling means quicker production without sacrificing quality!
Additionally, proper venting within the mould design helps eliminate trapped air during filling—a common culprit behind flaws like bubbles or voids in injected products made from various types of injection moldable plastics. Ultimately, investing time into thoughtful mold design pays dividends; it directly correlates with achieving consistent results across all produced units while reinforcing brand reputation through superior product offerings.
Future Trends in Plastic Injection Molding
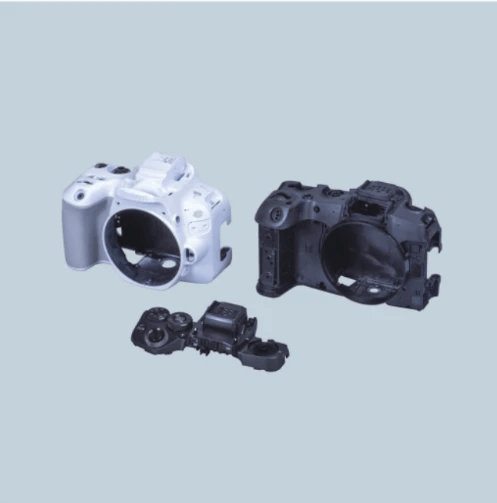
The landscape of plastic injection molding is rapidly evolving, driven by technological advancements and increasing demand for sustainability. Innovations in the field are enhancing the efficiency and capabilities of high-quality injection molding processes, paving the way for exciting developments. As industries continue to embrace these changes, understanding future trends becomes essential for businesses looking to stay competitive.
Innovations in Injection Molding Technology
Recent innovations in injection molding technology are transforming how products are designed and manufactured. From advanced robotics and automation to smart manufacturing solutions, the integration of technology is streamlining production processes and improving precision. These advancements allow for more complex designs using injection moldable plastics while ensuring high quality injection molding standards are met consistently.
One notable trend is the use of 3D printing technologies alongside traditional mould injection moulding methods, which enables rapid prototyping and reduces lead times significantly. The combination of these technologies allows manufacturers to create custom molds more efficiently, resulting in better product quality and reduced waste. As a result, companies can respond faster to market demands without compromising on the quality of their plastic molding.
Moreover, machine learning algorithms are being employed to optimize the injection molding process by predicting failures before they occur and adjusting parameters in real-time. This proactive approach not only enhances productivity but also contributes to cost savings over time, reinforcing the importance of investing in cutting-edge technology for successful mold plastic injection operations.
Sustainable Practices in the Industry
Sustainability has become a key focus within the plastic injection molding industry as environmental concerns grow stronger among consumers and regulators alike. Manufacturers are increasingly adopting eco-friendly practices that minimize waste and reduce energy consumption during production processes. This shift not only benefits the planet but also aligns with consumer preferences for sustainable products made through high-quality injection molding techniques.
One effective approach is utilizing biodegradable or recycled materials for producing injection moldable plastics, which helps decrease reliance on virgin resources while lowering carbon footprints. Additionally, companies are investing in energy-efficient machinery that consumes less power during operation—making a significant impact on overall sustainability goals within their facilities. By implementing such measures, businesses can improve their reputation while contributing positively to environmental conservation efforts.
Furthermore, sustainable practices extend beyond material selection; they also involve optimizing production workflows to minimize scrap rates during mould injection moulding processes. By focusing on reducing waste at every stage—from design through manufacturing—companies can achieve greater efficiency while maintaining high standards of quality assurance throughout their operations.
The Rise of Custom Mold Plastic Injection
As markets become increasingly diverse and competitive, there’s been a notable rise in demand for custom mold plastic injection solutions tailored specifically to unique customer needs. Businesses recognize that off-the-shelf products often fall short when it comes to meeting specific requirements or achieving desired aesthetics—prompting them towards bespoke options offered by expert partners like Baoyuan.
Custom mold designs allow manufacturers greater flexibility when creating intricate shapes or incorporating multiple features into a single component using advanced techniques like double-color molding or insert molding strategies—ensuring superior product performance without sacrificing quality standards associated with high-quality injection molding practices. This level of customization not only enhances functionality but also helps brands differentiate themselves from competitors who rely solely on generic offerings available on the market today.
Moreover, as consumer preferences shift towards personalized experiences across various sectors—from automotive parts to consumer electronics—the ability to produce small series runs with precision becomes crucial for success within this landscape dominated by rapid change demands driven largely by technological advancements across industries globally.
Conclusion
In summary, plastic injection molding stands out as a highly efficient and versatile manufacturing process, particularly for producing high-quality injection molding products in various industries. This method not only streamlines production but also offers the flexibility needed for small series production runs, allowing businesses to innovate without significant upfront costs. Understanding the intricacies of injection moldable plastics and the role of expert partners like Baoyuan can lead to superior outcomes in your projects.
Key Takeaways on Plastic Injection Molding
Plastic injection molding is a crucial technique that enables manufacturers to create complex shapes with precision and consistency. The process involves melting plastic and injecting it into a mold, where it cools and solidifies into the desired form. By leveraging high quality injection molding techniques, companies can produce durable components that meet stringent quality standards while optimizing cost-effectiveness.
Why Choose Expert Partners like Baoyuan
Choosing partners like Baoyuan for your mold plastic injection needs ensures that you benefit from their extensive expertise in mold design and production. Their commitment to using advanced technology-driven solutions allows for innovative designs that enhance efficiency and product quality in every project. With their focus on quality assurance, Baoyuan stands out as a reliable choice for businesses aiming to achieve exceptional results with their plastic molding processes.
The Future of High-Quality Injection Molding
The landscape of high-quality injection molding is evolving rapidly, driven by innovations in technology and a growing emphasis on sustainability within the industry. As manufacturers adopt more eco-friendly practices, we can expect an increase in demand for custom mold plastic injection solutions tailored to specific market needs. This shift will not only enhance product performance but also ensure that businesses remain competitive in an ever-changing marketplace.