Introduction
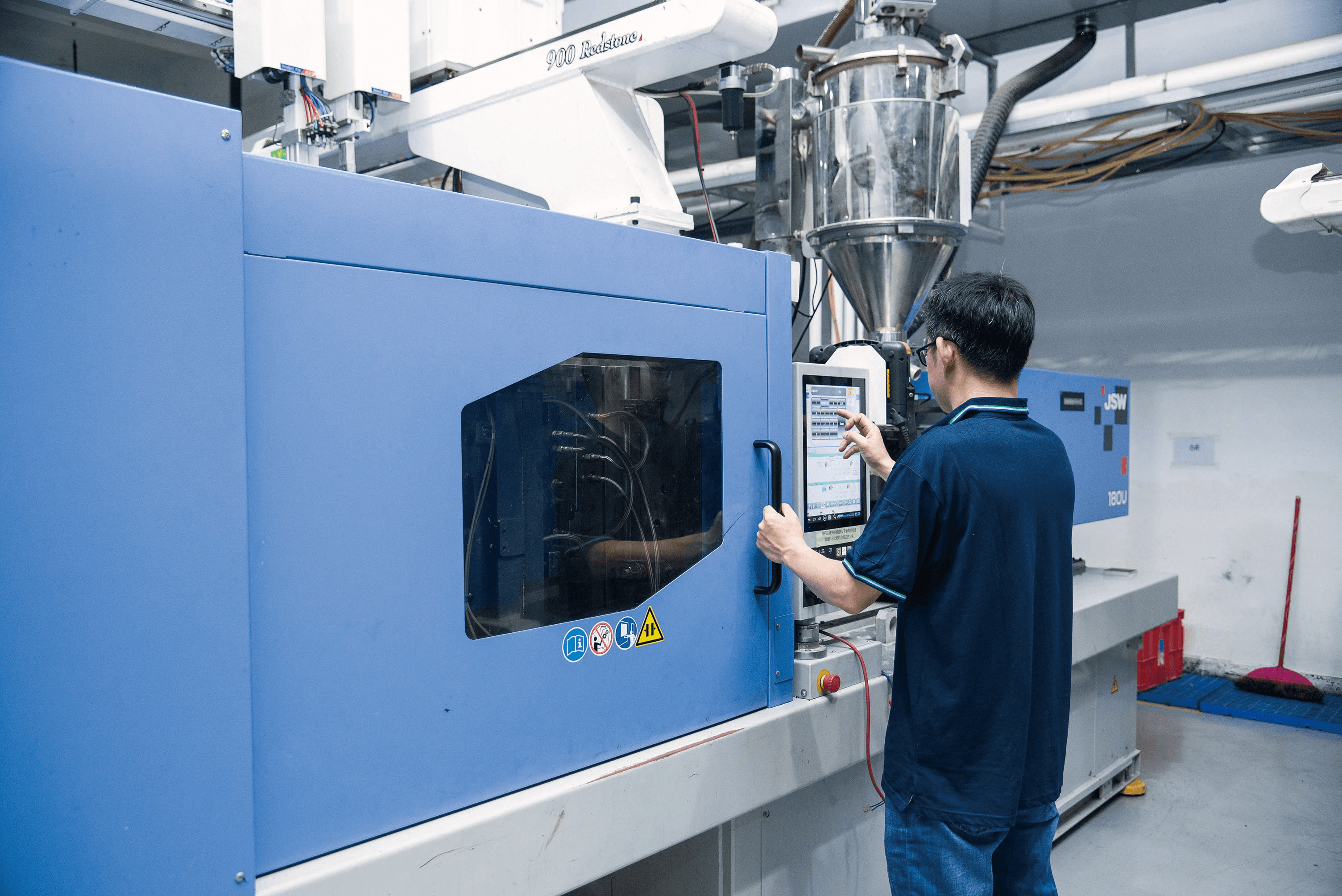
In the world of manufacturing, plastic injection molding stands out as a revolutionary technique that has transformed various industries, particularly the automotive sector. This method allows for the efficient production of intricate designs and high-quality automotive plastic parts, making it a go-to solution for auto parts manufacturers seeking to meet consumer demands. With its ability to produce durable and lightweight components, plastic injection molding has become integral in shaping modern vehicles.
Overview of Plastic Injection Molding
Plastic injection molding is a manufacturing process that involves injecting molten plastic into a mold to create specific shapes and designs. This technique is celebrated for its precision and versatility, enabling the production of complex geometries that would be challenging with other methods. As one of the most widely used processes in creating plastic auto parts, it offers both speed and efficiency, allowing manufacturers to keep pace with market demands.
Importance in the Automotive Sector
The automotive sector relies heavily on injection molding due to its ability to produce high volumes of consistent quality parts at lower costs. From interior components like dashboards to exterior panels such as bumpers, automotive plastic parts are essential for vehicle functionality and aesthetics. Moreover, as consumers increasingly prioritize fuel efficiency and reduced vehicle weight, the demand for lightweight plastic auto parts continues to rise.
Rise of Automotive Injection Molding
In recent years, there has been a significant surge in automotive injection molding practices among manufacturers looking to innovate their product lines. The combination of advanced materials and cutting-edge technologies has led to improved performance characteristics in automotive parts manufacturers' offerings. As electric vehicles gain traction and sustainability becomes a priority, this rise reflects an industry-wide shift toward more efficient production methods that embrace both innovation and environmental responsibility.
Types of Automotive Plastic Parts
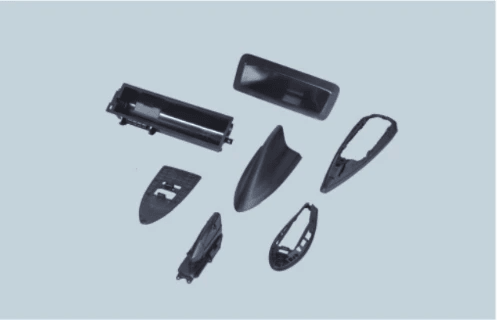
Plastic injection molding has revolutionized the automotive industry, enabling the production of a variety of components that are both lightweight and durable. Automotive plastic parts are integral to modern vehicles, offering manufacturers flexibility in design and function. Let’s delve into the different types of automotive plastic parts that play crucial roles in vehicle performance and aesthetics.
Interior Components and Trim
From dashboard panels to door trims, plastic auto parts are essential for creating comfortable and stylish interiors. Auto parts manufacturers leverage injection moldable plastics to produce intricate designs that enhance the overall look and feel of a vehicle's cabin.
The benefits extend beyond aesthetics; these interior components also contribute to safety and functionality. For instance, molded plastic can be used for airbag housings or acoustic panels that reduce noise inside the vehicle. With advancements in injection molding technology, manufacturers can create lightweight yet sturdy interior elements that meet consumer demands for both style and safety.
Exterior Panels and Bumpers
Exterior panels and bumpers are another significant category where automotive plastic parts excel, thanks to their ability to withstand impact while maintaining a sleek appearance. Injection molding allows for the mass production of complex shapes required for modern car designs, making it easier for manufacturers to achieve aerodynamic profiles without sacrificing strength or durability.
Auto parts manufacturers utilize high-performance plastics in their bumpers not only for aesthetics but also for energy absorption during collisions, enhancing passenger safety significantly. The integration of these materials through automotive injection molding techniques ensures consistency in quality while reducing overall production costs—an attractive proposition in today’s competitive market.
Engine Components and Housings
Engine components might not be the first thing that comes to mind when thinking about plastic auto parts; however, they play an increasingly vital role in modern vehicles. Automotive injection molding enables the creation of lightweight engine housings and covers that help improve fuel efficiency without compromising performance or safety standards.
These injection moldable plastics can withstand high temperatures and harsh environments found within an engine compartment, making them ideal candidates for various applications like air intake manifolds or coolant reservoir tanks. As auto parts manufacturers continue innovating with advanced materials through injection molding processes, we can expect even more sophisticated solutions tailored specifically for engine performance enhancement.
Role of Auto Parts Manufacturers
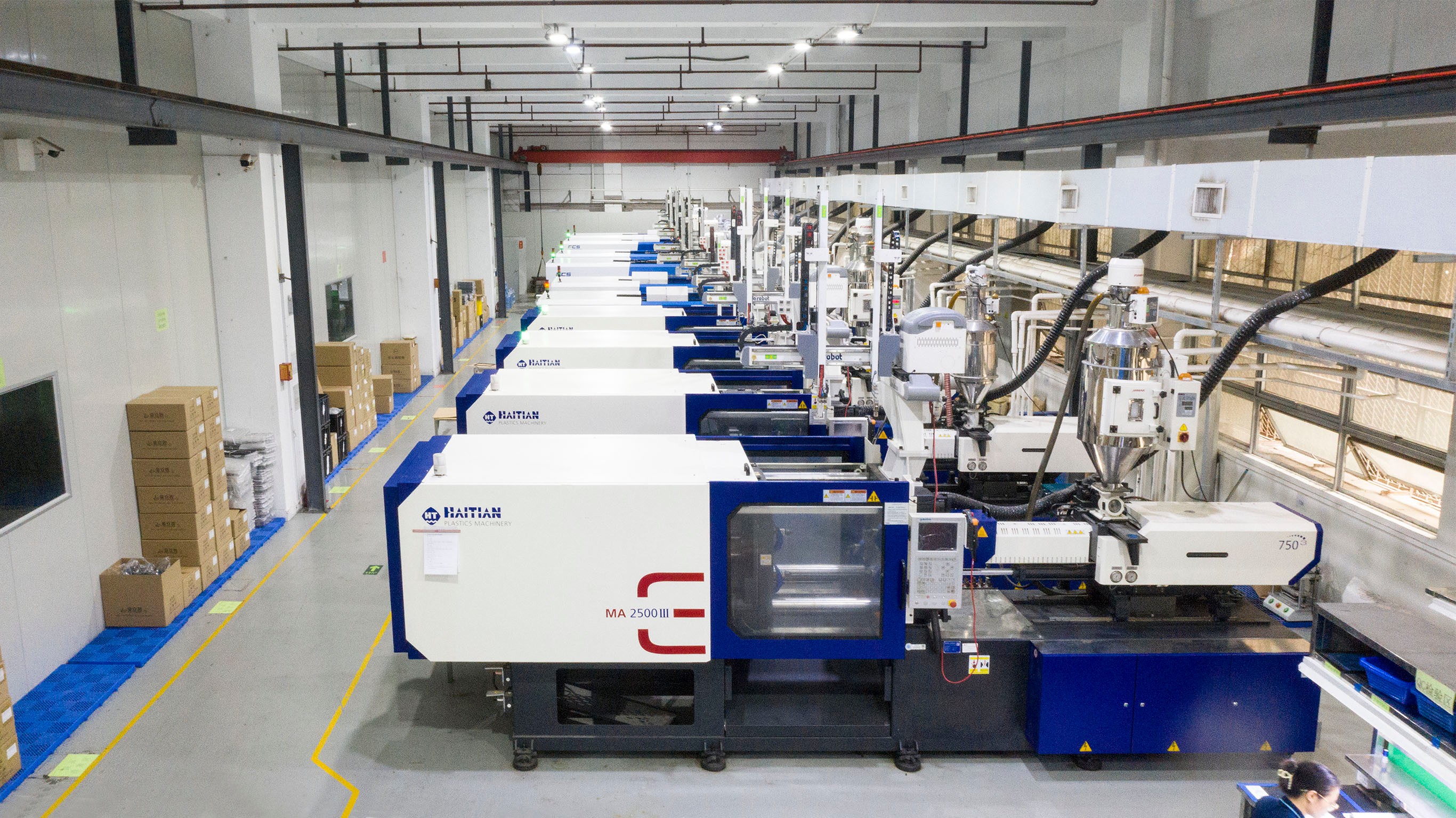
The role of auto parts manufacturers in the automotive injection molding landscape is pivotal. These manufacturers are not just suppliers; they are strategic partners who collaborate closely with automotive companies to ensure that the plastic auto parts meet the exact specifications and performance standards required for modern vehicles. Their expertise in plastic injection molding allows them to produce high-quality, durable automotive plastic parts that contribute significantly to vehicle performance and aesthetics.
Collaboration with Automotive Companies
Collaboration between auto parts manufacturers and automotive companies is essential for innovation and efficiency in production processes. By working together from the design phase, both parties can optimize the use of injection moldable plastics, ensuring that components are not only functional but also cost-effective to produce at scale. This partnership often leads to shared research initiatives, where advancements in materials and technologies can be tested before mass production, ultimately benefiting consumers through better-performing vehicles.
Quality Standards and Certifications
Quality standards and certifications play a crucial role in the relationship between automotive parts manufacturers and their clients. To maintain competitiveness in the market, these manufacturers must adhere to rigorous quality control measures throughout the injection molding process. Certifications such as ISO/TS 16949 ensure that automotive plastic parts meet industry benchmarks for safety, durability, and reliability—factors that are non-negotiable for car manufacturers seeking to uphold their brand reputation.
Examples of Leading Manufacturers like Baoyuan
Known for its commitment to quality and advanced manufacturing techniques, Baoyuan specializes in producing a wide range of plastic auto parts that cater specifically to the needs of various automobile makers worldwide. Their strategic collaborations with major automotive brands highlight how effective partnerships can drive progress within the industry by leveraging state-of-the-art technology alongside traditional craftsmanship.
Advantages of Injection Molding
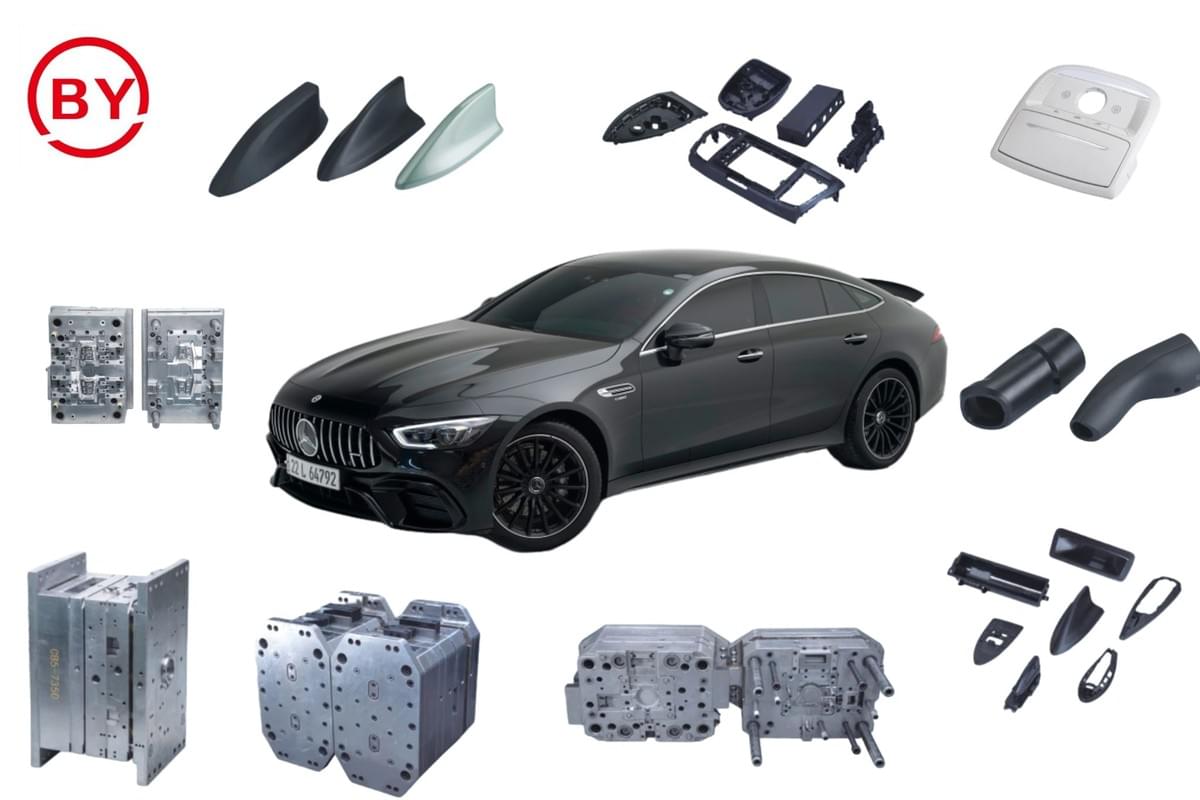
Injection molding is revolutionizing the way automotive parts manufacturers create and supply components for vehicles. This process not only streamlines production but also enhances the overall quality of automotive plastic parts. As a result, auto parts manufacturers are increasingly turning to plastic injection molding to meet their needs.
Cost Efficiency and Mass Production
By utilizing advanced machinery and techniques, manufacturers can produce large quantities of plastic auto parts at a fraction of the cost compared to traditional manufacturing methods. This scalability allows automotive parts manufacturers to keep up with market demands without breaking the bank.
Moreover, once the initial mold is created, producing additional units becomes significantly cheaper; this is especially beneficial for high-volume production runs often required in the automotive sector. The reduction in waste material during the injection molding process also contributes to lower costs, making it an attractive option for companies looking to maximize their profit margins while maintaining quality standards in their automotive plastic parts.
Design Flexibility with Injection Moldable Plastics
Another key advantage of injection molding lies in its design flexibility, allowing for intricate shapes and features that were previously challenging or impossible to achieve with other manufacturing techniques. Automotive injection molding enables designers to create complex geometries that enhance both functionality and aesthetics in vehicle components. This versatility means that auto parts manufacturers can innovate freely without being constrained by traditional design limitations.
Additionally, injection moldable plastics can be easily tailored with additives or colorants during processing, leading to customized solutions that meet specific requirements or branding needs. Such adaptability not only fosters creativity but also helps manufacturers respond swiftly to changing consumer preferences within the competitive automotive market.
Enhanced Durability of Automotive Plastic Parts
Durability is paramount when it comes to automotive applications; luckily, plastic injection molding produces robust components designed to withstand harsh conditions over extended periods. The use of high-quality materials in conjunction with precise manufacturing processes ensures that these automotive plastic parts exhibit excellent impact resistance and longevity compared to alternatives made from less durable materials.
Furthermore, advancements in polymer technology have led to the development of specialized injection moldable plastics that offer enhanced thermal stability and chemical resistance—crucial traits for engine components and exterior panels exposed to varying environmental factors. Consequently, auto parts manufacturers can provide products that not only meet but exceed industry standards for performance and reliability.
Innovations in Injection Molding Technology
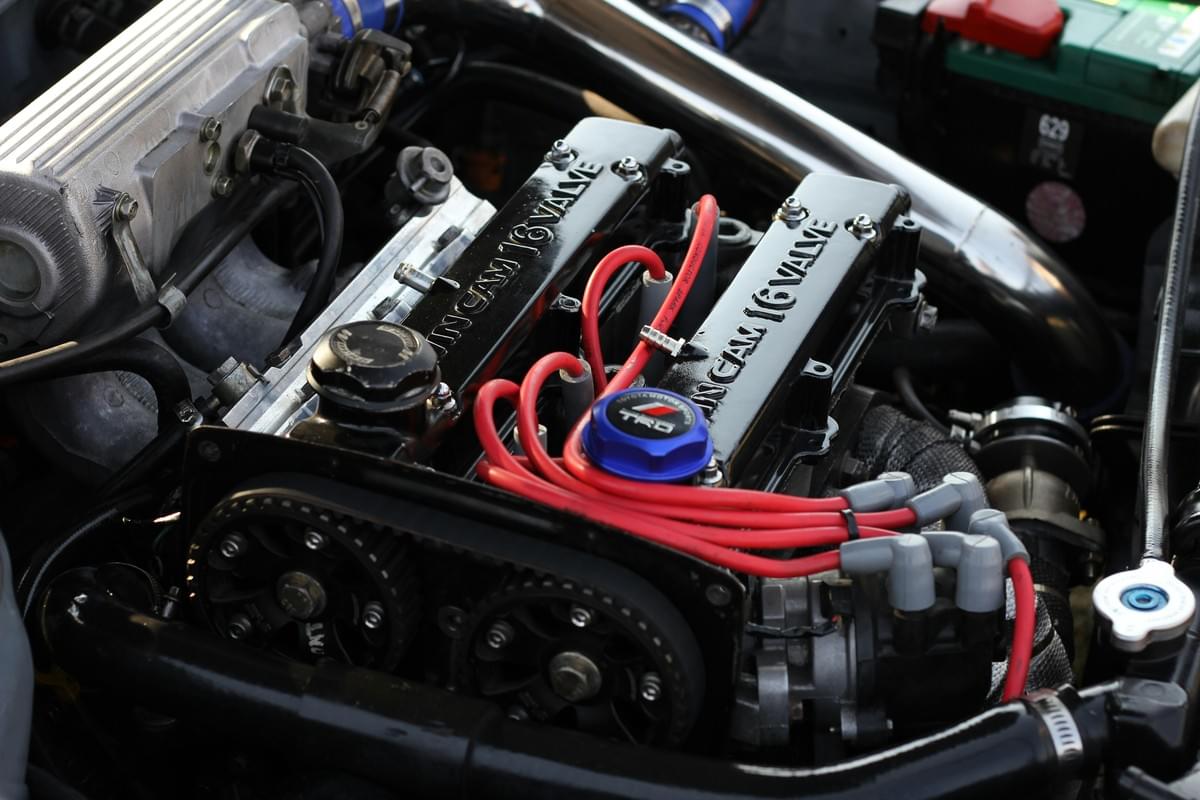
The automotive industry is experiencing a seismic shift thanks to innovations in injection molding technology. These advancements are not only enhancing the quality and efficiency of automotive plastic parts but also addressing the growing demands for sustainability and performance. As auto parts manufacturers embrace these changes, they are better equipped to meet market expectations while staying competitive.
Use of Advanced Materials
The introduction of advanced materials has revolutionized automotive injection molding, allowing for the creation of lighter yet stronger plastic auto parts. Manufacturers are now utilizing high-performance thermoplastics and composites that enhance durability while reducing weight, which is crucial for fuel efficiency. This shift to injection moldable plastics means that automotive parts manufacturers can design components that withstand extreme conditions without compromising on performance or safety.
Additionally, these advanced materials often offer improved aesthetic qualities, enabling more intricate designs that appeal to consumers' tastes. The flexibility provided by modern plastics allows for greater creativity in product development, resulting in innovative interior and exterior components that enhance vehicle appeal. Ultimately, the use of advanced materials in injection molding is paving the way for a new era of automotive design and functionality.
Automation and Robotics in Production
Automation and robotics are transforming the landscape of plastic injection molding within the automotive sector by streamlining production processes and increasing efficiency. With robotic arms handling tasks such as loading materials, assembling components, or even quality control checks, manufacturers can achieve higher precision with reduced labor costs. This technological integration not only speeds up production but also minimizes human error—ensuring that each batch of automotive plastic parts meets stringent quality standards.
Moreover, automation enables auto parts manufacturers to respond swiftly to changing market demands by adjusting production schedules without significant downtime. The result? A more agile manufacturing process capable of producing a diverse range of plastic auto parts tailored to specific customer needs or trends in vehicle design. As robotics continue to evolve, we can expect further enhancements in both speed and accuracy within the realm of automotive injection molding.
Sustainability in Automotive Injection Molding
Sustainability has become a cornerstone principle driving innovations in automotive injection molding technology today. As environmental concerns grow among consumers and regulatory bodies alike, auto parts manufacturers are increasingly adopting eco-friendly practices throughout their production processes. This includes using recycled materials for injection moldable plastics and implementing energy-efficient machinery that reduces carbon footprints during manufacturing.
Furthermore, sustainable practices extend beyond material selection; they encompass entire lifecycle assessments aimed at minimizing waste during production and ensuring recyclability at end-of-life stages for plastic auto parts. By prioritizing sustainability within their operations, automotive parts manufacturers not only comply with regulations but also resonate with eco-conscious consumers looking for greener options when purchasing vehicles or replacement components. Ultimately, this commitment to sustainability will shape future trends within the industry as it aligns profitability with environmental responsibility.
Challenges Facing Automotive Parts Manufacturers
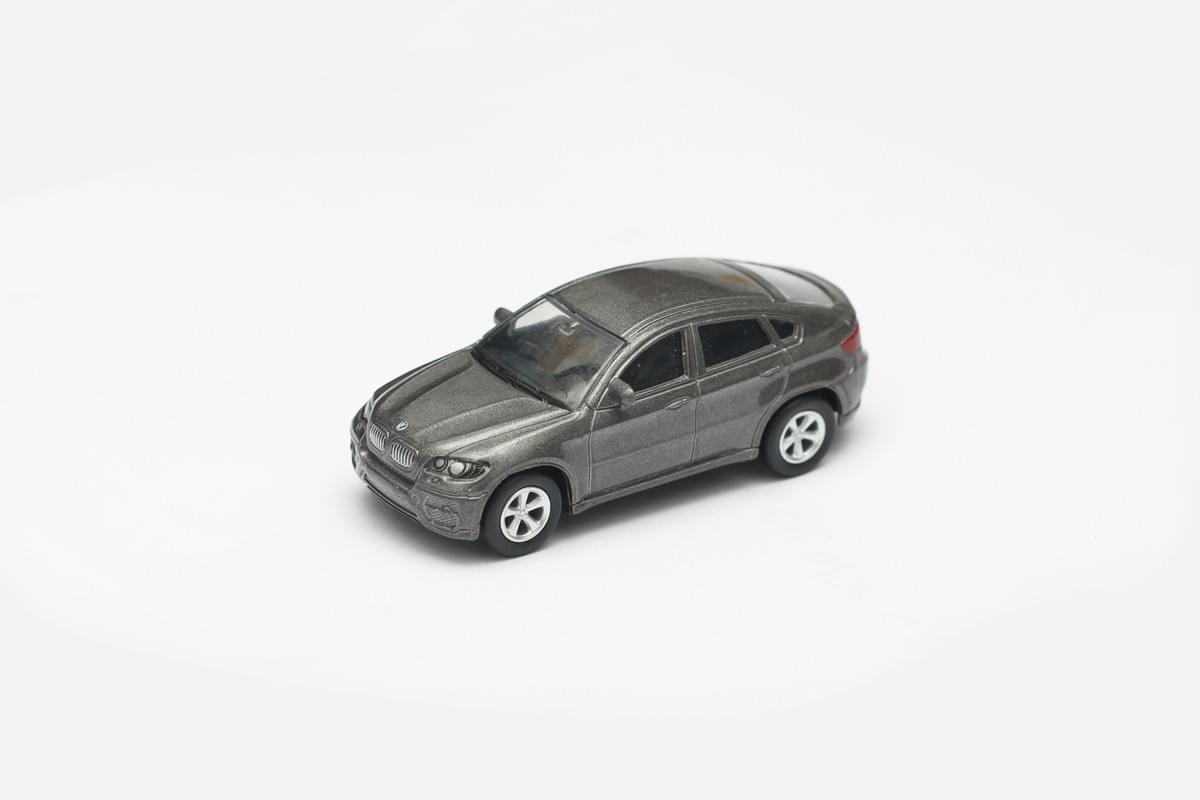
In the rapidly evolving landscape of automotive injection molding, manufacturers face a myriad of challenges that can significantly impact their operations and product quality. From selecting the right materials to navigating fierce competition, these hurdles require strategic approaches to ensure success in the automotive sector. Additionally, regulatory compliance and environmental considerations are increasingly becoming top priorities for automotive parts manufacturers striving to meet market demands while adhering to legal standards.
Material Selection and Performance
One of the foremost challenges in plastic injection molding is choosing the right materials that not only meet performance specifications but also align with cost constraints. Automotive plastic parts must exhibit durability, impact resistance, and temperature stability, which means auto parts manufacturers need to stay updated on advancements in injection moldable plastics. The wrong material choice can lead to failures in performance or aesthetics, ultimately affecting customer satisfaction and brand reputation.
Moreover, as vehicles become more sophisticated with integrated technology and safety features, the demand for high-performance materials increases. Manufacturers must balance the need for innovative materials with practical considerations like production costs and supply chain limitations. This intricate dance between material selection and performance is a challenge that defines modern automotive injection molding.
Competition and Market Demands
The automotive industry is notoriously competitive, with numerous players vying for market share by producing high-quality plastic auto parts at lower prices. Auto parts manufacturers find themselves under constant pressure to innovate while simultaneously reducing costs—a balancing act that can be tricky when it comes to maintaining quality standards in injection molding processes. As consumer preferences shift toward electric vehicles (EVs) and sustainable practices, companies must adapt quickly or risk being left behind.
Additionally, rapid technological advancements mean that manufacturers need to stay ahead of trends such as lightweight materials or smart components integrated into plastic auto parts. This ever-evolving landscape requires agility from automotive parts manufacturers who must anticipate market demands while keeping production efficient through advanced techniques like automation in injection molding processes. The competition isn't just about price; it's about delivering cutting-edge solutions that resonate with both consumers and OEMs alike.
Regulatory Compliance and Environmental Impact
Navigating the maze of regulatory compliance is another significant challenge facing automotive parts manufacturers today. With increasing scrutiny on environmental impacts associated with production methods—including waste management and emissions—companies engaged in automotive injection molding need robust strategies for sustainability without compromising on quality or efficiency. Regulations vary by region but are increasingly focused on reducing carbon footprints while promoting recycling initiatives within the industry.
Furthermore, staying compliant often requires investments in new technologies or processes which can strain budgets—especially for smaller firms trying to compete against larger players who may have more resources at their disposal. As consumers become more environmentally conscious, there's a growing expectation for auto parts manufacturers to adopt sustainable practices throughout their production cycles—from sourcing raw materials through manufacturing methods all the way to end-of-life recycling solutions for plastic auto parts. Balancing compliance with innovation will be crucial as these challenges continue shaping the future of automotive injection molding.
Conclusion
The world of automotive injection molding is evolving rapidly, driven by technological advancements and market demands. As auto parts manufacturers strive to meet the needs of modern vehicles, the focus on innovation and efficiency becomes paramount. The future promises a blend of cutting-edge materials and methods that will redefine how automotive plastic parts are designed and produced.
Future Trends in Automotive Injection Molding
One prominent trend in automotive injection molding is the increasing use of advanced materials that enhance performance while reducing weight. Manufacturers are exploring new injection moldable plastics that offer better durability and flexibility, catering to the diverse requirements of modern vehicles. Additionally, automation and smart manufacturing processes are set to revolutionize production lines, allowing for faster turnaround times and improved precision in creating plastic auto parts.
The Shift Towards Sustainable Practices
Sustainability is no longer just a buzzword; it’s becoming a core principle for automotive parts manufacturers worldwide. The shift towards sustainable practices involves not only using recycled materials but also developing eco-friendly injection molding processes that minimize waste. As consumers demand greener options, embracing sustainability in automotive injection molding will be crucial for manufacturers looking to maintain their competitive edge.
Key Takeaways for Auto Parts Manufacturers
For auto parts manufacturers navigating the complex landscape of automotive injection molding, several key takeaways emerge. First, staying ahead with innovative technologies and materials can enhance product offerings and meet evolving market demands effectively. Second, prioritizing sustainability in production practices will not only comply with regulatory standards but also resonate with environmentally-conscious consumers seeking reliable automotive plastic parts.