Introduction
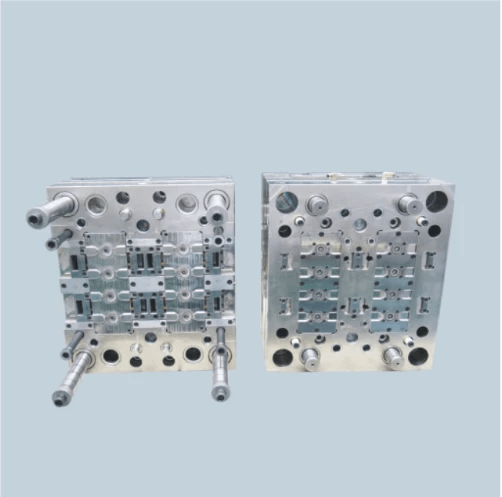
In the world of injection molding, short shots can be a manufacturer’s worst nightmare. A short shot occurs when the molten plastic fails to completely fill the mold cavity, leading to incomplete parts and wasted materials. Understanding short shot injection molding is crucial for anyone involved in production, as it directly impacts quality and efficiency.
Understanding Short Shots in Injection Molding
Short shots are often the result of several underlying issues that can plague the injection molding process. These include insufficient material supply, inadequate mold venting, and fluctuating material temperatures—all of which can lead to premature filling of molds. By grasping what causes these short shots, manufacturers can take proactive steps to prevent them from occurring.
Importance of Mitigating Short Shots
Mitigating short shots is not just about maintaining product quality; it also affects overall production costs and timelines. When parts come out incomplete due to short shot injection molding, it leads to increased scrap rates and additional rework or replacement efforts. Therefore, addressing this issue is vital for maintaining competitive advantage and ensuring customer satisfaction.
Overview of Effective Solutions
So how do you prevent short shots in injection molding? The key lies in optimizing various parameters such as injection speed and material drying techniques while regularly maintaining equipment for peak performance. Additionally, understanding how to fix short shots involves adjusting process parameters or even revising mold designs when necessary—making it essential for manufacturers to be equipped with effective solutions tailored specifically for their operations.
What Causes Short Shot Injection Molding?
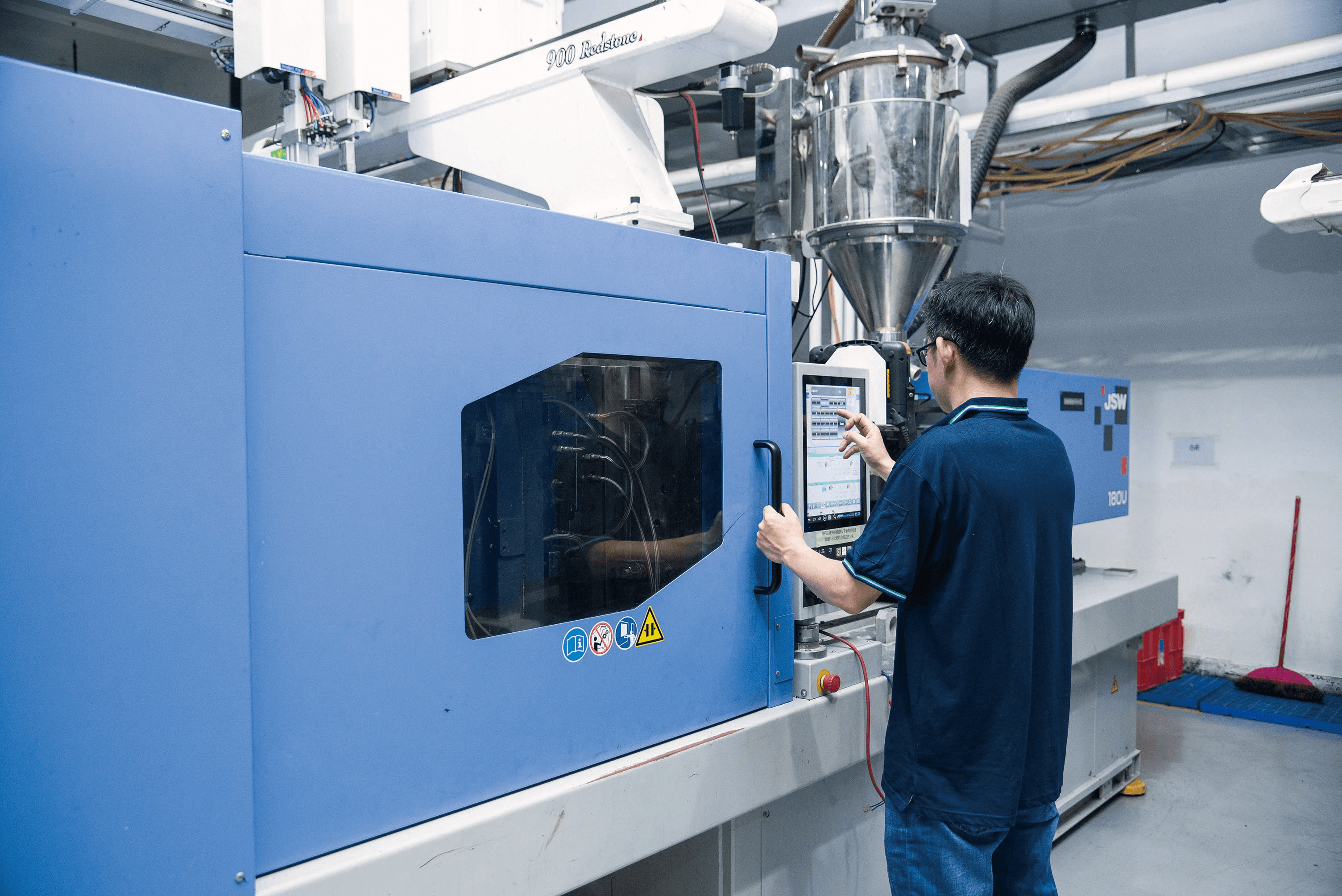
Short shot injection molding occurs when the mold cavity is not completely filled with material, leading to incomplete parts. Understanding the root causes of this issue is crucial for manufacturers aiming to enhance product quality and efficiency. Let’s dive into some of the primary factors that contribute to short shots in injection molding.
Insufficient Material Supply
One of the most common short shot injection molding causes is an insufficient supply of material during the injection process. This can happen if there’s a blockage in the feed system or if the material reservoir runs low, preventing adequate flow into the mold cavity. To prevent short shot issues, it’s essential to monitor material levels and ensure that there’s always enough supply available for each cycle.
Inadequate Mold Venting
Inadequate mold venting can also lead to short shots by trapping air within the mold cavity, which prevents proper filling with molten plastic. When air pockets form, they create pressure imbalances that disrupt material flow and can result in incomplete parts. Addressing this issue often involves improving vent design or adding additional vents to ensure smooth air escape during injection.
Material Temperature Issues
Material temperature plays a critical role in achieving successful injection molding outcomes; if it’s too low, viscosity increases, making it difficult for the molten plastic to fill all areas of the mold effectively. Conversely, excessively high temperatures can lead to degradation of materials before they even enter the mold cavity. Regularly checking and adjusting temperature settings is vital for preventing short shots and ensuring optimal performance throughout production cycles.
How Do You Prevent Short Shot in Injection Molding?
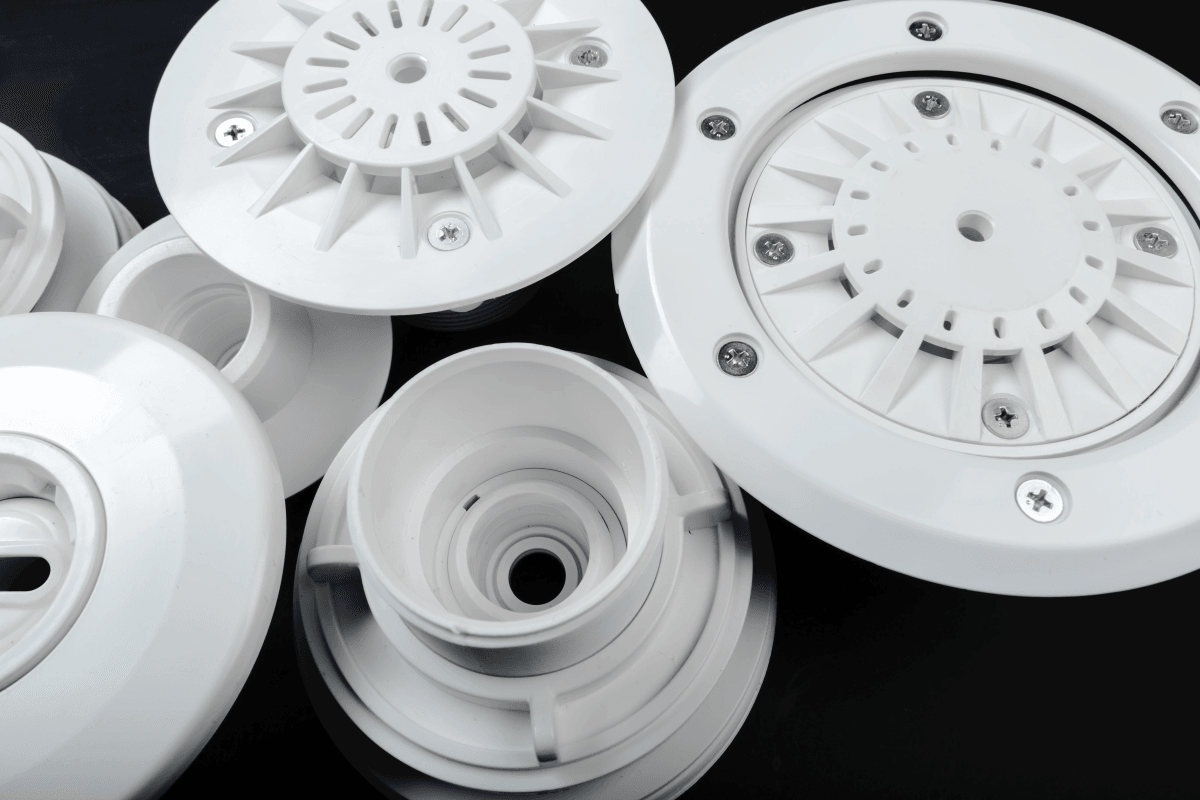
Preventing short shots in injection molding is crucial for producing high-quality parts and maintaining efficiency. By understanding the common causes of short shot injection molding, manufacturers can implement effective strategies to mitigate these issues. Here, we explore three essential methods: optimizing injection speed, ensuring proper material drying, and regularly maintaining equipment.
Optimize Injection Speed
One of the primary solutions to prevent short shots is optimizing injection speed during the molding process. If the injection speed is too slow, it may not fill the mold cavity adequately, leading to incomplete parts or short shots. Conversely, if it’s too fast, it could create turbulence and air entrapment that exacerbate short shot injection molding issues.
To find the sweet spot for injection speed, manufacturers should conduct tests and adjust parameters based on material properties and mold design. This careful calibration not only helps prevent short shots but also enhances overall production efficiency. Remember: a well-timed injection can mean the difference between a full part and a frustrating defect.
Ensure Proper Material Drying
Another key factor in preventing short shots in injection molding lies in ensuring that materials are adequately dried before processing. Moisture content can significantly affect material flow; wet materials may not melt properly or fill molds completely, resulting in what many refer to as a short mold defect.
Implementing proper drying techniques tailored to specific materials can dramatically reduce instances of short shot injection molding caused by moisture-related issues. Regularly checking moisture levels prior to processing will help maintain optimal material conditions for consistent results. After all, a dry material is a happy material!
Regularly Maintain Equipment
Finally, regular maintenance of equipment is vital for preventing short shots in the long run. Worn-out machinery or misaligned components can lead to inconsistent performance during the injection process, increasing the risk of defects like short shots or other related problems.
Establishing a routine maintenance schedule ensures that all parts of your equipment are functioning optimally and reduces unexpected breakdowns during production runs. Keeping an eye on wear-and-tear allows manufacturers to address potential issues before they escalate into costly downtime due to repeated failures from short shot injection molding causes.
How to Fix Short Shots?
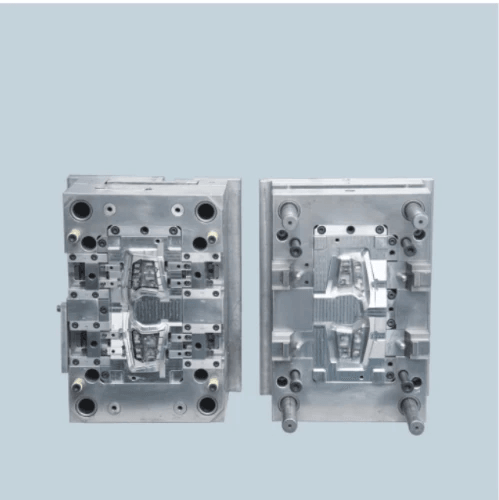
When faced with short shot injection molding, it’s essential to identify effective strategies for resolution. Short shots can lead to significant production issues and increased costs, so understanding how to fix short shots is crucial for maintaining efficiency in manufacturing. Here, we explore three key approaches: adjusting process parameters, revising mold design, and conducting trial runs.
Adjusting Process Parameters
One of the first steps in addressing short shot injection molding is adjusting the process parameters. This includes fine-tuning the injection speed, pressure, and cooling time to ensure that the material fills the mold completely. By making these adjustments, manufacturers can often resolve short shot issues without extensive redesigns or additional expenses.
Additionally, monitoring the temperature of both the material and mold is vital; insufficient heating can lead to material viscosity issues that contribute to short shots. Ensuring optimal conditions allows for better flow of materials into intricate mold designs. Ultimately, a careful balance of these parameters can significantly reduce instances of short shots.
Revising Mold Design
If adjusting process parameters doesn’t yield satisfactory results, it may be time to consider revising the mold design itself. A common cause of short mold defects is inadequate venting or poorly designed gates that restrict material flow during injection molding processes. By reassessing these elements and incorporating features like improved venting systems or strategically placed gates, manufacturers can enhance filling efficiency.
Moreover, analyzing the geometry of the mold can uncover potential design flaws that contribute to incomplete filling. Sometimes even minor tweaks in wall thickness or part complexity can make a world of difference in preventing short shots from occurring again. In essence, a well-thought-out mold design is crucial for mitigating issues related to short shot injection molding.
Conducting Trial Runs
After making adjustments or revisions, conducting trial runs becomes imperative in assessing whether changes have effectively resolved any existing issues with short shots. These trials provide invaluable data on how well new settings or designs perform under real-world conditions while allowing manufacturers to observe any lingering problems firsthand.
During trial runs, it’s essential to analyze results meticulously—look out for patterns indicating recurring causes behind any remaining short molds or defects in production quality. This iterative approach not only helps in fixing current issues but also paves the way for continuous improvement in future projects by identifying best practices tailored specifically for your production line.
Exploring 2 Shot Injection Molding

In the world of injection molding, short shots can be a real headache, but there's a technique that helps mitigate these issues: 2 shot injection molding. This innovative process allows manufacturers to combine two materials or colors in one cycle, enhancing product functionality and aesthetics while reducing the likelihood of defects like short shots. By utilizing this method, companies can not only improve their production efficiency but also create more complex designs that meet modern consumer demands.
Benefits of Dual Injection Techniques
The benefits of dual injection techniques are manifold, particularly when it comes to tackling short shot injection molding problems. First and foremost, this approach allows for better control over material distribution, significantly reducing the chances of encountering short shots during production. Additionally, by combining materials with different properties in one shot, manufacturers can achieve superior strength and durability without the need for separate processes or additional handling.
Moreover, using 2 shot injection molding can streamline manufacturing processes by cutting down on cycle times and reducing waste associated with traditional methods. This efficiency not only saves time but also decreases costs associated with labor and material usage. Ultimately, dual injection techniques offer an effective solution to prevent short shots while enhancing product quality.
Applications in Modern Manufacturing
2 shot injection molding has found its place across various sectors in modern manufacturing due to its versatility and effectiveness in addressing issues like short mold defects. Industries such as automotive often utilize this technique to create complex components that require multiple materials for enhanced performance—think rubber seals combined with rigid plastic parts for improved functionality. Similarly, consumer electronics frequently benefit from dual injections to produce sleek designs that incorporate soft-touch surfaces alongside hard plastics.
Medical device manufacturing also leverages 2 shot injection molding for creating intricate parts that require stringent cleanliness standards and precision—two factors crucial in avoiding defects like short shots or other inconsistencies during production. As technology continues to advance, more industries are likely to adopt this method as they seek innovative ways to enhance their products while minimizing potential pitfalls such as what causes short mold issues.
Comparing Costs and Efficiency
When comparing costs and efficiency between traditional single-shot processes versus 2 shot injection molding techniques, it's essential to consider both initial investment and long-term savings regarding how do you prevent short shots in injection molding? While the equipment required for dual injections may have a higher upfront cost due to complexity, the return on investment is often realized through reduced cycle times and lower defect rates—effectively addressing how to fix short shots?
Furthermore, producing multi-material components in one go eliminates secondary operations typically needed after single-shot production; this not only cuts costs but also minimizes handling errors that could lead back into the realm of short mold defects. In summary, while there may be an initial financial hurdle when adopting 2 shot techniques compared to traditional methods focused on fixing existing problems like short shots or material flow issues, the overall efficiency gains make it a worthy consideration for many manufacturers looking towards future growth.
Addressing Short Mold Defects
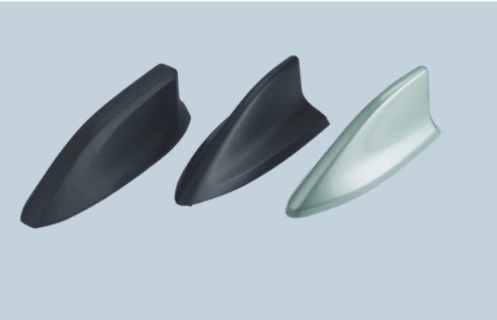
Short mold defects can be a significant issue in the world of injection molding, particularly when they lead to short shot injection molding scenarios. These defects not only affect the quality of the final product but can also lead to increased production costs and wasted materials. Understanding how to identify these design flaws, improve mold design, and implement effective quality control measures is crucial for any manufacturer seeking to enhance their processes.
Identifying Design Flaws
The first step in addressing short mold defects is identifying the underlying design flaws that may be causing them. Common issues include inadequate gate placement, insufficient draft angles, and poor cooling channel design, all of which can contribute to short shot injection molding problems. By analyzing these aspects during the initial stages of mold development, manufacturers can pinpoint what is the cause of short molds before they become costly production issues.
Furthermore, it’s essential to review past production runs for patterns that may indicate recurring design flaws. If certain products consistently exhibit short shots or other defects, it’s time for a deeper investigation into your mold designs and processes. This proactive approach not only saves time but also helps in determining how do you prevent short shot in injection molding from becoming a habitual problem.
Techniques for Mold Design Improvement
Once design flaws are identified, implementing effective techniques for mold design improvement becomes paramount. One method is optimizing gate locations to ensure even material distribution during the injection process; this minimizes risks associated with short shot injection molding causes like uneven flow paths or cold spots within the mold cavity. Additionally, introducing features like vents or risers can help facilitate better air evacuation and material flow.
Another significant technique involves refining cooling channels within the mold itself; ensuring uniform cooling helps maintain consistent temperatures throughout the molded part. This practice aids in preventing thermal-related issues that could lead to defects such as warping or incomplete filling—common culprits behind how to fix short shots effectively. Regularly reviewing and updating your mold designs based on feedback from trial runs will keep your manufacturing process agile and responsive.
Quality Control Measures
Implementing robust quality control measures is essential for catching potential issues before they escalate into larger problems like short shot injection molding scenarios or other defects arising from poor molds. Regular inspections during both pre-production setup and ongoing operations are vital practices that should not be overlooked; this includes checking material consistency and verifying machine settings against established standards.
Moreover, employing statistical process control (SPC) methods can provide valuable insights into production trends over time—allowing teams to quickly react if deviations occur that could signal an impending defect situation like a short shot injection molding incident due to equipment failure or material variability. Training staff on recognizing early warning signs further enhances your ability to maintain high-quality standards while reducing waste associated with defective products.
In summary, addressing short mold defects requires a multifaceted approach involving identification of design flaws, improvement techniques tailored for specific challenges faced by molds today, and stringent quality control measures that keep your operations running smoothly while minimizing costs associated with rework or scrap parts.
Conclusion
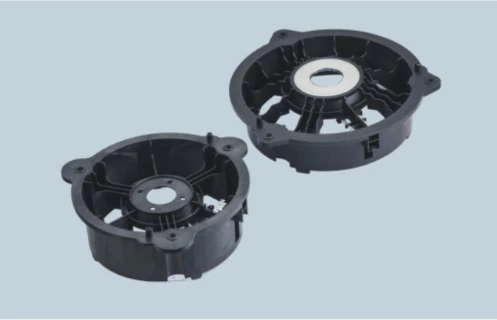
In the world of injection molding, short shots can be an unwelcome surprise, leading to wasted materials and time. Understanding the causes of short shot injection molding is crucial for manufacturers aiming to produce high-quality parts efficiently. By implementing effective strategies, such as optimizing injection speed and ensuring proper material drying, companies can mitigate these issues significantly.
Key Takeaways on Mitigating Short Shots
To prevent short shots in injection molding, it’s essential to address common culprits like insufficient material supply and inadequate mold venting. Regular equipment maintenance plays a vital role in keeping the process smooth and efficient, thus avoiding costly errors. Remember, understanding how to fix short shots is just as important as preventing them; adjusting process parameters can make all the difference.
Future Trends in Injection Molding
The future of injection molding is looking bright with advancements in technology such as 2 shot injection molding gaining traction. This technique not only enhances product functionality but also reduces production times by combining two materials into one part seamlessly. As manufacturers continue to innovate and refine their processes, addressing issues like short mold defects will become increasingly sophisticated.
Insights from the Baoyuan Team on Best Practices
The Baoyuan Team emphasizes that a proactive approach is key when dealing with short shot injection molding causes. By continuously revising mold designs and conducting trial runs, manufacturers can identify potential problems before they escalate into larger issues. Their best practices highlight that investing time in quality control measures leads to long-term savings and improved product quality.