Introduction
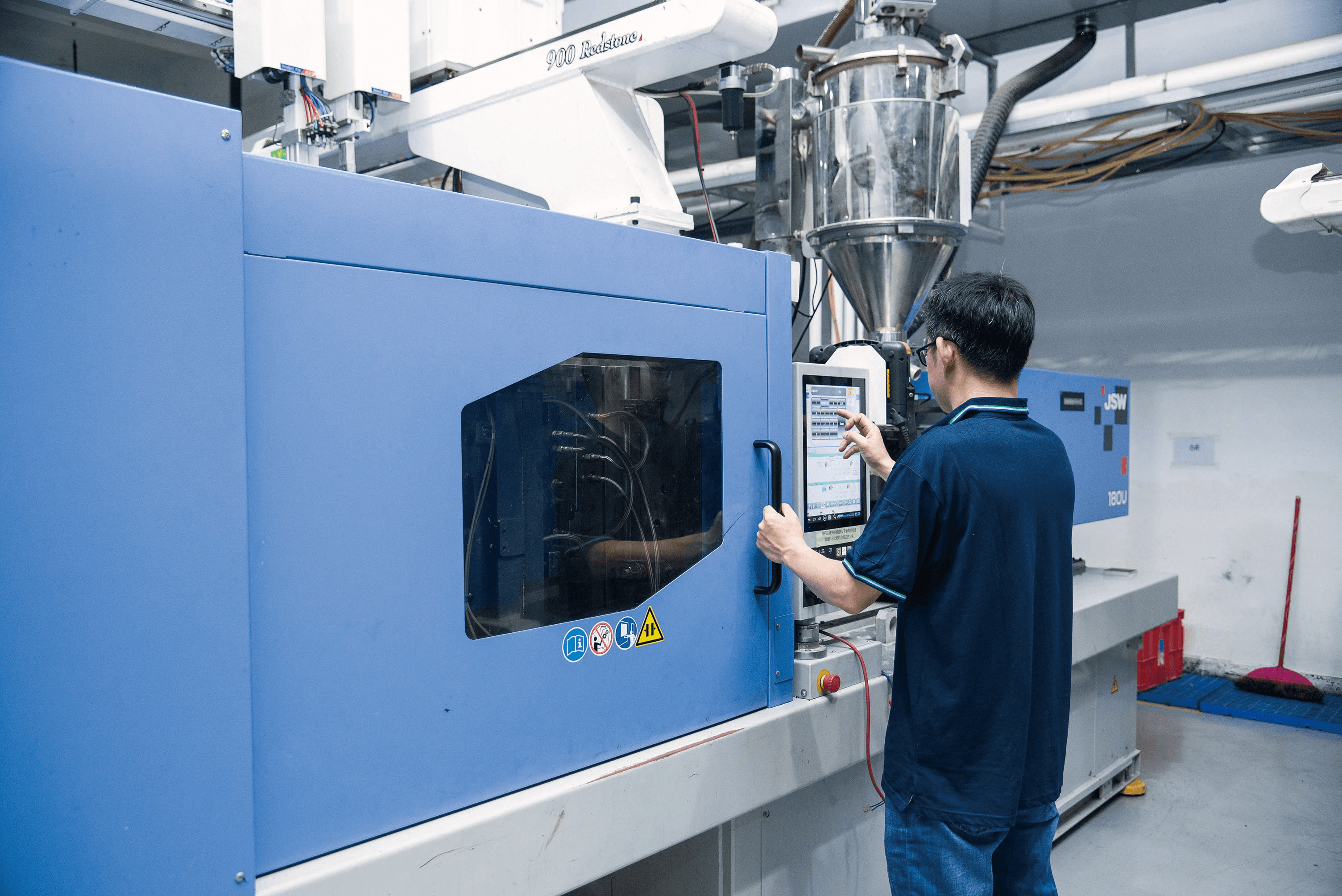
In the world of manufacturing, liquid injection molding has emerged as a game-changing technique, particularly for producing intricate parts with precision and efficiency. This innovative method allows for the seamless integration of materials like liquid silicone rubber (LSR), which is renowned for its versatility and durability. As industries continue to evolve, understanding what is the process of liquid injection molding becomes essential for anyone looking to stay ahead in production technology.
Understanding Liquid Injection Molding
Liquid injection molding is a specialized process that involves injecting liquid materials into a mold to create various products. This technique is particularly effective when working with materials such as LSR, which offers unique properties that enhance product performance. By grasping the nuances of this method, manufacturers can optimize their operations and produce high-quality components tailored to specific applications.
Key Benefits of Liquid Injection Molding
The key benefits of liquid injection molding include increased design flexibility, reduced waste, and enhanced production speed. With this method, manufacturers can create complex geometries that would be challenging or impossible with traditional methods. Additionally, the silicone injection molding process allows for rapid prototyping and high-volume production without compromising quality.
Why Choose Liquid Silicone Rubber?
Choosing liquid silicone rubber (LSR) offers numerous advantages over other materials like room temperature vulcanizing (RTV) silicones. LSR is known for its excellent thermal stability, chemical resistance, and biocompatibility—making it an ideal choice for medical devices and consumer goods alike. Moreover, understanding what is the difference between RTV and LSR can help businesses make informed decisions about material selection based on their specific needs.
What is Liquid Injection Molding?
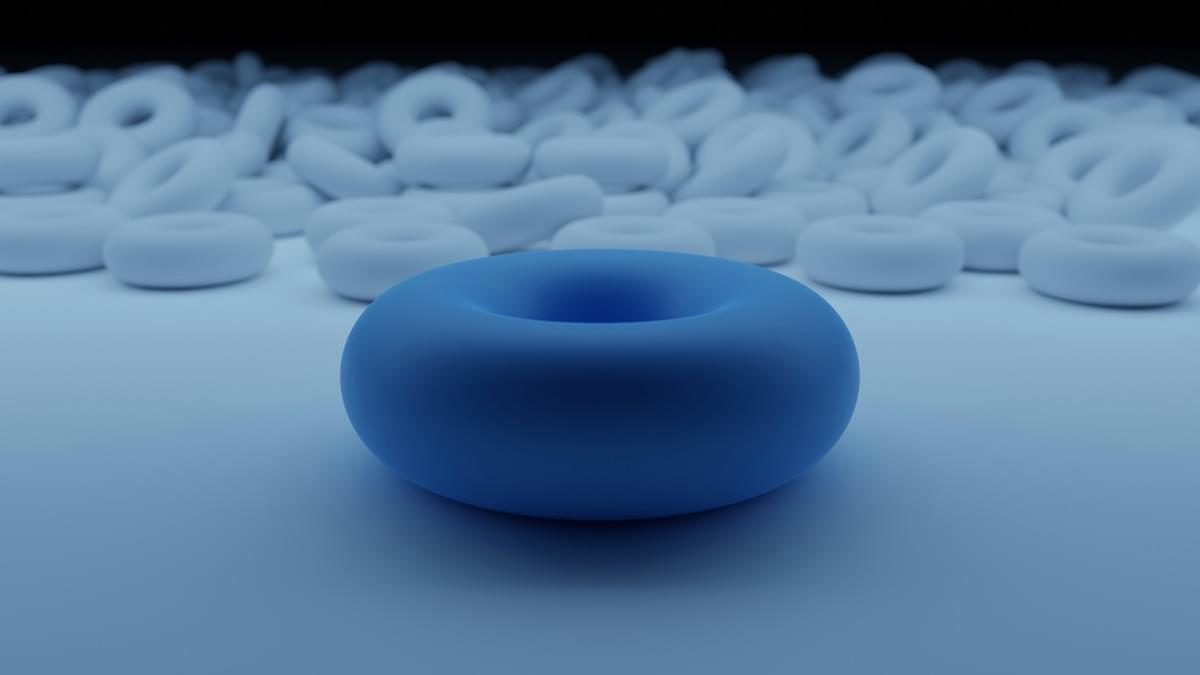
Liquid injection molding is an innovative manufacturing technique that allows for the precise shaping of liquid silicone rubber (LSR) into various forms and components. This process utilizes a silicone injection molding machine to inject liquid silicone into molds, creating parts with exceptional detail and durability. With its efficiency and versatility, liquid injection molding has become a go-to method in many industries.
Overview of the Process
The process of liquid injection molding begins with the preparation of liquid silicone rubber, which is then heated and mixed to achieve optimal viscosity. Once ready, the silicone is injected into a closed mold using a specialized silicone injection molding machine under controlled pressure and temperature conditions. After cooling and curing, the mold opens to reveal the finished product, showcasing the precision that this method can achieve.
Key Components Involved
Several key components are essential for effective liquid injection molding. The primary elements include the silicone injection molding machine, which features a heated barrel for mixing and injecting LSR; molds that define the shape of the final product; and cooling systems that ensure quick solidification of injected materials. Together, these components work harmoniously to facilitate what is known as the LSR method—an efficient way to produce high-quality silicone parts.
Common Applications in Industry
Liquid injection molding finds applications across various industries due to its flexibility and efficiency in producing complex shapes. Common uses include manufacturing medical devices like seals or gaskets, automotive parts such as weather stripping or connectors, and consumer goods like kitchenware or electronics housings. As industries continue to innovate, understanding what is the process of liquid injection molding becomes increasingly important for developing new products while maintaining high standards.
What is the Process of Liquid Injection Molding?
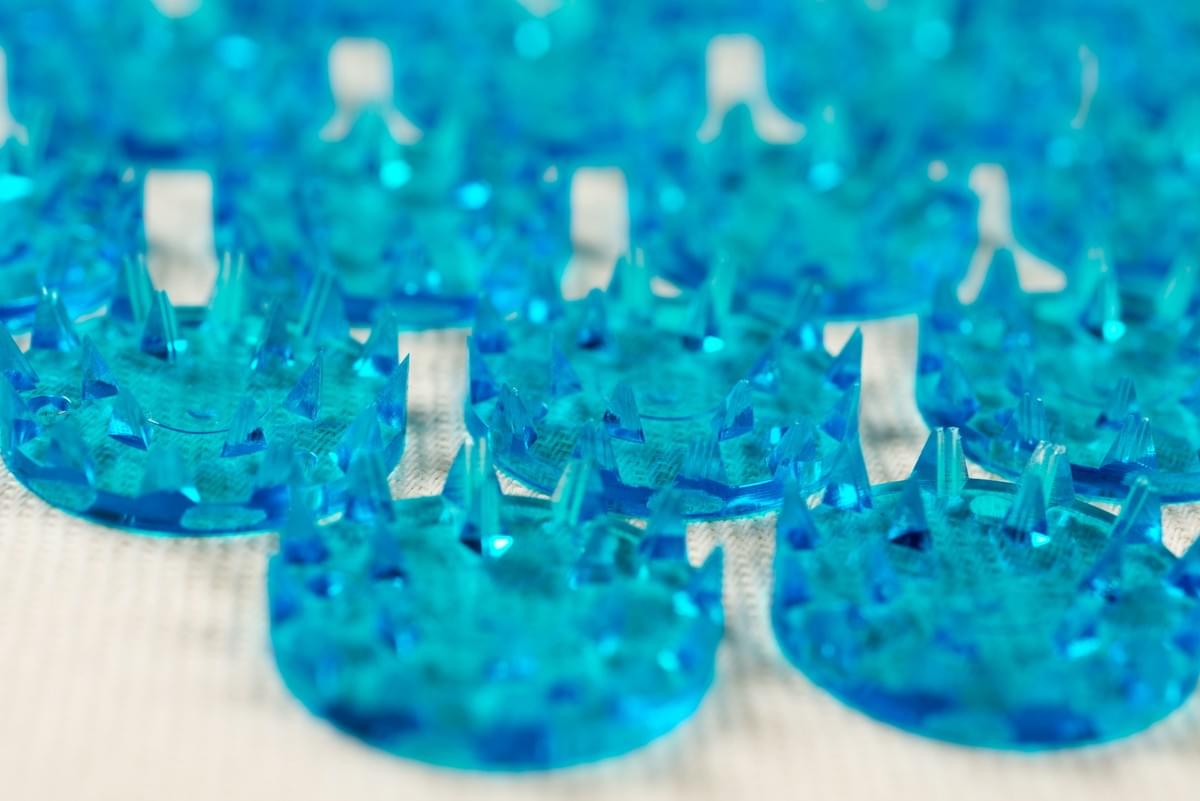
Liquid injection molding is a sophisticated procedure that transforms liquid silicone rubber (LSR) into high-quality products through a series of systematic steps. Understanding this process is crucial for those looking to leverage the benefits of liquid injection molding, especially when it comes to applications requiring precision and durability. From the initial mixing of materials to the final curing phase, each step plays a vital role in ensuring optimal results.
Step-by-Step Breakdown of the Process
The process begins with preparing the liquid silicone rubber, where two components—base polymer and curing agent—are carefully mixed in precise ratios. This mixture is then fed into a silicone injection molding machine, where it is heated and pressurized before being injected into a mold cavity. Once injected, the silicone undergoes curing, solidifying into its final shape while retaining its unique properties.
Following curing, the molds are opened to release the finished product. The entire process can be repeated quickly for high-volume production runs, making it ideal for industries needing consistent quality across numerous units. Understanding these steps helps clarify what is the process of liquid injection molding and why it's favored for producing intricate designs.
Role of the Silicone Injection Molding Machine
At the heart of liquid injection molding lies the silicone injection molding machine, which plays an indispensable role in maintaining efficiency and precision throughout production. This specialized equipment ensures that LSR is heated to optimal temperatures before being injected into molds under controlled pressure conditions. The machine's design allows for quick cycle times while maintaining consistent quality in every batch produced.
Moreover, modern machines often come equipped with advanced features such as temperature control systems and automated processes that enhance productivity further. These innovations ensure that manufacturers can keep pace with market demands while adhering to strict quality standards inherent in industries like automotive or medical devices—where understanding what is the LSR method becomes critical for success.
Quality Control Measures
Quality control measures are paramount throughout every stage of liquid injection molding to ensure that products meet industry specifications and customer expectations. Techniques such as regular monitoring of temperature and pressure during processing help maintain consistency across batches while identifying any potential issues early on in production cycles.
Additionally, post-mold inspections are conducted using various methods including visual checks and advanced testing technologies like ultrasound or X-ray imaging to detect defects or inconsistencies within finished parts. By implementing robust quality control measures alongside an efficient silicone injection molding process, manufacturers can confidently deliver products that stand out in terms of reliability and performance.
What is the Difference Between RTV and LSR?
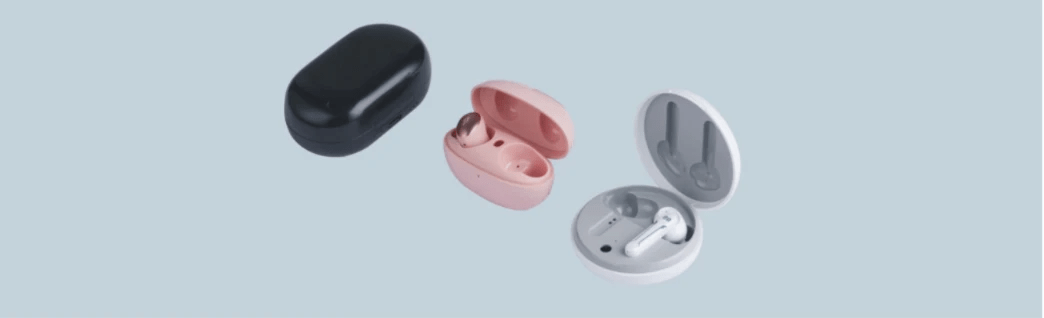
When diving into the world of silicone materials, two prominent types often come up: Room Temperature Vulcanizing (RTV) silicone and Liquid Silicone Rubber (LSR). Understanding the nuances between these two can greatly influence your choice in applications, particularly in processes like liquid injection molding. So, what is the difference between RTV and LSR? Let’s break it down.
Defining RTV and LSR Concepts
RTV silicone is a type of silicone that cures at room temperature, making it a go-to choice for quick repairs or mold-making projects. It's typically available in two-part systems where a catalyst is mixed with a base to initiate curing. On the other hand, LSR is designed for high-performance applications and requires heat to cure, which allows it to be processed through methods like liquid injection molding.
The versatility of RTV makes it ideal for smaller-scale projects or prototyping, while LSR shines when high-volume production is needed due to its efficient curing process. Both types have their own unique advantages and are favored in different scenarios based on project requirements. However, understanding their core differences can help you make informed decisions regarding what is the process of liquid injection molding or what is the process of LSR.
Comparison of Properties and Uses
When comparing properties, RTV generally has a lower tensile strength than LSR but offers excellent flexibility and ease of use for small applications. In contrast, LSR boasts superior mechanical properties including higher tensile strength and tear resistance, making it suitable for demanding environments like automotive parts or medical devices. The ability to withstand extreme temperatures also sets LSR apart in industrial settings where reliability is paramount.
In terms of uses, RTV finds its niche in crafts, molds for casting materials like resin or plaster, while LSR dominates industries requiring precision parts such as seals or gaskets created through processes like silicone injection molding. Furthermore, because of its fast curing time when heated properly during manufacturing processes such as liquid injection molding, LSR significantly reduces cycle times compared to RTV options.
Industry Preferences for Each Type
Industry preferences often lean towards using LSR due to its compatibility with high-speed production techniques like liquid injection molding that require rapid turnaround times without sacrificing quality. Many manufacturers favor this method because it allows them to produce large quantities efficiently while maintaining consistent product integrity throughout each batch produced by machines specifically designed for silicone injection molding processes.
Conversely, RTV remains popular among hobbyists and small businesses that prioritize ease-of-use over mass production capabilities; it's an accessible option without needing specialized equipment like a silicone injection molding machine. Ultimately, your choice between these two will depend on factors such as project scale, required performance characteristics, and whether you're asking yourself how to mold liquid silicone effectively.
What is the Process of LSR?
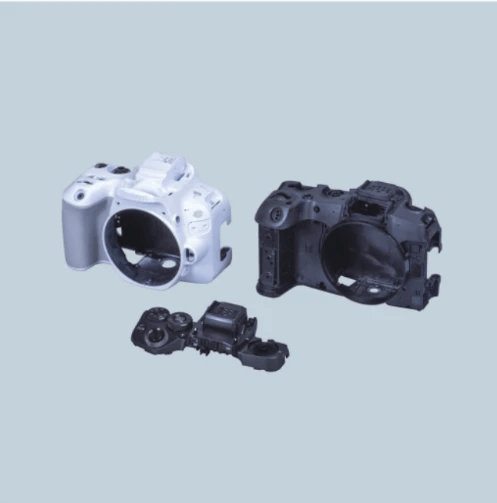
Liquid Silicone Rubber (LSR) processing is a specialized method within the realm of liquid injection molding, designed to create precision parts with exceptional quality and durability. This method leverages the unique properties of silicone to produce flexible, heat-resistant components that can withstand harsh environments. Understanding what is the process of LSR involves delving into its specific steps, advantages, and suitability for high-volume production.
Detailed Analysis of LSR Procedure
The process of LSR begins with two-component materials—base silicone and a curing agent—being precisely mixed in a silicone injection molding machine. Once mixed, this viscous material is injected into a mold under high pressure, allowing it to fill intricate designs and cavities effectively. After sufficient curing time within the mold, the finished product is ejected, showcasing the remarkable detail achievable through this innovative silicone injection molding process.
Key stages in what is the process of liquid injection molding include preparation, mixing, injection, curing, and demolding. Each step requires careful monitoring to ensure optimal performance and quality control throughout production. By understanding these stages in detail, manufacturers can better appreciate how to mold liquid silicone effectively while minimizing defects or inconsistencies in their products.
Advantages of Using LSR
One significant advantage of using Liquid Silicone Rubber lies in its outstanding thermal stability; it can withstand extreme temperatures without losing its structural integrity or flexibility. Moreover, LSR offers excellent chemical resistance which makes it suitable for various applications across industries such as automotive and medical devices. The rapid cure times associated with LSR also enhance productivity by enabling faster cycle times compared to traditional materials.
In addition to these benefits, manufacturers often find that using LSR reduces waste due to its precise nature during the silicone injection molding process. The ability to produce complex geometries without compromising strength or durability adds another layer of appeal for engineers seeking innovative solutions in product design. Thus, understanding what is the difference between RTV (Room Temperature Vulcanization) and LSR becomes essential when choosing materials for specific applications.
LSR in High-Volume Production
When considering high-volume production scenarios, Liquid Silicone Rubber stands out as an ideal choice due to its efficiency and repeatability within manufacturing processes like liquid injection molding. The streamlined procedure allows companies to scale up their output without sacrificing quality or precision—an essential factor for meeting market demands consistently. Furthermore, advancements in technology have enhanced silicone injection molding machines' capabilities, making them more adept at handling large quantities while maintaining rigorous standards.
The adaptability offered by LSR enables manufacturers not only to meet current production needs but also prepare for future innovations that may arise within their industries. As businesses increasingly seek sustainable solutions that minimize waste while maximizing efficiency—LSR's role will likely expand further across various sectors looking for reliable materials that perform under pressure (literally!).
In summary, exploring what is the process of LSR reveals numerous advantages over traditional methods like RTV while highlighting its pivotal role in high-volume production scenarios where speed meets precision seamlessly.
How to Mold Liquid Silicone?
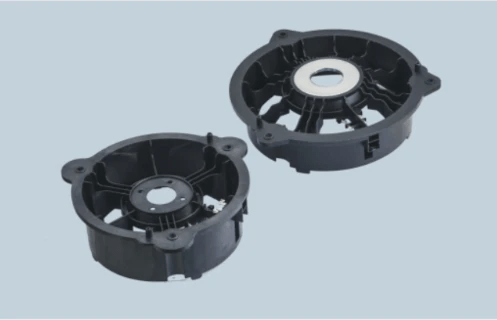
Molding liquid silicone is an art and a science, combining precision with creativity. This process, often referred to as liquid injection molding, involves several essential techniques that ensure high-quality results. Understanding these techniques can significantly enhance the efficiency and effectiveness of your silicone injection molding process.
Essential Techniques for Effective Molding
To master how to mold liquid silicone, it’s crucial to understand the role of temperature control in the silicone injection molding machine. Maintaining optimal temperatures ensures that the liquid silicone flows smoothly into the mold without any interruptions or defects. Additionally, utilizing proper mold design—such as incorporating vents and ensuring adequate draft angles—can significantly improve the overall quality and consistency of your final products.
Another key technique is the precise timing of injection cycles during the liquid injection molding process. This includes understanding when to inject the liquid silicone and how long to maintain pressure in the mold before cooling begins. By calibrating these timings accurately, you can reduce cycle times and enhance production efficiency while ensuring that each molded part meets stringent quality standards.
Lastly, selecting appropriate additives or colorants can also influence both aesthetic appeal and functional properties of molded parts. These enhancements should be compatible with liquid silicone rubber (LSR), which leads us into a deeper understanding of what is the process of LSR? The right combination of techniques will not only streamline production but also elevate your products' marketability.
Troubleshooting Common Issues
Even seasoned professionals encounter challenges when working with liquid silicone rubber in their molding processes. One common issue is air entrapment; this occurs when air bubbles become trapped within the molded part due to improper venting or rapid injection speeds during what is known as the LSR method. To combat this problem, ensure that your molds are designed with adequate venting channels and adjust your injection speed accordingly.
Another frequent challenge involves incomplete filling of molds, which can occur if there isn’t enough pressure applied during injection or if there are blockages in flow paths within complex molds. Regular inspections and maintenance of your silicone injection molding machine are essential for preventing such issues from arising in the first place.
Lastly, surface imperfections like blemishes or uneven textures can detract from product quality; these may arise from contamination or incorrect curing conditions during what is the process of liquid injection molding? Ensuring a clean workspace and closely monitoring curing times will help maintain high-quality standards throughout production.
Best Practices for Optimal Results
Achieving optimal results in how to mold liquid silicone requires adherence to best practices throughout every stage of production. First off, always ensure that you’re using high-quality raw materials suited for your specific application; this directly affects both performance and durability in end products produced via LSR methods.
Regularly calibrating your silicone injection molding machine is another vital practice that cannot be overlooked; even minor deviations can lead to significant variations in product quality over time. Implementing routine maintenance checks will keep machinery running smoothly while minimizing downtime caused by unexpected breakdowns.
Finally, fostering open communication among team members involved in different stages—from design engineers to production staff—will help identify potential issues early on while sharing insights for continuous improvement across all aspects related to what is the difference between RTV and LSR? Establishing a culture focused on quality assurance will pay dividends by producing reliable products that meet customer expectations consistently.
Conclusion
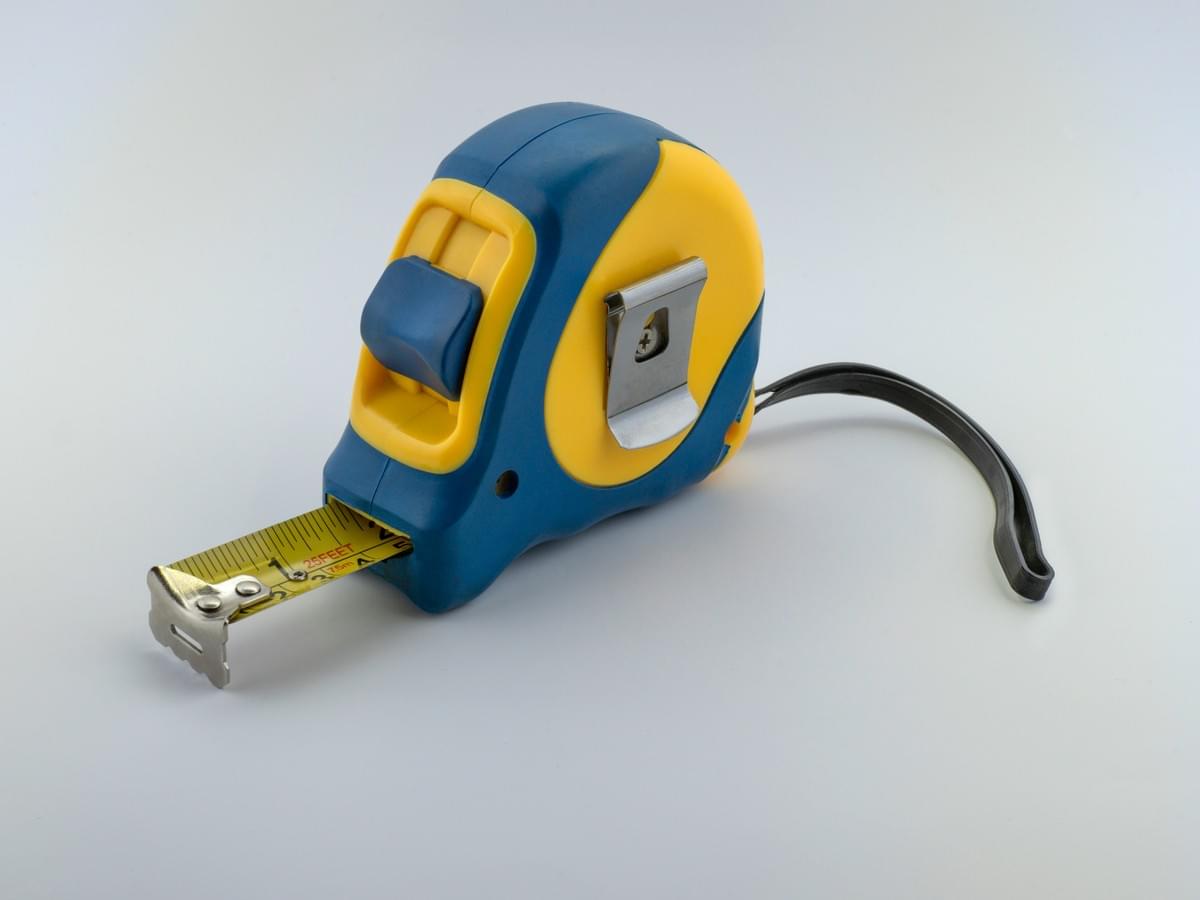
As we wrap up our exploration of liquid injection molding, it's clear that mastering this process opens the door to a world of innovative manufacturing possibilities. Understanding the nuances of liquid injection molding, including what is the process of liquid injection molding? and how it differs from other methods, can significantly enhance production efficiency and product quality. The versatility offered by materials like Liquid Silicone Rubber (LSR) makes it an attractive option for various industries, ensuring that your products not only meet but exceed market expectations.
Mastering the Liquid Injection Molding Process
To truly master the liquid injection molding process, one must grasp its intricacies—from understanding what is the difference between RTV and LSR? to navigating through the silicone injection molding process itself. Each element plays a vital role in achieving optimal results, whether you’re working on prototypes or high-volume production runs. Familiarity with how to mold liquid silicone effectively can prevent common pitfalls and elevate your manufacturing game.
Innovative Applications and Future Trends
The landscape of liquid injection molding is ever-evolving, with new applications emerging in sectors like automotive, medical devices, and consumer electronics. As we delve into what is the process of LSR?, we see that advancements in technology are paving the way for even more innovative uses—think smart devices or sustainable solutions using eco-friendly materials. Keeping an eye on future trends will not only keep you competitive but also inspire creative applications that push boundaries.
Partnering with Experts like Baoyuan
When it comes to mastering techniques such as how to mold liquid silicone or understanding what is the LSR method?, partnering with industry experts like Baoyuan can be a game changer. Their experience with state-of-the-art silicone injection molding machines ensures you have access to cutting-edge technology and best practices tailored to your specific needs. Collaborating with seasoned professionals helps streamline processes while also providing insights into overcoming challenges within the silicone injection molding process.