Introduction
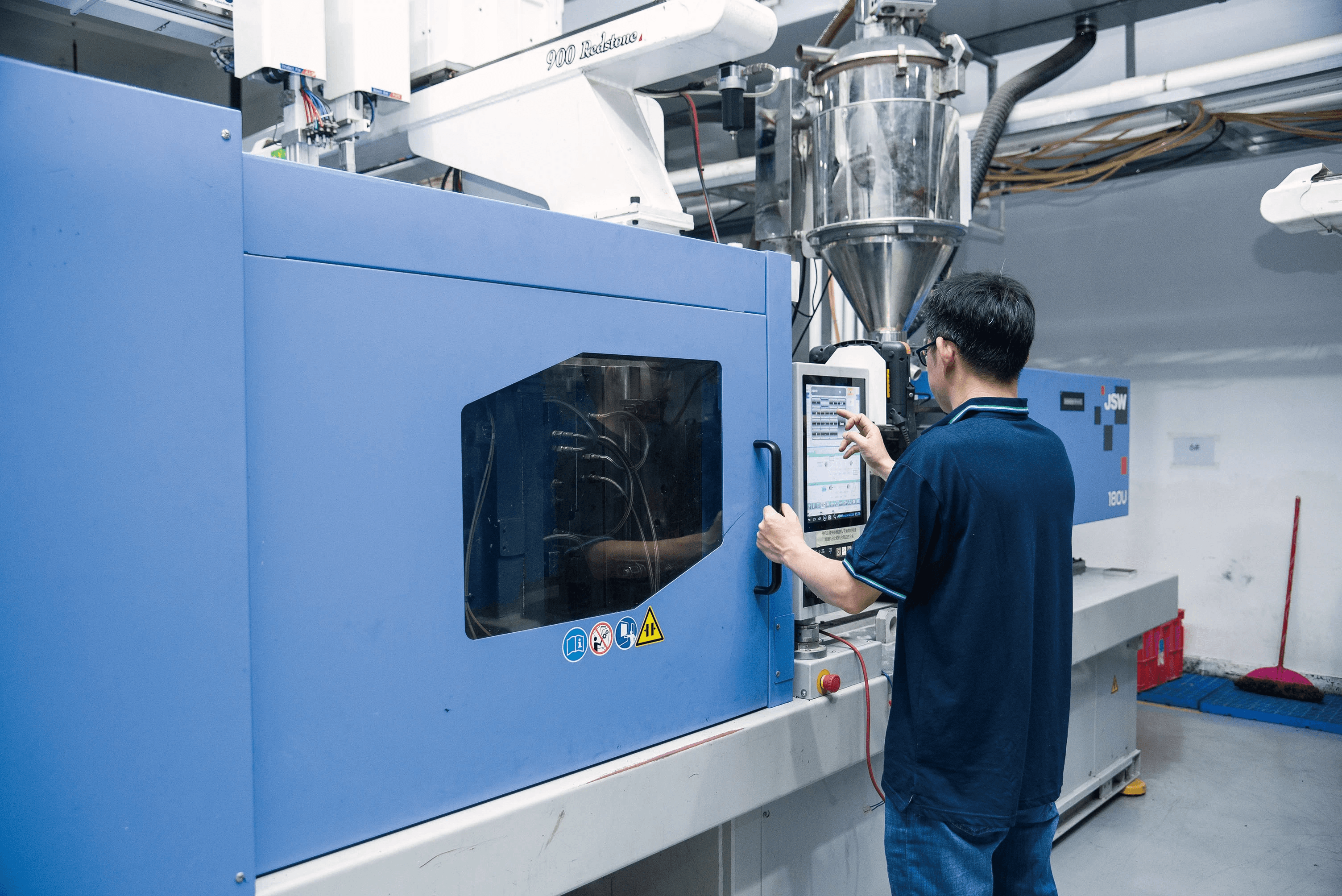
Large injection molding is a fascinating and essential process in the manufacturing world, enabling the production of oversized plastic components with precision and efficiency. This technique caters to various industries, from automotive to aerospace, where large parts are crucial for functionality and performance. As we delve into this topic, we'll also explore foam injection molding—a specialized method that adds a new dimension to large-scale production.
What is Large Injection Molding?
Large injection molding refers to the process of creating substantial plastic parts by injecting molten material into a custom-designed mold. Unlike traditional injection molding, which often focuses on smaller components, this method is specifically tailored for larger items that require robust design and durability. It plays a vital role in industries where size matters, leading to innovations that push the boundaries of what's possible in manufacturing.
Applications of Large Injection Molding
The applications of large injection molding are vast and varied, encompassing sectors such as automotive manufacturing, construction equipment production, and even consumer goods. For instance, large components like vehicle bumpers or housing for industrial machinery are often produced using this technique due to its ability to create complex shapes with high strength-to-weight ratios. Moreover, as industries evolve and demand increases for larger products—like tanks or enclosures—large injection molding continues to be at the forefront of meeting these requirements.
Exploring Foam Injection Molding
Foam injection molding takes large injection molding a step further by incorporating gas into the polymer during processing, resulting in lightweight yet strong components through structural foam injection techniques. This innovative approach not only reduces material costs but also enhances thermal insulation properties—making it ideal for applications requiring both durability and energy efficiency. As manufacturers seek ways to optimize their processes while maintaining quality standards, foam injection molding stands out as an effective solution worth exploring.
Understanding Large Injection Molding
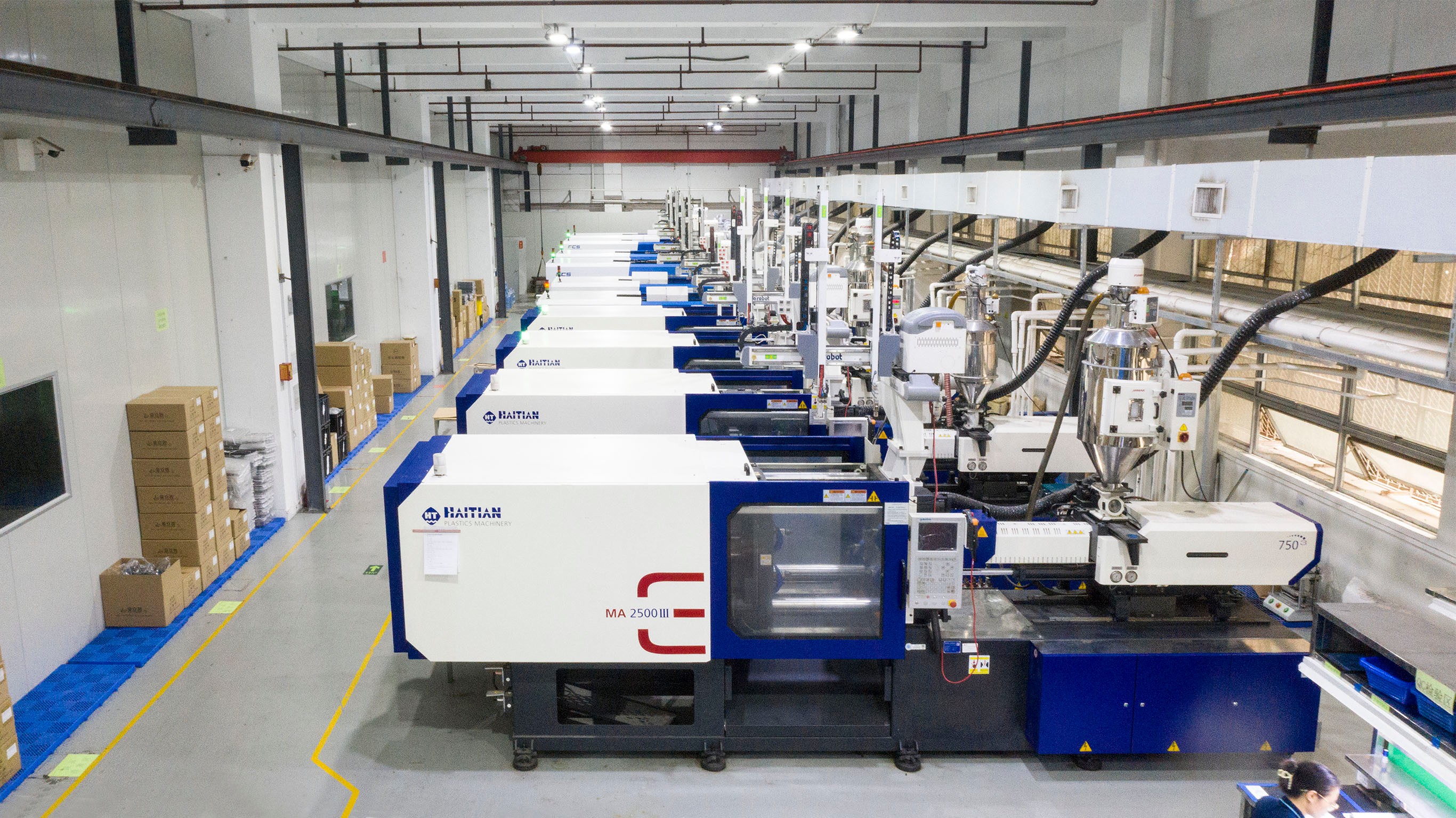
Large injection molding is a fascinating process that allows manufacturers to create substantial and complex parts with precision. This technique stands out for its ability to produce large components consistently, making it a go-to solution for many industries. As we delve deeper, let's explore the key benefits of this method, the industries that rely on it, and the common materials used.
Key Benefits of Large Injection Molding
One of the most significant advantages of large injection molding is its efficiency in producing high-volume parts with minimal waste. With advanced technology like foam injection molding and structural foam injection, manufacturers can achieve lightweight yet sturdy components, reducing material costs while maintaining quality. Additionally, large injection molding allows for intricate designs and features that are difficult to replicate through other manufacturing methods.
Another benefit is the scalability of production; once a mold is created, it can be used repeatedly to produce thousands or even millions of identical parts. This consistency not only helps in maintaining quality but also optimizes production timelines. Moreover, large injection molding offers flexibility in design modifications, enabling companies to adapt quickly to changing market demands without significant downtime.
Lastly, when considering large injection molding cost factors such as labor and overhead are generally lower compared to alternative methods like machining or hand assembly. This makes it an attractive option for businesses looking to maximize their return on investment while minimizing production expenses.
Industries Utilizing Large Injection Molding
Large injection molding finds applications across various sectors due to its versatility and efficiency in producing sizable components. The automotive industry heavily relies on this process for creating parts like bumpers, dashboards, and other structural elements that require both strength and precision. Similarly, the aerospace sector utilizes large injection molded components for everything from interior fittings to critical structural parts.
Beyond automotive and aerospace applications, industries such as consumer goods frequently employ large injection molding techniques for items like containers or furniture pieces that need durability without compromising aesthetics. Medical device manufacturers also benefit from this technology by creating robust housings or specialized equipment designed for high-performance environments.
In addition to these traditional sectors, emerging fields such as renewable energy are starting to harness the capabilities of large injection molding too—think wind turbine blades or solar panel frames made from lightweight yet durable materials via structural foam injection techniques.
Common Materials for Large Injection Molding
Thermoplastics are among the most common choices due to their ease of processing; they can be melted down multiple times without degrading—perfectly aligning with how large you can injection mold! Polypropylene (PP) and polycarbonate (PC) are popular thermoplastics used extensively across different industries.
For applications requiring enhanced strength-to-weight ratios or thermal resistance properties, engineers often turn towards reinforced plastics infused with glass fibers or carbon fibers during the mold creation process—ideal candidates when considering why is injection moulding not suitable for larger products? These reinforcements help mitigate some challenges associated with larger molds while ensuring product integrity remains intact.
Additionally, foam materials play a crucial role in enhancing performance characteristics through processes like foam injection molding or structural foam injections; these methods create lightweight structures ideal for reducing shipping costs while maintaining strength standards necessary in demanding environments.
How Large Can You Injection Mold?
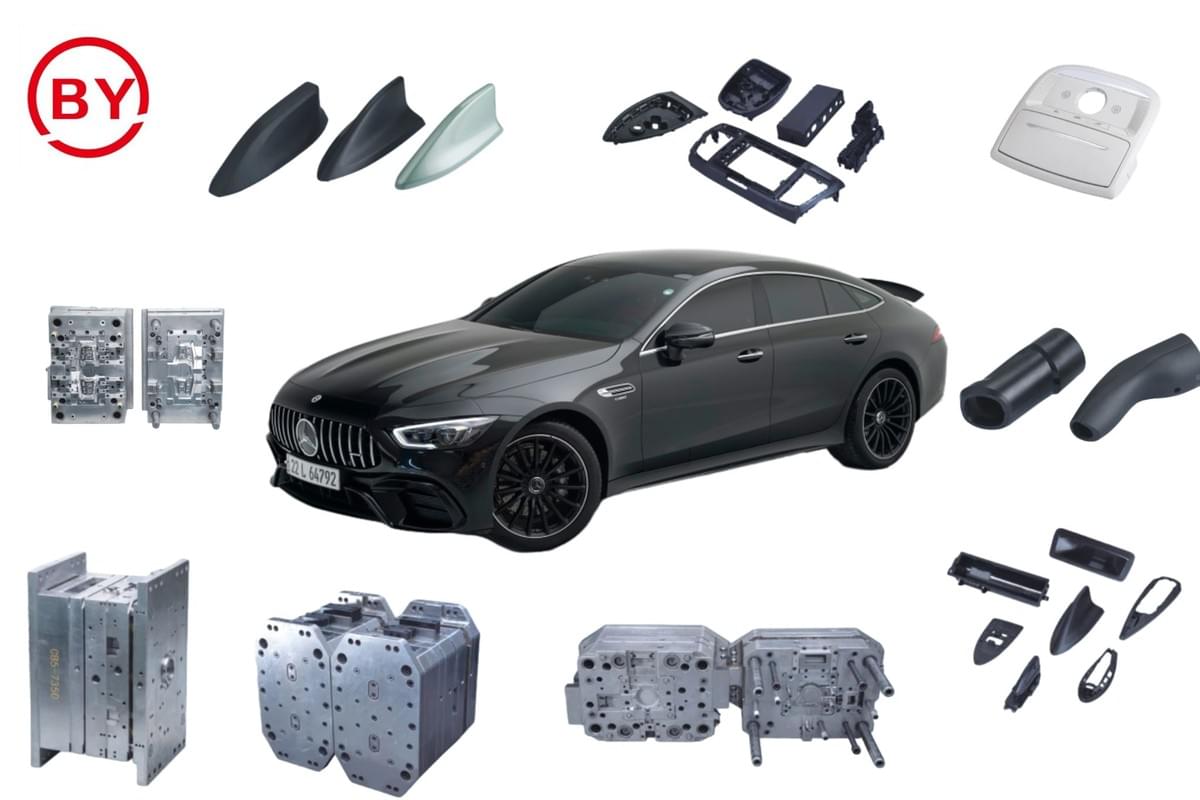
Maximum Part Sizes in the Industry
In the world of large injection molding, part sizes can vary dramatically depending on the machinery and technology used. Typically, manufacturers can create parts weighing several hundred pounds and measuring up to 20 feet in length or more. However, some specialized equipment allows for even larger dimensions, pushing boundaries that were once thought impossible in traditional manufacturing processes.
Factors Affecting Large Part Capabilities
Several factors influence how large you can injection mold, including machine size, material properties, and design complexity. Larger machines require more space and higher investment costs but offer greater flexibility for producing massive components. Additionally, materials like structural foam injection can help mitigate some weight-related challenges while still maintaining structural integrity—an essential consideration when exploring whether Can injection molding be used for large parts?
Real-World Examples of Large Injection Molding
Real-world applications of large injection molding showcase its potential across various industries—from automotive to aerospace. For instance, manufacturers have successfully created large vehicle body panels that enhance aerodynamics while reducing weight through foam injection molding techniques. These examples illustrate not only the feasibility of producing oversized items but also highlight innovations that make such endeavors economically viable despite concerns like Why is injection moulding not suitable for large products?
Can Injection Molding Be Used for Large Parts?
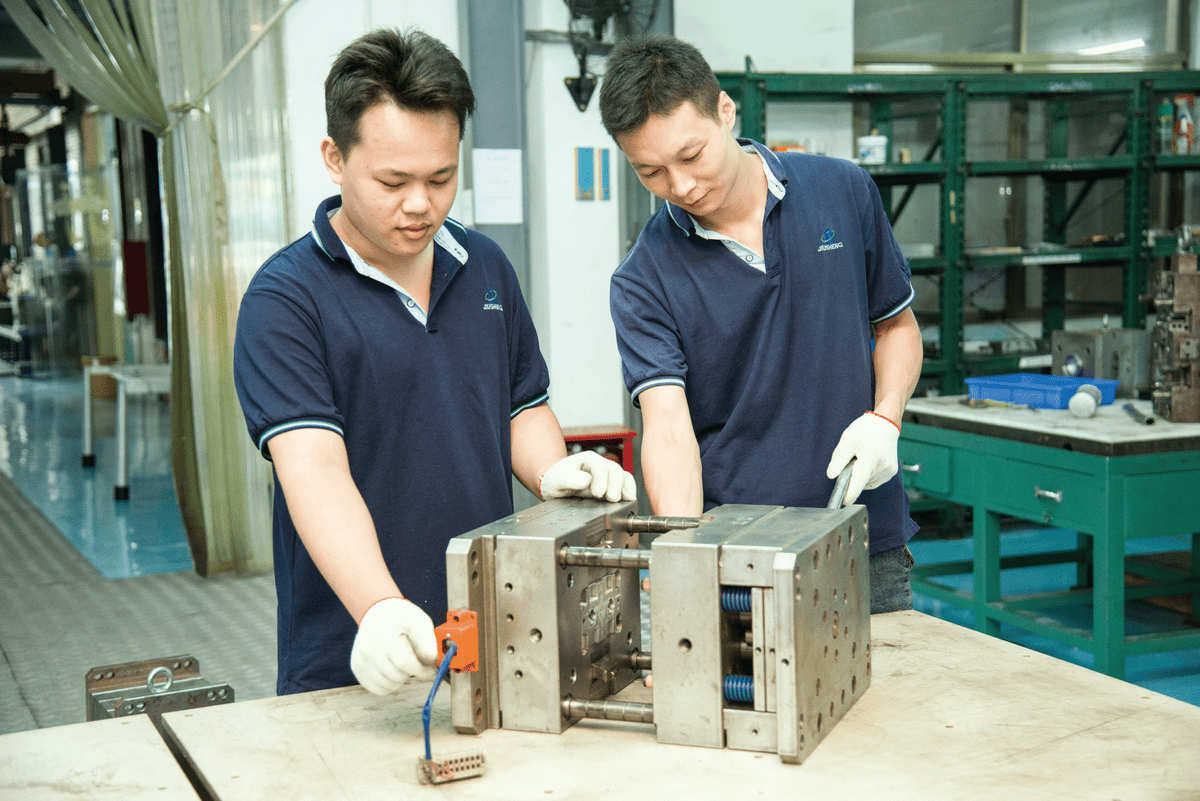
The Role of Technology in Large Molding
Technology plays a pivotal role in enabling large injection molding processes to thrive. Advanced machinery and computer-aided design (CAD) software have revolutionized how manufacturers approach large part production. With innovations like multi-cavity molds and automated systems, companies can efficiently produce larger components while maintaining precision and quality.
Moreover, specialized techniques such as structural foam injection are gaining traction, allowing for lighter yet robust parts that traditional methods struggle to achieve. This technology not only enhances the capabilities of large injection molding but also reduces material waste—a win-win for both manufacturers and their clients. As these technologies evolve, they continue to push the boundaries of how large you can injection mold.
Limitations of Traditional Injection Molding
Despite its many benefits, traditional injection molding does have limitations when it comes to producing large products. One major challenge is the size constraints imposed by existing machinery; not all machines are equipped to handle significant volumes or dimensions. This limitation often leads manufacturers to rethink designs or consider alternative manufacturing methods altogether.
Additionally, there are inherent challenges in achieving uniform cooling across larger parts which can result in warping or inconsistencies during production. These issues raise questions about durability and performance—critical factors when considering why injection moulding may not be suitable for certain large products. Consequently, understanding these limitations is essential for anyone venturing into the realm of large part production.
Innovations in Large Part Production
The landscape of large part production is rapidly changing thanks to ongoing innovations within the industry. Companies are increasingly turning to foam injection molding techniques that allow them to create lightweight structures with impressive strength characteristics—perfect for applications where weight savings matter most! Structural foam injection has emerged as a game changer by enabling manufacturers to produce larger components without compromising on quality or performance.
Furthermore, advancements in materials science mean that new polymers designed specifically for high-volume applications are hitting the market regularly—offering options that were previously unavailable for large injections molds. As these innovations continue shaping how we think about manufacturing processes like injection molding contract manufacturing, they open doors previously thought closed due to size constraints or cost implications associated with larger projects.
Why is Injection Moulding Not Suitable for Large Products?
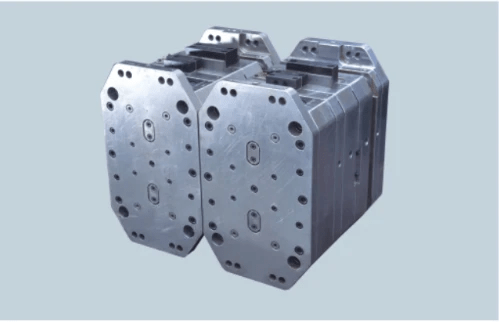
Challenges in Large Part Design
Designing large parts for injection molding introduces a multitude of challenges that can complicate production. For starters, achieving uniform wall thickness is critical; variations can lead to warping or defects in the final product, which is particularly problematic when dealing with large dimensions. Moreover, ensuring proper cooling and solidification times becomes increasingly complex as part size increases, necessitating advanced engineering solutions that may not always be available.
Furthermore, in foam injection molding and structural foam injection scenarios, achieving the desired density and structural integrity poses additional difficulties. Large products must also accommodate features like ribs or bosses without compromising strength; this requires careful planning and testing during the design phase. Ultimately, these design challenges contribute to longer lead times and increased risk of failure in production.
Cost Implications of Large Injection Molding
Cost considerations play a significant role when evaluating why injection molding may not be suitable for larger products. The initial investment required for larger molds can be staggering; custom molds designed for big parts often run into six figures or more. This hefty upfront cost needs to be justified by high production volumes, which isn’t always feasible depending on market demand.
Additionally, operational costs escalate due to longer cycle times associated with larger parts; this means more energy consumption and labor hours are required per unit produced. Maintenance costs also increase as larger machines are typically more complex and expensive to repair when something goes awry during production runs. As a result, companies must weigh these financial implications carefully against their potential return on investment before committing to large injection molding projects.
Comparison with Alternative Manufacturing Methods
When considering large part manufacturing options beyond traditional methods like large injection molding, alternatives often present compelling advantages. Techniques such as additive manufacturing (3D printing) allow for greater flexibility in design without incurring prohibitive costs associated with custom molds needed for traditional processes. This capability makes it easier to iterate designs quickly while minimizing waste—something that's particularly appealing in today’s fast-paced market.
Moreover, other methods like rotational molding or CNC machining offer unique benefits when producing sizable components; they often come with lower tooling costs and shorter lead times compared to their injected counterparts. While these methods may lack some characteristics of foam injection molding—such as lightweight structures—they provide viable pathways that cater specifically to projects where traditional injection might falter due to cost or complexity concerns.
In conclusion, while there’s no denying that large injection molding has its merits, it's essential to consider its limitations regarding design challenges and cost implications thoroughly before diving into a project involving sizable components.
Large Injection Molding Cost Considerations
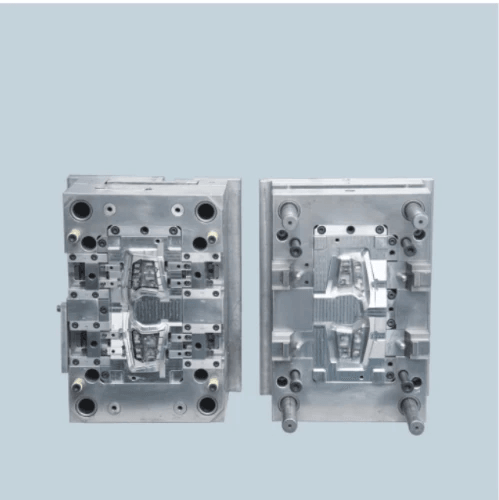
When diving into the world of large injection molding, understanding the cost implications is crucial for successful project execution. The expenses associated with large injection molding can vary significantly based on various factors, including material choice, part complexity, and production volume. By grasping these cost considerations, companies can make informed decisions that align with their budget and project goals.
Factors Influencing Molding Costs
Several elements play a pivotal role in determining the overall costs of large injection molding projects. Firstly, the choice of materials is critical; specialized plastics or structural foam injection options often come at a premium compared to standard materials. Additionally, the intricacy of the design impacts costs—more complex parts may require advanced molds and longer production times, leading to higher expenses.
Another significant factor is the scale of production; larger volumes typically reduce per-unit costs due to economies of scale in manufacturing. However, initial setup costs for molds and machinery remain substantial regardless of volume. Understanding these factors helps businesses assess whether they should pursue traditional methods or explore alternatives like foam injection molding for larger parts.
Budgeting for Large Injection Projects
Budgeting for large injection projects involves careful planning and consideration of multiple components. Companies must account for upfront costs such as mold design and fabrication alongside ongoing operational expenses like material procurement and machine maintenance. It's also wise to include contingencies in your budget to cover unexpected challenges that may arise during production.
Moreover, when exploring “how large can you injection mold?”, it’s essential to factor in potential adjustments needed in your budget if larger dimensions require custom molds or specialized equipment. Keeping close communication with your injection molding contract manufacturing partner ensures that any changes are promptly addressed without derailing your financial plan. A well-structured budget not only keeps projects on track but also allows companies to seize opportunities as they arise.
Case Studies: Cost Analysis for Large Parts
Examining real-world case studies provides valuable insights into cost analysis for large parts produced through injection molding techniques. For instance, one company utilized structural foam injection to create a sizable automotive component—initial estimates projected high costs due to mold complexity but were offset by reduced material usage and faster cycle times during production runs.
Another example involved a manufacturer producing an oversized industrial part via traditional methods; while initial investments were substantial due to mold fabrication, subsequent orders benefitted from lower unit prices as production volumes increased over time. These cases illustrate that while “why is injection moulding not suitable for large products?” might seem evident at first glance due to high initial costs or technological limitations, innovative approaches often reveal hidden efficiencies that make such projects viable.
Conclusion
In the rapidly evolving world of manufacturing, large injection molding stands out as a transformative process that continues to shape various industries. With innovations like foam injection molding and structural foam injection, manufacturers are pushing the boundaries of what is possible in terms of size and complexity. As we look to the future, understanding how large you can injection mold will be crucial for businesses aiming to remain competitive.
Innovations Transforming Large Injection Molding
The landscape of large injection molding is being revolutionized by cutting-edge technologies that enhance efficiency and reduce waste. Innovations such as advanced robotics and smart monitoring systems allow for precise control over the molding process, enabling larger parts to be produced with exceptional accuracy. Additionally, techniques like structural foam injection are making it feasible to create lightweight yet sturdy components that were previously unimaginable.
Future Trends in Large Part Manufacturing
Looking ahead, several trends are likely to define the future of large part manufacturing through injection molding. The demand for sustainable practices is prompting companies to explore eco-friendly materials and processes that minimize environmental impact while maintaining high quality. Moreover, as industries increasingly seek customization, advancements in digital technology will enable more flexible production methods tailored specifically for large parts.
Partnering with Experts Like Baoyuan for Success
To navigate the complexities of large injection molding cost and production challenges effectively, partnering with experienced professionals is essential. Companies like Baoyuan specialize in injection molding contract manufacturing, offering expertise in both traditional and innovative techniques tailored for large parts. By collaborating with industry leaders who understand both the potential and limitations—such as why injection moulding may not always be suitable for larger products—businesses can optimize their operations and achieve remarkable results.