Introduction
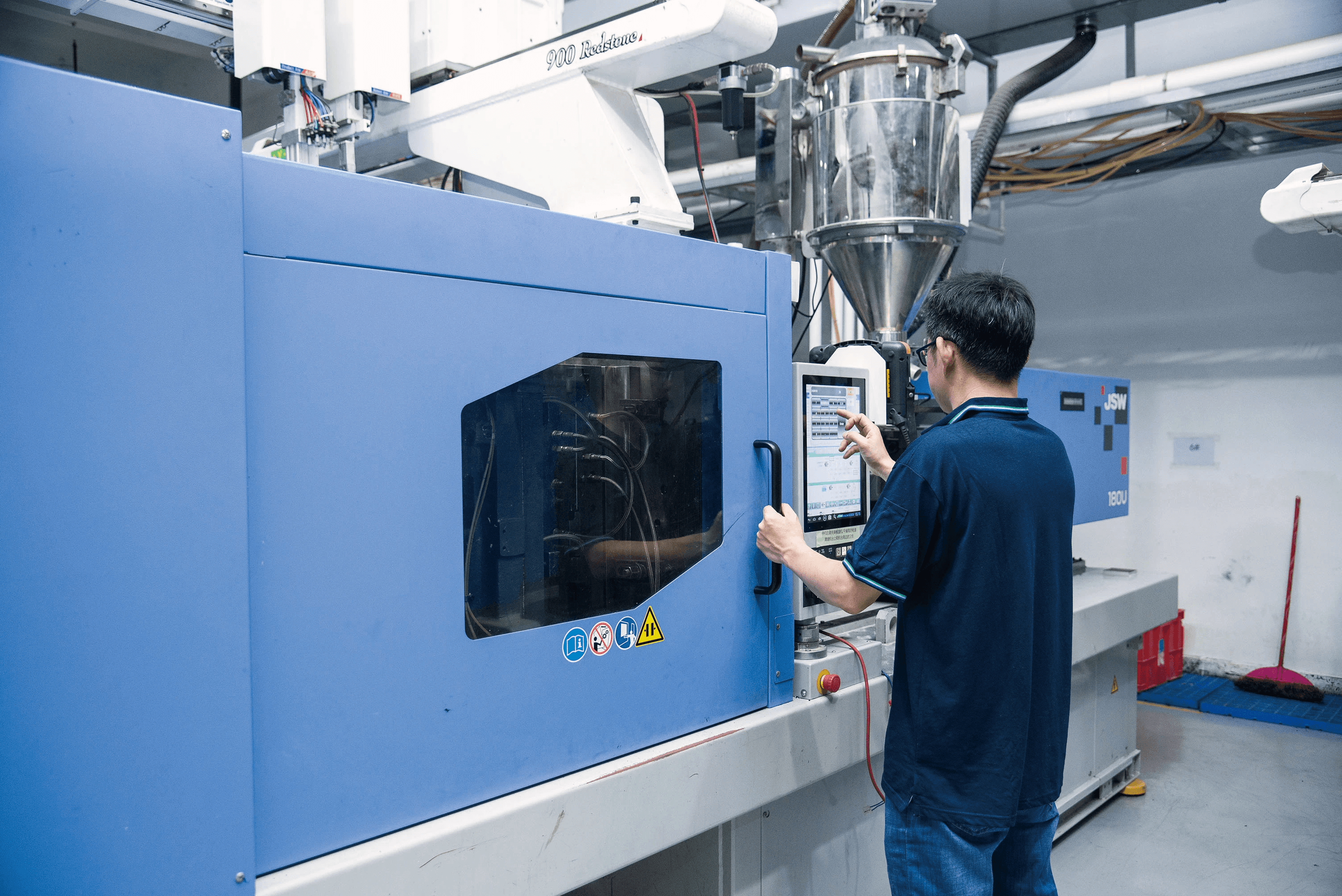
Injection molding is a fascinating process that has revolutionized the manufacturing industry, allowing for the mass production of intricate parts with remarkable precision. Understanding injection molding components is essential for anyone involved in production, design, or engineering fields. These components not only dictate the quality and efficiency of the final product but also play a crucial role in determining the overall cost-effectiveness of manufacturing.
Understanding Injection Molding Components
So, what are the components of injection molding? At its core, this process involves several key elements working harmoniously to transform raw materials into finished products. From injection nozzles to heating systems, each component serves a specific purpose that contributes to the seamless operation of an injection molding machine.
Importance of Efficient Design in Molding
Efficient design in molding is not just a luxury; it’s a necessity for optimizing production cycles and minimizing waste. The question What are the parts of injection molding process? leads us to realize that every component must be designed with precision to enhance performance and reduce downtime. A well-thought-out design can significantly impact production speed and quality, making it imperative for manufacturers to prioritize efficiency.
Overview of Injection Mold Components
When delving into what materials are used in injection molding, one quickly discovers a diverse range from standard plastics to advanced composites tailored for specific applications. Each material choice influences not just aesthetics but also functionality and sustainability within the manufacturing process. As we explore further into injection mold components, we will uncover how these elements work together to create high-quality products while addressing environmental considerations as well.
Key Injection Molding Components
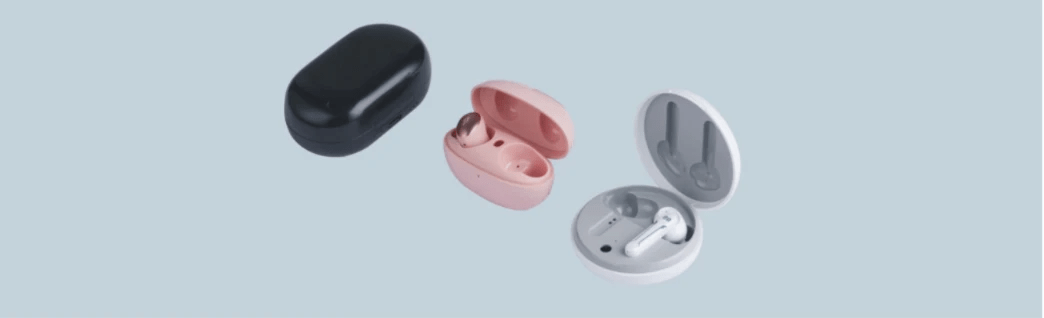
When diving into the world of injection molding components, it’s essential to understand how each part plays a crucial role in the overall process. The efficiency and effectiveness of these components can significantly influence production quality and speed. Let's explore the key elements that make up this fascinating technology.
Overview of Injection Molding Machine
At the heart of any injection molding operation is the injection molding machine. This complex piece of machinery is designed to melt plastic pellets, inject them into a mold, and then cool them to form solid parts. Understanding what are the components of injection molding machine is vital for anyone involved in manufacturing, as each component contributes to seamless operation and high-quality output.
The main types of injection molding machines include hydraulic, electric, and hybrid models, each offering distinct advantages depending on production needs. Hydraulic machines are known for their power and versatility, while electric machines excel in precision and energy efficiency. Hybrid models combine both technologies for optimal performance in various applications.
Essential Parts of the Injection Process
Now that we have an overview of the machine itself, let’s delve into what are the parts of injection molding process that facilitate this intricate operation. The essential parts include a hopper for feeding raw materials, a barrel where melting occurs, an injector for transferring molten plastic into molds, and cooling channels to solidify the material post-injection.
Each component must work harmoniously to ensure smooth transitions from one stage to another within the process cycle. For instance, if the cooling system is inefficient or improperly designed, it could lead to defects in molded products or extended cycle times—both detrimental to productivity. Therefore, understanding these essential parts helps manufacturers optimize their operations effectively.
Understanding the Mold Design
Mold design is perhaps one of the most critical aspects when discussing injection mold components because it directly affects product quality and production efficiency. A well-designed mold not only ensures accurate shaping but also facilitates easy ejection after cooling—a crucial step that can save time during production runs.
What are the components of injection molding molds? Typically they consist of core and cavity sections which define part geometry; ejector pins that help remove finished products; runner systems that guide melted plastic; and cooling channels that manage temperature throughout production cycles. Each element must be meticulously planned based on material properties and desired product characteristics.
In summary, understanding these key injection molding components—from machines to processes—enables manufacturers to enhance productivity while maintaining high standards in quality control.
What are the Components of Injection Molding?
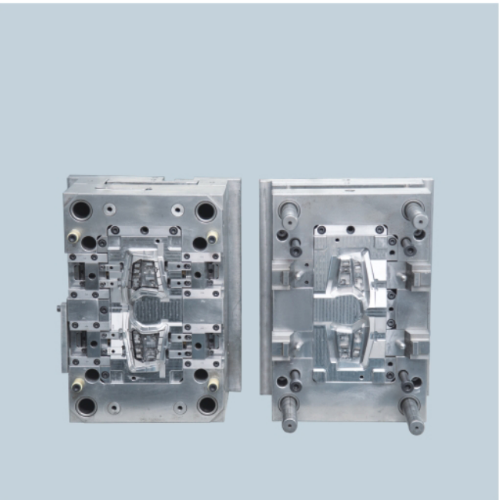
Injection molding is a fascinating process that involves several critical components working in harmony to create high-quality products. Understanding what are the components of injection molding is essential for anyone involved in manufacturing, as each part plays a unique role in ensuring efficiency and precision. This section delves into essential injection molding components, focusing on nozzles, pistons, and temperature control systems.
Insights into Injection Nozzles
Injection nozzles are vital elements of the injection molding machine that facilitate the flow of molten plastic into the mold cavity. They come in various designs and sizes, tailored to meet specific production requirements and material characteristics. The choice of nozzle can significantly influence cycle times and product quality; thus, understanding what are the parts of injection molding process includes recognizing how crucial these components are.
A well-designed nozzle minimizes pressure loss and optimizes flow rates, which directly impacts production efficiency. By selecting appropriate nozzle types—such as hot runner or cold runner systems—manufacturers can enhance their output while reducing waste material. Ultimately, insights into injection nozzles reveal their importance not just in functionality but also in achieving cost-effective solutions within the realm of injection molding components.
The Role of Injection Pistons
Injection pistons serve as another integral component within the injection molding machine by controlling the movement of molten plastic from the barrel to the mold cavity. These pistons ensure that materials are injected at precise pressures and speeds, which is critical for maintaining product consistency and quality during production runs. When considering what materials are used in injection molding processes, it’s important to note how piston design can affect compatibility with different plastics.
The efficiency of an injection piston directly correlates with cycle time; faster movements lead to shorter cycles but require careful calibration to avoid defects like warping or incomplete fills. Furthermore, advancements in piston technology have led to improved energy efficiency and reduced wear on machinery over time—benefits that manufacturers can't afford to overlook when evaluating their equipment's performance. Thus, understanding the role of injection pistons provides deeper insights into what are the components of injection molding machines that contribute to overall productivity.
Importance of Heating and Cooling Systems
Heating and cooling systems play a pivotal role in regulating temperatures throughout the injection molding process, ensuring optimal conditions for both melting materials and solidifying finished products. These systems help maintain consistent temperatures across molds during production cycles; this consistency is crucial for achieving uniformity in product dimensions—a key concern when discussing tolerances within injection mold components.
Effective heating ensures that thermoplastics melt evenly before being injected into molds while cooling systems allow for rapid solidification once materials have filled cavities completely. As such, understanding what materials are used in injection molding can guide decisions about heating requirements based on thermal properties unique to each type of plastic or composite material employed during manufacturing processes.
In summary, heating and cooling systems not only enhance product quality but also contribute significantly to energy efficiency—a win-win situation for manufacturers aiming for sustainability alongside profitability!
What Materials are Used in Injection Molding?
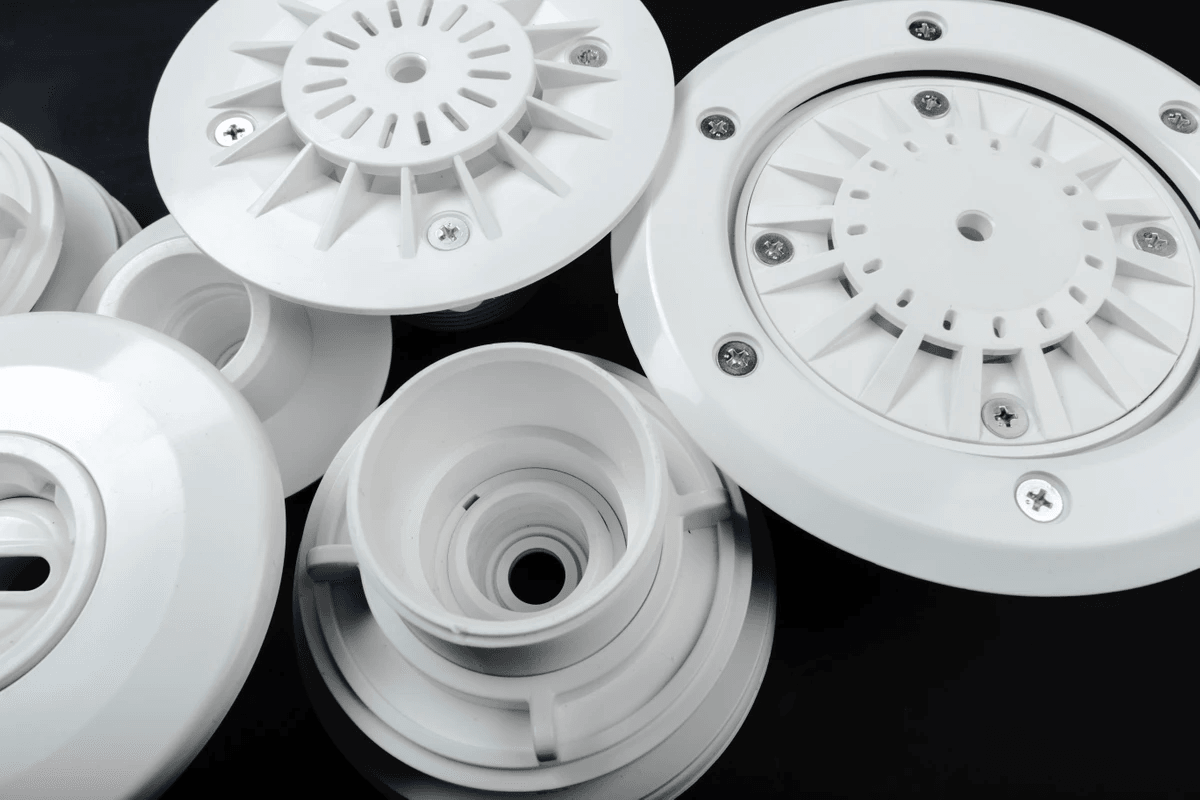
When diving into the world of injection molding, one can't help but notice the pivotal role that materials play. Understanding what materials are used in injection molding is essential for anyone involved in this industry, as they directly impact the performance and cost-effectiveness of the final product. From thermoplastics to composites, the selection of materials is a crucial step that influences everything from mold design to production efficiency.
Popular Plastics in the Industry
Among the most widely used plastics in injection molding are polycarbonate (PC), polypropylene (PP), and acrylonitrile butadiene styrene (ABS). These materials are favored for their unique properties—PC offers high impact resistance, PP boasts excellent fatigue resistance, and ABS provides a good balance between toughness and rigidity. Each of these plastics contributes significantly to various applications across industries, showcasing the diversity found within injection mold components.
In addition to these common options, there are also engineering-grade plastics like nylon and polyoxymethylene (POM) that offer enhanced mechanical properties for more demanding applications. The versatility of these materials ensures that manufacturers can find suitable solutions tailored to specific requirements within their projects. Ultimately, understanding what are the components of injection molding helps engineers select appropriate plastics that align with both functionality and production goals.
The Benefits of Composite Materials
Composite materials have gained popularity in injection molding due to their superior strength-to-weight ratio and enhanced durability. By combining different raw materials—such as fiberglass or carbon fiber with traditional plastics—composites provide unique benefits that single-material options often cannot match. These advantages make them ideal for applications requiring lightweight yet robust solutions, particularly in automotive and aerospace sectors.
Moreover, composites can be engineered to exhibit specific properties such as increased thermal stability or improved chemical resistance, making them incredibly versatile within various contexts. This adaptability allows manufacturers to optimize their products by utilizing advanced injection mold components designed specifically for composite processing techniques. As industries continue seeking innovative approaches for efficiency and performance, composite materials will remain at the forefront of material selection discussions.
Environmental Considerations in Material Selection
In recent years, environmental considerations have become increasingly significant when selecting materials for injection molding processes. With growing awareness around sustainability issues, many companies now prioritize eco-friendly options among what materials are used in injection molding projects. Biodegradable plastics or recycled content polymers represent a shift towards greener practices while still delivering acceptable performance levels.
Additionally, understanding how certain plastic choices impact recycling efforts can influence material selection strategies within organizations committed to reducing waste footprints. Manufacturers must also consider regulatory compliance regarding material safety standards as they navigate these environmental challenges while maintaining production efficiency with their chosen injection mold components. Emphasizing sustainable practices not only enhances brand reputation but also aligns with global trends toward responsible manufacturing.
Achieving Efficiency with Injection Mold Components
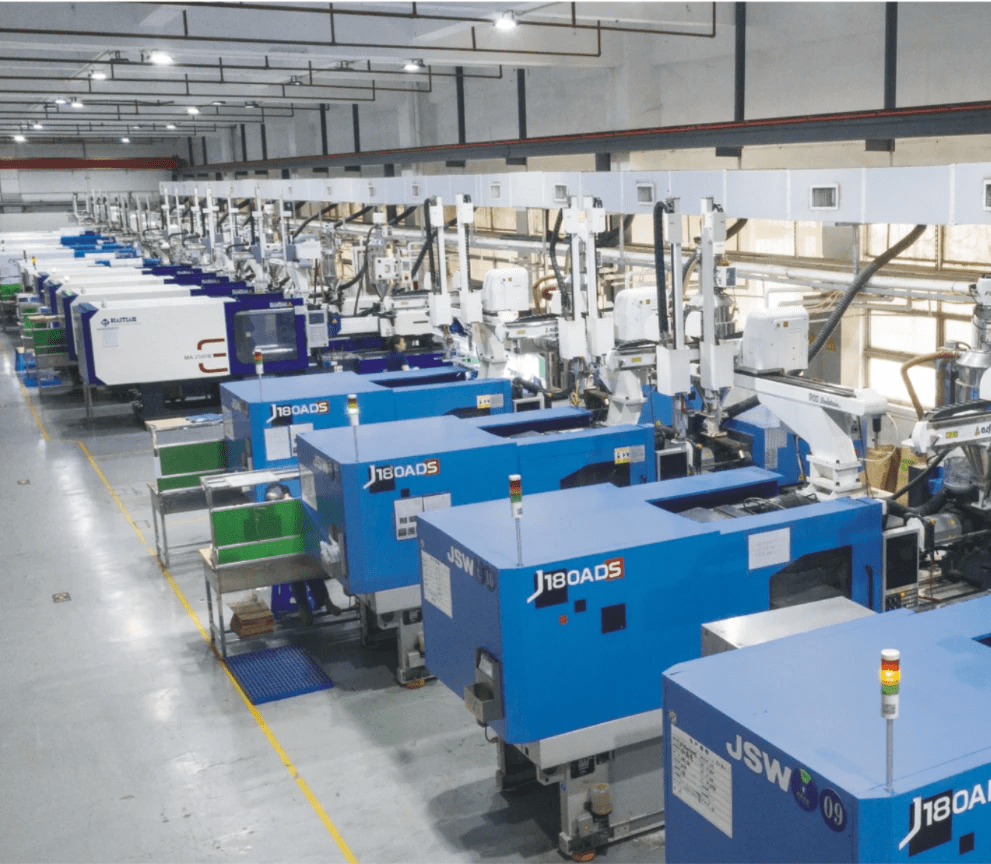
In the world of manufacturing, efficiency is king, especially when it comes to injection molding components. The design of molds can significantly influence production speed and overall output quality. By understanding how various elements work together within the injection molding machine, manufacturers can optimize their processes and deliver better products faster.
How Mold Design Impacts Production Speed
The mold design is a crucial factor in determining how quickly an injection molding process can operate. Efficiently designed molds allow for quicker cycle times, reducing the overall time required to produce each part. For instance, incorporating features like streamlined flow paths or multiple cavities can enhance throughput, making it vital to consider these aspects when asking: what are the components of injection molding that contribute to faster production?
Moreover, a well-thought-out mold design minimizes the need for excessive maintenance and repairs during production runs. This not only saves time but also reduces downtime costs associated with machinery malfunctions or adjustments. Ultimately, understanding what are the parts of the injection molding process that facilitate speed will empower manufacturers to innovate further in their designs.
The Significance of Tolerances and Fits
Tolerances and fits are fundamental concepts in injection molding that directly affect product quality and efficiency. Properly set tolerances ensure that parts fit together seamlessly without requiring extensive post-production adjustments or rework. When considering what materials are used in injection molding, it's essential to select those that maintain dimensional stability under varying conditions while adhering to specified tolerances.
Additionally, achieving precise fits between components helps minimize defects during assembly and improves overall product functionality. A slight misalignment due to poor tolerance can lead to significant issues down the line—think increased scrap rates or customer dissatisfaction! Therefore, manufacturers must pay close attention to these details within their injection mold components for optimal performance.
Innovations in Mold Technology
Innovation is at the heart of improving efficiency in any manufacturing process, including injection molding technology. Recent advancements have introduced smart molds equipped with sensors that monitor temperature and pressure in real-time—allowing for immediate adjustments during production cycles based on feedback data. This not only enhances consistency but also addresses potential issues before they escalate into costly problems.
Furthermore, 3D printing technologies have revolutionized mold design by enabling rapid prototyping and customization tailored specifically for unique projects or complex geometries. As manufacturers explore what are the components of injection molding necessary for cutting-edge applications, they find themselves better positioned to meet diverse market demands while enhancing productivity.
To sum it up: embracing innovations in mold technology leads directly toward improved efficiency across all stages of production involving various injection mold components!
Baoyuan’s Expertise in Molding Solutions
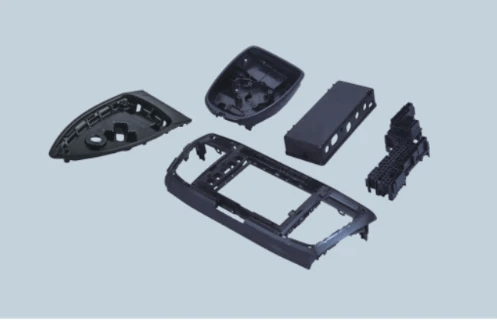
When it comes to injection molding components, Baoyuan stands out as a leader in the industry. Their commitment to innovation and quality ensures that they not only meet but exceed client expectations. With a keen understanding of what are the components of injection molding, Baoyuan integrates specialized techniques that enhance both performance and efficiency.
Specialized Techniques in Mold Design
Baoyuan employs advanced methodologies in mold design that set their products apart from the competition. By utilizing state-of-the-art software and simulation tools, they meticulously analyze every aspect of the injection molding process, ensuring optimal flow and minimal waste. This attention to detail allows them to create molds that are not only efficient but also durable, maximizing the lifespan of their injection mold components.
What are the parts of injection molding process? At Baoyuan, each phase is carefully considered—from material selection to cooling strategies—allowing for seamless integration of all elements involved. Their specialized techniques enable them to adapt designs based on specific client needs, making them a versatile partner for various industries.
Quality Assurance Practices by Baoyuan
Quality assurance is at the heart of Baoyuan's operations, ensuring that every batch meets stringent industry standards. They implement rigorous testing protocols throughout the production cycle, from initial design through final inspection of injection molding components. This commitment guarantees reliability and consistency in what materials are used in injection molding processes.
In addition to traditional quality checks, Baoyuan leverages advanced technology such as automated inspection systems and real-time monitoring during production runs. These practices not only reduce errors but also enhance overall efficiency by identifying potential issues before they escalate into costly problems. Clients can rest easy knowing that each component is crafted with precision and care.
The Impact of Skilled Personnel on Efficiency
The role of skilled personnel cannot be overstated when discussing what are the components of an injection molding machine or process; they are truly the backbone behind successful operations at Baoyuan. Their team comprises experienced professionals who bring a wealth of knowledge about both traditional methods and innovative techniques in mold design and manufacturing processes.
Investing in ongoing training ensures that staff remain up-to-date with industry advancements while honing their skills related to various materials used in injection molding applications. This expertise translates directly into enhanced productivity levels and reduced lead times for clients seeking high-quality mold solutions quickly. In essence, skilled personnel help bridge the gap between complex engineering concepts and practical execution.
Conclusion
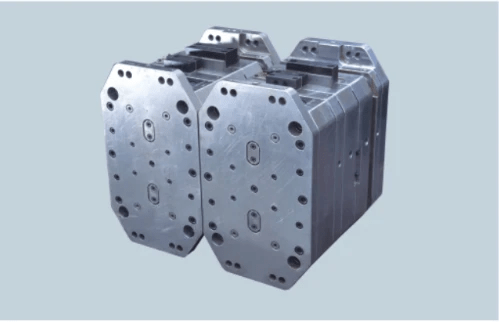
In wrapping up our exploration of injection molding components, it’s clear that understanding the intricacies of this process is crucial for anyone involved in manufacturing. From the essential parts of the injection molding machine to the specific materials used in injection molding, each element plays a significant role in achieving high-quality results. By grasping what are the components of injection molding and how they interact, manufacturers can optimize their production processes and enhance product quality.
Summary of Injection Molding Essentials
Injection molding is a complex yet fascinating process that relies on various components to function effectively. Key elements include the injection machine itself, which houses critical parts like nozzles and pistons, as well as intricate mold designs that shape the final product. Additionally, understanding what materials are used in injection molding—ranging from popular plastics to composite materials—can significantly influence both performance and sustainability.
Enhancing Designs for Improved Performance
To boost efficiency and performance in injection molding processes, manufacturers must pay close attention to mold design and component selection. The right combination of tolerances and fits can drastically reduce production time while ensuring consistent quality across batches. Moreover, innovations in injection mold components are paving the way for more effective designs that not only enhance productivity but also cater to evolving market demands.
Future Trends in Injection Molding Components
Looking ahead, several trends are set to transform the landscape of injection molding components. Advances in technology will likely lead to smarter machines equipped with real-time monitoring systems that optimize every aspect of production—from material usage to energy consumption. Furthermore, increased focus on sustainability will drive demand for eco-friendly materials used in injection molding processes, pushing manufacturers toward greener practices without compromising on quality.