Introduction
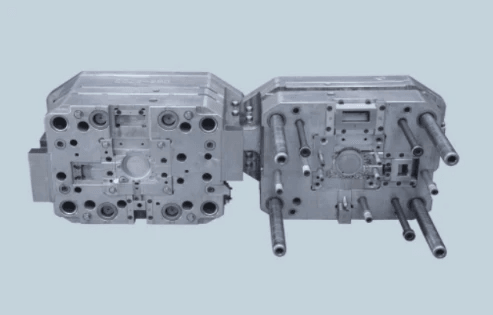
Understanding Injection Molding Tolerance
Injection molding tolerance can significantly impact both functionality and aesthetics of molded parts. A well-defined tolerance range helps manufacturers avoid costly rework and ensures that products perform as intended. By grasping what the tolerance for mold entails, engineers can design components that are not only precise but also reliable.
Importance of Precision in Production
Precision in production isn't just a nice-to-have; it's essential for maintaining competitiveness in today's fast-paced market. How precise can injection molding be? With advancements in technology and materials, manufacturers can achieve remarkable levels of accuracy, often within thousandths of an inch. This level of precision directly correlates with customer satisfaction and product performance.
Overview of Key Factors Affecting Tolerance
Several key factors affect injection molding tolerances, including material selection, mold design, process parameters, and quality control measures. For instance, understanding ISO standards for injection molding helps ensure compliance with industry norms while optimizing injection molding tolerances across various applications. Additionally, the ISO tolerance standard for plastic parts provides guidelines that aid manufacturers in achieving consistent quality throughout their production processes.
Material Selection and Its Impact
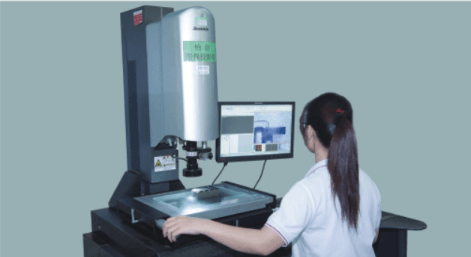
In the realm of injection molding, selecting the right material is crucial for achieving optimal injection molding tolerance. The choice of polymer can significantly influence the final product's dimensional accuracy and overall performance. Understanding how materials behave under various conditions is essential for manufacturers aiming for precision and consistency.
How Materials Influence Injection Molding Tolerance
Materials play a pivotal role in determining what is the tolerance for injection molding. Different polymers exhibit varying shrinkage rates, thermal expansion characteristics, and flow properties, all of which directly impact dimensional stability during production. By selecting materials with predictable behaviors, manufacturers can enhance their ability to meet stringent ISO standards for injection molding.
When assessing what is the tolerance for mold design, it’s essential to consider how specific materials respond to temperature changes and mechanical stress during the injection process. For example, a material that expands more than others under heat may lead to larger tolerances than desired if not accounted for properly. Therefore, understanding these material properties allows engineers to fine-tune their processes and optimize injection molding tolerances effectively.
The Role of Polymer Properties
Polymer properties are fundamental when discussing how precise can injection molding be? Characteristics such as viscosity, melting temperature, and tensile strength dictate how well a polymer will perform in an injection mold setup. For instance, high-viscosity polymers may require higher pressures during injection, which could affect the final part's dimensions if not carefully controlled.
Moreover, different types of polymers will have unique cooling rates that influence shrinkage after they are ejected from the mold—this directly relates to what is the tolerance for mold dimensions post-production. Materials with lower shrinkage rates tend to yield parts that adhere more closely to specified tolerances compared to those with higher variability in shrinkage behavior. Hence, understanding these properties is vital when optimizing injection molding tolerances.
Choosing the Right Resin for Precision
Choosing the right resin is critical in ensuring that your products meet both functional requirements and strict ISO tolerance standards for plastic parts. Resins come in various formulations tailored to specific applications; thus picking one aligned with your project’s needs can minimize deviations from intended specifications. It’s important to evaluate factors like application environment—whether it involves exposure to chemicals or extreme temperatures—to ensure you select a resin that maintains its integrity under those conditions.
Additionally, conducting thorough testing on potential resins helps determine how they will perform concerning what are acceptable tolerances within your production cycle. This proactive approach allows manufacturers not only to achieve better precision but also ensures compliance with relevant standards governing plastic components in their industry sector—ultimately leading towards optimizing injection molding tolerances across production lines.
The Ins and Outs of Mold Design
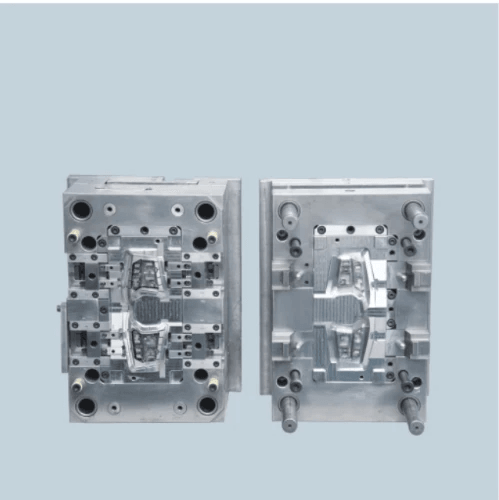
What is the Tolerance for Injection Molding?
So, what is the tolerance for injection molding? Tolerance in this context refers to the allowable deviation from a specified dimension in molded parts. Typically, tolerances can range from ±0.005 inches (0.127 mm) for smaller components to ±0.020 inches (0.508 mm) for larger ones, depending on various factors like material choice and part complexity. Understanding these limits is essential for manufacturers aiming to achieve consistent quality while optimizing injection molding tolerances.
Moreover, it's important to note that different materials may have varying inherent tolerances due to their physical properties during cooling and solidification phases. This means that when you ask, What is the tolerance for mold? you're not just looking at numbers; you're considering how those numbers interact with your chosen materials and processes as well. Adhering to ISO standards for injection molding can also provide guidelines on acceptable tolerances specific to plastic parts.
Essentials of Precision Mold Construction
Precision mold construction is fundamental in achieving desired injection molding tolerance levels; after all, a poorly designed mold can lead to significant production errors down the line! Key elements include selecting high-quality materials that can withstand repeated cycles without warping or degrading over time and ensuring meticulous machining processes that create accurate cavity shapes. Additionally, incorporating features such as cooling channels helps maintain uniform temperature across molds—another factor critical for achieving tight tolerances.
Furthermore, understanding how different aspects of mold design contribute toward overall precision is vital; even small variations in cavity dimensions can lead to large discrepancies in final product measurements due to compounding effects during production runs. Utilizing advanced technologies like CAD software allows designers to simulate potential issues before they arise—essentially helping them avoid pitfalls related directly back to optimizing injection molding tolerances! Ultimately, investing time upfront into precision mold construction pays dividends by reducing waste and rework later on.
How Design Flaws Affect Tolerance
Design flaws are like gremlins lurking in your manufacturing process—they often go unnoticed until it's too late! A single miscalculation or oversight during mold design can lead directly toward compromised injection molding tolerance levels resulting in defective parts or costly reworks down the line! Common issues include inadequate draft angles causing difficulty with part ejection or poorly placed gates leading uneven filling patterns—all detrimental effects when striving for precision.
Additionally, these flaws don’t just affect one batch; they can create systemic problems affecting multiple production runs if left unaddressed! Regular audits against ISO tolerance standards for plastic parts help catch these issues early on while providing benchmarks against which performance can be measured consistently over time—ensuring that quality remains a top priority throughout every stage of production! By recognizing how design flaws impact overall tolerances early in development phases, manufacturers position themselves better within competitive markets focused heavily on efficiency and excellence!
Process Parameters: The Dialing In
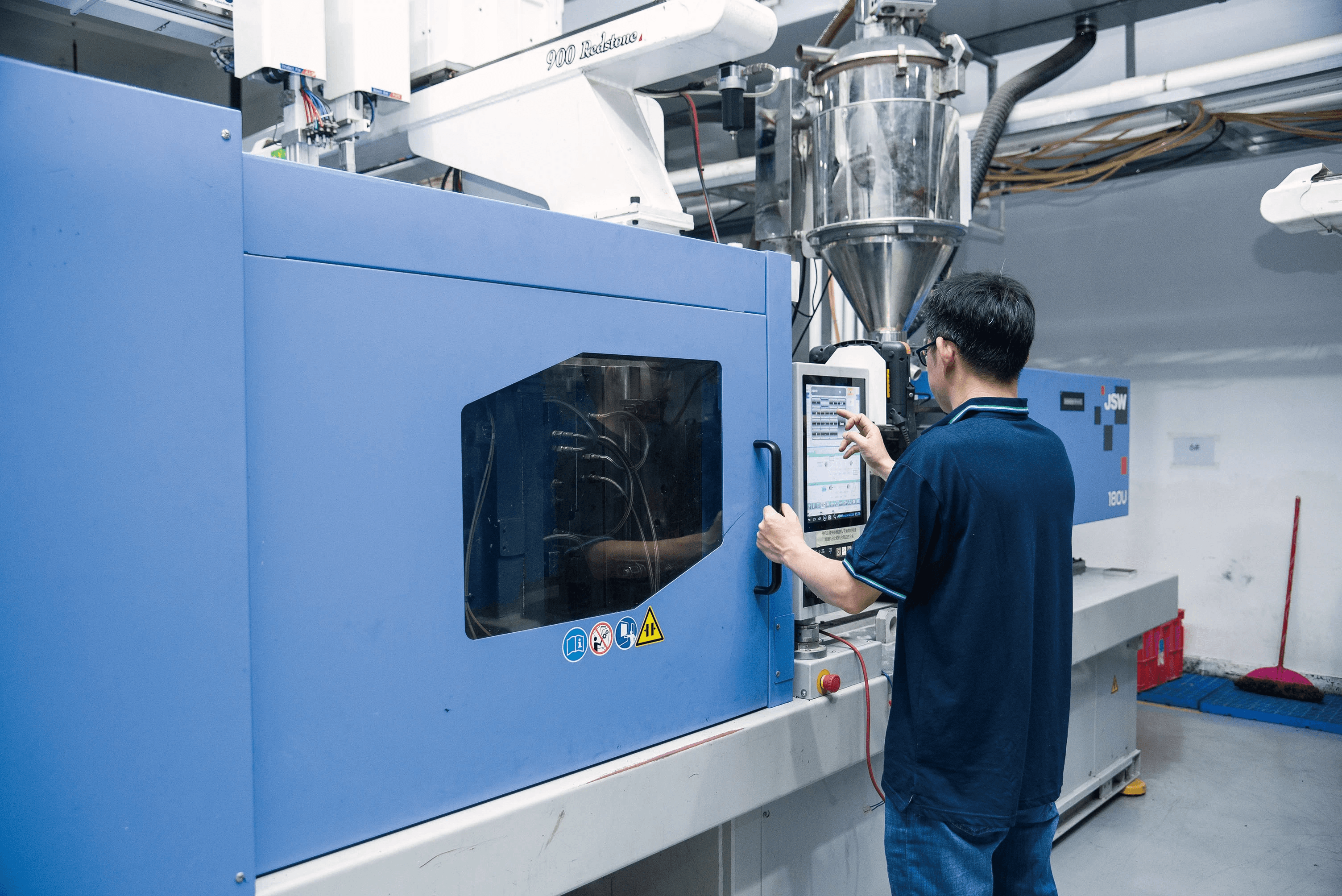
The success of injection molding hinges on a variety of process parameters that must be meticulously controlled to achieve the desired injection molding tolerance. Each variable plays a crucial role in determining how closely the final product adheres to specifications, making it essential for manufacturers to understand what is the tolerance for injection molding and how these factors can be optimized. By fine-tuning these parameters, companies can enhance precision and ensure consistent quality across production runs.
Key Injection Molding Process Variables
When discussing injection molding tolerance, it's vital to consider several key process variables that influence outcomes. These include injection speed, pressure, cooling time, and material flow rates. Adjusting any of these parameters can directly affect the final dimensions of molded parts; thus, understanding what is the tolerance for mold design becomes critical in achieving optimal results.
One primary variable is injection speed—too fast can lead to defects like warping or incomplete filling, while too slow may result in poor surface finish or inadequate packing pressure. Similarly, cooling time must be carefully calibrated; if parts cool too quickly or slowly, they may warp or shrink unevenly, impacting overall tolerance levels. Therefore, mastering these key variables is essential for anyone serious about optimizing injection molding tolerances.
How Temperature Affects Final Product Tolerance
Temperature control is another cornerstone of achieving precise injection molding tolerances. Both the melt temperature of the polymer and the mold temperature significantly influence how well materials fill cavities and solidify into their final shapes. A consistent melt temperature ensures uniform flow characteristics during injection; if it's too high or low, it can lead to variations that compromise what are considered acceptable tolerances in production.
Moreover, maintaining an optimal mold temperature helps manage cooling rates and reduces internal stresses within molded parts—an essential factor when considering what are ISO standards for injection molding quality assurance. If temperatures fluctuate excessively during production runs, it could lead to dimensional inaccuracies that fall outside acceptable limits established by ISO tolerance standards for plastic parts. Thus, precise temperature management isn't just a technical necessity; it’s a strategic move toward ensuring high-quality outputs.
The Importance of Cycle Time Optimization
Cycle time optimization stands out as a pivotal element in refining injection molding processes while keeping an eye on tolerances. Shorter cycle times mean increased productivity but must not come at the cost of precision; hence balancing speed with accuracy is crucial when asking how precise can injection molding be? Efficient cycle times allow manufacturers to maximize output without sacrificing quality—a delicate dance between efficiency and adherence to stringent tolerances.
To achieve this balance effectively requires ongoing analysis of all process variables—from cooling times to ejection speeds—to ensure they align with desired outcomes without introducing variability that could jeopardize product integrity. Additionally, consistent evaluation against established metrics allows teams to identify areas where adjustments might improve both cycle times and overall part quality further enhancing efforts toward optimizing injection molding tolerances overall.
Ultimately, focusing on these process parameters enables manufacturers not only to meet but exceed expectations around what constitutes acceptable tolerances in their products while adhering strictly to relevant ISO standards—setting them apart in a competitive marketplace.
Quality Control and Measurement Techniques
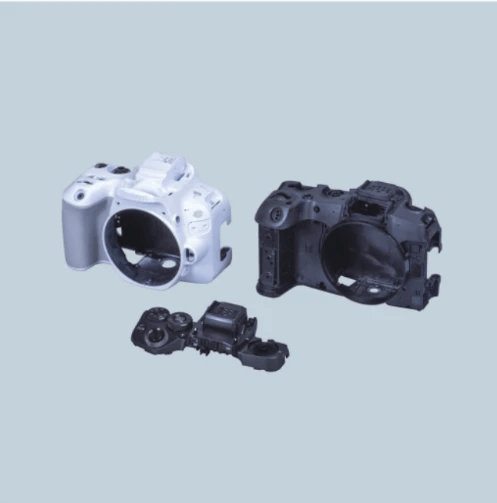
Quality control and measurement techniques are paramount in ensuring that injection molding tolerances are met consistently. These processes not only help maintain product quality but also enhance production efficiency. Understanding the standards and techniques available can significantly impact the overall success of injection molding projects.
What are the ISO Standards for Injection Molding?
The ISO standards for injection molding serve as a framework to guide manufacturers in achieving high-quality production outcomes. Specifically, these standards outline acceptable levels of accuracy, which directly relate to what is considered acceptable injection molding tolerance. For instance, the ISO tolerance standard for plastic parts provides specific guidelines on how precise can injection molding be, ensuring that products meet industry requirements and customer expectations.
Adhering to these ISO standards not only helps in maintaining consistent quality but also fosters trust among clients who rely on precision in their products. Additionally, compliance with international standards can open doors to new markets by showcasing a commitment to quality assurance and excellence in manufacturing practices. In essence, understanding what are the ISO standards for injection molding is crucial for any organization aiming to optimize their injection molding tolerances.
Techniques for Measuring Tolerance
Measuring tolerance accurately is essential in assessing whether a molded part meets its design specifications. Various techniques exist for this purpose, including calipers, micrometers, and coordinate measuring machines (CMM), each offering different levels of precision when determining what is the tolerance for mold components. Employing advanced measurement tools allows manufacturers to identify deviations from desired specifications early in the production process.
Moreover, utilizing statistical process control (SPC) methods can help monitor variations over time, providing insights into how well current processes adhere to established tolerances. This proactive approach not only enhances quality assurance but also assists in optimizing injection molding tolerances by identifying trends or issues before they escalate into larger problems. Ultimately, effective measurement techniques form the backbone of successful quality control efforts within the realm of injection molding.
Ensuring Consistency in Quality Assurance
Consistency is key when it comes to maintaining high-quality output in any manufacturing environment—especially within injection molding operations where even minor deviations can lead to significant issues down the line. One way organizations ensure consistency is through regular audits and inspections aligned with established ISO standards for injection molding; this helps confirm that all processes adhere strictly to defined tolerances throughout production cycles.
Furthermore, implementing robust documentation practices allows teams to track changes over time while providing clear records of compliance with specified tolerances; this transparency fosters accountability among personnel involved in production activities as well as instills confidence among stakeholders regarding product reliability and performance metrics related specifically back towards optimizing Injection Molding Tolerances.
Lastly, fostering a culture that prioritizes continuous improvement encourages employees at all levels—from operators up through management—to remain vigilant about potential areas needing enhancement or adjustment concerning both processes utilized during manufacturing operations along with final product evaluations based upon defined criteria surrounding what is considered acceptable when discussing aspects like “injection molding tolerance.”
The Role of Skilled Personnel in Tolerances
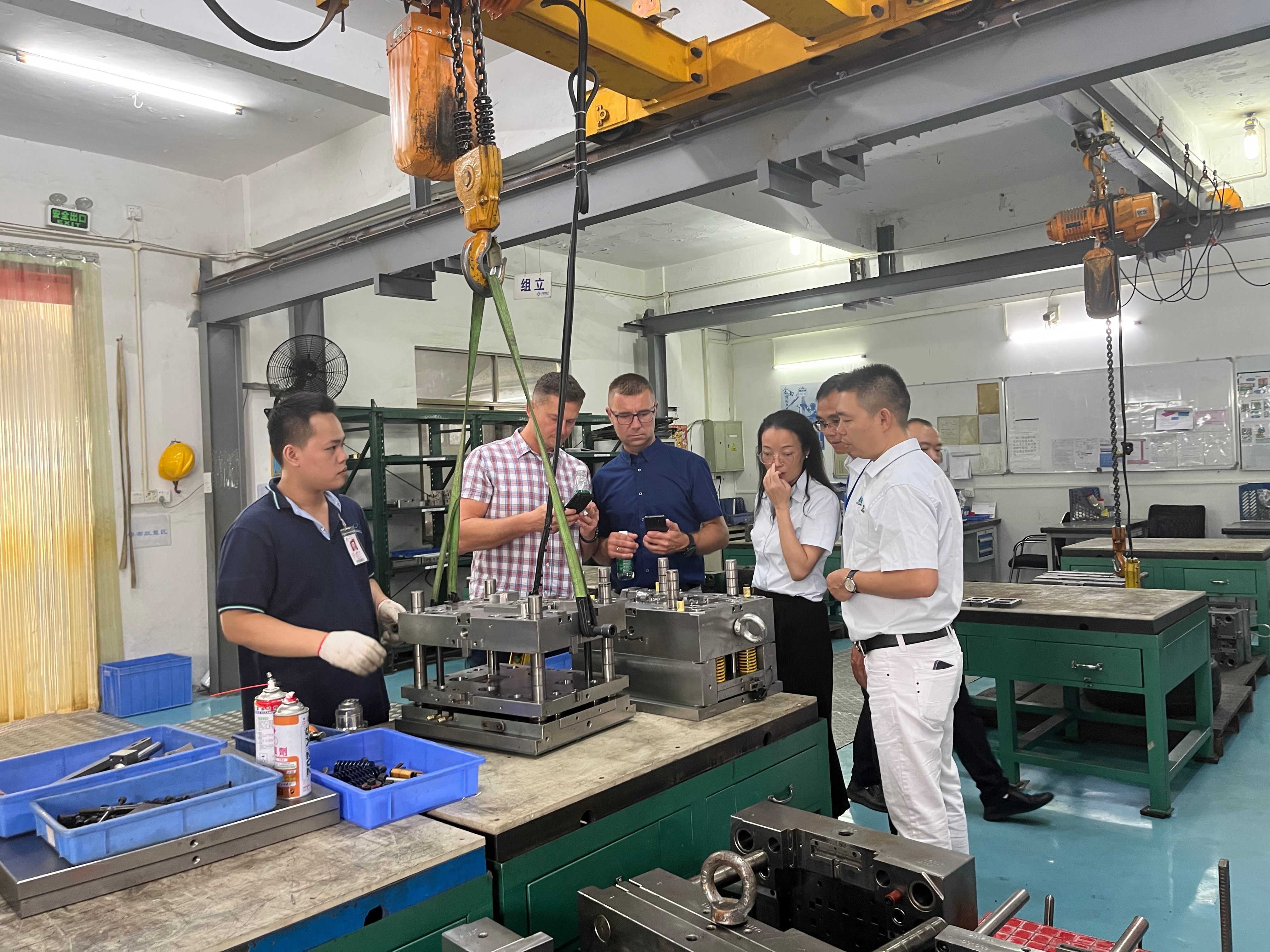
In the realm of injection molding, skilled personnel play a pivotal role in achieving and maintaining high levels of precision and accuracy. Their expertise not only impacts the overall quality of the molded parts but also directly influences injection molding tolerance. With an understanding of what is the tolerance for injection molding, these professionals can make informed decisions that lead to optimal outcomes.
How Expertise Influences Precision
The relationship between expertise and precision cannot be overstated when discussing injection molding tolerance. Skilled operators are adept at monitoring process parameters and adjusting them as needed to maintain tight tolerances throughout production runs. Moreover, their knowledge extends to understanding what is the tolerance for mold design, which allows them to anticipate potential issues before they arise, ensuring that tolerances remain within specified limits.
The Baoyuan Team's Impact on Tolerance Optimization
At Baoyuan, a commitment to precision is reflected in their team's approach towards optimizing injection molding tolerances. This skilled workforce brings together years of experience across various projects, ensuring they understand not just the technical aspects but also the nuances involved in achieving ideal results. By leveraging their collective knowledge, Baoyuan has established itself as a leader in delivering products that consistently meet or exceed expectations regarding what are the ISO standards for injection molding.
The Baoyuan team actively engages in continuous improvement practices aimed at refining processes further and enhancing product quality. They conduct regular training sessions focused on best practices related to mold design and manufacturing techniques—essentially fostering an environment where everyone contributes towards understanding what is the tolerance for mold construction. This collaborative spirit has been instrumental in driving innovation within their operations while maintaining rigorous attention to detail necessary for optimizing injection molding tolerances.
Training and Skills Development in the Industry
Investing in training and skills development is crucial for any organization aiming to excel at maintaining high standards of precision within their production processes—especially when it comes to injection molding tolerance. As technology evolves rapidly with new materials and methodologies emerging regularly, ongoing education ensures that personnel remain up-to-date with industry advancements while honing their craft further. This commitment helps answer questions like how precise can injection molding be by equipping teams with contemporary techniques tailored towards achieving tighter tolerances.
Moreover, standardized training programs focusing on ISO tolerance standard for plastic parts provide employees with essential knowledge about compliance requirements while emphasizing best practices across various applications within the field of plastic manufacturing. By fostering a culture centered around continuous learning opportunities paired with hands-on experience gained through real-world projects, companies can cultivate an adept workforce capable of meeting ever-increasing demands related to production efficiency without compromising quality.
Conclusion
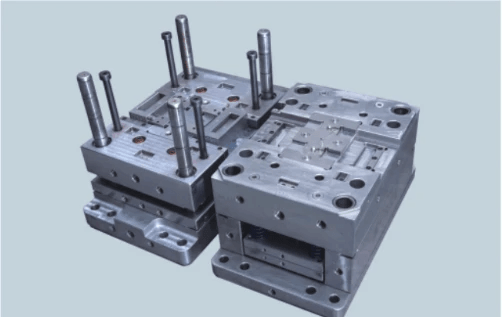
In the realm of injection molding, understanding and achieving precision is paramount. The interplay of material selection, mold design, process parameters, and skilled personnel all contribute to the overall injection molding tolerance. By recognizing these factors, manufacturers can enhance their production quality and meet stringent industry standards.
Recap of Injection Molding Tolerance Factors
When we ask, What is the tolerance for injection molding? it encompasses a multitude of elements including material properties, mold design intricacies, and process variables. Each factor plays a critical role in determining how precise injection molding can be; from the choice of resin to how well molds are constructed. Additionally, adherence to ISO standards for injection molding ensures that products consistently meet quality benchmarks while minimizing variations in dimensions—after all, nobody wants a wonky part!
Future Trends in Injection Molding Precision
Looking ahead, advancements in technology are set to redefine what is possible with injection molding tolerance. Innovations like real-time monitoring systems and AI-driven analytics are paving the way for unprecedented precision levels in production processes. As industries increasingly demand tighter tolerances—often dictated by ISO tolerance standards for plastic parts—the focus will shift towards optimizing injection molding tolerances through automation and smarter manufacturing practices.
Strategies for Optimizing Injection Molding Tolerances
To truly master optimizing injection molding tolerances, companies must implement a multifaceted approach that includes rigorous training programs for personnel and investment in high-quality materials and equipment. Regular audits against ISO standards for injection molding can help identify areas needing improvement while ensuring compliance with industry expectations.