Introduction
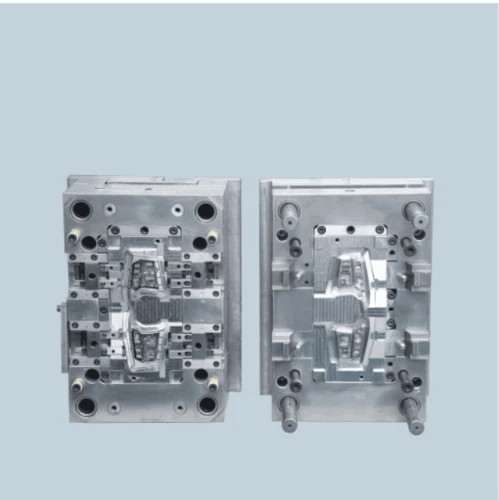
Injection molding is a fascinating process that transforms raw materials into a multitude of products we use daily. This method, primarily focused on plastic injection molding, allows manufacturers to create complex shapes and designs efficiently. Understanding the intricacies of injection molding is crucial for anyone involved in design or production within various industries.
Understanding Injection Molding
At its core, injection molding involves injecting molten material into a pre-designed mold to produce parts with high precision and repeatability. The types of injection molding can vary widely, from single-color applications to more complex double-color processes that enhance aesthetics and functionality. By mastering the art of mold plastic injection, manufacturers can achieve remarkable results tailored to specific needs.
Importance of Injection Molding in Industry
The significance of injection molding in industry cannot be overstated; it is a cornerstone for producing everything from automotive components to household goods. This technique not only reduces waste but also enhances production speed, making it essential for meeting consumer demands efficiently. As industries evolve, the reliance on advanced plastic injection molding techniques continues to grow, driving innovation and competitiveness.
Overview of Materials Used
A diverse range of materials can be used in the plastic injection molding process, with each offering unique properties suited for different applications. Injection moldable plastics include thermoplastics and thermosets, each chosen based on their performance requirements and end-use characteristics. By understanding these materials and how they interact with various types of injection molding machines, designers can make informed choices that optimize product quality and functionality.
What is Injection Molding
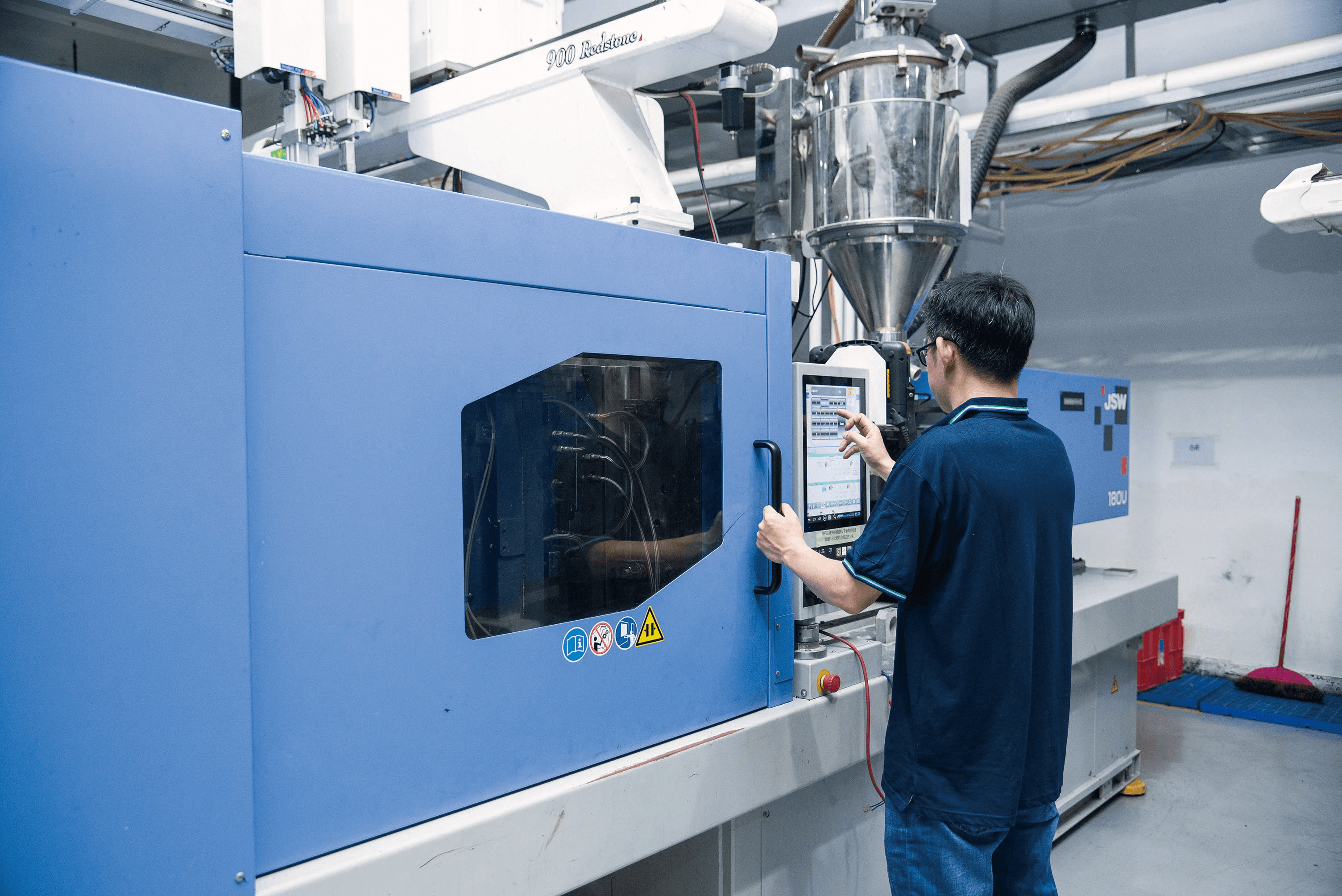
Injection molding is a manufacturing process that allows for the mass production of plastic parts with high precision and repeatability. This technique involves injecting molten plastic into a mold, where it cools and solidifies into the desired shape. As a cornerstone of modern manufacturing, injection molding stands out for its efficiency and ability to produce complex geometries.
Definition of Injection Molding
At its core, injection molding is the process of creating parts by forcing molten material into a mold cavity. This method is predominantly used for plastic materials but can also accommodate metals and glass in specialized applications. The versatility of injection molding has made it one of the most popular types of injection molding techniques in various industries.
How Injection Molding Works
The magic of injection molding lies in its systematic approach: first, raw plastic pellets are heated until they become a viscous liquid. This molten plastic is then injected under pressure into a pre-designed mold plastic injection, where it takes on the shape of the cavity as it cools down. Once solidified, the mold opens to release the finished part, making this process both efficient and effective for producing large quantities.
Key Components of Injection Molding
An injection molding machine consists of several critical components that work together seamlessly to create high-quality products. The main elements include the hopper (which feeds raw materials), barrel (where heating occurs), screw (that mixes and injects material), and the mold itself (the heart of any plastic injection molding operation). Understanding these components helps demystify how different types of injection molding can be achieved based on specific production needs.
Types of Injection Molding
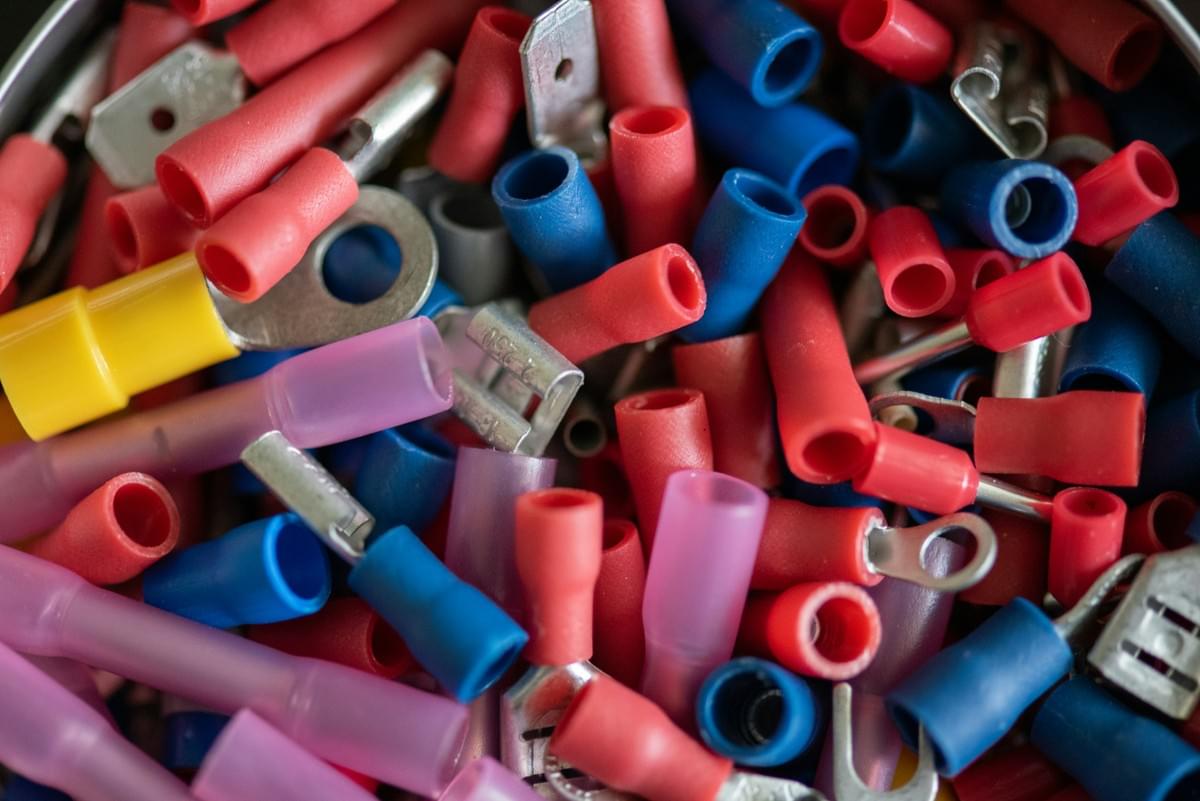
Overview of Injection Molding Techniques
Injection molding has evolved into a diverse field with several techniques designed to enhance efficiency and product quality. Common types of injection molding include traditional injection molding, blow molding, and rotational molding, each serving distinct purposes in manufacturing. By understanding these methods, businesses can optimize their production processes while ensuring they use appropriate mold plastic injection strategies.
In traditional plastic injection molding, molten plastic is injected into a mold cavity where it cools and solidifies into the desired shape. Blow molding is often used for hollow objects like bottles; air pressure inflates a parison inside a mold to create a seamless container. Rotational molding allows for uniform wall thickness in large hollow parts by rotating the mold while heating it—perfect for creating tanks or playground equipment.
Single-Color vs. Double-Color Molding
One significant distinction in types of injection molding lies between single-color and double-color (or multi-material) processes. Single-color molding involves injecting one type of plastic into a mold to create a uniform product; this process is straightforward and cost-effective for simpler designs. However, when aesthetics or functionality demand more complexity—like varying colors or material properties—double-color plastic injection molding comes into play.
Double-color molds are designed to inject two different materials or colors simultaneously or sequentially within one cycle. This technique not only enhances visual appeal but also allows manufacturers to combine materials with different characteristics—such as rigidity and flexibility—in one part. The result? A product that’s not only attractive but also functional without requiring additional assembly steps.
Variants in Injection Molding Equipment
The equipment used in plastic injection molding varies significantly based on the chosen technique and production requirements. Standard injection machines are designed primarily for single-material processes; however, advancements have led to specialized machines capable of handling complex tasks like multi-material injections or high-speed production runs. Understanding these variants helps manufacturers select an appropriate machine that aligns with their specific needs.
For instance, some modern machines come equipped with advanced features such as servo drives that enhance energy efficiency during operation while maintaining precision control over the injection process. Additionally, there are hybrid machines that combine hydraulic and electric technologies for optimal performance across various applications—from small-scale runs to large-volume productions using diverse types of injection molded plastics.
In summary, knowing about different types of injection molding techniques—including single-color versus double-color options—and recognizing equipment variations can significantly impact production efficacy and product quality in any manufacturing environment.
Injection Moldable Plastics
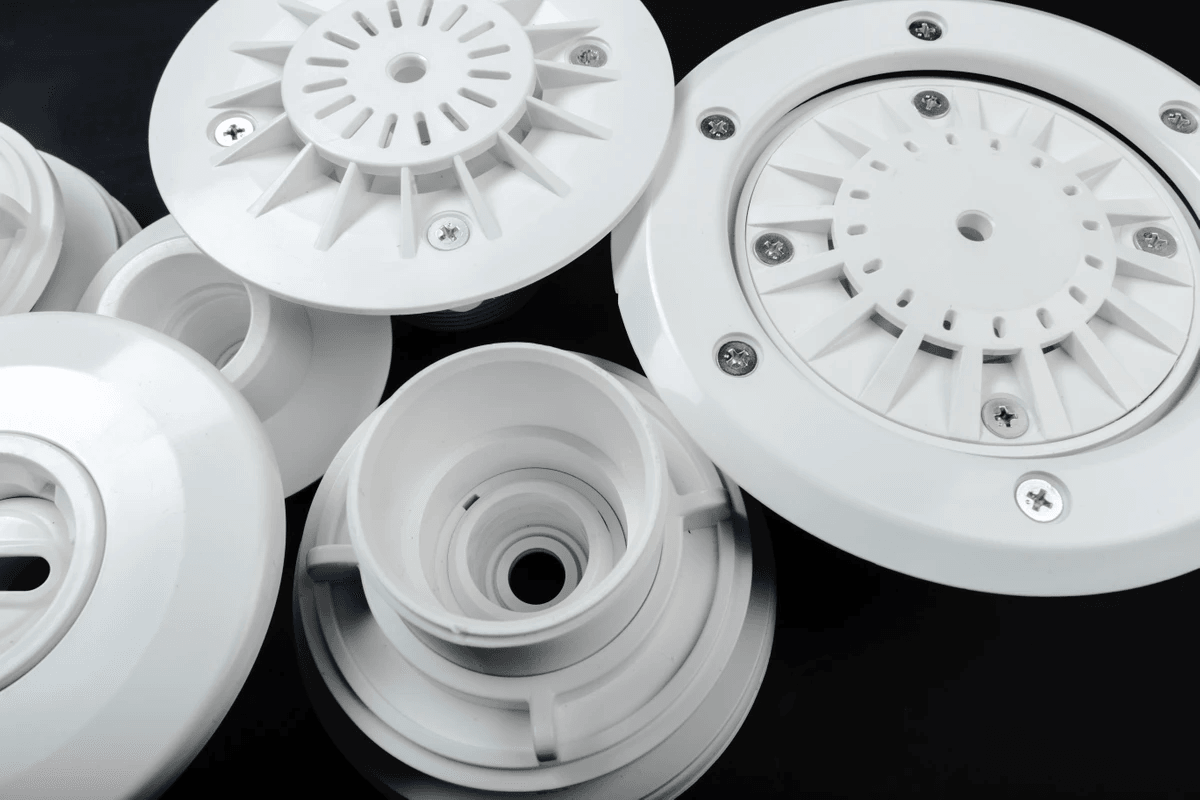
Injection moldable plastics are the backbone of the plastic injection molding industry. They encompass a wide variety of materials, each with unique properties that make them suitable for different applications. Understanding these types of injection molding materials is essential for optimizing production processes and achieving desired product characteristics.
Common Types of Injection Moldable Plastics
These versatile materials can be melted and reshaped multiple times without significant degradation, making them ideal for various plastic injection molding applications. Examples include polyethylene (PE), polypropylene (PP), polystyrene (PS), and polyvinyl chloride (PVC), each offering distinct advantages in terms of strength, flexibility, and resistance to chemicals.
Thermosets, on the other hand, are another category worth mentioning. Once cured through heat or chemical processes, thermosetting plastics cannot be remelted or reshaped; they become rigid and stable under high temperatures. This characteristic makes them perfect for applications requiring durability and stability, such as electrical components and automotive parts.
Comparison of Thermoplastics and Thermosets
The key difference between thermoplastics and thermosets lies in their behavior during heating processes. Thermoplastics soften when heated, allowing easy processing in an injection molding machine mold, while thermosets undergo a chemical change that hardens them irreversibly upon curing. This fundamental distinction influences their respective uses in the world of injection molding.
In terms of flexibility, thermoplastics offer greater adaptability due to their ability to be reprocessed multiple times without losing performance quality. Conversely, thermosets provide superior thermal stability and mechanical strength once set but lack the reusability that many manufacturers desire today in sustainable practices like mold plastic injection recycling efforts.
Ultimately, choosing between these two types depends on specific application requirements—considering factors such as temperature resistance, mechanical properties needed for the end product, cost-effectiveness in production runs using an injection molding machine.
Applications of Various Plastics in Molding
Different types of injection molding applications utilize specific plastics based on performance needs across industries like automotive, consumer goods, medical devices, electronics manufacturing among others. For instance, polypropylene is widely used in packaging due to its lightweight nature combined with excellent moisture resistance—perfect for food containers made via plastic injection molding techniques.
On the flip side, engineering-grade plastics like polycarbonate are favored for products requiring high impact resistance—think safety goggles or electronic housings molded using advanced techniques within an efficient injection molding machine setup. Moreover, specialized formulations like flame-retardant ABS find their niche within sectors demanding stringent safety standards such as aerospace or electrical industries.
In summary, understanding the diverse range of injection moldable plastics empowers manufacturers to select suitable materials tailored to meet specific project demands while enhancing overall efficiency throughout the entire plastic injection molding process—from design through production stages utilizing cutting-edge equipment available today.
The Injection Molding Machine
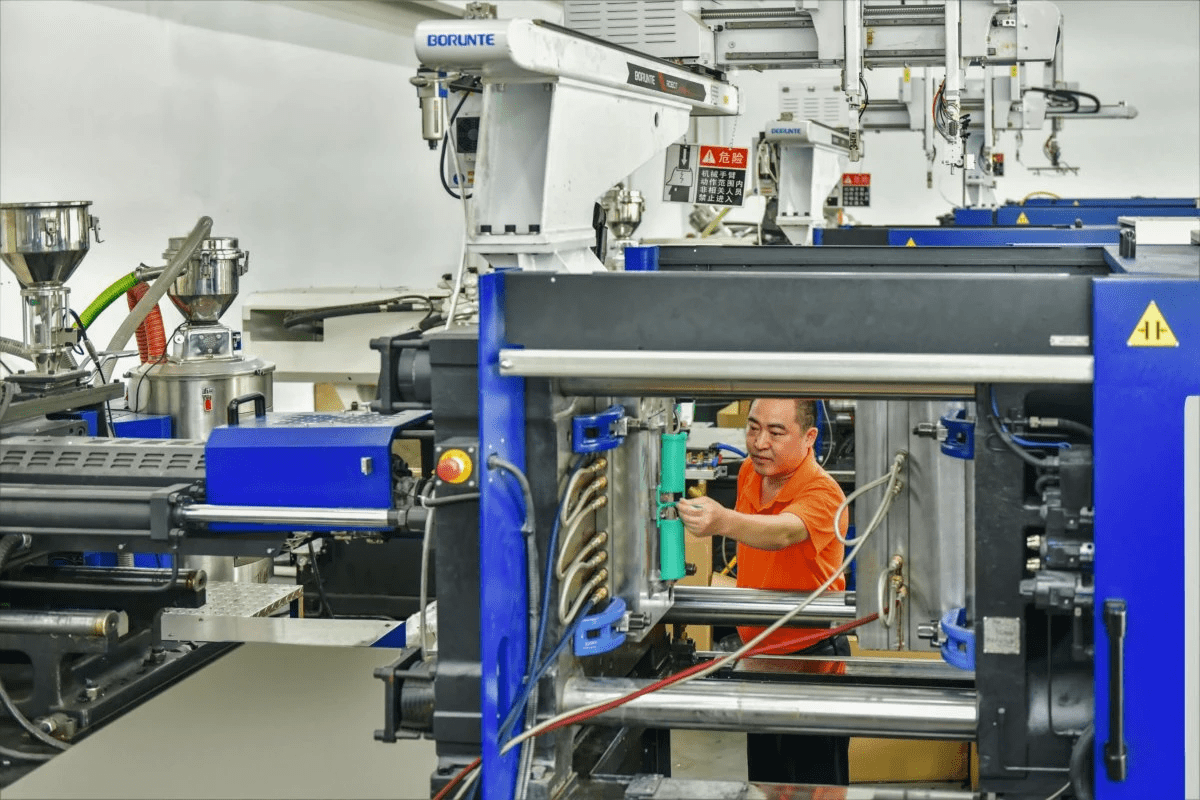
The injection molding machine is the heart of the plastic injection molding process, transforming raw plastic into intricate shapes and components. Understanding its anatomy, operation, and recent innovations is crucial for anyone involved in the industry. This section delves into these elements to provide a comprehensive view of this essential equipment in mold plastic injection.
Anatomy of an Injection Molding Machine
An injection molding machine consists of several key components: the hopper, barrel, screw, nozzle, and mold. The hopper feeds raw materials—often in pellet form—into the barrel where they are heated to a molten state by heaters surrounding it. The screw then rotates to mix and push the molten plastic through the nozzle into the injection moldable plastics mold, where it takes shape.
Another critical part is the clamping unit that holds the two halves of the mold together under pressure during injection. This ensures that no material leaks out during the molding process while also allowing for quick opening once cooling is complete. Understanding these components helps in appreciating how different types of injection molding can be applied effectively across various applications.
How the Injection Molding Machine Operates
The operation of an injection molding machine begins with loading plastic pellets into the hopper before being conveyed into a heated barrel. Here, heating elements melt down these pellets until they reach a specific viscosity suitable for injection into molds. Once melted, a reciprocating screw or plunger injects this molten plastic at high pressure through a nozzle into an accurately designed cavity within an injection molding machine mold.
After filling the cavity, cooling channels within the mold help solidify and set the shape as it cools down over time—this step is crucial in determining product quality and cycle time efficiency. Once cooled sufficiently, hydraulic or mechanical systems open up to release finished parts from their molds without damage. This entire process showcases how precision engineering allows for mass production of complex shapes using various types of injection molding techniques.
Innovations in Injection Molding Technology
Innovation continues to drive advancements in injection molding technology, enhancing efficiency and sustainability within production lines. Recent developments include improvements in energy efficiency through electric-driven machines that reduce power consumption compared to traditional hydraulic systems while maintaining high speed and accuracy during operation. Additionally, advancements like 3D printing technology are being integrated with conventional methods to create hybrid processes that allow for rapid prototyping alongside traditional plastic injection molding techniques.
Smart manufacturing technologies such as IoT devices are also revolutionizing how machines operate by providing real-time data analytics on performance metrics like temperature control and cycle times—allowing manufacturers to optimize their processes continuously. Furthermore, innovations focusing on sustainable practices have led to increased use of biodegradable materials as well as recycling initiatives aimed at reducing waste associated with traditional plastics used in mold plastic injections.
The Role of Baoyuan in Injection Molding
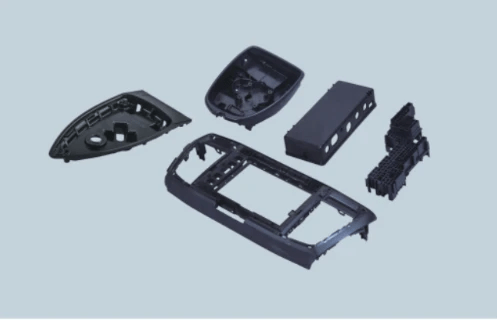
Baoyuan plays a pivotal role in the injection molding industry, leveraging its expertise to enhance the efficiency and quality of plastic injection molding processes. With a focus on innovative design and cutting-edge machinery, Baoyuan ensures that its products meet the diverse needs of clients across various sectors. Understanding the nuances of mold plastic injection is crucial for producing high-quality components that stand the test of time.
Baoyuan’s Expertise in Mold Design
Baoyuan's commitment to innovation means they continually adapt their designs to incorporate new materials and technologies, keeping pace with evolving industry standards. Their knowledge extends across various types of injection molding techniques, allowing them to tailor solutions that meet specific client requirements. As a result, customers benefit from molds that are not only efficient but also versatile enough for different applications.
Quality Assurance in Plastic Injection Molding
Quality assurance is at the heart of Baoyuan's operations when it comes to plastic injection molding. They implement rigorous testing protocols throughout the production process to ensure that every component meets stringent quality standards before leaving their facility. By focusing on both the performance of their injection molding machines and the integrity of their molds, they guarantee high-quality output consistently.
The use of state-of-the-art technology in their quality control processes allows Baoyuan to detect potential issues early on, significantly reducing waste and improving overall efficiency. This proactive approach ensures that clients receive reliable products made from top-notch injection moldable plastics with minimal defects or inconsistencies. Ultimately, this commitment to quality reinforces Baoyuan's reputation as a leader in the field.
Baoyuan's Contributions to Industry Standards
Baoyuan doesn't just follow industry standards; they actively contribute to shaping them within the realm of plastic injection molding. Through collaboration with other industry leaders and participation in key forums, Baoyuan helps establish best practices that elevate manufacturing processes across various sectors. Their insights into advancements in injection molding technology set benchmarks for others striving for excellence.
Moreover, by sharing knowledge about different types of injection molding methods and innovations related to injection molding machines, they foster an environment where continuous improvement is encouraged within the industry as a whole. Their dedication not only benefits individual clients but also enhances competitiveness among manufacturers globally by raising expectations for quality and efficiency standards.
In conclusion, Baoyuan stands out as an invaluable player in the world of plastic injection molding through its expertise in mold design, rigorous quality assurance practices, and contributions toward setting higher industry standards.
Conclusion
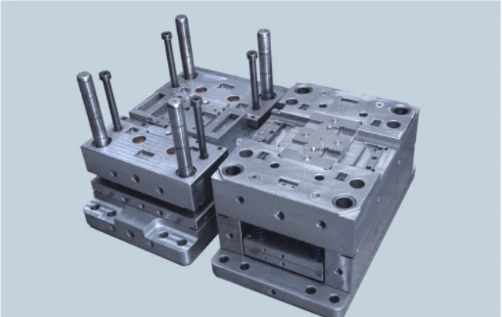
In wrapping up our exploration of injection molding, it’s clear that this manufacturing technique is not just a cornerstone of modern production but also a field ripe with innovation and potential. Understanding the various types of injection molding, from single-color to double-color processes, equips businesses and individuals alike with the knowledge necessary to make informed decisions in their projects. As we look ahead, the future trends in this industry promise exciting advancements that will continue to shape how we create and utilize mold plastic injection.
Future Trends in Injection Molding
The landscape of plastic injection molding is evolving rapidly, driven by technological advancements and sustainability goals. Innovations such as smart injection molding machines equipped with AI capabilities are set to enhance efficiency and precision in production processes. Additionally, there’s a growing emphasis on using eco-friendly materials among various types of injection molding techniques, ensuring that moldable plastics are not only effective but also environmentally responsible.
Benefits of Understanding Injection Molding
Grasping the intricacies of injection molding opens up a world of advantages for manufacturers and designers alike. Knowledge about different types of injection molding allows for better material selection and design choices that can lead to cost savings and improved product quality. Furthermore, understanding how an injection molding machine operates can significantly reduce downtime during production by anticipating potential issues before they arise.
Why Choose Professional Injection Molding Services
When it comes to executing complex designs or high-volume production runs, opting for professional plastic injection molding services can make all the difference. Experienced providers bring expertise in mold design and quality assurance that ensures your products meet industry standards consistently. By leveraging advanced machinery tailored for specific applications—like those found in specialized injection moldable plastics—you’ll benefit from enhanced efficiency and superior results compared to DIY approaches.