Introduction
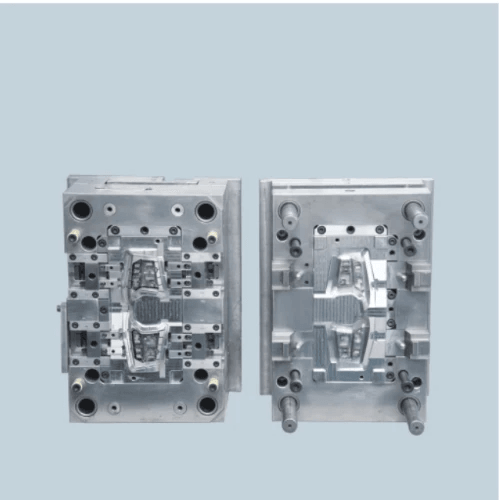
In the world of manufacturing, two processes often come to the forefront: injection molding and thermoforming. These techniques are pivotal in producing a wide array of plastic products, each with its unique advantages and applications. Understanding the nuances of injection molding vs thermoforming can significantly impact your project’s outcome, from design to production efficiency.
Understanding Injection Molding and Thermoforming
Injection molding is a process that involves injecting molten plastic into a mold to create intricate shapes and designs. On the other hand, thermoforming utilizes heat to soften plastic sheets, which are then formed over molds or into specific shapes. To grasp what is better than injection molding or when to choose one method over the other, it’s essential to explore how these processes work fundamentally.
Comparing Manufacturing Techniques
When comparing manufacturing techniques like injection molding vs thermoforming, it’s crucial to consider factors such as material usage, production speed, and complexity of designs. Injection molding typically offers greater precision for complex shapes but can require higher initial setup costs compared to thermoforming. Conversely, while thermoforming is generally faster for simpler designs and requires less investment upfront, it may not achieve the same level of detail as injection molding.
Applications of Each Process
Both injection molding and thermoforming have distinct applications across various industries. For instance, injection molding is frequently used for high-volume production runs where durability is paramount—think automotive parts or consumer electronics housings. Thermoforming shines in applications requiring lightweight packaging solutions or custom trays; understanding what is the difference between thermoplastic and injection molding can also help clarify why certain materials are chosen for specific applications.
What is Injection Molding?
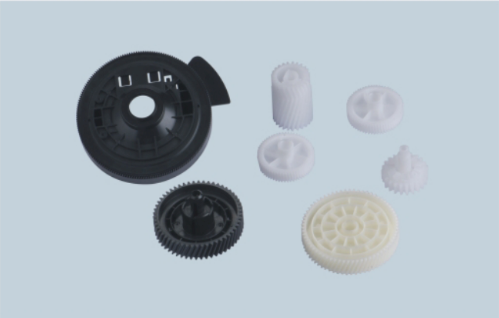
Injection molding is a manufacturing process widely used for producing parts by injecting molten material into a mold. This technique is particularly favored for its ability to create complex shapes with high precision and repeatability, making it ideal for large-scale production. In the ongoing debate of injection molding vs thermoforming, it's crucial to understand the nuances of this method.
Definition and Overview
At its core, injection molding involves forcing heated plastic or other materials into a mold cavity under high pressure. Once cooled, the material solidifies and takes on the shape of the mold, resulting in a finished product that can be removed easily. This process allows manufacturers to produce intricate designs that would be challenging or impossible with other methods like thermoforming.
When discussing what is better than injection molding, one must consider factors such as production volume, part complexity, and material selection. While it excels in many areas, there are alternative methods that might suit specific needs better depending on project requirements. Understanding these differences helps clarify what is the difference between thermoplastic and injection molding.
The Process Explained
The injection molding process begins with heating plastic pellets until they melt into a viscous liquid. This liquid is then injected into a precisely crafted mold under high pressure, filling every nook and cranny to ensure an accurate replication of the desired part design. After allowing time for cooling and solidification, the mold opens to release the finished product.
One key aspect that differentiates injection molding from other techniques like extrusion lies in its ability to produce more intricate shapes without extensive post-processing work. In contrast to processes like thermoforming which often require additional steps for trimming or finishing edges, injection molded parts typically come out ready for use or minimal processing right away. Thus, understanding what is the difference between molding and forming can significantly influence manufacturing decisions.
Common Materials Used
Injection molding primarily utilizes thermoplastics such as polyethylene (PE), polypropylene (PP), polystyrene (PS), and acrylonitrile-butadiene-styrene (ABS). These materials are popular due to their excellent flow characteristics when heated and their ability to return to solid form upon cooling without losing structural integrity.
In addition to thermoplastics, some applications may utilize thermosetting plastics or metals through specialized processes tailored for those materials; however, these cases are less common in standard injection molding scenarios compared to thermoforming techniques which often favor thinner sheets of plastic materials like PVC or PETG. Understanding these common materials can help clarify why certain industries prefer one method over another when comparing injection molding vs thermoforming.
What is Thermoforming?
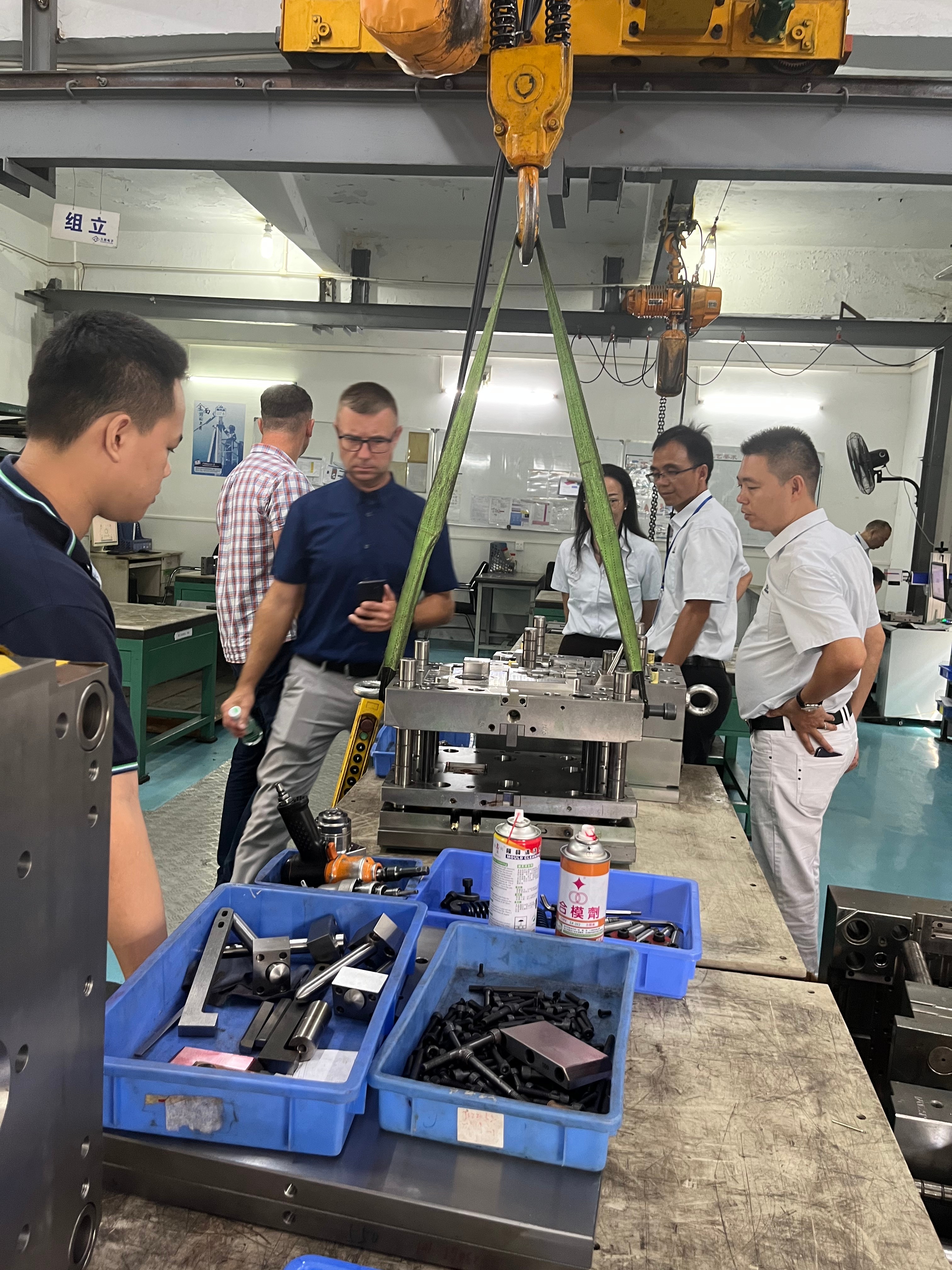
Thermoforming is a manufacturing process that involves heating a thermoplastic sheet until it becomes pliable, then shaping it over a mold to create various products. This technique is particularly favored for its efficiency and versatility in producing large quantities of items with relatively low tooling costs. Understanding thermoforming requires comparing it to other methods like injection molding, which leads us to explore the nuances between these two popular manufacturing processes.
Definition and Overview
At its core, thermoforming is all about transforming flat sheets of thermoplastic into three-dimensional shapes through heat and pressure. The process typically involves heating the plastic until it reaches a malleable state, followed by forming it over or into a mold using vacuum or pressure techniques. Unlike injection molding, which injects molten plastic into molds, thermoforming relies on the physical manipulation of heated sheets—thus raising questions like What is the difference between thermoplastic and injection molding?
The Process Explained
The thermoforming process begins with heating the thermoplastic sheet in an oven until it softens. Once pliable, the sheet is placed over a mold and formed either by applying vacuum pressure or using mechanical means to press the material into shape. After cooling and solidifying, the final product can be trimmed from excess material—a method that offers significant advantages when considering What is better than injection molding? due to its lower cost for smaller production runs.
Common Materials Used
Thermoforming primarily utilizes various types of thermoplastics such as polyvinyl chloride (PVC), polystyrene (PS), polyethylene terephthalate (PET), and acrylonitrile butadiene styrene (ABS). These materials are chosen for their flexibility during processing and durability once formed—a crucial factor when determining What is the difference between molding and forming? Different materials also impact factors like strength, weight, and cost-effectiveness in applications ranging from packaging to automotive components.
Key Differences Between Molding and Forming

When discussing manufacturing techniques, particularly injection molding vs thermoforming, it’s essential to understand the fundamental differences in their processes. Injection molding involves injecting molten material into a mold, while thermoforming shapes plastic sheets by heating and stretching them over a mold. This distinction leads to various applications and outcomes, making it crucial for manufacturers to choose the right method based on their needs.
Comparing Manufacturing Processes
The processes of injection molding and thermoforming are distinct yet complementary in the world of manufacturing. In injection molding, thermoplastic materials are heated until they become liquid and then injected into molds under high pressure, allowing for intricate designs and tight tolerances. On the other hand, thermoforming requires heating a sheet of plastic until pliable and then forming it over a mold; this method is generally simpler but may not achieve the same level of detail as injection molding.
What is the difference between thermoplastic and injection molding? While thermoplastics can be used in both methods, injection molding specifically refers to how these materials are processed into finished products. The choice between these two fabrication techniques often boils down to project requirements—complexity versus simplicity—and desired production volume.
Strength and Durability Factors
Strength and durability are critical considerations when comparing injection molding vs thermoforming. Injection molded parts typically exhibit superior strength due to their dense structure created by high-pressure processing, making them ideal for applications requiring robust components. In contrast, thermoformed products may be less durable since they often rely on thinner materials that can be more susceptible to damage or deformation under stress.
Moreover, when evaluating what is better than injection molding for specific applications, one must consider factors like intended use and environmental conditions affecting durability. For instance, if lightweight parts with adequate strength suffices (think packaging), then thermoforming could be a viable option despite its relative weakness compared to molded pieces. Ultimately, understanding the differences in strength helps manufacturers select the best process tailored to their product's functional demands.
Cost Considerations
Cost plays a significant role in deciding between injection molding and thermoforming for production projects. Generally speaking, while initial setup costs for injection molds can be quite high due to complexity—often leading one to wonder what is the difference between injection molding and extrusion—the per-unit cost decreases significantly with larger production runs thanks to efficiency gains from automation.
Conversely, thermoforming typically has lower initial costs since it requires less complex tooling; however, this advantage may diminish with higher volumes as labor-intensive processes come into play during production runs. Therefore, determining which process offers better value hinges on balancing upfront expenses against long-term production costs while considering volume needs—ultimately guiding manufacturers toward an informed decision about whether they should opt for thermoforming or stick with traditional injection methods.
Pros and Cons of Injection Molding
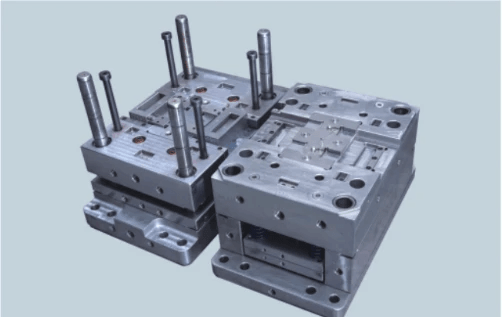
Injection molding is a widely used manufacturing process with its own set of advantages and disadvantages. Understanding these can help you determine if it’s the right choice for your project, especially when comparing injection molding vs thermoforming. Let’s dive into the perks and pitfalls of this technique.
Advantages of Injection Molding
One of the standout benefits of injection molding is its ability to produce complex shapes with high precision, making it ideal for intricate designs. This process also allows for high-volume production, which means lower costs per unit as production scales up. Additionally, injection molding can use a wide range of thermoplastic materials, offering flexibility in design and functionality—perfect for those wondering what is better than injection molding?
Another significant advantage is durability; parts produced through injection molding tend to have superior strength compared to those made through other methods like extrusion or thermoforming. This strength translates into longevity in various applications, from automotive components to consumer goods. Furthermore, the ability to incorporate multiple materials or colors in one mold adds an aesthetic appeal that many manufacturers find invaluable.
Disadvantages of Injection Molding
While there are many benefits, injection molding isn’t without its drawbacks. One major disadvantage is the high initial cost associated with creating molds; these expenses can be daunting for small-scale projects or startups. Additionally, once a mold is created, any changes can be costly and time-consuming—this rigidity often raises questions about what is the difference between thermoplastic and injection molding?
Another concern is that the process itself can produce waste material if not managed properly during production runs. This waste not only impacts costs but also raises environmental concerns that modern manufacturers are increasingly trying to address. Lastly, while injection molded parts are strong, they may lack some flexibility compared to thermoformed products; this could limit their application in certain industries.
Ideal Use Cases
Injection molding shines in scenarios where precision and volume are paramount—think automotive parts or medical devices that require strict adherence to specifications and standards. It’s also well-suited for producing consumer products at scale where durability plays a key role; items like plastic containers or electronic housings often benefit from this method's strengths.
However, understanding what is better than injection molding depends on specific project needs; if you require larger items with less precision or lower startup costs, alternatives like thermoforming might be more appropriate. In cases where design flexibility and rapid prototyping are essential—such as packaging design—thermoforming could easily outshine traditional injection methods.
In summary, while evaluating the pros and cons of injection molding versus other processes like extrusion or thermoforming might seem daunting at first glance, knowing its strengths helps make informed decisions tailored to your project's requirements.
Pros and Cons of Thermoforming
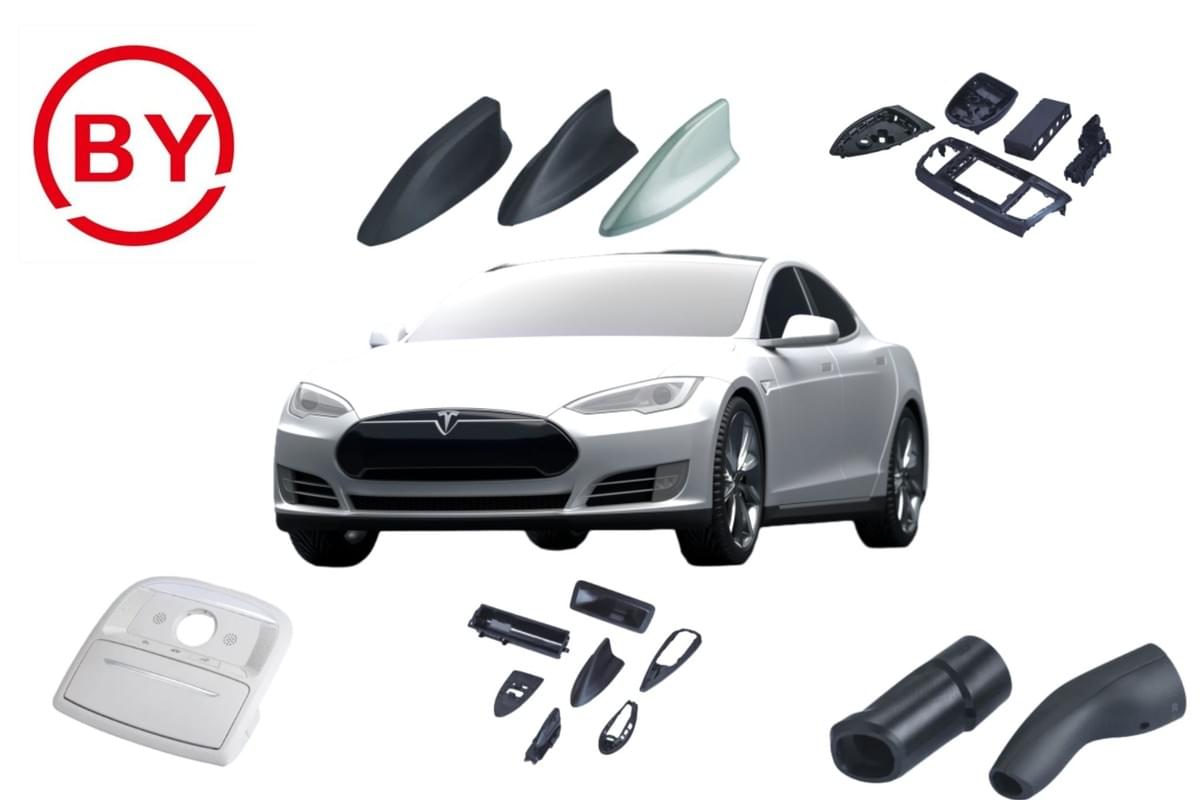
Thermoforming is a popular manufacturing process that offers distinct advantages and disadvantages when compared to methods like injection molding. Understanding these pros and cons can help you make an informed decision when choosing between injection molding vs thermoforming for your project. In this section, we’ll explore what makes thermoforming tick, from its benefits to its limitations, and the scenarios where it shines.
Advantages of Thermoforming
One of the standout advantages of thermoforming is its ability to produce large parts quickly and efficiently. This method allows for rapid prototyping and shorter lead times, making it ideal for projects that require speed without sacrificing quality. Additionally, thermoformed products tend to have a lower tooling cost compared to injection molding, which can be a game-changer for smaller businesses or startups looking to minimize upfront investments.
Another perk of thermoforming is its versatility in material selection. It works well with various thermoplastics, enabling manufacturers to choose materials that best suit their needs without being locked into rigid specifications like with some injection molding processes. This flexibility not only caters to diverse applications but also enhances the potential for creative designs.
Lastly, the finished products from thermoforming often exhibit excellent surface finishes and clarity, making them visually appealing—perfect for consumer-facing applications such as packaging or retail displays. When weighing options like What is better than injection molding? consider how these aesthetic qualities could impact your product's marketability.
Disadvantages of Thermoforming
While there are many benefits to using thermoforming, there are also notable disadvantages that should be considered carefully. One significant drawback is that it typically has lower strength compared to products made through injection molding; this can limit its use in high-stress applications where durability is crucial. For example, if you're comparing What is the difference between thermoplastic and injection molding? you'll find that thermoplastic components made via thermoforming may not withstand heavy loads as well as those produced through more robust methods.
Additionally, the complexity of shapes achievable with thermoforming may be limited when compared with injection molding's capabilities. Intricate designs or features often require more advanced tooling in other processes; thus, if your project demands high precision or complex geometries, you might find yourself at a crossroads here: What is the difference between molding and forming? The answer lies in their respective capabilities.
Finally, while tooling costs may be lower initially with thermoforming, they can add up over time if multiple molds are needed for different parts or variations—especially when considering production scale-up later on. So before diving into this method blindly based on initial cost savings alone, weigh all factors carefully against your long-term production goals.
Ideal Use Cases
Thermoforming shines brightest in specific scenarios where its strengths align perfectly with project requirements. It’s particularly effective for producing large-scale items like trays or containers used in food packaging—where speed and efficiency are paramount—and where aesthetics play a crucial role in consumer appeal due to clear visibility of contents inside packaging.
Moreover, industries such as automotive often utilize thermoformed parts for interior components because they allow designers freedom while maintaining reasonable costs during prototyping phases before moving onto more expensive methods like injection molding when mass production begins—showing how understanding injection molding vs thermoforming can guide strategic decisions across various stages of product development.
Lastly, small-batch productions benefit significantly from this technique since low-volume runs do not justify the high initial costs associated with creating molds required by traditional methods like extrusion or injection molding processes—making it an excellent choice for testing markets or introducing new product lines without excessive financial risk involved upfront.
Injection Molding vs Thermoforming: Real-World Applications
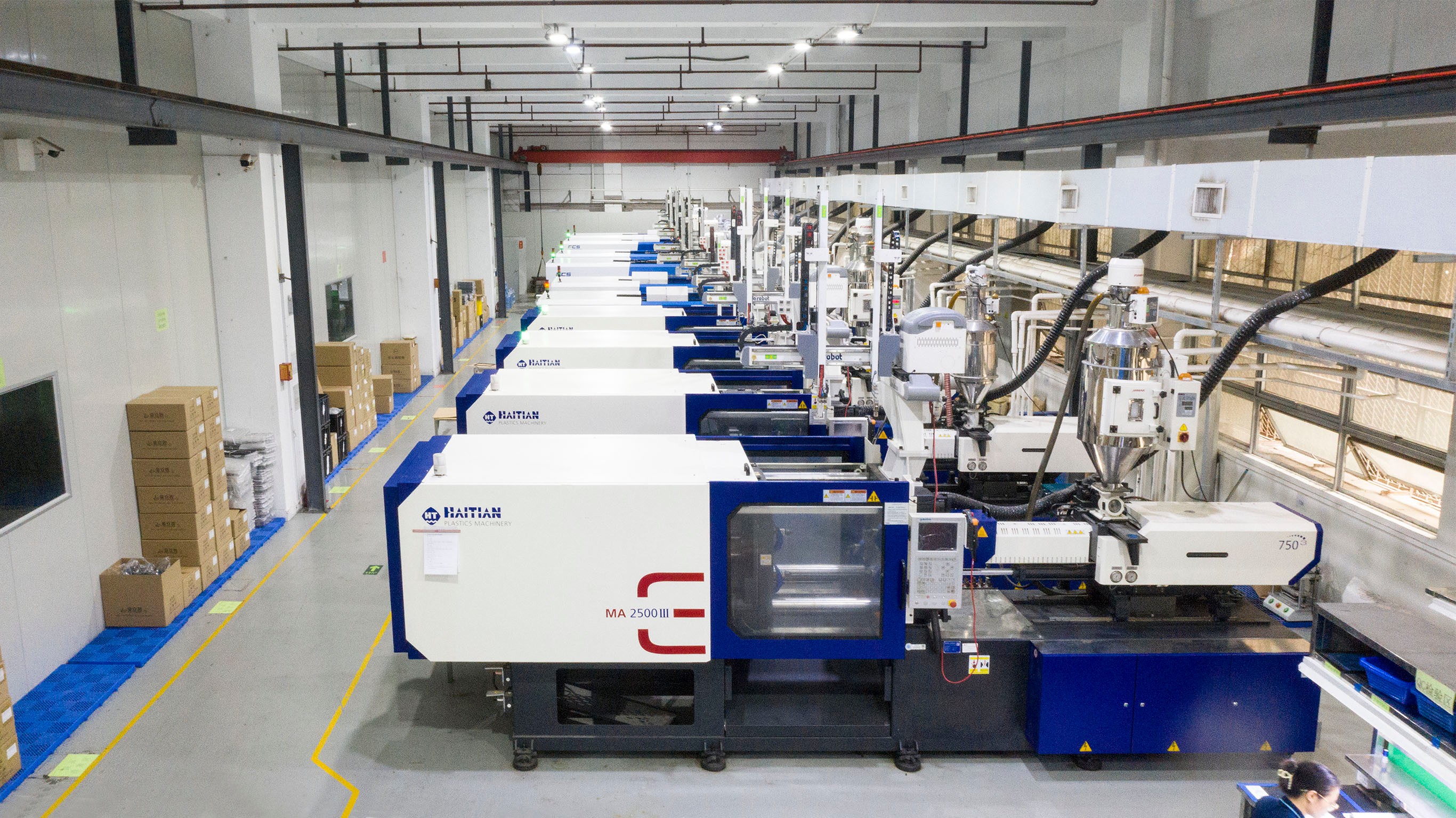
When it comes to manufacturing processes, understanding the real-world applications of injection molding and thermoforming can make all the difference in project outcomes. Each method has its unique strengths and weaknesses, making them suitable for different industries and products. By examining these applications, we can better grasp how to leverage both techniques effectively.
Industry Use Cases
Injection molding is widely used in industries such as automotive, consumer goods, and electronics due to its ability to produce complex shapes with high precision. For instance, car manufacturers rely on injection molding for creating intricate components like dashboards and bumpers that require durability and exact specifications. On the other hand, thermoforming shines in packaging industries where lightweight materials are needed; think of those clamshell packages you often see at the store or trays for food items.
In addition to packaging, thermoforming is also popular in medical device manufacturing where custom shapes are required quickly without extensive tooling costs. The question often arises: what is better than injection molding? Well, for certain applications involving larger parts or lower production volumes, thermoforming can be more efficient and cost-effective. Therefore, understanding the industry use cases helps clarify what is the difference between thermoplastic and injection molding.
Choosing the Right Method
Choosing between injection molding vs thermoforming ultimately depends on several factors including material properties, production volume, and design complexity. If you need high-volume production with precise tolerances, injection molding usually takes the cake due to its automated processes that ensure consistency across thousands of units. Conversely, if you're working on a prototype or a low-volume project requiring rapid turnaround times with less stringent tolerances—thermoforming might just be your best bet.
Another consideration is what is the difference between molding and forming in terms of flexibility; while injection molds are fixed once created (which can be expensive), thermoformed molds are typically simpler and less costly to produce—allowing for quick changes as designs evolve. This adaptability makes it easier for businesses to pivot based on market demands without breaking the bank on tooling costs.
Impact on Production Time
Production time varies significantly between these two methods; understanding this impact can help streamline manufacturing schedules effectively. Injection molding generally offers faster cycle times once set up since multiple parts can be produced simultaneously using multi-cavity molds—this means quicker delivery timelines for large orders! However, initial setup time may take longer due to mold fabrication.
On the flip side, thermoforming boasts shorter lead times especially when producing prototypes or small batches because it requires less complex tooling compared to injection molds—making it a go-to choice when speed is essential over mass production efficiency. So when considering production timelines alongside cost factors like what is the difference between injection molding and extrusion processes? It’s crucial to weigh these elements carefully before making your choice!
Conclusion
As we wrap up our exploration of injection molding and thermoforming, it’s clear that both manufacturing techniques have their unique strengths and weaknesses. Understanding the nuances of each process is crucial for making informed decisions in production. Whether you lean towards injection molding vs thermoforming may depend on your specific project requirements, budget constraints, and desired outcomes.
Summary of Injection Molding Benefits
Injection molding is renowned for its ability to produce high-precision parts with complex geometries at a rapid pace. This method excels in creating durable products from thermoplastics, making it suitable for industries like automotive and consumer goods. Additionally, the efficiency of injection molding can lead to lower costs per unit when producing large quantities, which is a significant advantage over other methods like extrusion.
Summary of Thermoforming Benefits
Thermoforming stands out for its versatility and lower initial setup costs compared to injection molding. It allows manufacturers to create larger parts with less material waste, making it an eco-friendlier option for projects requiring substantial surface areas or simple shapes. Moreover, thermoforming is often favored for short production runs or prototypes due to its faster turnaround time compared to traditional molding processes.
Making the Right Choice for Your Project
When deciding between injection molding vs thermoforming, consider factors such as project scale, complexity, and material requirements. For intricate designs that demand precision and durability, injection molding might be your best bet; however, if you’re looking at larger components with simpler designs or smaller production runs, thermoforming could be the way to go. Ultimately, understanding what is better than injection molding—or when to choose one method over another—will help streamline your manufacturing process and enhance product quality.