Introduction
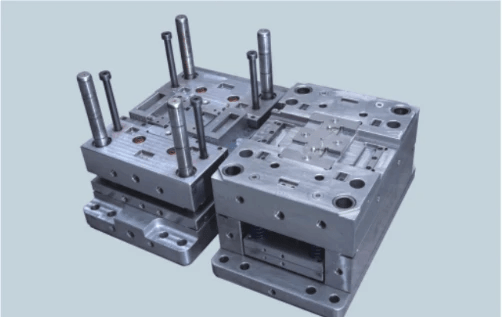
In the ever-evolving landscape of manufacturing, two techniques have emerged as frontrunners: 3D printing and injection molding. While both methods serve the purpose of creating tangible products from digital designs, they do so in fundamentally different ways. Understanding the nuances of 3D printing vs injection molding is crucial for businesses looking to optimize their production processes.
Understanding 3D Printing and Injection Molding
3D printing, also known as additive printing, builds objects layer by layer from a digital file, allowing for complex geometries and intricate designs that traditional methods struggle to achieve. In contrast, injection molding involves creating a mold into which molten plastic is injected, producing high volumes of identical parts with remarkable precision. The choice between these two manufacturing processes often hinges on project requirements such as design intricacy and production scale.
Key Differences in Manufacturing Methods
The primary distinction between 3D printing and injection molding lies in their approach to material usage and production speed. While 3D printing plastic allows for rapid prototyping and customization at lower initial costs, injection printing excels in producing large quantities efficiently once the mold is established. These differences can significantly impact timelines, budgets, and overall project feasibility depending on whether you lean towards low-cost 3D printing or high-volume injection 3D printing.
Choosing Between 3D Printing and Injection Molding
Deciding between these two manufacturing giants requires careful consideration of your project's specific needs—be it cost efficiency or design flexibility. For small runs or unique customizations, low-cost 3D printing can be a game-changer; however, if mass production is your goal, the upfront investment in injection molding may pay off handsomely over time. Ultimately, weighing the advantages of each method will guide you toward making an informed choice tailored to your production ambitions.
Cost Considerations
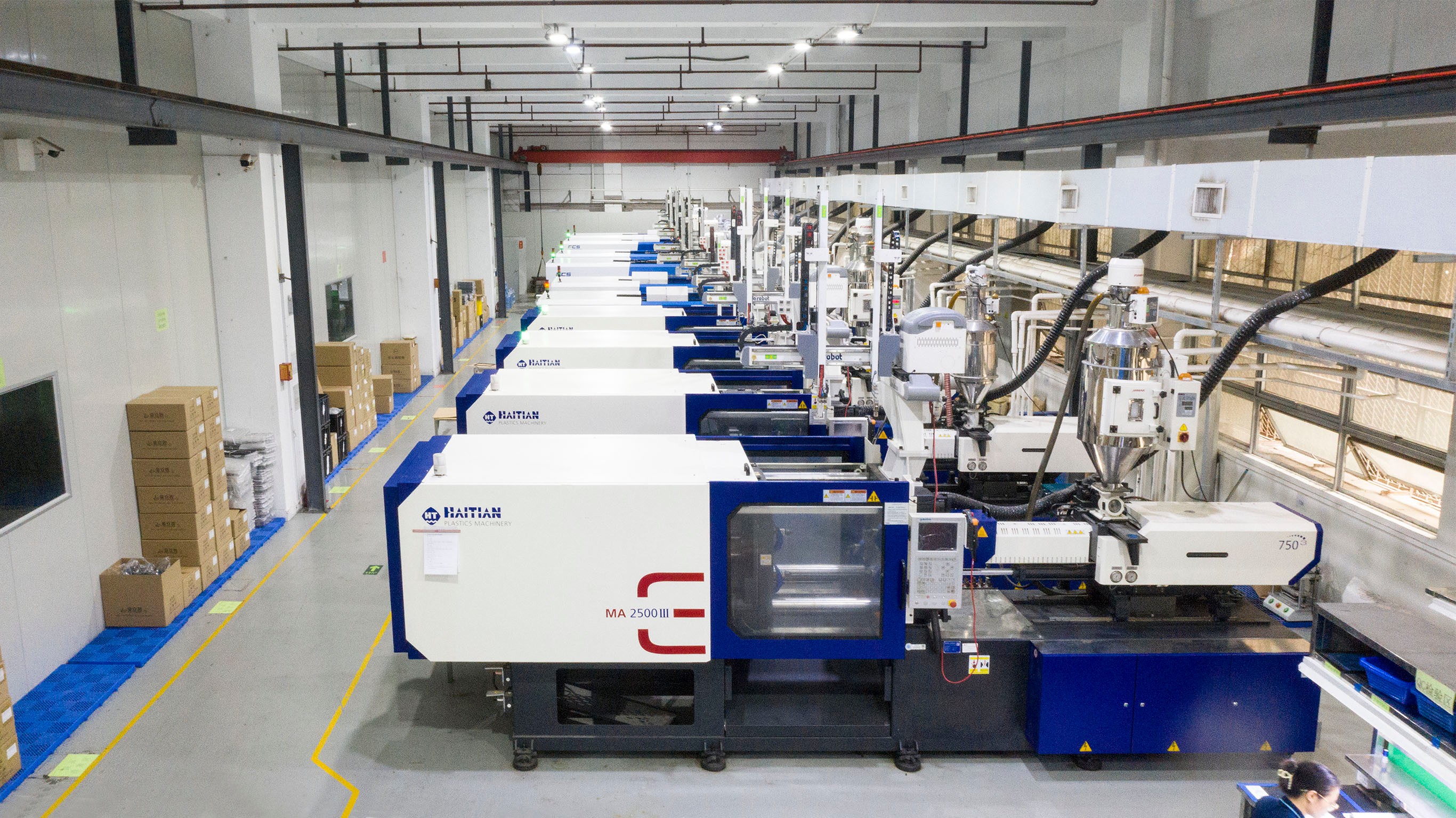
Initial Setup and Material Costs
The initial setup costs for injection molding can be quite steep, primarily due to the need for custom molds and tooling. These molds are often expensive to design and manufacture, making injection printing a significant upfront investment. On the other hand, 3D printing offers a more accessible entry point; with low-cost 3D printing options available, you can start producing parts without breaking the bank on mold creation.
Material costs also vary between these two methods. While injection 3D printing typically utilizes materials that require higher upfront investment in bulk quantities, 3D printer plastic can be sourced at lower prices for smaller runs or prototypes. This flexibility makes additive printing an attractive option for startups or projects with limited budgets looking to test designs before committing to larger-scale production.
Long-Term Savings with Injection Molding
Despite its higher initial costs, injection molding often leads to significant long-term savings when producing high volumes of parts. Once the molds are created, they can produce thousands of identical items at a rapid pace—reducing per-unit costs dramatically as production scales up. In contrast, while low-cost 3D printing is economical for small runs or prototypes, it may not provide the same cost efficiency when large quantities are required.
Moreover, injection molded parts usually have superior strength and durability compared to many 3D printed alternatives due to the material properties achieved through high-pressure molding techniques. This means fewer defects and less waste over time—further contributing to long-term savings in both material usage and labor costs associated with quality control measures. So if you're planning on mass-producing components that need to withstand rigorous use, investing in injection molding could pay off handsomely.
Cost-Effectiveness of Low Cost 3D Printing
The ability to quickly iterate designs without incurring hefty mold fees allows designers greater creative freedom while keeping budget constraints manageable. For many businesses looking at a test-and-learn approach before committing fully to a design direction or product line expansion, additive printing proves invaluable.
Additionally, advancements in technology have made high-quality materials available for 3D printer plastic at competitive prices—allowing even small businesses access to professional-grade outputs without excessive financial burden. This democratization of manufacturing means that startups can compete effectively against larger firms by leveraging innovative production methods like low-cost 3D printing while maintaining quality standards that satisfy customer expectations.
Production Volume
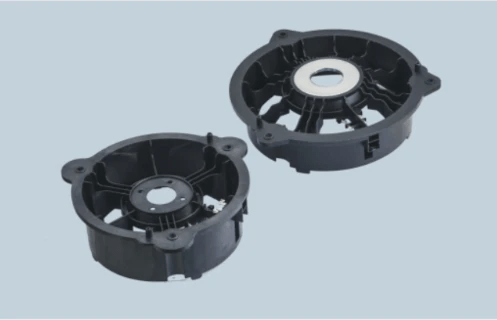
Best Practices for High-Volume Production
For high-volume production, injection molding generally reigns supreme due to its ability to produce large quantities of parts quickly and consistently. By creating a mold that can be used repeatedly, injection printing allows manufacturers to churn out thousands of identical pieces with minimal variation. However, when considering 3D printing vs injection molding for high volumes, it's essential to keep in mind that while low-cost 3D printing may be suitable for prototyping or small runs, it typically lacks the speed and efficiency needed for mass production.
To maximize efficiency in high-volume scenarios using injection molding, companies should focus on optimizing mold design and material selection. This includes choosing durable materials that can withstand repeated use while ensuring that the molds are designed for quick cycle times. On the other hand, if you lean towards additive printing methods like 3D printing plastic technologies, consider streamlining your designs for faster print times while still maintaining quality.
Ideal Uses for Additive Printing
Additive printing shines in areas where customization and rapid prototyping are key factors. Industries such as aerospace, automotive, and healthcare benefit greatly from the flexibility offered by 3D printer plastic technologies; they can create complex geometries that would be impossible or prohibitively expensive with traditional manufacturing methods like injection molding. For instance, custom components tailored specifically to individual specifications can be produced quickly without the need for extensive tooling changes.
Moreover, low-cost 3D printing is perfect for short runs or one-off projects where speed trumps volume—think art installations or bespoke consumer products. When you need a unique part made fast without breaking the bank on molds or setup costs, additive manufacturing is your best friend! Thus, knowing when to leverage these capabilities can lead to significant advantages over traditional methods.
Scalability of Injection 3D Printing
Scalability is a critical consideration when comparing production methods; here’s where injection 3D printing shows its true potential in larger batch productions. Once an initial investment is made in mold creation—a cost-effective long-term strategy—manufacturers can scale up operations with relative ease by increasing machine run time or adding additional machines without major redesigns necessary each time a new product line emerges.
However, scaling up with traditional 3D printing requires careful planning since each unit takes time to print individually—a stark contrast to how quickly molds produce parts via injection molding techniques. While innovations in multi-material printers are emerging that may change this dynamic over time (and certainly worth watching), currently there remains a clear delineation between what works best at scale versus what excels at customization through additive processes.
Ultimately choosing between these two giants—3D printing vs injection molding—requires understanding not just your current needs but future aspirations as well!
Design Flexibility
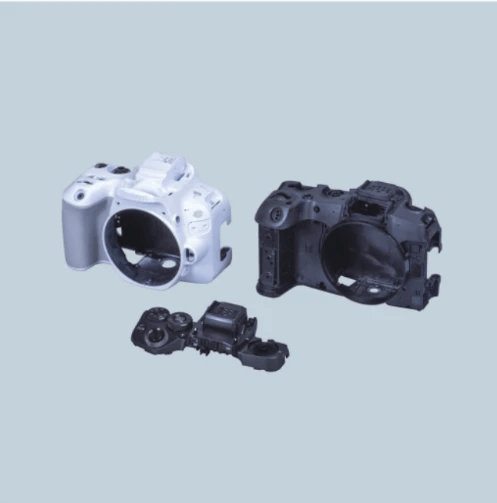
Creative Freedom with 3D Printer Plastic
One of the standout advantages of 3D printing is the sheer variety of 3D printer plastic available for different applications. From flexible materials to rigid options, creators can select the perfect fit for their projects, enabling them to push boundaries in design. This versatility not only enhances creativity but also allows for rapid prototyping, where ideas can be tested and iterated quickly without significant cost implications.
Constraints in Injection Printing
In contrast, injection printing comes with its own set of limitations that can stifle creativity. The need for molds means that any design changes require time-consuming adjustments or completely new setups, which can be both costly and tedious. Additionally, intricate designs may not translate well into injection molded parts due to flow limitations and material constraints, making it challenging to achieve the same level of detail as found in low-cost 3D printing.
Customization Opportunities with Baoyuan's Expertise
With Baoyuan's expertise in additive manufacturing, customization opportunities abound that cater specifically to unique project needs. Whether you're looking for bespoke designs or small batch runs tailored to specific requirements, Baoyuan excels at leveraging 3D printing technology effectively. By combining their knowledge with advanced techniques in 3D printing vs injection molding debates, they ensure clients receive personalized solutions that maximize both functionality and aesthetics.
Speed of Production
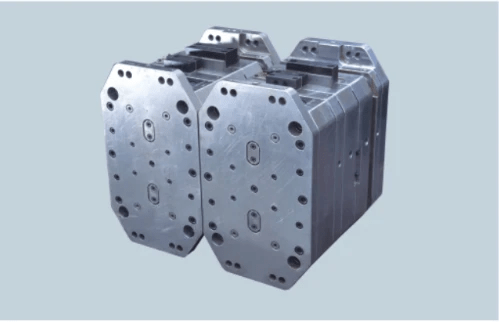
Speed Advantages of 3D Printing
3D printing shines in its ability to produce parts almost instantaneously compared to traditional methods. With low cost 3D printing, you can go from concept to creation in a matter of hours rather than weeks, making it an attractive option for small batches or one-off designs. Furthermore, since there’s no need for mold creation, designers can experiment freely with different shapes and features without worrying about the lengthy setup times associated with injection printing.
Lead Times for Injection Molding
On the flip side, injection molding has its own set of lead times that can be quite lengthy due to the initial setup required for mold creation. Once molds are created—often taking weeks or even months—the actual production runs are fast; however, that upfront time investment can be a deterrent for projects needing quick turnaround. Consequently, while injection 3D printing might excel in high-volume situations once established, it cannot compete with the rapid prototyping capabilities of 3D printers when speed is crucial.
Balancing Speed and Quality
While speed is essential in manufacturing decisions, it's vital not to sacrifice quality in pursuit of quicker production times. With additive printing technologies like low cost 3D printing offering rapid results, there’s still a risk of compromising on durability or finish quality if not managed correctly. Thus, finding a balance between speed and quality should guide your choice between methods; sometimes opting for slower injection molding may yield better long-term results despite longer lead times.
Material Options
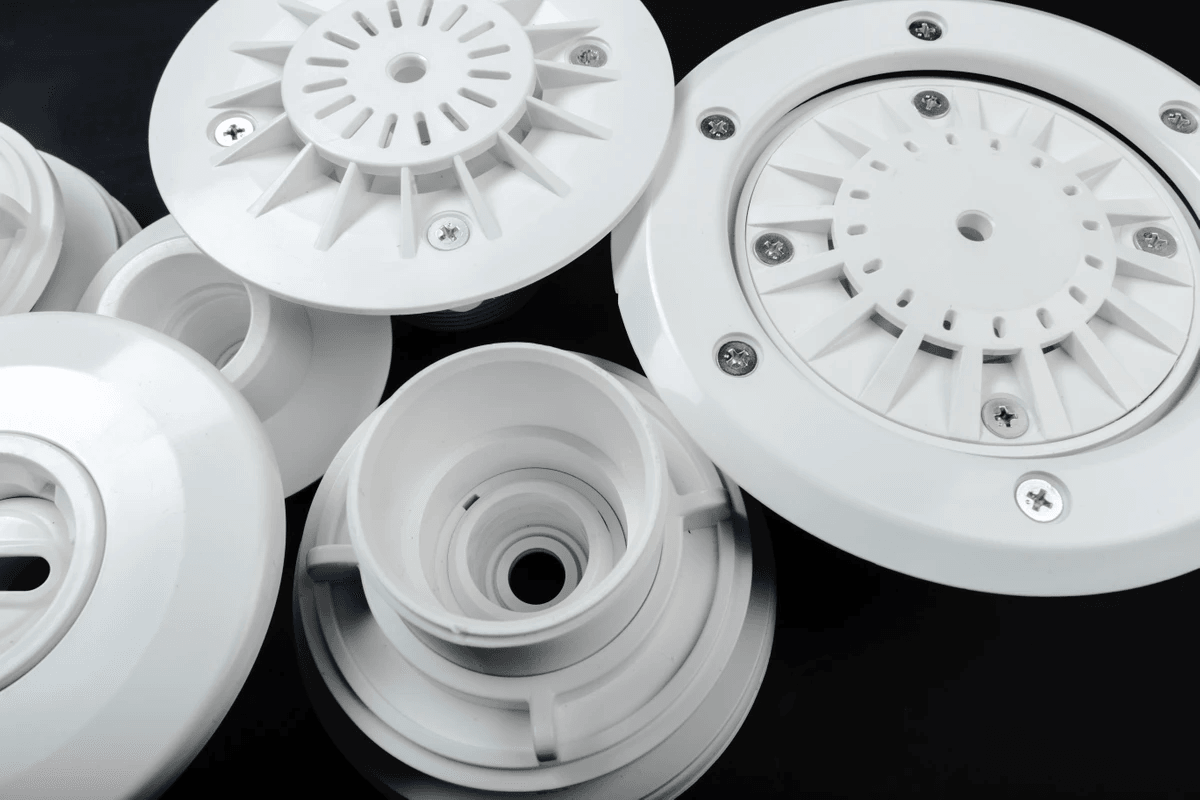
Variety in Materials for 3D Printing
One of the standout features of 3D printing is its impressive variety of materials available for use. From flexible filaments to rigid plastics, additive printing opens up a world where creativity knows no bounds. This flexibility allows designers to experiment with different types of 3D printer plastic, ensuring that they find the perfect match for their specific requirements.
Low-cost 3D printing has democratized access to these diverse materials, giving even small businesses the ability to produce prototypes and custom parts without breaking the bank. This versatility is particularly beneficial for industries like healthcare and automotive, where specialized materials can enhance functionality and performance. Ultimately, this wide selection empowers manufacturers to innovate without being limited by traditional constraints.
Strength and Durability in Injection Molding
On the flip side, injection molding excels when it comes to producing strong and durable parts that can withstand rigorous conditions. The process typically involves using high-quality thermoplastics that are engineered for strength, making it ideal for high-volume production runs where consistency is key. With injection printing, manufacturers can achieve impressive mechanical properties that are often superior to those found in many 3D printed components.
Moreover, injection 3D printing allows for intricate designs while maintaining structural integrity—an essential factor when creating parts intended for heavy-duty applications or long-term use. This durability makes injection molding a preferred choice in industries such as consumer electronics and automotive manufacturing where reliability is non-negotiable. Thus, while additive methods offer creative freedom, injection molding stands tall with its robust material capabilities.
Innovations in 3D Printing Plastic Types
The landscape of materials available for 3D printing continues to evolve at an astonishing pace thanks to ongoing innovations in technology and chemistry. New types of 3D printer plastic are being developed that exhibit enhanced properties such as increased heat resistance or improved tensile strength—features that were once exclusive to traditional manufacturing processes like injection molding. These advancements not only expand the range of applications but also bridge some gaps between additive processes and conventional methods.
Additionally, researchers are exploring biocompatible materials suitable for medical applications or sustainable options made from recycled substances—pushing the boundaries further than ever before in low-cost 3D printing solutions. As these innovations unfold, they promise exciting possibilities that could redefine how we think about material choices across various industries while keeping costs manageable without sacrificing quality or performance.
In conclusion, whether you lean toward the versatility offered by additive methods or the durability provided by injection molding will largely depend on your specific project requirements and goals—making it essential to weigh all material options carefully before deciding on a manufacturing approach.
Conclusion
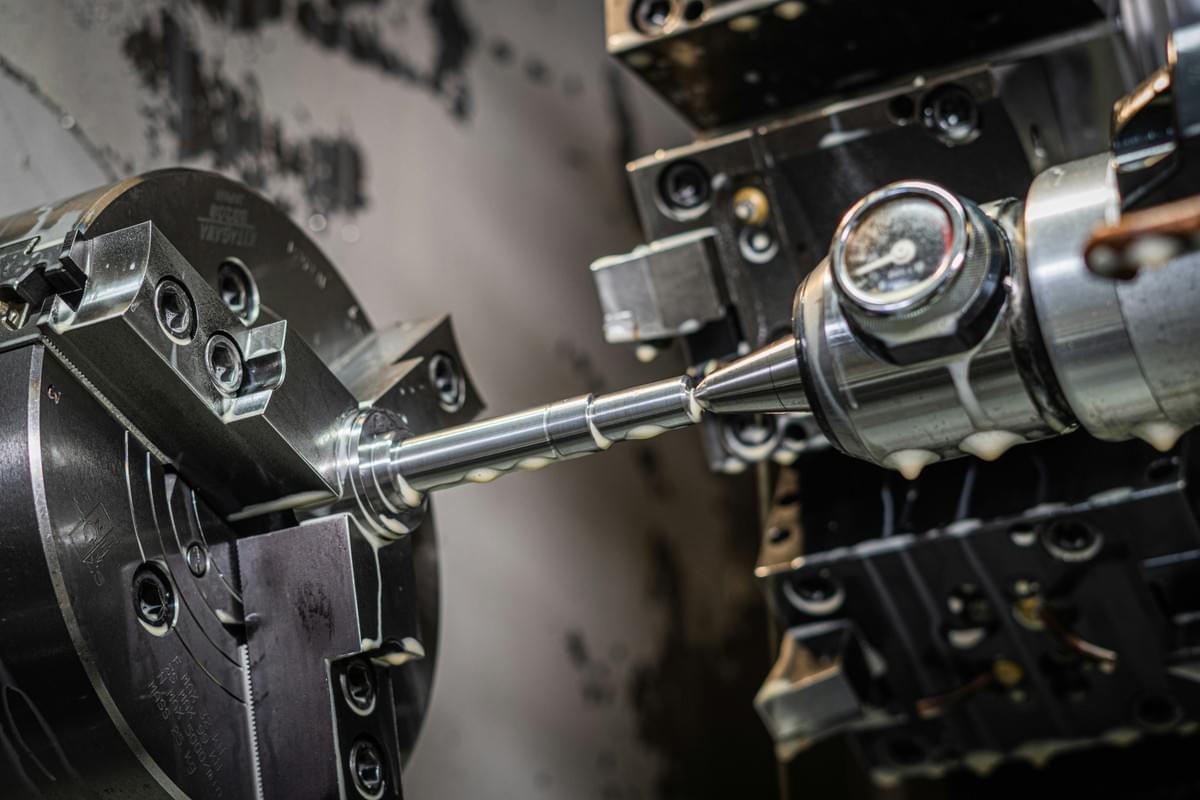
In the world of manufacturing, the debate between 3D printing vs injection molding continues to spark interest among designers and engineers alike. Each method brings its own strengths and weaknesses to the table, making it crucial to understand your project's specific needs before diving in. Whether you’re leaning towards low cost 3D printing for prototyping or considering the robust capabilities of injection printing for mass production, knowing your options will set you on the right path.
Making the Right Choice for Your Project
Choosing between 3D printing and injection molding is not a one-size-fits-all decision; it heavily depends on factors like volume, design complexity, and budget constraints. If your project involves intricate designs or requires rapid prototyping, additive printing might be your best bet due to its flexibility with 3D printer plastic materials. On the other hand, for high-volume production runs where durability is key, injection 3D printing could prove more advantageous in terms of efficiency and material strength.
Balancing Cost and Quality in Manufacturing
When weighing cost against quality in manufacturing processes, both methods have their merits that can’t be overlooked. While initial costs for 3D printing can be lower with low cost 3D printing options available, long-term savings may lean toward injection molding if you're producing large quantities consistently. Ultimately, finding a balance between upfront investments and ongoing expenses is essential to ensure that your choice aligns with both quality standards and financial viability.
The Future of 3D Printing vs Injection Molding
Looking ahead, both additive technologies and traditional methods like injection molding are evolving rapidly—each pushing boundaries in different ways. Innovations in 3D printer plastic types are expanding possibilities for customization while enhancing material properties that were once exclusive to injection molded parts. As industries continue to explore these advancements, understanding how these technologies intersect will be vital for making informed decisions about future projects.