Introduction
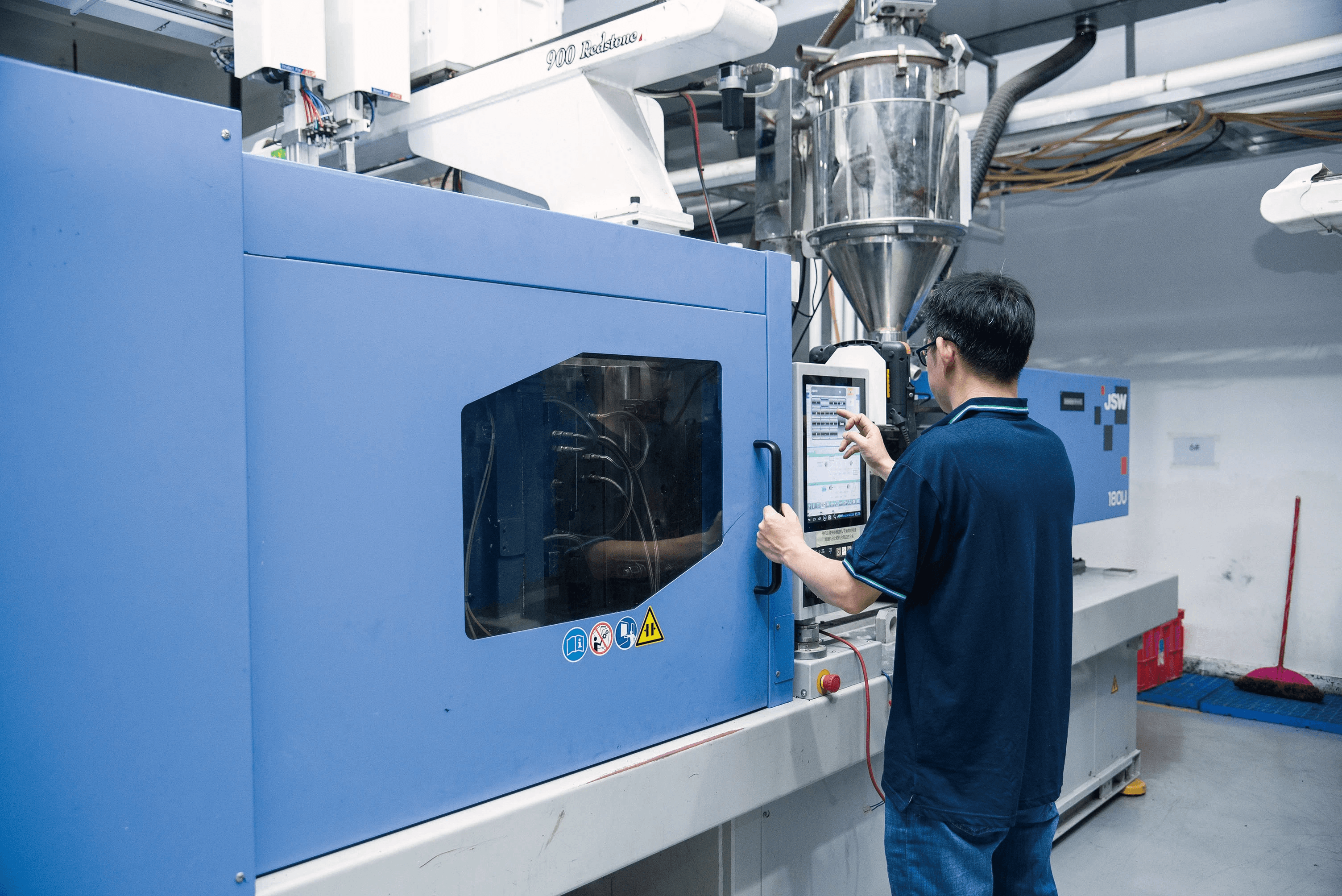
In the ever-evolving landscape of healthcare, injection molding for medical devices has emerged as a cornerstone technology, revolutionizing how medical products are designed and produced. This method not only enhances the efficiency of manufacturing but also ensures that high-quality standards are met consistently. With innovations in medical device manufacturing, the reliance on injection molding techniques has grown, leading to improved patient outcomes and streamlined production processes.
The Role of Injection Molding in Medicine
Injection molding plays a pivotal role in medicine by enabling the mass production of complex components with precision and reliability. This technique allows manufacturers to create intricate designs that are essential for various medical applications, from surgical instruments to diagnostic equipment. By facilitating the rapid production of high-quality products, injection molding significantly contributes to meeting the increasing demand for advanced medical devices.
Innovations in Medical Device Manufacturing
The field of medical device manufacturing is witnessing remarkable innovations that leverage cutting-edge technologies in injection molding. These advancements include the development of new materials and processes that enhance product performance while reducing costs. As a result, manufacturers can now produce a wider array of devices tailored to specific healthcare needs, showcasing what is the latest technology in injection molding.
Overview of Injection Molding Techniques
Understanding injection molding techniques is crucial for grasping how this process benefits the healthcare sector. Various methods exist within this realm, each designed to address different challenges associated with producing medical devices efficiently and effectively. From multi-material injection molding to overmolding, these techniques enable manufacturers to create versatile products that cater to diverse applications—so what are the applications of injection molding?
Understanding Injection Molding for Medical Devices
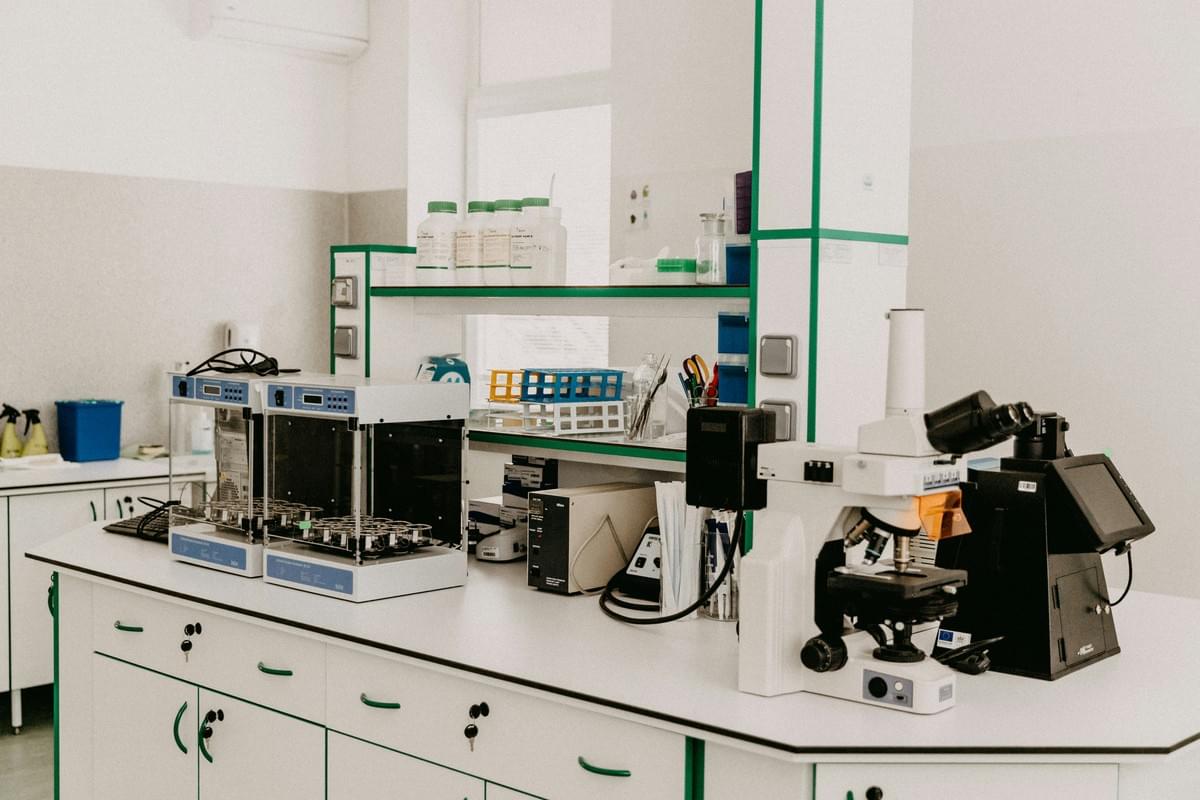
Injection molding is a pivotal process in the manufacturing of medical devices, transforming raw materials into precise and complex shapes that meet stringent healthcare standards. This technique allows for high-volume production with remarkable consistency, making it a go-to method in the medical field. By understanding what injection molding is and how it works, we can appreciate its significant impact on patient care and device innovation.
What is Injection Molding?
At its core, injection molding is a manufacturing process where molten material—typically plastic—is injected into a mold to create specific shapes and components. This process begins with heating thermoplastic or thermosetting polymers until they become liquid, after which they are forced into molds under high pressure. Once cooled and solidified, the resulting parts can be easily removed from the mold, ready to be used in various medical applications.
The beauty of injection molding for medical devices lies in its ability to produce intricate designs that are often required for advanced medical technology. From syringes to surgical instruments, this method enables the creation of lightweight yet durable components essential for modern healthcare solutions. Furthermore, advancements in machinery have allowed manufacturers to explore what is the latest technology in injection molding that enhances efficiency and precision.
Benefits of Injection Molding in Healthcare
One of the primary benefits of injection molding in healthcare is its capacity for mass production without compromising quality or accuracy. This means that thousands—or even millions—of identical parts can be produced quickly, which is crucial when meeting urgent demands for life-saving equipment or disposable supplies. Additionally, due to its efficiency and reduced waste generation compared to other manufacturing methods, injection molding proves economically advantageous.
Another key advantage is the versatility it offers; various materials can be utilized based on specific requirements such as biocompatibility or sterility—essential factors when considering what products can be made from injection molding within the medical field. Moreover, this technique supports complex geometries that allow designers to innovate while ensuring functionality and safety are maintained throughout a product's lifecycle.
Furthermore, with growing concerns over sustainability in manufacturing processes, many companies are now investing in eco-friendly materials suitable for injection molding applications—showcasing how this technique adapts to modern challenges while still delivering high-quality results.
Techniques Utilized in Injection Molding
The realm of injection molding encompasses several techniques tailored specifically for producing medical devices efficiently and effectively. One common approach includes multi-material or co-injection molding where two different plastics are combined during production; this allows manufacturers to create parts with varying properties such as flexibility or rigidity within a single component. Such innovations expand possibilities regarding what are the applications of injection molding across diverse healthcare sectors.
Another noteworthy technique involves insert molding—a process where pre-formed components (like metal inserts) are placed directly into molds before injecting plastic around them—resulting in strong bonds between different materials ideal for creating robust devices like dental tools or surgical instruments requiring precision engineering.
Finally, advancements like 3D printing integration with traditional injection methods exemplify how manufacturers continue exploring cutting-edge solutions; these developments not only streamline production but also enhance customization capabilities—a significant factor when considering what is injection molding technique in dentistry specifically designed dental devices tailored to individual patient needs.
Latest Technologies in Injection Molding
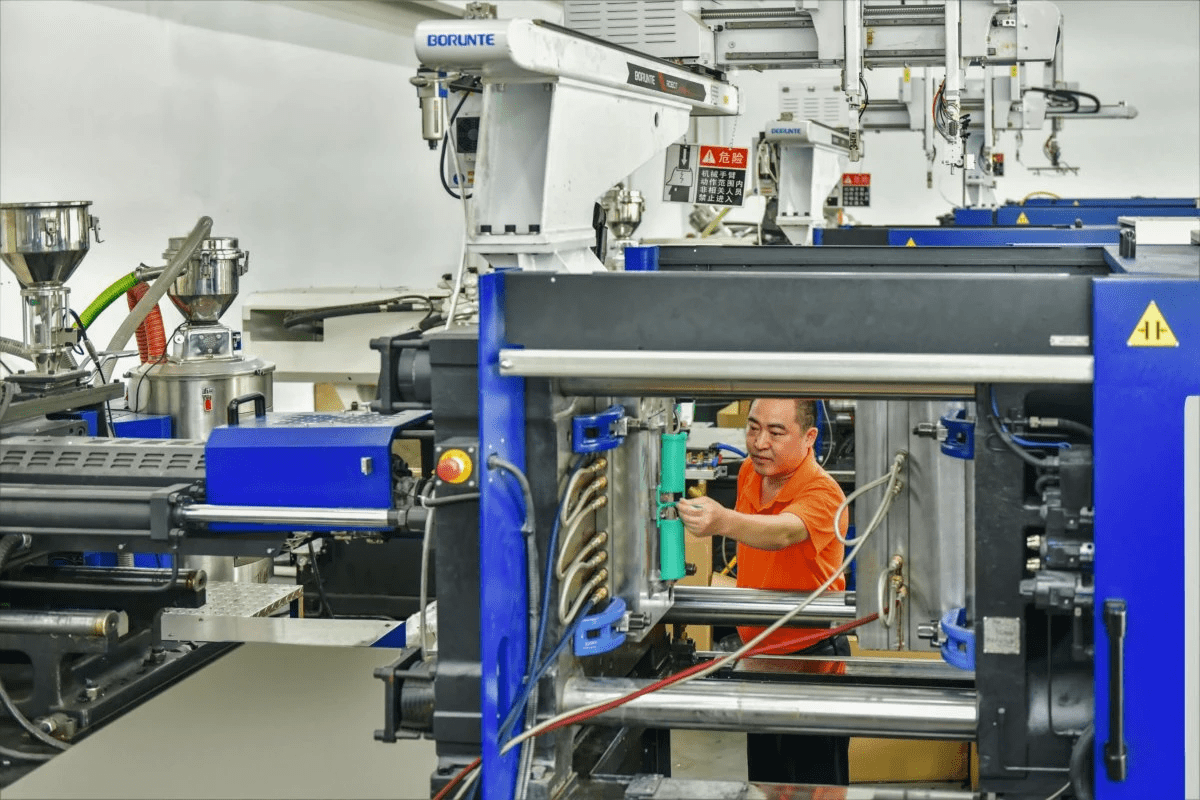
In the ever-evolving landscape of medical device manufacturing, injection molding for medical devices has witnessed remarkable technological advancements. These innovations not only enhance production efficiency but also improve the quality and precision of medical products. As manufacturers strive to meet stringent regulatory standards, staying updated on the latest technologies becomes crucial for success in this competitive field.
Advancements in Machinery and Materials
The machinery used in injection molding for medical devices has seen significant upgrades, with a focus on automation and precision. Advanced injection molding machines now incorporate features such as real-time monitoring and adaptive control systems that optimize production processes. Additionally, new materials designed specifically for healthcare applications—such as biocompatible polymers—allow manufacturers to create products that are safer and more effective.
Moreover, these advancements enable the creation of complex geometries that were previously challenging to achieve. With improved mold designs and enhanced cooling techniques, manufacturers can produce intricate components with reduced cycle times. This leads to faster turnaround times for critical medical devices, ultimately benefiting patient care.
Impacts of Robotics on Injection Molding
Robotics is revolutionizing injection molding processes by introducing unprecedented levels of automation and efficiency. Robotic arms are increasingly employed in handling tasks such as loading materials, removing finished products from molds, and performing quality inspections—all of which streamline operations significantly. This integration not only reduces labor costs but also minimizes human error, ensuring consistent product quality.
Furthermore, robotics allows for greater flexibility in production lines dedicated to injection molding for medical devices. Automated systems can quickly adapt to different product designs or batch sizes without extensive reconfiguration time, thus meeting the dynamic demands of healthcare markets effectively. As a result, manufacturers can respond swiftly to changes in consumer needs while maintaining high standards.
What is the latest technology in injection molding?
The latest technology making waves in injection molding includes 3D printing integration alongside traditional methods. By combining additive manufacturing with conventional injection molding processes, companies can create prototypes rapidly while refining their designs before mass production begins. This hybrid approach not only accelerates development timelines but also enhances customization options—perfectly aligning with what products can be made from injection molding.
In addition to 3D printing advancements, smart sensors embedded within machinery provide real-time data analytics that help optimize performance throughout the production cycle. These sensors monitor variables such as temperature and pressure during the process—allowing immediate adjustments that ensure high-quality outcomes consistently across batches. With these innovations at hand, it's clear how vital it is to stay informed about what are the applications of injection molding within various sectors including healthcare.
Applications of Injection Molding in Medical Devices
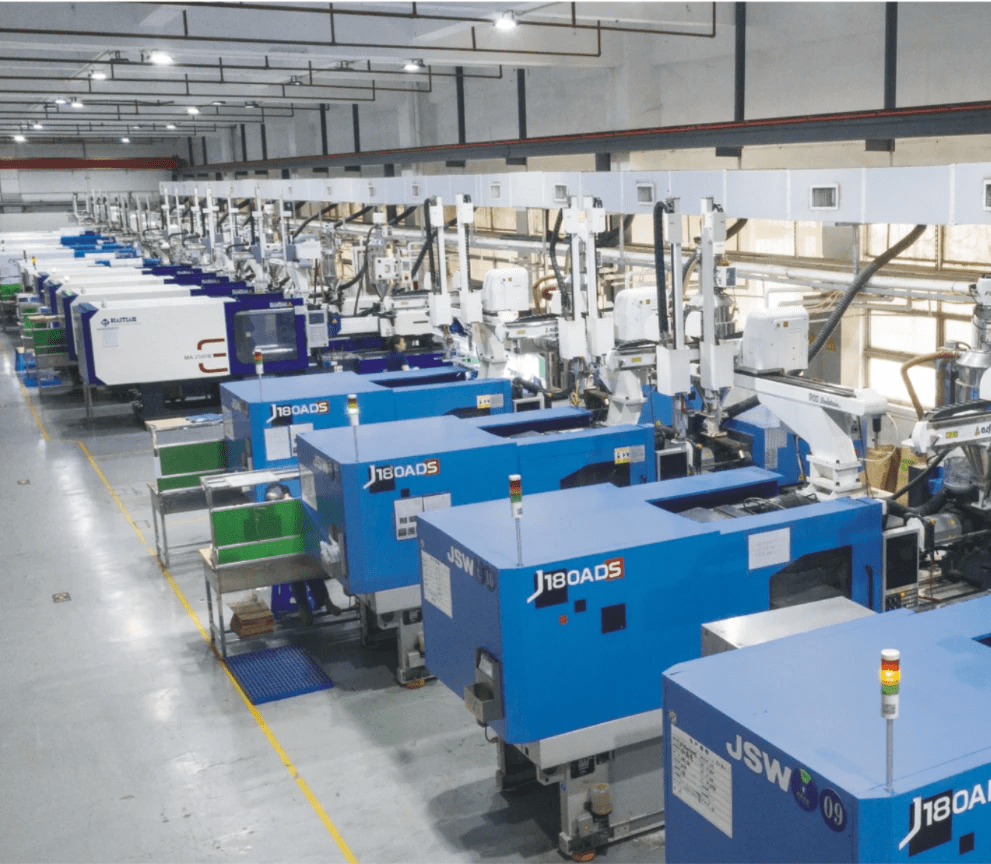
Injection molding for medical devices has revolutionized the healthcare industry by enabling the production of complex shapes and components that meet strict regulatory standards. This manufacturing technique is not only efficient but also allows for high-volume production, ensuring that essential medical devices are available when needed most. From life-saving equipment to everyday disposable supplies, injection molding plays a crucial role in maintaining patient care.
Life-Saving Equipment and Components
Life-saving equipment and components are among the most critical applications of injection molding for medical devices. Items such as surgical instruments, ventilator parts, and drug delivery systems are produced using this technique to ensure precision and reliability under pressure. The ability to create intricate designs with biocompatible materials means that these life-saving tools can be both effective and safe for patient use.
Moreover, advancements in injection molding technology have allowed manufacturers to produce components with enhanced functionality, such as integrated sensors or user-friendly features. This innovation not only improves the performance of medical devices but also enhances the overall experience for healthcare providers and patients alike. As we explore what products can be made from injection molding, it's clear that life-saving devices benefit immensely from this manufacturing method.
Disposable Medical Supplies
Disposable medical supplies are another area where injection molding shines brightly. Items like syringes, IV bags, and surgical gloves are produced at scale using this efficient process, ensuring that hospitals have a steady supply of necessary tools without compromising on quality or safety. The ability to produce these items quickly helps healthcare facilities manage their resources effectively while adhering to hygiene standards.
The versatility of injection molding allows manufacturers to create a wide variety of disposable products tailored specifically for different medical needs. By utilizing innovative materials and designs, companies can enhance the functionality of these supplies while keeping costs manageable. This brings us back to our earlier question: what are the applications of injection molding? Clearly, disposable medical supplies represent a significant portion of its diverse applications.
What are the applications of injection molding?
The applications of injection molding extend far beyond just life-saving equipment and disposables; they encompass a wide range of products designed for various healthcare needs. From diagnostic devices like blood glucose meters to dental tools used in procedures—it's evident that this manufacturing technique supports numerous facets within medicine. Additionally, custom molded solutions allow companies to innovate continuously while meeting specific market demands.
For instance, specialized molds can be created for unique device requirements or even patient-specific solutions in fields such as orthopedics or prosthetics—showcasing how adaptable this technology truly is! Furthermore, as we ponder what is the latest technology in injection molding?, we find exciting developments like 3D printing integration that promise even greater customization options moving forward.
In summary, whether it’s through producing reliable life-saving equipment or versatile disposable supplies, injection molding plays an indispensable role in modern medicine—enhancing patient care with every molded piece created.
Products Made from Injection Molding
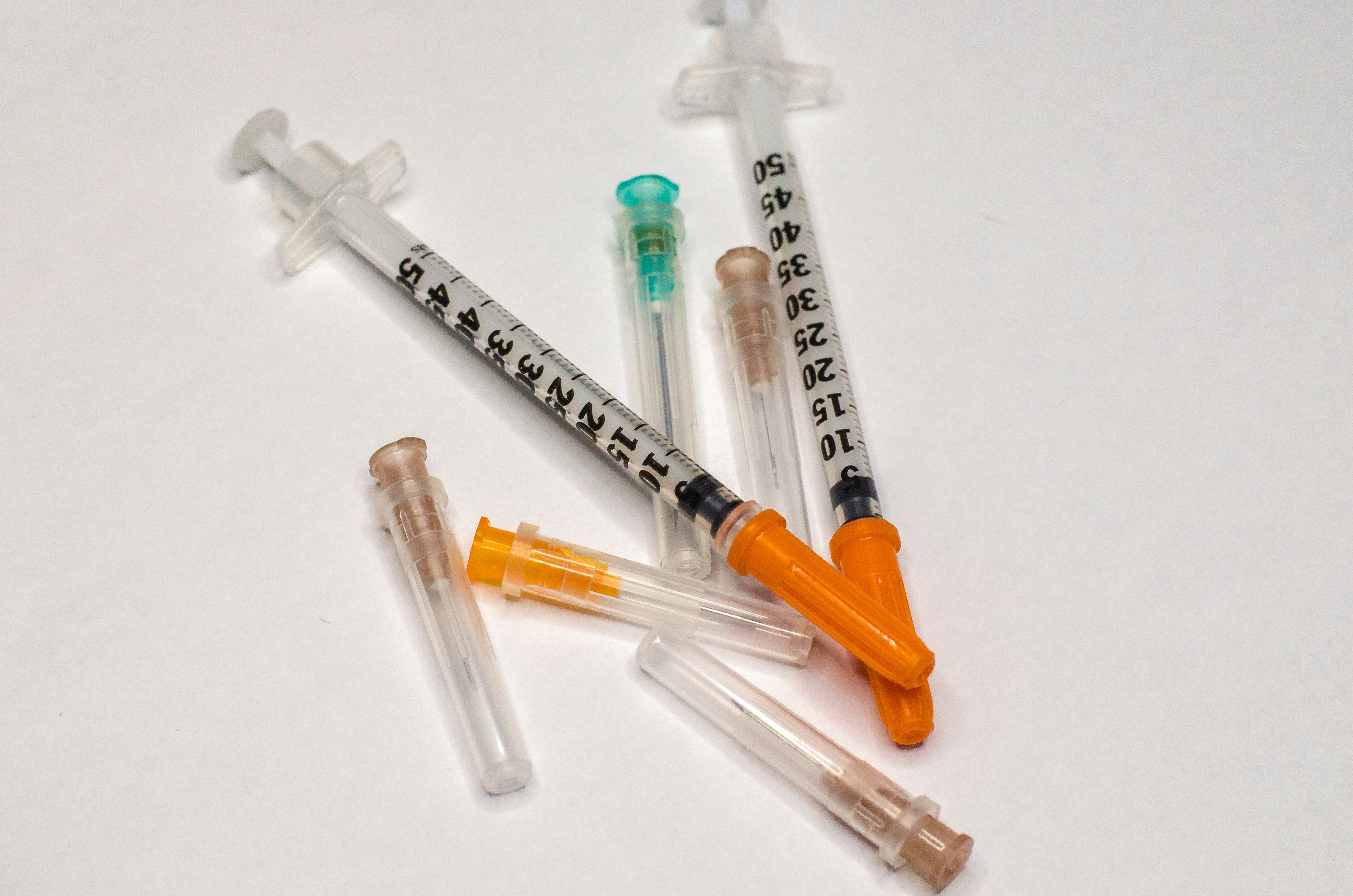
Injection molding for medical devices has revolutionized the healthcare industry by providing efficient, precise, and cost-effective manufacturing solutions. This versatile technique allows for the production of a wide range of medical products, each tailored to meet specific needs in patient care and treatment. From surgical instruments to complex diagnostic devices, injection molding plays a pivotal role in ensuring that healthcare professionals have access to reliable tools.
Common Medical Device Examples
Some of the most common medical devices produced through injection molding include syringes, IV bags, and surgical trays. These items are essential for various medical procedures and are designed to meet stringent safety standards while being produced at scale. Moreover, due to the efficiency of injection molding for medical devices, manufacturers can create these products with minimal waste and high precision.
In addition to syringes and IV bags, other notable examples include catheters, dental trays, and orthopedic implants. Each of these products benefits from the consistency that injection molding provides—ensuring that every item is identical in quality and functionality. This level of precision is crucial in healthcare settings where even minor discrepancies can lead to significant complications.
Custom Molded Solutions for Healthcare
The beauty of injection molding lies not only in mass production but also in its ability to create custom molded solutions tailored specifically for unique medical applications. Manufacturers can design molds that cater to specialized requirements—be it a specific shape or material composition—allowing healthcare providers to address niche needs effectively. This flexibility makes injection molding an invaluable tool when developing innovative solutions that enhance patient care.
For example, custom molded components can be designed for prosthetics or orthopedic supports that fit individual patients perfectly. Such personalized solutions not only improve comfort but also promote better healing outcomes by ensuring proper alignment and support during recovery periods. The ability to produce these tailored products quickly further emphasizes the advantages of using injection molding techniques.
What products can be made from injection molding?
The range of products that can be made from injection molding is vast and varied within the medical field—a testament to its versatility as a manufacturing method. Beyond standard items like syringes and surgical trays, this technology enables the production of complex multi-part assemblies used in advanced diagnostic devices or robotic surgical systems. Each product benefits from improved durability and performance thanks to high-quality materials used during manufacturing.
As we explore what are the applications of injection molding further, it's clear that this technique extends into areas such as dental equipment as well—think about specialized dental trays or orthodontic appliances crafted through precise molds designed specifically for patient comfort! The continued evolution within this space raises questions about what is the latest technology in injection molding? Innovations such as 3D printing integration with traditional methods are paving new paths toward even more sophisticated product development.
Injection Molding Technique in Dentistry
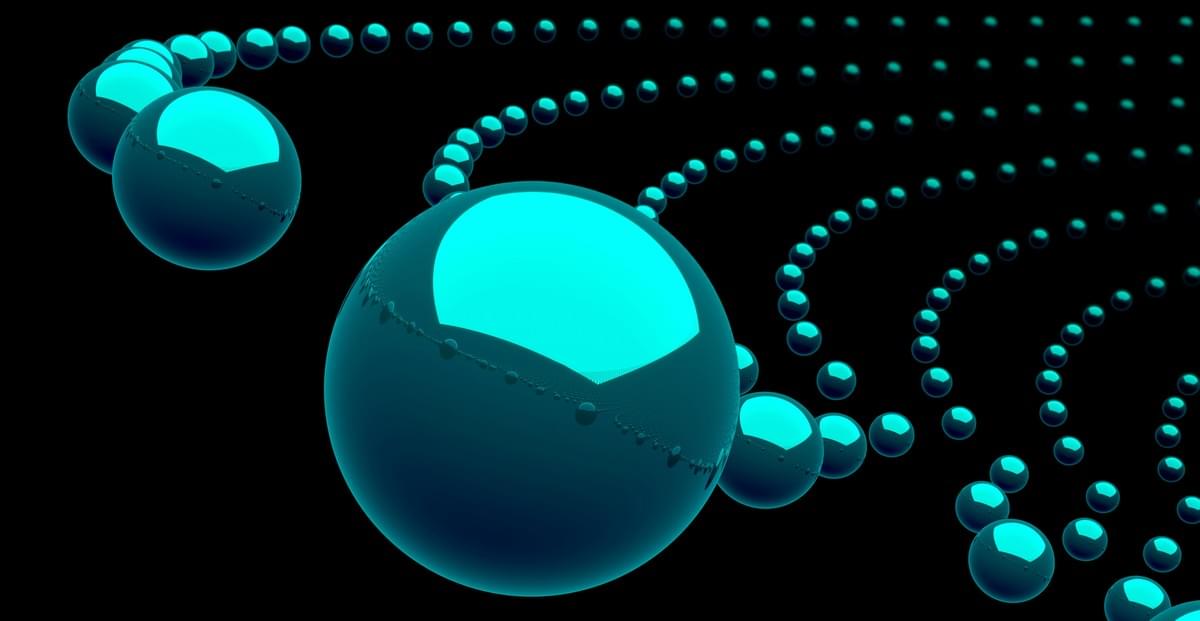
Injection molding has become a game-changer in the field of dentistry, allowing for the production of highly precise and customized dental devices. This technique not only enhances the functionality of dental products but also ensures that they meet stringent health standards. As the demand for innovative solutions grows, injection molding for medical devices is carving out a significant niche within the dental industry.
Specialized Dental Devices
Specialized dental devices such as crowns, bridges, and orthodontic aligners are increasingly being produced using injection molding techniques. These devices require high levels of accuracy and consistency to ensure they fit comfortably and effectively in patients' mouths. With advancements in technology, manufacturers can create intricate designs that were previously difficult to achieve, showcasing just one of the many applications of injection molding.
The versatility of injection molding allows for a variety of materials to be used, including biocompatible polymers that are safe for oral use. This opens up opportunities for creating products that not only perform well but also enhance patient comfort and satisfaction. In this way, specialized dental devices manufactured through injection molding are revolutionizing patient care by offering more reliable solutions.
Integrating Technology in Dental Manufacturing
Integrating technology into dental manufacturing processes is crucial for enhancing efficiency and precision; this is where modern injection molding shines. The latest technology in injection molding includes advanced robotics and automated systems that reduce human error while speeding up production times. Such innovations allow manufacturers to produce large volumes of high-quality dental products quickly.
Moreover, digital design tools enable dentists to customize treatments based on individual patient needs seamlessly. As a result, the collaboration between healthcare professionals and manufacturers becomes more effective—leading to better outcomes for patients who require specialized dental care. By embracing these advancements in injection molding techniques, the industry can continue pushing boundaries toward improved patient experiences.
What is Injection Molding Technique in Dentistry?
So what exactly is the injection molding technique in dentistry? Simply put, it’s a process where heated material is injected into a mold to create precise shapes needed for various dental applications. This method allows manufacturers to produce complex geometries with exceptional detail—perfect for crafting everything from intricate aligners to durable prosthetics.
In essence, this technique streamlines production while maintaining high standards necessary for medical-grade equipment; thus ensuring safety and efficacy within patient care settings. The ability to reproduce designs consistently makes it an ideal choice when considering what products can be made from injection molding within dentistry specifically—and beyond!
As we look ahead at future trends in medical device manufacturing, it's clear that innovations like these will continue shaping how we approach healthcare solutions across various fields.
Conclusion
As we wrap up our exploration of injection molding for medical devices, it's clear that this manufacturing technique is not just a passing trend; it's the backbone of modern healthcare innovation. The future of medical device manufacturing is bright, with advancements in technology paving the way for more efficient, reliable, and cost-effective production methods. From smarter machinery to new materials, the industry is poised for transformative changes that will enhance patient care and streamline processes.
Future Trends in Medical Device Manufacturing
Looking ahead, one of the most exciting future trends in medical device manufacturing is the integration of smart technologies into injection molding processes. Innovations such as IoT-enabled machinery and AI-driven analytics are set to revolutionize how we approach production efficiency and quality control. As we ponder what is the latest technology in injection molding?, it’s evident that these advancements will not only improve operational capabilities but also lead to more personalized and adaptable medical solutions.
Baoyuan’s Expertise in Injection Molding
At Baoyuan, expertise in injection molding goes beyond mere production; it encompasses a commitment to quality and innovation tailored specifically for healthcare applications. With years of experience under our belt, we understand what products can be made from injection molding that meet stringent regulatory standards while ensuring patient safety. Our dedication to continuous improvement positions us at the forefront of developments in this field, making us a trusted partner for those looking to leverage cutting-edge techniques.
The Impact of Injection Molding on Patient Care
The impact of injection molding on patient care cannot be overstated; it facilitates the creation of life-saving devices that are both reliable and affordable. By exploring what are the applications of injection molding?, we find a wide array ranging from surgical instruments to prosthetics—each designed with precision for optimal performance. Moreover, understanding what is injection molding technique in dentistry reveals how specialized dental devices can enhance treatment outcomes while ensuring comfort for patients.