Introduction
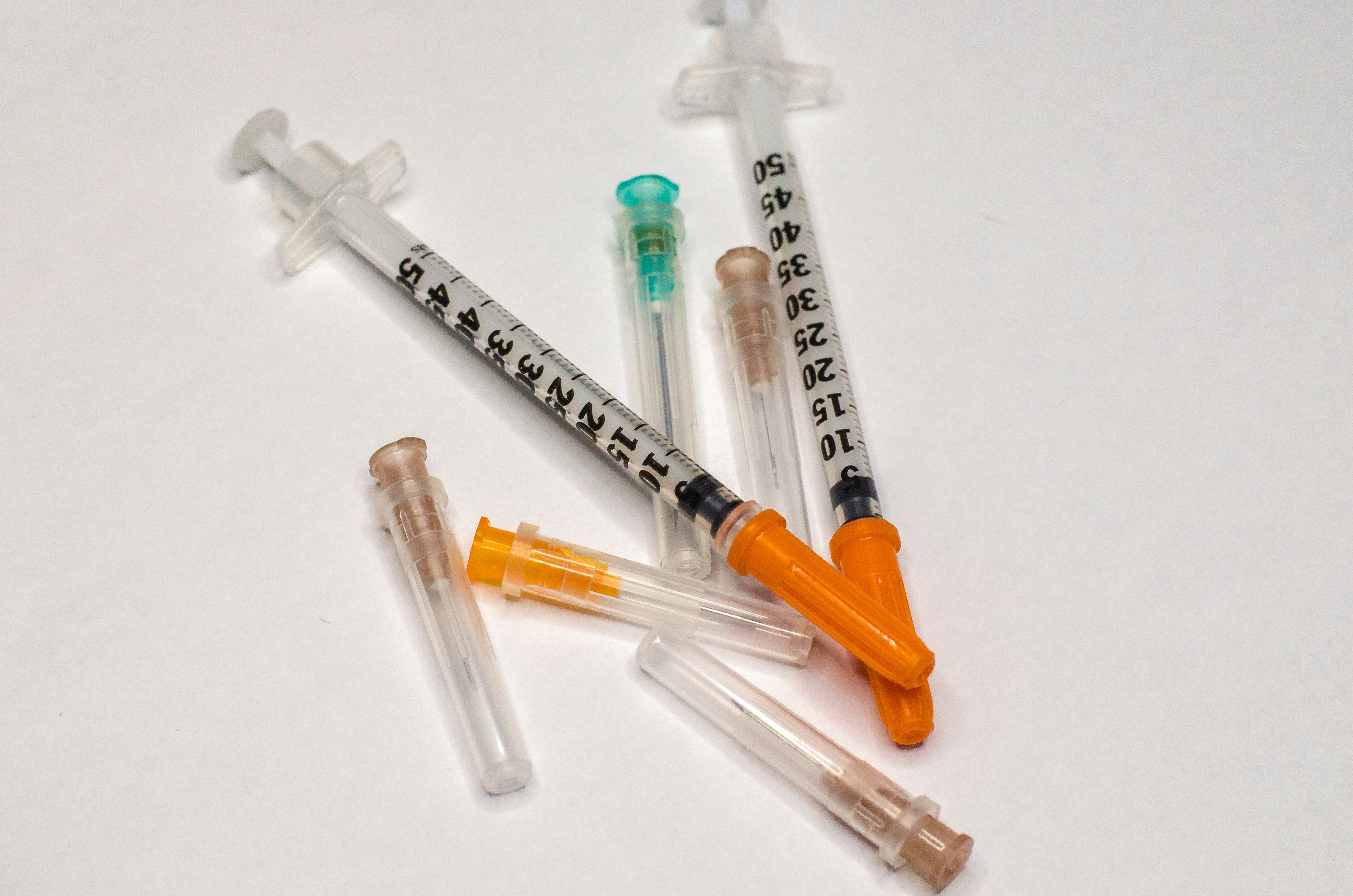
In the ever-evolving landscape of healthcare, plastic injection molding medical parts have emerged as a cornerstone technology, revolutionizing the way medical devices are produced. This process involves injecting molten plastic into molds to create precise and consistent components that meet stringent industry standards. As we delve deeper into what is medical injection molding, it becomes clear that this technique not only enhances product quality but also accelerates production timelines.
Overview of Medical Injection Molding
Medical injection molding is a specialized manufacturing process tailored for producing high-quality plastic components used in various healthcare applications. The process begins with the melting of thermoplastic materials, which are then injected into molds under high pressure to form intricate shapes. From syringes to surgical instruments, this method ensures that each piece meets rigorous specifications while maintaining cost-effectiveness and efficiency.
Importance of Plastic Components in Healthcare
Plastic components play an indispensable role in modern healthcare, offering versatility and reliability that metal or glass alternatives often cannot match. These materials are lightweight, durable, and can be easily sterilized—qualities essential for medical applications where safety is paramount. Moreover, the ability to create complex geometries through medical molding allows for innovative designs that enhance patient care and improve outcomes.
Leading Players in Medical Molding
The realm of medical injection molding is populated by several key players who drive innovation and set industry standards. Companies like Baoyuan lead the charge with their expertise in producing high-quality plastic injection molding medical parts tailored for diverse applications. Alongside notable competitors, these industry leaders continue to push boundaries through technological advancements and sustainable practices, shaping the future of healthcare manufacturing.
What is Medical Injection Molding?
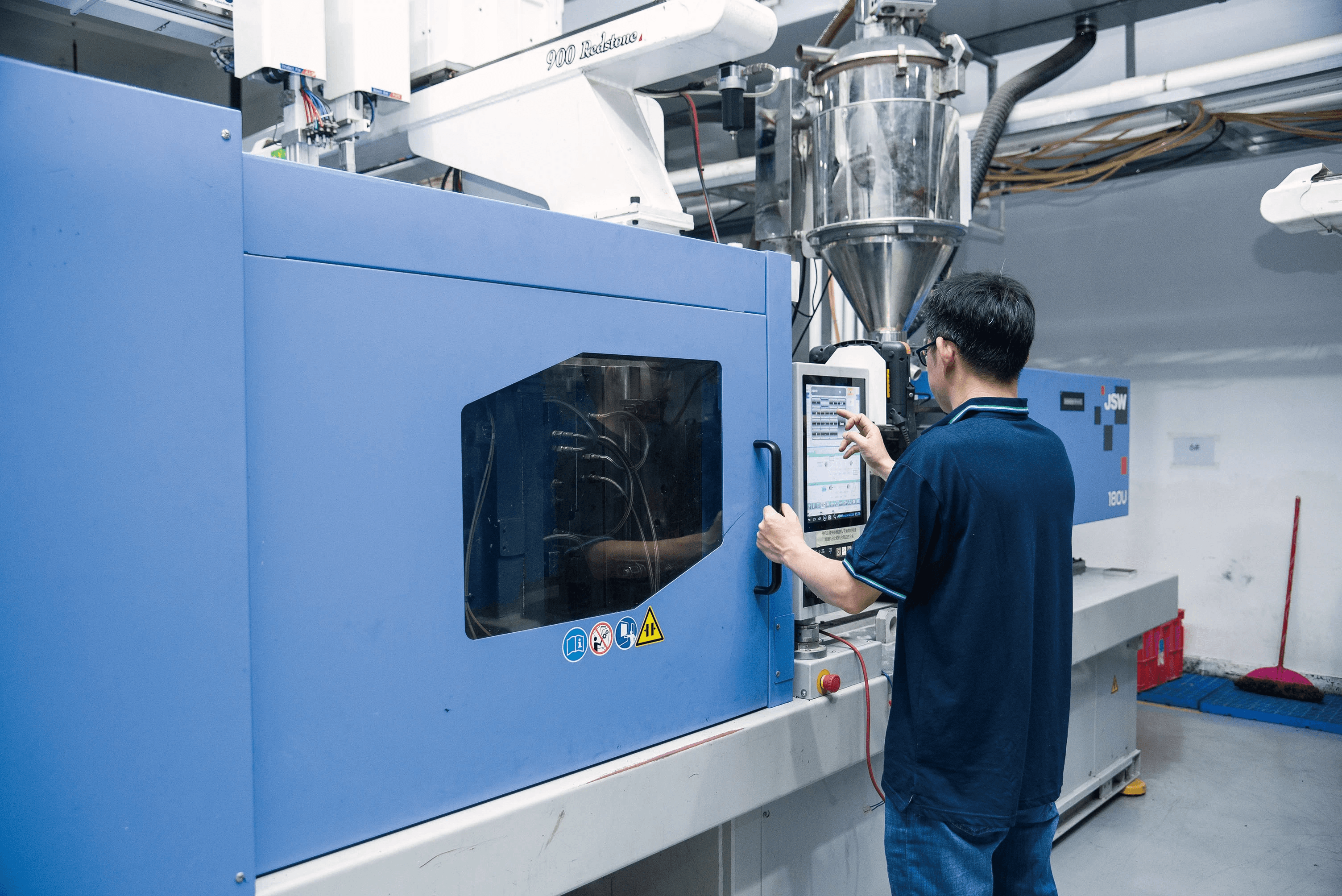
Medical injection molding is a specialized manufacturing process that creates plastic components for the healthcare industry. This technique involves injecting molten plastic into a mold to produce precise and consistent parts used in various medical applications. By utilizing advanced technology, medical injection molding companies can ensure high-quality production that meets strict regulatory standards.
Definition and Process
At its core, medical injection molding refers to the process of forming plastic materials into specific shapes suitable for medical devices and equipment. The process begins with heating thermoplastic materials until they become pliable, followed by injecting this molten material into a meticulously crafted mold under high pressure. Once cooled and solidified, the molded parts are ejected from the mold, ready for further processing or assembly.
This method is particularly favored in creating plastic injection molding medical parts due to its ability to produce complex geometries with exceptional precision and repeatability. The entire operation can be automated, allowing manufacturers to scale production efficiently while maintaining stringent quality control measures essential in healthcare settings.
Applications in the Healthcare Sector
Medical injection molding finds diverse applications across the healthcare sector, producing everything from syringes and surgical instruments to implantable devices and diagnostic tools. These plastic components are crucial for ensuring safety, reliability, and functionality in medical procedures. As technology advances, the demand for innovative solutions continues to grow; thus, companies specializing in medical molding are constantly exploring new applications.
The versatility of this process allows manufacturers to create customized solutions tailored specifically for various healthcare needs—be it single-use items or complex multi-component assemblies. With an increasing focus on patient safety and efficiency in healthcare delivery, the role of plastic injection molding medical parts has never been more significant.
Advantages of Medical Injection Molding
The advantages of using medical injection molding are numerous and compelling for both manufacturers and end-users alike. First off, precision and consistency stand out as key benefits; each part produced through this method adheres closely to exact specifications required by regulatory bodies like the FDA. This level of accuracy ensures that every component functions as intended when used in critical applications.
Cost-effectiveness is another major advantage; once molds are created, mass production becomes economically viable due to reduced labor costs per unit produced compared to traditional manufacturing methods. Additionally, speed of production plays a vital role—medical injection molding allows rapid turnaround times from design conception through final product delivery without sacrificing quality.
In summary, understanding what is medical injection molding reveals not just its definition but also its vast potential within healthcare applications through precision engineering techniques that cater specifically to industry needs while addressing common challenges faced by manufacturers today.
Key Benefits of Plastic Injection Molding Medical Parts
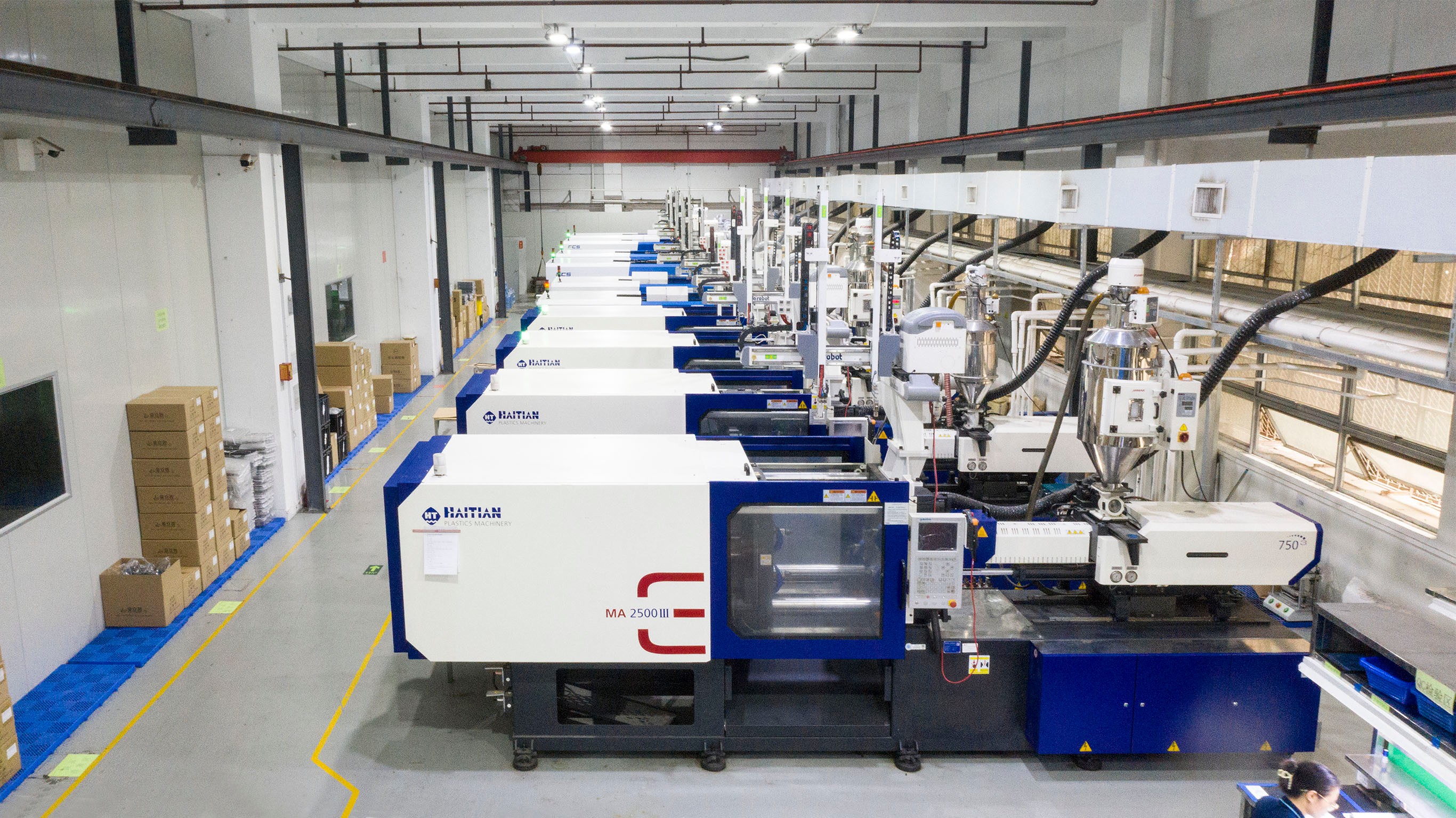
Plastic injection molding medical parts have revolutionized the healthcare sector by offering a multitude of benefits that enhance both manufacturing processes and patient outcomes. The precision, cost-effectiveness, and speed of production associated with medical injection molding make it an essential component in the creation of high-quality medical devices and components. As healthcare continues to evolve, the advantages provided by this technology remain critical for meeting the demands of modern medicine.
Precision and Consistency
One of the standout features of plastic injection molding medical parts is their remarkable precision and consistency. This process allows manufacturers to create components that meet stringent specifications, ensuring that each part performs reliably in critical applications like surgical instruments or drug delivery systems. Additionally, the repeatability inherent in medical injection molding means that every batch produced maintains uniform quality, which is vital for patient safety.
Precision also extends to complex geometries that are often required in advanced medical devices. Whether it’s intricate designs for implants or finely detailed housings for electronic devices, plastic injection molding can achieve these specifications without compromising on quality. Ultimately, this level of accuracy not only enhances product performance but also instills confidence among healthcare professionals who rely on these components daily.
Cost-Effectiveness
When considering what is medical injection molding? It's essential to recognize its cost-effectiveness as a significant advantage in producing plastic components for healthcare applications. The efficiency of the mold-making process reduces waste material and maximizes resource use, leading to lower production costs over time. Furthermore, once molds are created, they can be used repeatedly to produce large volumes at minimal additional expense.
This cost-effectiveness extends beyond just manufacturing; it also encompasses long-term savings associated with durability and reliability in end-use applications. For instance, high-quality plastic injection molded parts tend to have longer lifespans compared to alternatives made from less durable materials. Consequently, hospitals and clinics benefit from reduced maintenance costs and fewer replacements over time.
Speed of Production
In today's fast-paced healthcare environment, speed is crucial—and that's where plastic injection molding truly shines! The ability to rapidly produce large quantities of medical parts makes this method ideal for meeting urgent demands within hospitals or during product launches by medical injection molding companies. With cycle times often measured in seconds rather than minutes or hours, manufacturers can respond swiftly to market needs without sacrificing quality.
Moreover, advancements in technology continue to streamline production processes even further—think automation and improved mold designs! These innovations not only enhance efficiency but also allow companies specializing in medical molding to scale operations quickly when necessary while maintaining high standards across all products produced. In essence, faster production translates directly into better patient care through timely access to crucial medical devices.
Common Problems with Injection Molding of Plastic Parts
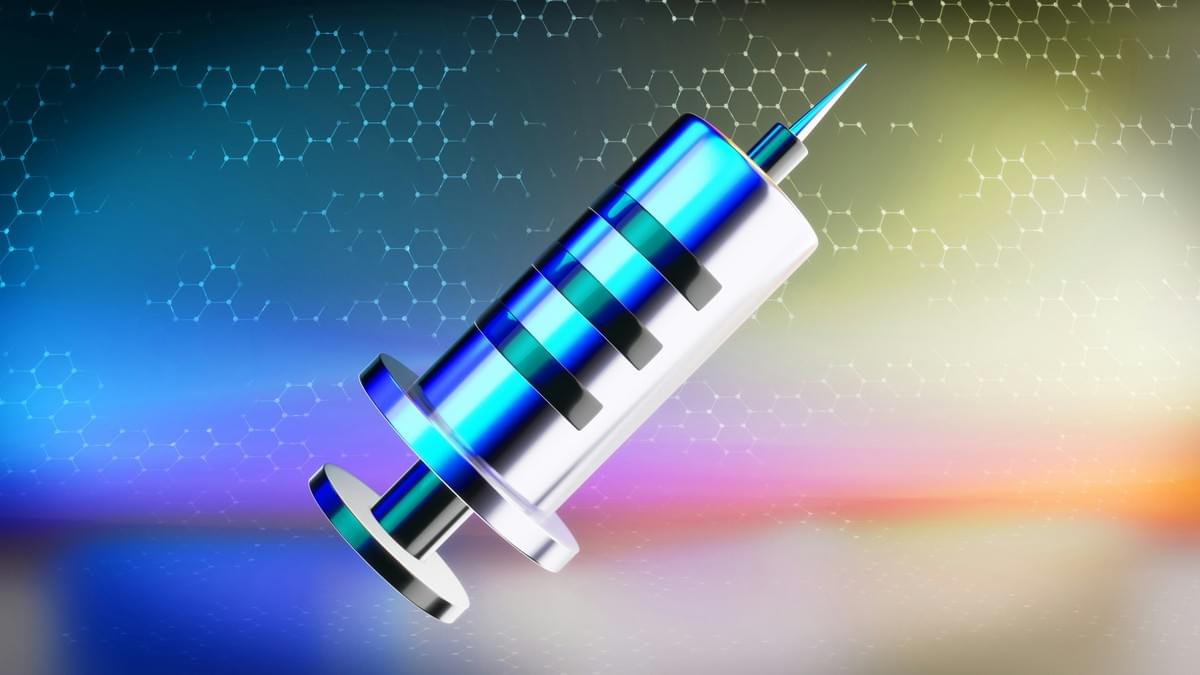
While plastic injection molding medical parts is a highly efficient manufacturing process, it is not without its challenges. Understanding these common problems can help manufacturers optimize their practices and ensure high-quality outcomes. Let's dive into some of the most pressing issues that can arise in this field.
Issues with Material Selection
Selecting the right materials for medical injection molding is crucial, yet it often poses a significant challenge. Different medical applications require specific properties such as biocompatibility, durability, and resistance to sterilization processes. If the wrong material is chosen, it can lead to product failure or even pose risks to patient safety, highlighting the importance of thorough research and testing in material selection.
Challenges in Design Complexity
Design complexity is another hurdle that many face when producing plastic injection molding medical parts. As healthcare technology advances, products are becoming more intricate, which can complicate the molding process. Complex designs may require specialized molds and advanced manufacturing techniques, increasing production times and costs while also raising the potential for defects.
Solutions for Quality Control
Quality control is essential in mitigating issues associated with medical injection molding companies and ensuring compliance with stringent regulations. Implementing rigorous testing protocols at various stages of production can help identify defects early on, reducing waste and enhancing overall efficiency. Additionally, investing in advanced monitoring technologies during the molding process ensures that each part meets required specifications consistently.
Major Medical Injection Molding Companies
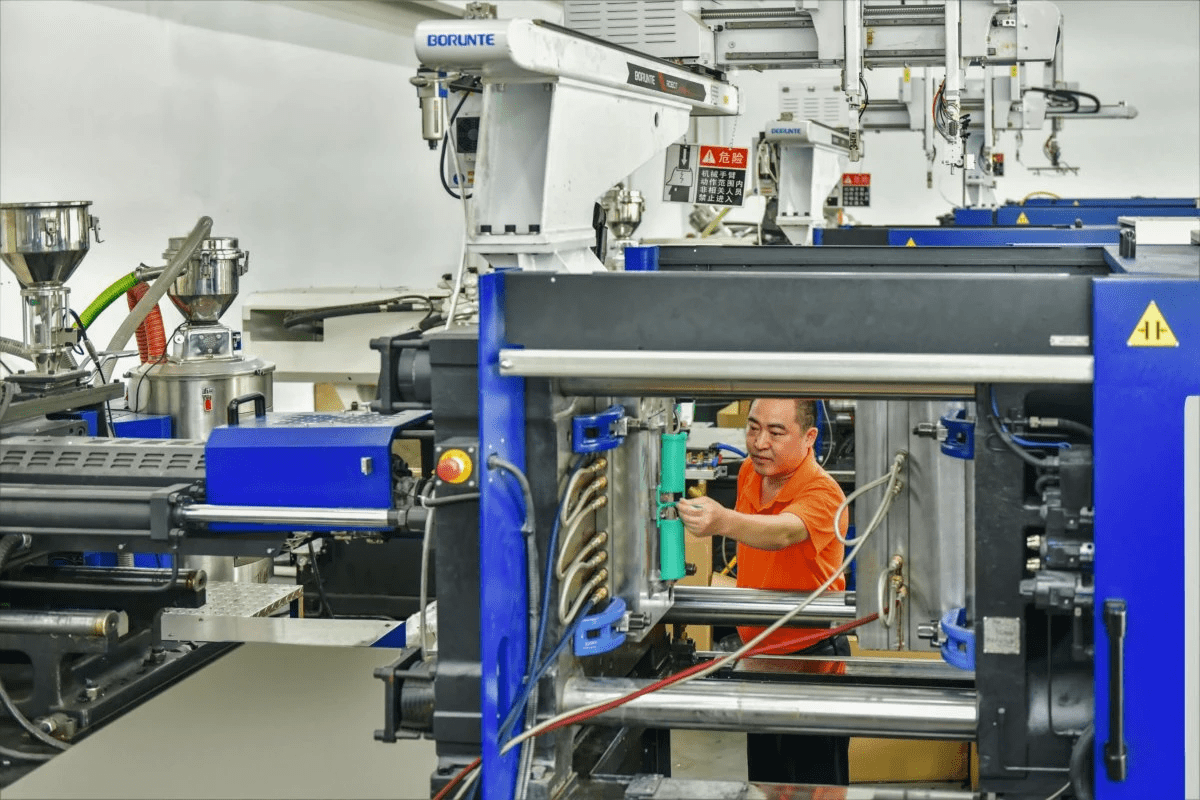
In the realm of medical injection molding, several companies have established themselves as leaders, driving innovation and setting industry standards. These medical molding companies not only specialize in producing plastic injection molding medical parts but also focus on improving processes to address common challenges in the industry. Understanding the expertise and innovations offered by these players is essential for anyone looking to grasp what is medical injection molding and its impact on healthcare.
Baoyuan's Expertise
Baoyuan stands out in the field of medical injection molding with its commitment to high-quality production and advanced technology. Specializing in plastic injection molding medical parts, Baoyuan utilizes state-of-the-art machinery and rigorous quality control measures to ensure that each component meets stringent healthcare regulations. Their experience spans a variety of applications, making them a go-to choice for organizations seeking reliable solutions in medical molding.
In addition to their technical prowess, Baoyuan emphasizes collaboration with clients to tailor solutions that meet specific needs. This client-centric approach not only enhances product quality but also fosters long-term partnerships within the healthcare sector. With a focus on continual improvement, Baoyuan remains at the forefront of addressing what are five common problems with injection molding of plastic parts through innovative processes.
Noteworthy Competitors
While Baoyuan leads the charge, numerous noteworthy competitors also contribute significantly to the landscape of medical injection molding companies. Firms like Medtronic and Philips Healthcare have established robust capabilities in producing plastic components essential for various medical devices. These companies leverage their extensive research and development resources to push boundaries within the field of medical injection molding.
Each competitor brings unique strengths: some excel in rapid prototyping while others focus on large-scale production efficiency or specialized materials suited for specific applications. The competition fosters an environment where innovation thrives, ultimately benefiting healthcare providers who rely on high-quality plastic injection molding medical parts for patient care. By understanding these players' contributions, one can better appreciate how they collectively advance what is medical injection molding.
Innovations from Industry Leaders
Innovation is a hallmark of success among leading players in the realm of medical injection molding, as they continuously seek ways to enhance efficiency and quality in production processes. For instance, advancements such as 3D printing integration into traditional methods allow for greater design flexibility while maintaining precision—addressing some common problems with injection molding of plastic parts head-on. These innovations not only streamline production but also reduce waste and costs associated with manufacturing.
Furthermore, many industry leaders are investing heavily in sustainable practices that align with global environmental goals while still delivering high-performance products through effective plastic injection molding techniques. This commitment ensures that future generations will benefit from both cutting-edge technology and environmentally responsible practices within healthcare manufacturing sectors.
As we look toward tomorrow’s challenges—such as increasing demand for personalized medicine—the role of these innovations becomes even more critical in shaping how we approach patient care through effective use of plastic components derived from advanced medical moldings.
Future Trends in Medical Molding
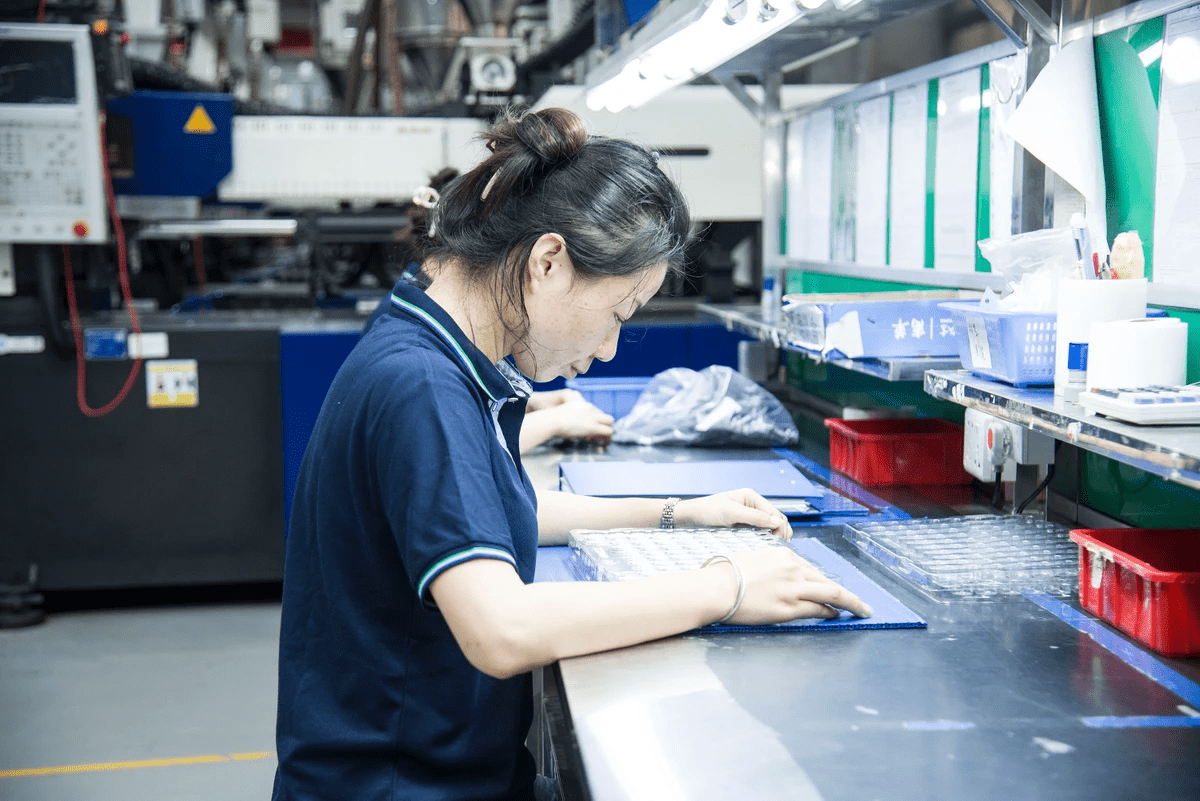
The landscape of medical molding is rapidly evolving, driven by technological advancements and a growing emphasis on sustainability. As we look to the future, the integration of innovative practices and materials will reshape how plastic injection molding medical parts are produced. This evolution not only enhances efficiency but also improves patient outcomes across the healthcare sector.
Advances in Technology
In recent years, the evolution of technology has significantly transformed what is medical injection molding? The incorporation of automation and robotics into the production process has increased precision while reducing human error. Additionally, advanced software solutions are now being used for design optimization, ensuring that even the most complex plastic injection molding medical parts are manufactured with accuracy and consistency.
Moreover, 3D printing technology is emerging as a complementary process to traditional injection molding techniques. This hybrid approach allows for rapid prototyping and customization of medical components, catering to specific patient needs or unique device requirements. As these technologies continue to develop, they promise to enhance not only productivity but also adaptability within medical injection molding companies.
Sustainability in Medical Injection Molding
Sustainability is becoming a cornerstone of modern manufacturing practices, including in the realm of medical injection molding. With an increasing focus on environmental impact, manufacturers are exploring biodegradable materials and recycling processes that can be integrated into their operations. By opting for sustainable materials in plastic injection molding medical parts production, companies can minimize waste while maintaining high-quality standards.
Furthermore, advancements in energy-efficient machinery are helping reduce carbon footprints associated with manufacturing processes. These eco-friendly innovations align with global efforts toward sustainability while ensuring that quality remains uncompromised in producing essential healthcare components. As more organizations prioritize green practices within their operations, we can expect a significant shift toward sustainable solutions in medical molding.
Impact on Patient Care
The ongoing advancements in medical injection molding directly influence patient care by enhancing product quality and availability. With improved precision from technological innovations, healthcare providers can rely on plastic injection molding medical parts that meet stringent safety standards without compromising performance or reliability. This reliability translates into better treatment options for patients and ultimately leads to improved health outcomes.
Additionally, quicker production cycles facilitated by modern technologies allow for faster delivery of critical components needed during surgeries or treatments. When every second counts in healthcare settings, these efficiencies can make a substantial difference in patient experiences and recovery times. Thus, as we embrace these future trends within the industry—ranging from advances in technology to sustainability—we're not just revolutionizing manufacturing; we're fundamentally enhancing patient care itself.
Conclusion
In summary, medical injection molding plays a pivotal role in the healthcare industry by providing high-quality, precise plastic components essential for medical devices and equipment. The process of medical injection molding ensures that plastic injection molding medical parts are manufactured to meet stringent safety and quality standards. As the demand for innovative healthcare solutions continues to rise, the importance of effective medical molding techniques cannot be overstated.
Recap of Medical Injection Molding's Role
Medical injection molding is not just about creating parts; it’s about ensuring patient safety and improving outcomes through reliable products. The ability to produce complex shapes with high precision makes this technique indispensable in developing everything from syringes to surgical instruments. By leveraging advanced technology, medical injection molding companies can deliver consistent quality while reducing waste and production costs.
Addressing Challenges in the Industry
Despite its advantages, the industry faces several challenges that need addressing, such as material selection and design complexity. What are five common problems with injection molding of plastic parts? These include issues like warping, poor surface finish, incomplete filling, air traps, and dimensional inaccuracies that can compromise product integrity. Tackling these challenges requires continuous innovation and rigorous quality control measures within the sphere of medical injection molding.
The Future of Plastic Injection Molding in Healthcare
Looking ahead, advancements in technology will further enhance the capabilities of plastic injection molding medical parts. Innovations such as 3D printing integration and smart materials promise to revolutionize how we think about design and functionality in healthcare applications. Moreover, a growing emphasis on sustainability will shape future practices within medical molding processes, ensuring that they not only meet current needs but also contribute positively to environmental goals.