Introduction
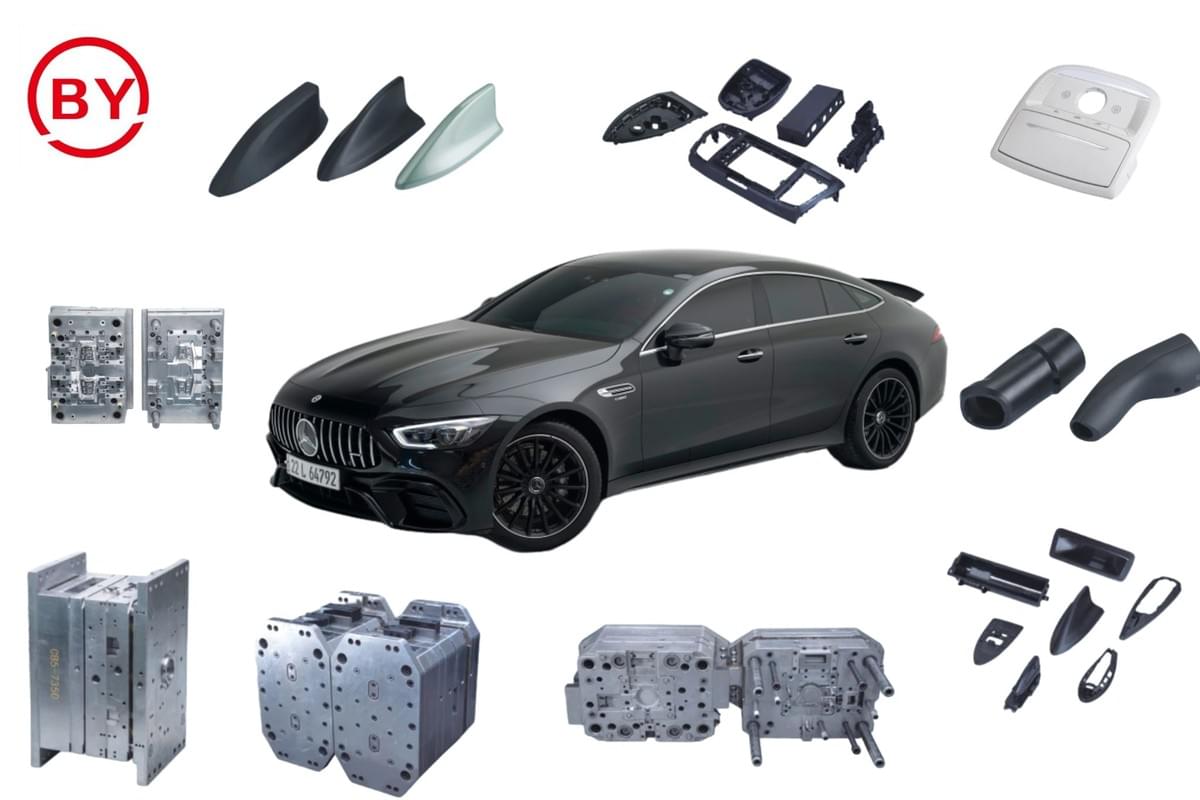
In the bustling world of appliance design, creativity meets engineering to create products that not only serve a purpose but also enhance our daily lives. The art of appliance design requires a delicate balance between aesthetics and functionality, making it an exciting yet challenging field. One of the key players in this game is lost core injection molding, an innovative technique that has revolutionized how we think about manufacturing.
The Art of Appliance Design
Designing appliances is akin to crafting a masterpiece; every detail counts, from the sleek lines of a refrigerator to the user-friendly interface of a washing machine. Designers must consider not just how an appliance looks but also how it performs and fits into our homes. This is where understanding what core in injection molding means becomes essential, as it directly impacts the quality and efficiency of the final product.
Why Injection Molding Matters
Injection molding is more than just a manufacturing process; it's an art form that allows designers to bring their visions to life with precision and speed. By utilizing techniques like lost core injection molding, manufacturers can create complex shapes and intricate designs that were once thought impossible. However, challenges arise along the way—questions such as How do you fix voids in injection molding? highlight the importance of mastering these techniques for optimal results.
Exploring Innovative Techniques
As we delve deeper into the world of injection molding techniques, we uncover methods like coring that enhance both efficiency and product quality. What is coring in injection molding? It's a process that allows for hollow sections within molded parts, reducing material usage while maintaining structural integrity. By exploring these innovative approaches, designers can push boundaries and create appliances that are not only functional but also environmentally friendly.
Understanding Injection Molding Techniques
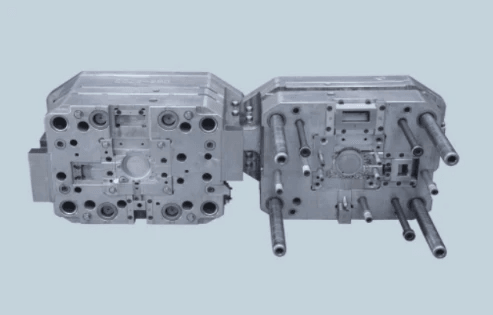
Injection molding is a fascinating and intricate process that plays a crucial role in the manufacturing of various appliances. Among the many techniques available, lost core injection molding stands out for its unique approach to creating complex geometries and hollow structures. In this section, we will delve into what lost core molding is, the significance of cores in injection molding, and how to tackle those pesky voids that can compromise product quality.
What is a lost core molding?
Lost core molding is an innovative technique used in injection molding that allows manufacturers to create intricate designs with internal cavities. Essentially, it involves using a temporary core that melts away or disintegrates after the part has been formed, leaving behind a hollow section. This method not only enhances design flexibility but also reduces material waste—making it an appealing choice for modern appliance design.
The beauty of lost core injection molding lies in its ability to produce lightweight parts without sacrificing strength or durability. By eliminating unnecessary material from the interior of components, manufacturers can achieve significant weight savings while maintaining structural integrity. It’s like having your cake and eating it too—only this cake won’t crumble under pressure!
The importance of core in injection molding
When discussing injection molding techniques, one cannot overlook the vital role played by cores. So, what is core in injection molding? Simply put, a core acts as a mold insert that defines the internal shape of the final product during the injection process. Without cores, achieving complex internal geometries would be nearly impossible.
How do you fix voids in injection molding?
Voids can be one of the most frustrating issues faced by manufacturers using traditional methods; however, understanding how to fix voids in injection molding can save both time and resources! Voids typically occur due to inadequate filling or improper cooling rates during production—essentially leaving unwanted air pockets within your finished product.
To tackle this problem effectively, manufacturers often turn to strategies like adjusting processing parameters (temperature and pressure), ensuring proper venting during mold filling, or incorporating advanced simulation tools prior to production runs. Additionally, implementing rigorous quality assurance practices can help catch potential issues early on—preventing costly rework down the line! With these troubleshooting tips up your sleeve, you’ll be well-equipped to combat any void-related challenges that may arise.
The Lost Core Injection Molding Advantage
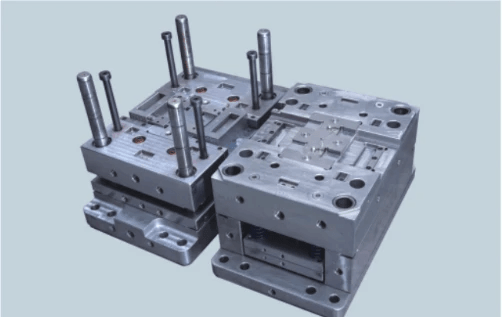
Lost core injection molding is revolutionizing the appliance design landscape, offering unique benefits that traditional methods struggle to match. This innovative technique allows for complex geometries and lightweight structures, making it a game-changer in manufacturing. By understanding the advantages of lost core injection molding, designers can optimize their products for both functionality and aesthetic appeal.
Benefits of lost core injection molding
One of the primary benefits of lost core injection molding is its ability to create intricate internal features without compromising the part's integrity. This technique eliminates the need for additional assembly processes, reducing labor costs and potential errors during production. Furthermore, lost core injection molding enhances material efficiency by minimizing waste, which is a crucial consideration in today's eco-conscious manufacturing environment.
Another significant advantage is the reduction of voids in injected parts. Voids can lead to structural weaknesses and affect product performance; however, with lost core techniques, these issues are often mitigated from the get-go. When considering What is a lost core molding? it becomes clear that this method not only streamlines production but also elevates product quality.
Designing for efficiency and quality
Designing with lost core injection molding requires a keen understanding of both form and function. By integrating specific design elements tailored for this technique, manufacturers can achieve remarkable efficiency while maintaining high-quality standards. The focus should be on optimizing wall thicknesses and ensuring proper flow paths within molds to prevent common issues associated with traditional techniques.
Moreover, understanding What is coring in injection molding? plays an essential role in maximizing these advantages. Effective coring facilitates better cooling rates during production cycles, significantly speeding up turnaround times without sacrificing quality or precision. Consequently, designers who embrace these principles will find themselves at the forefront of innovation in appliance manufacturing.
Case studies demonstrating successful applications
Numerous case studies highlight successful applications of lost core injection molding across various industries—particularly within appliance design where complexity reigns supreme. For instance, one leading manufacturer utilized this technique to produce lightweight yet durable components for kitchen appliances that required intricate internal structures for optimal performance. The result was not only a reduction in material costs but also enhanced functionality that delighted consumers.
In another example, an automotive parts supplier adopted lost core methods to create complex engine components with reduced weight while maintaining strength—a critical factor when considering fuel efficiency standards today. These success stories underscore how embracing advanced injection molding techniques can lead to substantial improvements across multiple sectors.
As we delve deeper into mastering coring in injection molding next, it's essential to recognize how these innovations pave the way for future developments in appliance design—ultimately shaping what we can expect from modern manufacturing processes.
Mastering Coring in Injection Molding
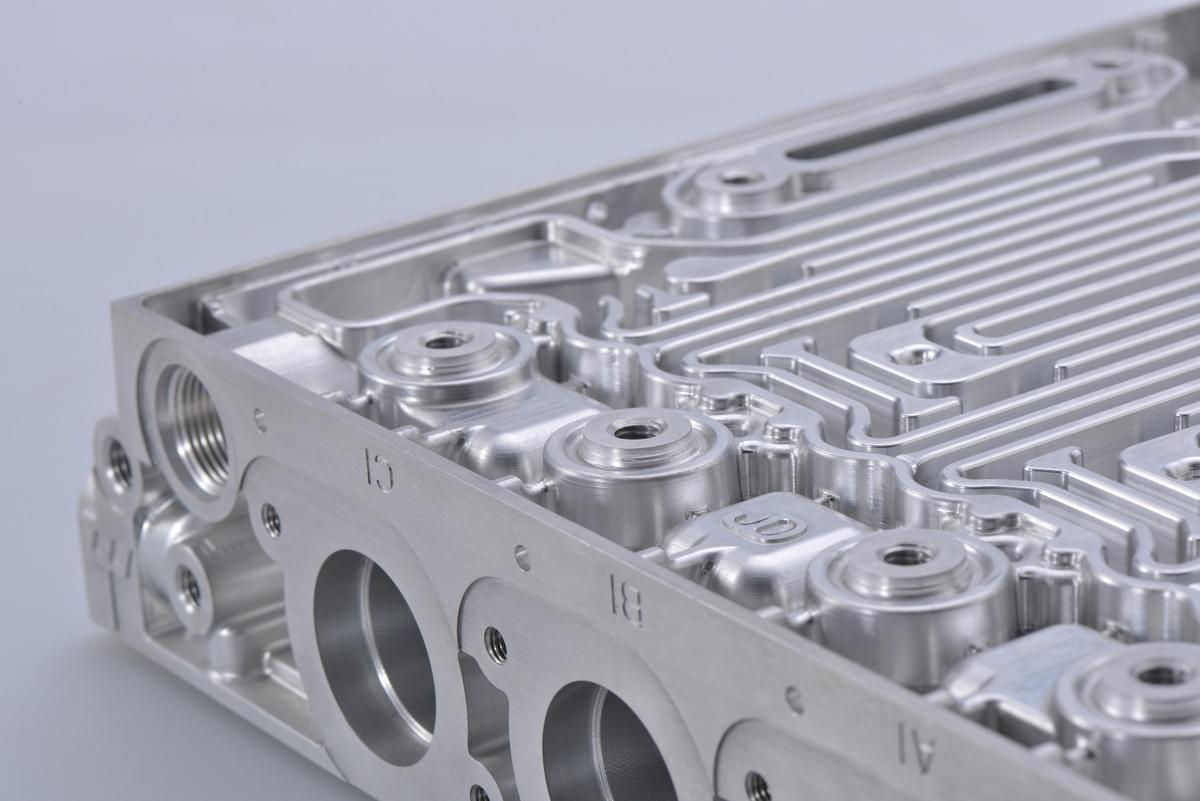
Coring is a crucial aspect of injection molding that can significantly influence the quality and efficiency of manufactured products. By understanding what coring is in injection molding, manufacturers can optimize their designs for better performance and reduced waste. In this section, we’ll explore the nuances of coring techniques, real-world applications, and how lost core injection molding is revolutionizing the industry.
What is coring in injection molding?
Coring in injection molding refers to the process of creating hollow sections within a molded part to reduce weight and material use while maintaining structural integrity. This technique involves using cores—essentially inserts or tools that shape the interior voids during the molding process. Understanding what core is in injection molding is vital for engineers and designers who aim to enhance product functionality without compromising on quality.
The importance of effective coring cannot be overstated; it allows for innovative designs that would otherwise be impossible with traditional solid moldings. Additionally, proper coring helps prevent defects like voids or weak spots, which can arise from inadequate material distribution during the injection phase. Ultimately, mastering coring techniques leads to more efficient production cycles and improved product performance.
Techniques for effective coring
When it comes to effective coring in lost core injection molding, several techniques stand out as particularly beneficial. First, designing cores with optimal geometries ensures even material flow throughout the cavity while minimizing stress concentration points. Using advanced materials for cores also plays a role; lightweight yet durable materials can withstand high temperatures without deforming during the process.
Another technique involves leveraging simulation software to predict how molten plastic will behave around the core during filling and cooling phases. This predictive modeling allows designers to adjust parameters proactively—reducing instances of voids in injection molding before they even occur. Finally, regular maintenance on molds ensures that any wear or damage does not adversely affect core functionality over time.
Real-world examples of coring success
Numerous industries have successfully incorporated effective coring strategies into their manufacturing processes through lost core injection molding techniques. For instance, automotive manufacturers have utilized these methods to create lightweight components that contribute to fuel efficiency without sacrificing safety standards. By integrating innovative core designs into their molds, they’ve managed to reduce overall vehicle weight significantly while maintaining structural integrity.
In consumer electronics, companies have also embraced advanced coring techniques to produce sleek devices with intricate internal structures—think smartphones with complex interiors but minimal exterior bulkiness! These successful applications showcase how effective coring not only enhances product design but also drives market competitiveness by allowing quicker production times at lower costs.
By examining these real-world examples of successful applications of what is a lost core molding approach within various industries, it's clear that mastering coring effectively leads to significant advantages in both product design and manufacturing efficiency.
Avoiding Common Pitfalls in Appliance Design
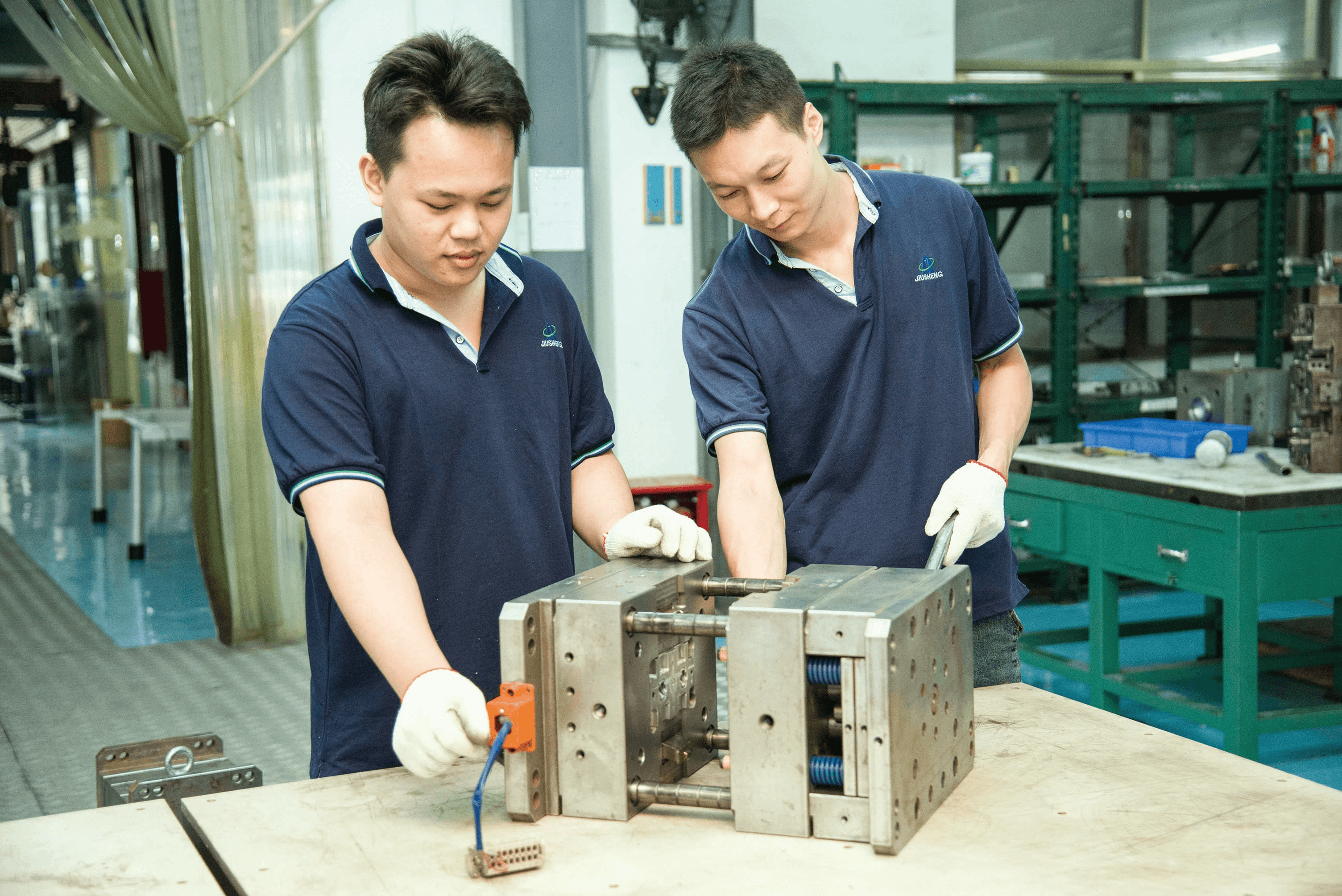
Designing appliances is a delicate dance, and avoiding common pitfalls can make all the difference between a product that shines and one that flops. The journey begins with understanding the intricacies of lost core injection molding, where identifying and resolving design flaws is crucial. By focusing on the core elements of injection molding techniques, designers can create products that not only meet consumer needs but also stand the test of time.
Identifying and resolving design flaws
To truly understand what is core in injection molding, one must first recognize that design flaws can arise from various sources, including material choice and geometric complexity. A thorough analysis during the design phase can help pinpoint areas where issues may arise, such as unexpected voids or weaknesses in structure. Once identified, these flaws can be resolved through iterative testing and adjustments to ensure a robust final product.
When considering lost core injection molding specifically, it’s vital to assess how the core interacts with other components throughout production. This technique allows for intricate designs while minimizing material waste; however, if not executed correctly, it could lead to significant problems down the line. Collaborating closely with engineers who understand what is a lost core molding will help mitigate risks associated with flawed designs.
Tips for preventing voids in products
Voids are like unwanted guests at a party—nobody wants them there! To prevent voids in products produced through injection molding techniques, it’s essential to maintain optimal conditions throughout the process. This includes ensuring proper temperature control during melting and injection phases as well as monitoring pressure levels closely.
Another effective strategy involves designing parts with uniform wall thicknesses to promote consistent flow of molten material within molds—this reduces chances of air entrapment leading to voids. Additionally, employing advanced techniques such as gas-assisted injection or using additives designed for better flow characteristics can significantly reduce incidences of void formation in your final products.
Lastly, regular maintenance of molds plays an integral role in preventing voids; keeping them clean and free from debris ensures smooth operation during production runs so you don’t end up asking yourself how do you fix voids in injection molding after they occur!
Quality assurance practices in injection molding
Quality assurance practices are paramount when it comes to successful appliance design through lost core injection molding processes. Implementing rigorous testing protocols at various stages—from initial prototypes all the way through mass production—helps catch potential defects early on before they become costly issues later down the line. Techniques such as X-ray inspection or ultrasonic testing provide insights into internal structures while confirming integrity across different components.
Moreover, establishing clear communication channels between designers and manufacturers encourages collaboration focused on quality improvements based on feedback gathered during production runs. Understanding what is coring in injection molding also helps teams identify critical areas needing attention throughout this collaborative process.
Finally, embracing continuous improvement methodologies allows teams to adapt their quality assurance practices over time based on lessons learned from previous projects—ensuring each new appliance design benefits from past experiences while remaining aligned with evolving industry standards.
Collaborating with Experts: The Baoyuan Team
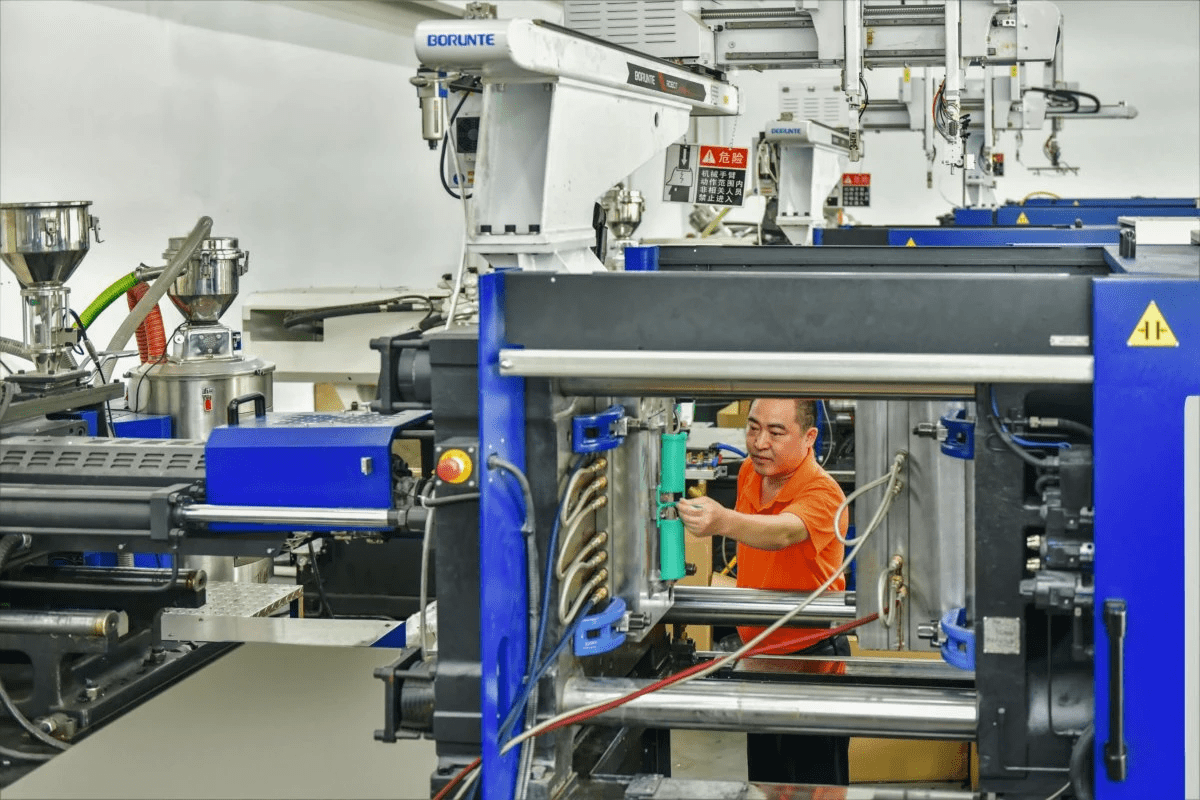
When it comes to mastering lost core injection molding, the expertise of seasoned professionals is invaluable. The Baoyuan team comprises specialists who not only understand the intricacies of injection molding techniques but also bring years of hands-on experience to the table. Their collaborative approach ensures that every design is optimized for efficiency and quality, ultimately leading to superior appliance designs.
The role of experienced personnel in design
Experienced personnel play a crucial role in the success of lost core injection molding projects. They possess an in-depth understanding of what is core in injection molding and how it influences the overall production process. By leveraging their insights, teams can identify potential pitfalls early on, such as voids that may arise during production, enabling timely adjustments before they become costly issues.
Moreover, these experts are adept at recognizing design flaws that could compromise product integrity. Their ability to troubleshoot and refine designs ensures that every component meets stringent quality standards while maintaining manufacturability. In essence, having experienced personnel on board transforms challenges into opportunities for innovation and improvement.
Leveraging technology in mold design
In today's fast-paced manufacturing landscape, technology plays a pivotal role in enhancing lost core injection molding processes. Advanced software tools allow designers to simulate various scenarios and outcomes before committing to physical prototypes. This means teams can experiment with different configurations and quickly determine how best to fix voids in injection molding without wasting valuable resources or time.
Additionally, cutting-edge technologies like 3D printing are revolutionizing mold design by enabling rapid prototyping and iteration cycles. This agility not only speeds up development but also allows for more intricate designs that were once deemed impractical or too costly to produce using traditional methods. By embracing these technological advancements, Baoyuan’s team can push the boundaries of what’s possible in appliance design.
Success stories from the Baoyuan team
The Baoyuan team has a rich history of successful projects showcasing their prowess in lost core injection molding techniques. One notable example involved redesigning a complex appliance component where traditional methods had failed due to excessive voids during production runs. By implementing innovative coring strategies—what is coring in injection molding—the team was able to enhance structural integrity while significantly reducing material waste.
Another success story highlighted their collaboration with a major appliance manufacturer facing challenges related to efficiency and cost-effectiveness in their production line. Through careful analysis and application of advanced mold technologies, they streamlined processes resulting in faster turnaround times without sacrificing quality—a win-win scenario! These examples illustrate how expert collaboration can lead not just to problem-solving but also groundbreaking advancements within the industry.
Conclusion

In the world of appliance design, understanding injection molding techniques is paramount to achieving optimal results. Lost core injection molding stands out as a revolutionary method that enhances both efficiency and quality in production. By mastering what is a lost core molding and its associated processes, designers can significantly improve the functionality and aesthetics of their products.
Key Takeaways on Injection Molding
Throughout this exploration of lost core injection molding, several key takeaways emerge. First, recognizing what is core in injection molding is crucial for developing high-quality components without voids or imperfections. Additionally, knowing how do you fix voids in injection molding can save time and resources during the manufacturing process, ensuring that appliances meet rigorous standards.
Another critical aspect is understanding what is coring in injection molding, which allows for better material distribution and reduced weight without sacrificing strength. These insights collectively underline the importance of adopting innovative injection molding techniques to stay competitive in today's market.
Future Trends in Appliance Design
Looking ahead, the future trends in appliance design will increasingly revolve around sustainability and smart technology integration. As manufacturers seek to minimize waste and energy consumption, methods like lost core injection molding will gain prominence due to their efficiency and reduced material usage. Moreover, advancements in automation and AI will likely streamline production processes further while enhancing precision.
Designers will also focus on creating more modular appliances that can be easily upgraded or repaired—an approach that aligns with consumer demand for longevity over disposability. This shift necessitates a deeper understanding of what is core in injection molding as designers tailor components for adaptability.
Maximizing Efficiency in Manufacturing
Maximizing efficiency in manufacturing hinges on continuous improvement and innovation within the production process. Embracing advanced techniques such as lost core injection molding not only optimizes material use but also reduces cycle times significantly—leading to faster turnarounds without compromising quality.
Furthermore, implementing robust quality assurance practices helps prevent common pitfalls associated with voids or defects by addressing how do you fix voids in injection molding before they become an issue. Ultimately, leveraging expertise from teams like Baoyuan can provide invaluable insights into mastering these techniques while ensuring that every product meets high standards of excellence.