Introduction
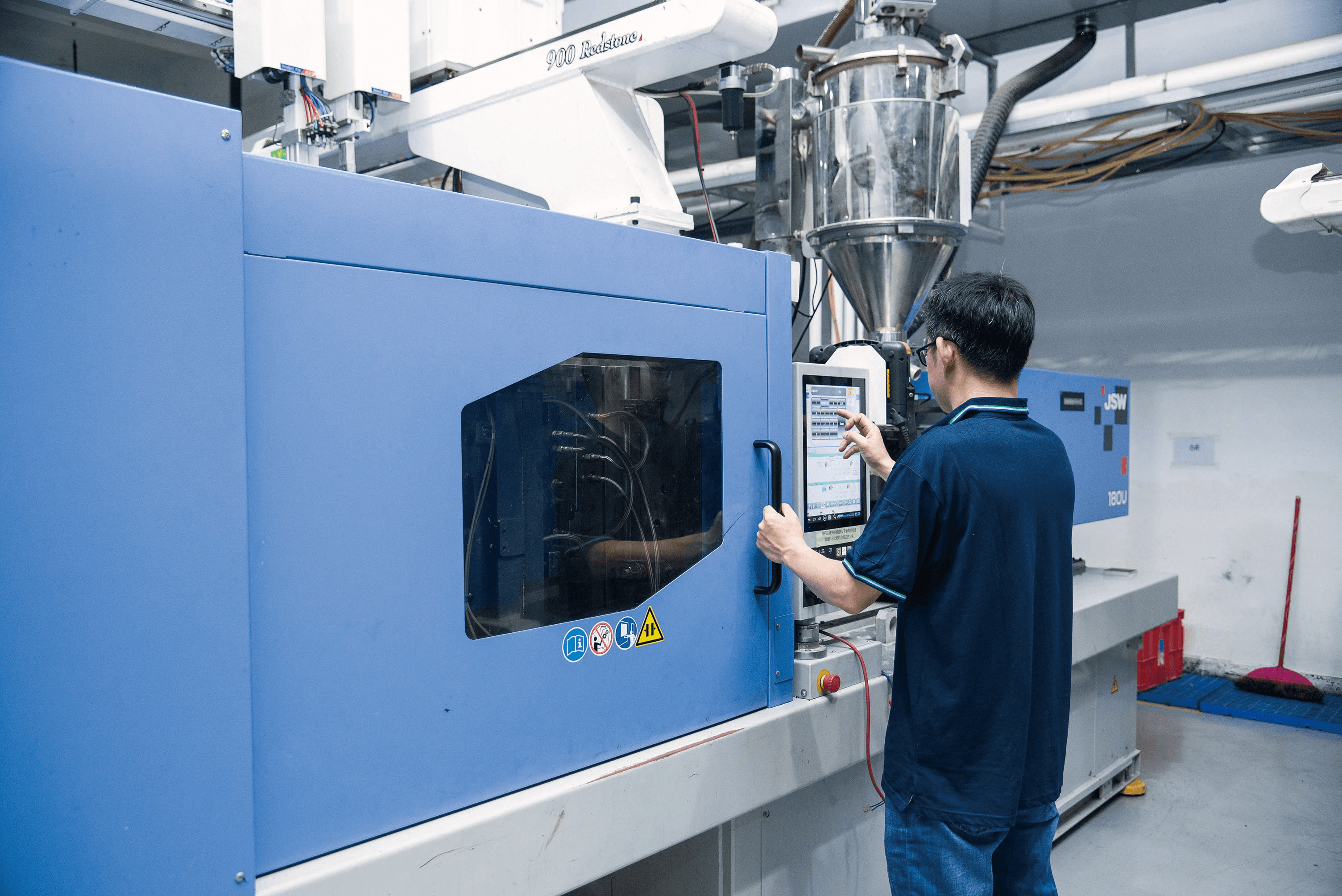
In the world of manufacturing, understanding injection molding cycle time is crucial for optimizing production efficiency and cost-effectiveness. This process involves a series of steps that determine how quickly a plastic part can be produced, impacting everything from lead times to overall profitability. With the right knowledge, manufacturers can significantly improve their operations by minimizing delays and maximizing output.
Understanding Injection Molding Cycle Time
Injection molding cycle time refers to the total duration required to produce one part through the injection molding process. This includes several stages: injection, cooling, and ejection, each contributing to the overall time taken for production. To answer the question How much time does injection molding take? one must consider these components along with variations in machinery and materials used.
Importance of Monitoring Cycle Times
Monitoring cycle times is essential for identifying inefficiencies within the production process, allowing manufacturers to make informed adjustments that enhance productivity. By keeping an eye on these metrics, companies can pinpoint bottlenecks and implement strategies on how to reduce injection molding cycle time effectively. Regular analysis also helps in maintaining quality control and ensuring that production aligns with market demands.
Key Factors Influencing Cycle Time
Numerous factors influence injection molding cycle time, including material properties, mold design, machine specifications, and environmental conditions during production. For instance, variations in plastic type can affect cooling rates significantly—this directly impacts the overall plastic injection molding cycle time. Understanding these factors enables manufacturers to fine-tune their processes and leverage tools like an injection molding cycle time formula or an injection molding cycle time chart for better decision-making.
The Basics of Injection Molding Cycle Time
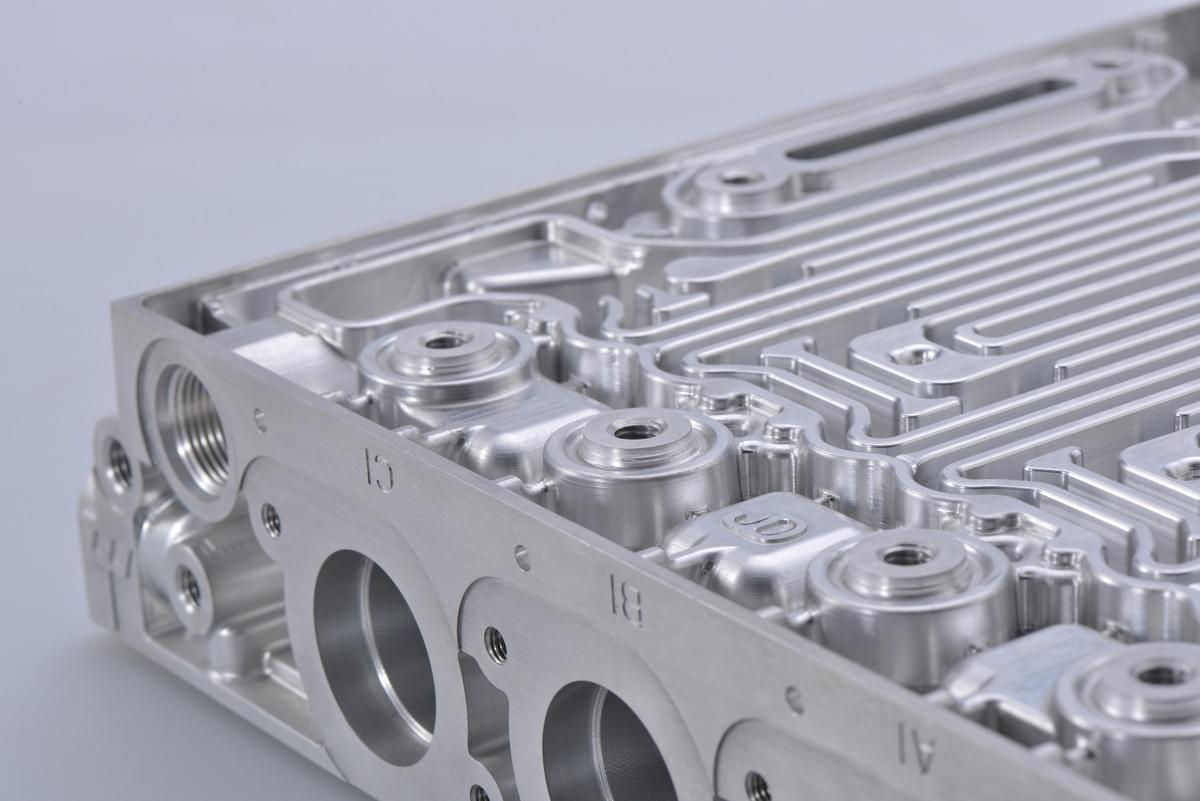
Understanding the injection molding cycle time is crucial for anyone involved in the manufacturing process. This section will break down the definition, components, and common metrics associated with cycle time, helping you grasp how much time does injection molding take? With a solid foundation, you'll be better equipped to explore strategies for optimization.
Definition and Components
Injection molding cycle time refers to the total duration it takes to produce a molded part from start to finish. This encompasses several components: injection time, cooling time, and ejection time. Each of these elements plays a vital role in determining how much time does injection molding take? Understanding these components allows manufacturers to pinpoint areas for improvement and efficiency.
Common Cycle Time Metrics
When discussing injection molding cycle times, various metrics come into play that can help assess performance. Typically measured in seconds or minutes per part produced, these metrics include average cycle time and production rate per hour. By analyzing these common cycle time metrics, manufacturers can effectively compare their processes against industry standards and identify opportunities for reducing injection molding cycle time.
Plastic Injection Molding Cycle Time Explained
Plastic injection molding cycle time is often broken down into several phases: heating the material, injecting it into the mold, allowing it to cool and solidify, and finally ejecting the finished product. Each phase has its own timing considerations that contribute to overall efficiency; thus understanding this breakdown is key when using an injection molding cycle time formula for calculations. Additionally, being aware of how different materials affect plastic injection molding cycle times can guide decisions on material selection based on production needs.
How Much Time Does Injection Molding Take?
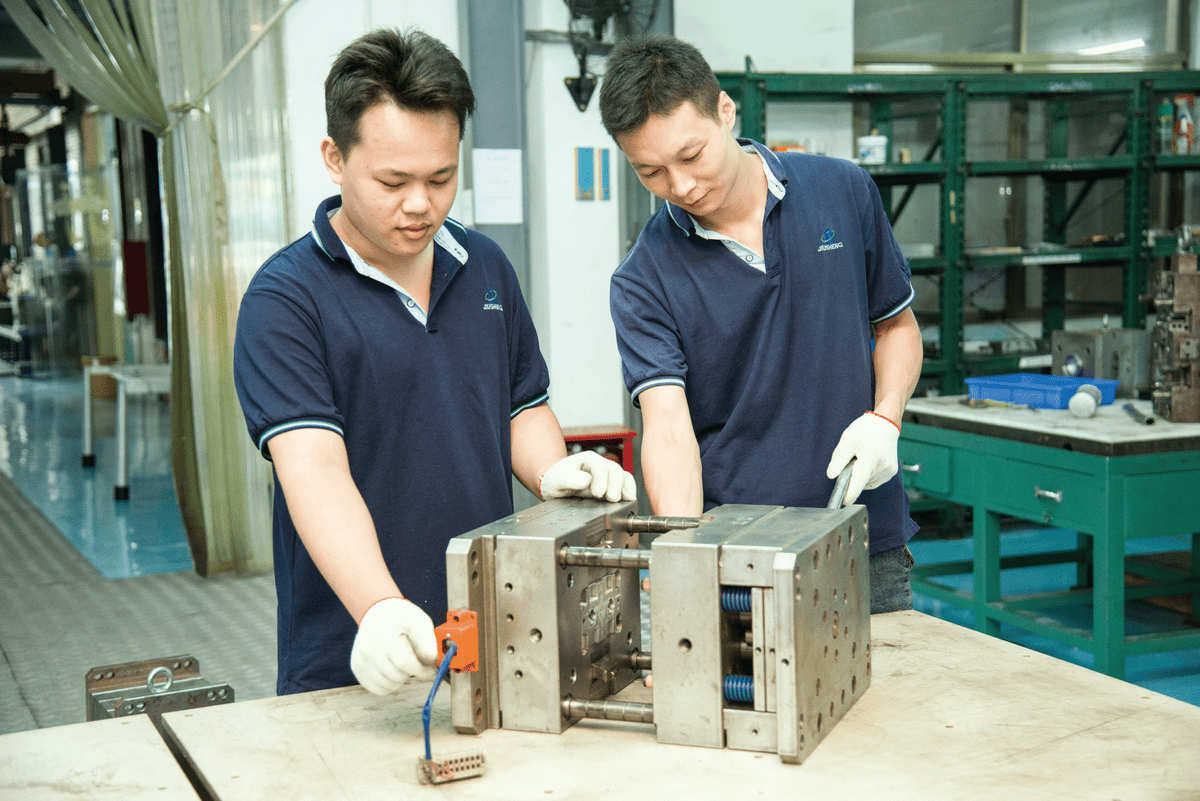
When it comes to understanding how much time injection molding takes, it's crucial to consider various factors that can significantly influence the overall process. The injection molding cycle time can vary based on the complexity of the part being produced, the type of material used, and the efficiency of the machinery involved. Additionally, external elements like ambient temperature and humidity can also play a role in determining how quickly a mold can be filled and cooled.
Factors Affecting Overall Time
Several key factors affect injection molding cycle time, making it essential to analyze each element carefully. The design of the mold is paramount; intricate designs may require longer cooling times, while simpler geometries generally yield faster cycles. Moreover, the type of plastic used impacts how well it flows during injection and how quickly it solidifies—materials with lower melting points often result in shorter cycle times.
Another significant aspect is machine performance; modern machines equipped with advanced technology can optimize processes and reduce downtime. Operator skill also plays a critical role; experienced personnel are more adept at troubleshooting issues that may arise during production, ensuring smoother operations. Lastly, maintenance schedules for equipment must be adhered to closely since poorly maintained machines can lead to unexpected delays in production.
Comparison of Different Processes
When comparing different manufacturing processes, it's important to note that injection molding generally offers quicker cycle times than methods like blow molding or compression molding. For instance, while traditional blow molding might take several minutes per part due to its reliance on air pressure for shaping materials, plastic injection molding cycle time typically ranges from 15 seconds to several minutes depending on part complexity and size.
Furthermore, reaction injection molding (RIM) has its own unique cycle time characteristics; what is the cycle time for reaction injection molding? It usually falls within a similar range as conventional methods but varies based on material properties and curing times involved in RIM processes. This comparison highlights why many manufacturers favor plastic injection over other techniques when speed is critical.
Case Studies in Efficient Production
To illustrate efficient production practices within the realm of injection molding cycle time management, let’s delve into some notable case studies. One company optimized their process by implementing real-time monitoring using an advanced injection molding cycle time chart that tracked performance metrics closely—this allowed them to identify bottlenecks immediately and adjust accordingly. By focusing on these data-driven insights along with employee training programs aimed at improving operational efficiency, they successfully reduced their overall production time by 20%.
Another example involves Baoyuan's approach to reducing injection molding cycle times through strategic investments in automation technology—these enhancements led not only to faster processing but also improved product consistency across batches. Their results showed a significant reduction in scrap rates as well as shorter lead times for clients seeking quick turnaround on custom parts. These case studies underscore how understanding factors influencing plastic injection molding cycle time can lead businesses toward greater efficiency and profitability.
Injection Molding Cycle Time Formula
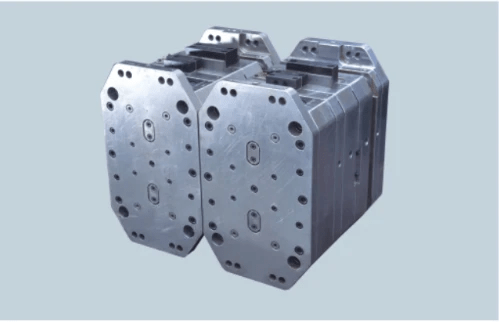
Understanding the injection molding cycle time formula is essential for manufacturers seeking to optimize their production processes. This formula not only provides a quantitative measure of the time required for each cycle but also helps in identifying areas for improvement. By dissecting this formula, businesses can better answer questions such as, How much time does injection molding take? and How to reduce injection molding cycle time?
Breakdown of the Formula
The injection molding cycle time formula can be broken down into several key components: injection time, cooling time, and ejection time. Injection time refers to how long it takes to inject the molten plastic into the mold cavity; cooling time is the period needed for the plastic to solidify; and ejection time is when the finished part is removed from the mold. Each of these elements contributes significantly to understanding overall plastic injection molding cycle time.
A common representation of this formula might look like this: Cycle Time = Injection Time + Cooling Time + Ejection Time + Other Delays (if applicable). By analyzing each segment, manufacturers can pinpoint inefficiencies and streamline their processes effectively. This breakdown not only clarifies what influences cycle times but also empowers teams with actionable insights on improving efficiency.
Practical Applications in Production
In practical terms, applying the injection molding cycle time formula can revolutionize production efficiency in numerous ways. For instance, by using this formula during initial setup or when transitioning between different molds, companies can estimate how much downtime they might experience and adjust their schedules accordingly. Additionally, monitoring these metrics over multiple production runs allows for data-driven decisions regarding machine maintenance and process adjustments.
When considering What is the cycle time for reaction injection molding?, it's crucial to compare it against standard practices in traditional plastic injection molding processes using our established formulas. This comparative analysis helps identify if reaction injection offers any significant advantages or if improvements are needed in conventional methods. Ultimately, accurate calculations based on this formula lead directly to enhanced productivity and reduced costs.
Tips for Accurate Calculations
To ensure accuracy when calculating your injection molding cycle times, consider implementing a systematic approach that includes regular monitoring and updates of your data inputs. Utilizing an injection molding cycle time chart can help visualize trends over different production batches while making it easier to identify anomalies or unexpected delays that could skew results. Furthermore, collaborating with team members who have hands-on experience with machinery will enhance your understanding of realistic timings versus theoretical calculations.
It's also beneficial to regularly review each component contributing to your total cycle times—especially cooling times—which often vary based on material properties and mold designs used in plastic injection molding cycles. Don't hesitate to leverage technology like simulation software that predicts potential bottlenecks before they arise; this proactive stance will keep you ahead of any issues related to how much time does injection molding take? By following these tips diligently, you'll be well-equipped not just with numbers but with strategies aimed at reducing those numbers effectively.
Strategies to Reduce Injection Molding Cycle Time
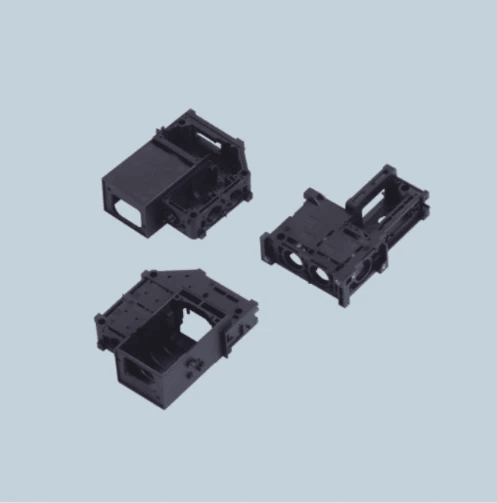
Reducing injection molding cycle time is crucial for enhancing productivity and lowering costs in manufacturing. Companies that master this process can significantly improve their bottom line while meeting customer demands more efficiently. So, how much time does injection molding take? The answer lies in understanding the strategies that industry leaders implement to optimize their operations.
Best Practices from Industry Leaders
Leading manufacturers often share a treasure trove of best practices aimed at minimizing plastic injection molding cycle time. One common approach is to analyze the entire production workflow, identifying bottlenecks that slow down the process. Techniques such as parallel processing and optimizing cooling times can lead to substantial reductions in overall cycle time, allowing companies to produce more parts in less time.
Another effective practice involves regular maintenance of machinery and tools used in the injection molding process. Ensuring that equipment operates at peak efficiency reduces downtime and enhances reliability, which directly impacts the injection molding cycle time formula used for planning production schedules. By adopting these best practices, companies not only streamline their processes but also foster a culture of continuous improvement.
Role of Technology in Optimization
Technology plays an indispensable role in reducing injection molding cycle time by providing innovative solutions for monitoring and enhancing production efficiency. Advanced software systems enable manufacturers to track real-time data on cycle times, allowing them to make immediate adjustments when necessary. This proactive approach helps answer the question: how to reduce injection molding cycle time? By leveraging technology, businesses can identify inefficiencies quickly and implement targeted solutions.
Moreover, automation technologies have revolutionized many aspects of the injection molding process, from material handling to quality control checks. Implementing robotics can significantly decrease manual labor requirements while ensuring consistent production speeds—further optimizing plastic injection molding cycle time. The integration of smart technologies such as IoT devices also provides insights into machine performance trends over time, leading to informed decision-making.
Baoyuan's Approach to Cycle Time Reduction
Baoyuan has taken a unique stance on reducing injection molding cycle time through innovative processes tailored specifically for its operations. Their strategy includes investing heavily in research and development aimed at refining materials used during production—leading to faster cooling rates and shorter overall cycles. Additionally, Baoyuan utilizes an intricate analysis of their injection molding cycle time chart which allows them to visualize data trends effectively.
By focusing on employee training programs centered around efficient operation techniques, Baoyuan ensures that all team members understand how critical their roles are in minimizing delays throughout the manufacturing process. This emphasis on expertise fosters a collaborative environment where everyone contributes towards achieving optimal results with minimal waste or downtime—key components when addressing what is the cycle time for reaction injection molding?
In conclusion, through best practices adopted from industry leaders combined with cutting-edge technology implementations and Baoyuan’s tailored approaches, companies can effectively tackle challenges associated with long plastic injection molding cycle times while positioning themselves for future success.
Monitoring Injection Molding Cycle Time
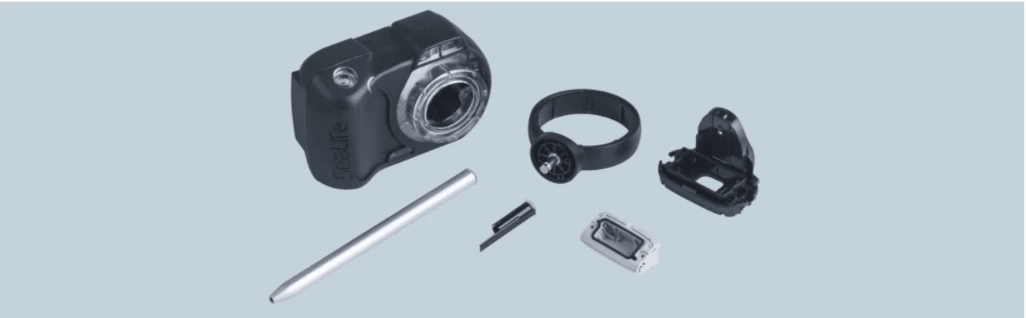
Monitoring injection molding cycle time is crucial for ensuring efficiency and productivity in manufacturing. By keeping a close eye on cycle times, manufacturers can identify bottlenecks, optimize processes, and ultimately improve overall output. This section will delve into the tools and techniques available for tracking cycle times, the use of charts for analysis, and how real-time adjustments can enhance efficiency.
Tools and Techniques for Tracking
To effectively monitor injection molding cycle time, various tools and techniques can be implemented. Advanced software solutions allow manufacturers to collect data automatically from machines, providing real-time insights into how much time does injection molding take? These systems often include dashboards that display key metrics related to the plastic injection molding cycle time, making it easier to spot trends or anomalies.
In addition to software tools, manual tracking methods such as checklists or logbooks can also be beneficial. While these methods may require more effort and are prone to human error, they still provide valuable insights when high-tech solutions are not available. Ultimately, the choice of tool depends on the scale of production and budget considerations—both of which influence how to reduce injection molding cycle time effectively.
Utilizing Injection Molding Cycle Time Charts
Injection molding cycle time charts serve as visual aids that help manufacturers analyze performance over specific periods. These charts can illustrate trends in cycle times across different production runs or highlight variations due to machine settings or material changes. By regularly reviewing these charts, manufacturers gain a clearer understanding of what constitutes normal operation versus outlier performances.
When assessing what is the cycle time for reaction injection molding compared to traditional methods, these charts become even more critical. They allow for side-by-side comparisons that reveal potential inefficiencies or advantages inherent in different processes. Ultimately, utilizing an injection molding cycle time chart empowers teams to make informed decisions about adjustments needed in their operations.
Real-time Adjustments for Efficiency
Real-time monitoring enables quick adjustments that can significantly enhance overall efficiency in production lines focused on reducing injection molding cycle time. By leveraging data collected through monitoring tools, operators can instantly identify issues such as overheating molds or inadequate cooling times—both factors that directly impact the plastic injection molding cycle time.
Implementing feedback loops allows operators not just to react but also proactively tweak settings based on historical data trends observed in their injection molding cycle time formula analyses. This dynamic approach ensures continuous improvement rather than relying solely on periodic reviews—which might miss immediate opportunities for optimization.
In summary, effective monitoring of injection molding cycle times encompasses various strategies from using advanced software tools to leveraging visual aids like charts and implementing real-time adjustments based on collected data insights.
Conclusion
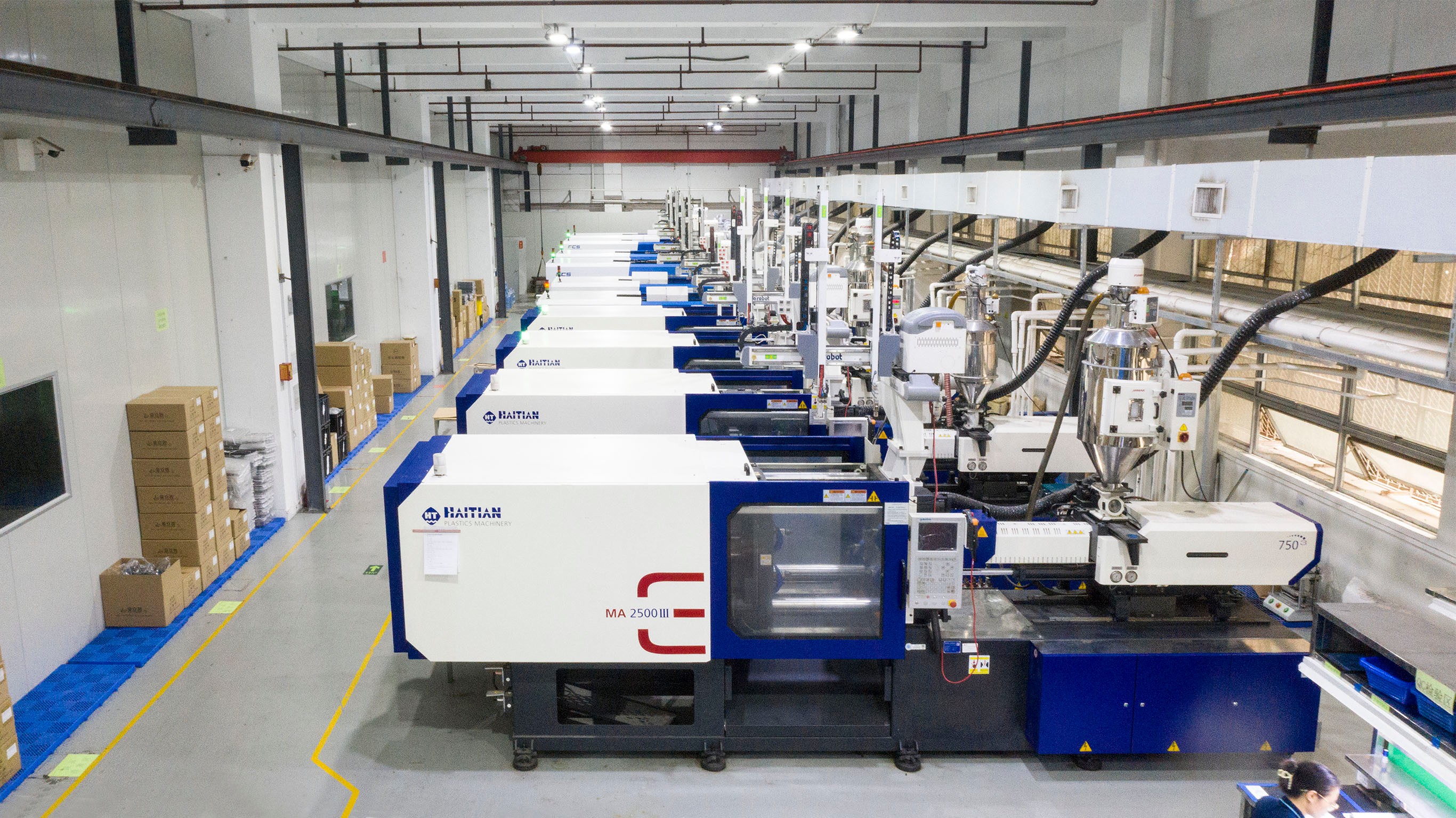
In the fast-paced world of manufacturing, understanding injection molding cycle time is crucial for efficiency and profitability. By mastering the intricacies of cycle time management, manufacturers can not only enhance productivity but also reduce costs. Whether you're asking yourself, How much time does injection molding take? or exploring ways to streamline operations, effective cycle time management is key.
Keys to Effective Cycle Time Management
To effectively manage injection molding cycle time, manufacturers must first establish a baseline by utilizing metrics like the injection molding cycle time formula. This allows for precise tracking and comparison against industry standards and personal benchmarks. Furthermore, implementing a detailed injection molding cycle time chart can help visualize trends and identify bottlenecks in production.
Another essential factor is continuous improvement through monitoring and adjusting processes based on real-time data. Regularly revisiting strategies on how to reduce injection molding cycle time will lead to enhanced efficiency and reduced waste over time. Ultimately, an agile approach that combines technology with best practices will yield the best results in managing cycle times effectively.
Future Trends in Injection Molding
The landscape of plastic injection molding is evolving rapidly, with advancements in technology paving the way for more efficient processes. One exciting trend is the integration of Artificial Intelligence (AI) and machine learning algorithms to optimize the injection molding cycle time dynamically. As these technologies mature, they promise to revolutionize how manufacturers calculate What is the cycle time for reaction injection molding? by providing real-time insights into process efficiencies.
Sustainability initiatives also play a significant role in shaping future practices within this sector; eco-friendly materials and energy-efficient machines are becoming standard rather than exceptions. Additionally, as global competition heats up, companies that leverage cutting-edge techniques will have a distinct advantage in managing their plastic injection molding cycle times effectively while meeting consumer demands for both quality and sustainability.
The Role of Expertise in Optimization
While technology provides tools for enhancing efficiency, human expertise remains irreplaceable when it comes to optimizing injection molding processes. Skilled professionals bring invaluable insights into how to reduce injection molding cycle time through experience-based decision-making that algorithms alone cannot replicate. Their knowledge enables organizations not only to implement changes but also to foresee potential challenges before they arise.
Moreover, training teams on interpreting data from tools like an injection molding cycle time chart fosters a culture of continuous improvement throughout an organization. By empowering employees with knowledge about their processes—how much time does injection molding take?—companies can cultivate innovation from within while remaining competitive in a rapidly changing industry landscape.