Introduction

Injection molding is a fascinating process that transforms raw plastic into intricate parts that we encounter in our daily lives. Understanding the fundamentals of injection molding is crucial for anyone involved in plastic manufacturing, whether you're a designer, engineer, or manufacturer of injection moulding machines. This introduction sets the stage for exploring the key aspects of plastic part design for injection molding and its significance in achieving high-quality products.
Understanding Injection Molding Fundamentals
At its core, injection molding is a method where molten plastic is injected into a mold to create specific shapes and designs. This process relies on various types of injection moldable plastics, each with unique properties that can influence the final product's performance and aesthetics. By grasping these fundamentals, designers can make informed decisions that enhance both functionality and manufacturability in their projects.
Importance of Plastic Part Design
Plastic part design is not just about aesthetics; it directly impacts the efficiency and success of the entire plastic injection process. Well-thought-out designs ensure optimal use of materials while minimizing waste during production—a critical factor in modern sustainable manufacturing practices. Additionally, effective plastic part design can significantly reduce production costs and lead times, making it essential for staying competitive in today's market.
Overview of the Injection Molding Process
The injection molding process begins with selecting appropriate materials followed by heating them until they become malleable enough to be injected into molds under pressure. Once cooled and solidified, these molded parts are ejected from their molds ready for further processing or assembly. Understanding this sequence helps designers appreciate how their choices affect everything from material selection to final product quality within the realm of plastic molding and manufacturing.
The Science Behind Injection Molding
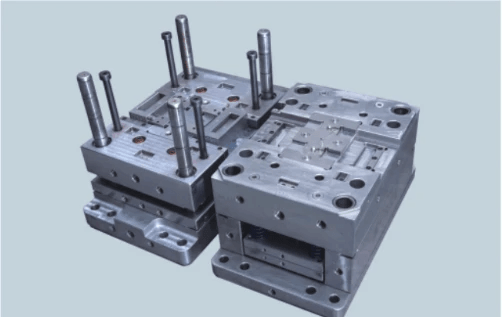
Injection molding is a fascinating process that combines art and science to create complex plastic parts. Understanding the intricacies of this method can significantly enhance your plastic part design for injection molding, ensuring efficiency and effectiveness in production. Let’s dive into the pivotal aspects that make injection molding a cornerstone of plastic manufacturing.
Material Selection for Injection Moldable Plastics
Choosing the right material is critical in the realm of plastic injection molding, as it directly affects both functionality and aesthetics of the final product. Injection moldable plastics come in various types, including thermoplastics, thermosets, and elastomers, each with unique properties tailored to specific applications. Manufacturers must assess factors such as strength, flexibility, temperature resistance, and cost when selecting materials for their designs to optimize performance during the plastic molding process.
The interplay between material choice and design cannot be overstated; a well-designed part may fail if incompatible materials are used in its production. For instance, using a brittle plastic might lead to premature breakage under stress while a more flexible option could provide durability without sacrificing shape integrity. Thus, understanding material characteristics is essential not only for effective plastic manufacturing but also for achieving desired outcomes in product quality.
Furthermore, advancements in polymer technology have expanded the range of available materials suitable for different applications in injection molding. From bio-based plastics to high-performance polymers, manufacturers now have an impressive arsenal at their disposal. This evolution invites designers to innovate boldly while ensuring that their selections align with sustainability goals and market demands.
How Injection Molding Operates
At its core, injection molding operates by melting plastic pellets and injecting them into a mold under high pressure—a straightforward yet highly refined process that can yield intricate designs efficiently. The cycle begins with heating up raw materials until they become molten; this liquid state allows them to flow easily into molds that shape the final product according to precise specifications defined during the design phase. Once injected into these molds—often made from steel or aluminum—the molten material cools down rapidly before being ejected as solidified parts ready for use or further processing.
This method offers remarkable advantages over traditional manufacturing processes; it allows for high-volume production runs with minimal waste compared to other techniques like machining or casting. Moreover, because multiple parts can be produced simultaneously using multi-cavity molds, manufacturers can significantly reduce costs associated with labor and time—making it an attractive option within competitive markets focused on efficiency and scalability in plastic manufacturing.
However, successful operation requires meticulous attention throughout each stage—from temperature control during melting to timing during cooling cycles—to ensure optimal results without defects such as warping or surface imperfections on finished pieces. A comprehensive understanding of how injection molding operates enables designers not only to create more effective products but also helps mitigate potential issues before they arise during production.
Key Components of an Injection Molding Machine
An injection molding machine is composed of several key components that work together harmoniously to execute the entire process efficiently. The primary elements include the hopper (where raw materials are fed), barrel (where heating occurs), screw (which mixes and transports melted plastics), mold (the cavity where shaping takes place), and ejection system (that removes finished products). Each component plays a vital role; any malfunction could disrupt operations or compromise product quality.
For instance, if the barrel fails to maintain consistent temperatures throughout its length due to inadequate insulation or faulty heating elements—this could lead directly to uneven melting patterns which affect how well plastics fill molds during injection cycles. Similarly crucial is ensuring proper alignment between molds so that there are no gaps allowing molten material leakage; precision here guarantees clean edges on all finished pieces essential for achieving high-quality standards expected from modern manufacturers engaged in plastic part design for injection molding.
Moreover, advancements continue within this sector as manufacturers seek out more efficient machines equipped with features like automated systems capable of monitoring performance metrics real-time—a trend likely driven by increasing demands around speed-to-market alongside sustainability concerns within global supply chains linked closely with eco-conscious practices across industries reliant upon effective plastic manufacturing techniques today!
Essential Principles of Plastic Part Design

Designing for Manufacturability in Injection Molding
Designing for manufacturability is a key principle in the realm of plastic part design for injection molding. This means creating parts that are easy to produce while minimizing waste and maximizing efficiency during the plastic molding and manufacturing process. Factors such as wall thickness, draft angles, and ribbing must be meticulously considered to ensure that the finished product can be reliably produced using injection moldable plastics.
To achieve optimal results, designers should collaborate closely with manufacturers of injection moulding machines early in the design phase. This collaboration provides insights into machine capabilities and limitations, ensuring that designs align with production realities. Ultimately, good manufacturability leads to shorter lead times and lower costs while maintaining high-quality standards.
Tolerances and Specifications in Plastic Manufacturing
Tolerances play a pivotal role in ensuring that components fit together seamlessly during assembly or function as intended when used separately. In plastic manufacturing, understanding how materials behave under various conditions helps determine appropriate tolerances for different applications within the context of plastic injection molding. Designers must specify tolerances clearly to avoid potential pitfalls during production.
The specifications set forth must account for factors such as shrinkage rates of specific plastics used in the injection process as well as environmental influences like temperature fluctuations or humidity levels that can affect dimension accuracy over time. By paying close attention to these elements, manufacturers can minimize defects caused by mismatched tolerances or specifications.
Moreover, it’s essential to communicate these specifications effectively across all teams involved—designers, engineers, and production staff—to ensure everyone is on the same page regarding expectations from both design and manufacturing perspectives.
Addressing Common Design Challenges
In any journey through plastic part design for injection molding, challenges are inevitable; however, they can often be anticipated and addressed proactively with proper planning. One common challenge includes managing warpage or distortion during cooling phases; this requires careful consideration of material selection as well as mold geometry when designing parts using plastic injection techniques.
Another frequent issue arises from inadequate draft angles leading to difficulty in ejecting parts from molds after cooling has occurred—resulting not only in damaged parts but also increased cycle times due to additional labor required for removal tasks! Designers should always evaluate how features such as undercuts may complicate ejection processes too; simplicity often yields better results when it comes down to efficient production workflows.
Finally, designers should never underestimate the importance of thorough testing throughout development stages—including prototyping—to identify potential issues before they escalate into costly mistakes once full-scale production begins! Embracing an iterative approach allows teams involved in both design and manufacturing realms greater flexibility while refining their strategies towards achieving optimal outcomes with every new project undertaken.
Choosing the Right Material
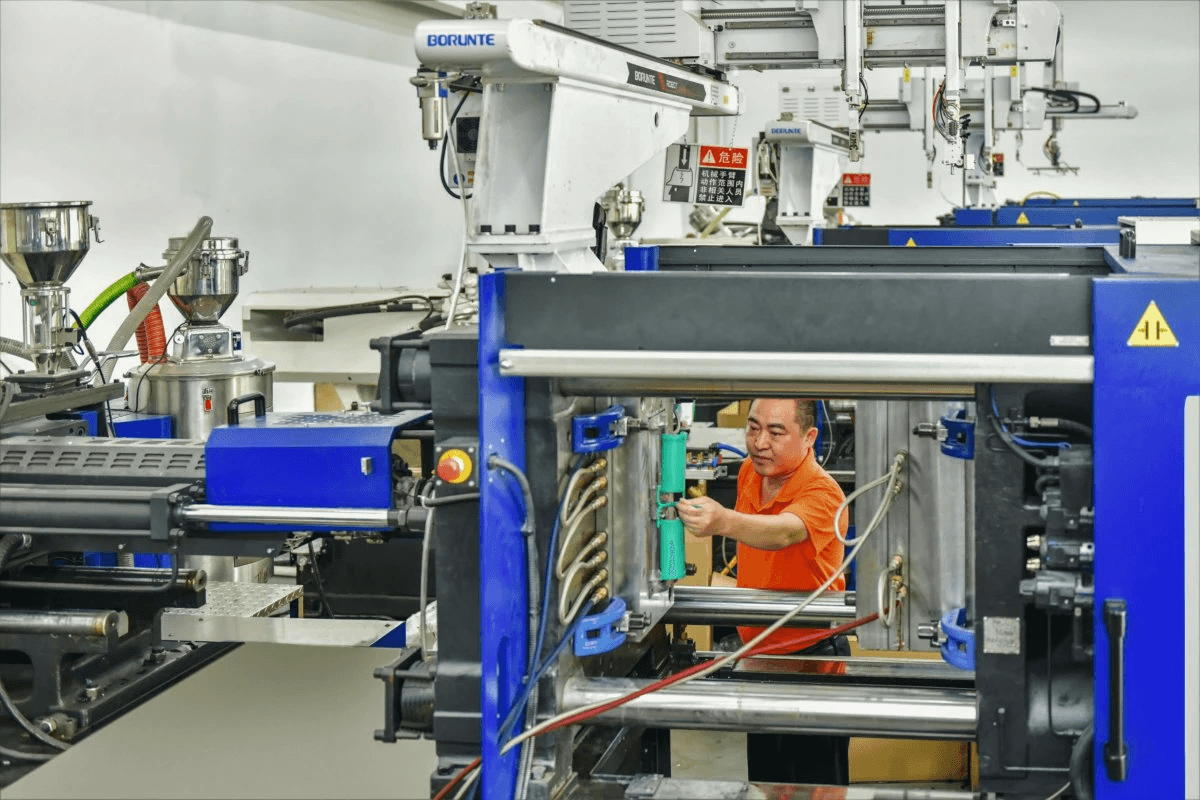
Selecting the right material is crucial in plastic part design for injection molding, as it directly influences the performance, aesthetics, and manufacturability of the final product. With a myriad of injection moldable plastics available, understanding their properties can help designers make informed choices that align with project requirements. This section will delve into common materials used in plastic manufacturing, their characteristics, and how they affect design decisions.
Properties of Common Injection Moldable Plastics
Injection moldable plastics come in various types, each with unique properties suited for specific applications. For example, Polypropylene (PP) is known for its excellent chemical resistance and flexibility, making it ideal for automotive components and household items. On the other hand, Acrylonitrile Butadiene Styrene (ABS) offers high impact resistance and good surface finish, making it a popular choice for consumer electronics and toys.
Another widely used material is Polycarbonate (PC), which boasts exceptional strength and transparency but can be more expensive than other options. Additionally, Nylon (PA) provides outstanding wear resistance and strength at elevated temperatures but may absorb moisture over time. Understanding these properties allows manufacturers to select the most suitable plastic injection materials that will enhance durability while meeting aesthetic goals.
Impact of Material Choice on Design
The choice of material significantly impacts both functionality and aesthetics in plastic part design for injection molding. Different plastics have varying shrink rates during cooling; hence designers must account for this when creating molds to ensure precise dimensions are achieved post-molding. Furthermore, some materials may require specific processing conditions such as temperature or pressure settings during plastic injection to achieve optimal results.
Additionally, certain materials lend themselves better to complex geometries or intricate designs due to their flow characteristics during the injection molding process. The weight-bearing capacity also varies across different plastics; thus selecting a robust material is critical if structural integrity is paramount in the application’s use case. Ultimately, understanding how material choice affects design empowers engineers to create innovative solutions that meet both functional demands and production efficiency.
Case Studies Using Different Plastics
Examining real-world applications illustrates how diverse choices of injection moldable plastics can lead to successful outcomes in plastic manufacturing projects. For instance, a manufacturer of an automotive component opted for glass-filled Nylon due to its superior strength-to-weight ratio; this decision resulted in a lightweight yet durable part that improved fuel efficiency without compromising safety standards.
In another case study involving consumer electronics packaging, using ABS allowed designers to achieve an aesthetically pleasing finish while ensuring robustness against drops or impacts during shipping—effectively reducing return rates due to damaged products post-delivery. Lastly, when developing medical devices requiring sterilization capabilities alongside mechanical strength requirements—Polypropylene emerged as an ideal candidate because it withstands high temperatures without degrading.
These examples highlight how strategic selection among various plastics can elevate product quality while addressing specific industry needs within the realm of plastic molding and manufacturing.
The Role of Prototyping in Injection Molding
Prototyping plays a pivotal role in the realm of plastic part design for injection molding, serving as a bridge between concept and production. It allows designers to visualize and test their ideas before committing to full-scale manufacturing, significantly reducing the risk of costly errors down the line. In an industry where precision is key, effective prototyping can streamline the transition from design to actual plastic manufacturing, ensuring that every detail aligns with expectations.
Benefits of Rapid Prototyping
Rapid prototyping offers numerous advantages that can enhance the plastic injection molding process. Firstly, it accelerates product development timelines; designers can quickly create tangible models to evaluate form and function without waiting for lengthy tooling processes. Additionally, rapid prototyping fosters innovation by allowing teams to experiment with various designs and materials, ultimately leading to optimized plastic part designs that are more efficient for injection molding.
Moreover, this approach reduces costs associated with traditional prototyping methods. By utilizing techniques such as 3D printing or CNC machining, manufacturers can produce prototypes with minimal investment in time and resources. This flexibility not only aids in refining designs but also improves communication among stakeholders by providing a physical representation of ideas during discussions about plastic molding and manufacturing.
Techniques for Effective Prototyping
To achieve effective prototyping in the context of injection moldable plastics, several techniques stand out as particularly beneficial. One popular method is 3D printing, which enables rapid creation of complex geometries that might be challenging or expensive to produce through conventional methods. This technique allows designers to iterate quickly on their concepts while also testing fit and functionality before moving on to full-scale production.
Another valuable technique is CNC machining, which provides high precision when creating prototypes from robust materials similar to those used in final production runs. This technique ensures that prototypes closely mimic the properties of parts produced through plastic injection molding processes. Additionally, utilizing silicone molds for small-batch prototypes can help assess design viability while saving time compared to traditional metal tooling.
Integrating these techniques into your workflow not only enhances efficiency but also encourages collaboration among design teams and manufacturers alike. By sharing insights gained from prototype testing—whether it’s feedback on aesthetics or functionality—teams can make informed decisions about adjustments needed before committing resources towards mass production.
How Prototyping Influences Final Design
The influence of prototyping on final design cannot be overstated; it serves as a crucial feedback loop within the process of plastic part design for injection molding. Early-stage prototypes allow designers to identify potential issues related to manufacturability or performance long before they become costly problems during mass production runs. This iterative approach helps ensure that each aspect aligns with both functional requirements and aesthetic considerations vital for market success.
Furthermore, insights gained from prototype testing often lead directly to refinements in material selection or modifications in geometry tailored specifically for optimal performance during plastic injection processes. For instance, if a prototype reveals weaknesses under stress tests conducted by manufacturers specializing in injection moldable plastics, adjustments can be made early on—saving time and resources later when scaling up production volumes.
Ultimately, effective prototyping cultivates a culture of continuous improvement within organizations focused on plastic molding and manufacturing practices. By embracing this iterative mindset throughout product development stages—from initial sketches through final designs—companies position themselves better against competitors while delivering high-quality products tailored precisely for consumer needs.
Quality Assurance in the Molding Process
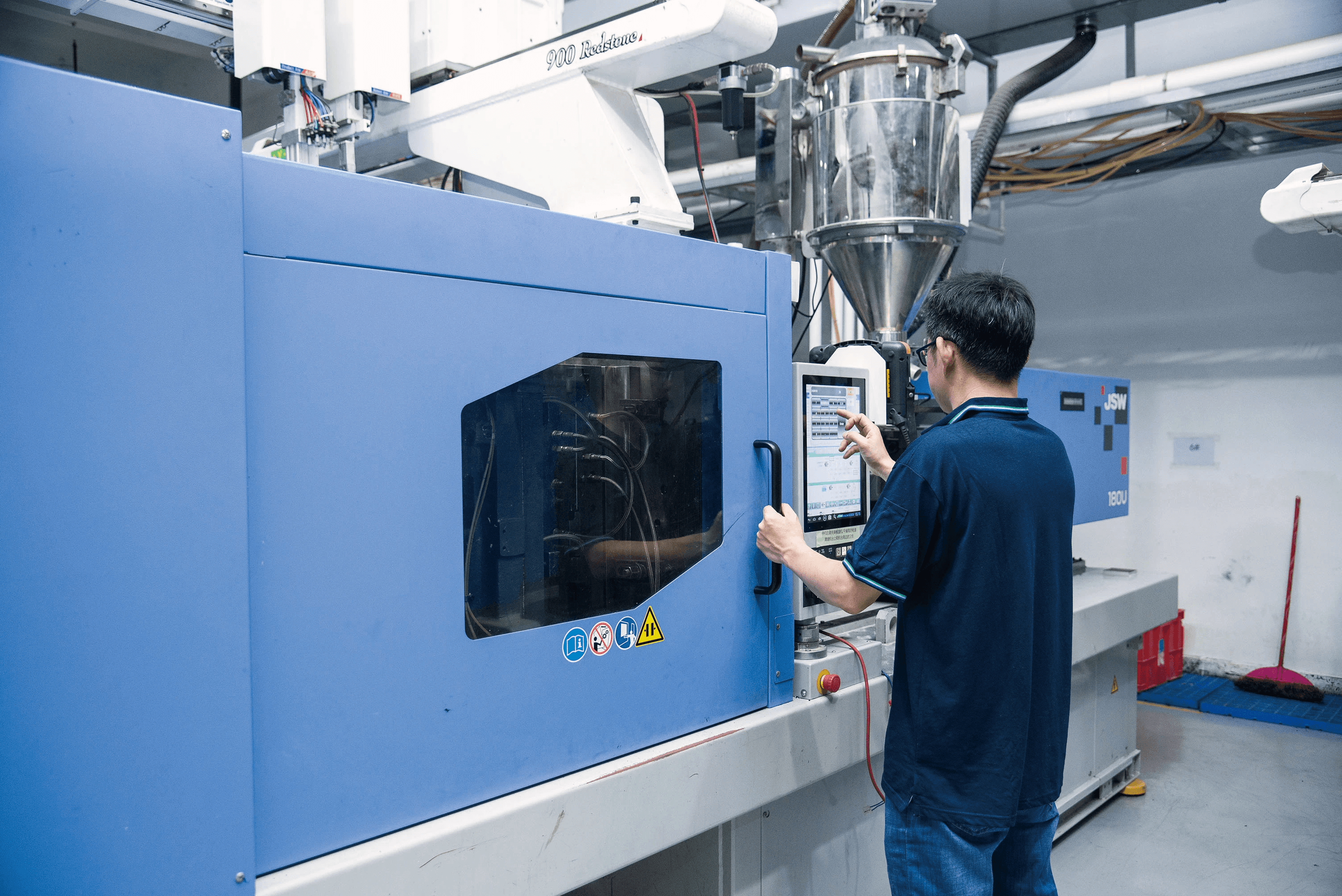
Quality assurance in the molding process is a crucial element that ensures the integrity and functionality of plastic parts designed for injection molding. As the demand for precision increases in plastic manufacturing, implementing effective quality control measures becomes paramount. This section will explore various inspection techniques, the importance of robust quality control systems, and how Baoyuan stands out as a manufacturer of injection moulding machines dedicated to ensuring quality.
Inspection Techniques for Plastic Parts
When it comes to plastic part design for injection molding, inspection techniques play a vital role in verifying that parts meet specified tolerances and performance criteria. Common methods include visual inspections, dimensional checks using calipers or gauges, and advanced techniques like laser scanning or X-ray imaging to detect internal defects. By employing these diverse inspection methods throughout the production process, manufacturers can identify potential issues early on, reducing waste and enhancing overall efficiency in plastic injection.
Moreover, integrating automated inspection systems can significantly reduce human error while increasing throughput during production runs. These systems can monitor critical parameters such as wall thickness and surface finish continuously, allowing for real-time adjustments to maintain quality standards. Ultimately, effective inspection techniques not only safeguard product integrity but also reinforce customer confidence in plastic manufacturing processes.
Importance of Quality Control Systems
Quality control systems are essential frameworks that ensure consistency and reliability throughout the entire plastic molding and manufacturing process. These systems encompass a variety of practices aimed at monitoring production stages from raw material selection through final assembly of injection moldable plastics. By establishing clear protocols and benchmarks within these systems, manufacturers can systematically address deviations from desired specifications before they escalate into larger issues.
Implementing rigorous quality control measures helps streamline operations by minimizing defects and rework costs associated with non-conforming products. Additionally, these practices contribute to compliance with industry standards and regulations which are increasingly stringent in today’s market landscape focused on sustainability and safety. Thus, investing in comprehensive quality control systems is not just beneficial; it's essential for any business aiming to thrive in the competitive field of plastic injection molding.
Baoyuan's Approach to Ensuring Quality
Baoyuan has carved out its niche as a leading manufacturer of injection moulding machines by prioritizing quality assurance at every stage of production. Their commitment begins with sourcing high-quality raw materials tailored specifically for making durable injection moldable plastics that withstand rigorous testing conditions. Furthermore, Baoyuan employs state-of-the-art technology integrated into their machinery which allows real-time monitoring during the production process—ensuring each batch meets stringent quality criteria.
The company also emphasizes continuous improvement through regular audits and feedback loops within their operational framework—a practice that fosters innovation while maintaining high standards across their product lines. Additionally, Baoyuan's team is trained extensively on best practices related to both manufacturing processes and inspection techniques—creating a culture where quality is everyone's responsibility rather than just an afterthought at the end of production runs. This holistic approach not only enhances product reliability but also boosts customer satisfaction—key factors driving success in today’s competitive landscape.
Conclusion
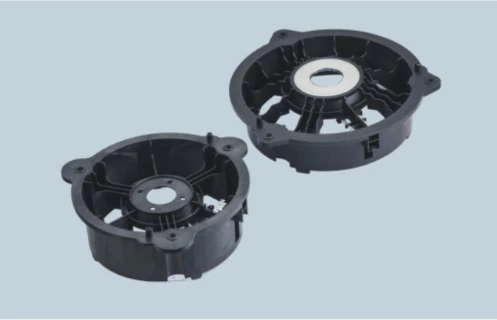
In wrapping up our exploration of injection molding, it’s clear that this manufacturing process is not just a method for creating plastic parts; it’s a blend of art, science, and engineering prowess. As we look to the future, advancements in plastic part design for injection molding will continue to evolve alongside emerging technologies. Keeping pace with these developments will be crucial for manufacturers aiming to stay competitive in the ever-changing landscape of plastic manufacturing.
The Future of Injection Molding Technology
The future of injection molding technology is bright and filled with potential innovations that promise to enhance efficiency and reduce costs. With the rise of smart manufacturing and Industry 4.0, we can expect more automated processes and real-time data analytics in plastic injection operations. These advancements will not only streamline production but also improve the quality of plastic moldable parts while minimizing waste—a win-win for both manufacturers and consumers alike.
Integrating Sustainability in Plastic Manufacturing
Sustainability is no longer just a buzzword; it has become an essential component in the world of plastic manufacturing. Manufacturers are increasingly adopting sustainable practices by using biodegradable materials and implementing recycling initiatives within their production lines. By focusing on eco-friendly options in plastic part design for injection molding, companies can significantly reduce their environmental footprint while still meeting consumer demands for high-quality products.
Best Practices for Successful Plastic Part Design
To achieve success in plastic part design for injection molding, embracing best practices is key. This includes thorough material selection based on desired properties such as strength, flexibility, and durability—ensuring that the chosen injection moldable plastics align with project goals from the start. Additionally, collaborating closely with experienced manufacturers of injection moulding machines can provide invaluable insights into optimizing designs for manufacturability while addressing common challenges faced during production.