Introduction
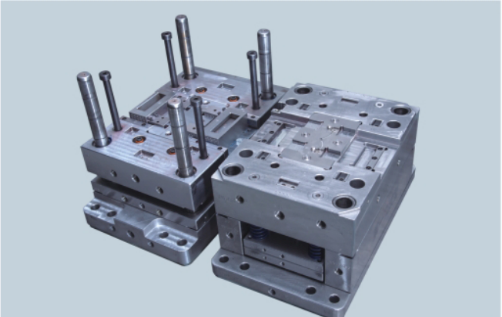
When it comes to manufacturing plastic products, understanding injection mold components is crucial. From exploring the various parts of a mold to mastering the basics of plastic injection molding, having a solid grasp of these concepts is essential for creating high-quality products efficiently.
Understanding Injection Mold Components
Injection mold components are the essential parts that make up a mold used in the plastic injection molding process. These components include the core and cavity, which play a critical role in shaping the final product.
Exploring Parts of Mold
The parts of a mold consist of various elements such as the sprue, runner, and gate, each serving a specific function in guiding molten plastic into the cavity to form the desired shape.
The Basics of Plastic Injection Molding
Plastic injection molding is a manufacturing process that involves injecting molten plastic material into a mold cavity under high pressure. This process allows for the production of complex and intricate plastic parts with precision and efficiency.
The Structure of Injection Mold Components
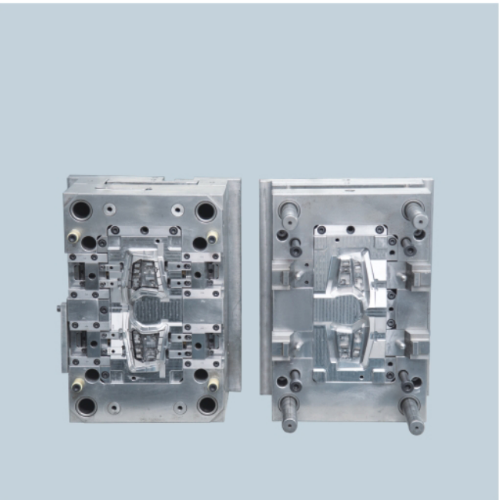
When it comes to injection mold components, the core and cavity play a crucial role in shaping the final product. The core component forms the internal features of the part, while the cavity component creates the external features. These two parts work together to produce a precise and accurate plastic product.
Core and Cavity Components
The core and cavity components are typically made from hardened steel or aluminum to withstand the high pressure and heat of the injection molding process. These components are meticulously designed to ensure that they fit together perfectly, allowing for smooth and consistent production of plastic parts.
The precision and durability of the core and cavity components are crucial to the success of the mold making process. These components must be able to withstand the intense pressure and heat generated during injection molding, ensuring that they maintain their shape and functionality over multiple production cycles. Additionally, their meticulous design allows for consistent and reliable production of high-quality plastic parts, meeting the standards of even the most demanding applications.
Mold Making Process
The mold making process involves intricate steps such as design, machining, and assembly. Skilled engineers use advanced software to create detailed blueprints for the mold components before precision machining techniques are employed to fabricate them. The final assembly involves fitting the core and cavity components together with other essential parts.
After the precision machining stage, the mold components are carefully inspected to ensure they meet the exact specifications outlined in the blueprints. Any imperfections or discrepancies are addressed and corrected before moving on to the final assembly. This meticulous attention to detail is crucial in ensuring that the mold functions flawlessly and produces high-quality parts.
Role of Baoyuan in Mold Design
Baoyuan specializes in injection mold design, bringing years of expertise to every project. Their team meticulously plans out every detail of the mold structure, ensuring that it meets all requirements for precision, durability, and efficiency in plastic part production.
With a deep understanding of injection molding core and cavity components, Baoyuan is able to deliver exceptional molds that meet strict quality standards while maximizing productivity for their clients.
Importance of Injection Molding Core and Cavity
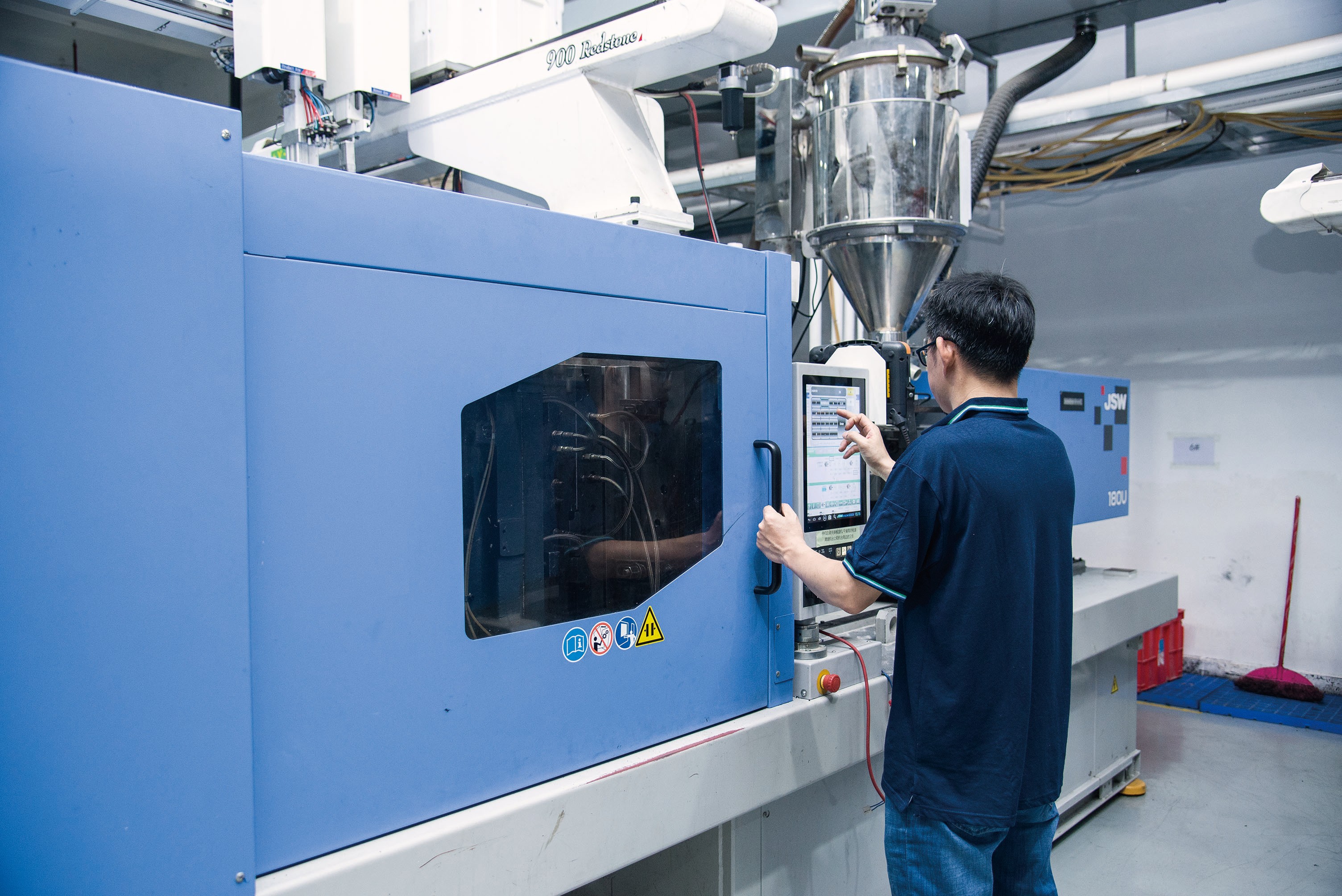
Precision in Design
Injection mold components, particularly the core and cavity, play a crucial role in the precision of the design. The accuracy and intricacy of these parts determine the final shape and features of the plastic product. Baoyuan's meticulous attention to detail ensures that every core and cavity is designed with utmost precision, guaranteeing high-quality end products. Additionally, precise mold components contribute to consistency in product dimensions, ensuring that each item meets the exact specifications required. This level of precision is essential for industries such as medical devices or aerospace, where even minor variations can have significant consequences.
Impact on Final Product Quality
The injection molding core and cavity directly impact the quality of the final product. Any imperfections or inaccuracies in these components can result in defects or flaws in the plastic parts. Baoyuan's commitment to excellence in mold making ensures that every core and cavity is crafted to perfection, resulting in flawless end products that meet industry standards.
In addition to the impact on final product quality, the precision and expertise in mold making also play a crucial role in reducing production costs. By ensuring that every core and cavity is crafted to perfection, Baoyuan minimizes the need for rework or adjustments, ultimately saving time and resources in the manufacturing process. This commitment to excellence not only results in flawless end products but also contributes to overall efficiency and cost-effectiveness.
Baoyuan's Expertise in Mold Opening
The expertise required for mold opening is paramount to achieving successful injection molding outcomes. Baoyuan's skilled technicians possess extensive knowledge and experience in mold opening procedures, ensuring smooth and efficient production processes. Their proficiency minimizes the risk of damage to injection mold components, prolonging their lifespan and maintaining optimal performance.
Furthermore, Baoyuan's expertise in mold opening extends to their ability to troubleshoot and resolve any issues that may arise during the process. Their technicians are adept at identifying potential problems and implementing effective solutions to ensure that production runs smoothly without any delays or setbacks. This proactive approach not only saves time and resources but also contributes to the overall efficiency of the injection molding operation.
Cold Slug Injection Molding
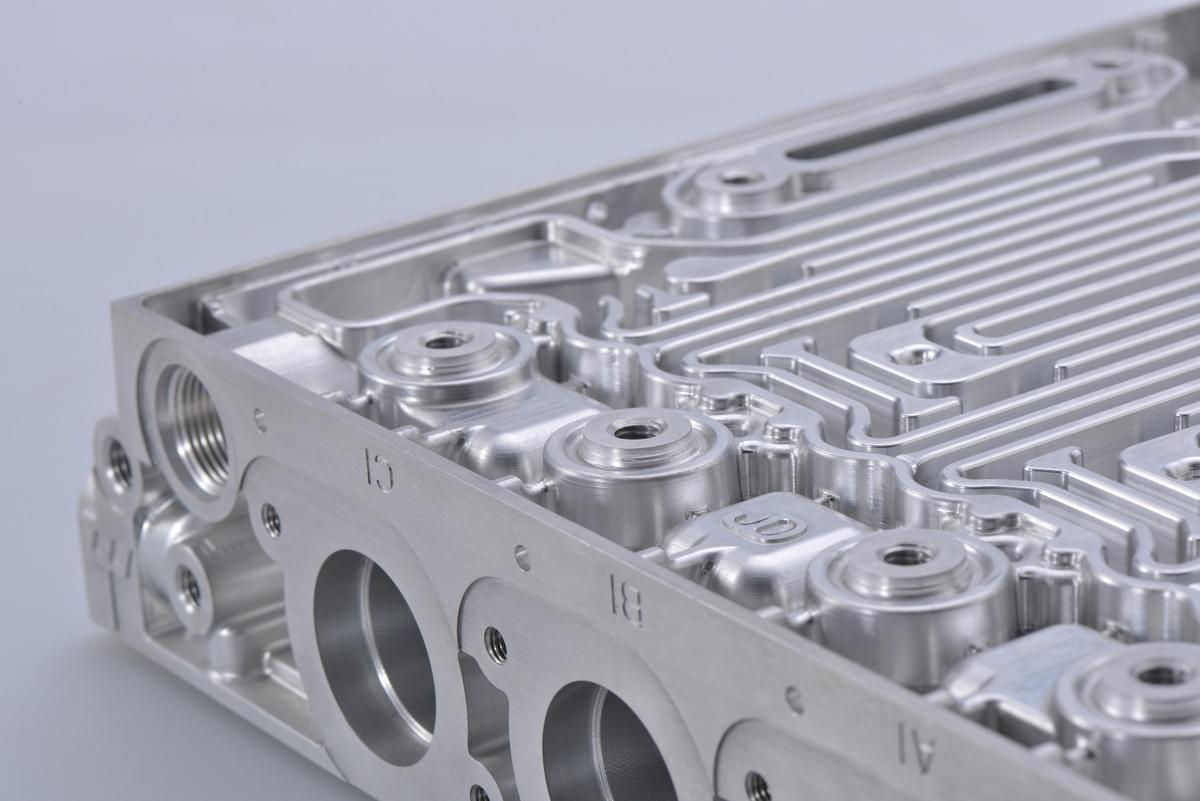
Cold slug injection molding is a process where a small amount of material is injected into the mold to push out any impurities before the actual molding takes place. This helps in ensuring that the final product is free from defects and imperfections. The process involves using a cold slug well to collect and remove the impurities, resulting in high-quality plastic parts.
Definition and Process
In cold slug injection molding, the mold is first partially filled with material, and then the remaining space is filled with molten plastic, pushing out any impurities or contaminants present in the mold. This process helps in preventing defects such as burn marks or discoloration on the final plastic parts. It is an essential step in ensuring that only high-quality products are produced through injection molding.
In addition to preventing defects, cold slug injection molding also helps in reducing cycle times and improving overall production efficiency. By removing impurities and contaminants from the mold, the process ensures that the final plastic parts are of high quality and meet industry standards. This results in cost savings for manufacturers as they can produce more parts in less time without compromising on quality.
Benefits and Limitations
The main benefit of cold slug injection molding is its ability to eliminate impurities and ensure the production of defect-free plastic parts. However, one limitation of this process is that it can increase cycle time due to the additional step involved in removing impurities from the mold. Despite this limitation, the benefits of producing high-quality parts outweigh the slight increase in cycle time.
Another benefit of cold slug injection molding is its ability to reduce the need for secondary processing and finishing, saving time and resources in the production process. By eliminating impurities at the outset, the final parts require less post-processing, resulting in faster turnaround times and lower production costs. This makes cold slug injection molding a cost-effective and efficient option for producing high-quality plastic parts.
Baoyuan's Specialization in Cold Slug Injection Molding
Baoyuan has established itself as a leader in cold slug injection molding by incorporating advanced techniques and technologies into its manufacturing processes. With a focus on precision and quality, Baoyuan ensures that its cold slug injection molding processes result in flawless plastic parts that meet even the most stringent industry standards.
With a team of experienced engineers and technicians, Baoyuan constantly explores new techniques and technologies to improve its cold slug injection molding processes. By staying at the forefront of industry advancements, Baoyuan is able to offer its clients innovative solutions that result in superior plastic parts. This commitment to innovation sets Baoyuan apart as a leader in the field of cold slug injection molding, ensuring that customers receive the highest quality products.
Quality Assurance in Injection Mold Components
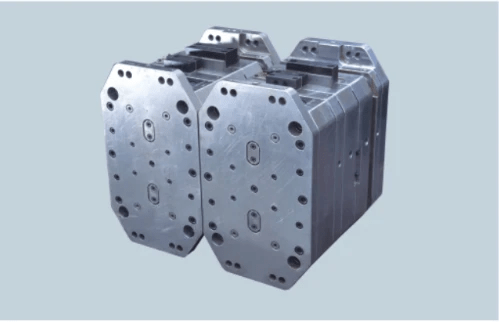
Inspection and Testing Methods
When it comes to ensuring the quality of injection mold components, thorough inspection and testing methods are essential. At Baoyuan, we employ advanced techniques such as coordinate measuring machines (CMM) and non-destructive testing to meticulously examine the parts of the mold for any defects or imperfections. Our rigorous quality control measures guarantee that every plastic injection molding part meets the highest standards of precision and durability.
In addition to using advanced techniques such as CMM and non-destructive testing, Baoyuan also implements a comprehensive visual inspection process to ensure that every detail of the injection mold components is thoroughly examined. Our team of skilled inspectors meticulously scrutinize each part for any surface imperfections or irregularities, leaving no stone unturned in our pursuit of flawless quality. This multi-faceted approach to inspection guarantees that our plastic injection molding parts not only meet but exceed industry standards for precision and durability.
Baoyuan's Proficiency in Quality Assurance
At Baoyuan, we take great pride in our proficiency in quality assurance for injection mold components. With years of experience and a team of skilled professionals, we have perfected our inspection processes to deliver flawless mold components that exceed our clients' expectations. Our commitment to excellence has earned us a reputation as a trusted leader in the injection molding industry, known for our unwavering dedication to quality.
Single-Color and Double-Color Plastic Products
In addition to ensuring the quality of individual injection mold components, Baoyuan specializes in producing single-color and double-color plastic products with impeccable precision. Whether it's intricate designs or complex geometries, our expertise allows us to create flawless plastic parts that meet the most demanding specifications. From concept to production, we offer comprehensive solutions for all your injection molding needs.
Furthermore, our state-of-the-art manufacturing facility and advanced technology enable us to produce single-color and double-color plastic products with exceptional consistency and accuracy. Our team of skilled engineers and technicians work tirelessly to ensure that every product meets the highest standards of quality and performance. With our unwavering commitment to excellence, you can trust Baoyuan to deliver superior plastic parts for your specific application.
Conclusion

When it comes to injection mold components, it's crucial to consider the precision and quality of the parts of the mold. Baoyuan plays a vital role in the injection molding industry by offering expertise in mold making, cavity design, and cold slug injection molding. Partnering with Baoyuan provides advantages such as top-notch quality assurance and proficiency in producing single-color and double-color plastic products.
Key Considerations for Injection Mold Components
The key considerations for injection mold components include precision in design, impact on final product quality, and expertise in mold opening. It's essential to prioritize these factors when choosing a partner for your injection molding needs.
It's crucial to also consider the material selection when it comes to injection mold components. The type of material used can greatly impact the durability and performance of the mold, as well as the final product. A knowledgeable partner will be able to advise on the best materials for your specific project, taking into account factors such as temperature resistance, strength, and cost-effectiveness.
Baoyuan's Role in Injection Molding Industry
Baoyuan's role in the injection molding industry is significant, as they specialize in core and cavity components, mold making process, and cold slug injection molding. Their expertise ensures that they can meet the diverse needs of clients across various industries.
Advantages of Partnering with Baoyuan
Partnering with Baoyuan offers numerous advantages, including their proficiency in quality assurance through inspection and testing methods. Additionally, their specialization in producing single-color and double-color plastic products sets them apart from other players in the industry.
Furthermore, Baoyuan's commitment to sustainability and environmental responsibility is another key advantage of partnering with them. Their use of eco-friendly materials and efficient production processes demonstrates their dedication to reducing their environmental impact, aligning with the values of many modern businesses and consumers. This focus on sustainability not only benefits the planet but also enhances the reputation of companies that choose to partner with Baoyuan.