Introduction
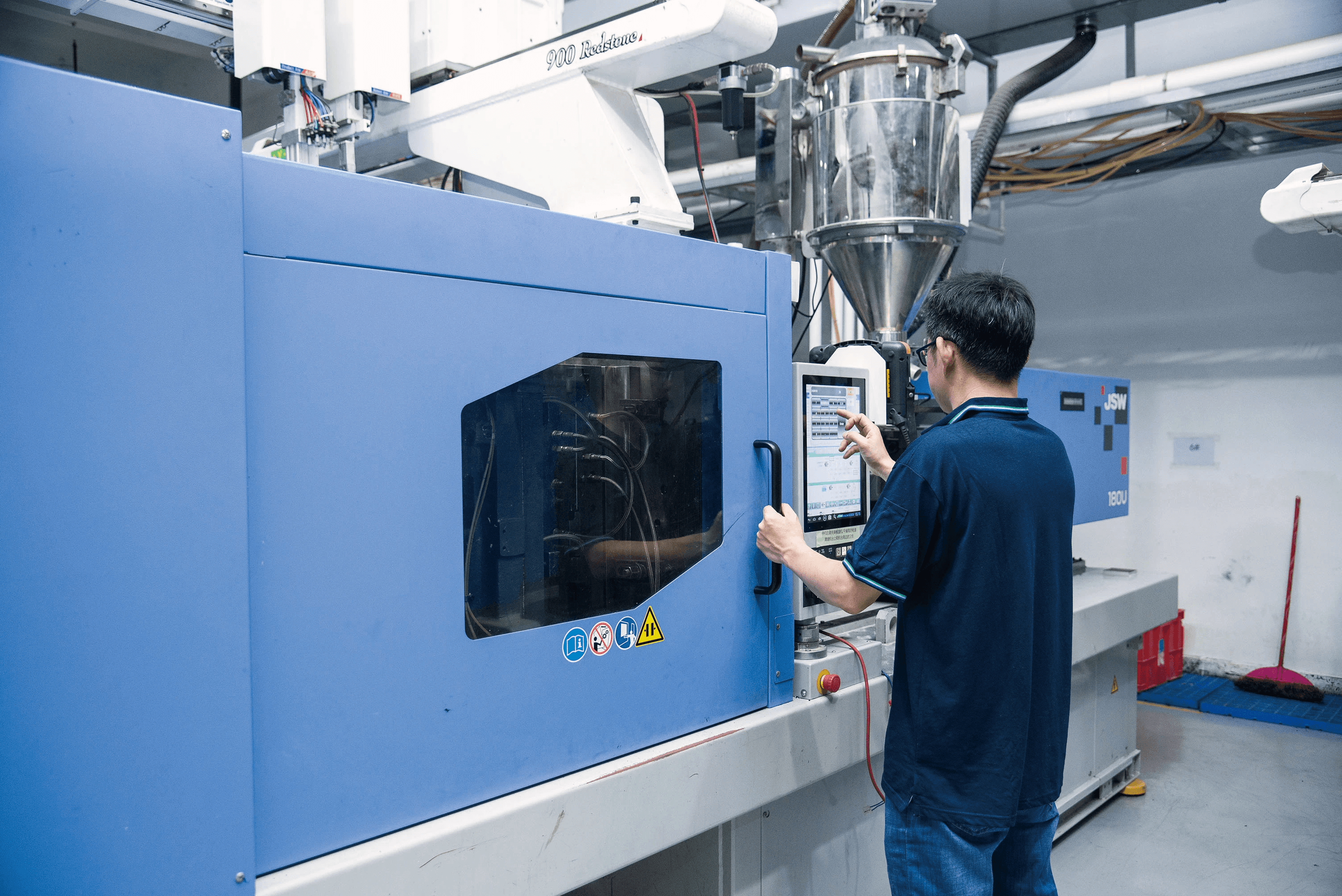
Injection molding is a widely used manufacturing process that allows for the efficient production of plastic parts. However, one common pitfall in this process is injection molding flash, which can compromise product quality and increase production costs. Understanding what flash is in injection molding, its causes, and how to prevent it is crucial for manufacturers aiming for high-quality outputs.
Understanding Injection Molding Flash
So, what is flash in injection molding? Flash refers to the unwanted excess material that seeps out of the mold cavity during the injection process, creating thin protrusions along part edges. This phenomenon typically occurs at mold parting lines or where there are gaps due to poor sealing, and it can significantly detract from the aesthetic and functional qualities of a finished product.
Importance of Preventing Flash
Preventing flash is essential not just for maintaining product integrity but also for optimizing production efficiency. Excessive flash can lead to higher scrap rates and increased labor costs associated with post-processing cleanup efforts. By addressing the root causes of injection molding flash early on, manufacturers can save time and resources while delivering superior products.
Overview of Flash and Burr Differences
While both flash and burrs are imperfections that can occur during manufacturing, they have distinct characteristics and implications. Flash typically appears as an unwanted extension of material at mold seams, while burrs are rough edges or ridges formed when material is cut or machined improperly. Understanding the difference between flash and burr not only aids in better quality control but also enhances overall manufacturing processes.
What is Flash in Injection Molding?
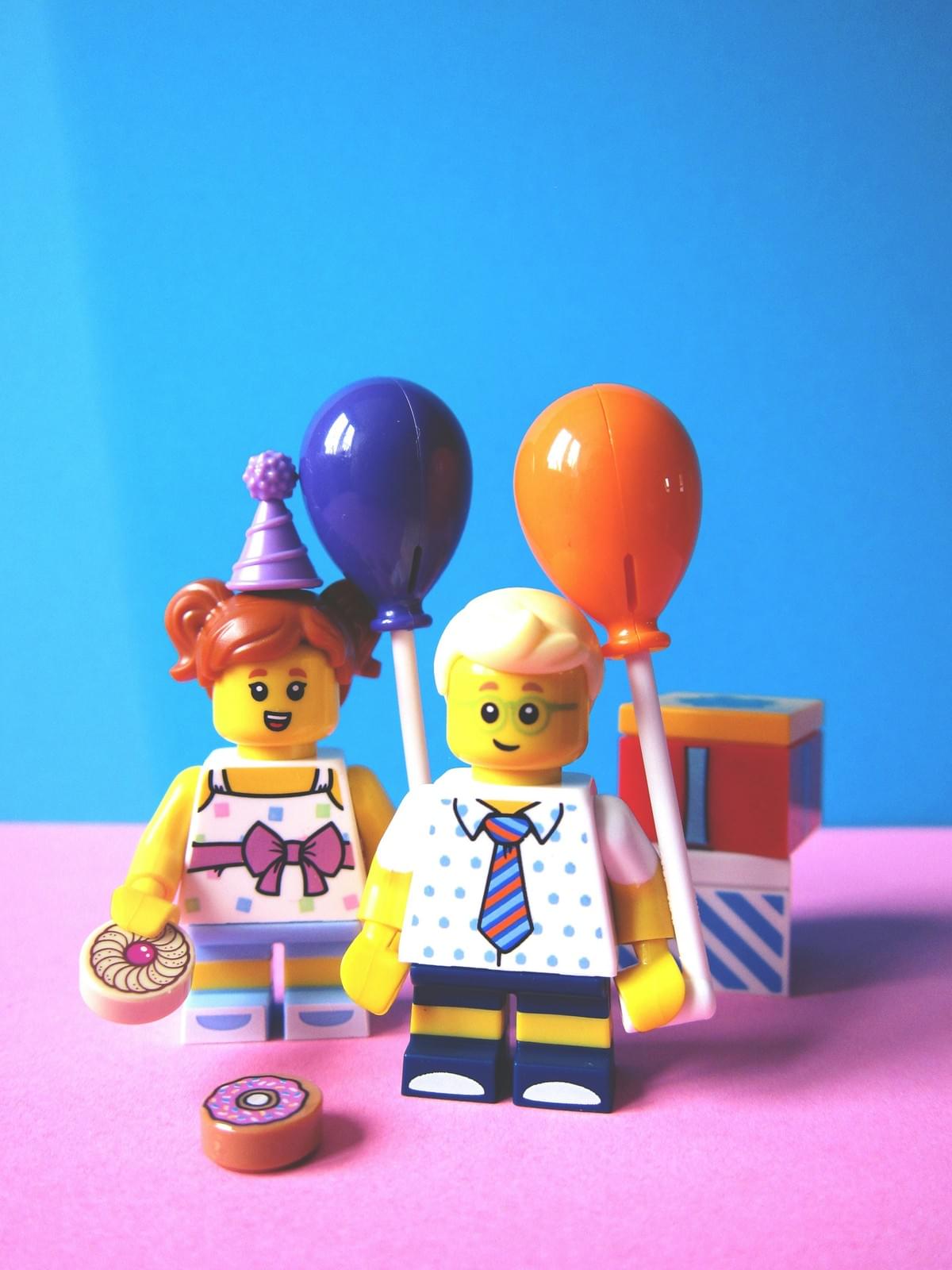
When we talk about injection molding flash, we're diving into a common yet pesky problem that can arise during the manufacturing process. Flash refers to the unwanted excess material that seeps out from the mold cavity during the injection of molten plastic or other materials. This phenomenon can occur when pressure is too high, molds are poorly designed, or even due to temperature fluctuations.
Definition and Characteristics
Flash in injection molding is characterized by thin, protruding edges of material that form along the parting line of a molded component. It often appears as an unsightly overflow, typically around corners or edges where two halves of a mold meet. This defect not only compromises the aesthetic appeal of the product but can also affect its functionality if not addressed promptly.
Common Examples in Production
In production settings, you might find injection molding flash appearing on various items like automotive parts, consumer electronics casings, and even toys. For instance, if an automotive panel has excessive flash along its edges, it may lead to difficulties during assembly or fitting with other components. These examples underscore how prevalent flash can be across different industries and products.
Impact on Product Quality
The presence of injection molding flash can significantly impact product quality by affecting both appearance and performance. Products with visible flash may be perceived as low quality by consumers, leading to dissatisfaction and potential returns. Moreover, excessive flash can interfere with assembly processes or cause functional issues down the line—making understanding what causes flash in injection molding crucial for manufacturers aiming for excellence.
What Causes Flash in Injection Molding?
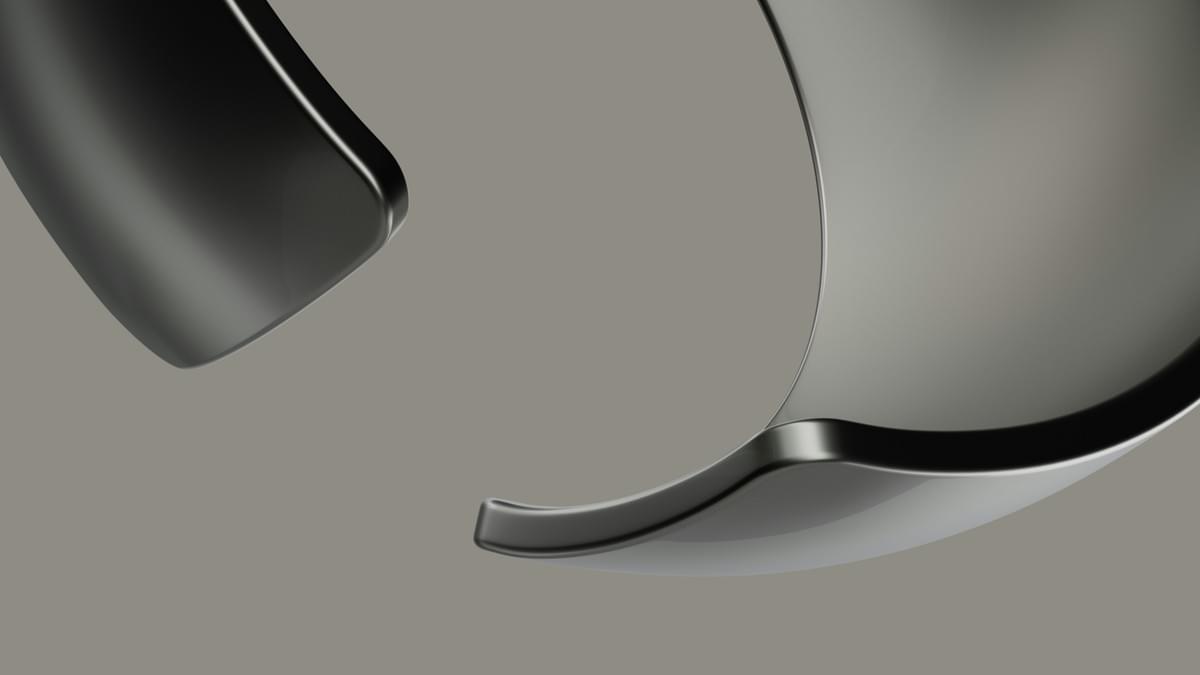
Understanding what causes injection molding flash is crucial for maintaining product quality and efficiency in manufacturing processes. Flash can occur due to a variety of factors, and identifying these causes is the first step in how to prevent flash in injection molding. By addressing these issues, manufacturers can enhance their production quality and reduce waste.
Mold Design Flaws
One of the primary culprits behind injection molding flash lies within mold design flaws. If the mold's alignment is off or if there are inadequate venting systems, excessive pressure can build up during the injection process, leading to unwanted material leakage along the parting line. This results in visible flash that not only affects aesthetics but also compromises functionality, making it essential to ensure precision in mold design.
Additionally, poor surface finish or wear on the mold can exacerbate flash issues by creating uneven surfaces that allow plastic to escape during injection. Manufacturers must regularly inspect and maintain molds to avoid these pitfalls and ensure they meet design specifications effectively. Ultimately, understanding what is flash in injection molding helps pinpoint why certain designs fail and how they can be improved.
Injection Pressure Issues
Another significant factor contributing to injection molding flash is improper injection pressure settings during production runs. High pressure may be necessary for certain materials or complex shapes; however, exceeding optimal levels can lead to excess material being forced into crevices around the mold edges. This overflow manifests as flash, negatively impacting both appearance and structural integrity.
Conversely, too low an injection pressure might not fill molds adequately, leading to incomplete parts rather than excessive flashing; however, finding a balance is key! Therefore, careful monitoring and adjustment of injection parameters are vital when considering how to prevent flash in injection molding processes effectively.
Material Selection and Temperature
The choice of materials used in conjunction with temperature settings plays a crucial role in determining whether or not you’ll encounter injection molding flash issues. Certain polymers may have higher tendencies toward expansion when heated or cooling inconsistently due to temperature fluctuations during processing could result in warping that encourages flashing at parting lines.
Choosing appropriate materials with stable thermal properties can mitigate such risks significantly while ensuring consistency across various batches produced over time! Additionally, maintaining proper temperature controls throughout the process aids manufacturers by reducing variations associated with different types of plastics—ultimately addressing concerns like what is the difference between parting line and flash?
In conclusion, being aware of what causes flash in injection molding allows manufacturers to implement effective strategies for prevention while enhancing overall production quality through informed choices regarding design flaws, pressure settings, materials used—and their respective temperatures!
How to Prevent Flash in Injection Molding?
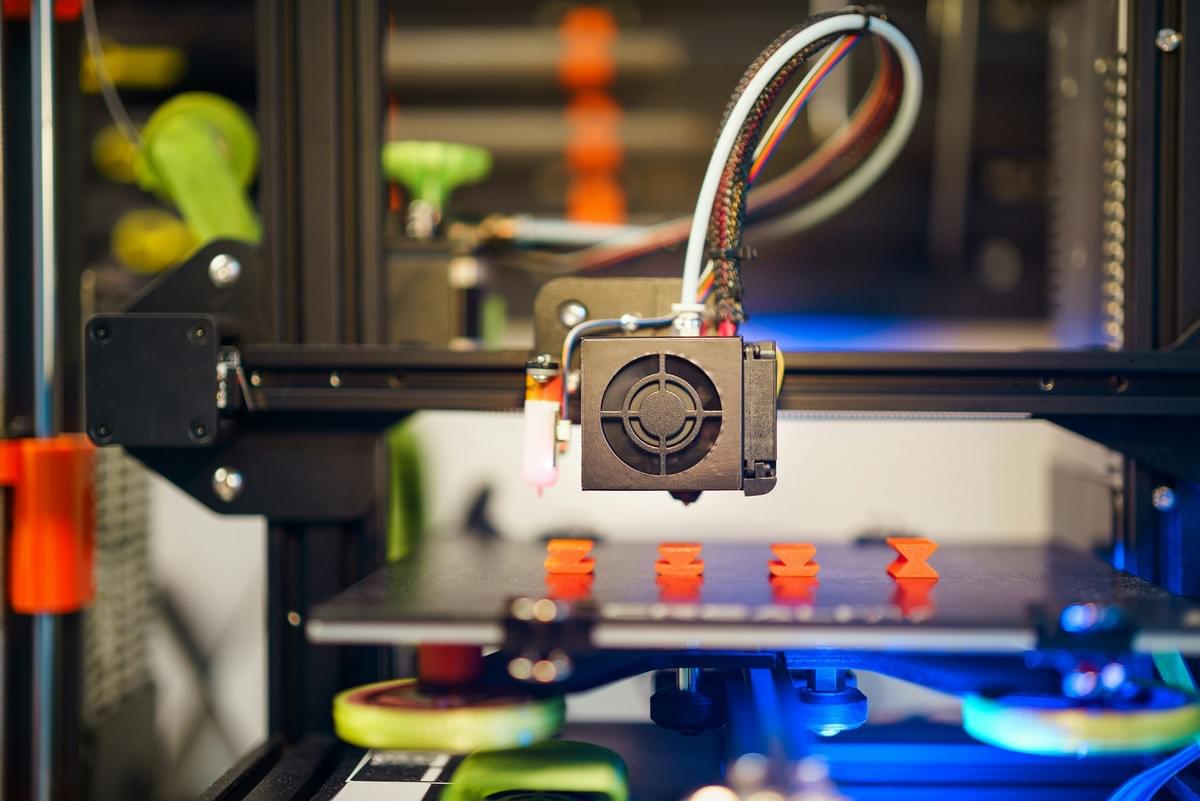
Preventing injection molding flash is crucial for maintaining product quality and reducing waste. By addressing the factors that contribute to flash, manufacturers can enhance efficiency and ensure that their products meet the required specifications. In this section, we will explore various strategies, including optimizing mold design, adjusting injection parameters, and considering material selection.
Optimizing Mold Design
The foundation of preventing injection molding flash lies in a well-engineered mold design. A properly designed mold will ensure that the material flows smoothly without excessive pressure buildup, which can lead to unwanted flash. Key considerations include ensuring adequate venting to allow trapped air to escape and designing precise parting lines to minimize any gaps where flash might occur.
Additionally, incorporating features like draft angles and fillets can further reduce the likelihood of flash by facilitating easier ejection of parts from the mold. Regularly reviewing and updating mold designs based on production feedback can also help identify potential issues before they escalate into costly problems. Remember, a proactive approach in mold design is essential for effective prevention of injection molding flash.
Adjusting Injection Parameters
Another critical aspect of preventing flash in injection molding involves fine-tuning injection parameters such as pressure, temperature, and speed. High injection pressures are often a leading cause of flash; therefore, it’s vital to find an optimal balance that allows for proper filling without excess force pushing material out at the seams. Understanding how these parameters interact can significantly impact whether or not you encounter issues with injection molding flash.
Moreover, maintaining consistent temperatures throughout the process ensures uniform material flow and reduces the chances of thermal expansion contributing to unwanted defects like flash. Regular monitoring and adjustments based on real-time data can help manufacturers stay ahead of potential problems related to injection molding flash sizes during production runs.
Material Considerations and Best Practices
Material selection plays a pivotal role in preventing what causes flash in injection molding processes. Using high-quality materials designed for specific applications helps minimize inconsistencies that could lead to defects such as burrs or flashes during production cycles. Additionally, understanding the characteristics of different polymers—such as their viscosity—can guide manufacturers toward making better choices that align with their specific requirements.
Implementing best practices like pre-drying materials before processing is another effective way to prevent moisture-related issues that could exacerbate flashing problems during manufacturing runs. Furthermore, training operators on recognizing signs of potential issues early on will enable them to take corrective actions before minor concerns turn into major setbacks involving both flashing and burrs.
What is the Difference Between Flash and Burr?
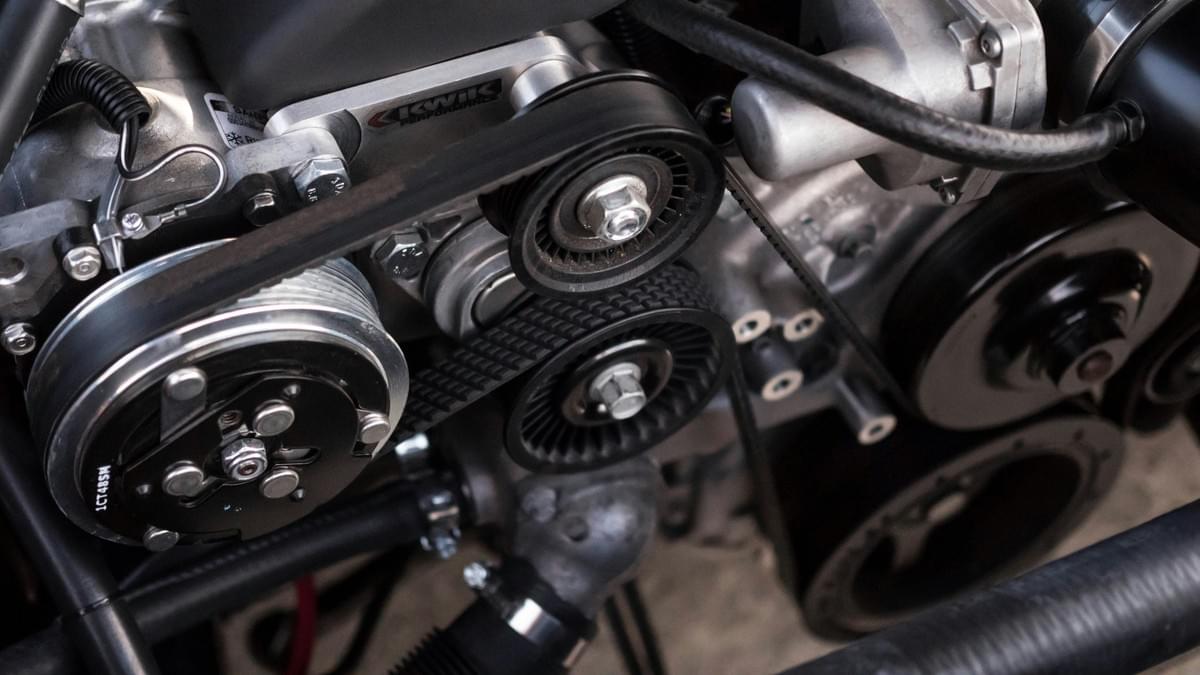
When diving into the intricacies of injection molding, understanding the difference between flash and burr is crucial. Both are imperfections that can occur during the manufacturing process, but they manifest differently and have distinct implications for product quality. Recognizing these differences can help in implementing effective strategies for quality assurance.
Definitions and Visual Differences
Flash refers to the excess material that seeps out of the mold cavity during injection molding, often appearing as thin, unwanted edges or membranes along the parting line. In contrast, a burr is a rough edge or ridge left on a part after machining or cutting processes, typically characterized by its jagged appearance. Visually, while flash tends to be more uniform and often follows the contours of the mold, burrs are irregular and can vary significantly in size.
Implications for Manufacturing
The presence of injection molding flash can compromise not only aesthetic qualities but also functional aspects of a product; it may interfere with assembly processes or lead to fitment issues in final applications. On the other hand, burrs usually necessitate additional post-processing steps like sanding or trimming to ensure parts meet specifications, which can increase production time and costs. Understanding what causes flash in injection molding—and how it differs from burrs—can guide manufacturers in optimizing their processes for efficiency.
Addressing Both Issues
To tackle both injection molding flash and burr issues effectively requires a multifaceted approach focused on prevention and correction strategies. For instance, ensuring precise mold design is key to minimizing flash occurrences while maintaining sharp cutting tools can reduce burr formation during machining operations. Additionally, implementing thorough inspection protocols allows teams to identify both problems early on—this proactive stance not only enhances product quality but also fosters continuous improvement in manufacturing practices.
What is the Difference Between Parting Line and Flash?
When diving into the world of injection molding, it’s essential to distinguish between two terms that often get confused: parting lines and flash. Understanding these concepts can save manufacturers time and money while ensuring product quality. So, let’s clarify these terms to enhance your injection molding knowledge.
Understanding Parting Lines
Parting lines are the visible seams that occur where two halves of a mold meet during the injection molding process. They are an integral part of mold design, allowing for proper alignment and closure when creating a product. While parting lines might be unavoidable, they should be designed to be as inconspicuous as possible, contributing to a smoother finish on the final product.
Distinguishing Features of Flash
On the other hand, injection molding flash refers to the unwanted excess material that seeps out from between mold halves during the injection process. Unlike parting lines, which are intentional and expected features of molded parts, flash is considered a defect that can compromise both aesthetics and functionality. Recognizing flash is crucial because it typically indicates issues such as improper mold design or excessive pressure during production—key factors in understanding what causes flash in injection molding.
Importance in Injection Molding
Understanding the difference between parting line and flash is vital for maintaining high-quality standards in manufacturing processes. While parting lines can be managed through careful design considerations, preventing injection molding flash requires ongoing attention to detail throughout production stages. By effectively addressing both issues—knowing how to prevent flash in injection molding while managing parting line visibility—manufacturers can enhance their overall efficiency and product quality.
Injection Molding Flash Sizes and Troubleshooting
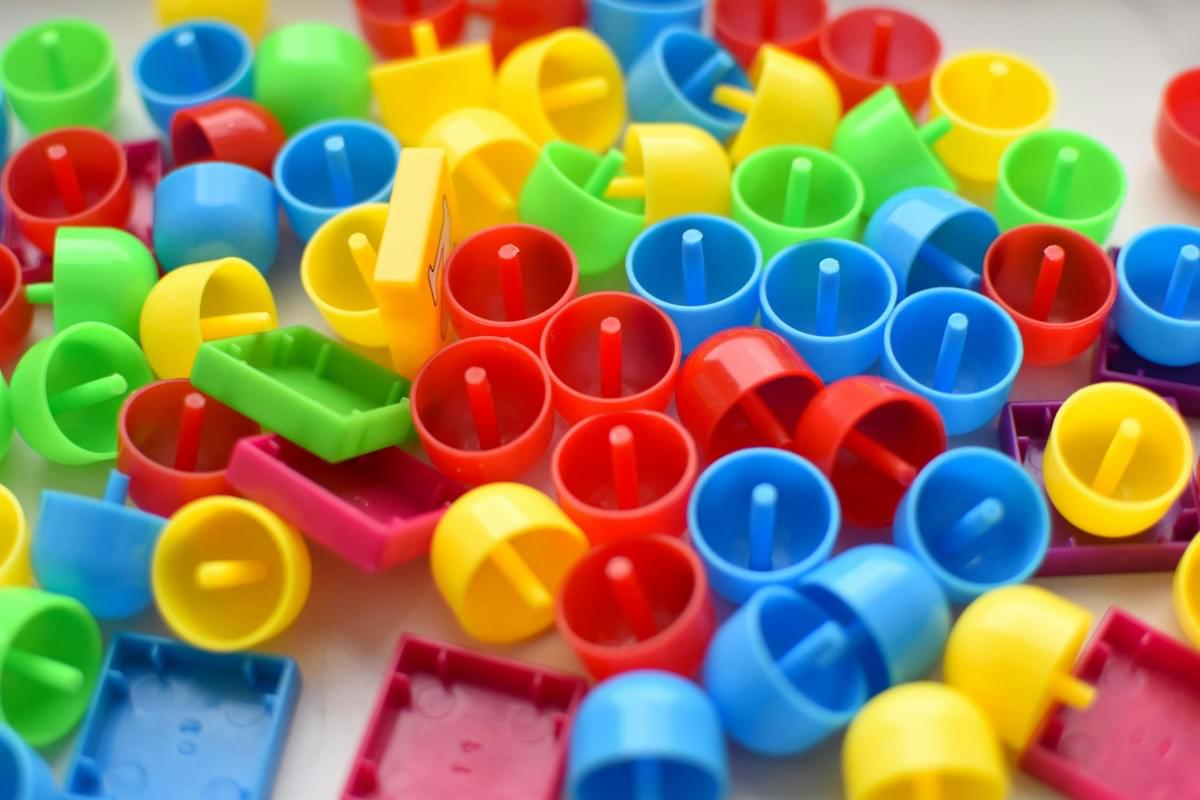
Common Flash Sizes Encountered
Injection molding flash can vary significantly in size, from tiny, barely noticeable edges to more pronounced protrusions that can affect functionality. Common sizes often range from 0.001 inches to over 0.020 inches; even small flashes can lead to problems if not addressed promptly. It's essential for manufacturers to be aware of these common flash sizes so they can implement effective measures for prevention and correction.
Troubleshooting Tips for Flash Issues
When dealing with injection molding flash, it's crucial to have a robust troubleshooting strategy in place. Start by examining the mold design; any inconsistencies or imperfections may contribute to what is flash in injection molding? Next, adjust your injection parameters such as pressure and temperature—these factors play a significant role in what causes flash in injection molding. Lastly, regularly review material selection; using the right materials can make all the difference when it comes to how to prevent flash in injection molding effectively.
Role of the Baoyuan Team in Quality Assurance
The Baoyuan team plays a pivotal role in quality assurance when it comes to managing injection molding flash issues. With their expertise, they help identify potential problems before they escalate into costly defects by conducting thorough inspections of mold designs and production processes. Their proactive approach ensures that manufacturers are equipped with strategies for effective prevention while also addressing any existing issues related to injection molding flash.
Conclusion
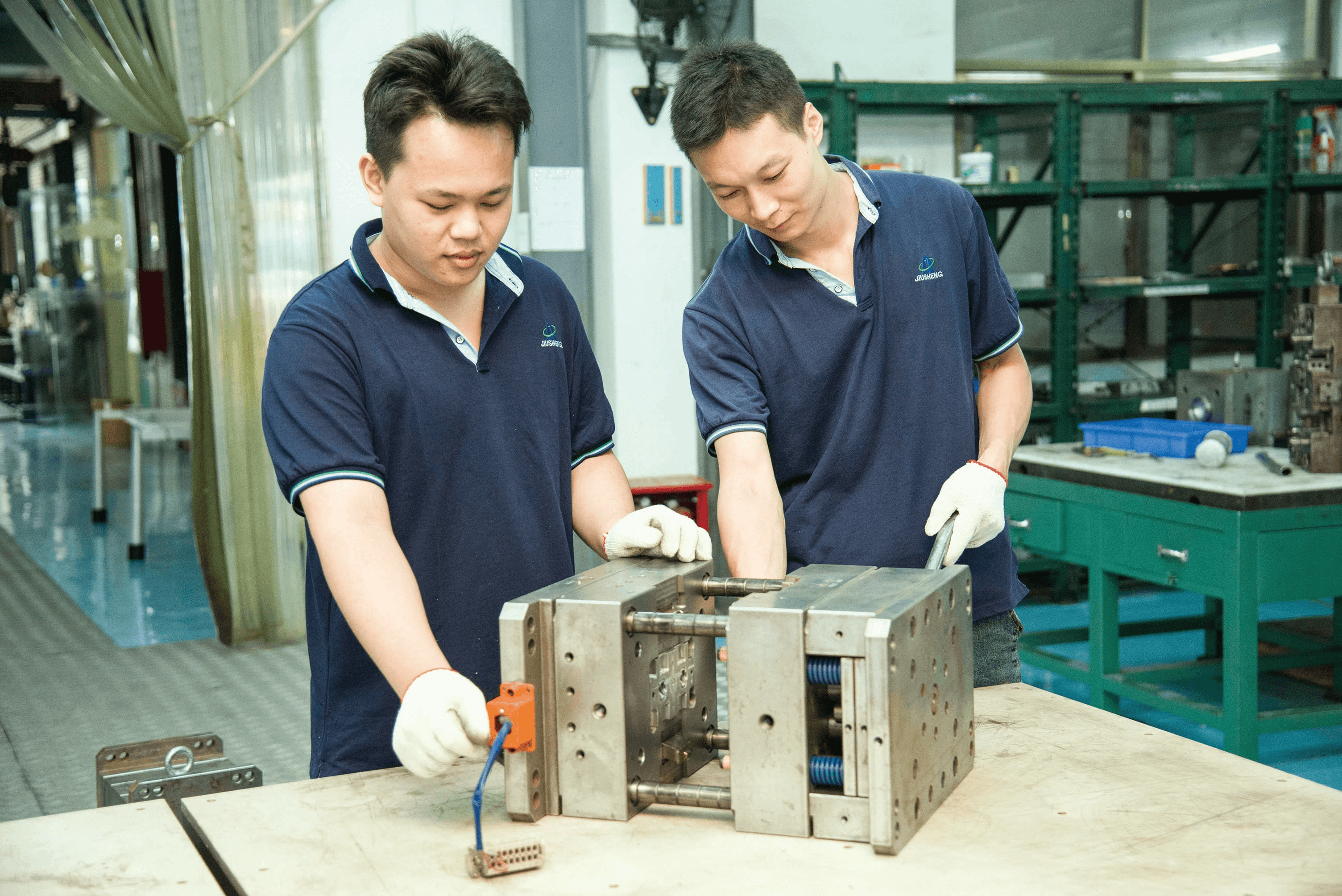
In summary, understanding injection molding flash is crucial for maintaining quality in production processes. By recognizing what flash in injection molding is and its implications for product integrity, manufacturers can take proactive steps to mitigate its occurrence. The insights gained through this discussion illuminate the importance of addressing flash effectively to enhance overall manufacturing efficiency.
Key Takeaways on Injection Molding Flash
Injection molding flash not only detracts from the aesthetic appeal of a product but can also compromise its functionality. It’s essential to grasp what causes flash in injection molding, which often stems from mold design flaws, excessive injection pressure, or improper material selection. Recognizing the differences between flash and burr is equally important, as it helps in identifying the right solutions for each issue.
Strategies for Effective Prevention
To prevent flash in injection molding, optimizing mold design is paramount; ensuring precision and proper alignment can significantly reduce risks. Adjusting injection parameters such as pressure and temperature also plays a vital role; these adjustments help maintain control over material flow during production. Additionally, careful consideration of material properties ensures compatibility with processing conditions, ultimately leading to fewer instances of injection molding flash.
Importance of Continuous Improvement in Processes
Continuous improvement in processes surrounding injection molding is essential for long-term success and quality assurance. Regularly assessing injection molding flash sizes encountered during production allows teams to identify patterns and implement corrective measures promptly. Engaging with professionals like the Baoyuan team fosters an environment where troubleshooting becomes a collaborative effort, ensuring that quality remains a top priority throughout the manufacturing lifecycle.