Introduction
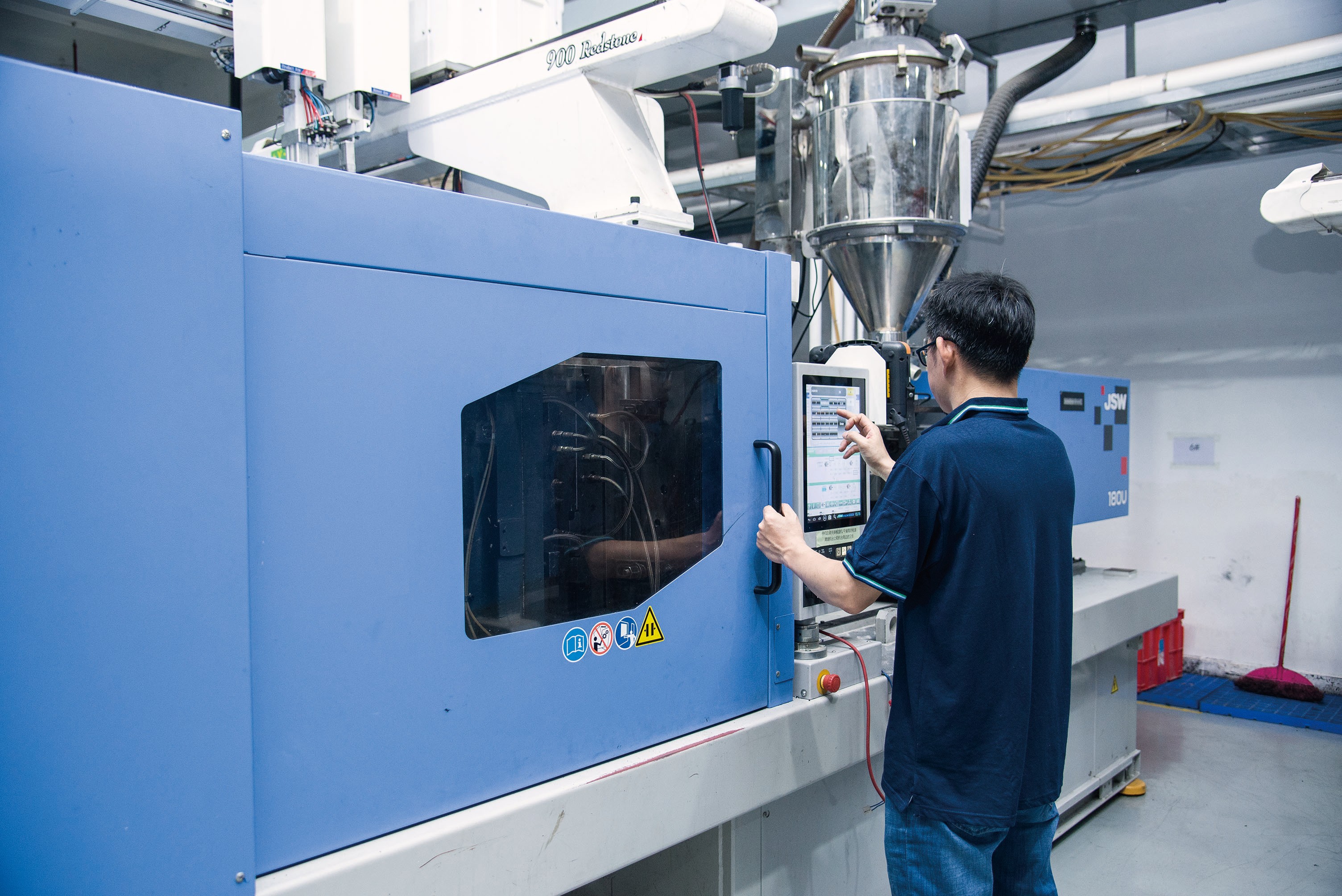
Welcome to the exciting world of injection molding, where creativity meets precision engineering to bring your ideas to life! At Baoyuan, we are experts in injection molding, utilizing cutting-edge technology and a team of skilled professionals to deliver top-notch results. Let's explore the fascinating injection molding process and its numerous benefits.
What is Injection Molding?
Injection molding is a manufacturing process that involves injecting molten material, typically plastic, into a mold cavity. This allows for the creation of complex shapes and intricate designs with high levels of accuracy and consistency. The versatility of injection molding makes it an ideal choice for producing a wide range of products, from intricate medical devices to durable automotive components.
The Baoyuan Team's Expertise
At Baoyuan, we take pride in our extensive expertise in injection molding. Our team consists of highly skilled engineers and technicians who are well-versed in the intricacies of mold design, material selection, and production processes. With years of experience, we have honed our craft to deliver exceptional results for our clients across various industries.
The Benefits of Injection Molding
Injection molding is a widely used manufacturing process that offers a variety of advantages, making it a valuable tool for businesses. Here are some of the key benefits of injection molding:
- Cost-effectiveness and high production efficiency: Once the mold is developed, injection molding can produce large volumes of parts quickly and at a relatively low cost per unit, making it ideal for high-volume production runs.
- Ability to create complex geometries and intricate details: Injection molding can make parts with very complex shapes and features, including thin walls, undercuts, and sharp corners. This allows for a high degree of design flexibility.
- Production of lightweight yet durable products: Many injection-moldable plastics are solid and durable while also being lightweight. This is beneficial in industries such as automotive and aerospace, where weight reduction is essential.
- Versatility of moldable plastics for various colors, textures, and finishes: Injection molding can use a wide range of plastics, each with its own unique properties. This allows manufacturers to choose the right material for their application and create parts with a variety of colors, textures, and finishes.
Injection molding's unique speed, precision, and versatility makes it a powerful tool for manufacturers across various industries.
The Process of Injection Molding
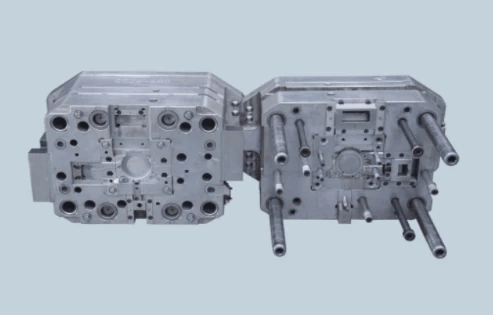
Mold Design and Creation
The first step in the injection molding process is mold design and creation. This involves creating a precise mold that will shape the plastic material into the desired final product. The mold is carefully designed to ensure that it can withstand the high pressures and temperatures involved while also producing accurate and consistent results.
Injection and Cooling Process
Once the mold is ready, the plastic injection molding process begins. The mold is filled with molten plastic resin and injected at high pressure into the cavity. After injection, the mold is cooled to solidify the plastic material into its final form. This cooling process must be carefully controlled to ensure the product retains its shape and structural integrity.
Ejection of the Final Product
After cooling, the final step in injection molding is ejecting the finished product from the mold. The mold opens, and a mechanism pushes or pulls out the solidified plastic part from inside. This ejection must be done carefully to avoid damaging or warping the product, as it's crucial for maintaining quality and consistency in production.
After the finished product is ejected, each part must be inspected to ensure that it meets the required specifications. Any defects or imperfections must be identified and addressed before the product can move on to the next stage of production. This thorough inspection process helps maintain a high standard of quality and consistency in the final output, ultimately contributing to customer satisfaction and trust in the brand.
Materials Used in Injection Molding
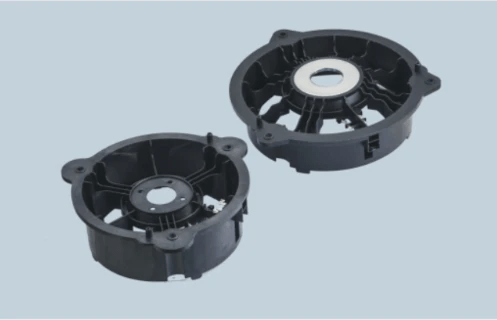
Types of Plastic Resins
When it comes to plastic injection molding, the choice of resin is crucial. Various types of plastic resin are available, each with its own unique properties and characteristics. From ABS to polypropylene, selecting the right resin is essential for achieving the desired strength, flexibility, and durability in the final product.
In addition to the base resin, additives and colorants can also significantly affect the performance and appearance of the final plastic product. Additives such as UV stabilizers, flame retardants, and impact modifiers can enhance the strength and durability of the resin, making it suitable for specific applications. Colorants add aesthetic appeal and serve practical purposes, such as identifying different parts or indicating product specifications. The careful selection and incorporation of additives and colorants can significantly enhance the overall quality of the plastic injection molded product.
Additives and Colorants
In addition to enhancing the performance and appearance of molded parts, additives, and colorants also play a crucial role in promoting recycling and sustainability in injection molding. By incorporating biodegradable additives or using colorants made from recycled materials, manufacturers can reduce the environmental impact of their products. This not only helps in minimizing waste but also contributes to a more sustainable approach to production. Furthermore, using additives that allow for easier separation of different materials during recycling can make the process more efficient and cost-effective.
Recycling and Sustainability
Insight molding is no exception, as sustainability becomes increasingly important in manufacturing processes. Many companies now use recycled materials in their injection molding processes to minimize environmental impact. Manufacturers can reduce waste by incorporating recycled plastics into production while maintaining high-quality products that meet industry standards.
Recycling and Sustainability
In addition to the efficient production process, injection molding contributes to sustainability through using recycled materials and the ability to create products that are easily recyclable. The Baoyuan team is committed to using eco-friendly plastic resins and implementing recycling practices in their manufacturing process. By utilizing recycled materials and designing products with end-of-life recycling in mind, injection molding plays a crucial role in reducing waste and promoting a more sustainable approach to manufacturing. With the increasing focus on environmental responsibility, injection molding has become an essential part of creating high-quality and environmentally friendly products.
Applications of Injection Molding
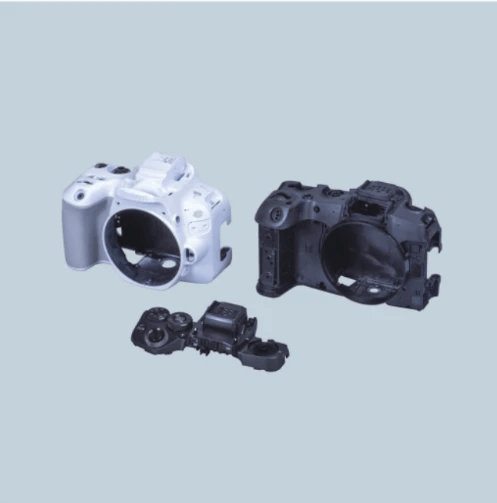
Injection molding plays a crucial role in the automotive industry, creating various components such as dashboards, bumpers, and interior trims. The process allows for the production of complex shapes and designs that are both durable and lightweight, making it an ideal choice for automotive manufacturers looking to enhance performance and efficiency.
Automotive Industry
The versatility of plastic injection molding makes it the go-to method for producing a wide range of consumer products. From kitchenware and electronic devices to toys and packaging materials, injection molding enables manufacturers to create large-scale, cost-effective products. This method also allows for customization, ensuring that consumer demands for unique designs and functionalities are easily met.
The automotive industry also benefits significantly from plastic injection molding. This method produces intricate and durable components such as dashboards, bumpers, and interior trims. With the ability to create complex shapes and designs, injection molding provides automotive manufacturers with the flexibility to meet the ever-changing demands of consumers. Additionally, the cost-effectiveness of this manufacturing process enables car makers to produce high-quality parts at a competitive price, ultimately benefiting both the industry and consumers.
Consumer Products
In medicine, injection molding is utilized to manufacture intricate components such as syringes, vials, and surgical instruments. The ability to produce precise and sterile medical devices using moldable plastics makes injection molding indispensable in the healthcare industry. Its efficiency in mass production also contributes to meeting the high demand for medical supplies worldwide.
Injection molding is not limited to the medical field; it is also widely used in the production of consumer products. From plastic toys and kitchen utensils to electronic components and household items, injection molding is crucial in manufacturing a wide range of everyday products. Its ability to create complex shapes and designs with high precision makes it a cost-effective and efficient method for producing consumer goods.
Medical Devices
Baoyuan is a leader in injection molding, a technique used to create high-quality plastic parts. They achieve this through a commitment to several key factors:
- Consistent Quality: Using injection molding, Baoyuan guarantees consistent product quality across every manufactured item.
- Diverse Applications: Injection molding allows Baoyuan to cater to a broad spectrum of industries, ensuring they can meet the needs of various clients.
- Sustainable Practices: Baoyuan prioritizes eco-friendly practices and continuously seeks advancements in injection molding to minimize environmental impact.
Baoyuan's dedication to quality, versatility, and sustainability in injection molding makes it a reliable partner for businesses across numerous industries.
Quality Assurance in Injection Molding
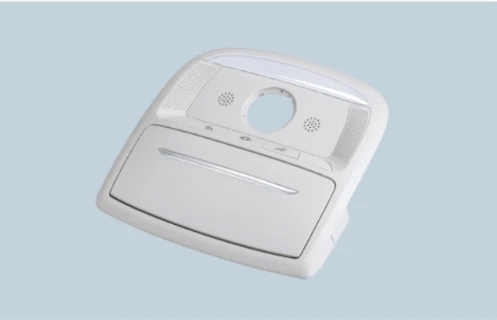
When it comes to ensuring top-notch quality in injection molding, the Baoyuan team employs advanced techniques that set them apart from the competition. With their extensive experience and expertise, they use cutting-edge technology to achieve precision and consistency in every product.
Baoyuan Team's Advanced Techniques
The Baoyuan team utilizes state-of-the-art machinery and software to optimize the injection molding process. From computer-aided design (CAD) for mold creation to sophisticated injection machines, they leave no stone unturned in their quest for perfection. Their commitment to staying ahead of the curve ensures that clients receive products of the highest quality.
The Baoyuan team also employs rigorous inspection and testing methods to ensure the quality of their products. They utilize advanced equipment and technology to conduct thorough checks on every batch of molded products, leaving no room for error. Adhering to strict quality control measures guarantees that clients receive flawless and reliable products that meet their exact specifications.
Inspection and Testing Methods
Ensuring exceptional quality is paramount for Baoyuan. Here's how they achieve this:
- Multi-stage Inspections: Baoyuan implements rigorous checks throughout the production process, from raw materials to finished products.
- Close Monitoring: They watchfully monitor the injection process, ensuring precision and consistency.
- Comprehensive Testing: Every finished product undergoes thorough testing to guarantee it meets their high standards.
- Continuous Improvement: Baoyuan doesn't settle. They regularly update their protocols to leverage the latest advancements in quality control.
By following these meticulous steps, Baoyuan ensures that only the best products reach its customers. Its unwavering commitment to quality control reflects its dedication to exceeding customer expectations.
Ensuring Consistency and Precision
Consistency is vital in injection molding; the Baoyuan team understands this better. By adhering to strict quality control measures, they ensure that each item meets exact specifications without fail. Their unwavering dedication to precision sets them apart as leaders in the industry.
The Baoyuan team's commitment to consistency and precision extends beyond meeting specifications. They also prioritize using high-quality materials and cutting-edge technology to ensure every product is of the highest standard. This dedication to excellence sets them apart as industry leaders and gives their clients peace of mind, knowing that they are receiving top-notch products.
Conclusion
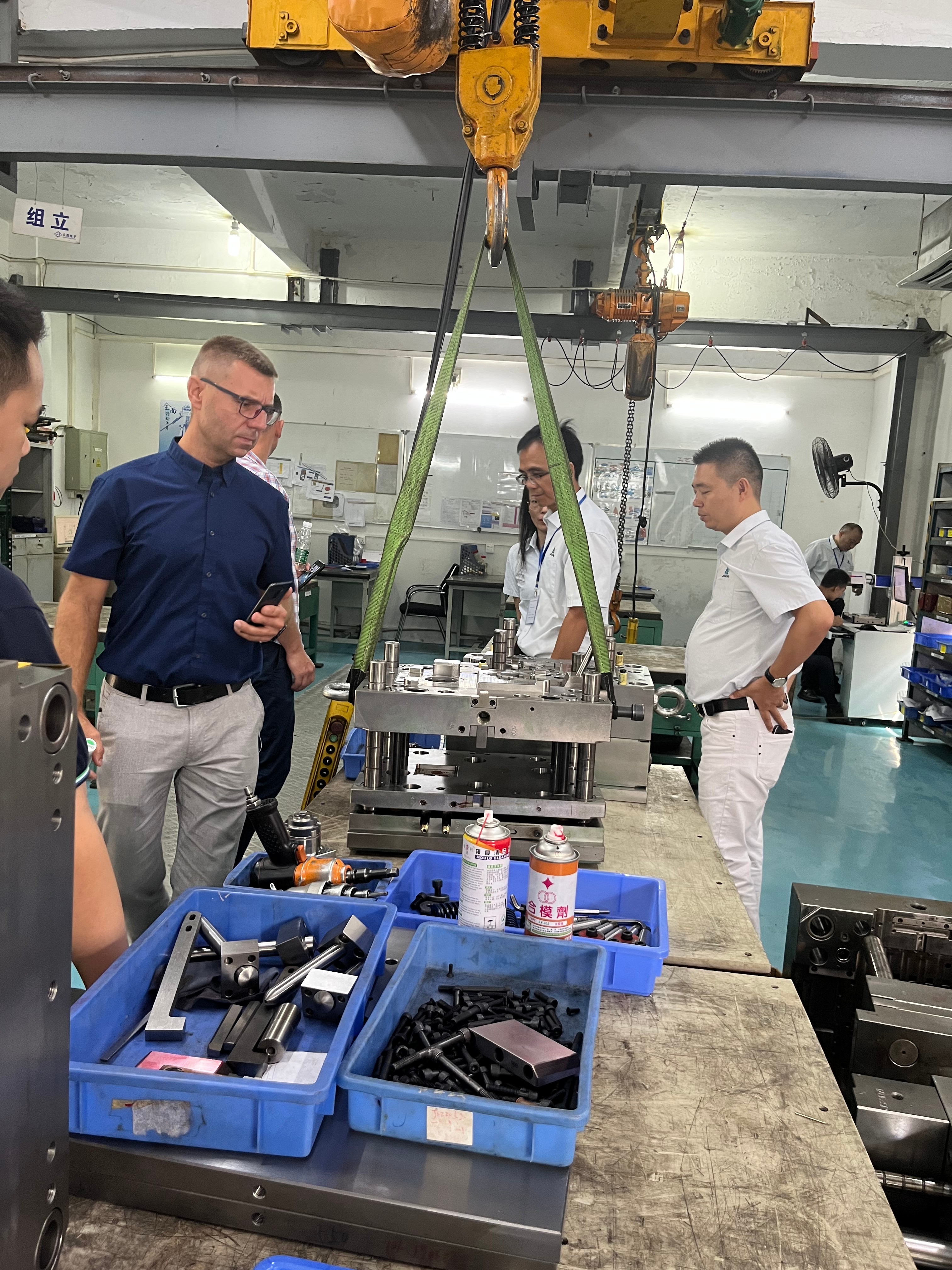
Over the years, injection molding has evolved with technological advancements, leading to innovations in mold design, material selection, and production processes. These innovations have allowed for more complex and intricate designs and improved manufacturing efficiency and cost-effectiveness.
At Baoyuan, we pride ourselves on delivering high-quality injection molding solutions. Our team of experts is committed to staying ahead of the curve by continuously improving our techniques and embracing new technologies. We strive for excellence in every aspect of our work, from mold design to final product inspection.
As technology continues to advance, the future of injection molding looks promising. With the development of new materials and processes, we can expect even greater precision, sustainability, and customization capabilities in injection molding. The industry is poised for further growth and innovation in the coming years.
From 3D printing molds to advanced simulation software, the world of injection molding is constantly evolving. These innovations enable greater design flexibility and faster production cycles while maintaining high-quality standards.
At Baoyuan, we go above and beyond to ensure that every project meets our clients' expectations. Our attention to detail and dedication to continuous improvement set us apart as a leader in the industry.
With advancements in automation and robotics, as well as sustainable material options, the future of injection molding holds exciting possibilities for more efficient and environmentally friendly manufacturing processes.