Introduction
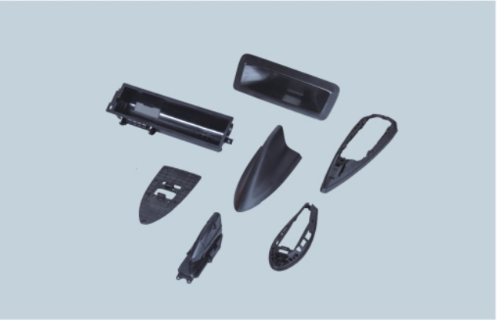
Plastic moulded components play a crucial role in various industries, including automotive, electronics, and consumer goods. These components are created through plastic moulding processes, which involve shaping molten plastic into a specific form. The importance of high-quality plastic moulded components cannot be overstated, especially in the automotive industry where performance and safety are paramount.
Understanding Plastic Moulded Components
Plastic moulded products are items made from shaping molten plastic into a specific form using a mould. These components are used in a wide range of applications due to their versatility and durability. They can be found in everyday items such as car parts, electronic devices, and household appliances.
Plastic moulded products are items made from shaping molten plastic into a specific form using a mould. These components are used in a wide range of applications due to their versatility and durability. They can be found in everyday items such as car parts, electronic devices, and household appliances.
Types of Plastic Moulding Processes
Moulded components are created through various plastic moulding processes such as injection moulding, compression moulding, and transfer moulding. Each process has its unique advantages and is suitable for different types of products based on factors like complexity, size, and material. Injection moulding, for example, is ideal for producing high volumes of small to medium-sized components with intricate details. On the other hand, compression moulding is best suited for larger parts with lower production volumes, while transfer moulding offers a good balance between the two processes, making it suitable for medium to large-sized components with moderate production quantities.
Importance of High-Quality Components in Automotive Industry
In the automotive industry, high-quality plastic moulded components are essential for ensuring vehicle performance, safety, and longevity. From interior trim pieces to under-the-hood parts, these components contribute to the overall reliability and efficiency of modern vehicles.
High-quality plastic moulded components not only enhance the aesthetic appeal of vehicles but also contribute to their overall functionality. With advancements in materials and manufacturing processes, these components are now lighter, stronger, and more durable than ever before. As a result, they play a crucial role in improving fuel efficiency and reducing emissions, making them an indispensable part of the automotive industry's efforts to create more sustainable transportation solutions.
Baoyuan: A Leader in Plastic Moulding
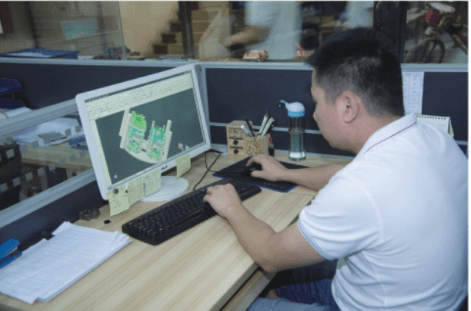
Baoyuan has established itself as a leader in plastic moulding, specializing in the production of high-quality plastic moulded components for various industries, including automotive. With a team of experienced senior management professionals, Baoyuan ensures that every aspect of the manufacturing process is handled with expertise and precision.
Baoyuan's Expert Senior Management Team
The expert senior management team at Baoyuan brings years of industry experience and knowledge to the table, ensuring that all aspects of plastic moulding are handled with utmost care and attention to detail. Their leadership and strategic guidance have been instrumental in establishing Baoyuan as a trusted provider of top-notch plastic moulded components for automotive applications.
The team's expertise extends to the use of advanced software for mould design and injection molding, allowing Baoyuan to stay at the forefront of technological innovation in the industry. By leveraging cutting-edge tools and techniques, the senior management team ensures that every product meets the highest standards of quality and precision. This commitment to staying ahead of the curve has solidified Baoyuan's reputation as a leader in delivering innovative plastic moulded components.
Advanced Software for Mould Design and Injection Molding
Baoyuan utilizes advanced software for mould design and injection molding, allowing for precise and efficient production processes. This cutting-edge technology enables Baoyuan to create intricate and complex designs with ease, ensuring that the resulting plastic moulded components meet the highest standards of quality and performance.
Furthermore, Baoyuan's use of advanced software for mould design and injection molding also allows for greater customization and flexibility in product development. This means that clients can request specific features or modifications to their plastic moulded components, and Baoyuan can easily accommodate these requests without sacrificing quality or efficiency. As a result, Baoyuan is able to provide tailored solutions that meet the unique needs of each client, setting them apart as a leader in the industry.
Quality Assurance for Single and Double-Color Plastic Products
Baoyuan places a strong emphasis on quality assurance for both single and double-color plastic products. Through rigorous testing procedures and meticulous attention to detail, Baoyuan ensures that every plastic moulded component meets or exceeds industry standards, providing customers with reliable and durable solutions for their automotive needs.
With an expert senior management team leading the way, advanced software for precise design and injection molding processes, as well as unwavering commitment to quality assurance, Baoyuan is truly a leader in the production of high-quality plastic moulded components for the automotive industry.
The Role of Plastic Moulded Components in Automotive Innovation
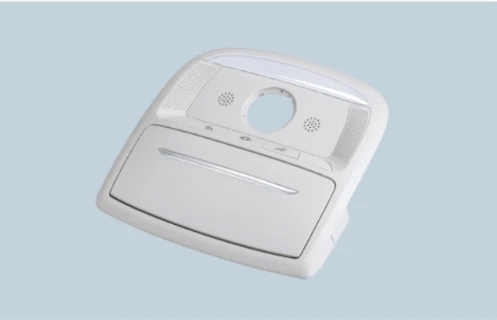
Enhancing Vehicle Performance with High-Quality Components
Plastic moulded components play a crucial role in enhancing vehicle performance by providing lightweight, durable, and high-strength solutions for automotive applications. These components are designed to withstand the rigors of daily use while contributing to improved fuel efficiency and overall vehicle dynamics.
Contribution to Lightweighting and Fuel Efficiency
One of the key benefits of plastic moulded components is their contribution to lightweighting, which is essential for improving fuel efficiency and reducing carbon emissions in modern vehicles. By replacing traditional metal parts with lightweight plastic alternatives, automotive manufacturers can achieve significant weight savings without compromising on strength or durability.
Meeting Industry Standards and Regulations
Plastic moulded components must meet stringent industry standards and regulations to ensure the safety and reliability of automotive vehicles. From impact resistance to temperature tolerance, these components are designed and tested to comply with various regulations, including those related to material composition, performance characteristics, and overall quality.
Exploring Different Types of Plastic Moulding
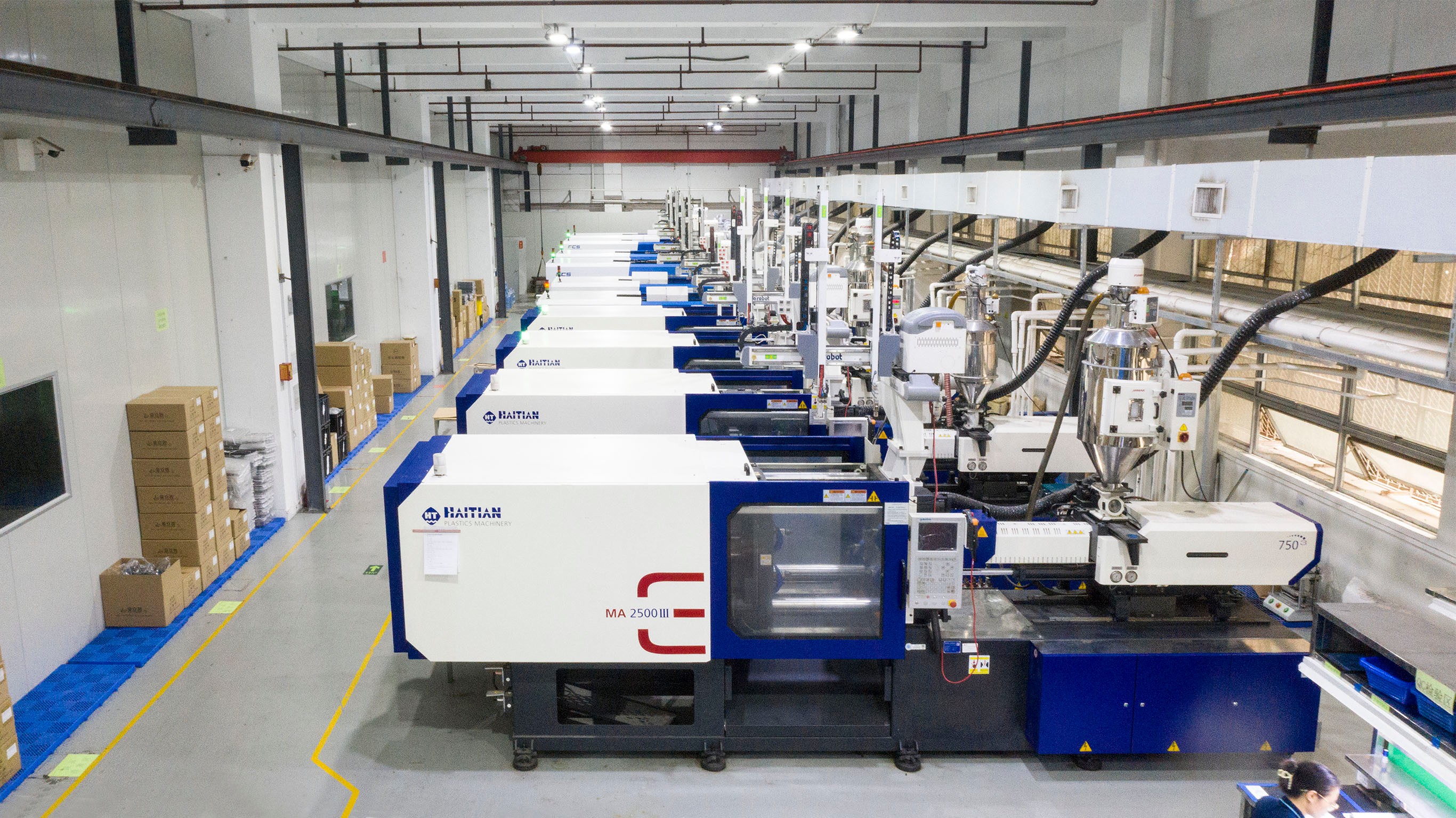
When it comes to plastic moulded components, understanding the various types of plastic moulding processes is crucial. Injection molding is a widely used method for producing plastic components, involving the use of an injection mold to create intricate shapes and designs. Compression molding, on the other hand, is ideal for automotive applications due to its ability to produce high-strength components. Lastly, transfer molding offers benefits such as reduced material waste and shorter production cycles, making it a cost-effective option for manufacturing plastic components.
Injection Molding: Components and Process
Injection molding involves the use of a mold cavity into which molten material is injected at high pressure to create complex shapes and designs. The process consists of several key components including the injection unit, clamping unit, and mold base. The molten material is forced into the mold cavity where it cools and solidifies before being ejected as a finished product. This method allows for high precision and repeatability in producing plastic moulded components.
Compression Molding for Automotive Applications
Compression molding is well-suited for automotive applications due to its ability to produce high-strength components with excellent dimensional stability. This process involves placing a pre-measured amount of material into an open mold cavity before closing it under heat and pressure. The material then spreads and takes the shape of the mold, resulting in strong and durable plastic components that meet automotive industry standards.
Understanding the Benefits of Transfer Molding
Transfer molding offers several advantages when it comes to producing plastic moulded components for automotive applications. This process allows for reduced material waste as excess material can be recycled, making it an environmentally friendly option. Additionally, transfer molding enables shorter production cycles and lower production costs compared to other methods, making it an efficient choice for manufacturing high-quality plastic components.
Remember that understanding the different types of plastic moulding processes is essential in choosing the right method for producing high-quality plastic moulded components in automotive applications!
Materials for High-Quality Plastic Moulded Components
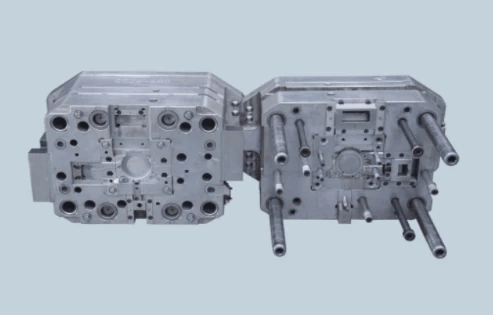
Plastic moulded components are manufactured using a variety of materials to ensure optimal performance and durability. The material selection plays a crucial role in determining the overall quality and functionality of the components.
Impact of Material Selection on Component Performance
The choice of material for plastic moulded components has a direct impact on their performance in automotive applications. Factors such as strength, flexibility, and resistance to heat and chemicals are carefully considered to ensure that the components meet industry standards for safety and reliability.
Advantages of Using Thermoplastics in Automotive Applications
Thermoplastics are commonly used in the production of plastic moulded components for automotive applications due to their versatility and cost-effectiveness. These materials can be easily molded into complex shapes, offering design flexibility while maintaining high strength and impact resistance.
Balancing Strength and Weight in Component Design
One of the key considerations in material selection for plastic moulded components is achieving a balance between strength and weight. Lightweight materials such as reinforced thermoplastics are preferred to reduce overall vehicle weight, contributing to improved fuel efficiency without compromising on performance or safety.
By carefully selecting materials such as thermoplastics for plastic moulded components, automotive manufacturers can ensure that their products meet stringent industry standards while optimizing performance and efficiency.
Quality Assurance and Testing for Plastic Moulded Components
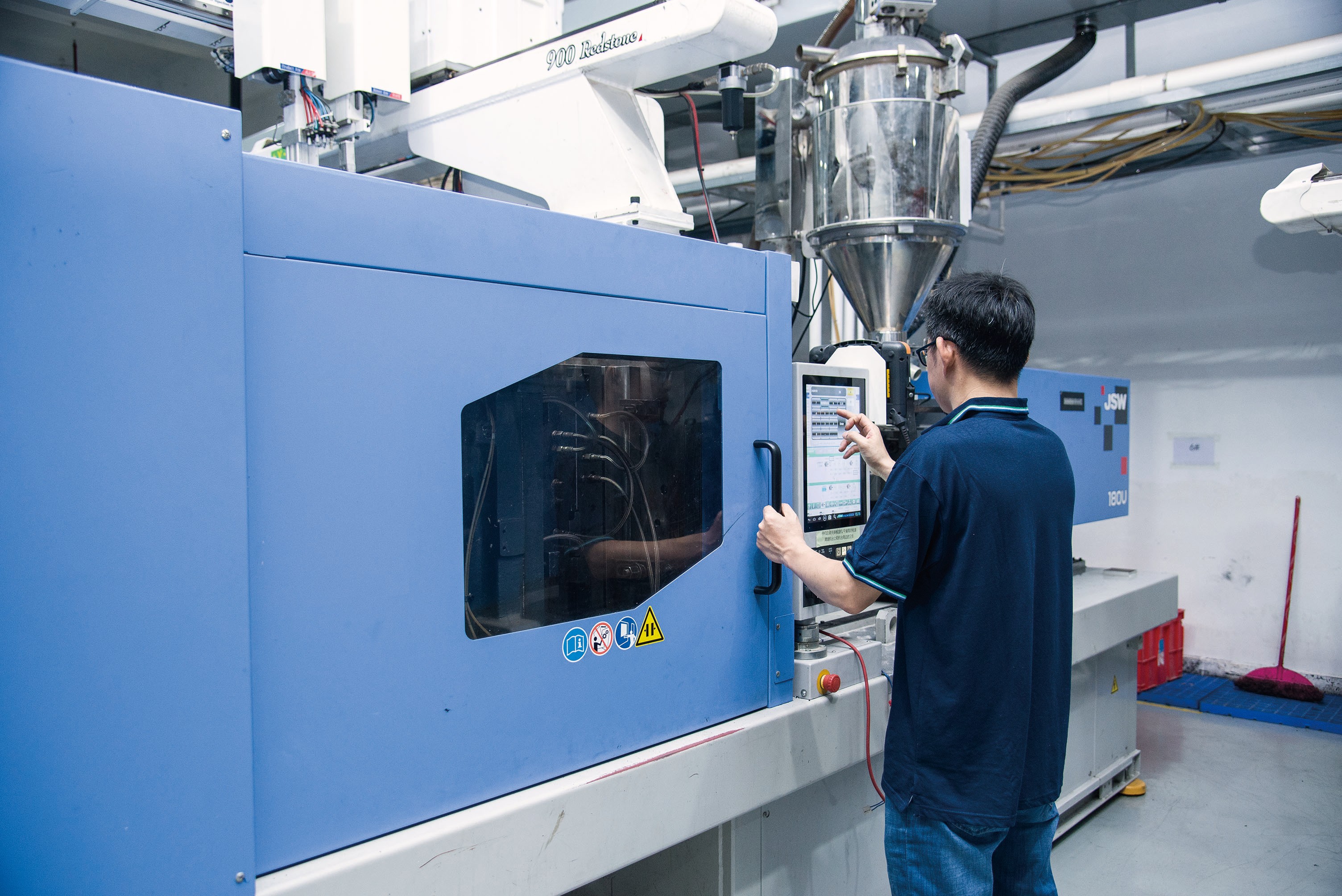
Importance of Rigorous Testing in Automotive Industry
In the automotive industry, the performance and safety of plastic moulded components are crucial. Rigorous testing is essential to ensure that these components can withstand the demands of vehicle operation and provide long-lasting reliability. From impact resistance to temperature tolerance, thorough testing guarantees that the components meet industry standards and regulations.
Baoyuan's Commitment to Quality Assurance
Baoyuan understands the significance of quality assurance in plastic moulding. With state-of-the-art testing facilities and a dedicated team, Baoyuan ensures that every component undergoes comprehensive testing to validate its durability, performance, and adherence to specifications. This commitment to quality assurance sets Baoyuan apart as a trusted partner for high-quality plastic moulded components in the automotive industry.
Meeting the Durability and Performance Standards
As vehicles continue to evolve with advanced technology and design, plastic moulded components must keep pace with increasing demands for durability and performance. Baoyuan's rigorous testing protocols guarantee that each component meets or exceeds industry standards for strength, resilience, and longevity. By consistently meeting these standards, Baoyuan contributes to advancing automotive innovation through reliable plastic moulded products.
Conclusion
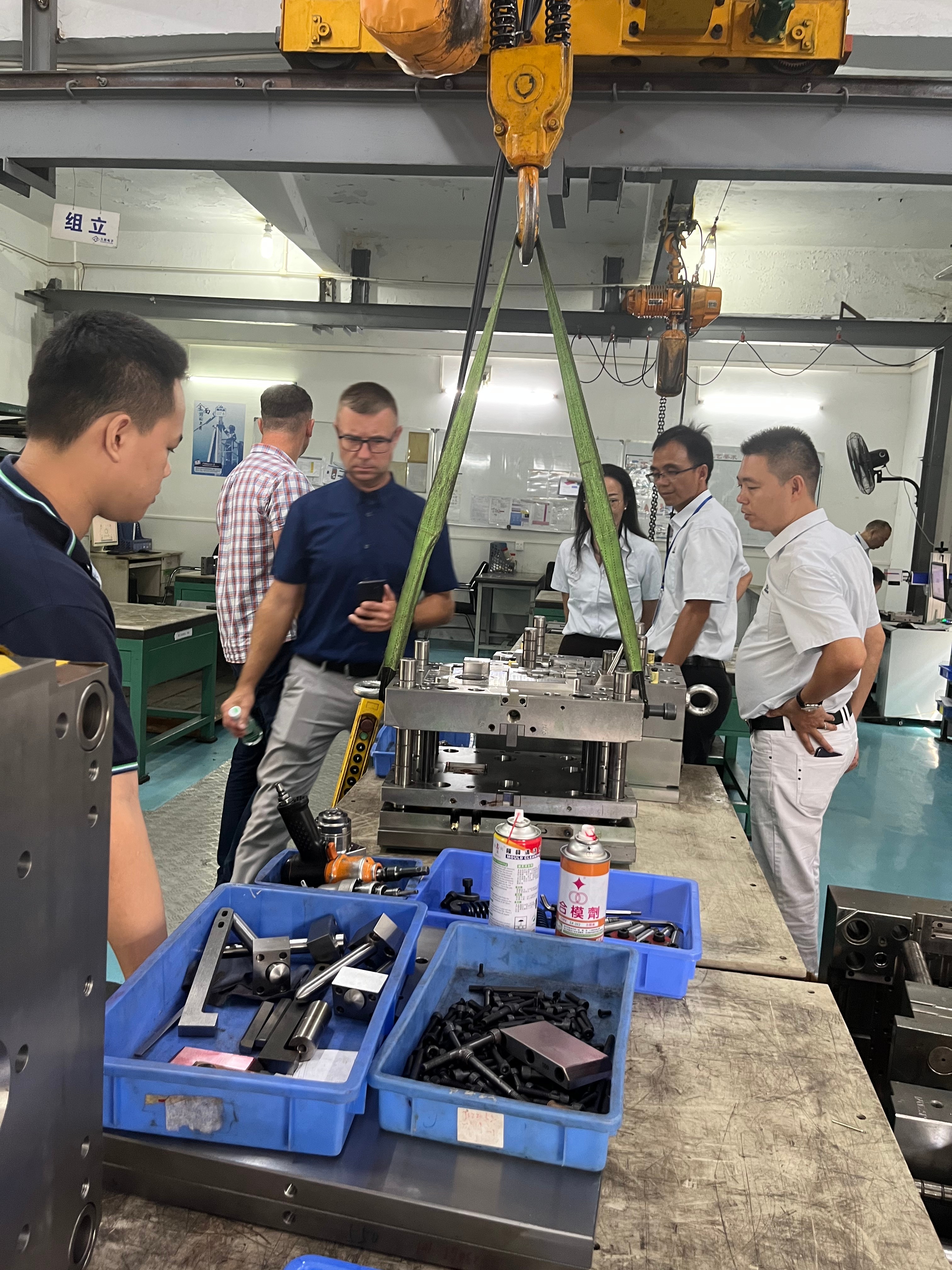
Plastic moulded components play a crucial role in the automotive industry, providing high-quality and durable solutions for vehicle performance and innovation. Baoyuan stands out as a reliable partner, offering expertise in mould design, advanced software for injection molding, and rigorous quality assurance. With a commitment to advancing the automotive industry with quality plastic components, Baoyuan is at the forefront of driving innovation and efficiency.
The Impact of High-Quality Plastic Moulded Components
High-quality plastic moulded components have a significant impact on vehicle performance and innovation in the automotive industry. These components enhance durability, fuel efficiency, and overall lightweighting of vehicles, contributing to advancements in automotive technology.
Baoyuan: A Reliable Partner for Automotive Moulded Components
Baoyuan's expertise in plastic moulding makes them a reliable partner for automotive moulded components. Their expert senior management team and advanced software for mould design and injection molding ensure top-notch quality products that meet industry standards and regulations.
Advancing Automotive Industry with Quality Plastic Components
With a commitment to providing high-quality plastic components, Baoyuan is dedicated to advancing the automotive industry through innovation and efficiency. Their focus on material selection, rigorous testing, and meeting durability standards sets them apart as a leader in the production of plastic moulded components.