Introduction
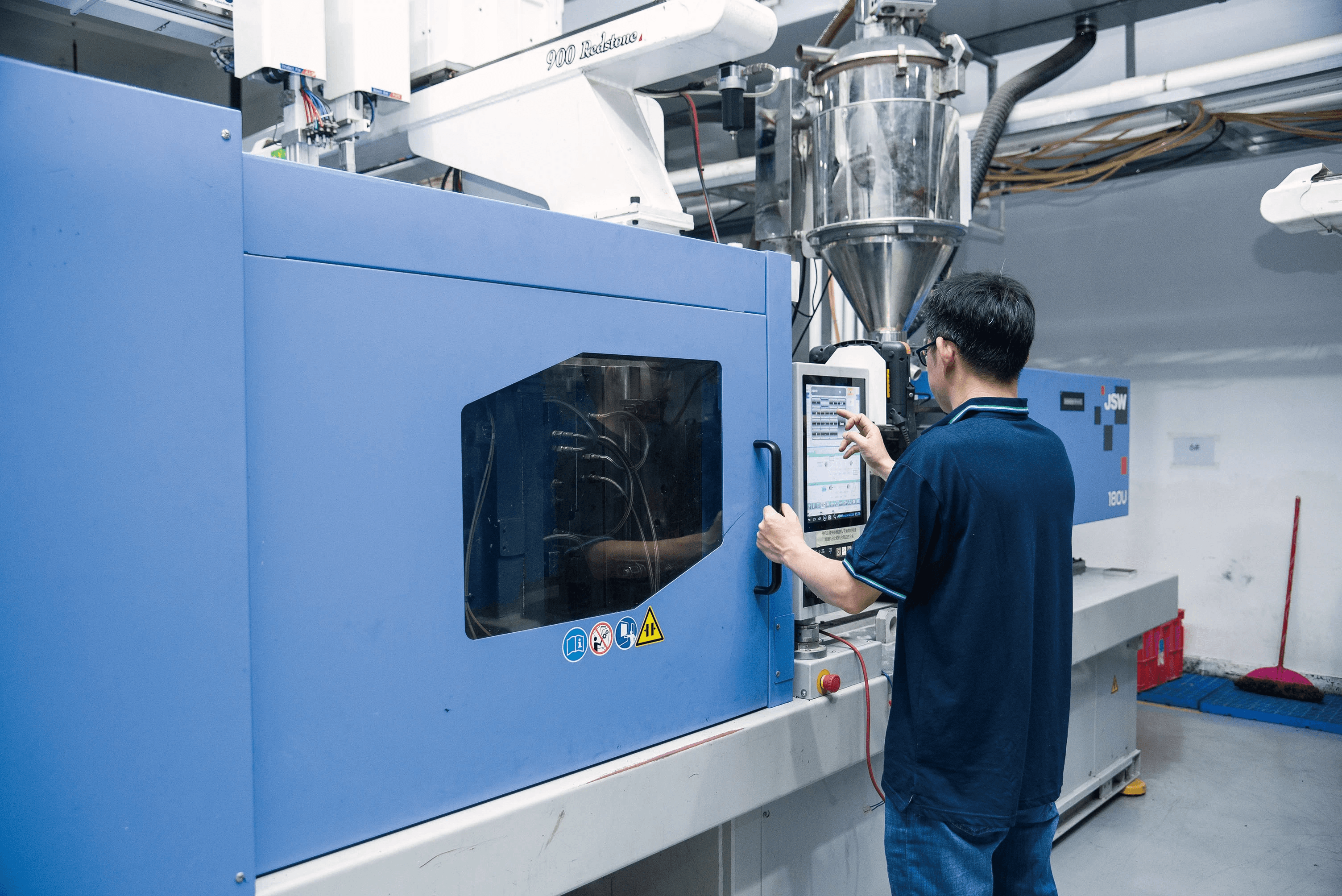
In the world of manufacturing, high precision plastic injection molding stands out as a key player, driving efficiency and innovation across various sectors. This advanced process allows for the creation of intricate designs with remarkable accuracy, making it an essential technique in producing everything from automotive parts to consumer electronics. As industries continue to evolve, understanding the nuances of plastic injection molding services becomes increasingly important for businesses looking to maintain a competitive edge.
Understanding High Precision Plastic Injection Molding
High precision plastic injection molding is a manufacturing process that involves injecting molten plastic into a mold to create precise and complex components. The importance of accurate molding cannot be overstated; it ensures that products meet stringent specifications and quality standards required by modern applications. With its ability to produce high volumes of uniform parts quickly, this method has become indispensable in industries such as aerospace, medical devices, and packaging.
The Role of Baoyuan in the Industry
Baoyuan has established itself as a leader in the field of mould injection moulding by consistently delivering high-quality solutions tailored to client needs. With years of experience and an unwavering commitment to excellence, Baoyuan leverages cutting-edge technology and skilled personnel to produce superior plastic injection molding molds. Their reputation for reliability and performance makes them a preferred partner for businesses seeking efficient production processes using injection moldable plastics.
Key Benefits of Injection Molding Services
The advantages of utilizing plastic injection molding services are numerous and impactful for businesses looking to scale their operations efficiently. Firstly, this method offers exceptional material versatility; manufacturers can choose from a wide range of thermoplastics that cater to specific performance requirements while ensuring durability. Additionally, the cost-effectiveness achieved through mass production means companies can significantly reduce per-unit costs while maintaining high standards—an essential factor in today’s competitive marketplace.
What is High Precision Plastic Injection Molding
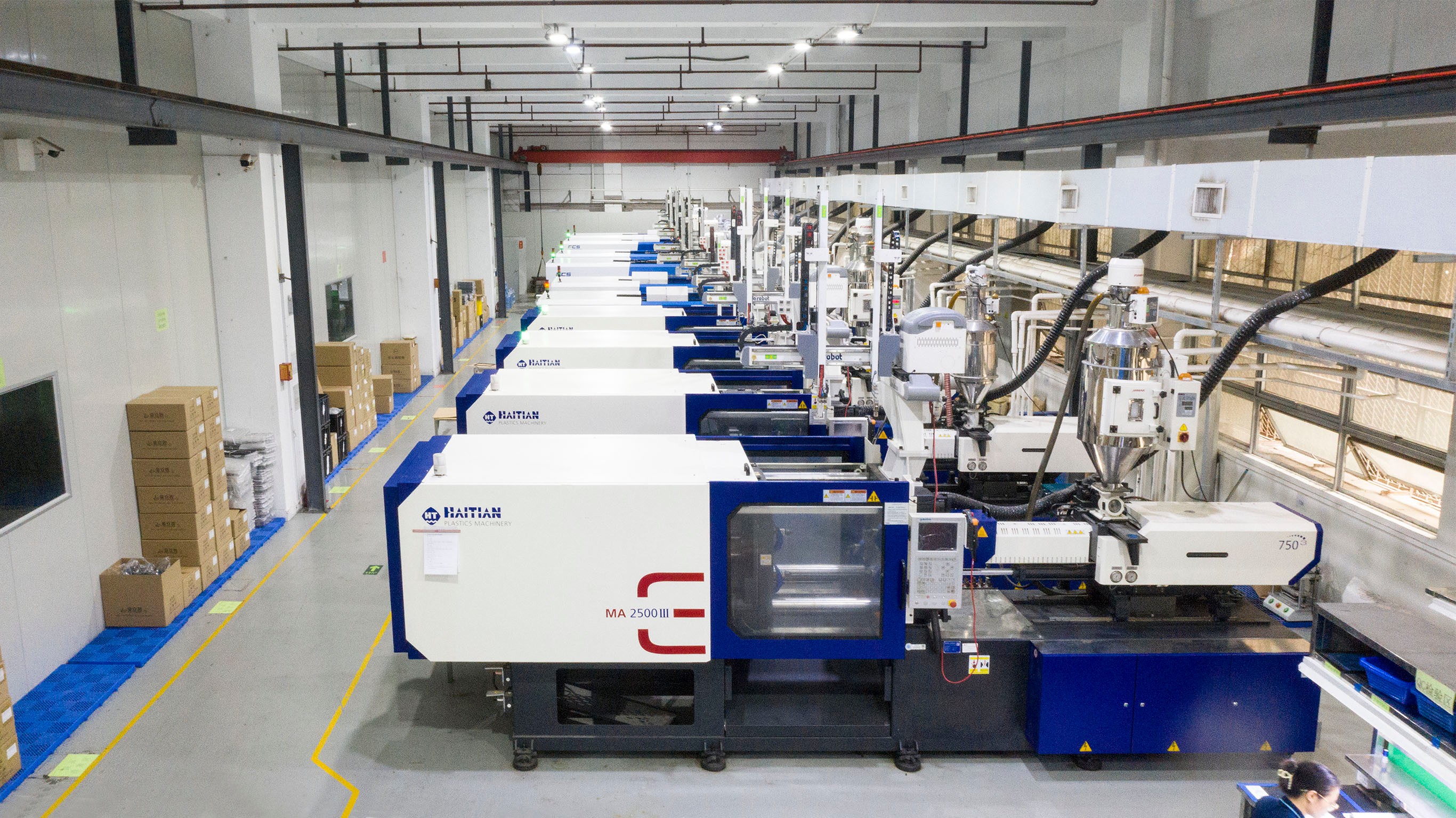
High precision plastic injection molding is a manufacturing process that produces intricate plastic parts with exceptional accuracy and consistency. This method utilizes advanced technology and specialized machinery to ensure that each component meets stringent specifications, making it ideal for industries where precision is paramount. By leveraging this technique, companies can achieve high-quality results while minimizing waste and production time.
Definition and Overview
At its core, high precision plastic injection molding involves injecting molten plastic into a precisely crafted mold to create various components. The process begins with the design of the mold, followed by heating the plastic until it reaches a liquid state before being injected into the mold cavity under high pressure. Once cooled, the solidified part is ejected from the mold, ready for further processing or assembly.
This technique stands out from traditional molding methods due to its ability to produce complex shapes with tight tolerances. The molds used in high precision applications are often made from durable materials like steel or aluminum, allowing for repeated use without significant wear or degradation. As a result, businesses can rely on consistent quality across large production runs.
Importance of Accurate Molding
Accurate molding is crucial in ensuring that each part produced meets both functional and aesthetic requirements. In industries such as automotive or medical devices, even minor deviations in dimensions can lead to catastrophic failures or costly recalls. Therefore, high precision plastic injection molding services must prioritize accuracy throughout every stage of production.
Achieving this level of precision requires skilled technicians who understand not only the intricacies of mold design but also how variables like temperature and pressure affect the final product's integrity. Furthermore, using advanced injection molding machines equipped with real-time monitoring systems enhances quality control by identifying issues before they escalate into larger problems. Ultimately, investing in accurate molding processes translates into improved product performance and customer satisfaction.
Applications in Various Industries
High precision plastic injection molding finds applications across numerous sectors due to its versatility and reliability. In the automotive industry, components such as dashboards, panels, and connectors are manufactured using this method to ensure safety and functionality at scale. Similarly, electronics manufacturers rely on precise molds for producing casings and internal parts that require exact specifications.
The medical field also benefits significantly from this technology; surgical instruments and devices must adhere to strict regulatory standards where any deviation could compromise patient safety. Other industries utilizing mould injection moulding include consumer goods, aerospace, packaging solutions, and more—each demanding unique designs tailored through sophisticated processes like those offered by Baoyuan’s expertise in injection moldable plastics.
Baoyuan's Expertise in Mould Injection Moulding
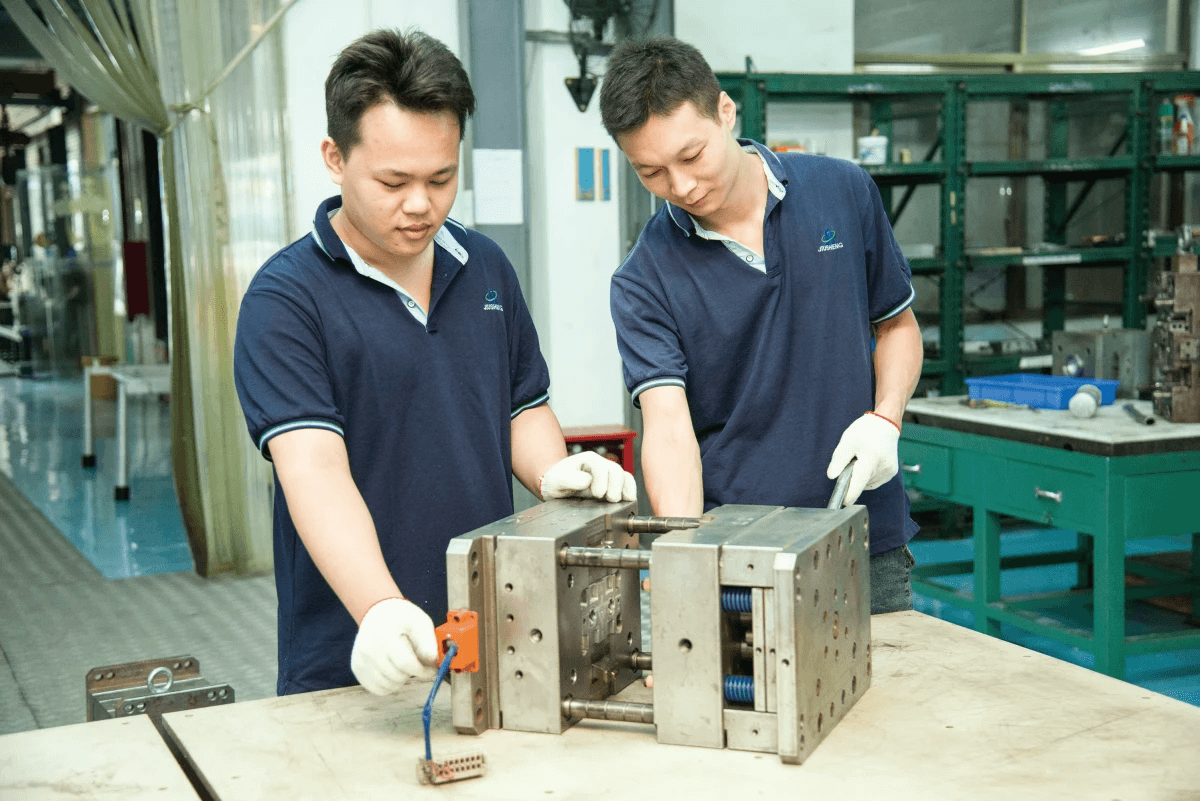
Baoyuan stands out in the realm of high precision plastic injection molding, thanks to its team of seasoned professionals and state-of-the-art technology. The company prides itself on delivering exceptional plastic injection molding services that meet the diverse needs of various industries. With a commitment to excellence, Baoyuan ensures that each project is handled with precision and care, from concept to completion.
Experienced Technical Personnel
At the heart of Baoyuan's success is its experienced technical personnel who bring years of expertise in mould injection moulding to the table. These professionals are not only skilled but also passionate about their craft, ensuring that every plastic injection molding mold they create meets stringent quality standards. Their deep understanding of injection moldable plastics allows them to tackle complex projects with confidence and efficiency.
Advanced Design Software Utilization
Baoyuan leverages advanced design software to optimize the entire process of mold plastic injection creation. This cutting-edge technology enables the team to create detailed 3D models, ensuring accuracy and functionality before production begins. By utilizing sophisticated software tools, Baoyuan can simulate various scenarios and refine designs for maximum efficiency in their plastic injection molding services.
Quality Assurance in Production
Quality assurance is paramount at Baoyuan, where rigorous testing protocols are implemented throughout the production process. Each step, from initial design through to final output using an injection molding machine, undergoes thorough inspection to guarantee high precision plastic injection molding results. This unwavering commitment to quality ensures that clients receive durable products made from top-notch materials like injection moldable plastics—ultimately enhancing business success across various sectors.
The Process of Plastic Injection Molding
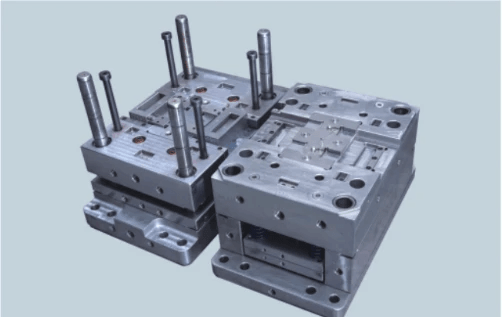
Plastic injection molding is a fascinating blend of art and science, transforming raw materials into intricate designs with high precision. This process begins by melting thermoplastic or thermosetting polymers, which are then injected into a mold under high pressure. Once cooled, the mold is opened to reveal perfectly formed components that can be used in various applications.
How Injection Molding Works
At its core, high precision plastic injection molding revolves around the principle of melting and shaping plastics. The process starts with the heating of plastic pellets until they become a viscous liquid, ready for injection. This molten plastic is then forced into a precisely engineered mold cavity where it takes on the desired shape as it cools and solidifies.
The efficiency of this method lies in its ability to produce complex shapes with remarkable accuracy and minimal waste. By utilizing advanced techniques in mould injection moulding, manufacturers can achieve tight tolerances that are essential for industries such as automotive and electronics. This level of precision ensures that every component fits seamlessly into larger assemblies, enhancing overall product quality.
Steps from Design to Production
The journey from design to production in plastic injection molding services involves several critical steps that ensure quality outcomes. Initially, engineers create detailed 3D models using advanced CAD software to visualize the final product before any physical work begins. Once the design is approved, prototypes may be created using rapid prototyping techniques to test functionality and fit.
After finalizing the prototype, it's time to create the plastic injection molding mold itself—a task requiring meticulous attention to detail and expertise in mould design. Following this, production commences where raw materials are fed into an injection molding machine that heats them up before injecting them into the prepared molds under high pressure. Finally, after cooling and solidifying within minutes, these molds are opened to release finished parts ready for assembly or further processing.
Role of Injection Molding Machines
Injection molding machines play a pivotal role in ensuring efficiency and consistency throughout the manufacturing process of high precision plastic injection molding. These machines come equipped with advanced technology that allows for precise control over temperature and pressure during each cycle—critical factors influencing product quality.
Moreover, modern machines can handle various types of plastics known as injection moldable plastics while maintaining optimal performance across different production runs. With capabilities ranging from small-scale operations to large-volume mass production, these machines adapt effortlessly based on project requirements—making them indispensable tools in any manufacturing environment focused on excellence.
Advantages of Injection Moldable Plastics
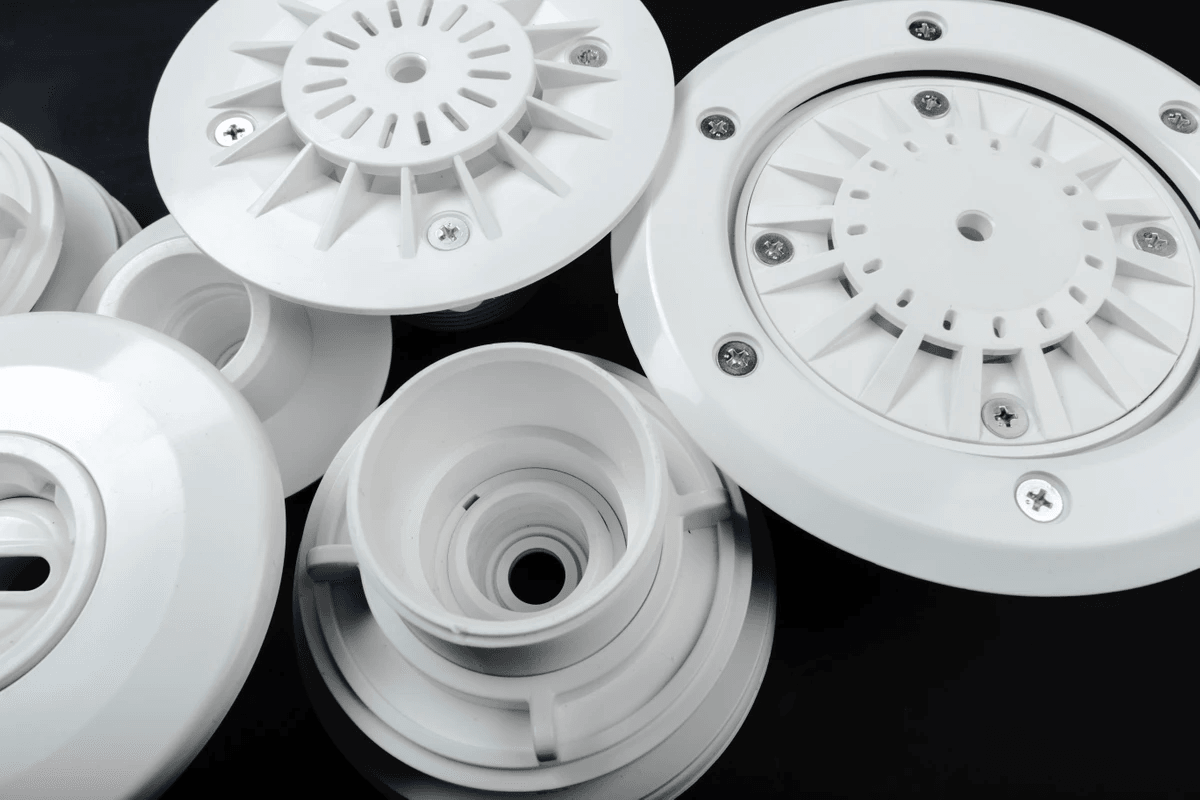
Injection moldable plastics have carved out a significant niche in manufacturing due to their numerous advantages. From the versatility of materials to cost-effectiveness and sustainability, high precision plastic injection molding offers solutions that are hard to beat. Let’s dive into what makes these plastics a go-to choice for industries across the board.
Material Versatility and Durability
One of the standout features of injection moldable plastics is their incredible material versatility. Manufacturers can choose from a wide array of plastic types, each with unique properties suited for specific applications, making high precision plastic injection molding adaptable to various needs. These materials not only provide durability but also maintain their integrity under different environmental conditions, ensuring that products last longer and perform better.
The ability to customize material blends further enhances this versatility; engineers can create specific formulations that meet stringent performance criteria without compromising on quality. For instance, using advanced mould injection moulding techniques allows for the incorporation of additives that improve strength or resistance to heat and chemicals. This level of customization solidifies plastic's role as a reliable material in sectors ranging from automotive to consumer goods.
Cost-Effectiveness for Mass Production
When it comes to mass production, few methods rival the cost-effectiveness offered by plastic injection molding services. The efficiency of the process translates into lower per-unit costs as production scales up, allowing businesses to meet market demands without breaking the bank. Additionally, once a plastic injection molding mold is created, it can produce thousands—or even millions—of identical parts at minimal incremental costs.
This economic advantage doesn’t just stop at production; it also extends to reduced waste during manufacturing processes compared to traditional methods like machining or milling. The precision inherent in high precision plastic injection molding minimizes scrap material while maximizing output quality, making it an attractive option for manufacturers looking to optimize their budgets while maintaining standards. Furthermore, with advancements in technology and machinery—like modern injection molding machines—companies can achieve faster turnaround times without sacrificing quality.
Environmentally Friendly Options
In today’s eco-conscious world, sustainability is more than just a buzzword; it's becoming essential in manufacturing practices—including those involving mould injection moulding processes. Many manufacturers are now focusing on developing environmentally friendly options within the realm of plastic injection molding by utilizing recycled materials and bio-based plastics that reduce carbon footprints significantly. High precision plastic injection molding not only facilitates this shift but also ensures that products maintain high performance levels despite being made from alternative materials.
Moreover, innovations in recycling technologies mean that post-consumer plastics can be reintroduced into the production cycle with minimal loss in quality or functionality—a win-win for both businesses and our planet! By choosing sustainable practices within their operations, companies can enhance their brand reputation while contributing positively toward environmental conservation efforts through responsible sourcing and manufacturing processes involving injection moldable plastics.
The Future of Plastic Injection Molding
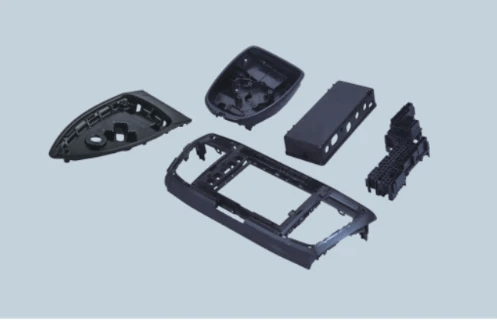
The landscape of high precision plastic injection molding is evolving at a remarkable pace, driven by technological advancements and the ever-increasing demand for efficiency and quality. As industries seek innovative solutions, plastic injection molding services are adapting to meet these challenges head-on. This section explores the innovations, trends, and sustainability efforts shaping the future of this crucial manufacturing process.
Innovations in Technology
The future of mould injection moulding is heavily influenced by cutting-edge technologies that enhance precision and reduce production times. For instance, the integration of artificial intelligence (AI) into injection molding machines allows for real-time monitoring and adjustments during the manufacturing process, ensuring optimal performance and consistency in product quality. Additionally, 3D printing technology is being utilized alongside traditional methods to create complex mold plastic injection designs that were previously thought impossible.
Moreover, advancements in materials science have led to the development of new types of injection moldable plastics that offer superior strength and flexibility while remaining lightweight. These innovative materials not only improve product performance but also expand application possibilities across various industries such as automotive, healthcare, and consumer goods. With ongoing research and development in this field, we can expect even more groundbreaking technologies that will redefine high precision plastic injection molding.
Trends in Molding Techniques
As industries evolve, so do the techniques employed in plastic injection molding. One notable trend is the shift towards multi-material injection molding processes that allow manufacturers to produce complex components with different material properties within a single cycle. This method enhances design flexibility while reducing assembly time—an appealing prospect for businesses looking to streamline their production lines.
Another emerging trend is the increased focus on automation within mould injection moulding facilities. Automated systems not only boost efficiency but also minimize human error during production runs—ensuring higher accuracy in every batch produced through advanced plastic injection molding processes. As companies strive for lean manufacturing practices, embracing these trends will be essential for maintaining competitiveness in a fast-paced market.
Sustainability in the Injection Molding Industry
Sustainability has become a cornerstone principle driving change across many sectors—including high precision plastic injection molding. Manufacturers are increasingly adopting eco-friendly practices by utilizing biodegradable or recycled materials as part of their plastic injection molding services portfolio. This shift not only appeals to environmentally conscious consumers but also aligns with global efforts toward reducing waste and carbon footprints.
Furthermore, innovations aimed at improving energy efficiency within injection molding machines are gaining traction as companies look to lower operational costs while minimizing environmental impact. Technologies such as servo-driven hydraulic systems help reduce energy consumption significantly during production cycles—making sustainable practices more accessible than ever before in moulding operations worldwide. By prioritizing sustainability alongside quality and efficiency, businesses can thrive while contributing positively to our planet’s future.
Conclusion
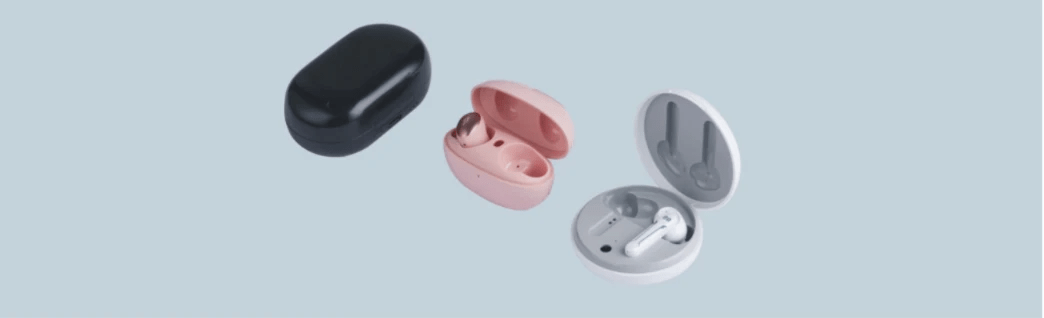
In wrapping up our exploration of high precision plastic injection molding, it’s clear that this manufacturing process is not just about creating parts; it’s about precision, efficiency, and adaptability. The benefits of utilizing plastic injection molding services extend far beyond mere cost savings; they encompass the ability to produce complex shapes with remarkable accuracy. With companies like Baoyuan at the forefront, the future of mould injection moulding looks exceedingly promising.
Key Takeaways on High Precision Plastic Injection Molding
High precision plastic injection molding is essential for industries that demand intricate designs and flawless execution. This process allows for the production of durable and lightweight components using injection moldable plastics, which are crucial in sectors ranging from automotive to medical devices. By understanding the importance of accurate molding and its applications, businesses can leverage these techniques to enhance their product offerings.
Why Choose Baoyuan for Your Molding Needs
Choosing Baoyuan for your mould injection moulding requirements means opting for a partner with seasoned expertise and cutting-edge technology. With experienced technical personnel and advanced design software, Baoyuan ensures that each plastic injection molding mold is crafted to meet rigorous standards. Their commitment to quality assurance throughout production guarantees that you receive products that not only meet but exceed expectations.
The Impact of Quality Molding on Business Success
Quality in plastic injection molding can make or break a business's reputation in today's competitive market. When companies invest in high precision plastic injection molding services, they are investing in reliability and customer satisfaction—two key elements for success. Ultimately, partnering with a trusted provider like Baoyuan can lead to enhanced product performance, reduced waste, and improved profitability.