Introduction
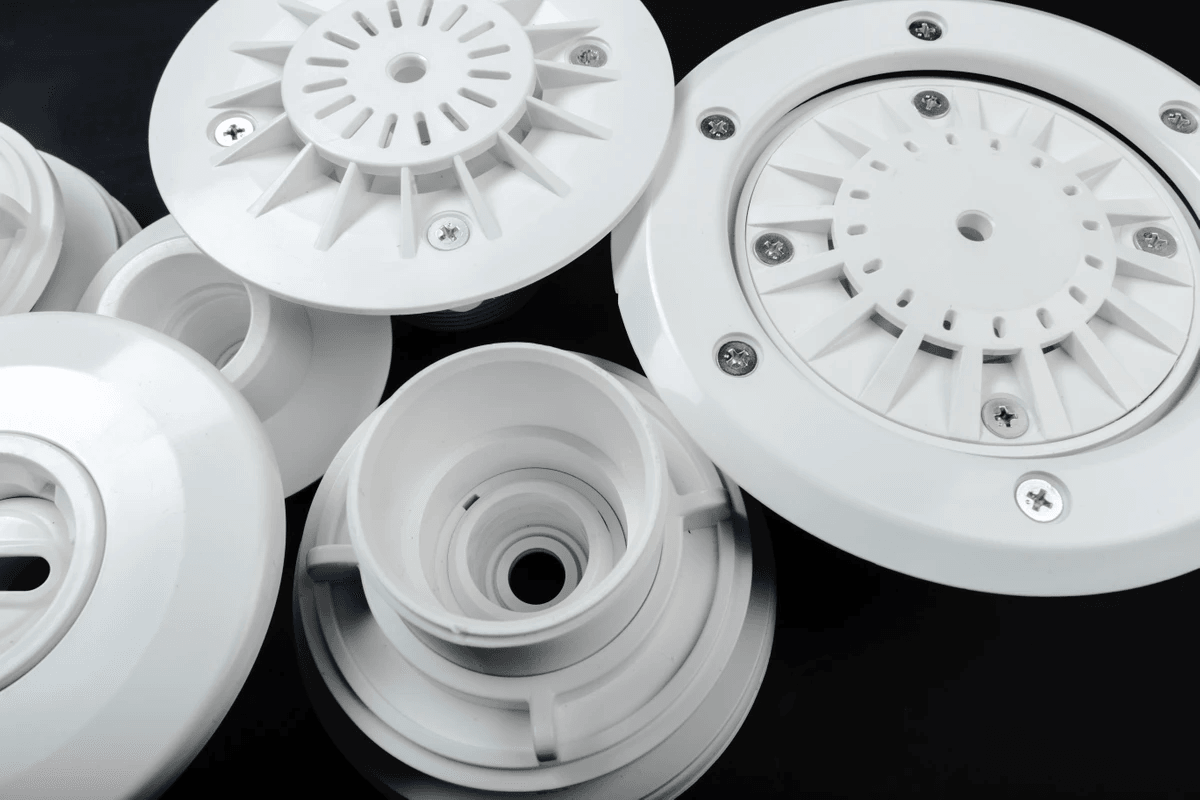
In the ever-evolving landscape of materials science, High Density Polyethylene (HDPE) stands out as a versatile and robust option for various applications. Its unique properties make it an essential player in multiple industries, from consumer goods to healthcare. Understanding HDPE and its importance is crucial for anyone looking to leverage its benefits in their projects.
Understanding HDPE and Its Importance
High Density Polyethylene is a type of thermoplastic made from petroleum, known for its high strength-to-density ratio. This characteristic not only contributes to its durability but also makes it a preferred choice in the manufacturing sector. As industries increasingly focus on sustainability and efficiency, high density polyethylene emerges as an eco-friendly option that can be easily recycled and repurposed.
The Fascinating World of Injection Molding
Injection molding is a manufacturing process that allows for the mass production of complex shapes with precision and speed—qualities that are essential for modern production lines. The question many ask is, Can HDPE be injection molded? The answer is a resounding yes! This method enables manufacturers to create intricate designs while maintaining the integrity of high density plastic components.
Key Benefits of High Density Polyethylene
The benefits of high density polyethylene extend beyond mere functionality; they encompass cost-effectiveness, environmental resistance, and exceptional durability. When considering materials for your next project, HDPE's ability to withstand harsh conditions while remaining lightweight makes it an attractive choice for producers worldwide. With its myriad advantages, it's no wonder that high density polymer products are increasingly dominating both consumer markets and industrial applications.
What is HDPE?
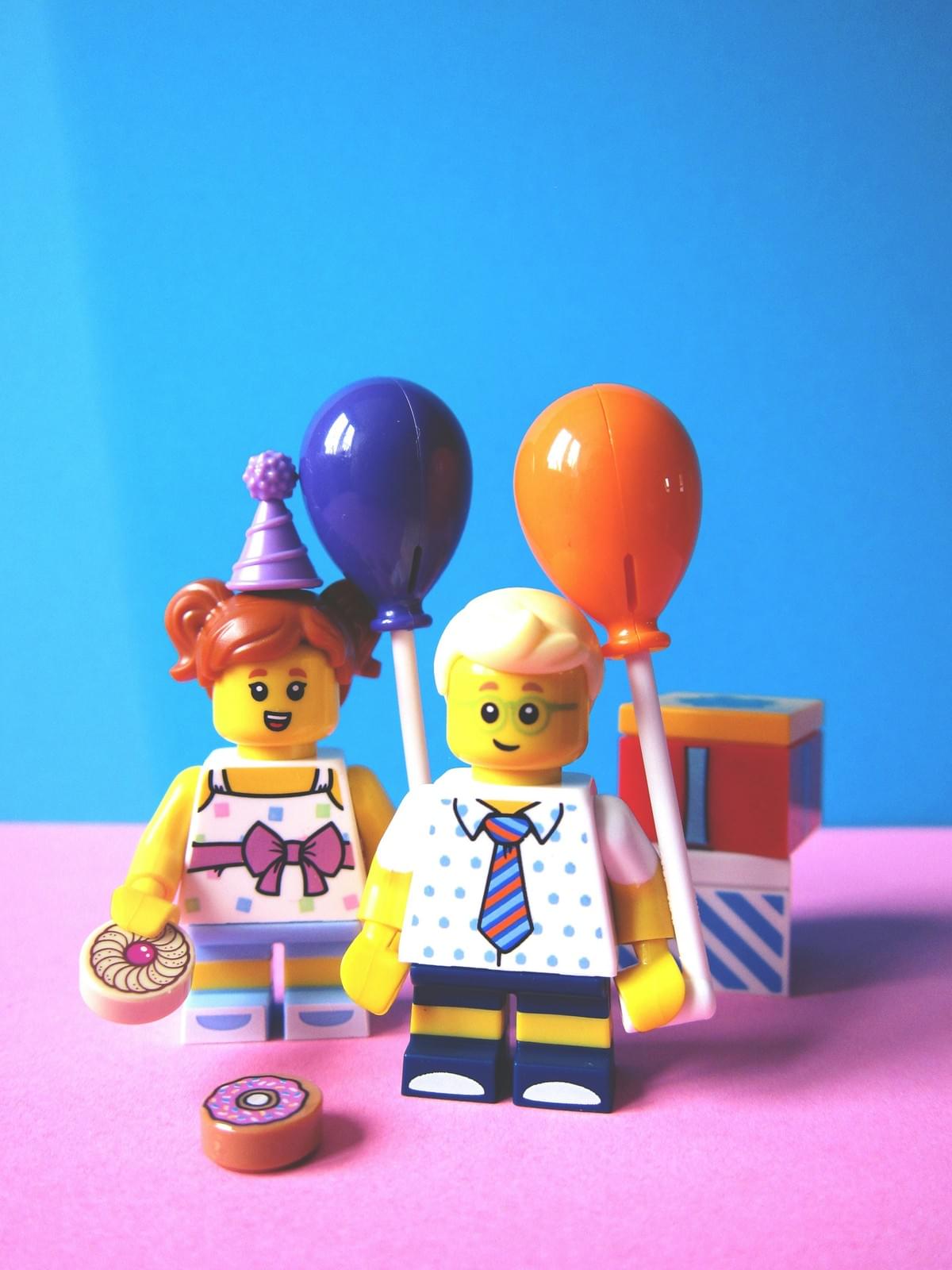
High Density Polyethylene, commonly known as HDPE, is a versatile thermoplastic that has become a staple in various industries due to its remarkable properties. This high density plastic boasts a linear structure with minimal branching, resulting in superior strength and durability compared to many other plastics. Its unique characteristics make it an ideal candidate for numerous applications, especially when considering processes like injection molding.
Characteristics of High Density Polyethylene
HDPE is renowned for its impressive tensile strength and resistance to impact, making it one of the toughest materials available in the plastic family. Additionally, this high density polymer exhibits excellent chemical resistance, allowing it to withstand harsh environmental conditions without degrading or losing integrity. Its lightweight nature combined with flexibility further enhances its appeal for manufacturers looking for reliable materials that can perform under pressure.
Comparison with Other Plastics
When we stack HDPE against other plastics like polypropylene (PP) or polyvinyl chloride (PVC), its advantages become clear. Unlike PVC, which can be brittle and less resistant to UV light, HDPE maintains its structural integrity even when exposed to sunlight and varying temperatures. Furthermore, while polypropylene provides good chemical resistance, it doesn't quite match the strength-to-weight ratio offered by high density polyethylene, particularly in demanding applications requiring injection molding.
Common Uses of HDPE
The versatility of high polyethylene means it's found everywhere—from everyday consumer goods to industrial components and beyond. Common uses include packaging containers such as milk jugs and detergent bottles due to their ability to resist impact and chemicals effectively. In addition to packaging, this high density plastic also plays a crucial role in manufacturing automotive parts and even medical devices thanks to its durability and reliability during injection molding processes.
Can HDPE Be Injection Molded?
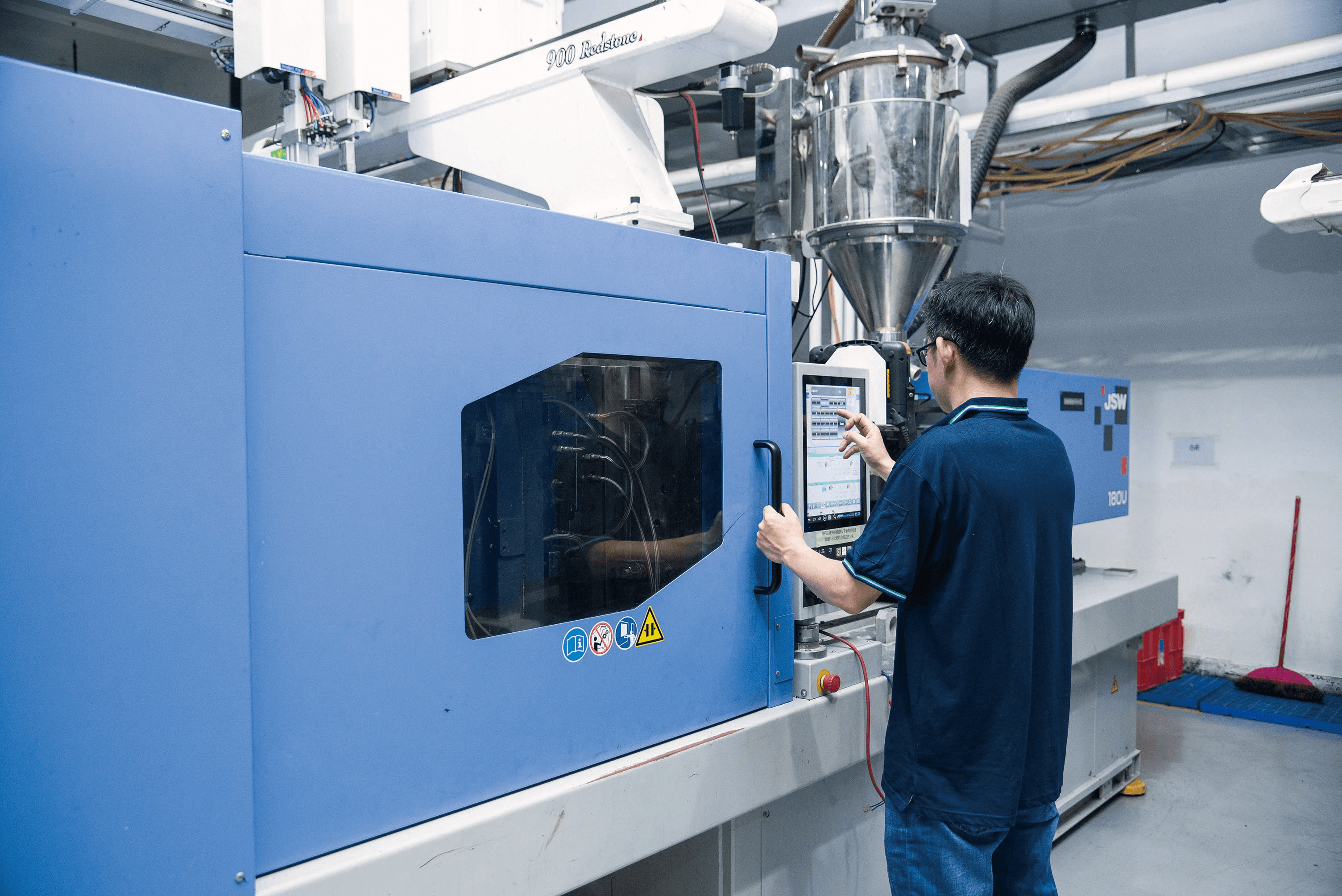
When it comes to the world of plastics, one question often arises: can HDPE be injection molded? The answer is a resounding yes! High density polyethylene (HDPE) is not only compatible with the injection molding process but also offers several advantages that make it a popular choice among manufacturers. This section will explore how HDPE fits into the injection molding landscape, its benefits, and some considerations to keep in mind.
The Injection Molding Process Explained
Injection molding is a manufacturing process that involves melting plastic and injecting it into a mold to create specific shapes and designs. For high density polyethylene, this process begins with heating the resin until it reaches a liquid state. Once melted, the liquid HDPE is injected into a precisely designed mould, where it cools and solidifies into the desired form—resulting in high-quality products made from high density plastic.
This method allows for intricate designs and consistent production of parts at scale. As one of the most widely used plastics, high density polymer like HDPE can be transformed into everything from containers to complex automotive parts through this efficient technique. Understanding how injection molding works helps clarify why many industries are turning to high polyethylene for their production needs.
Advantages of Using HDPE for Injection Molding
One of the standout advantages of using HDPE in injection molding is its remarkable durability and strength. High density polyethylene exhibits excellent resistance to impact and stress, making it an ideal choice for products that require longevity under various conditions. Additionally, HDPE's lightweight nature contributes to cost savings in shipping and handling without compromising on quality.
Another significant benefit lies in its environmental resistance; high density plastic can withstand harsh chemicals and UV exposure without degrading quickly. This characteristic makes it suitable for outdoor applications or environments where other materials may falter over time. Furthermore, using HDPE in plastic injection molding processes tends to be cost-effective due to lower material costs combined with efficient production cycles.
Limitations and Considerations
While there are many benefits associated with using high density polyethylene in mould injection moulding, it's essential to consider some limitations as well. One potential drawback is that while HDPE has great flexibility when molded into shapes, it may not hold intricate details as well as some other plastics during the cooling process—leading to potential imperfections in highly detailed designs.
Another consideration involves temperature sensitivity; although HDPE has a good melting point for many applications, excessive heat during processing can lead to degradation if not carefully managed. Additionally, while recycling options exist for high density polymer products made from HDPE, they may not always be as readily available compared to other types of plastics like PET or PVC.
In conclusion, while there are considerations when asking can hdpe be injection molded?, its numerous advantages make it an attractive option for various industries looking for durable solutions.
Benefits of High Density Plastic
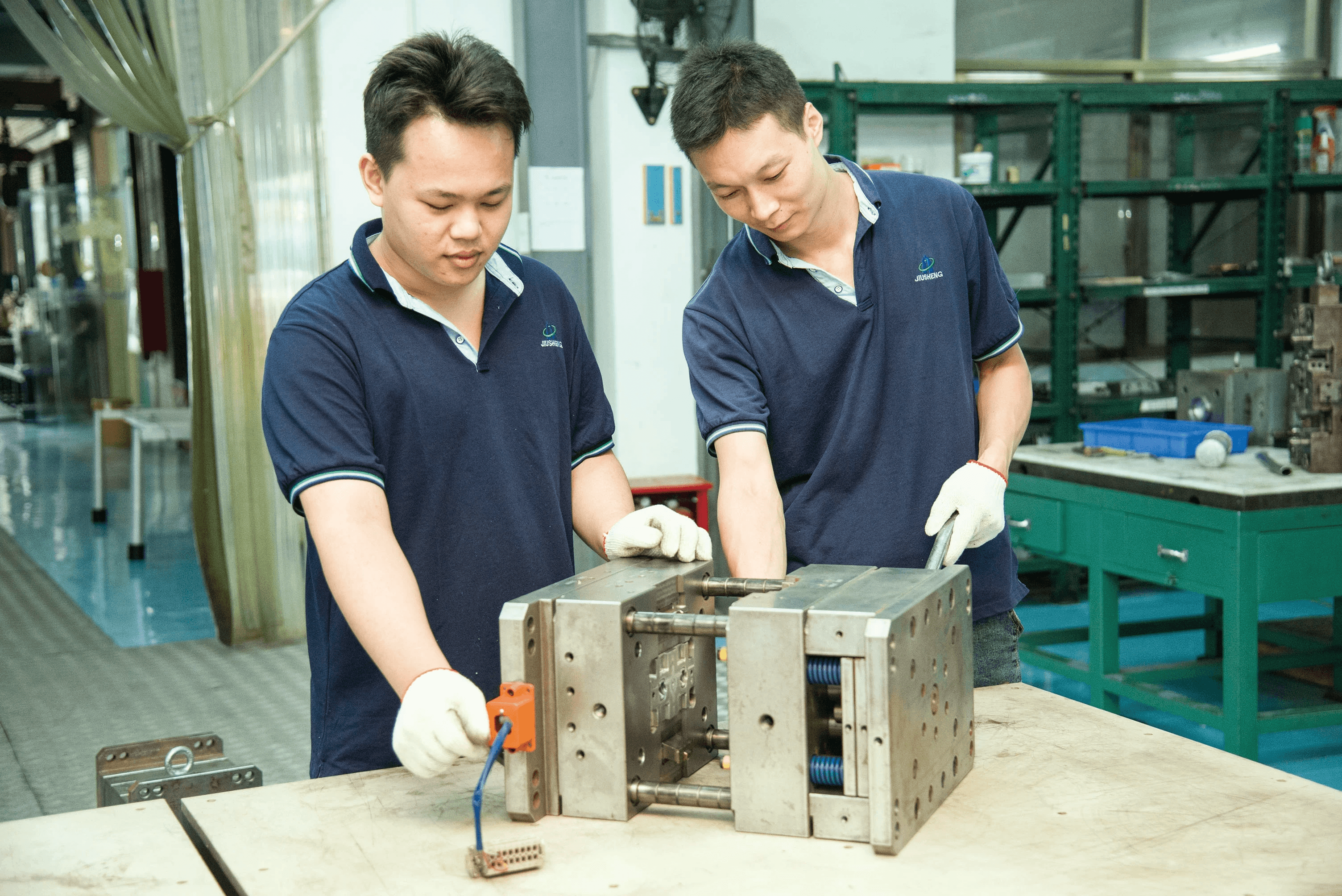
High Density Polyethylene (HDPE) is not just another plastic; it’s a powerhouse in the world of materials. Its unique properties make it a go-to choice for various applications, thanks to its durability, environmental resistance, and cost-effectiveness in production. In this section, we’ll delve into why high density plastic stands out in the realm of injection molding and beyond.
Durability and Strength
One of the most remarkable features of high density polyethylene is its exceptional durability and strength. HDPE boasts a high tensile strength that enables it to withstand significant stress without breaking or deforming, making it ideal for products that require resilience. This characteristic is particularly beneficial in injection molding applications where parts must endure wear and tear over time.
When considering whether can HDPE be injection molded, its robustness plays a crucial role; molded components are often subjected to rigorous conditions. The sturdy nature of high density polymer ensures that products maintain their integrity under pressure, heat, and impact. As such, manufacturers frequently turn to HDPE when they need reliable materials that won’t compromise on performance.
Environmental Resistance
Another significant advantage of HDPE is its impressive environmental resistance. This high density plastic can withstand exposure to various chemicals and harsh weather conditions without degrading or losing functionality over time. Whether it's UV radiation from sunlight or corrosive substances found in industrial settings, HDPE remains steadfast.
This resilience makes high density polyethylene an excellent choice for outdoor applications and environments where other plastics might falter. Additionally, since many consumers are becoming increasingly eco-conscious, the ability of HDPE to last longer reduces waste and promotes sustainability—a win-win situation for both manufacturers and the planet!
Cost-Effectiveness in Production
Cost-effectiveness is a critical factor when selecting materials for production processes like mould injection moulding. High density polyethylene offers an economical solution due to its relatively low material costs combined with its long-lasting properties—meaning fewer replacements are needed over time. This efficiency translates into reduced overall expenses for businesses looking to optimize their production lines.
Moreover, the ease with which high polyethylene can be processed during injection molding further enhances its cost benefits; less energy is required during manufacturing compared to other plastics that demand more complex processing techniques. When companies weigh their options for plastic injection molding projects, choosing HDPE often leads them down a path of financial prudence while still delivering quality products.
Applications of High Density Polymer
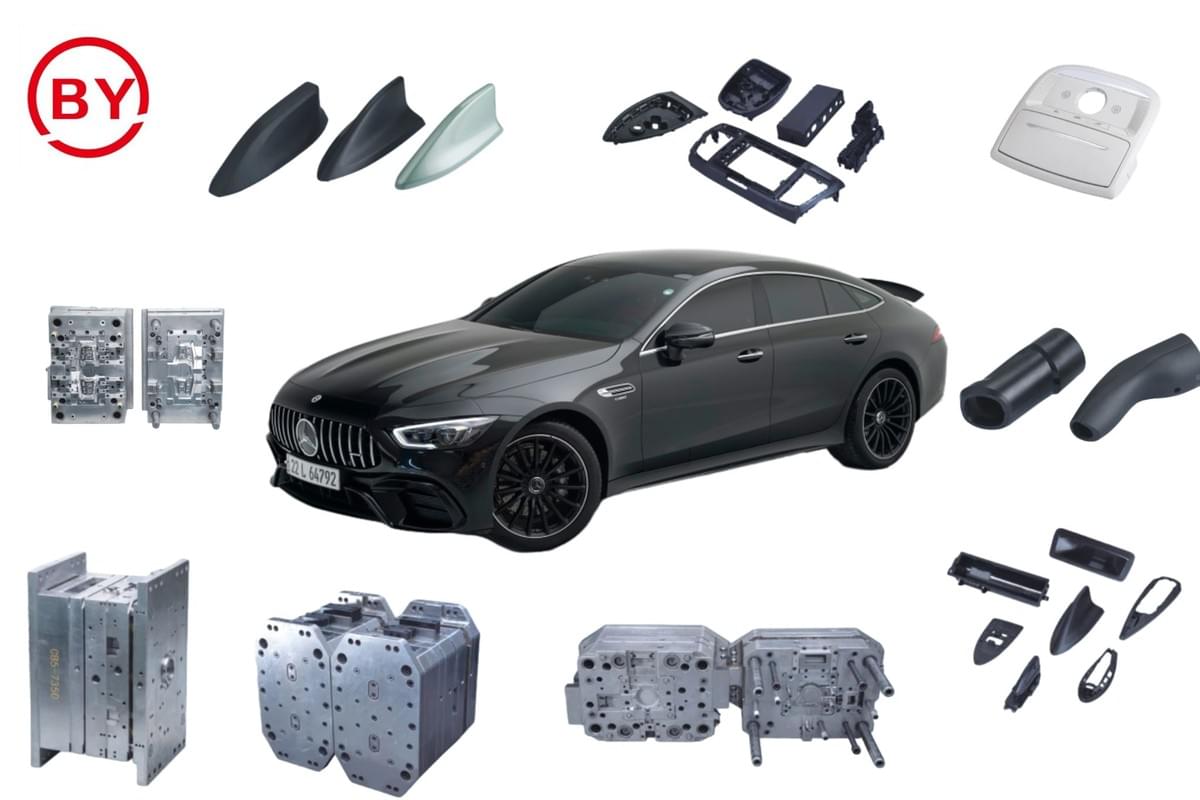
High density polyethylene (HDPE) is a versatile material that finds its way into various sectors, thanks to its unique properties and the advantages it offers in injection molding. From consumer goods to industrial components, HDPE’s adaptability makes it a preferred choice in many applications. This section explores the diverse uses of high density polymer across different industries.
Consumer Goods and Packaging
When it comes to consumer goods, high density plastic reigns supreme due to its robust nature and lightweight characteristics. Items such as bottles, containers, and toys are commonly made from HDPE because they can withstand wear and tear while maintaining their shape over time. The injection molding process allows manufacturers to create intricate designs efficiently, making high polyethylene an ideal choice for packaging solutions that require durability and aesthetic appeal.
In the realm of packaging, HDPE is particularly favored for its recyclability and resistance to moisture, which helps preserve product integrity. The ease with which high density polymer can be molded into various shapes means brands can innovate without sacrificing quality or performance. As consumers increasingly demand sustainable options, the use of HDPE in consumer goods continues to rise.
Automotive and Industrial Components
The automotive industry has also embraced high density polyethylene for a multitude of applications ranging from fuel tanks to interior components. Thanks to its strength-to-weight ratio, HDPE helps improve fuel efficiency while providing durable parts that can withstand harsh conditions. With the advancements in mould injection moulding techniques, manufacturers can produce complex automotive components with precision using high density plastic.
In industrial settings, high polyethylene is utilized for creating storage containers, pallets, and piping systems due to its chemical resistance and longevity. These attributes make it a top contender when considering materials that need to endure tough environments without compromising functionality or safety. As industries continue seeking efficient production methods through plastic injection molding processes, HDPE remains at the forefront of innovation.
Medical and Healthcare Applications
High density polymer has carved out a significant niche in medical applications where cleanliness and reliability are paramount. Items such as surgical trays, medical tubing, and pharmaceutical containers often utilize HDPE due to its non-reactive nature with various substances used in healthcare settings. The ability of this material to be sterilized further enhances its suitability for medical use while ensuring patient safety is not compromised.
Moreover, the flexibility offered by injection molding allows for custom designs tailored specifically for healthcare needs—whether it's ergonomic handles on surgical tools or specialized containers for medication storage. As healthcare technology advances rapidly alongside increasing regulations around materials used in medical devices, the role of high density polyethylene becomes even more critical in meeting these standards effectively.
Mould Injection Moulding Techniques
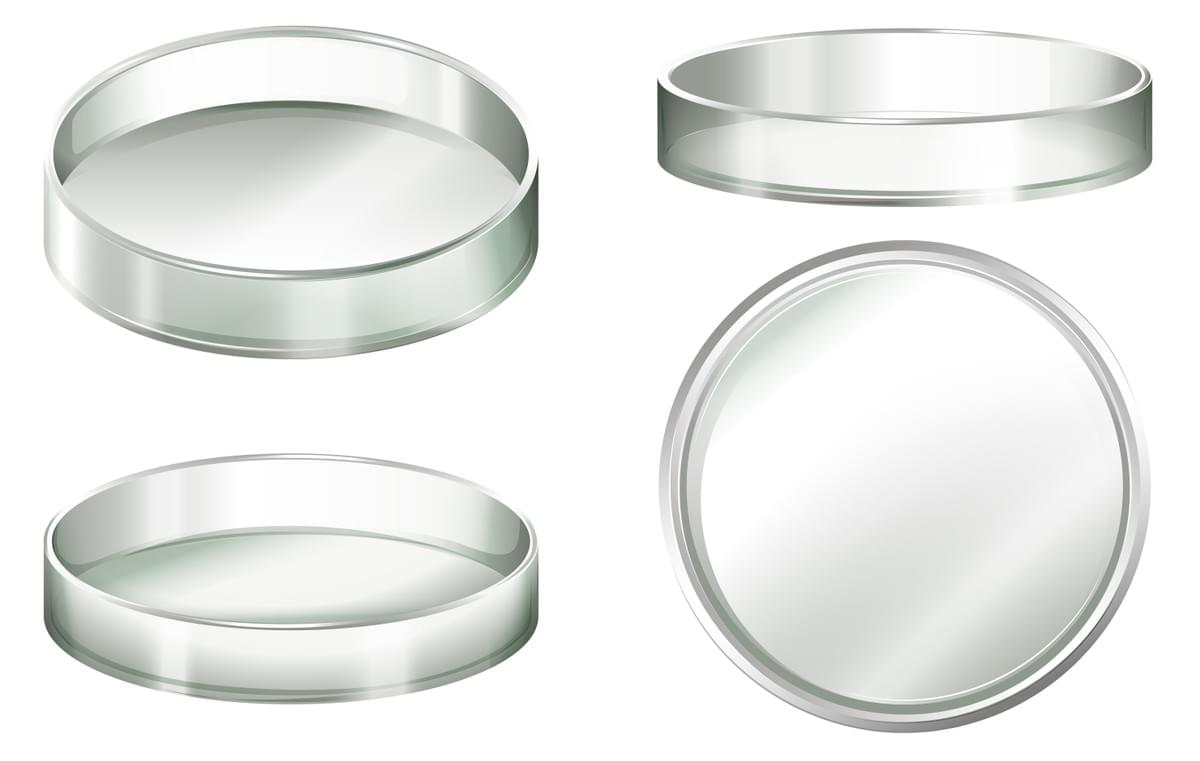
When it comes to mould injection moulding, the design and construction of the mould are paramount. A well-engineered mould ensures that high density polyethylene (HDPE) is shaped accurately and consistently during the injection molding process. The intricacies involved in creating these molds include selecting materials that can withstand high pressure and temperature, as well as ensuring precise dimensions to maintain product quality.
Overview of Mould Design and Construction
Mould design is a critical step in the plastic injection molding process, especially when working with high density plastic like HDPE. Designers must consider factors such as part geometry, draft angles, and cooling channels to optimize production efficiency. Furthermore, the choice of materials for constructing the mould itself can significantly affect durability and longevity, making it essential to choose materials that can endure repeated cycles without degrading.
Innovations in Moulding Technology
The world of mould injection moulding is constantly evolving, thanks to innovations that enhance efficiency and precision. Recent advancements include 3D printing technology for rapid prototyping of molds, which allows for quicker adjustments before full-scale production begins. Additionally, smart manufacturing techniques are being integrated into traditional processes to monitor performance in real-time—ensuring that every batch produced from high density polymer maintains consistent quality.
Quality Assurance in Plastic Injection Molding
Quality assurance is non-negotiable in the realm of plastic injection molding—especially when dealing with high polyethylene products destined for consumer use or critical applications like medical devices. Rigorous testing protocols help identify defects early on by examining aspects such as dimensional accuracy and surface finish. By implementing comprehensive quality control measures throughout the production cycle, manufacturers can confidently answer the question: Can HDPE be injection molded? with a resounding yes.
Conclusion
In wrapping up our exploration of high density polyethylene (HDPE) and its role in injection molding, it’s clear that this material has a lot to offer. From its robust characteristics to its versatility in various applications, HDPE stands out as a premier choice for many projects. Whether you’re delving into consumer goods or industrial components, understanding the benefits of high density plastic can significantly influence your decisions.
Why Choose HDPE for Your Projects
Choosing HDPE for your projects is akin to picking the Swiss Army knife of plastics—it's adaptable and reliable! The unique properties of high density polyethylene make it ideal for injection molding processes, allowing manufacturers to create intricate designs with ease. Additionally, its durability and resistance to environmental factors ensure that products made from HDPE stand the test of time, making it an economical choice in the long run.
The Future of High Density Polyethylene
The future looks bright for high density polyethylene as innovations in mould injection moulding continue to evolve. With advances in technology enhancing the efficiency and precision of plastic injection molding, we can expect even more applications for this versatile polymer. As industries seek sustainable options, HDPE's recyclability and low environmental impact position it favorably in a world increasingly focused on eco-friendly solutions.
Insights from the Baoyuan Team
The Baoyuan Team emphasizes that understanding whether can HDPE be injection molded is crucial for anyone considering this material for their next project. Their insights reveal that not only is HDPE suitable for a wide range of applications, but it also offers significant advantages over other materials when molded correctly. By leveraging their expertise in high density polymer processing, they help clients maximize both quality and efficiency in production.