Introduction
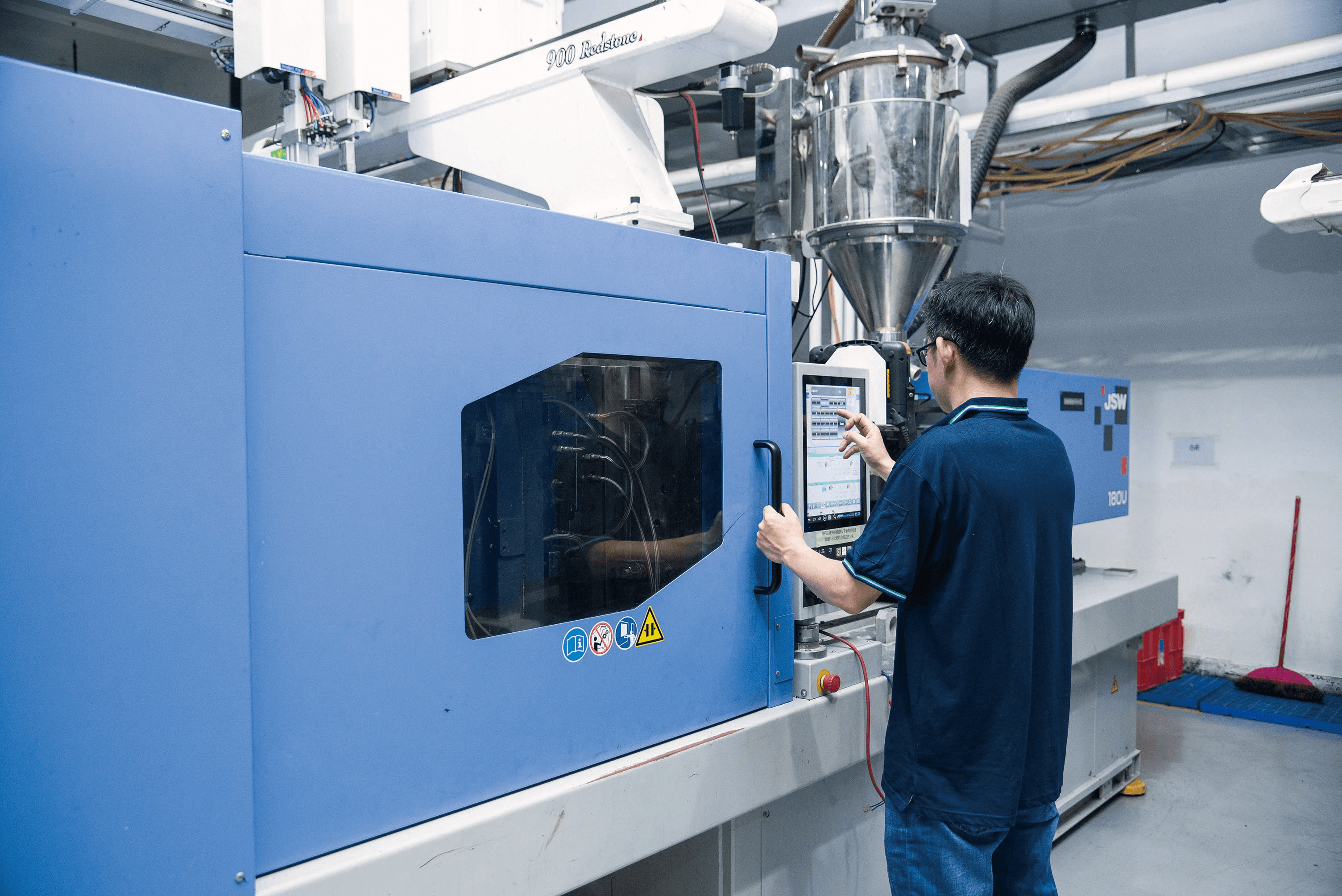
In the world of manufacturing, particularly in injection molding, flow lines are a common yet often misunderstood phenomenon. These visible streaks or patterns on molded parts can significantly impact the aesthetic and functional quality of products. Understanding flow lines in injection molding is crucial for manufacturers aiming to enhance product quality and reduce waste.
Understanding Flow Lines in Injection Molding
Flow lines in injection molding occur when molten plastic flows into a mold cavity, creating visible marks as it cools and solidifies. These lines can be caused by various factors, including material selection, temperature variations, and mold design flaws. Differentiating flow lines from weld lines—another type of defect—is essential for effective troubleshooting.
Importance of Addressing Flow Line Defects
Addressing flow line defects is vital not just for aesthetics but also for maintaining product integrity and functionality. Flow marks can indicate uneven cooling or improper material flow, which may compromise the strength and durability of the final product. By understanding how do you prevent flow lines in injection molding, manufacturers can enhance their production processes and deliver higher-quality items to their customers.
Overview of Injection Molding Process
The process flow of injection molding involves several key phases: injection, cooling, and ejection. During these stages, careful attention must be paid to parameters like temperature and pressure to minimize defects such as weld lines or flow marks. Additionally, implementing effective strategies like flow analysis in injection molding helps ensure that each phase contributes to an efficient overall workflow.
What are Flow Lines in Injection Molding?
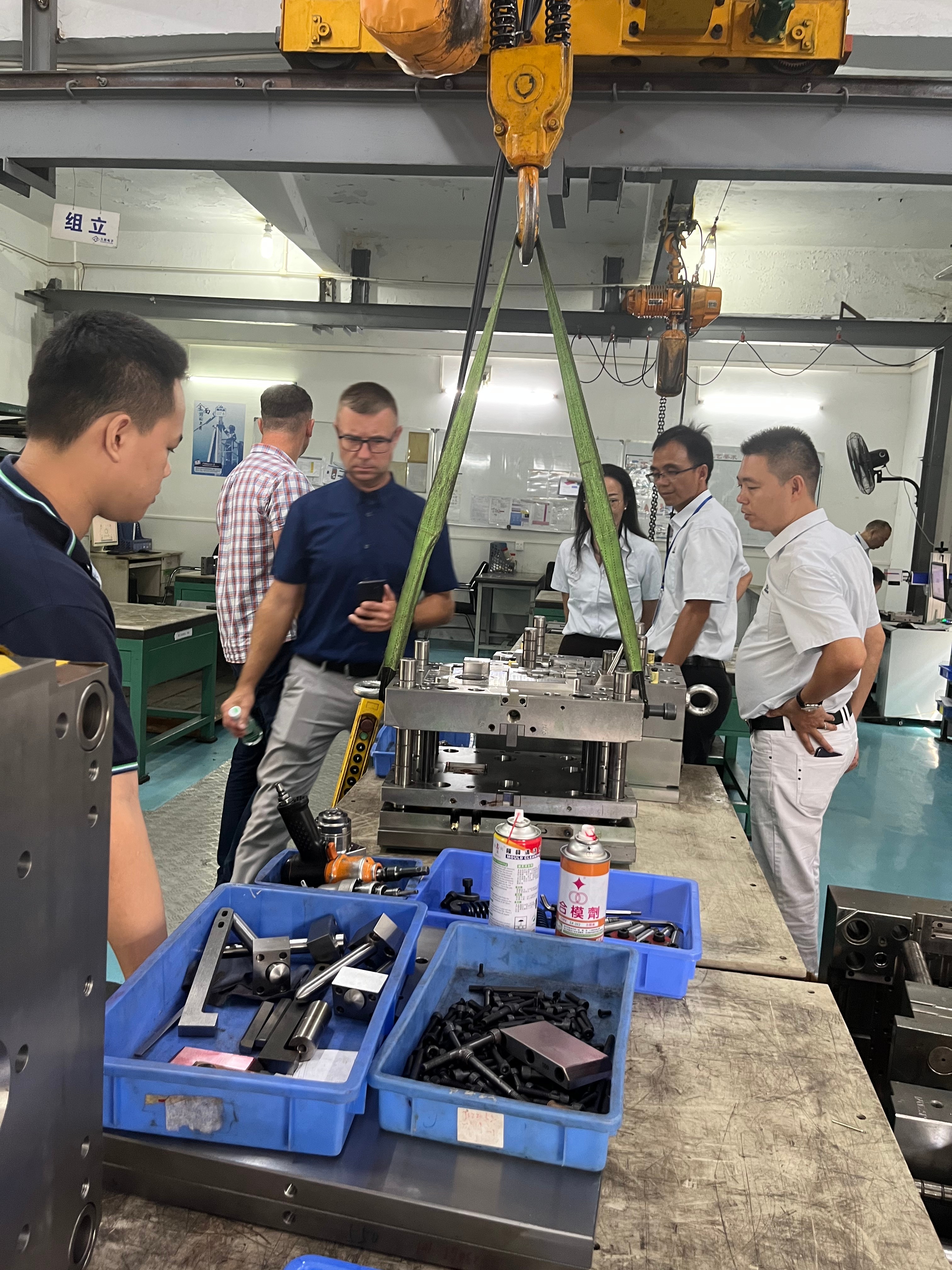
Flow lines are a common phenomenon in the world of injection molding, often impacting the aesthetic and functional quality of molded parts. These lines appear as streaks or patterns on the surface of the finished product, resulting from variations in material flow during the injection process. Understanding flow lines in injection molding is essential for manufacturers seeking to enhance their product quality and minimize defects.
Defining Flow Lines in Injection Molding
Flow lines in injection molding refer to visible marks or streaks that occur on the surface of a molded part due to uneven cooling or inconsistent flow of molten plastic within the mold cavity. These imperfections can be particularly noticeable on larger surfaces where material has traveled different distances, causing variations in cooling rates. While they may not always compromise structural integrity, flow lines can significantly detract from a part's visual appeal and marketability.
Common Causes of Flow Lines
Several factors contribute to the formation of flow lines during the injection molding process. One primary cause is inadequate melt temperature, which can lead to premature cooling before complete filling occurs, resulting in uneven flow patterns. Other culprits include improper gate design or placement, insufficient injection speed, and variations in material viscosity—all of which can exacerbate flow line defects if not carefully managed.
Differentiating Flow Lines from Weld Lines
While both flow lines and weld lines involve issues related to material flow during injection molding, they stem from different causes and exhibit distinct characteristics. Weld lines occur when two separate flows of molten plastic meet but do not fully fuse together due to insufficient heat or pressure—a scenario often seen at junctions where multiple gates converge within a mold cavity. In contrast, flow lines are more about surface aesthetics caused by inconsistent cooling rather than fusion failure; thus recognizing these differences is vital for implementing effective solutions when asking how do you prevent flow lines in injection molding?
What is a Flowmark in Injection Molding?
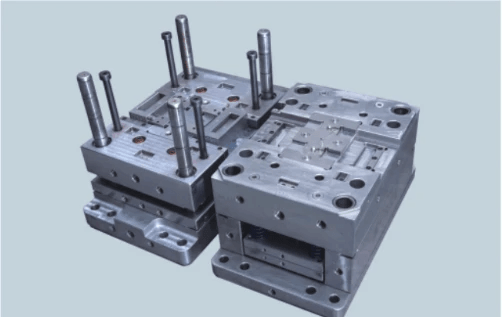
In the realm of injection molding, flowmarks are defects that can significantly impact the aesthetic and functional quality of molded products. These marks appear as streaks or lines on the surface of an injection-molded part, often caused by variations in material flow during the injection process. Understanding what a flowmark is in injection molding is vital for manufacturers aiming to produce high-quality components without visual or structural flaws.
Characteristics of Flowmarks
Flowmarks are typically characterized by their linear appearance, which can resemble streaks or bands across the surface of a molded part. Unlike weld lines injection molding, which occur at the junctions where two flow fronts meet, flowmarks result from inconsistent material flow that creates uneven cooling and solidification patterns. The presence of these defects often indicates issues with processing parameters such as temperature, pressure, or even mold design.
Implications of Flowmarks for Product Quality
The implications of flowmark defects extend beyond mere aesthetics; they can also affect product performance and durability. Depending on their severity and location, flowmarks may weaken structural integrity or lead to areas prone to failure under stress. Therefore, addressing these defects is crucial for maintaining high standards in product quality and ensuring customer satisfaction.
Solutions to Mitigate Flowmark Defects
To prevent flowmark defects effectively, manufacturers should focus on optimizing their processes through various strategies. First off, ensuring proper temperature control during the injection process can help achieve uniform material flow and minimize discrepancies that lead to flow marks. Additionally, advanced mold design techniques can enhance material distribution within the cavity—this ties back into how do you prevent flow lines in injection molding? By implementing these solutions alongside regular maintenance checks and thorough training for operators on best practices in handling materials and machinery, companies can significantly reduce the occurrence of both flow marks and other related defects.
How Do You Prevent Flow Lines in Injection Molding?
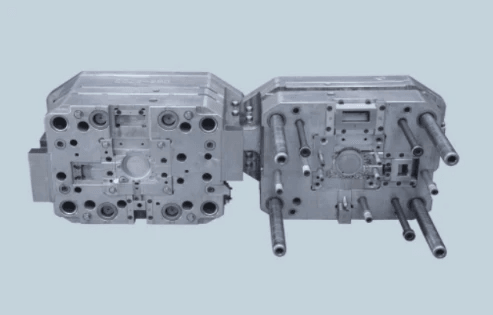
Preventing flow lines in injection molding is crucial for achieving high-quality products. Addressing this issue involves a multi-faceted approach, focusing on material selection, temperature and pressure adjustments, and advanced mold design techniques. By implementing these strategies, manufacturers can significantly reduce the occurrence of flow lines injection molding defects.
Optimizing Material Selection
Choosing the right material is fundamental in preventing flow lines in injection molding. Different polymers have varying flow characteristics, and selecting a material with optimal viscosity can enhance the filling process and minimize defects. Additionally, incorporating additives or modifying the resin can improve flow properties, helping to combat issues like weld lines injection molding that may arise during production.
Material selection also influences how well the product withstands stress during cooling and ejection phases. A well-chosen material will not only mitigate flow mark defects but also contribute to overall product durability and performance. Therefore, understanding the specific requirements of your application is key to making informed decisions about material selection.
Proper Temperature and Pressure Adjustments
Temperature and pressure play pivotal roles in the injection molding process; improper settings can lead to unwanted flow lines injection molding defects. Maintaining optimal melt temperatures ensures that materials remain fluid long enough to fill molds completely without premature solidification. Similarly, adjusting injection pressure allows for better control over how materials enter the mold cavity, reducing turbulence that can lead to flow marks.
Monitoring cooling temperatures is equally important since rapid cooling can create uneven shrinkage patterns that exacerbate existing flaws like weld lines injection molding. Regularly calibrating equipment helps ensure these variables are consistently maintained within ideal ranges throughout production runs. Ultimately, fine-tuning these parameters not only prevents flow line issues but also enhances overall efficiency.
Utilizing Advanced Mold Design Techniques
Advanced mold design techniques are essential for minimizing flow lines in injection molding processes effectively. Implementing features such as improved gate placement or using multi-cavity molds can facilitate more uniform filling patterns while reducing stress concentrations that lead to defects like flow marks or weld lines injection molding issues.
Incorporating simulation tools for mold design allows engineers to visualize potential problems before production starts; this proactive approach helps identify areas where modifications may be needed for optimal performance during actual runs. Moreover, employing cooling channels strategically within molds aids in maintaining consistent temperatures throughout the part’s surface area—further reducing risks associated with uneven shrinkage or warping.
In conclusion, by focusing on optimizing material selection, properly adjusting temperature and pressure settings, and utilizing advanced mold design techniques, manufacturers can effectively prevent flow lines in injection molding processes while enhancing product quality overall.
What is Flow Analysis in Injection Molding?
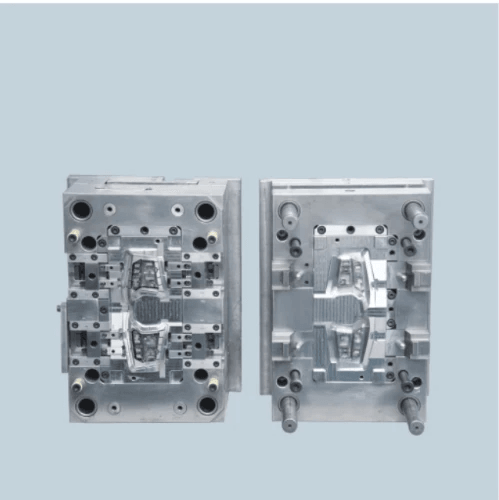
Flow analysis in injection molding is a critical process that examines how the molten plastic flows within the mold cavity. This analysis helps identify potential issues like flow lines and weld lines, ensuring that products meet quality standards. By understanding flow patterns, manufacturers can optimize their processes to minimize defects and enhance product performance.
Importance of Flow Analysis for Quality
The significance of flow analysis in injection molding cannot be overstated when it comes to maintaining product quality. It enables manufacturers to detect early signs of defects such as flow lines and flow mark defects, which can compromise the integrity of the final product. By utilizing flow analysis, companies can make informed decisions on how to prevent flow lines in injection molding, ensuring a smoother production process and better end results.
Tools and Software for Flow Analysis
A variety of tools and software are available to facilitate effective flow analysis in injection molding. These technologies simulate the injection process, allowing engineers to visualize how materials fill the mold cavity while identifying potential problem areas like weld lines in injection molding. Popular software options include Moldflow, SolidWorks Plastics, and Autodesk Simulation, each providing unique features tailored for optimizing the process flow of injection molding.
Case Study: Baoyuan’s Approach to Flow Analysis
Baoyuan has successfully implemented advanced flow analysis techniques to tackle issues related to flow lines in injection molding. By integrating state-of-the-art simulation software into their workflow, they have significantly reduced defects associated with improper material flow patterns. Their commitment to continuous improvement through detailed analysis not only mitigates risks like flow marks but also enhances overall production efficiency.
The Process Flow of Injection Molding
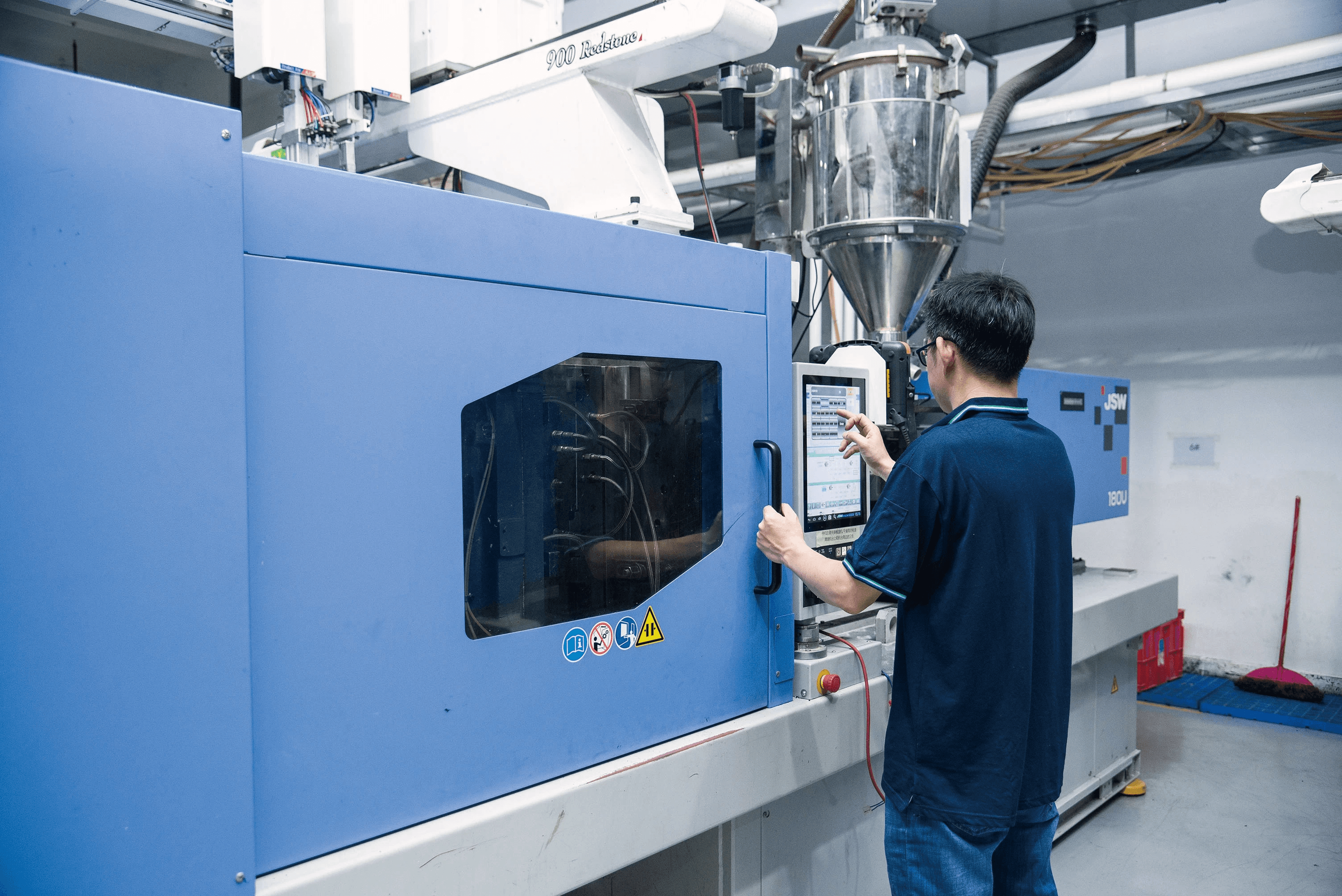
Understanding the process flow of injection molding is crucial for anyone involved in manufacturing. This workflow encompasses a series of steps from material preparation to the final product, ensuring that flow lines in injection molding are minimized. A well-executed process flow not only enhances product quality but also streamlines production efficiency.
Overview of the Injection Molding Workflow
The injection molding workflow begins with raw materials, typically thermoplastics or thermosetting polymers, which are fed into a heated barrel. Here, they are melted and prepared for injection into a mold cavity where they take shape. Following this, the cooling and solidification processes occur before the finished part is ejected from the mold—each step critical in preventing defects such as flow marks and weld lines in injection molding.
Key Phases: Injection, Cooling, and Ejection
The key phases of injection molding consist of injection, cooling, and ejection—each playing a vital role in achieving high-quality products. During the injection phase, molten plastic is injected into a precisely designed mold under pressure; it’s crucial to maintain optimal conditions to avoid flow mark defects. Afterward, during cooling, the material solidifies within the mold; if this step is rushed or improperly executed, it can lead to unwanted flow lines or weld lines in injection molding.
Once cooling is complete, we move on to ejection—this involves removing the finished part from the mold without causing damage or distortion. The timing and technique used during ejection can significantly impact surface integrity and overall quality; therefore, understanding how do you prevent flow lines in injection molding becomes essential here.
Role of Cycle Times in Minimizing Defects
Cycle times play an integral role in minimizing defects throughout the entire process flow of injection molding. Shorter cycle times can enhance productivity but may compromise quality if not managed carefully; thus striking a balance is vital for success. By analyzing cycle times through effective flow analysis in injection molding techniques, manufacturers can identify areas for improvement that reduce occurrences of both flow marks and weld lines while ensuring consistent output.
In summary, mastering each phase of the process flow not only helps mitigate potential defects but also contributes to continuous improvement efforts within manufacturing operations.
Conclusion
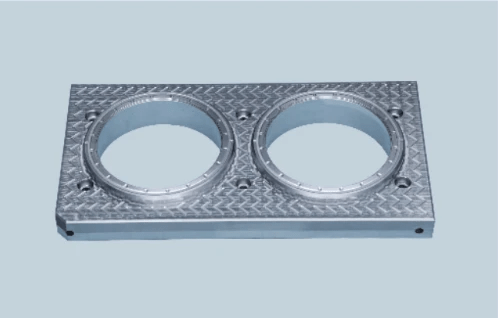
In the dynamic world of injection molding, managing flow lines is crucial for maintaining product quality and operational efficiency. Understanding the intricacies of flow lines, flowmarks, and the overall process flow of injection molding empowers manufacturers to address defects proactively. By implementing effective strategies and leveraging advanced technologies, companies can significantly reduce the occurrence of flow line defects and enhance their production outcomes.
Key Takeaways for Managing Flow Lines
When it comes to managing flow lines in injection molding, several key takeaways emerge. First, optimizing material selection plays a pivotal role in preventing these pesky imperfections from ruining your products. Additionally, understanding how to prevent flow lines in injection molding through proper temperature and pressure adjustments can make a significant difference in achieving a flawless finish.
Another important aspect is recognizing that weld lines injection molding can often be confused with flow lines; however, they are distinct issues requiring different solutions. By differentiating between these two types of defects, manufacturers can tailor their approaches more effectively. Finally, embracing advanced mold design techniques not only helps minimize defects but also enhances overall production efficiency.
Importance of Continuous Improvement in Molding
Continuous improvement is the lifeblood of any successful manufacturing process, including injection molding. Regularly assessing practices related to flow analysis in injection molding ensures that manufacturers stay ahead of potential defects like flow marks and weld lines. Adopting a mindset focused on improvement fosters innovation and encourages teams to seek out new methods for enhancing product quality.
Furthermore, investing time in training staff about what a flowmark in injection molding entails will empower them to identify issues early on before they escalate into bigger problems. Cultivating an environment where feedback is valued leads to better practices over time—ultimately resulting in fewer defects and higher customer satisfaction rates. Remember that every small adjustment contributes to the larger goal of consistent quality.
Resources for Further Learning on Injection Molding
For those eager to dive deeper into the complex world of injection molding, numerous resources are available that cover everything from basic principles to advanced techniques like flow analysis in injection molding. Industry publications often provide insightful articles about managing common challenges such as flow mark defects or optimizing mold design processes effectively.
Online courses and webinars hosted by leading experts offer valuable knowledge on how do you prevent flow lines in injection molding while exploring innovative technologies shaping the industry today. Engaging with professional communities or forums dedicated to this field can also provide real-world insights from peers facing similar challenges—making it easier than ever before to stay informed about best practices.