Baoyuan
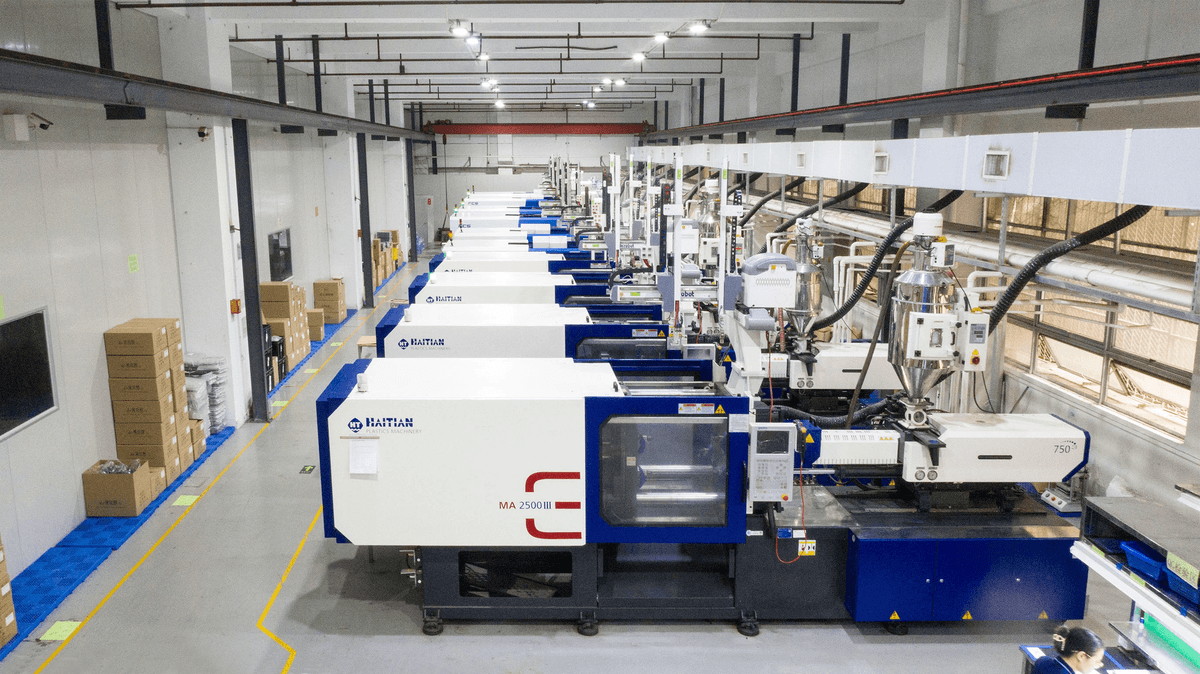
Baoyuan stands out in the automotive injection molding landscape, showcasing a blend of innovative mold design and advanced manufacturing techniques. The company has carved a niche by focusing on the specific needs of the injection plastic automobile sector, ensuring that their products meet the high standards required by automotive manufacturers. With a commitment to quality and efficiency, Baoyuan is a key player among automotive injection molding companies.
Expertise in Mold Design
At Baoyuan, expertise in mold design is not just an asset; it's a cornerstone of their operations. The team utilizes state-of-the-art technology to create molds that are tailored for specific applications within the automotive industry. This meticulous attention to detail ensures that each injection plastic automobile component fits perfectly and functions optimally, reducing waste and enhancing production efficiency.
Proficient in Injection Molding Techniques
They employ methods that allow for precise control over temperature and pressure, ensuring high-quality outputs every time. This expertise translates into reduced cycle times and lower costs, making them an attractive partner for those looking into injection plastic automobile production.
Focus on Quality Assurance
Quality assurance is paramount at Baoyuan, where rigorous testing protocols are implemented at every stage of production. The company uses only top-grade materials—often asking What kind of plastic is used in automobiles?—to ensure durability and performance under demanding conditions. By prioritizing quality throughout their processes, they not only meet but often exceed industry standards for automotive components made via Automotive Injection Molding.
Husky Injection Molding Systems
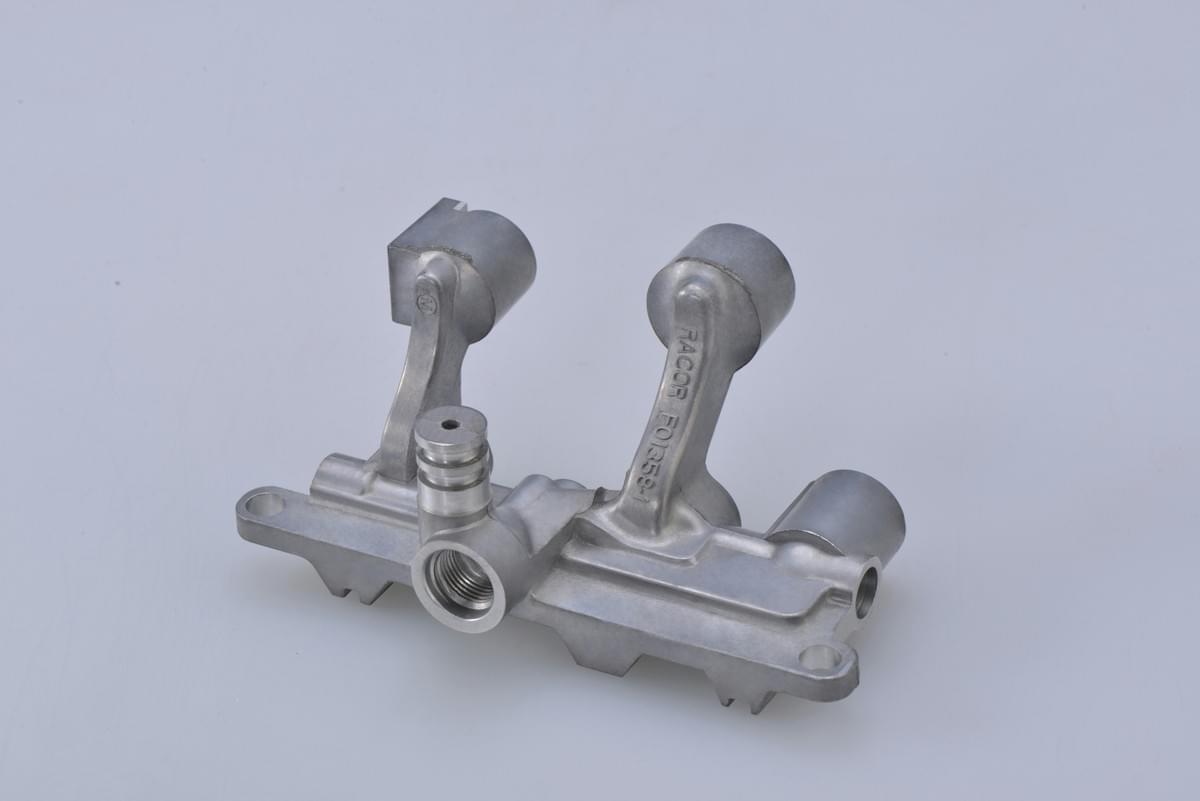
Husky Injection Molding Systems stands at the forefront of the automotive injection molding landscape, revolutionizing how manufacturers approach production. Their pioneering injection technology is designed to optimize efficiency and precision, making them a go-to partner for automotive companies looking to enhance their processes. By focusing on cutting-edge advancements in injection plastic automobile applications, Husky has solidified its reputation as a leader in the industry.
Pioneering Injection Technology
Husky's commitment to innovation in injection technology allows them to produce high-quality components that meet the demanding standards of the automotive sector. Their advanced systems utilize state-of-the-art techniques that ensure consistent quality and performance, which is crucial when considering what kind of plastic is used in automobiles. By employing these technologies, Husky not only enhances production speed but also reduces waste, significantly impacting the overall cost of injection plastic automobile manufacturing.
In exploring what is the injection method of plastic, it’s essential to understand that Husky employs a variety of approaches tailored specifically for automotive needs. Their machines are engineered for versatility and adaptability, allowing manufacturers to switch between different types of materials seamlessly. This flexibility positions Husky as a key player among automotive injection molding companies striving for excellence in production.
Custom Solutions for Automotive Needs
Whether it's designing molds or optimizing processes for specific vehicle components, their team collaborates closely with clients to ensure every requirement is met efficiently. This customer-centric approach not only addresses immediate needs but also fosters long-term partnerships built on trust and reliability.
The ability to create specialized solutions means that Husky can cater to various aspects of automotive production—from exterior panels made from robust plastics to intricate interior components requiring precise finishes. The question What kind of plastic is used in automobiles? often leads back to materials like polypropylene and ABS, which are staples in Husky's offerings due to their durability and lightweight characteristics. With such expertise, they effectively lower the overall injection plastic automobile cost while maintaining high standards.
Global Reach and Support
With operations spanning across multiple continents, Husky boasts a global reach that ensures support wherever their machines are deployed. This extensive network allows them not only to sell equipment but also provide ongoing assistance—an invaluable asset for businesses navigating complex production environments within Automotive Injection Molding sectors worldwide. Customers can rely on Husky's vast resources and knowledge base regardless of geographical location.
In addition to physical presence, their commitment extends into digital realms with online support tools designed for troubleshooting and efficiency optimization—because who doesn’t love having help at their fingertips? As industries evolve towards more sustainable practices, having a partner like Husky who understands both local market needs and global trends becomes essential for any manufacturer aiming at success in today’s competitive landscape.
Engel
Engel is a frontrunner in the field of Automotive Injection Molding, consistently pushing the boundaries of what is possible with injection molding machines. Their commitment to innovation ensures that they remain at the forefront of technology, enabling manufacturers to produce high-quality components for vehicles more efficiently than ever before. With a strong emphasis on sustainability and automotive applications, Engel is not just shaping the future of injection plastic automobiles; they're redefining it.
Innovation in Injection Molding Machines
Engel's dedication to innovation in injection molding machines has led them to develop cutting-edge technologies that enhance production capabilities for automotive manufacturers. By employing advanced techniques such as multi-component injection and in-mold labeling, they are able to create intricate designs that meet the demands of modern vehicle manufacturing. This innovation not only improves efficiency but also reduces costs associated with producing various plastic components used in automobiles.
In terms of performance, Engel machines are designed to handle a wide range of materials and offer exceptional precision during the injection process. This versatility allows manufacturers to choose from different types of plastics used in injection molding, ensuring they can meet specific requirements for durability and strength needed for automotive applications. Ultimately, Engel’s innovations help answer critical questions like What kind of plastic is used in automobiles? by providing tailored solutions that enhance product quality.
Sustainable Manufacturing Practices
Sustainability is a cornerstone of Engel's operational philosophy, particularly when it comes to their impact on Automotive Injection Molding processes. They have implemented practices that minimize waste and energy consumption while maximizing efficiency throughout their production lines. By focusing on sustainable manufacturing methods, Engel addresses environmental concerns while still delivering high-quality injection plastic automobile components.
Their commitment extends beyond just reducing waste; Engel also invests heavily in research aimed at developing bio-based plastics that can be utilized within their systems. These eco-friendly alternatives provide viable options for manufacturers seeking greener solutions without sacrificing performance or quality—answering questions like What plastic is used in injection? with innovative materials designed for sustainability. As a result, companies partnering with Engel can confidently align themselves with eco-conscious practices.
Strong Focus on Automotive Applications
Engel’s strong focus on automotive applications makes them one of the leading Automotive Injection Molding companies today. Their expertise enables them to cater specifically to the unique demands and challenges faced by car manufacturers when producing various parts—from dashboards to exterior panels—using advanced injection molding techniques tailored for these needs. This specialization ensures that clients receive not only high-quality products but also insightful guidance throughout the entire manufacturing process.
Furthermore, Engel recognizes the evolving landscape within the automotive industry where electric vehicles and lightweight materials are becoming increasingly prevalent. By adapting their technologies accordingly, they remain relevant and capable of meeting future demands while addressing common queries about cost-effectiveness—“What is the injection method of plastic?” The answer lies within Engel’s advanced methodologies which optimize production costs without compromising quality or performance.
In conclusion, if you're looking into investing in an efficient partner for your next project involving an injection plastic automobile component, look no further than Engel! Their blend of innovative machinery and sustainable practices positions them as a top choice among automotive manufacturers aiming for excellence without sacrificing environmental responsibility.
Arburg
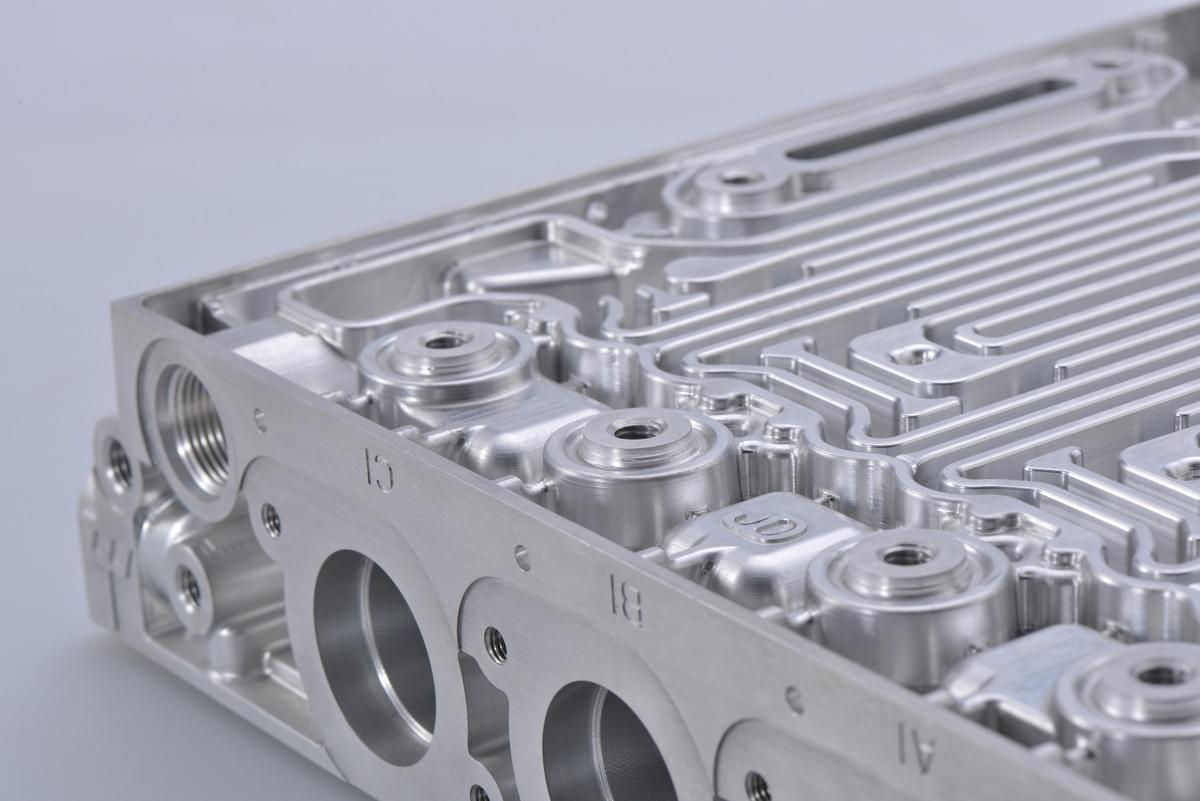
Arburg stands tall in the realm of Automotive Injection Molding, showcasing a rich tapestry of versatile injection molding capabilities that cater to the diverse needs of the automotive industry. Their innovative approach allows for the production of complex shapes and components, which are essential in modern vehicles. With their advanced technology, Arburg has become a go-to partner for companies seeking high-quality injection plastic automobile parts.
Versatile Injection Molding Capabilities
They employ a range of techniques that adapt to various materials and specifications, making them an invaluable player among automotive injection molding companies. The ability to use different types of plastics—like ABS, polycarbonate, and polypropylene—enables Arburg to meet specific requirements in terms of durability and performance for automotive applications.
Advanced Production Techniques
Arburg doesn't just stop at versatility; they also embrace advanced production techniques that streamline manufacturing processes and enhance quality control. By integrating automation and smart technology into their production lines, they ensure that every piece produced meets stringent automotive standards. This commitment not only reduces costs associated with injection plastic automobile manufacturing but also boosts efficiency—a win-win for any automotive company looking to stay competitive.
Commitment to Efficiency and Quality
They meticulously monitor every phase of production, from initial designs to final products, ensuring that only the best materials are used—after all, what kind of plastic is used in automobiles can make or break a vehicle's performance? Their focus on efficiency translates into lower injection plastic automobile costs while maintaining high standards for durability and safety.
Milacron
Milacron stands as a formidable player in the realm of Automotive Injection Molding, offering comprehensive manufacturing solutions that cater to the specific needs of the automotive sector. With a deep understanding of injection plastic automobile technology, they provide innovative approaches that streamline production processes and enhance product quality. Their commitment to excellence ensures that clients receive tailored solutions designed to meet their unique requirements.
Comprehensive Manufacturing Solutions
Milacron's comprehensive manufacturing solutions encompass everything from initial design to final production, making them a one-stop shop for automotive companies. They utilize cutting-edge technology and advanced machinery to deliver high-quality injection plastic components that are crucial for modern vehicles. By integrating various stages of production, Milacron helps reduce lead times and costs associated with the injection plastic automobile process.
The company employs a variety of plastics suitable for automotive applications, ensuring durability and performance in every component produced. This versatility in materials allows them to cater to diverse client demands while maintaining high standards in quality assurance. As questions arise about what kind of plastic is used in automobiles, Milacron confidently offers insights into their extensive range of options tailored specifically for vehicle manufacturing.
Specialized in Injection Plastic Automobile Technology
Milacron specializes in injection plastic automobile technology, which plays a vital role in shaping the future of vehicle design and functionality. Their expertise lies not just in producing parts but also understanding what is the injection method of plastic and how it can be optimized for efficiency and cost-effectiveness. This specialization ensures that automotive manufacturers can rely on Milacron for innovative solutions that push the boundaries of traditional manufacturing techniques.
In an industry where precision is paramount, Milacron’s focus on specialized technologies means they can produce intricate designs with remarkable accuracy using advanced injection molding techniques. This capability not only enhances aesthetics but also contributes significantly to vehicle performance and safety standards—essential factors when considering what kind of plastic is used in automobiles today. By staying at the forefront of technological advancements, they ensure their clients remain competitive within an ever-evolving market.
Customer-Centric Approach
What sets Milacron apart from other automotive injection molding companies is their unwavering customer-centric approach. They prioritize understanding each client's unique challenges and goals, which allows them to develop customized solutions tailored specifically to those needs—whether it’s reducing the injection plastic automobile cost or enhancing production efficiency through smarter methodologies. This dedication fosters long-term partnerships built on trust and reliability.
Furthermore, by engaging closely with customers throughout every stage—from conceptualization to delivery—Milacron ensures transparency and open communication channels that facilitate quick problem-solving when necessary. Their team actively seeks feedback and continuously refines processes based on client input, demonstrating their commitment not just to products but also relationships within the industry ecosystem. In a landscape where competition is fierce among automotive injection molding companies, this focus on customer satisfaction truly makes Milacron stand out.
Conclusion
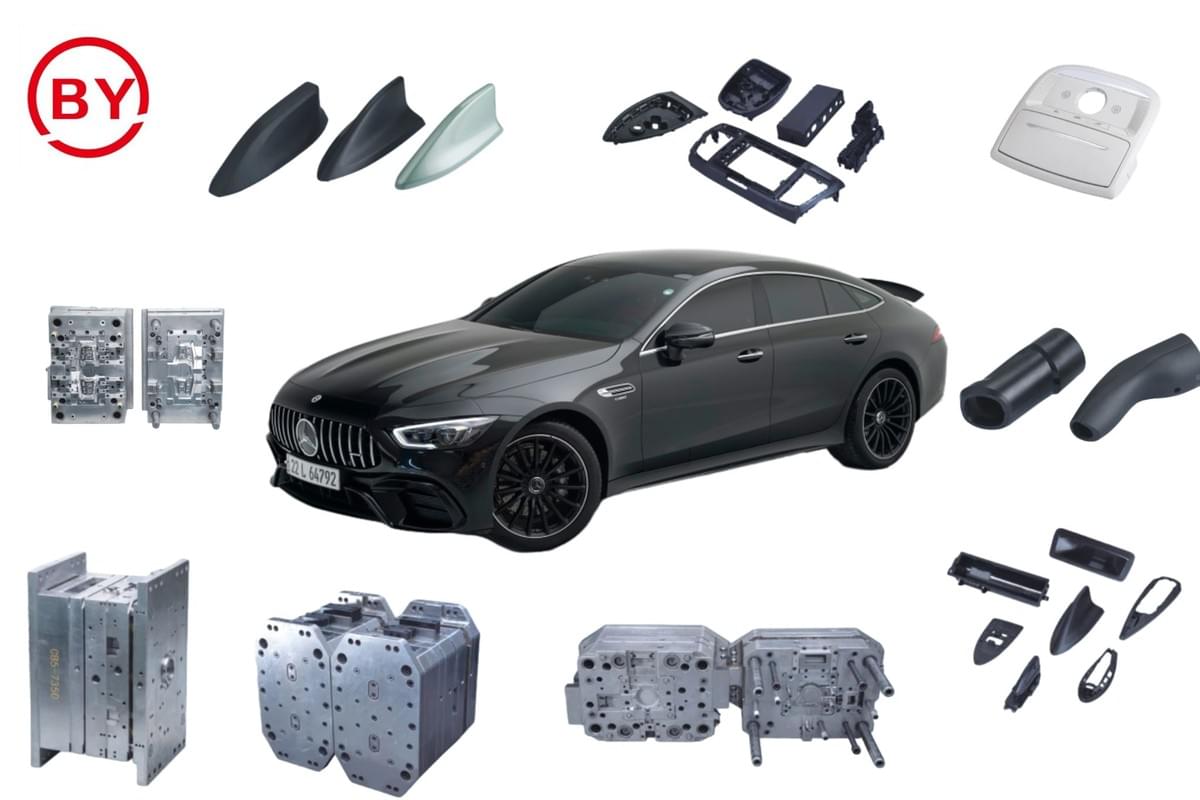
In the rapidly evolving landscape of the automotive industry, the role of Automotive Injection Molding cannot be overstated. Leading companies like Baoyuan, Husky, Engel, Arburg, and Milacron are at the forefront of this transformation, utilizing innovative techniques and high-quality materials to produce essential components for vehicles. With a focus on efficiency and sustainability, these automotive injection molding companies are shaping the future of how we think about and use injection plastic in automobiles.
Leading Companies in Automotive Injection Molding
The automotive sector is heavily reliant on specialized manufacturers that excel in injection molding techniques. Companies such as Baoyuan and Husky Injection Molding Systems have set benchmarks with their advanced mold designs and pioneering technologies. Their expertise not only enhances product quality but also significantly reduces production costs associated with injection plastic automobile components.
The Future of Injection Plastic in Vehicles
As we look ahead, the future of injection plastic in vehicles appears promising, driven by technological advancements and a growing demand for lightweight materials. Innovations in automotive design increasingly favor plastics due to their versatility; they can be molded into complex shapes while providing durability at a lower weight compared to traditional materials. The evolution of what kind of plastic is used in automobiles will likely lead to even more efficient manufacturing processes that reduce costs while enhancing performance.
Choosing the Right Automotive Injection Molding Partner
Selecting an appropriate partner for your injection molding needs is crucial for success in today’s competitive market. Factors such as expertise in specific types of plastics—like those commonly used in automobiles—and a strong commitment to quality assurance should guide your decision-making process. Ultimately, understanding what is the injection method of plastic? along with its benefits can help you navigate through options available among various Automotive Injection Molding companies.